Aluminum Extrusions
Aluminum extrusions are versatile linear products highly valued across a wide range of structural applications. This popularity stems from aluminum's excellent strength-to-weight ratio and the cost-effectiveness of the extrusion process. Similar to other metal extrusions, aluminum can be shaped through hot or cold extrusion, where aluminum stock is forced through a die to create a variety of forms. These include angles, beams, channels, profiles, and extruded tubing.
Extruded aluminum products, such as channels, shapes, and profiles, combine strength and lightweight properties, making them ideal for numerous structural applications. They are commonly used in light poles, building and window frames, lighting fixtures, car bumpers, hardware joints, trim, and many other components in the construction, industrial, and automotive sectors. Precision tolerance extrusion allows for the creation of complex shapes designed to interlock with other structures or serve specialized purposes, such as heat sinks for cooling electronics, refrigerators, and heat engines.
Aluminum's inherent properties—strength, resistance to rust and temperature variations, ease of fabrication, and complete recyclability—make it a preferred choice for building and structural materials. These attributes ensure aluminum and its alloys remain a go-to option for applications demanding reliability, durability, and sustainability.
History of Aluminum Extrusion
Joseph Bramah, a locksmith and inventor of the hydraulic press, patented the first metal extrusion process in 1797. While perfecting a pick-proof lock, he collaborated with blacksmith Henry Maudslay, an engineering genius, to develop a method of forcing soft metal through a mold using a hand-driven plunger. This process initially created parts for locks but later led to the development of tools and items applicable across various industries. In 1820, Thomas Burr utilized the hydraulic press with lead in a process called "squirting," enabling the production of pipes and rods. This innovation set the stage for standardized metal extrusion.
Aluminum was identified as an elemental metal in 1807 but was considered a luxury due to the high costs of processing raw material. Although abundant and 100% recyclable, aluminum is rarely found in pure form and requires extensive processing for extraction. In the late 1880s, Charles Martin Hall and Paul Héroult independently developed a smelting process using electrolysis, known as the Hall-Héroult process. This breakthrough drastically reduced aluminum's cost, making it more affordable than gold and opening avenues for industrial design. Shortly after, Karl Josef Bayer introduced a chemical process to extract aluminum from ore. Both the Hall-Héroult and Bayer methods remain in use today.
The first extrusion press was built in Pennsylvania in 1904, facilitating the rapid growth of the automotive and aircraft industries. Advances in sheet aluminum production for these industries led to the aluminum rolling machine, patented in Switzerland by Robert Victor Neher in 1910. This technology enabled the creation of aluminum foil, which became a household staple.
In 1935, the newly established Aluminum Association held its first meeting in New York. As World War II began, the U.S. became a leader in aluminum processing. Aluminum was integral to manufacturing airplane frames, ship infrastructure, and mess kits. During the war, recycling drives like "Aluminum for the Defense" and "Tinfoil" were organized, often exchanging movie tickets for balls of used foil. Between 1940 and 1945, the U.S. produced 296,000 aircraft, more than half of which relied heavily on aluminum.
The launch of Sputnik I, a Soviet satellite, in 1957 marked the start of the space race. Sputnik, a two-foot-diameter aluminum alloy sphere weighing about 200 pounds, highlighted aluminum's importance in aerospace. Today, 50-90% of spacecraft are made with aluminum alloys.
In 1959, Coors Brewing Company revolutionized the drink packaging industry by introducing the two-piece aluminum can with a pop-top lid. They later pioneered the first "cash-for-cans" recycling program, further promoting aluminum use.
Aluminum Extrusions Benefits and Advantages
The versatility of aluminum has established it as one of the most sought-after materials in design and construction. Its unique properties—high strength-to-weight ratio, corrosion resistance, conductivity, ductility, non-magnetic nature, and recyclability—make it indispensable across industries, from aerospace to housing.
Machining Advantages
Aluminum’s malleability complements the extrusion process, allowing for complex or simple shapes like extruded tubing, angles, and profiles. This reduces the need for additional manufacturing, cutting down on assembly time. While other metals can be extruded, aluminum achieves shapes that are unattainable with alternatives.
Cost Efficiency
Aluminum is one of the most cost-effective metals for extrusion. Compared to casting, roll forming, molding, and forging, extrusion costs are significantly lower, enhancing profitability.
Structural Integrity
Even after extrusion, aluminum retains its structural integrity, allowing for intricate designs and easy alloying for added strength.
Lightweight Durability
Aluminum is strong yet lightweight, offering equivalent structural integrity at half the weight of other materials.
Attractive Finishes
The aluminum anodizing process enables protective or decorative finishes in virtually any color, enhancing design flexibility.
Low Maintenance
Naturally resistant to corrosion, aluminum requires minimal upkeep, as its inherent finish provides long-lasting durability.
Recyclability
Aluminum can be recycled indefinitely without losing strength, making it a preferred material for consumers, fabricators, and environmental agencies alike.
The Process of Extruding Aluminum
The extrusion process may involve "hot," "warm," or "cold" extrusion, each with unique benefits. Aluminum stock, or "billet," is pressed through a die to form specific profiles. Direct extrusion involves a stationary die and a moving ram, while indirect extrusion uses a stationary billet and a moving die. Cold extrusion at room temperature yields strong components with minimal finishing, while warm extrusion offers enhanced ductility and lower energy consumption. Hot extrusion, performed at higher temperatures, is often used for intricate designs.
After extrusion, aluminum is straightened, aged, precision-cut, and treated as needed. Its recyclability, light weight, and thermal properties make it an ideal material for various applications, from heat shielding to structural components.
Extrusion Process Types
Direct Extrusion: The billet is heated to 750–925°F, softened, and pressed through a die by a ram, forming the desired shape.
Indirect Extrusion: The die is pressed through a stationary billet, reducing friction and enhancing speed and profile precision.
Cold Extrusion: Conducted at room temperature, this method produces strong, simple shapes with minimal oxidation and superior mechanical properties.
Finishing Aluminum Extrusions
Once extrusions are aged, they are precision-cut, bent, or mitered as needed. They may be painted or anodized to enhance appearance and durability. Aluminum’s adaptability ensures its continued dominance in modern design and manufacturing.
Characteristics of Aluminum Extrusions
For over a century, aluminum has proven itself as one of the most versatile manufacturing materials. To address evolving challenges, it has undergone continuous advancements in fabrication, processing, and alloy development. Modern aluminum extrusions are the culmination of these innovations, offering unmatched design flexibility and functionality.
Design Versatility and Manufacturability
Aluminum profiles provide nearly limitless adaptability in design and manufacturing. Their compatibility with other design elements reduces the need for secondary processing, such as welding and machining, streamlining production and enhancing efficiency.
Strength and Structural Integrity
Aluminum's naturally high strength-to-weight ratio makes it ideal for structural applications. When specific designs require enhanced strength, this can be achieved through strategic alloy placement, variable wall thickness, and internal reinforcements. These features ensure the structural integrity of extrusions for demanding applications.
Complex and Seamless Constructs
Aluminum extrusions can be machined into intricate, single-piece shapes without mechanical joints. Products like one-piece extruded tubing, angles, and sections offer superior strength and durability, reducing the risk of failure under pressure over time.
Customization for Diverse Applications
Whether addressing manufacturability, functionality, or aesthetic requirements, aluminum extrusions meet these objectives without compromising structural integrity. Their adaptability makes them a preferred material for custom product solutions.
Accelerated Time-to-Market
Aluminum tooling is simpler and faster compared to steel tooling. This results in lower costs and shorter lead times, making aluminum extrusions an excellent choice for rapid prototyping, testing, and product launches.
Lightweight Advantage
Weighing approximately one-third of iron and steel, aluminum extrusions are easier to handle, cost-efficient to ship, and ideal for weight-sensitive applications.
Improved Assembly Efficiency
Innovative aluminum extrusion designs significantly reduce assembly time by simplifying fabrication and assembly processes.
Corrosion Resistance
Aluminum's natural resistance to corrosion is enhanced through processes like anodizing, which adds a protective layer and an attractive finish. This makes extrusions suitable for applications requiring durability and aesthetics.
These characteristics set aluminum extrusions apart from other manufacturing materials, offering exceptional versatility and performance.
Design Aspects of Aluminum Extrusions
The design of extruded aluminum parts varies depending on their intended use, with considerations for weight, assembly, functionality, and finishing costs. There are two primary classes of aluminum extrusions:
- Solid Profiles: Created using a flat die, these have uniform wall thickness and are cost-effective to produce.
- Hollow Profiles: Produced with a two-part die consisting of a mandrel and a bridge, these profiles can feature cavities for specialized applications.
The dies used for extrusion are typically made from tool steel, such as SIS 2242, and are precision-crafted using electrical discharge machining (EDM). EDM applies rapid electrical discharges to erode the die blank into the desired profile. Simple designs minimize costs, but intricate profiles can be custom-made for specific applications.
When designing the die, it’s important to consider the final product requirements. Complex profiles may need additional machining to achieve smooth surfaces and precise tolerances. The International Tolerance Grade scale is used to determine allowable dimensional variations and appropriate wall thickness.
Standardized extruded parts are widely available, while custom extrusions require collaboration with experienced manufacturers. A reliable manufacturer considers all aspects of the project, from concept to finished product, ensuring proper material selection, design optimization, and cost efficiency.
Industries That Use Aluminum Extrusions
The widespread application of aluminum extrusions spans numerous industries due to their adaptability and lightweight properties. Examples include:
- Automotive and Transportation: Aluminum channels and profiles are used in trains, SUVs, semi-trucks, and cars for components like panels, runners, and bumpers.
- Machinery and Industrial Equipment: Lightweight and durable, extruded tubing and profiles are used in scaffolding, mining equipment, and process machinery.
- Office and Medical Furniture: Aluminum tubing and channels contribute to functional and durable furniture designs.
- Building and Construction: Aluminum profiles serve both practical and aesthetic purposes, including structural beams, ceiling frameworks, decorative trim, and window paneling.
- Medical and Electronics Industries: Small, precision extrusions are fabricated into heat sinks and other components requiring close tolerances.
With their ability to be extruded into complex, close-tolerance shapes, aluminum extrusions offer unparalleled versatility and performance across diverse applications.
Aluminum Extrusion Images and Illustrations
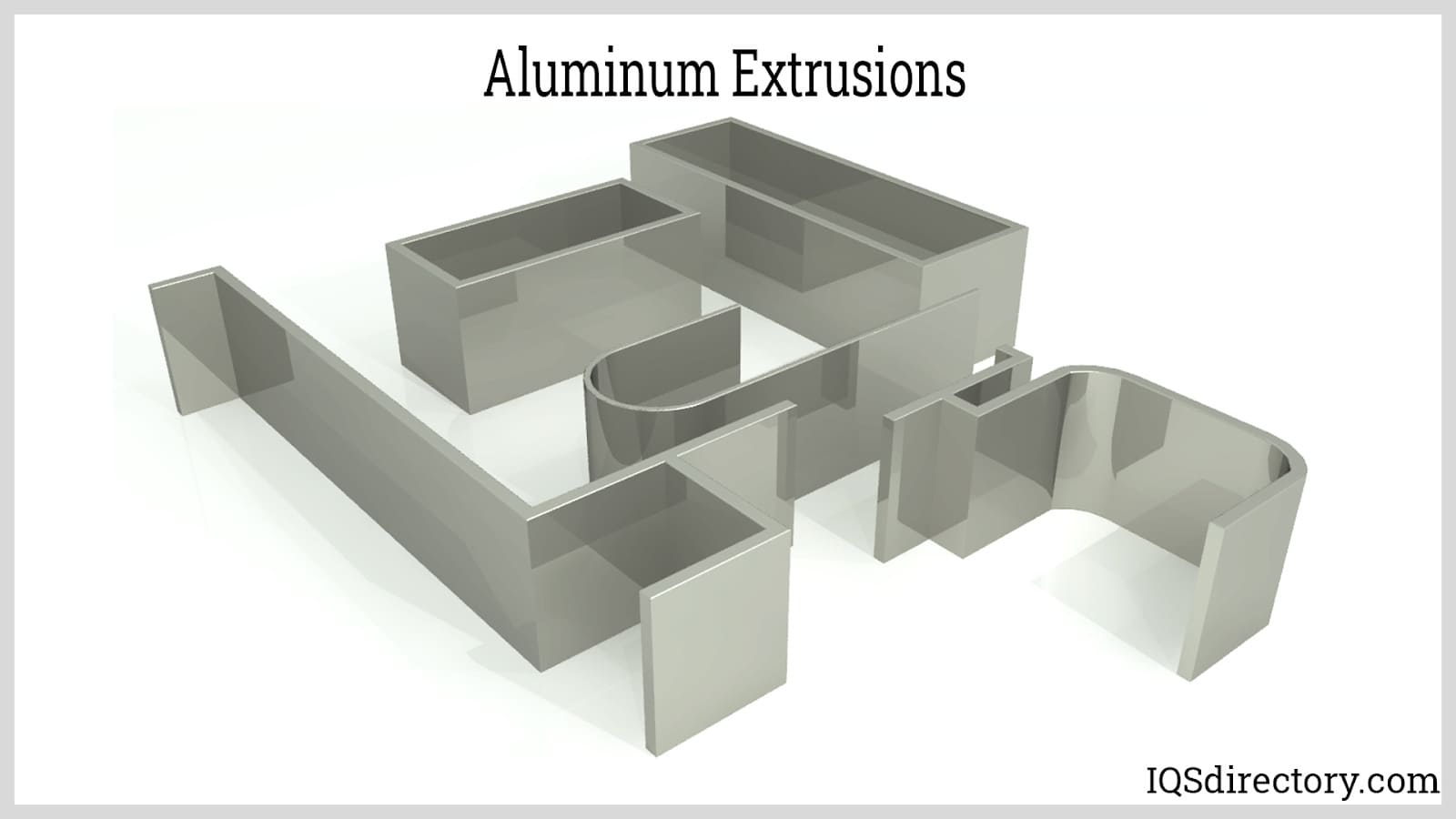
Extruded aluminum is a metal shaping process that involves forcing a preheated or cold aluminum billet through a die profile that has a cross-sectional shape.
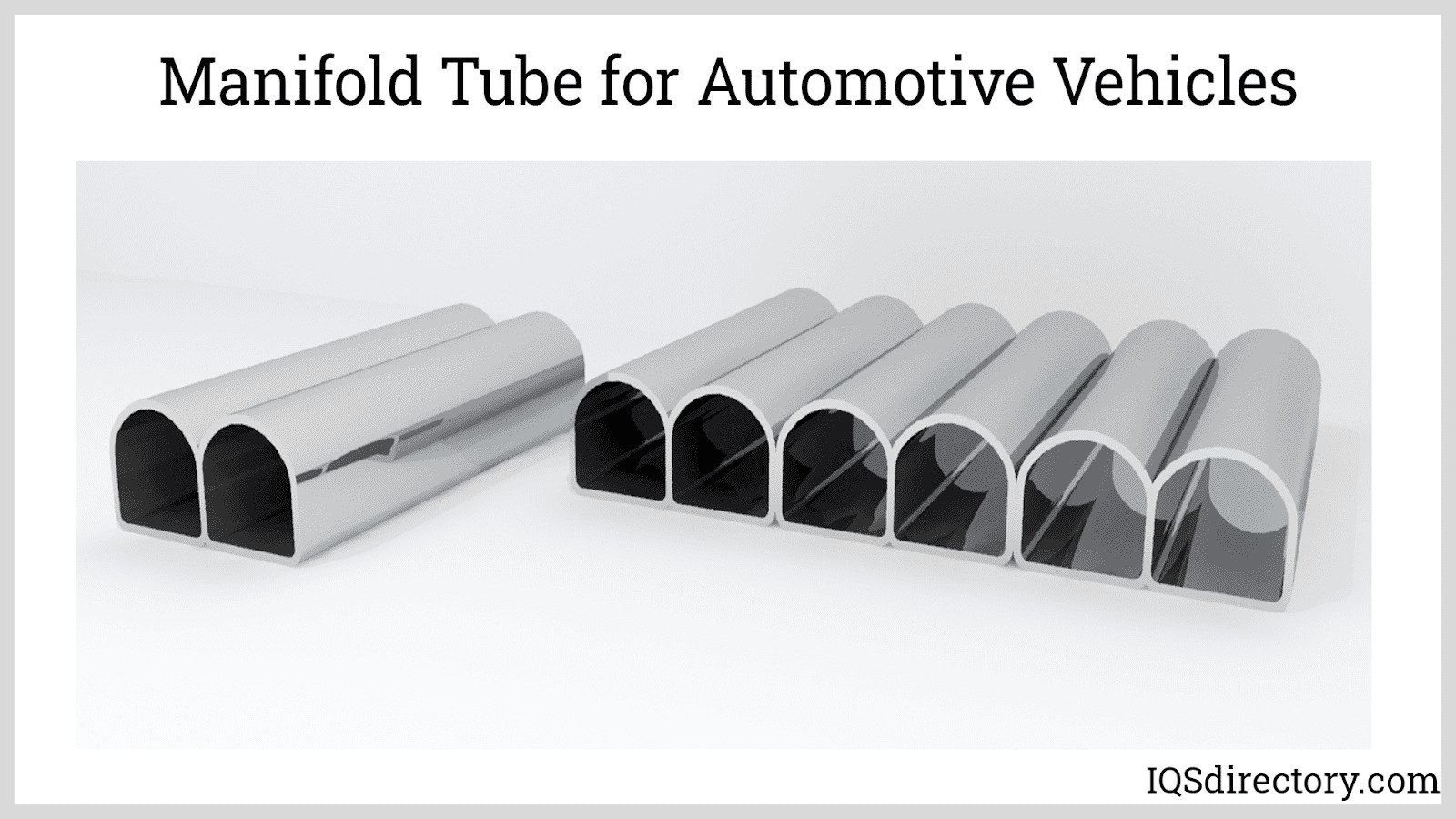
An example of the uses of extruded aluminum are the usage in the automotive industry.
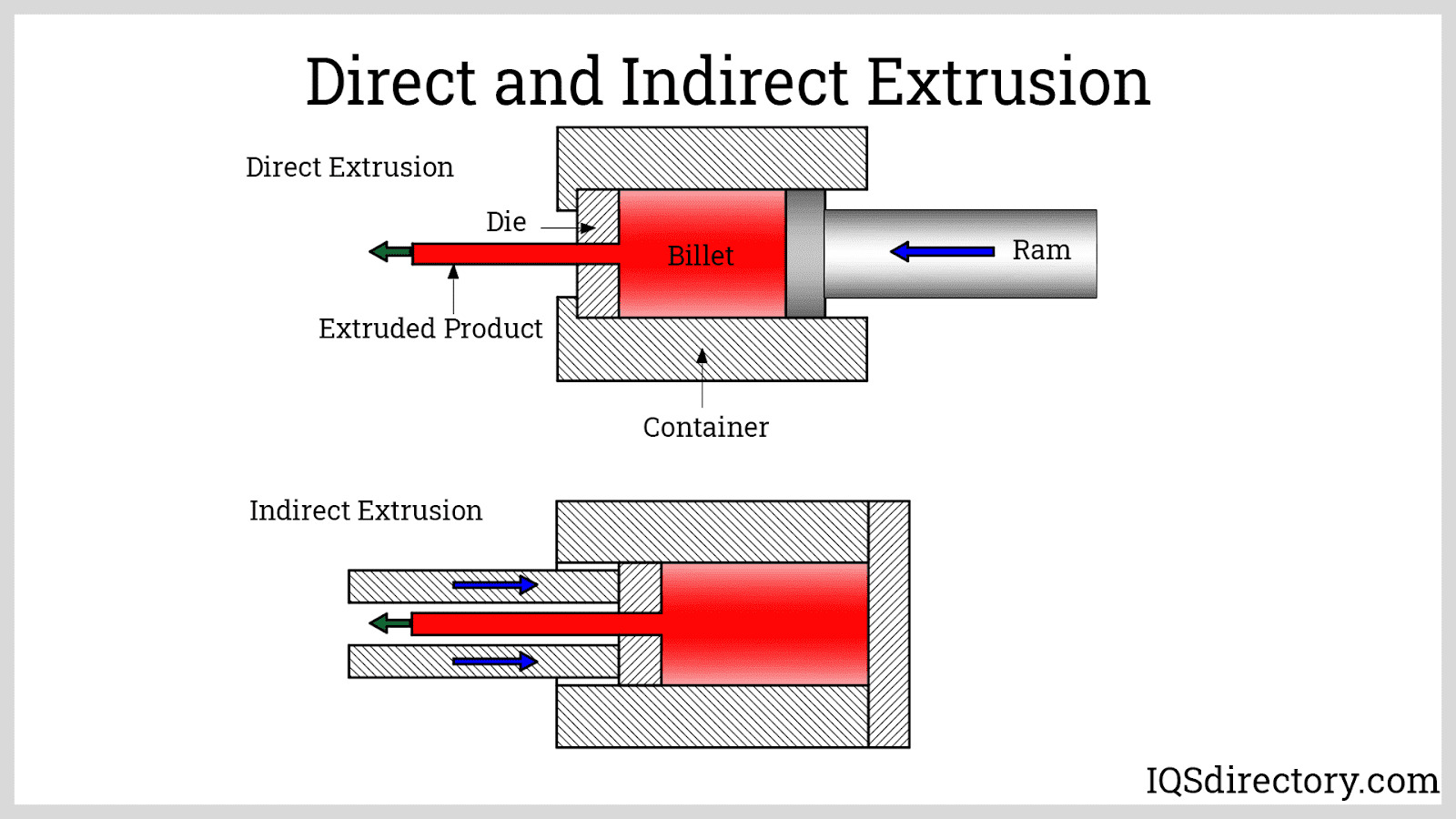
Direct extrusion is a process where the ram travel and metal flow are in the same direction, while indirect extrusion is the opposite.
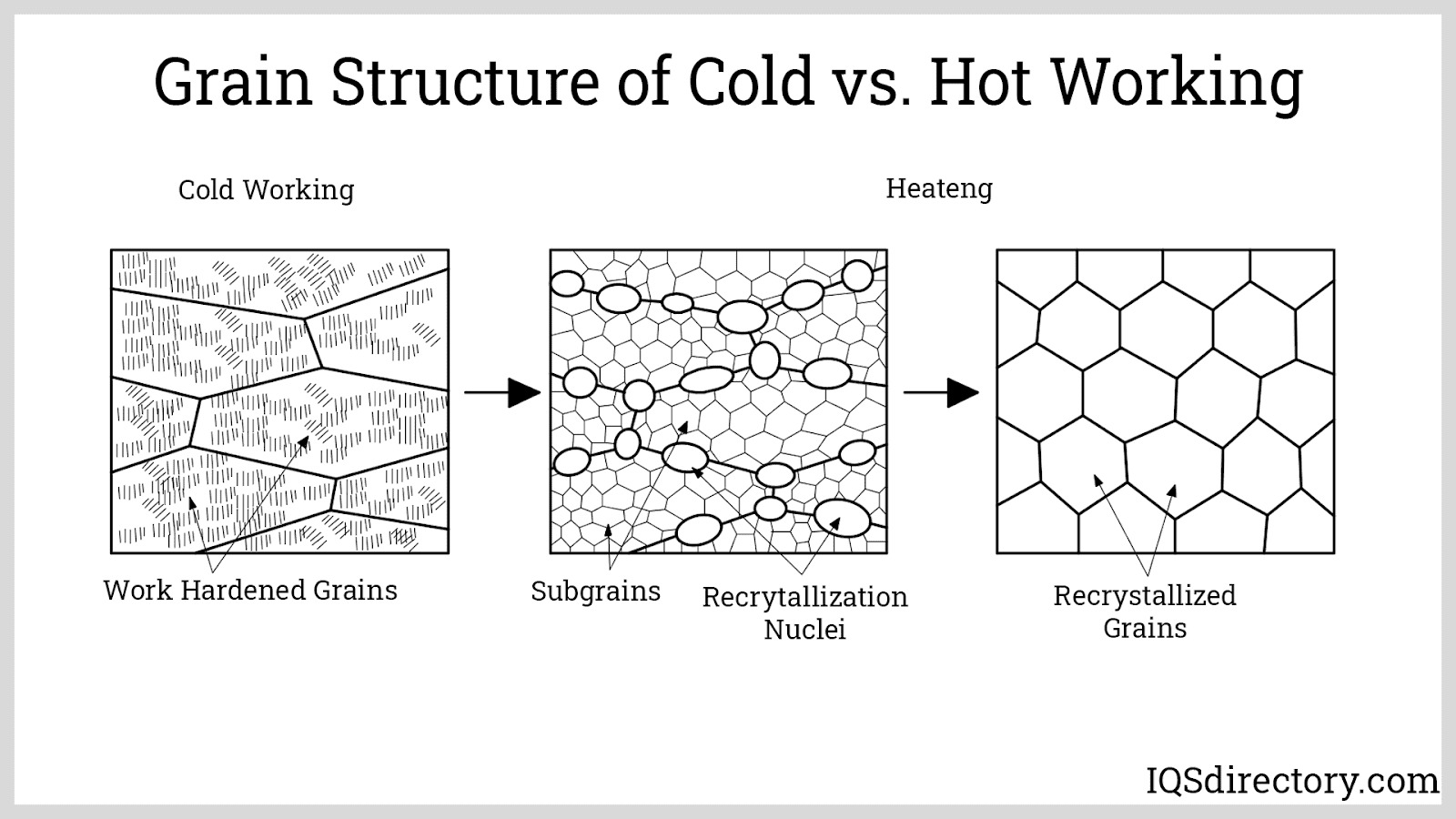
Hot extrusion is done above the aluminum‘s recrystallization temperature, where its microstructure begins to change while cold extrusion is done below recrystallization temperatures, typically at room temperatures.
Things to Consider When Purchasing Aluminum
Aluminum has long been a cornerstone in diverse industries, finding applications in transportation, construction, solar energy, medicine, electronics, and beyond. Its versatility, enhanced by advances in product design and engineering, continues to inspire innovation across various sectors.
To aid product development teams in determining the suitability of aluminum extrusion for their needs, we have outlined key considerations that encompass production, design, and performance variables.
Strength-to-Weight Ratio of Aluminum
Aluminum's high strength-to-weight ratio makes it indispensable in industries like aerospace and construction. However, as demands for higher performance escalate, standard extruded aluminum components sometimes fall short of meeting modern requirements.
Engineers and manufacturers are pushing the boundaries, prompting suppliers to develop innovative alloys that significantly narrow the strength gap between aluminum and other materials. Key advancements also focus on improving formability, machinability, and wear resistance.
These developments are particularly evident in the automotive sector. For instance, Audi crafted the R8 entirely from aluminum, while Ford reduced the weight of its F-150 pickup truck by 700 pounds through the extensive use of aluminum. Aluminum extrusion techniques, such as webbing to reinforce tubing, are proving critical in achieving these advancements. Properly executed, aluminum extrusion meets challenging strength and safety requirements without compromise.
Corrosion Resistance and Durability
Durability is a pivotal consideration in material selection, and aluminum’s corrosion resistance enhances both its longevity and aesthetic appeal. When exposed to air, aluminum forms a natural oxide layer that protects against corrosive elements. This protection can be further enhanced through anodizing and other finishing techniques.
Industries such as heavy infrastructure, solar energy, and medicine are capitalizing on aluminum's corrosion-resistant properties. From bridges and shipping vessels to solar frameworks and medical equipment, extruded aluminum products reliably meet demanding fabrication and durability requirements.
Manufacturing Efficiency and Processing Time
Reducing costs and optimizing manufacturing processes are ongoing challenges for design and development teams. Aluminum extrusion offers solutions by streamlining production. Extrusion can integrate multiple smaller components, optimizing the weight-to-strength ratio and reducing assembly complexity.
Collaborating with original equipment manufacturers (OEMs) can further enhance the efficiency of extrusion processes, cutting production and assembly times while maintaining high-quality outputs.
Turnaround Time and Supply Chain Efficiency
In today’s competitive market, swift manufacturing and delivery are vital. Aluminum extrusion outpaces many alternative materials in terms of turnaround time. Close collaboration between product developers and OEMs can further reduce lead times, ensuring products reach the market efficiently.
Shape Options for Aluminum Extrusions
While extrusion methods have remained consistent for decades, evolving technologies demand innovative solutions. The functional approach to extrusion design prioritizes the intended use of the structure over predefined shapes. By focusing on functionality, engineers can develop cost-effective, structurally sound designs that cater to specific applications while enabling adaptability for other uses.
This approach eliminates design limitations and fosters innovation, benefiting industries and customers alike.
Glossary of Aluminum Extrusion Terms
Aluminum Angles
L-shaped parts with two intersecting legs forming a 90-degree angle.
Aluminum Beams
Structural components used in construction.
Aluminum Channels
Linear, narrow shapes often used as supportive frames.
Aluminum Extruded Tubing
Hollow, linear products available in cylindrical, square, or rectangular forms for applications like downspouts and structural supports.
Aluminum Frames
Modules used in framing systems for enclosures and workstations.
Aluminum Profiles
Stock shapes customized for various applications.
Aluminum Trim
Long, narrow shapes tailored for specific purposes.
Architectural Aluminum
Decorative and structural components for construction.
Extruded Aluminum
Shapes formed by forcing heated aluminum through dies.
Heatsink
Devices that absorb and dissipate heat.
Metal Extrusions
Components formed through hot or cold extrusion, primarily from softer metals like aluminum alloys.
Structural Aluminum
Lightweight, durable, and corrosion-resistant alloys used in high-strength applications.
T-Slotted Aluminum Extrusions
Versatile components for enclosures, shelving, and industrial applications.
Common Aluminum Alloys
- 6061 Aluminum Series: A heat-treatable alloy known for its strength, corrosion resistance, and versatility in structural applications.
- 6063 Aluminum Series: Renowned for machinability and used in architectural applications like windows and stair rails.
Key Terminology
- Aging: The process of altering aluminum alloy properties, either naturally at room temperature or artificially at controlled high temperatures.
- Billet: Heated aluminum material forced through a die to create extrusions.
- Bright Dipping: A chemical process that gives aluminum a reflective, mirror-like finish.
- Yield Strength: The maximum stress aluminum can withstand without permanent deformation.
By considering these factors and leveraging aluminum’s unique properties, industries can unlock new opportunities for innovation, efficiency, and performance across a wide array of applications.
More Aluminum Extrusions Information