Automation Equipment
Automation encompasses a broad spectrum of technologies and practices that have fundamentally transformed manufacturing. By employing computer-controlled, automated, and robotic machinery, tasks like material handling, product forming, welding, milling, grinding, cleaning, assembly, and packaging are performed with precision and efficiency. Automation extends beyond traditional manufacturing, seamlessly integrating into systems that sort mail, package goods, and process food products. These systems may operate under human supervision, guided by production managers, or autonomously, functioning independently beyond initial programming and routine maintenance.
The History of Automation
The Industrial Age marked a pivotal shift toward automated production. Henry Ford's revolutionary assembly line in 1913 redefined manufacturing, bringing work to laborers via conveyor systems and drastically increasing productivity. Yet even before Ford, Ransom Olds pioneered assembly line concepts in 1901, achieving remarkable efficiency gains.
Advancements in automation continued, exemplified by the automated bottle-blowing machine of 1905, which transformed glass production efficiency. As industrial demand grew, innovations like the sectional electric drive control in 1919 enabled consistent paper production by precisely managing drying times. In Japan, synchronized automation emerged in 1930 with the invention of accurate electrical timers, setting the stage for post-World War II developments that positioned the nation as a leader in automated manufacturing.
The 1960s ushered in robotic arms capable of simple repetitive tasks, culminating in the Stanford Arm of 1969, which introduced multi-functional capabilities. By the 1980s, the Computer Age revolutionized manufacturing with Computer Integrated Manufacturing (CIM) and Computer Numerical Control (CNC) systems. These technologies enabled rapid prototyping and precise mass production, paving the way for additive manufacturing in the 2010s, where 3D printing began shaping complex objects from digital models.
Industrial Automation Design and Uses
Automation systems are tailored to execute specific tasks through synchronized processes. Using servo mechanisms, pneumatics, and advanced computer control, these systems ensure materials are delivered and processed with impeccable timing. Conveyor systems, whether belt-driven, pneumatic, or bucket-based, transport items through steps that may involve forming, cutting, welding, or coating. In food processing, automated machines clean, sort, and package products to ensure uniform quality.
Glass, plastic, and metal production benefit significantly from automation. Automated smelting, molding, and extrusion processes efficiently create components, while robotic welding and cutting provide precision in assembly. These systems not only streamline production but also enhance safety, reduce waste, and maintain consistent quality.
What Automation Means For Industry
Automation enhances safety by minimizing human exposure to hazardous environments, reducing accidents, and eliminating repetitive motion injuries. Economically, automated systems lower production costs by operating continuously without breaks or shift changes. This ensures higher output with fewer errors. However, fully automated "dark" factories, while highly efficient, pose risks of cascading failures if malfunctions occur. To mitigate this, electronic monitoring and remote surveillance systems are integrated for real-time oversight.
Automation Industry Images, Diagrams and Visual Concepts
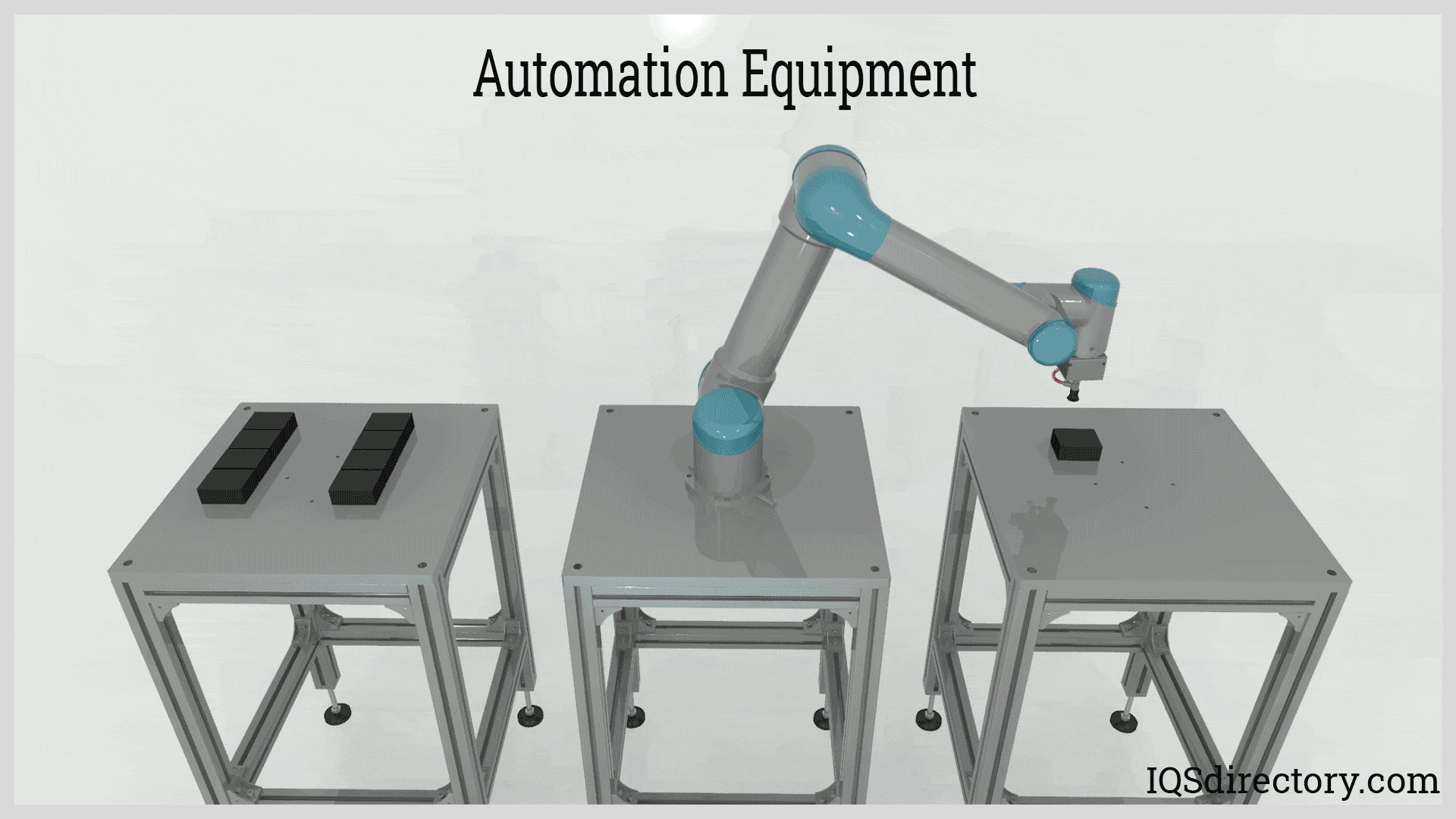
Automation systems are an integration of sensors, controls, and actuators designed to perform functions with minimal or no human intervention.
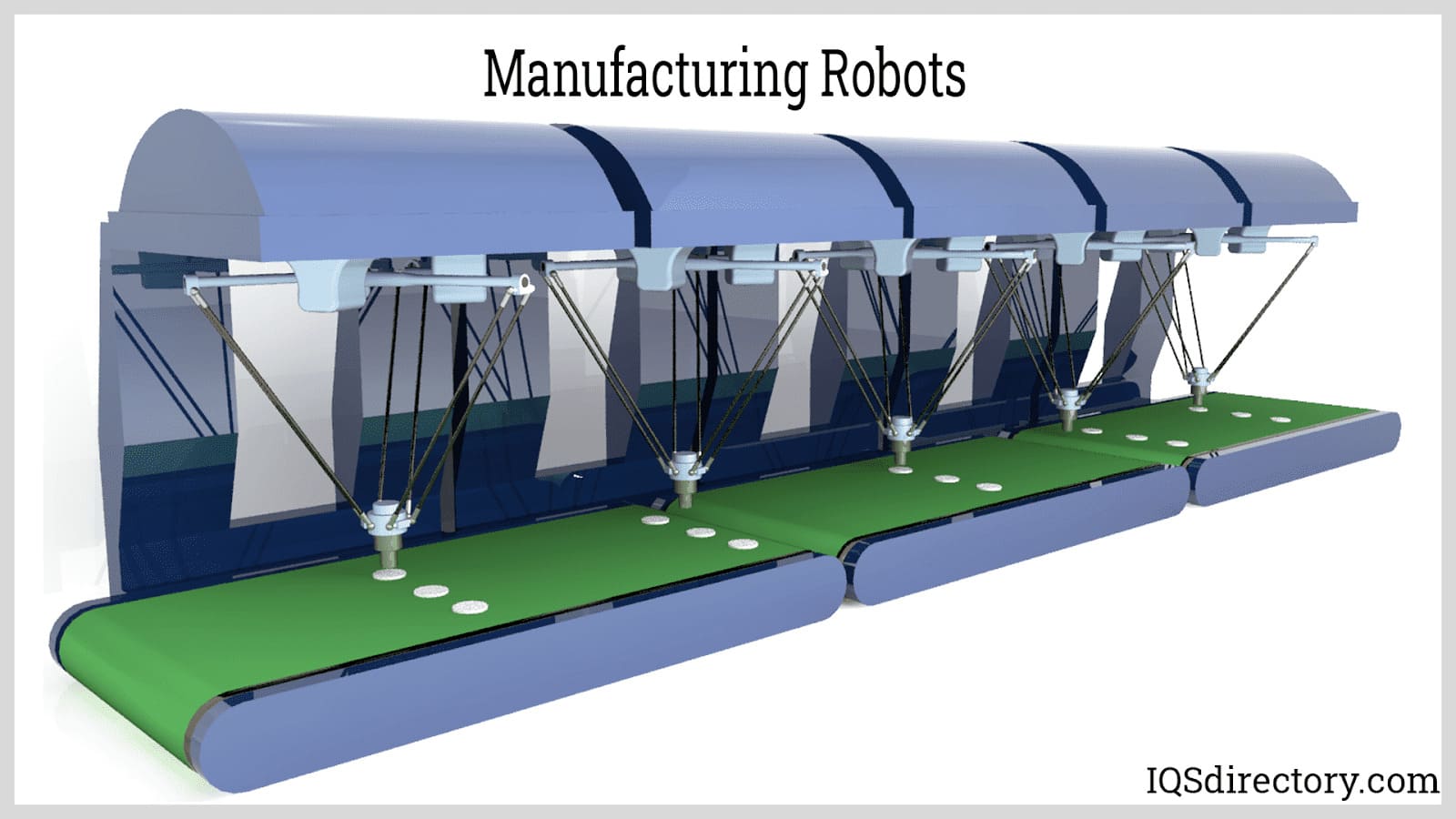
Robots do not experience fatigue and there processing speed is much faster than humans with continuous operation.
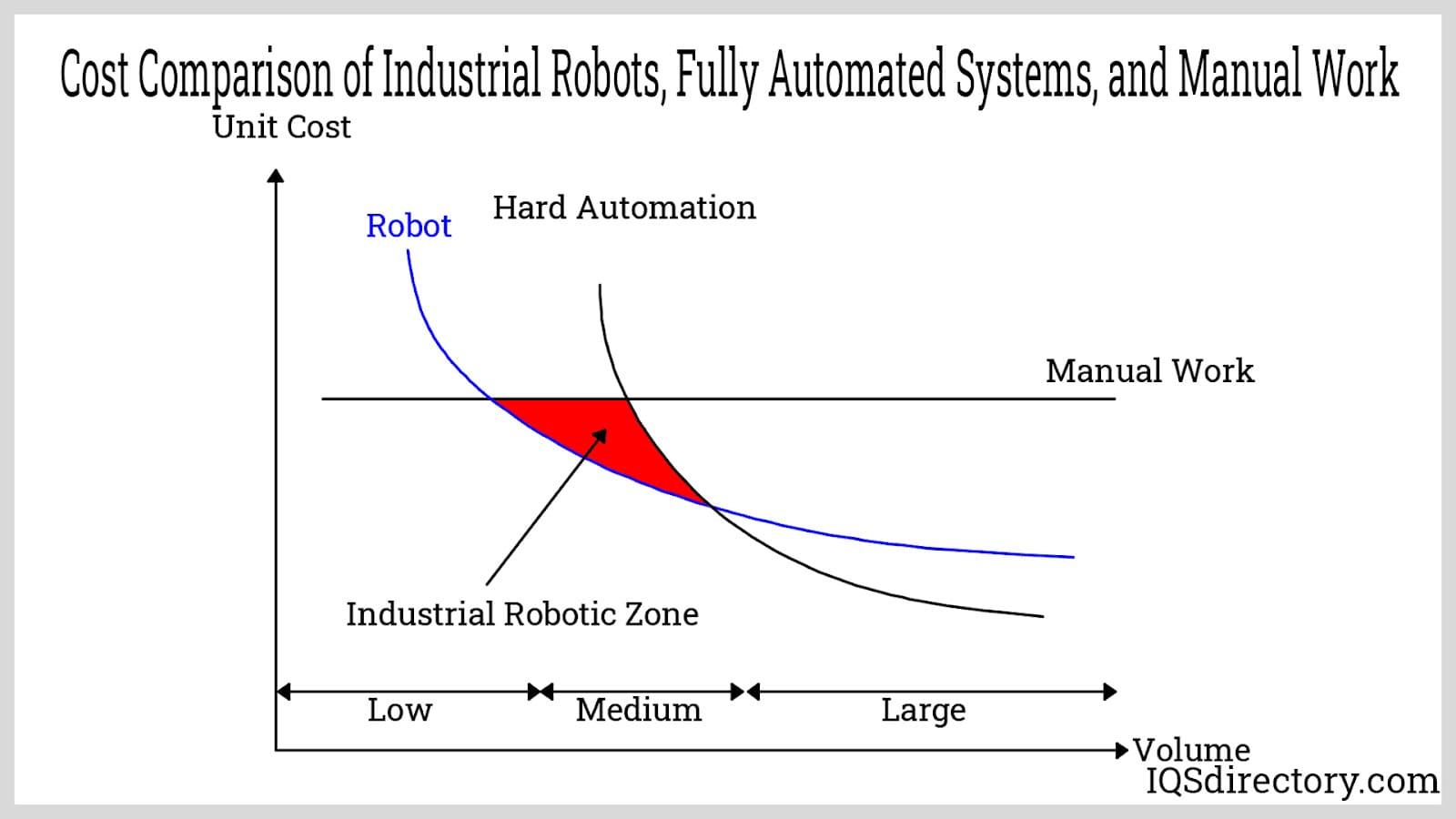
Wastes less raw material and fewer human resource costs once the robotic system is online, an increase product quality, and an increase in production rate.
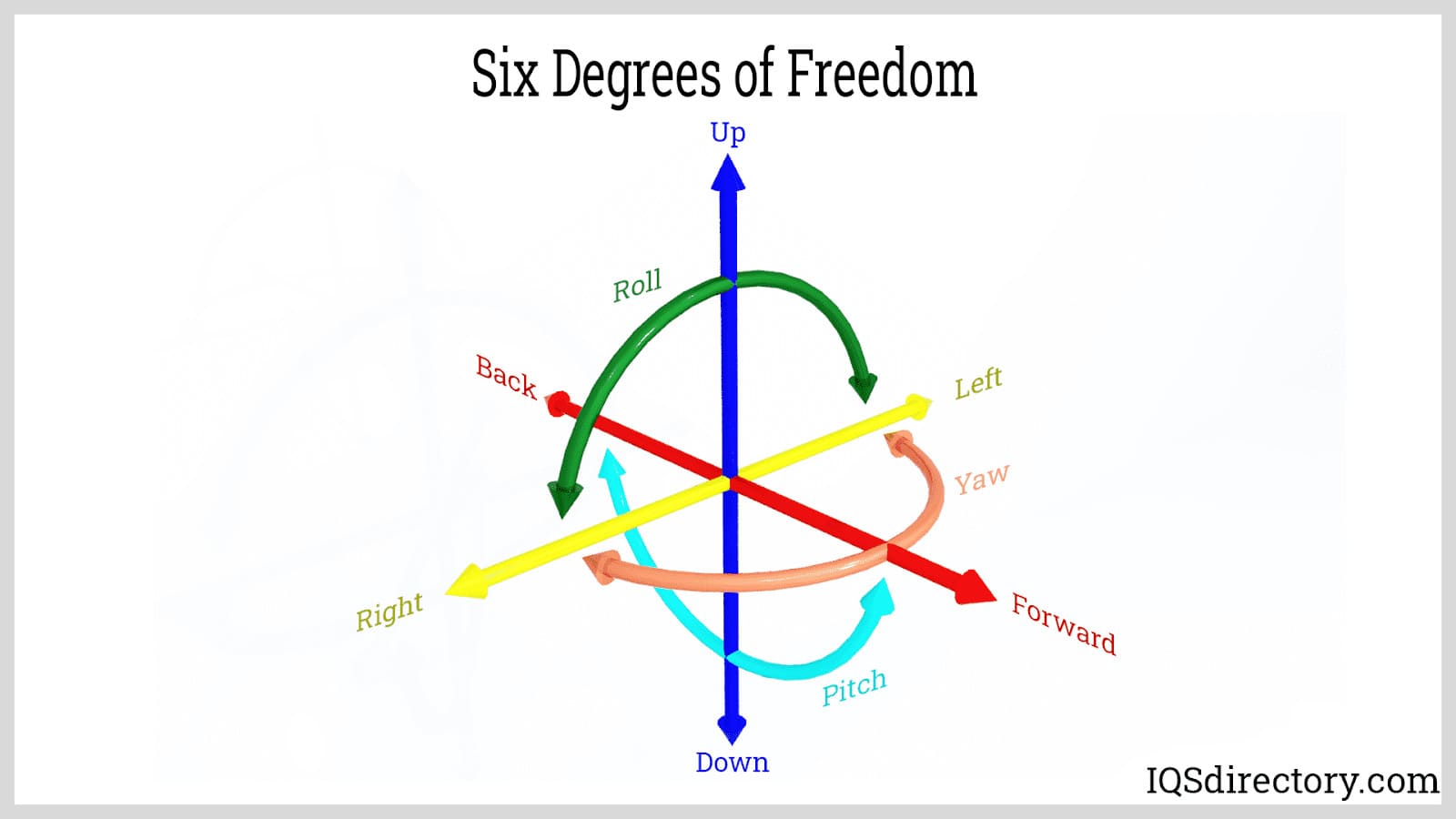
The number of axes and degrees of freedom define a robot's movability.
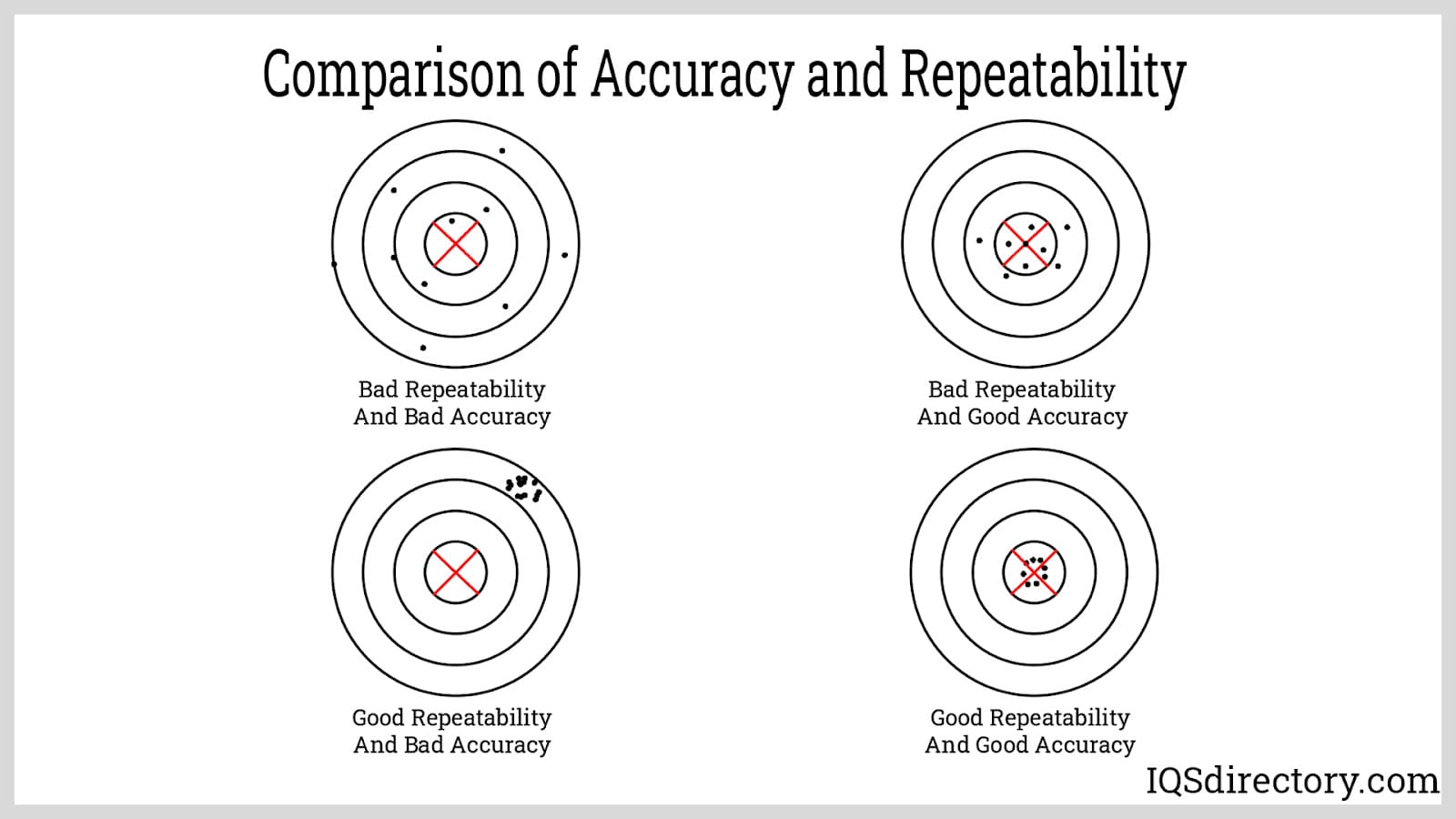
Accuracy and repeatability are the two main characteristics to determine the effectiveness of a robot in task performance.
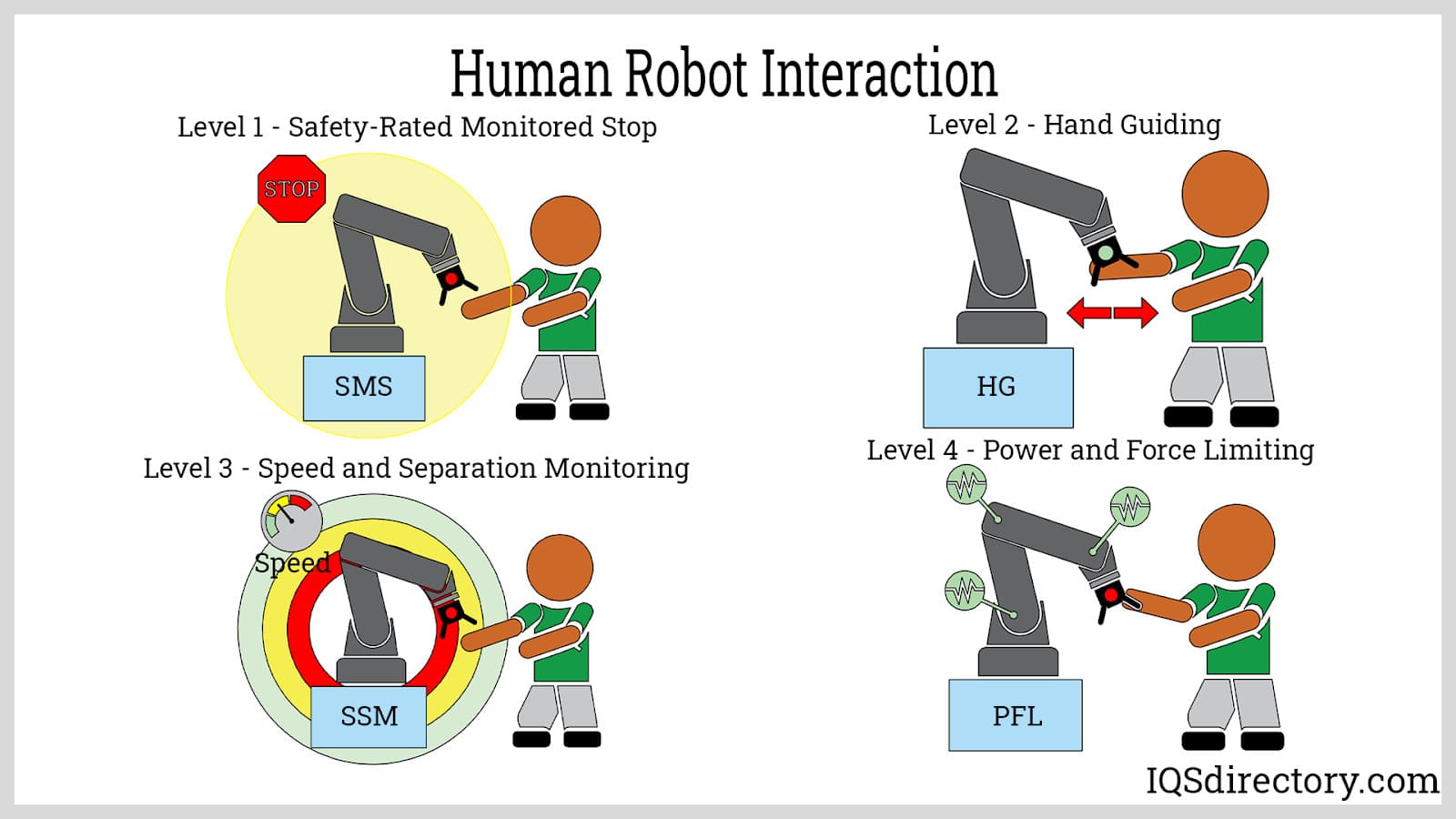
Collaborative robots allow to work safely and include safety features power limiting, safety monitored stop, hand guiding, speed and separation
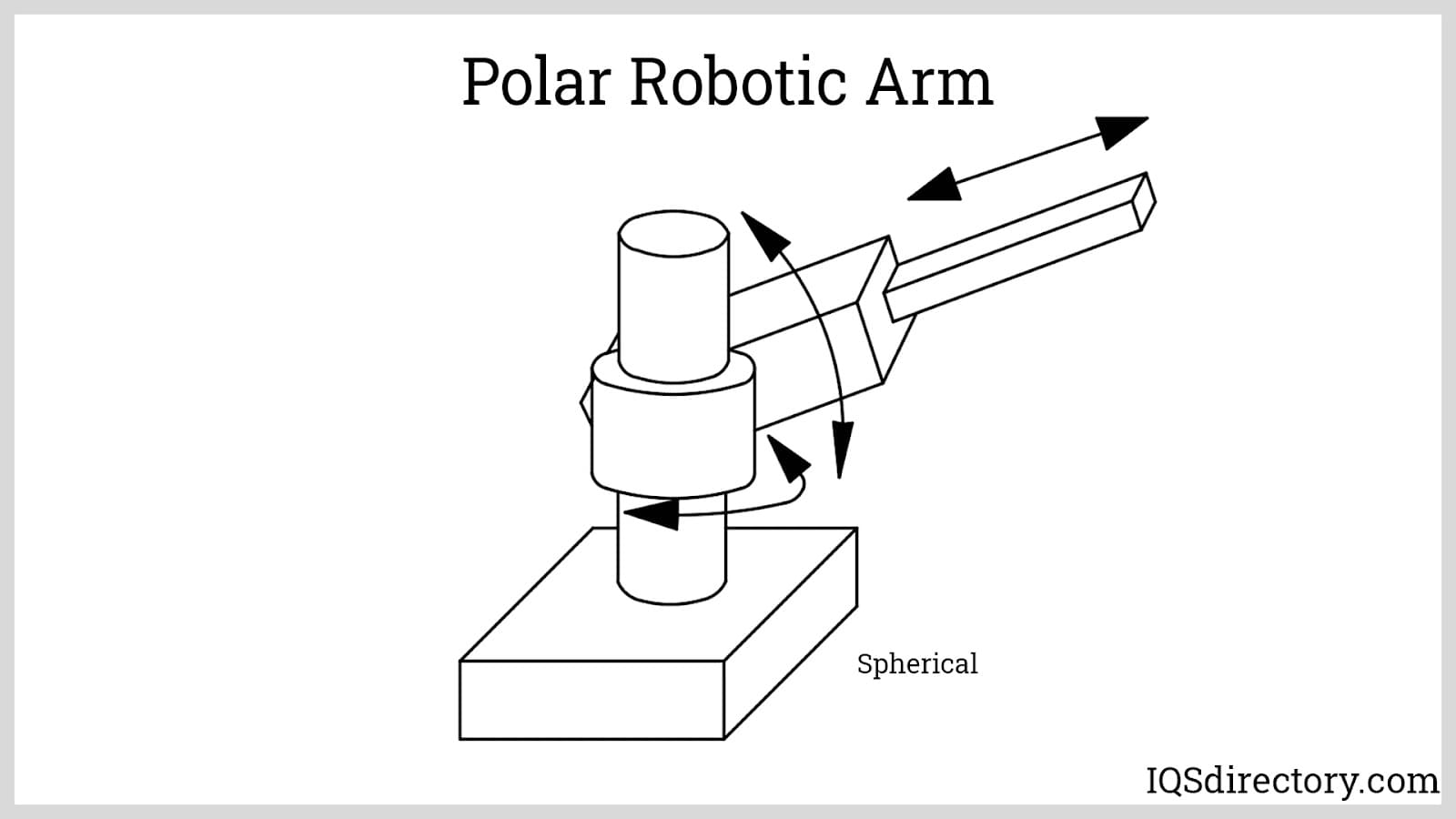
A type of arm configuration which allows for a fixed range of motion depending on the joints.
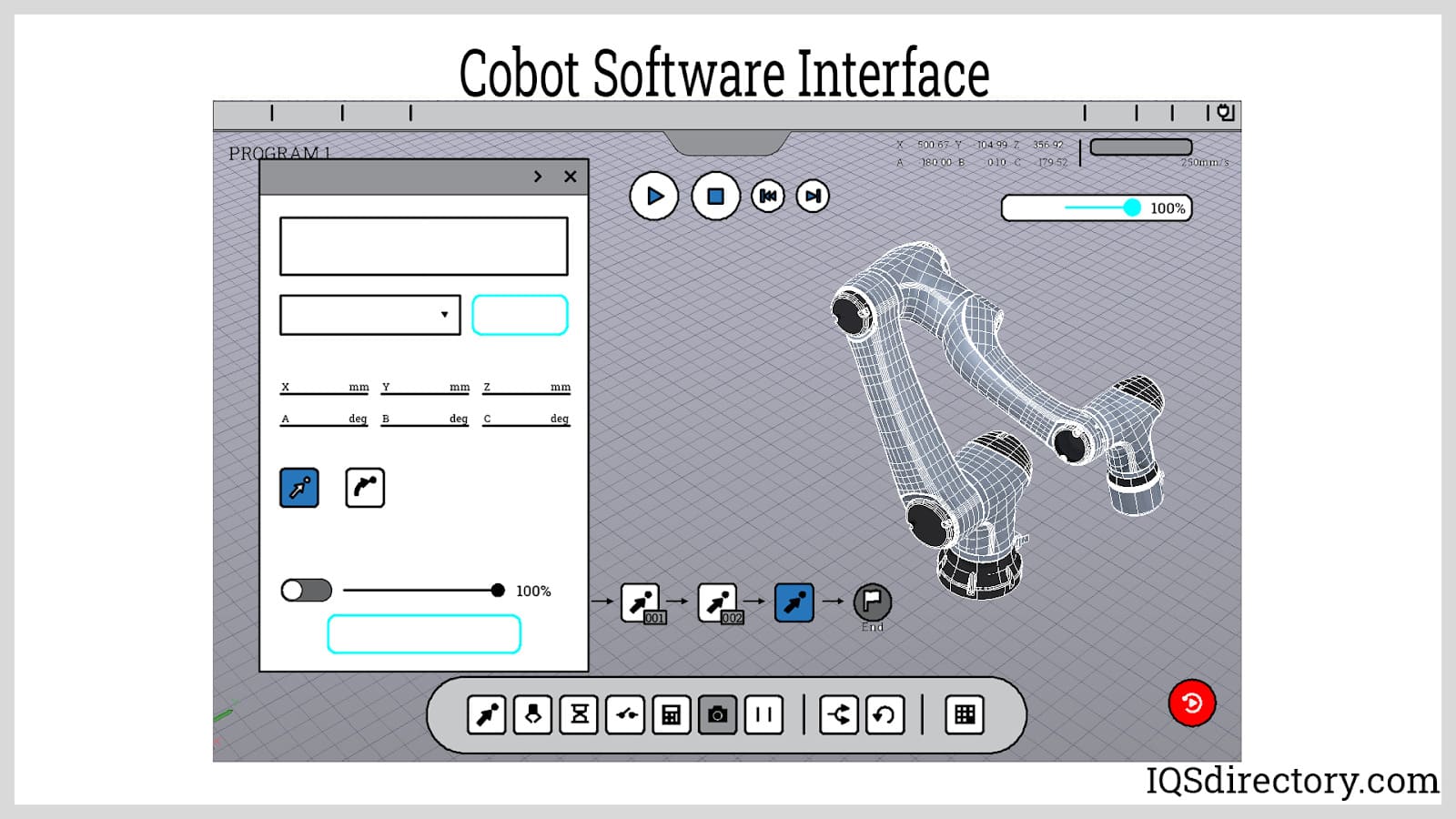
Applications are available for designing and programming collaborative robot applications which have an instinctive and user-friendly.
Types of Automation in Industry
Modern automation employs various methodologies, including:
- Computer-Aided Design (CAD): Facilitating the creation of intricate designs that guide production.
- Computer-Aided Manufacturing (CAM): Enabling computer-controlled processes on assembly lines.
- Additive Manufacturing (AM): Creating complex objects layer by layer from digital models.
- Robotic Automation: Performing multi-axial tasks with precision.
These technologies, complemented by innovations like rapid prototyping and systems integration, have made manufacturing more adaptive and scalable.
Automated Manufacturing Proper Care and Standards
Automated systems require stringent adherence to maintenance schedules and regulatory standards to ensure smooth operation. Regular inspections, cleaning, and calibration prevent breakdowns and maintain efficiency. Standards set by organizations such as OSHA, FDA, ANSI, and ASTM regulate safety, cleanliness, and quality across industries, while guidelines like Current Good Manufacturing Practices (CGMP) ensure compliance in sectors like pharmaceuticals.
Other Automation Equipment Types
Machine automation refers to the computer-operated machines used in an assembly line.
Manufacturing automation refers to the computer-operated equipment and machines found in a manufacturing setting.
Automation Equipment Terms
Actuator
An essential device in closed-loop control systems, translating the control signal from the final control element into action by the control device.
Adjustable Speed
The ability to vary a motor's speed manually or automatically, ensuring that the desired operating speed remains constant regardless of the load.
Assembler
A software tool that converts assembly language instructions into machine-readable code.
Automation
The implementation of systems, processes, or equipment to operate and control functions automatically, reducing or eliminating the need for human intervention. This encompasses the methods and tools employed to achieve automated control.
Automated Storage & Retrieval System
A complex arrangement of controlled systems designed to automatically place and retrieve loads from specified storage locations.
Axis
Any part of a machine or system that moves and requires controlled motion. Coordinated multi-axis systems combine several axes of motion for complex tasks.
Bill of Material
A detailed list of all subassemblies, components, and raw materials that constitute a parent assembly.
CAD (Computer-Aided Design)
Also known as CADD (Computer-Aided Design and Drafting), this system can be integrated with CAM systems to enhance design and manufacturing processes.
CAM (Computer-Aided Manufacturing)
The application of computer technology to generate data that controls a portion or the entirety of the manufacturing process.
Calibration
The process of determining and setting the accuracy or scale graduations of a measuring instrument.
CIM (Computer-Integrated Manufacturing)
The integration of computer systems into every aspect of manufacturing to streamline operations.
Conveyor Belt
A continuously moving belt used to transport objects along an assembly process.
Dark Factory
A fully automated plant floor that operates without human labor.
FMC (Flexible Machine Centre)
An automated system typically comprising CNC machines with robotic systems that load, unload, and transport parts through the system.
JIT (Just-in-Time)
A manufacturing strategy where each operation is precisely synchronized with subsequent processes, minimizing waste and maximizing efficiency.
Load Cell
A transducer that measures force or weight, functioning through strain gauges mounted within the cell on a force beam.
Network
A connected system of computers and peripherals that facilitates communication and data exchange.
Proximity Switch
A contactless sensor that detects the presence or absence of an object and triggers circuit closures or openings in response.
RP (Rapid Prototyping)
A critical phase in assembly system design where small-scale prototypes are created to test key features. This includes sketches, low-fidelity models, CAD visualizations, rapid application development, or video prototyping, accelerating the development of large-scale projects.
Robotics
The design, study, and application of robots, especially in manufacturing and related processes.
Sensor
A device designed to measure motion, forces, or torques acting on a body or joint, providing critical feedback for various applications.
Systems Integration
The coordination of multiple automation functions within a single system to achieve a unified goal.
More Automation Equipment Information