Roll Forming
Roll forming is a highly efficient metal forming process in which metal is shaped through a sequence of rollers. This technique produces some of the most widely utilized metal products available today.
A key characteristic of roll forming is that it does not rely on heat, and the rollers used in the process do not alter the surface properties of the metals. These attributes make it particularly suitable for shaping polished metals, coated metals, and other materials where aesthetic and surface qualities must remain intact.
The process is commonly employed to bend sheet metal into rounded shapes or frames, referred to as roll formed parts. These parts are valued for their precision, offering tight tolerances and the ability to conform to a wide range of shapes, angles, and curves.
Roll forming services serve a broad spectrum of industries, including automotive manufacturing, building construction, architecture, carpentry, fencing, appliances, utilities, and more.
Benefits of Roll Forming
Roll forming is an exceptional method for shaping coated, finished, cured, or otherwise treated metals. Because the process does not involve heat and rollers can be coated with non-reactive powders or oils, it preserves the surface properties of metals. This makes roll forming ideal for polished and coated metals or any material requiring the preservation of aesthetic properties.
Robust and Efficient
Roll forming is a fast and efficient process that produces high-quality parts and products. Depending on the setup, roll formers can shape between 30 and 600 feet of metal per minute. Additionally, most roll formers utilize nearly 94% of the stock metal during operations, minimizing waste and maximizing material efficiency. While processes involving punching or surface reduction generate more waste, they still benefit from the inherent efficiency of roll forming.
Rapid Turnaround Times
Roll forming enables the creation of complex designs in a matter of hours. With a roll former capable of cutting 30 to 600 feet of metal per minute, manufacturers can achieve high productivity. Moreover, pre-sourced coils in desired cuts streamline production, allowing manufacturers to focus on design conceptualization and implementation.
Increased Consistency
Roll forming ensures exceptional uniformity and accuracy, making it particularly advantageous for large orders. Every piece produced is consistent, delivering high-quality results across the entire production lot.
Low Production Cost
By sourcing pre-cut metal strips from external manufacturers, roll forming facilities save on time and labor. This process reduces production costs while maintaining efficiency. Furthermore, the use of identical strips minimizes material waste and ensures consistent part production.
Energy Savings
Since roll forming does not require heat, it significantly reduces energy or fuel costs. Unlike other metal-forming methods that rely on heat to bend materials, roll forming achieves precision without the need for high-energy inputs.
Higher Production Volume in Less Time
The continuous nature of roll forming allows manufacturers to achieve high production volumes in minimal time. As long as the roll former is supplied with metal strips, it can continuously produce shaped products with exceptional accuracy and efficienc
Flexibility
Roll forming is a versatile method suitable for both ferrous and non-ferrous metals. It can produce complex designs and profiles that are difficult to achieve using other methods like cross-section cutting or stamping. The process is ideal for creating diverse shapes such as C channels, J channels, U channels, metal rings, and various trims. Additionally, pre-finished materials with layers of paint, coating, or plating can be processed without compromising quality.
Fewer Secondary Operations
Roll forming can integrate additional operations such as cutting, notching, perforating, or punching during the initial production stage. This reduces the need for secondary processing, enhances structural integrity, and results in superior product assembly.
Roll Formed Products
Roll forming is used to produce a wide variety of parts and products, including:
- Angle Irons, Aluminum Angles, and Steel Angles: Common in carpentry and construction.
- Metal Trim and Channels: Used in industrial, commercial, and consumer applications.
- Metal Rings: Applied in buttons, hose connectors, street signs, and door lock hardware.
- Metal Tubes and Wall Panels: Enhance office aesthetics or protect factory walls from debris and sparks.
Specific roll-formed items include C channel frames, car frames, fence posts, angled posts, stabilizers, and railings.
History of Roll Forming
The origins of rolling technology trace back to 600 B.C. in the Middle East and South Asia. Early techniques were rudimentary but demonstrated the same principles later refined by Leonardo da Vinci.
Europe’s first rolling machinery, the slitting mill, emerged in 1590. It shaped flat iron bars into plates and created slits for barrel hoops. Modern roll forming began in the late 1700s when Henry Cort patented grooved rolls for forming iron bars. Over time, the process evolved to accommodate various metals, from lead to today’s extensive material range.
In the 20th century, CNC technology revolutionized roll forming by automating precision design and production, enabling high-volume manufacturing of intricate parts.
Roll Forming Materials
Roll forming accommodates a wide range of ferrous and non-ferrous metals, including:
- Aluminum: Lightweight, corrosion-resistant, non-magnetic, and highly conductive.
- Tin: Soft, malleable, and corrosion-resistant, often alloyed for enhanced properties.
- Steel: Available in galvanized, stainless, and carbon forms, known for its strength and durability.
- Brass: A versatile copper-zinc alloy with varying levels of hardness, malleability, and corrosion resistance.
- Titanium: Renowned for its strength-to-weight ratio, corrosion resistance, and high melting point.
- Zinc: A bluish-white, brittle metal used in alloys like galvanized steel and brass.
- Zirconium: Lustrous, malleable, and highly resistant to corrosion.
These materials demonstrate roll forming’s adaptability and effectiveness in shaping diverse metals for various applications.
Roll Forming Images, Diagrams and Visual Concepts
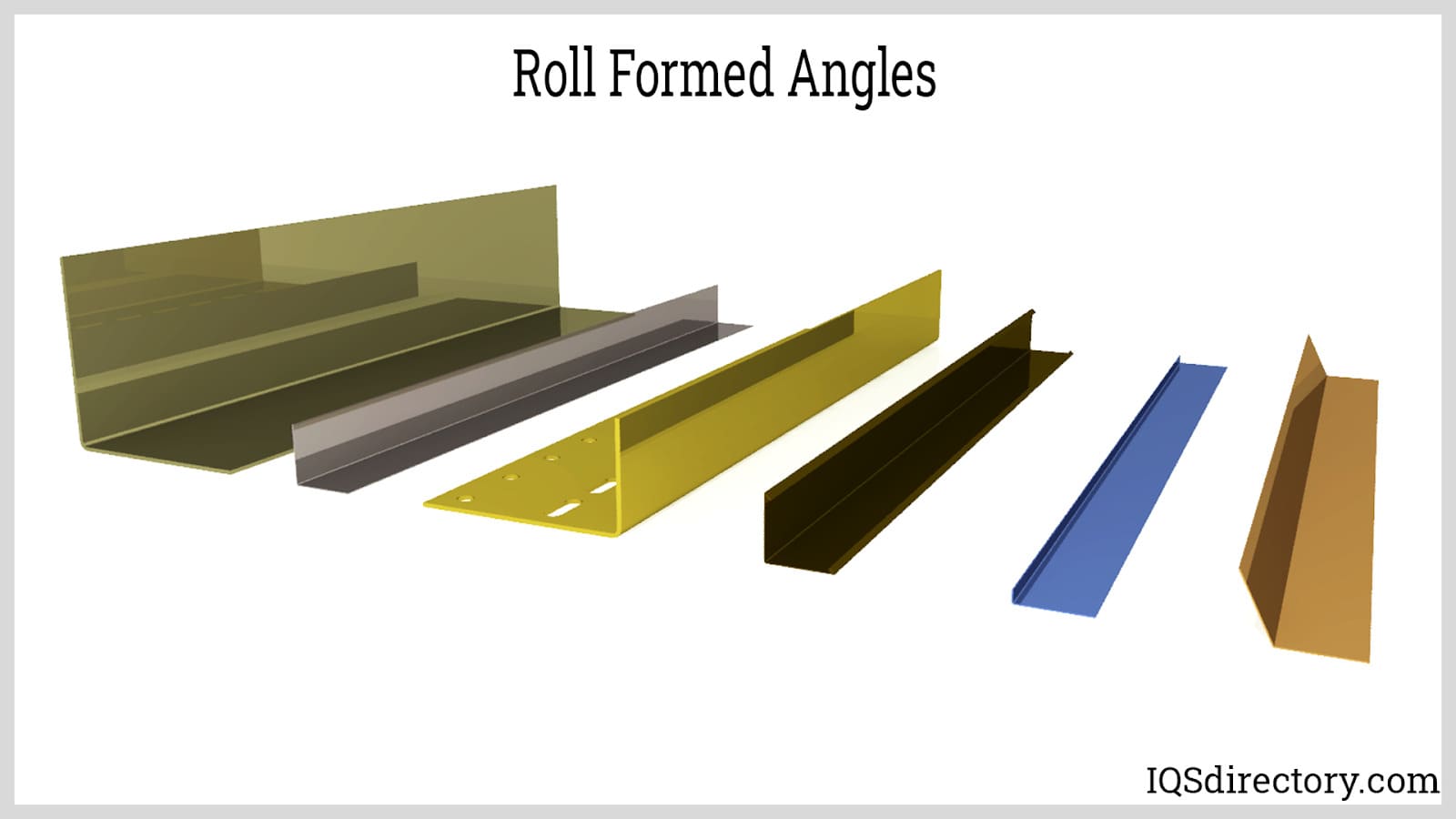
Roll forming process allows for the creation of different patterns or angles using an assortment of metals.
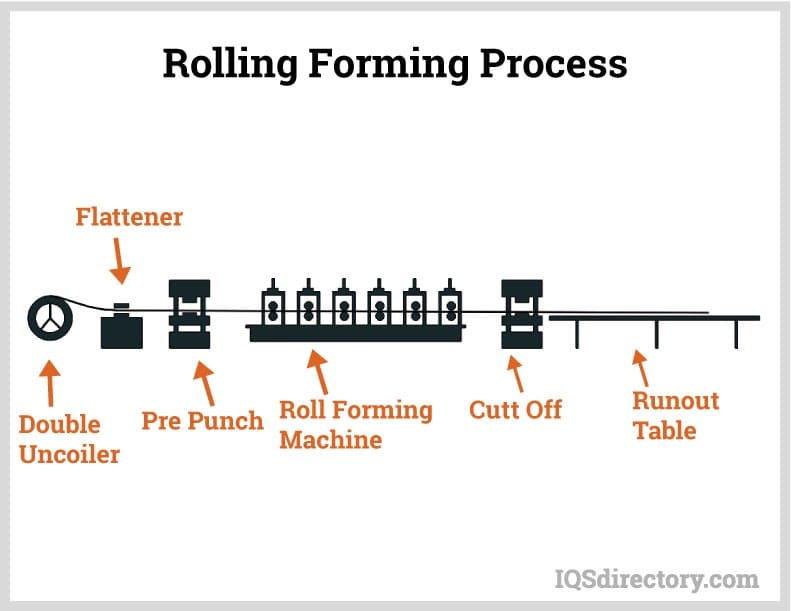
The steps of the roll forming process.
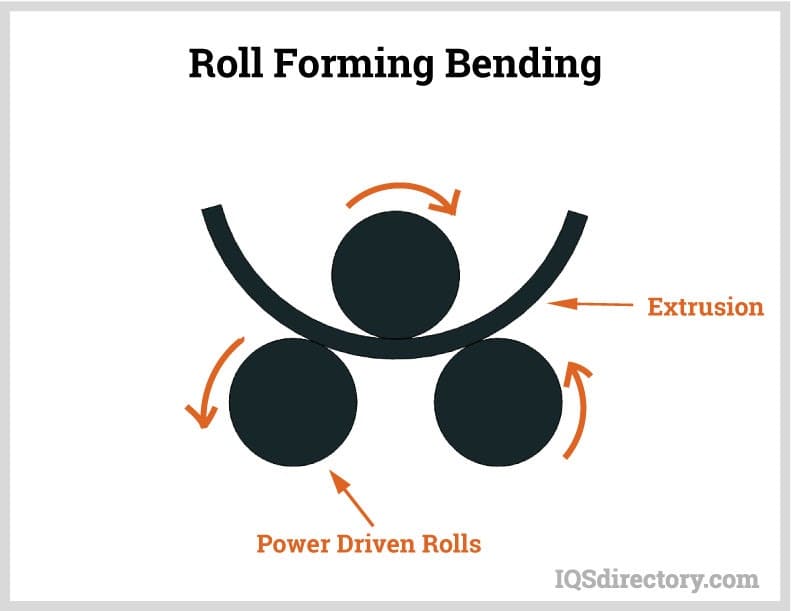
Roll bending uses three rollers bend a plate to produce a desired curve.
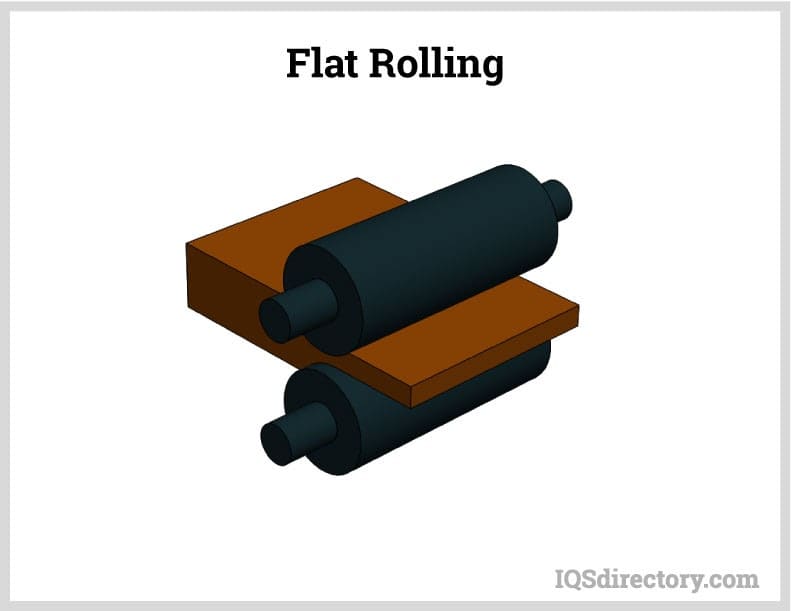
Two working rollers rotating in opposite directions which elongates the material due and creates the desired thickness of the material.
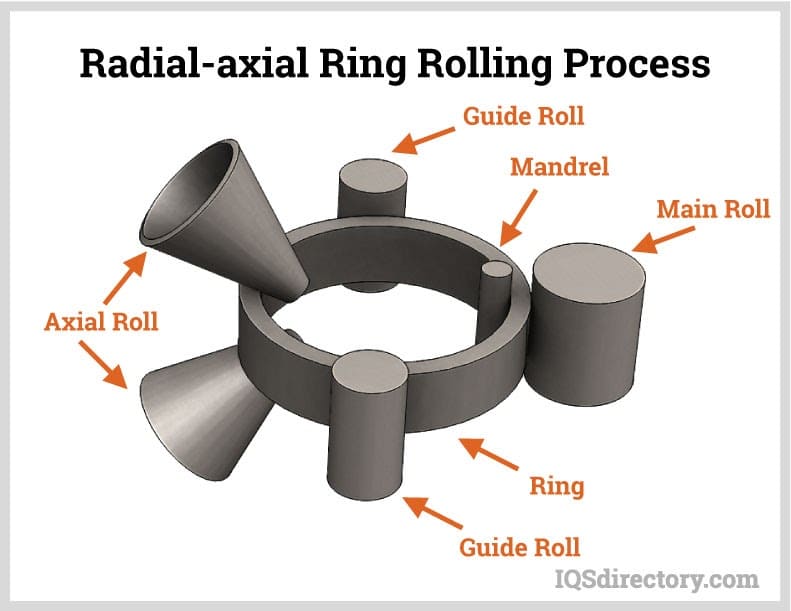
A ring of small diameter is rolled between two rollers to increase the diameter of the ring.
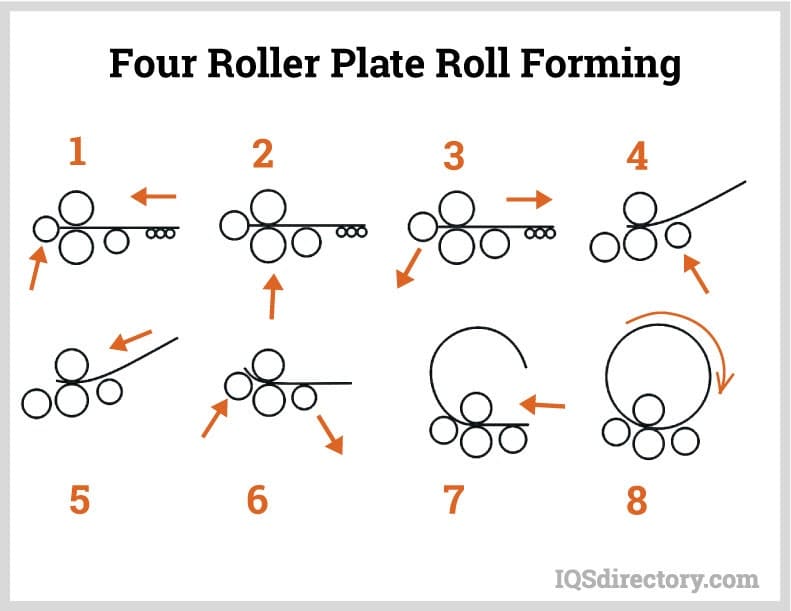
The four roller systems used in forming a cylinder.
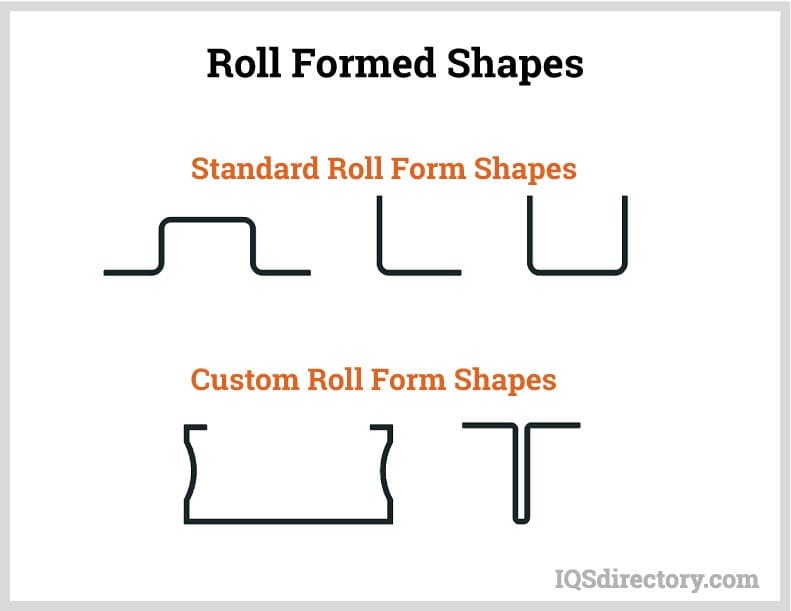
Shape rolling cuts different shapes which does not involve changing the metals thickness to produce irregular shaped channels and trim.
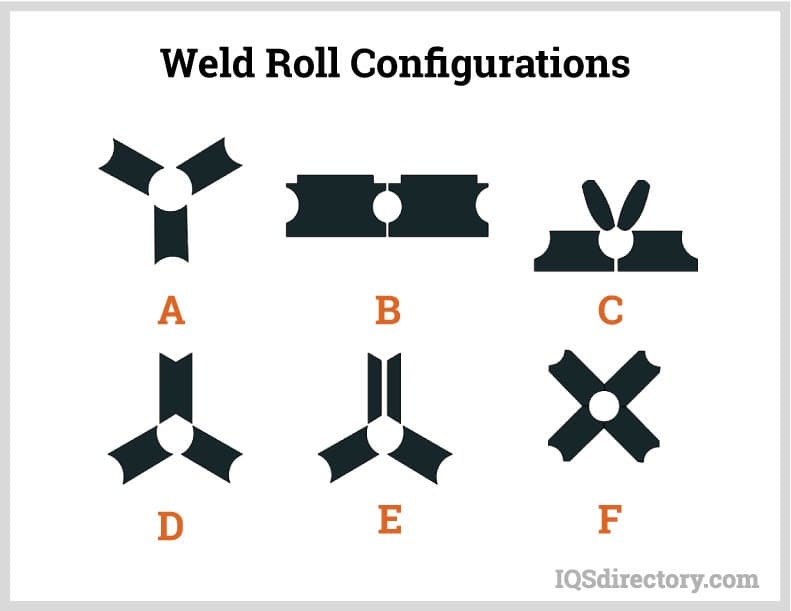
When roll forming tubes the process must include one of these configurations.
Roll Forming Process
Select Metal Type
Roll formed parts are created from metal strips, often coiled for easy feeding into roll forming machinery. This process accommodates various materials, allowing manufacturers to tailor solutions to specific applications.
Feed Metal to Rollers
The roll forming process begins by feeding a stock of metal into the first set of horizontal, rotating rollers, known as roller dies. These dies are carefully designed to produce uniform and consistent cross-sectional profiles. Typically, this process occurs at room temperature, termed cold roll forming.
Shaping the Metal
The initial roller die sets tightly conform to the metal's contours, gradually shaping it as it passes through each subsequent set of rollers. Each die in the sequence is positioned to achieve a specific transformation of the metal strip, creating the desired shape step by step. For example, to produce circular clamps, a metal strip is fed into rollers that progressively shape its cross-section from a straight line to a backward "C."
Cutting to Length
After achieving the desired form, the metal strip is cut to the required length. In post-cut roll forming, cutting occurs after shaping, while in pre-cut roll forming, materials are cut before entering the machine.
Roll Forming Design
Custom roll forming offers extensive flexibility. Machines can be configured to produce diverse metal shapes with nearly any bend radius, size, or sheet thickness. Pre-finished components delivered in pre-cut condition streamline assembly and manufacturing processes.
Roll Forming Machinery
Basic roll forming machines include:
- Entry Section: Where metal is inserted.
- Roller Station: Where roller dies shape the metal.
- Cut-Off Press: Cuts the formed metal to length.
- Exit Section: Where completed parts are discharged.
Some machines integrate additional features like laser or TIG welding, bend rolling, and punching, reducing secondary operations. Manufacturers can also customize systems with open-loop or closed-loop configurations for precise control.
Considerations for Roll Forming
- Labor Intensity: Roller configuration requires skilled professionals for precision. Advances in computer control mitigate this but can be costly.
- Limitations: Sealed ring products cannot be directly roll-formed without welding or fastening.
To maximize the benefits of roll forming:
- Choose Certified Manufacturers: Look for ISO 9001:2008 certification for quality assurance and competitive pricing.
- Evaluate Competence: Review company websites, testimonials, and reviews to assess expertise and service quality.
- Discuss Requirements: Share specific needs and request quotes from multiple manufacturers.
- Seek Customization: Ensure the manufacturer offers tailored solutions, including prototypes and fast turnaround times.
Roll Formed Products, Tools, and Services
Aluminum Angles
Bent or connected pieces of aluminum that form an angle.
Aluminum Channels
Open or closed rectangular tubes made from aluminum.
Bent or joined pieces of heavy-duty metal, often used to support structures.
Angles
Roll-formed from various metals, commonly stainless steel, to provide support in two directions. These often feature holes or slots for connecting parts, enhancing strength and stability.
Channels
Serve as support systems for numerous roll-formed products, such as frames and rails.
Custom Roll Forming
A service offering the fabrication of custom roll-formed products.
Roll-formed products designed to provide support systems for frames and rails.
Circular roll-formed parts used for joining and sealing applications.
Fits along the edge of a product or component.
Sheets of roll-formed metal designed to cover walls.
Outboard Mills
Roll-forming machines with housings that support both ends of the roll tooling shafts.
Post-Cut Roll Forming
A process using continuous metal rolls, cutting pieces to size only after roll forming. This method is the most common, efficient, consistent, and least troublesome.
Pre-Cut Roll Forming
A process where material is cut to length before entering the roll-forming machine. Primarily used for low-volume applications.
Roll Formed Products
Metal pieces shaped by passing through a series of rollers.
Machines designed to roll form metals into desired shapes.
Roll-formed products created by bending steel sheet metal.
Steel roll-formed products that serve as support system frames and rails.
Rings
Commonly roll-formed from other shapes to function as container seals and lids, often made from stainless steel.
Roll Forming Terms
Accumulator
Equipment that stores metal coil, allowing uninterrupted roll forming while new material is joined to the coil.
Auxiliary Operations
Secondary processes conducted alongside roll forming.
Camber
A deviation from a straight line in a roll-formed part.
Coiling
The process of transforming heated flat sheet metal into spiral coils.
Cold Work
Deforming metal at room temperature to increase strength and hardness.
Drive System
The mechanism providing power to roll-forming machines, moving metal coils through them.
Ductility
The ability of metal to bend or form without fracturing.
Elastic Limit
The maximum stress a metal can endure without permanent deformation.
End Flare
Deformation occurring at the end of a roll-formed part.
End Joiner
Equipment used to connect two coils, ensuring the continuous feed of metal coils into the roll-forming machine.
Ferrous Metal
Metal with iron as a significant component.
Similar to a C channel, but with edges forming the “brim” of a hat.
Levelers
Mechanisms ensuring flatness of metal fed into the roll-forming machine.
Non-ferrous Metal
Metal lacking significant iron content.
Plastic Deformation
Permanent changes in the shape of metal after surpassing its elastic limit, achieved through applied stress.
Pickling
A cleaning process for steel coils using hydrochloric acid to remove impurities like rust, preparing the material for roll forming.
Reel Kinks
Imperfections in metal coils.
Roll Changing
Replacing rolls on roll-forming equipment, a lengthy and costly procedure.
Slit Edges
The edges of sheet or strip metal resulting from rotary slitting to width.
Springback
Deformation in a roll-formed part caused by insufficient stretching beyond the elastic limit.
Sweep
A horizontal deviation from a straight line in a formed part, caused by misaligned horizontal rolls or uneven forming pressure.
Tolerance
The acceptable variation from specified product dimensions, such as cross-sectional measurements.
Trimming
Removing excess metal from a formed part to ensure consistency.
Twist
A corkscrew-like deformation in a roll-formed part, caused by extreme pressure during the forming process.
Yield Strength
The maximum stress a material can withstand without permanent deformation.
More Roll Forming Information