Anodized Aluminum
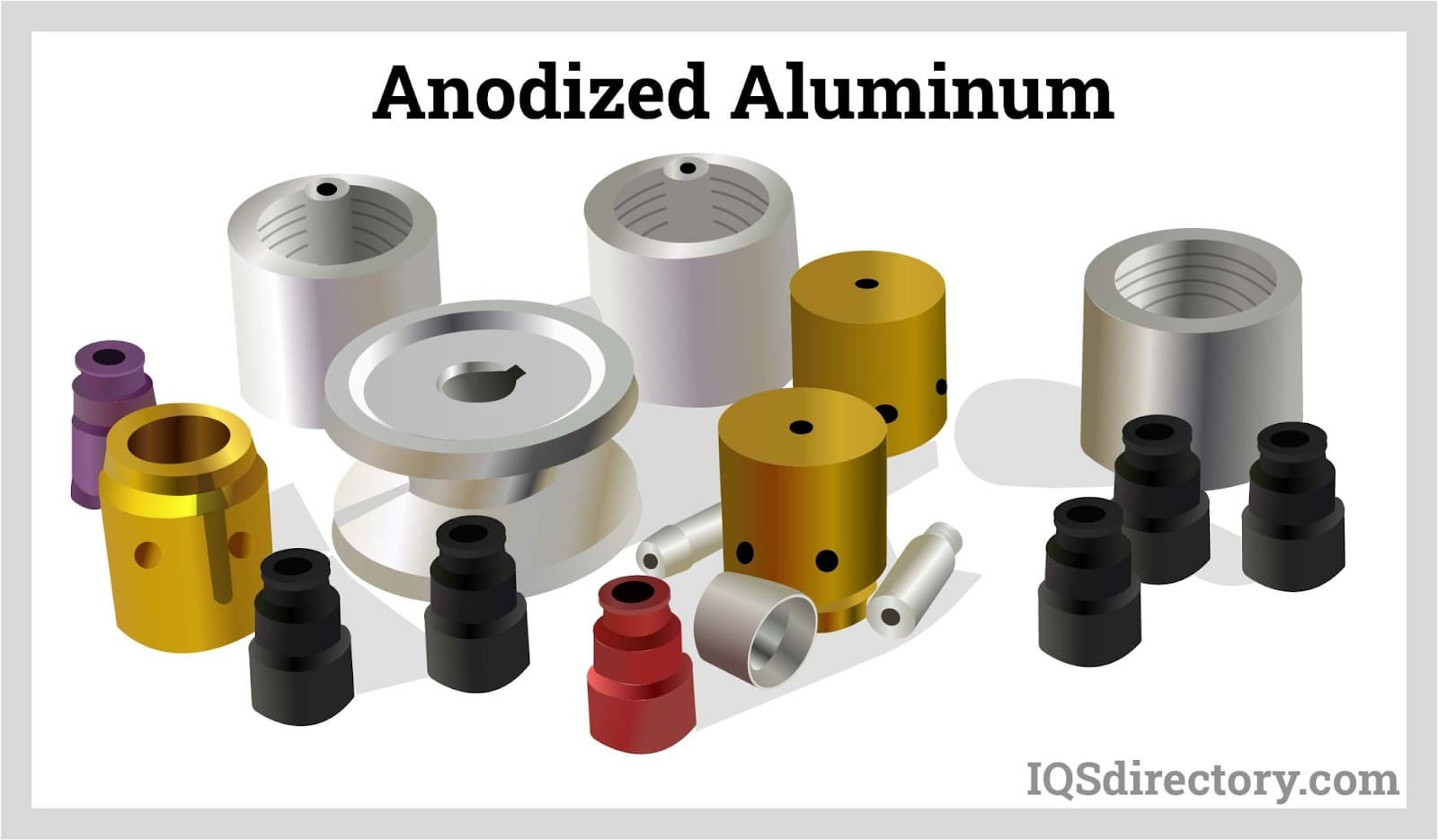
Metal processing is the cornerstone of metal production, encompassing a diverse range of fabrication techniques—from stamping and pressing to bending, cutting, and roll forming. Each method incorporates precise processing steps tailored to transform flat metal into custom configurations, meticulously crafted to meet exacting industrial requirements.
Metal processing is crucial in creating durable products by engineering and fabricating parts with precision and functionality. It encompasses a wide range of techniques, from tempering metals to enhance durability, to annealing for increased malleability. Each method undergoes rigorous testing to ensure it meets exacting standards and delivers precise dimensions crucial for the integrity of the final product.
Aluminum anodizing enhances the aluminum by thickening its natural oxide layer through a hardening process. This method capitalizes on aluminum's inherent ability to oxidize upon exposure to air, forming a protective layer that shields the metal from corrosion, rust, and wear. Strengthening the aluminum surface through anodization significantly bolsters its durability and resistance, reinforcing its appeal as a versatile and enduring material choice.
Anodizing aluminum offers an additional dimension by enabling vibrant color enhancements. This electrolytic surface treatment not only hardens the metal but also enhances its non-conductivity while creating a porous surface ideal for vibrant color infusion.
Electrical discharge machining (EDM) is a recent advancement in metal processing, which employs electrical energy to cut, drill, etch, and machine metals with remarkable precision. Integrated into CNC machines, EDM excels in crafting intricate geometries and achieving meticulous detailing. Its versatility shines through its ability to handle both hard, solid surfaces and delicately perform precise machining on softer materials.
Manufacturers use diverse methods to safeguard metals against environmental factors and wear. Techniques such as painting, coating with specialized materials, and applying powdered substances are often used for protection. An innovative approach to metal preservation involves electroless nickel plating, where a nickel alloy layer, deposited using nickel phosphorous or nickel boron, is applied directly onto the substrate to enhance durability and resilience.
To form the nickel layer, immerse the workpiece in a water solution containing nickel salt and a phosphorus agent. This chemical mixture evenly deposits nickel onto the workpiece, requiring no electricity or external stimulus for the process to occur.
In today's era of electronic equipment and systems, safeguarding them from external electromagnetic signals is crucial to maintaining uninterrupted operation and peak performance. Random electromagnetic interference (EMI) originates from diverse sources, whether human-made or natural phenomena. Its impacts can range from service disruptions and data loss to complete system failures, underscoring the necessity for robust protection measures.
EMI shielding constitutes a mechanical device specifically engineered to counteract electromagnetic interference. Crafted from various metals, these shields are meticulously shaped and tailored to integrate seamlessly into the housings, enclosures, and casings of electronic equipment. The choice of metal varies based on the specific application requirements and the level of protection mandated.
Heat treatment stands as one of the foremost methods for processing metals, aimed at modifying their atomic structure to enhance physical, chemical, and mechanical properties. This transformative process involves subjecting the metal to controlled heating and subsequent cooling cycles, meticulously adjusting its behavioral traits and overall characteristics.
To prolong the lifespan and optimize performance of metals, they undergo treatment with various coatings—thin layers of materials applied directly to the substrate. These coatings encompass a range of options such as powders, paints, and metal layers. Beyond bolstering protection against environmental factors, metal coatings can enhance aesthetics by introducing colors and textures, thereby adding to their visual appeal.
Aluminum anodizing is a surface hardening process that enhances aluminum alloys by thickening the natural oxide layer through electrolytic passivation. This method is employed to boost resistance against corrosion and wear. While anodizing can be applied to various metals, aluminum is often preferred among anodizers due to its inherent susceptibility to corrosion, exacerbated by alloying elements like copper and iron.
Learn more about aluminum anodizing.
EDM, short for electrical discharge machining, is a specialized tooling method harnessing electrical energy to cut, drill, etch, and machine metal parts with precision. Renowned for its accuracy, EDM excels in crafting intricate geometries and details, particularly when guided by CNC EDM machines. This versatile process is effective for machining both tough materials and delicate substances that pose challenges for traditional cutting methods.
Learn more about edm.
Electroless nickel (EN) plating employs an auto-catalytic chemical process to apply a layer of nickel alloy—typically nickel-phosphorus or nickel-boron—onto solid substrates such as metal or plastic workpieces. Critical to this method is the use of a reducing agent, such as hydrated sodium hypophosphite, which interacts with metal ions to facilitate the precise deposition of nickel onto the substrate.
Learn more about electroless nickel plating.
EMI shielding involves the use of electrically conductive materials, such as metals like aluminum or copper, to protect electronic devices from electromagnetic interference (EMI). This interference can disrupt electronic signals, leading to malfunction or data loss in sensitive equipment. By enclosing devices or components in conductive enclosures, applying coatings, or using shielded cables and gaskets, EMI shielding creates a barrier that reflects or absorbs electromagnetic waves, preventing them from penetrating or escaping from the shielded area. Effective shielding is crucial in industries like telecommunications, aerospace, and medical devices, where reliable operation without interference is paramount.
Learn more about emi shielding.
Heat treating refers to a range of methodologies aimed at transforming the atomic composition of metals or crystalline structures to imbue them with advantageous physical, chemical, and mechanical attributes, including enhanced strength and ductility. These advanced production and manufacturing techniques employ precise heating and cooling processes to meticulously alter the performance characteristics of industrial materials.
Learn more about heat treating.
Coating services encompass a spectrum of techniques designed to apply a fine layer of material onto another, known as the substrate. Coatings fulfill diverse roles, primarily shielding the substrate from environmental elements like corrosion and physical abrasion. Additionally, coatings impart customized aesthetic qualities such as color, tint, fragrance, and texture, enhancing the substrate's visual and tactile appeal beyond its inherent properties.
Learn more about coating services.