Hot Melt Adhesives
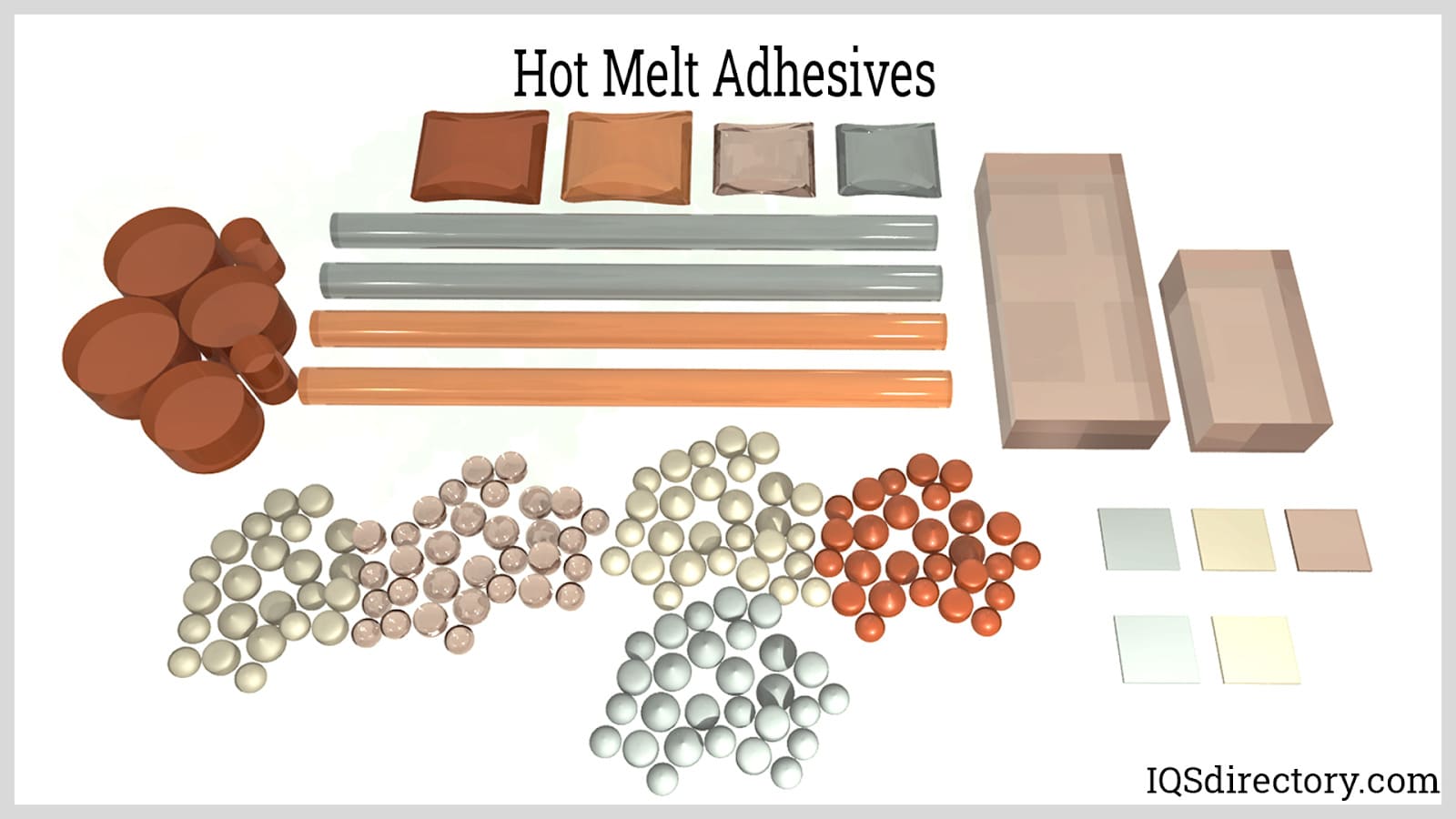
Hot melt adhesives are also known as glue adhesives. They are thermoplastic polymer adhesives that are solid at room temperature. Hot melt adhesives liquefy if heated to a temperature above their softening point...
Please fill out the following form to submit a Request for Quote to any of the following companies listed on
This article will take an in-depth look at epoxy adhesives.
The article will bring more detail on topics such as:
This chapter provides an overview of epoxy adhesives, detailing their creation process and operational mechanisms.
Epoxy: Epoxy glue is a thermosetting adhesive composed of an epoxy polymer resin and a hardener. It facilitates the adhesion or joining of diverse surfaces, creating a durable, lasting bond capable of withstanding extreme stresses and environmental conditions.
Adhesive: Pertains to the process of sticking to surfaces or objects.
Epoxy adhesives are the dominant choice in the realm of industrial adhesives, and they are known for being among the most versatile structural adhesives available. Their popularity is largely due to the strength of the cured product and their remarkable ability to bond with numerous materials. Additionally, these epoxy resin glue formulations are easily tailored to meet specific project requirements.
Various types of epoxy resin are used in formulating epoxy adhesives, which define the glue's core properties. For instance, a heat-resistant epoxy resin is optimal where temperature resilience is needed, whereas a flexible epoxy resin is preferable if movement comes into play.
To assess the effectiveness of an epoxy adhesive, examining the basic makeup of its compounds is insightful. Epoxies are generated through the polymerization of a blend of resin and hardener. The primary components of epoxy adhesives are epoxy resin and a curing agent, though additional ingredients such as fillers, tougheners, plasticizers, and other additives like silane coupling agents, defoamers, and colorants can be incorporated as needed.
Constituent | Ingredient | Main Role |
---|---|---|
Primary | Epoxy resin, reactive diluent | Adhesive base |
Primary | Curing agent or catalyst, accelerator | Curing enhancement |
Modifying | Filler | Altering properties |
Modifying | Toughener | Durability enhancement |
Modifying | Plasticizer | Increase flexibility |
Additive | Coupling Agent | Optimizes adhesion |
Additive | Colorant | Adds color |
Table 1: Epoxy Adhesive Components
The primary production of epoxy resins involves reacting active hydrogens from phenols, alcohols, amines, and acids with epichlorohydrin (ECH) under tightly controlled conditions. An alternative method involves using peroxide to oxidize an olefin, producing cycloaliphatic epoxy resins similarly.
Bisphenol A diglycidyl ether, often termed bisphenol A type epoxy resin, was the pioneer commercially produced epoxy resin and remains the most prevalent, making up approximately 75% of industrial epoxy resin use by volume.
This type of epoxy resin, commonly used in epoxy adhesives, owes its utility to its chemical structure composed of numerous functional groups and crucial properties.
Curing starts when the resin mixes with a designated catalyst, triggering an exothermic process as molecular chains engage at chemically active sites. The resulting covalent bonds between the epoxy resin's epoxy groups and the hardener's amine groups allow the polymer to cross-link, impacting the epoxy's rigidity and strength. By adjusting curing conditions like temperature and choosing specific resins and hardeners, it is possible to customize mechanical strength and resistance traits to meet diverse applications and operational contexts.
Epoxy adhesives adhere to many material types, and their characteristics are influenced by the system's chemistry and the specific cross-linking employed. These adhesives excel in chemical and heat resistance, adhesion, water resistance, and offer suitable mechanical and electrical insulation properties.
As the most common structural adhesives, epoxy types are available in one-component or two-component systems. One-component epoxies generally cure at temperatures between 250 and 300°F, resulting in products with substantial strength, excellent metal bonding, and strong environmental and chemical resistance, making them a preferred alternative to welding and riveting.
Pre-catalyzed one-component systems cure with mild heat, boosting efficiency and minimizing errors caused by air entrapment. The cure time for these systems is shorter compared to two-component systems. For two-component epoxy systems, catalyzation can occur at ambient temperatures, with heat further enhancing cross-linking and improving properties.
Offering versatility, two-component solutions can bond most surfaces and stand out for enduring constant force or weight over prolonged periods, resisting physical and chemical influences, and thus showcasing remarkable stability.
Highly adaptable, these epoxies serve various applications such as bonding, sealing, coating, and encapsulation across industries like electronics, medical devices, and aerospace. Special formulations offer properties like flame retardancy, cryogenic serviceability, rapid curing, and high-temperature resistance.
Some crucial factors to keep in mind when selecting epoxy adhesives are:
For optimal adhesion, an adhesive should adequately 'wet out' the surface, allowing it to spread and cover the surface area effectively, enhancing the contact and bonding forces between the adhesive and the substrate.
Key design elements to consider for an adhesive joint include:
Bond strength is influenced by conditions like temperature, moisture, chemicals, and weather exposure. It's advisable to test potential adhesives under conditions mimicking the actual service environment when degrading factors are likely.
Assessing adhesives involves not only performance but also considerations for their application. What application method will be employed? Is it a single or dual-component system?
Early planning of dispensing, mixing, and applying methods can lead to considerable time and cost savings, preventing potential production delays.
Ultimately, evaluating adhesives necessitates selecting and testing several candidates in the application, comparing properties through standardized tests. Sampling and personal trials are critical for informed decision-making.
Determining an appropriate cure schedule is vital for achieving optimal adhesive performance. Considerations include:
Epoxies are often paired and mixed as needed to extend their shelf life and minimize waste. Newer dual-barrel cartridges with static mixers allow dispensing premixed components in correct ratios for consistent application quality. In electronics, pre-mixed, frozen epoxies are popular, needing thawing right before use.
Resistance to chemicals and flames is critical in some applications. A primary feature of epoxies is their resilience to a broad array of substances like acids, bases, solvents, fuels, fluids, and both salt and freshwater, suitable for harsh chemical exposure and environments.
Certain epoxies also meet flammability standards for applications adhering to rigorous specifications (e.g., Underwriters Laboratories, an international safety certification organization). Specialized epoxies can enhance device longevity in challenging settings.
Epoxies often connect electronic and electromechanical assemblies to maintain electrical or thermal conductivity. These adhesives can attach heat sinks to components producing thermal energy during operation, ensuring better heat distribution for effectiveness.
Electrically conductive epoxies establish connections requiring electric conductivity for signal transfer or static discharge, easing the creation of reliable, high-performance devices for design and process engineers.
This chapter delves into the comprehensive classes and types of epoxy adhesives available today. Epoxy adhesive technology, known for its superior bonding strength, versatility, and chemical resistance, plays an essential role in industries ranging from construction, automotive manufacturing, and aerospace engineering to electronics assembly and DIY repairs. Understanding different classes and specialty epoxy formulations helps users select the most effective adhesive solution for their application, ensuring reliable, long-lasting bonds across a variety of materials and demanding environments.
Epoxy adhesives are broadly classified into one-component and two-component epoxy glue systems, both of which generate exceptionally strong connections but differ in curing process, application requirements, and end-use performance characteristics. These structural adhesives are frequently chosen for their high performance and durability in industrial and commercial applications.
In general, two-component epoxy resin adhesives provide greater mechanical strength, long-lasting durability, and chemical resistance compared to single-component epoxy adhesives. This makes them ideal for high-strength bonding, structural adhesive applications, and situations where elevated load-bearing capacity or thermal stability is critical.
Prior to application, the two components of 2K (two-component) epoxy resin adhesives—resin and hardener or catalyst—must be thoroughly mixed. The chemical reaction between these parts triggers the curing process and results in a rigid, cross-linked structure with excellent adhesive strength. 2K epoxy adhesives offer enhanced versatility, making them suitable for use across all market segments, including automotive, aerospace, marine, electronics, construction, and general manufacturing sectors. They're somewhat more complex to use due to mixing requirements, and the working (pot) life can range from a few minutes to several hours, depending on the industrial epoxy adhesive formulation.
These 2K epoxy resin adhesives typically cure at room temperature, although certain formulations allow accelerated curing through applied heat or external energy sources like ultraviolet (UV) radiation. The strongest, most durable epoxy bonds are often achieved with longer curing times. As a result, these adhesives are used in applications requiring structural integrity, gap filling, and resistance to mechanical stress, impact, and vibration.
2K epoxy glue systems bond effectively to nearly any substrate, including wood, metals (such as steel and aluminum), plastics (like ABS, PVC), ceramics, composites, and numerous types of rubber. They are highly resistant to physical and chemical exposure, such as solvents and moisture, and can withstand operating temperatures from 95 to 200°C (200 to 390℉). This makes them a preferred choice for demanding industrial adhesive applications and heavy-duty repair or maintenance projects.
Unlike 2K epoxy glue, one-component epoxy resin adhesives are pre-mixed and ready to use, requiring no mixing prior to application. They generally have a paste-like or thixotropic consistency, allowing for easy application via trowel, syringe, or bead extrusion, which is particularly useful for precise dispensing and automated processes. These adhesives are engineered to cure at elevated temperatures, typically between 120°C and 175°C, based on their chemical formulation.
One-part epoxy heat-cure adhesive systems provide efficient gap filling and sealing capabilities, especially between metal surfaces in high-stress environments. These products are commonly available as heat-curing epoxy films or sheets, making them ideal for large-scale bonding or lamination tasks in the aerospace and automotive industries.
In addition to aerospace structural bonding, one-part epoxy adhesives are widely used in construction as durable tile adhesives, for flooring installation, and in electrical component potting, thanks to their high adhesion strength, chemical and temperature resistance, and ease of application. Their quick processing and consistent bond quality make them a staple in assembly lines and precision manufacturing processes.
The various types of epoxy adhesives include both standard and specialty formulations engineered to address unique bonding challenges, performance requirements, and environmental factors.
DGEBA epoxy, or diglycidyl ether of bisphenol A (BPA), is the earliest and most widely used adhesive-grade epoxy resin. This base resin, with a low raw material cost and wide catalyst compatibility, serves as the foundation for countless epoxy adhesive formulations. DGEBA adhesives find extensive use in electronics, automotive, construction, and marine industries, where strong, durable bonds and chemical resistance are paramount.
DGEBA epoxy-based industrial adhesives can be formulated to cure at room temperature or via applied heat, adapting to diverse manufacturing needs. Available in low molecular weight liquid, semi-solid, and solid forms, DGEBA resins can be further modified, such as brominated variations for flame-retardant applications in circuit boards and electrical insulation. As a result, DGEBA epoxy adhesives are highly favored for their versatility, customizability, and balance of performance characteristics.
Waterborne epoxy adhesives, sometimes called aqueous or water-based epoxies, are innovative solutions developed for users seeking low-VOC, environmentally friendly bonding options. While epoxies are naturally hydrophobic and do not dissolve in water, chemical modification or emulsification with surfactants enables resins to disperse in aqueous systems. The resulting adhesives provide strong, reliable bonds with significantly reduced environmental impact—key for green building certifications or environmentally conscious manufacturing. The ultimate mechanical and chemical stability depends on the surfactant type and production technique selected for emulsification.
Epoxy acrylate resin adhesives, which include vinyl ester and specialized UV-curable resins, combine features from both epoxy and polyester chemistries. These resins cure rapidly at ambient temperatures and can also be activated by peroxides or radiation (UV/EB). Advantages over traditional epoxy glues include lower viscosity, increased flexibility, superior wetting, and fast cure times—although they may exhibit higher cure shrinkage. Industry applications for epoxy acrylate adhesives include flooring, protective coatings, composites, and rapid-curing repairs where speed and toughness are critical.
Traditional epoxy adhesives are valued for their rigidity and high strength, but some applications require toughened or flexible epoxy glue to absorb impact or vibration. Long-chain aliphatic epoxies can be blended into formulations to impart flexibility while maintaining strong cohesive bonds. These flexible epoxy adhesives are commonly employed for laminating safety glass, sound and vibration damping, encapsulating sensitive electronic components, and bonding materials subjected to temperature changes or dynamic loads. They balance hardness with elongation to meet modern design and manufacturing needs—making them a critical tool in both industrial and consumer adhesive applications.
Epoxy novolac adhesives are renowned for their exceptional chemical resistance and performance at elevated temperatures. With higher crosslink density than standard BPA epoxies, these high-grade resins offer superior protection against aggressive solvents, acids, and thermal cycling, making them ideal for use in chemical processing equipment, pipelines, protective coatings, and electronics manufacturing. Epoxy novolac adhesives typically require elevated temperature cures for maximum performance but can also be processed at room temperature for less demanding applications.
Challenges including high viscosity have been addressed by modern formulations, allowing easier processing and broader application of these high-performance epoxy adhesives. Epoxy novolacs are most often found in two-component (2K) systems, ensuring the highest level of chemical and thermal stability for the most demanding industrial uses.
Room temperature cure epoxy adhesives, often supplied in a two-component format, are prized for their ease of use and rapid development of mechanical properties without the need for specialized heating equipment. Mixing the epoxy resin with its curing agent (hardener) initiates a cross-linking reaction that produces a tough thermoset bond, tightly adhering to substrates like metals, composites, wood, or plastics. Formulators can tailor the pot life, open time, and final properties—making these products ideal for field repairs, maintenance, and general-purpose bonding under ambient conditions.
Fast-curing, room temperature epoxy adhesives often employ mercaptans or tertiary amine accelerators to significantly shorten fixture and cure times. When rapid strength development is essential—for example, in quick repairs, emergency fixes, or assembly-line production—these systems deliver excellent adhesion and a secure bond within 15 to 30 minutes, with full cure achieved in approximately 24 hours. Users must act promptly due to the limited working life of these high-speed epoxy glues.
Aliphatic polyamines are commonly employed as curing agents in epoxy adhesive formulations designed for ambient curing. Modified polyamine hardeners facilitate epoxide cross-linking, allowing adhesive manufacturers to fine-tune properties such as cure speed, bond toughness, and ease of handling. This versatility enables epoxy resin adhesives to fulfill a range of industrial, automotive, aerospace, and even DIY adhesive applications where temperature-sensitive substrates or rapid deployment are necessary.
UV-curable epoxy adhesives represent a breakthrough in high-speed assembly and electronic device manufacturing, as they deliver rapid curing and strong, reliable bonds with minimal exposure to ultraviolet light. These innovative adhesive formulations are especially valuable in electronics assembly, image sensor module production, touch panel and display manufacturing, and any application demanding fast throughput and excellent adhesive performance under cleanroom or high-volume production conditions.
Recent advancements in UV-cationic and UV-acrylate hybrid formulations have enabled new levels of efficiency and reliability for production processes, extending the reach of instant-cure epoxy adhesives to even more sophisticated and critical applications. UV cure epoxies are not affected by oxygen inhibition, exhibit minimal shrinkage during cure, and provide enhanced adhesion compared to traditional acrylate UV adhesives used in optical or medical device bonding.
UV cationic epoxy adhesives are formulated with cycloaliphatic epoxy resins and photo-initiators that respond swiftly to ultraviolet light by generating strong acids, catalyzing fast cationic polymerization. These structural adhesives are valued for their low cure shrinkage and absence of surface cure problems, in contrast to free-radical systems, enabling precise and bubble-free bonds in optoelectronic and microelectronic assemblies.
UV cationic epoxy adhesives may require additional thermal curing after UV exposure to achieve full strength or when bonding certain substrates. This post-cure step ensures optimal bond durability and performance, particularly for mission-critical or safety-related components.
Hybrid UV/thermal cure epoxy adhesives combine the instant curing capability of UV acrylate adhesives with the strength and reliability of thermally-cured epoxies. This unique combination addresses common limitations in traditional UV adhesives—such as surface cure issues, shadowed areas, and cure shrinkage—while enhancing final bond strength, chemical resistance, and environmental durability.
Formulations typically include acrylic monomers, epoxy resins, suitable photo-initiators, and epoxy curing agents. Some hybrid adhesives add thermal initiators, such as peroxides, to ensure complete curing in areas not reached by UV light. These advanced adhesives are prized for their high processing speed and robust performance in assembly lines, microelectronics, optical devices, and precision repairs.
Overall, the versatility, dependability, and performance of epoxy adhesive products have resulted in widespread adoption for countless bonding, sealing, and encapsulation scenarios across major industries. When selecting an epoxy adhesive, users should evaluate factors such as substrate compatibility, environmental exposure, service temperature, mechanical load, and required cure profiles to ensure optimal results. Leading suppliers and manufacturers offer a wide range of epoxy adhesive formulations—including custom solutions—to meet even the most specific technical requirements.
This chapter will discuss the applications and benefits of epoxy adhesives.
The applications of epoxy adhesives include:
The benefits of epoxy adhesives include:
The drawbacks of epoxy adhesives include:
Epoxy adhesives provide excellent adherence to a wide range of surfaces and are the most commonly used structural adhesives. Epoxy adhesives can be cured at room temperature, at increased temperatures, or via UV light radiation, depending on the type of curing agent used. Numerous epoxy adhesives, either one-component or two-component, have been marketed and widely utilized in various industrial production and applications for bonding metals, concrete, glass, ceramics, concrete, many plastics, wood, and other materials.
Hot melt adhesives are also known as glue adhesives. They are thermoplastic polymer adhesives that are solid at room temperature. Hot melt adhesives liquefy if heated to a temperature above their softening point...
Silicone adhesive is a versatile water resistant polymer whose primary ingredient is silica, a common form of sand found in quartz. The term silicone refers to a group of polymers that have a siloxane bond with organic compounds. The production of silicone adhesives begins...
Pressure-sensitive adhesive tapes consist of a backing material film coated with an adhesive intended for relatively low-stress applications. Light pressure, usually done by the fingertips, is applied to initiate the binding. In the sticking process, the fluid properties...
Carpet tape is a double-sided tape designed for securing carpets or rugs to the floor. It's made of strong, durable, and adhesive material that can hold the carpet in place and prevent it from sliding or wrinkling. Carpet tape is used in
One kind of pressure-sensitive self-adhesive tape is foam tape. It has one of several different backing materials and is made of foam. It may have adhesive on one or both sides. Foam tapes are, at their most basic level, tapes that are applied to uneven or
Industrial coatings are a type of substance that is spread over a surface of various derivatives like concrete or steel. They are engineered chemically to give protection over industrial products that include pipelines and...
Labels are an important aspect of product packaging, identification, presentation, and traceability. They are a way of communicating the manufacturer to the customers and the rest of the world. Labels promote the brand of the product and...
A mailing tube is a sturdy, solid, and durable cardboard container designed for shipping long slender devices and products or rolled up maps, banners, and posters. The indestructible exterior of mailing tubes...
Masking tape is pressure sensitive, thin and very adhesive, easy to tear paper that is used in various tasks ranging from masking off areas that are not to be painted or as insulation for electric wires among other...
Paper tubes consist of paper or paperboard sheet layers wound together to form strong, hollow, and usually cylindrical shapes. The paper layers are laminated or bonded together using adhesives. The wall thickness of the tube can vary depending on the number of layers wrapped during manufacturing...
A poster tube is a cylindrical, triangular, or rectangular hollow prism that is commonly used to transport rollable, unframed art, important documents, or long and slender materials. They also carry objects like...
PTFE stands for polytetrafluoroethylene and is a synthetic fluoropolymer used widely in many industries and many other applications. PTFE is also commonly referred to as thread seal tape, teflon tape, and plumber‘s tape...
A shipping tube is a long container used for mailing long items that are rolled or folded to fit in the tube. They are constructed of various types of materials with Kraft paper being the most common and widely...
A Sonotube® is a cardboard concrete forming tube made of waxed paper or lamination that is wound into a tube into which concrete is poured to create supports, columns, and supports for posts. Sonotube® is a registered trademark owned by SPC RESOURCES, INC...
A tape and label core is a thick durable tube that forms the center of a label or tape roll with the same shape as that of a toilet paper or paper towel core but is sturdier and more resilient. Although the shape of tape and...