Electric Heaters
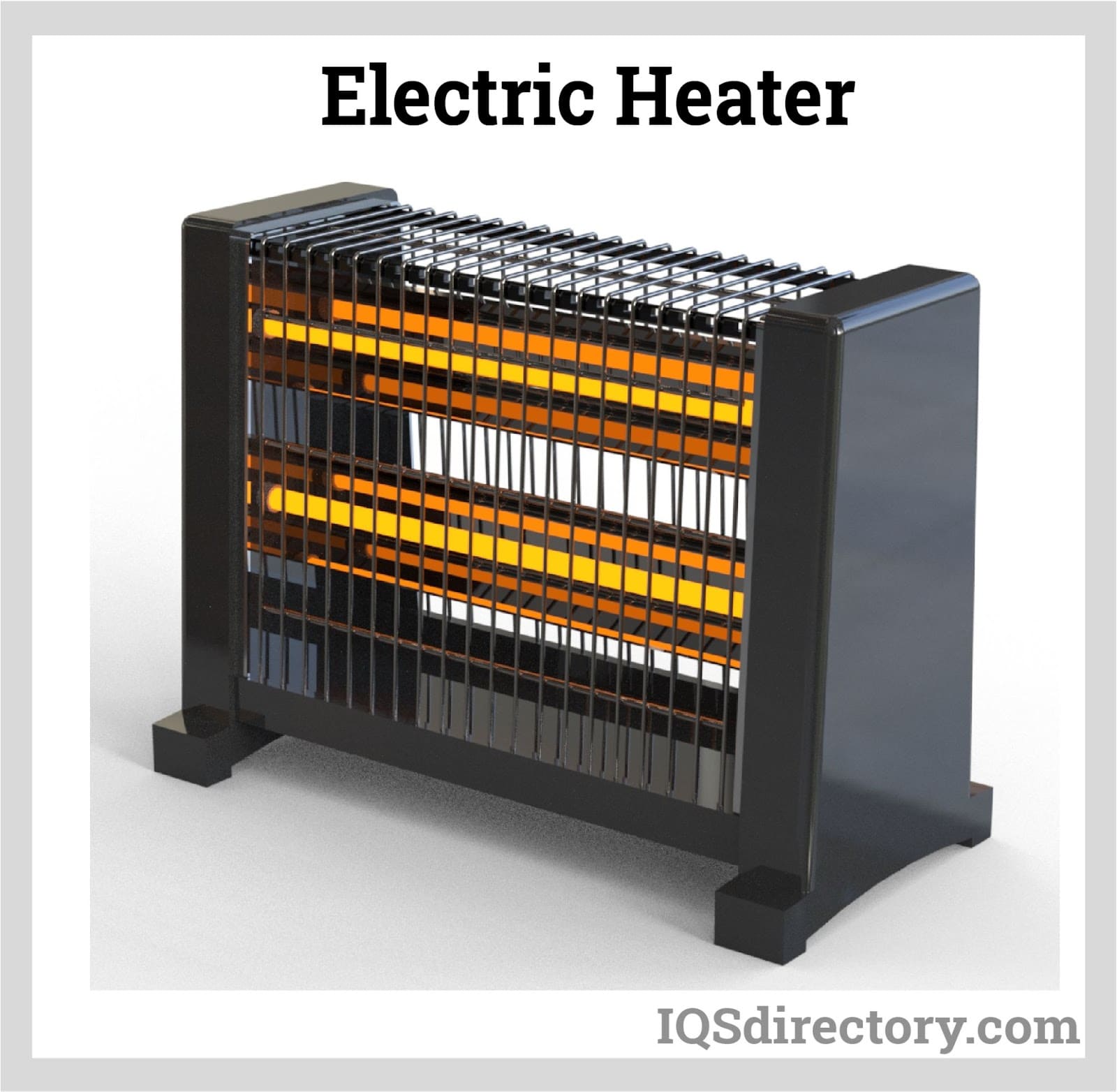
The term processing equipment is a generic term that has several meanings depending what manufacturer is using it. The equipment used to shape, change, fabricate, and transform a substance from one form to another can be defined as processing equipment. The use of processing equipment can be found in several industries especially those that include heating, drying, mixing, baking, and pulverizing.
The three most common forms of processing equipment are those that are used to dry, heat, or mix materials. Heating has multiple industrial uses from bringing a substance to its melting point to increasing the temperature to make a material, such as plastic, pliable. Different methods of drying can be found in the production of clothes to the manufacturing of corrugated boxes, while mixers are used to combine any number of materials.
When searching for processing equipment, it is important to have a clear definition of the use of the equipment and the required result. Producers, designers, engineers, and manufacturers are readily available to provide guidance and help so that the machine that is purchased fits the application.
The use of heat as an industrial component is found in every aspect of the development and production of commercial and industrial products. How heat is supplied varies and depends a great deal on the design of the production process. A very common method for supplying heat is electric heaters that are capable of being configured to meet the special needs of any application, whether a process requires air heat or duct heat.
One of the constant concerns of food producers is contamination. Industrial dryers are a way of avoiding such problems. By passing final and raw materials through air, rotary, or flash dryers, producers are assured that their products have uniform consistency as well as the removal of moisture that can carry bacterial growths. Industrial dryers have become a vital part of food production as a way to ensure quality.
An essential part of food production is industrial mixers that are used to blend a wide variety of powdered, granular, and other forms of bulk materials. The mechanism of an industrial mixer can be paddle driven or ribbon blenders. The type of mixer depends on the types of materials to be mixed and blended, which can be either dry or wet. The advantage of industrial mixers is their ability to combine any type of substance thoroughly and completely, whether it is liquid or solid.
The use of industrial ovens goes far beyond the preparation of food. Industrial ovens are the essential thermal device used for heat treating and curing a wide range of products, whether they are industrial or commercial. The purpose of heat treating is to speed up the molecular activity of a substance. The process of heat treating is designed to enhance and perfect products.
A unique form of process equipment is a pressure vessel that is designed to store liquids and gases at pressure levels beyond normal atmospheric pressure. There is a wide range of types of pressure vessels that includes compression chambers, pressure reactors, and autoclaves. Pressure vessels are designed to operate at 15 psi and are made from durable metals, high strength plastics, or fiberglass. The construction of pressure vessels is regulated by legislation and industry standards.
An interesting form of process equipment is pulverizing machines that are designed to change large clumps or blocks into fragments, pieces, and free flowing material. Pulverizers fall into a wide range of categories with their differences dictated by the type of material being transformed. The types of materials handled by a pulverizer include bricks, concrete, plastic, different types of rocks, and wood.
Another method for changing bulk materials that are in bulk or powder form is a vibratory feeder. Many bulk materials will cake or become solid during transport. To convert the substances into production quality, a vibratory feeder loosens the material and feeds it into a hopper. They are used by industries that have powdered or granular materials as a part of their process.
Process equipment is a vital part of the manufacturing. They assist with the completion of difficult operations that are required for the production of final products.
Electric heaters are utilities used for heat generation.
The use of electric heaters throughout industry, commerce and consumer products contexts is widespread and varied; the number of different heater configurations and applications grows almost daily. Some heater varieties resemble each other very closely. Band heaters and strip heaters, for example, are distinguished from each other only by the fact that band heaters are usually slightly smaller and more flexible than strip heaters.
The variety of electric heaters on the market is astounding, sometimes with cross over styles and sometimes not. Cartridge heaters sometimes qualify as immersion heaters, but not always. Sometimes, a heater‘s name is descriptive of its use, as is the case with drum heaters. In other cases, a heater‘s name is descriptive of its configuration, as is the case with tubular heaters. Some heater terms can be used interchangeably; air heaters and duct heaters are both used in HVAC filter systems to heat air, though a free-standing space heater could also be considered an air heater but not a duct heater. Both could be described as circulation heaters, though some circulation heaters are used to heat liquids in a containment system. All of these heaters can be considered process heaters, depending on their use, and they are all likely to feature wire or coil heating elements with ceramic, mineral or other insulation material. Despite the seeming interchangeability of terms and the confusion it can cause, each variety contributes to an important industrial process or commercial utility as well as some purposes in the context of consumer products. Learn more about electric heaters.
Industrial dryers are often integrated into the final processing stages of a variety of bulk materials for the final removal of contaminating moisture.
Products such as dry cereal or flour are rotated through an air dryer, rotary dryer or flash dryer to ensure the bulk solid or powdered material has the proper uniform consistency and will not grow bacteria due to moisture. Learn more about dryers.
Industrial mixers in a variety of configurations are used to blend multiple bulk or powdered materials together as part of a bulk material processing system.
Mixers used in powder & bulk applications are typically paddle mixers or ribbon blenders; sometimes powdered or dry materials are mixed with wet materials to form products such as bread dough or slurries. Learn more about industrial mixers.
Industrial ovens are thermal processing machines that provide various applications with the very important process of heat treating.
During this process, heat speeds up the molecular activity inside an object. Inside solid objects, molecules are arranged in lattices that vibrate from the heat, while in gases, these molecules collide. Learn more about industrial ovens.
Pressure vessels, often referred to as air pressure tanks are used for the storage and containment of fluids, vapors or gases at pressure levels greater than that of atmospheric pressure.
They are designed to operate at pressures more than 15 psi, and are made of a variety of metals, high-strength plastic or fiberglass. The tanks are usually cylindrical in shape with a horizontal or vertical orientation. Learn more about pressure vessels.
Size reduction equipment is a broad term that refers to machines or devices that are used to reduce the size of materials.
The use of size reduction equipment has a long history, dating back to ancient times when people used simple tools like stones to break down large materials into smaller pieces.
Today, size reduction equipment has become more advanced and is widely used in various industries such as mining, food processing, and chemical production. Learn more about size reduction equipment.
Vibratory feeders are conveying ramps or feeding tubes which assist in transferring bulk and powder solids to and from conveyors, processes and hoppers.
By vibrating the discharge end of a hopper or conveyor, powdered material caked on the sides and within is loosened until it falls freely.
Bulk handling sometimes uses vibratory feeding ramps to convey over short distances, and most bulk bag filling, bag dumping and hoppers are equipped with vibrating feeders. Learn more about vibrating feeders.