Vacuum Pumps
Vacuum pumps are mechanical devices that create partial or complete vacuums by removing gas from a sealed and enclosed area. They are designed to extract air or gases, reducing the pressure inside a container. Unlike air compressors, which increase gas pressure by reducing volume and are often used together with vacuum pumps, vacuum pumps focus solely on gas removal to generate vacuums.
Quick Links to Vacuum Pumps Information
The History of Vacuum Pumps
The earliest artificial vacuums were created for scientific demonstrations and experimentation. Typically, these systems used glass enclosures, often similar in size to large jars. The glass container would be placed upside down on a surface, its edges sealed with a liquid. Air was extracted using an air pump connected through an outlet at the base.
The first practical vacuum pumps were invented by Otto Von Guericke, a Prussian physicist and engineer, in 1650. He developed the first air pump capable of producing a partial vacuum and achieving much lower pressure than earlier devices. In 1654, Guericke famously demonstrated his pump's effectiveness with the Magdeburg hemispheres experiment, where two teams of horses failed to pull apart hemispheres sealed by a vacuum. Following Guericke's invention, Robert Boyle and Robert Hooke further improved vacuum pump technology.
Vacuum pump innovation resumed in 1855 with Heinrich Geissler's invention of the mercury displacement pump, which paved the way for vacuum tubes. In the 19th century, Nikola Tesla created an apparatus using a Sprengel pump, achieving very high levels of vacuum.
The earliest vacuum pumps from this period were simple, low-capacity fans. Each time a fan blade passed the outlet of the vacuum enclosure, it pushed air through an exhaust port, generating a vacuum. The natural drive for pressure equilibrium caused air from inside the enclosure to be expelled, repeating the process until most air was removed.
Modern vacuum pump systems still operate on similar principles, though advances in efficiency and performance have greatly expanded their capabilities. Today, a wide range of vacuum pumps serves the diverse needs of industries and scientific applications requiring controlled vacuum environments.
Advantages of Vacuum Pumps
Vacuum pumps improve operational efficiency and provide precise atmospheric pressure control in various systems. They are unmatched in their ability to evacuate gas compared to other methods, such as suction. Additionally, vacuum pumps are valued for their robust durability and long-lasting performance.
Design of Vacuum Pumps
A typical vacuum pump setup includes one or more pump units, an inlet port, and an exhaust (outlet) port. Advanced systems may incorporate metal chambers with secure metal gasket seals. Components are usually constructed from corrosion-resistant materials such as stainless steel or titanium to ensure longevity and reliability.
During vacuum pump system design, manufacturers evaluate important criteria such as maximum and minimum flow rates, required vacuum levels, pump speed, the size of the chamber, and the type of gases or liquids being processed.
If desired, manufacturers of vacuum systems can engineer custom configurations and operating methods. For example, a basic system can generate a low vacuum, while high vacuum applications may require a combination of multiple pumps, typically a rapid pump and a positive displacement pump, along with a vacuum chamber.
All vacuum pumps operate by expelling air from a closed container and preventing its return. For optimal functionality, many vacuum pumps utilize vacuum pump oil to lubricate moving parts and promote smooth system operation.
Vacuum Pump Images, Diagrams and Visual Concepts
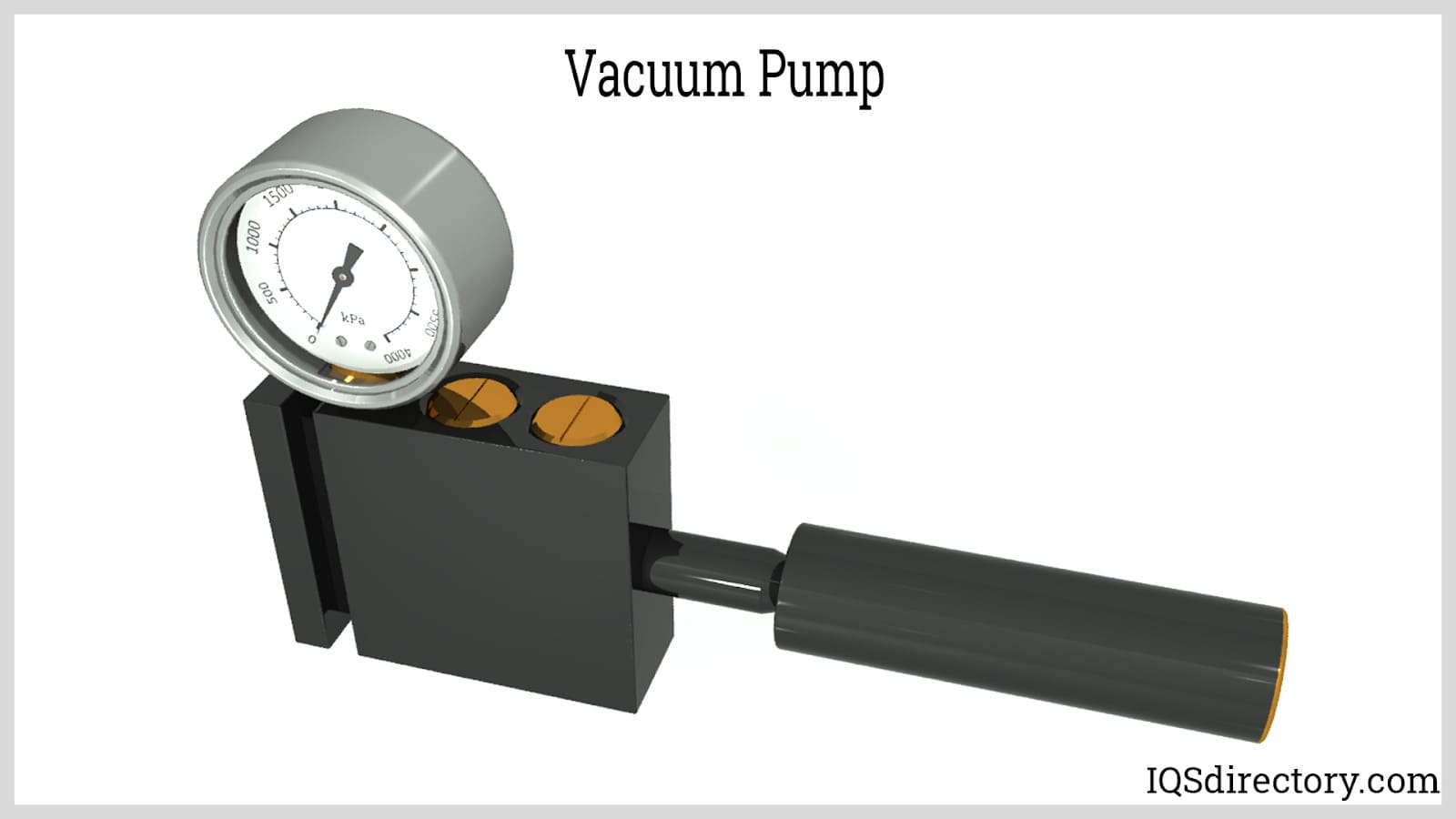
Vacuum pumps generate a low-pressure or partial vacuum by removing air molecules from inside a sealed chamber.
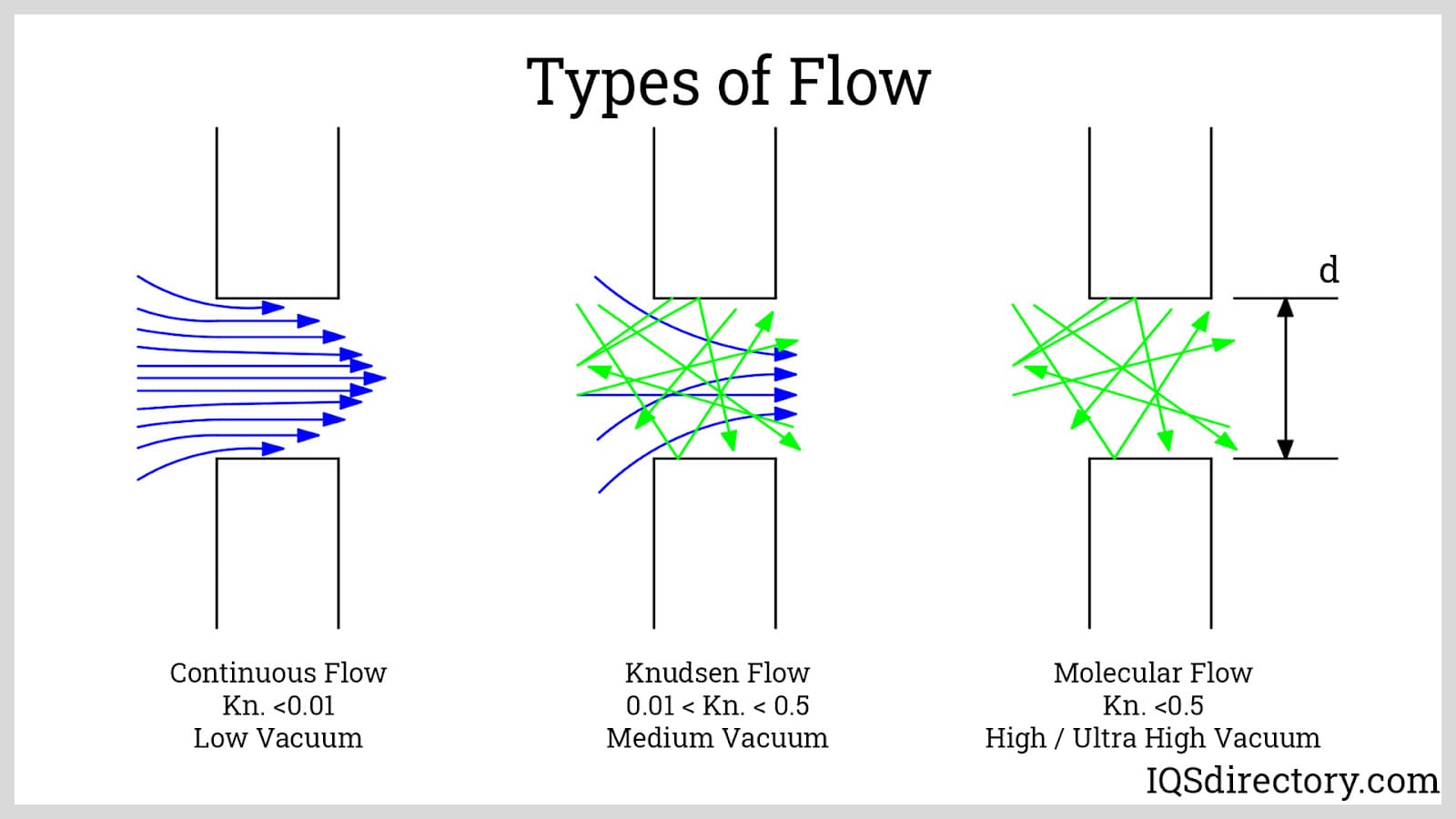
Viscous flow fluids can be mechanically transported by positive displacement vacuum pumps.
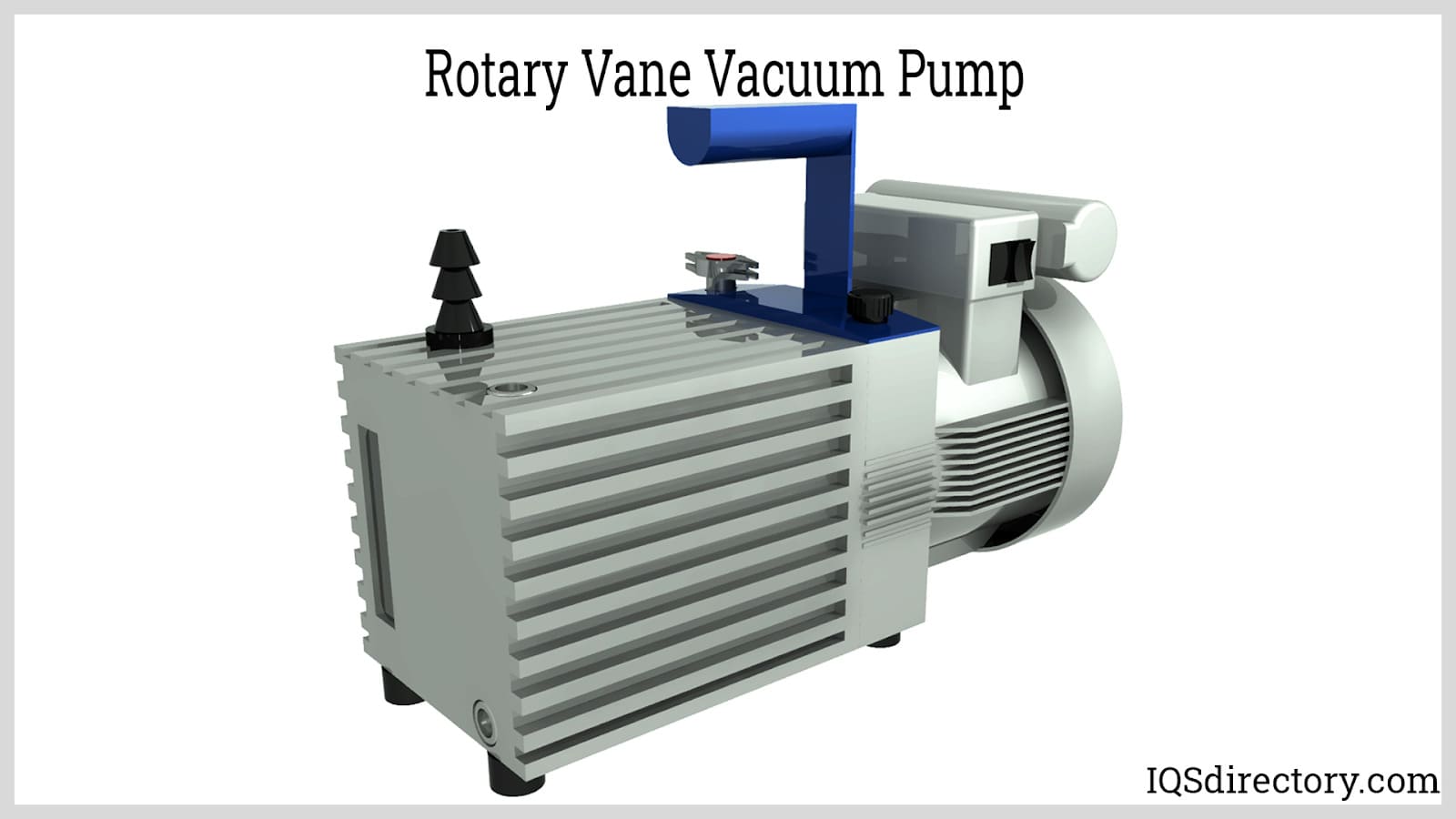
Rotary vane vacuum pumps create low-pressure areas by moving rotating components against the pump housing.
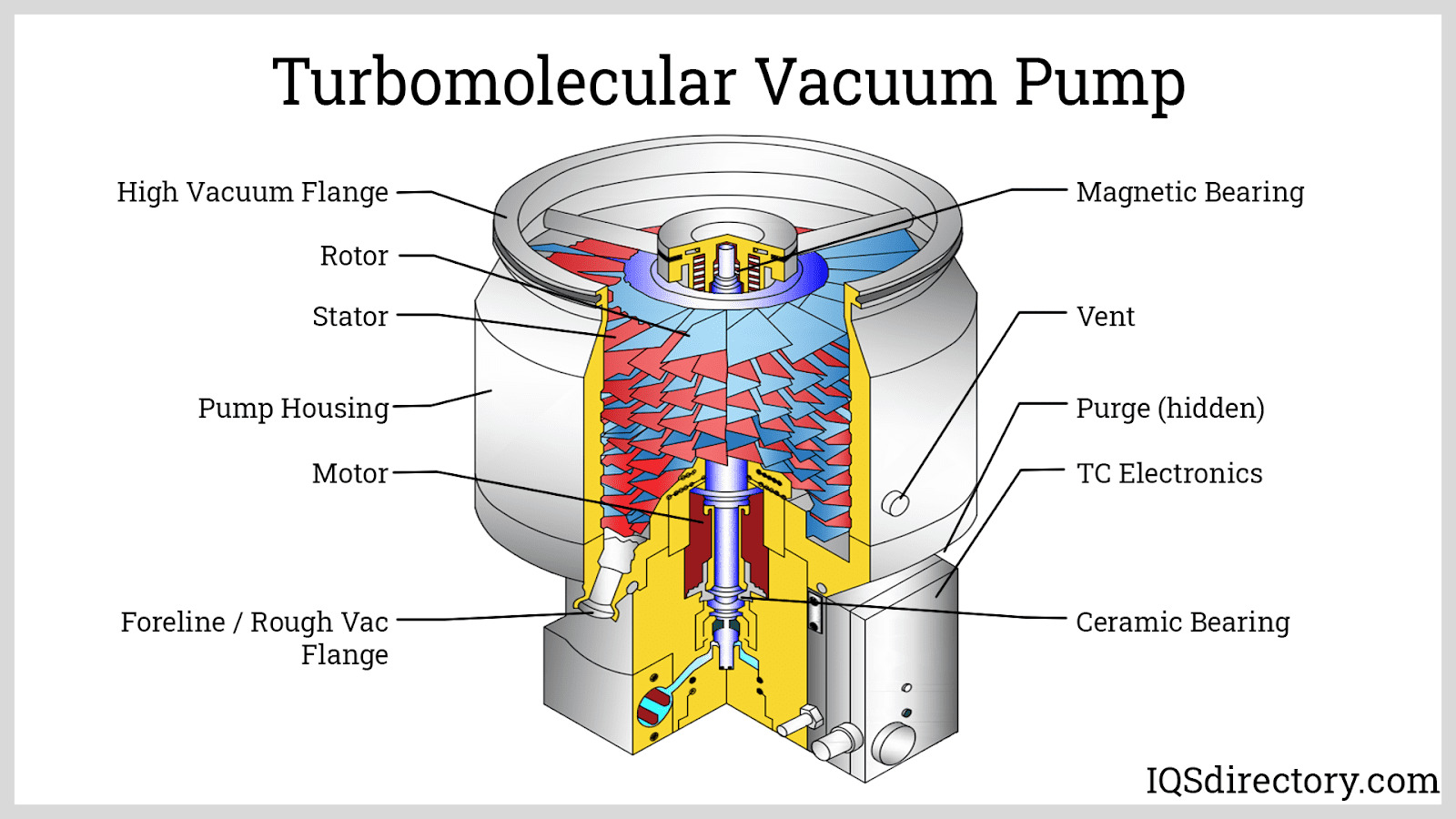
Turbomolecular vacuum pumps use several stages of rotating and stationary turbine blades. The angled rotating blades transfer momentum to gas molecules, moving them axially to the exhaust.
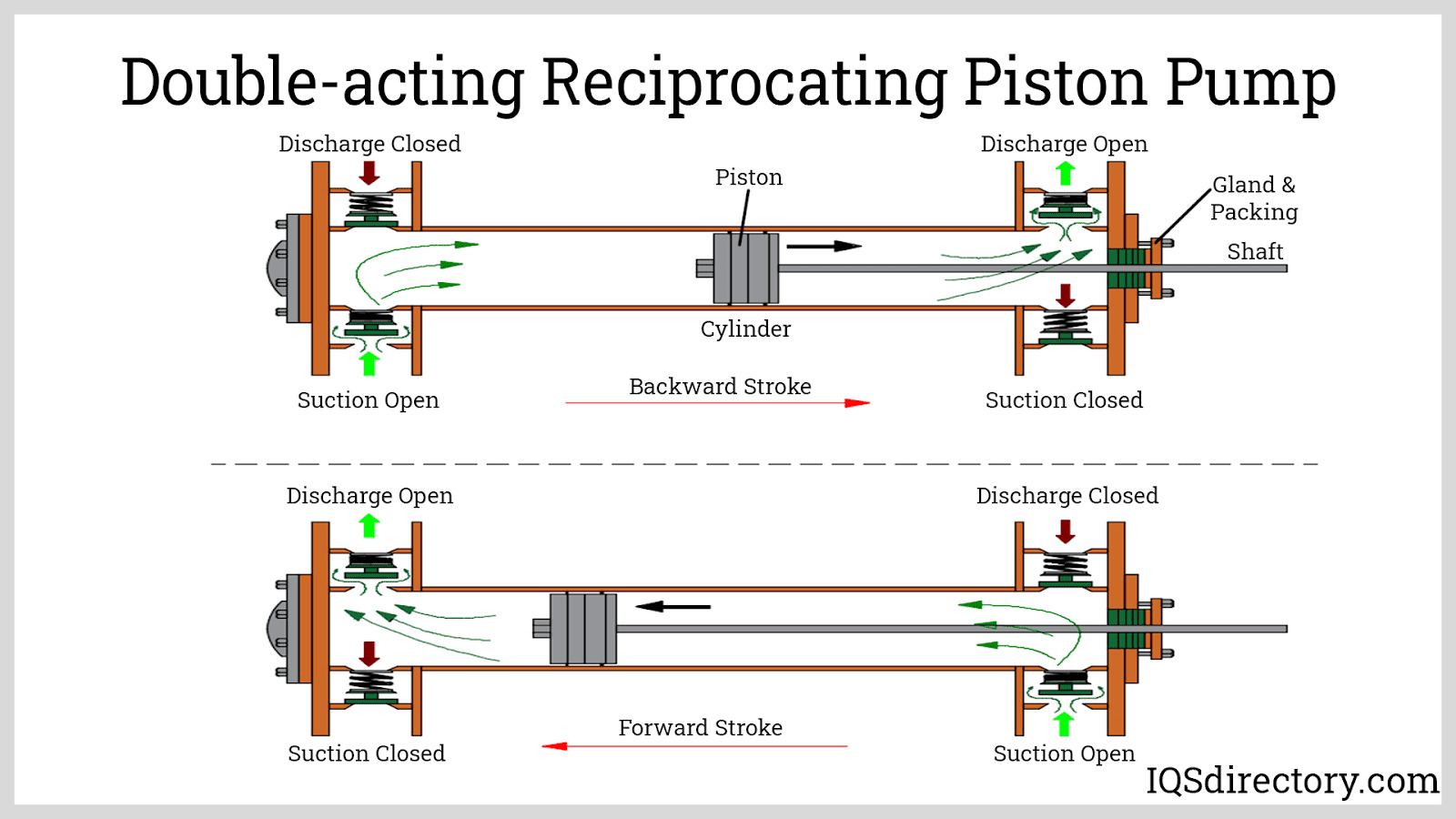
A double-acting pump produces both vacuum and compression in a single stroke.
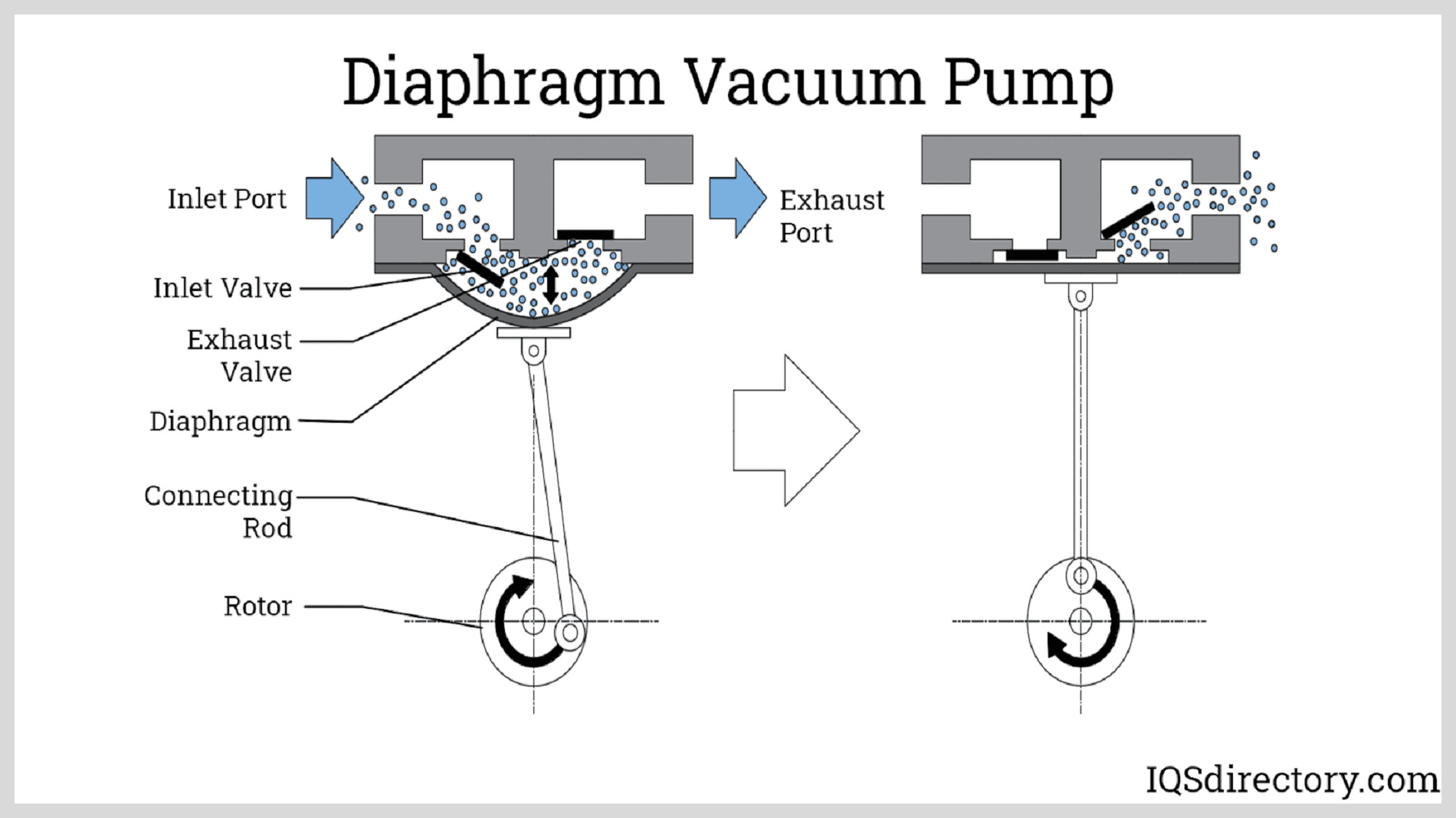
Diaphragm vacuum pumps feature a flexible metal or elastomer membrane that forms a sealed chamber for gas evacuation.
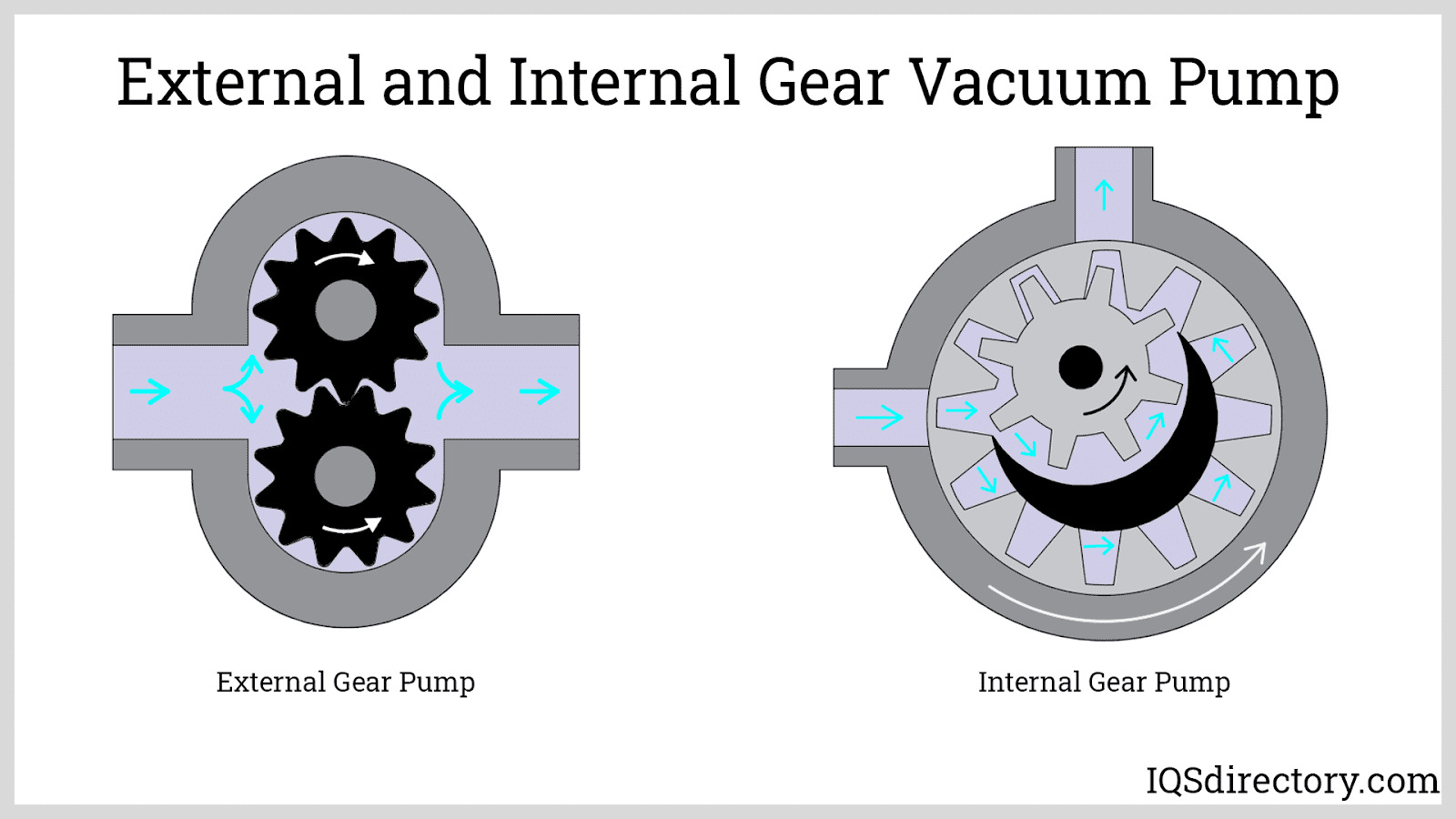
Gear vacuum pumps have two intermeshing rotors—either external or internal gears—with one gear driving the other to move gases.
Types of Vacuum Pumps
Positive Displacement Pump
These pumps create a vacuum by repeatedly expanding and exhausting a sealed cavity. Examples of positive displacement pump types include rotary vane vacuum pumps, scroll pumps, piston pumps, diaphragm pumps, and liquid ring vacuum pumps. Positive displacement pumps are typically straightforward in design and are ideal for generating low-level vacuums.
In positive displacement pumps, a vacuum is formed by increasing the volume within a sealed chamber, reducing its pressure below atmospheric levels. As pressure drops, the target gas or liquid is drawn in, the chamber is sealed, and the contents are expelled through an outlet. This process only achieves a partial vacuum. Manual water pumps are a common example of this type.
Rotary-Vane Pump
Rotary-vane pumps are air-cooled, oil-sealed, and direct-driven, suited for clean, dry, and non-reactive gases. They are known for their low carbon emissions and reliable operation when properly maintained.
The rotary vane pump shares similarities with the screw air compressor, also called a rotary-screw compressor, which compresses gas using positive displacement.
Screw Air Compressor
Rotary-screw compressors are positive displacement gas compressors that use meshing helical screws to compress gas efficiently.
Piston Vacuum Pump
This regenerative pump uses rotating pistons of varying strokes to move fluids through check valves during each cycle.
Diaphragm Pump
Diaphragm pumps include one or two flexible diaphragms that pulse to move fluid, while check valves maintain controlled flow direction.
Liquid Ring Vacuum Pump
Liquid ring pumps are designed for evacuating both dry and wet gases and can also handle condensable vapors and small liquid droplets. The condensing effect in the liquid ring improves upstream capacity by allowing gas to contact the liquid ring surface.
Momentum Transfer Pump
These pumps remove air molecules from a vacuum chamber by accelerating them using high-speed gas jets or rotating fans. Examples include diffusion pumps and turbomolecular pumps, which can achieve very low-pressure vacuums.
Momentum transfer pumps blow chamber molecules out using high-speed blades or jets. Designed for larger areas and higher pumping speeds, these pumps sweep volumes more frequently than mechanical pumps.
Diffusion Pump
Diffusion pumps utilize vapor jets of oil or mercury to eject gas molecules. Heated oil or another vapor is forced through jets, colliding with gas molecules and transporting them from the chamber.
Turbomolecular Pump
These pumps use high-speed fans to impart momentum to gas molecules, moving them from the inlet toward the outlet efficiently.
Turbo molecular pumps are axial-flow turbines intended for molecular flow conditions. With alternating rotor and stator disks, their inclined blades increase the velocity and direction of gas molecules from inlet to outlet.
Both diffusion and turbomolecular pumps need to work with mechanical pumps, since their exhaust cannot be vented directly to atmospheric pressure. They require a partial vacuum at the exhaust to function properly.
Entrapment Pump
Entrapment pumps capture gases either by heating or cooling, making them easier to trap. The two main types are cryogenic and ion pumps, each utilizing a distinct method to generate vacuum.
Cryogenic Pump
Cryopumps use extremely low temperatures to trap gases as solids on cold surfaces, called arrays. These gas-binding pumps operate by condensation or sorption of gases onto surfaces kept cold by refrigeration, reducing vapor pressures to negligible levels.
Operating below 120° Kelvin, cryogenic pumps create vapor pressures that are much lower than the vacuum pressure.
Ion Pump
Ion pumps achieve ultra-high vacuum by reacting with gases and embedding them into the pump walls. Both cryogenic and ion pumps require periodic regeneration, using various pumps and valves for optimal performance. Ion pumps are often paired with getter pumps for ultra-high vacuum applications.
Vacuum pumps can also be classified by whether they use liquids in the process, as wet or dry systems.
Wet Vacuum Pump
Wet vacuum pumps use a liquid at some stage in the pumping process, often oil as a lubricant or sealing medium. Liquid seal vacuums use fluids within the enclosure to form air-tight seals for compression.
Oil-Sealed Vacuum
Oil-sealed vacuum pumps are used for high-intensity vacuum needs, as oil forms an effective seal between moving parts. An oil separator is required downstream to prevent contamination of the vacuum enclosure or exhaust.
Dry Vacuum Pump
Dry vacuum pumps, unlike wet pumps, do not use any liquids during operation. They operate without fluids such as water or oil, minimizing environmental concerns and reducing disposal costs. Dry pumps can be configured for hot or cool operation as needed, and they help reduce emissions and improve solvent recovery.
Wet vacuum pumps typically reach lower vacuum levels but require more frequent maintenance and can disrupt operations if they fail. For critical applications—such as aircraft instrumentation—dry vacuum pumps are generally chosen for their reliability and minimal maintenance needs.
Laboratory Vacuum Pump
Laboratory vacuum pumps provide controlled vacuum environments for applications such as electron microscopy and laboratory experiments.
Medical Vacuum Pump
Medical vacuum pumps are used for suction during surgeries and radiotherapy. They remove air from sealed devices and are adapted specifically for medical procedures.
Some vacuum pumps don’t fit neatly into categories and are listed individually, such as high vacuum pumps and electric vacuum pumps.
High Vacuum Pump
High vacuum pumps extract air particles from a closed gas volume, achieving pressures between 10-2 and 10-8 Torr. These pumps convert mechanical rotation into pneumatic suction and flow, generating hydraulic or pneumatic effects as they remove gases.
Electric Vacuum Pump
Electric vacuum pumps use an electrical connector for grounding and power supply, providing efficient and strong vacuum performance. They are increasingly used in automotive manufacturing to help meet emission standards.
Air Pumps
Air pumps move gases against pressure gradients, converting mechanical energy into pneumatic power for various applications.
Ejector Pumps
Ejector or vapor pumps use vapor streams operating primarily under viscous flow conditions to generate vacuum.
Heavy Duty Vacuum Pumps
Heavy duty vacuum pumps are designed for tough conditions, handling highly saturated vapors or solid particles entering the inlet stream.
Industrial Vacuum Pumps
Industrial vacuum pumps are robust units used in manufacturing and processing industries to generate vacuum for a range of applications.
Laboratory Vacuum Pumps
Laboratory vacuum pumps are specialized devices that remove gases from sealed volumes to create vacuums for scientific and medical uses. They are designed for compact spaces, sensitive equipment, and clean environments.
Mechanical Pumps
Mechanical vacuum pumps use moving components such as pistons, vanes, or rotary elements to transport gas or vapor.
Non Positive Displacement Pumps
These pumps utilize kinetic energy to create pressure gradients in moving air streams.
Oilless Vacuum Pumps
Oilless vacuum pumps generate vacuum by removing gases from a closed space without the use of oil lubrication, minimizing maintenance and contamination.
Rotary Piston Vacuum Pumps
Rotary piston vacuum pumps are industrial-grade, heavy-duty solutions for environments with high levels of contaminants.
Side Channel Pumps
Side channel pumps feature multiple circular hollow rings in the housing and impeller, creating low-pulse suction ideal for industrial applications that need precise air handling.
Small Vacuum Pumps
Small vacuum pumps are compact devices that generate a vacuum in sealed chambers. Despite their size differences, they function similarly to larger industrial vacuum pumps.
Vac Pumps
Vac pumps, another term for vacuum pumps, are used to remove gases from a sealed environment and create a vacuum.
Vacuum Pump Systems
Vacuum pump systems are assemblies of one or more pumps with accessories designed to efficiently remove gas molecules from a chamber, resulting in pneumatic or hydraulic suction and vacuum.
Vacuum Pump Applications
Businesses across many industries depend on vacuum pump systems for the reliable operation of a variety of processes.
Industries utilizing vacuum pumps include: industrial manufacturing, scientific and laboratory research, healthcare, vacuum coating, and food processing.
Common applications in these fields are:
- Ion implantation, semiconductor manufacturing, dry etching, photolithography, and atomic layer deposition.
- Electron microscopy (including uranium enhancement) and analysis of solid, liquid, gas, and biological specimens.
- Radiotherapy, radiopharmacy, and radiosurgery.
- Vacuum coating for metals, glass, and plastics for durability and appearance (such as Formula One engine covers).
- Milking machinery and other equipment in dairy operations.
Other vacuum forming applications include: eyeglass lens manufacturing, light bulb production, plastic molding operations, lamination, safety glass production, and removing impurities from air conditioning systems.
Standards and Specifications for Vacuum Pumps
Your vacuum pump system may need to comply with various safety and construction standards based on your application and region. Certifications such as ISO and, for the USA, OSHA, are important for ensuring the effectiveness and safety of your vacuum system.
Things to Consider When Purchasing Vacuum Pumps
With the wide array of vacuum pump options available, selecting the right industrial vacuum pump can be challenging. Familiarity with industry terminology helps you make informed decisions.
Important Terms
When evaluating pumps, you’ll often see "Cubic Feet per Minute" (CFM), which measures the speed of vacuum flow. CFM is especially relevant for electric rotary vane and piston pumps, indicating how quickly the pump can evacuate air from a system or tank.
Another key measurement is Inches of Mercury (Hg), which indicates vacuum strength, similar to how horsepower measures motor power. This measurement is essential when the holding power of a pump is more critical than the speed of vacuum creation, as in metal and plastic machining industries.
The Right Manufacturer
The choice of vacuum pump manufacturer or supplier is crucial to your project's success. Partner with a company that is experienced, knowledgeable, and capable of meeting your requirements. Start by reviewing the supplier list above, visit their websites, short-list several companies, and contact them to discuss your specific needs, budget, and schedule. Select the manufacturer who best demonstrates the ability to fulfill your requirements.
Proper Care for Vacuum Pumps
With proper maintenance, your vacuum pump system can remain durable and provide long service life. What does proper care involve?
Effective care includes staying aware of the typical issues associated with your pump type so you can spot problems early. This allows you to address potential issues before they escalate. Also, for pump systems using lubricating oil, ensure the oil level never drops below recommended levels to avoid damage.
Vacuum Pump Accessories
Depending on your needs, vacuum pump accessories to consider include: vacuum gauges, vacuum bag sets, compressor kits, additional safety valves, power cord assemblies, and vacuum hoses.
Vacuum Pump Terms
Absorption
The process by which a gas or vapor penetrates beyond the surface of a solid or liquid, usually through diffusion, and becomes bound or trapped internally.
Absolute Pressure
This is the total pressure exerted by a fluid, combining atmospheric and gauge pressures. In vacuum systems, it is measured above a perfect vacuum (zero pressure), typically in pounds per square inch absolute (psia).
Adsorption
The process where gas or vapor molecules adhere to the surface of a solid or liquid.
Air Intake Filter
A component installed at the intake port of a vacuum pump or compressor, designed to trap insoluble contaminants from fluids using a porous medium.
Anneal
A vacuum heat treatment process used to relax a material and homogenize regions of a substrate affected by internal stress.
Atmosphere
A unit of pressure that supports a 29.92" column of mercury at 0°C at sea level. Daily atmospheric pressure varies slightly around this value.
Atmospheric Pressure
The pressure the Earth's atmosphere exerts in all directions, equal to about 14.7 psi at sea level. It is the force applied on a unit area by the atmosphere's weight.
Back Pressure
The resistance to fluid flow within a system.
Backstreaming
The movement of pump operational fluid vapor in the direction of the evacuated area.
Baffle
A system of cold surfaces placed between a pump's inlet and the chamber, designed to condense backstreaming vapor and return it to the pump.
Bake-out
The process of heating vacuum system components during pumping to accelerate the removal of adsorbed and absorbed gases.
Barometer
A device for measuring atmospheric pressure, usually expressed in inches of mercury (in. Hg) at a specific location.
Baseplate
A support plate for a belljar and its enclosed components, providing mechanical, electrical, and other connections within a vacuum system.
Belljar
A cylindrical vacuum chamber with a detachable seal, supported by a baseplate.
Cathode
The negative electrode in an electron device. In an ion pump, the cathode is the most negative electrode, able to emit electrons and collect positive ions.
Check Valve
A two-way valve that allows flow in one direction while preventing flow in the opposite direction. Check valves can function as directional or pressure control devices.
Condensation
The transformation of a vapor into a liquid or solid state.
Conductance
The ratio of throughput to pressure difference between two cross-sections inside a pumping system under steady-state conditions.
Cross-over Pressure
The pressure at which pumping transitions from one pump to another, enabling higher speed or lower pressure operation.
Degassing
The intentional removal of gas from a material, typically by heating it under vacuum conditions.
Dessicant Dryer
A moisture-absorbing material used to remove water vapor from air.
Differential Pressure Switch
A switch with both low and high-pressure settings. Fluid pressure triggers an electric switch to perform specific work.
Diffusion
The movement of particles from areas of higher concentration to areas of lower concentration.
Displacement
In positive displacement compressors, it is the total volume swept by the moving element. Displacement per revolution depends on chamber size; displacement per minute depends on speed.
Feedthrough
Also called "pass-through," it is a device enabling the transfer of electric current, fluids, or motion through a vacuum system wall.
Flow Rate
The quantity of fluid passing a point per unit time, often measured in cubic feet per minute (cfm).
Fluid Power
Energy transmitted and regulated using a pressurized fluid within a closed circuit.
Gauge Pressure (psig)
Pressure measured relative to atmospheric pressure, indicating the force per area due to a fluid.
Head
This term often denotes gauge pressure, representing energy per pound from pressure, elevation, or velocity, and is expressed in height units.
Hydrostatic Pressure
The equal exertion of pressure in all directions at points within a stationary gas or liquid in an enclosed space.
Ionization
The formation of ions by adding or removing electrons from atoms or molecules.
Isothermal
The expansion or compression of gas at a constant temperature, generally occurring slowly to allow heat exchange.
Kinetic Energy
Energy resulting from motion, imparted to a fluid either by spinning it rapidly or by introducing a catalyst in the flow direction.
Laminar Flow
Gas flow with sufficient velocity to move efficiently over surfaces, minimizing turbulence and resistance.
Lubricator
A pneumatic component that injects atomized oil into the air stream for lubrication purposes.
Manometer
An instrument used to measure the pressure of gases and vapors.
Maximum Vacuum Rating
The highest level of vacuum recommended for a particular pump model.
Mean Free Path
The average distance a gas molecule travels before colliding with another molecule or a surface.
Negative Gauge Pressure
Also known as "gauge vacuum" or "vacuum level," it is the reduction in pressure measured in inches of mercury (in. Hg) as air is removed from a system. Note: absolute negative pressure does not exist.
Nude Gauge
A vacuum gauge designed for direct insertion into a vacuum system without its own housing.
Open Capacity
The amount of air, in cfm, exhausted per minute when a vacuum pump operates without pressure or vacuum resistance.
Outgassing
The evaporation of substances, such as oil or dirt, after being placed in a vacuum or low-pressure environment.
Permeation
The passage of gas through a solid, typically by diffusion, and possibly involving surface interactions like adsorption or migration.
Pneumatic Fluid Power
Energy managed and delivered within a sealed circuit using pressurized fluid.
Positive Gauge Pressure
The pressure measured above atmospheric pressure.
Pressure
The force exerted per unit area on a surface, commonly measured in pounds per square inch (psi) or MegaPascals (MPa).
Pressure Switch
An electrical switch that is activated by changes in fluid pressure.
Psia (Pounds per Square Inch Absolute)
Pressure measured from a perfect vacuum, indicating total pressure without atmospheric influence.
Psig (Pounds per Square Inch Gauge)
Pressure measured above or below atmospheric pressure, indicating either positive or vacuum pressure.
Quick Exhaust Valve
A valve that rapidly releases air to the atmosphere, bypassing the directional valve to minimize back pressure.
Receiver Tank
A tank that stores gas under pressure or vacuum, providing a source of pneumatic power. Receiver tanks help handle sudden demand, reduce frequent cycling of an air compressor or vacuum pump, and dampen pulsations.
Residual Gas Analyzer
Also called a "partial pressure analyzer" or "partial pressure gauge," it measures both the quantity and types of gases present in a vacuum chamber.
Residual Gas
Gas that remains in a vacuum chamber after the pump-down process is complete.
Safety Valve
A valve designed to open fully and quickly to relieve excess pressure once a set limit is exceeded.
Sight Ports
Glass-covered openings that allow observation of the interior of a vacuum system.
Solid-state
Refers to devices that control current without moving parts, heated filaments, or vacuum gaps.
Sorption
A general term for the uptake of gas or vapor by a solid, whether through adsorption or absorption.
Standard Air
Defined as air at 68°F, 14.7 psia pressure, and 36% relative humidity.
Standard Temperature and Pressure (STP)
Also called "standard operating conditions," it refers to the reference temperature and pressure—usually 760 mm Hg (1 atm), 25°C—for comparison of values.
Surface Damage
Physical or chemical changes to a surface that reduce its regularity, symmetry, or alter its composition.
Torr
A pressure unit equal to 1/760th of a standard atmosphere.
Trap
A device used to capture and retain vapors or gases on cold or adsorbent surfaces.
Turbulent Flow
Non-laminar gas flow at high pressures and velocities, characterized by irregular movement.
Vacuum
A space containing air or gas at pressures below atmospheric, measured in inches of mercury (in. Hg).
Vacuum Chamber
The sealed container from which air or gas is evacuated for a process or experiment.
Vacuum Gauge
An instrument used to measure gas pressure below atmospheric levels.
Vacuum Rated Capacity
The cfm of air a vacuum pump can exhaust at its rated speed, usually specified for vacuums from 0 in. Hg to the maximum rating.
Vacuum Relief Valve
A valve that allows modulated atmospheric air into a system to regulate vacuum levels.
Vacuum System
An assembly including pumps, valves, chambers, lines, and instruments used to perform vacuum processes or experiments.
Vapor Pressure
The saturated vapor pressure at a specific temperature for any substance, a constant value for comparison.
Venturi Vacuum Pumps
These pumps work based on the Venturi effect, where a liquid or gas flows through a tube that narrows and then widens, causing a pressure drop as the tube contracts.
Viscosity
The measure of a fluid’s resistance to flow under pressure.
Viscous Flow
Describes gas flow—turbulent or laminar—through channels where the mean free path is much smaller than the channel dimensions, making collisions between molecules the main factor in flow behavior.
Volumetric Efficiency
Also called "volumetric ratio," it is the percentage ratio of a pump's actual output to its calculated theoretical output.
More Vacuum Pump Information
Vacuum Pump Informational Video