Epoxy Adhesives
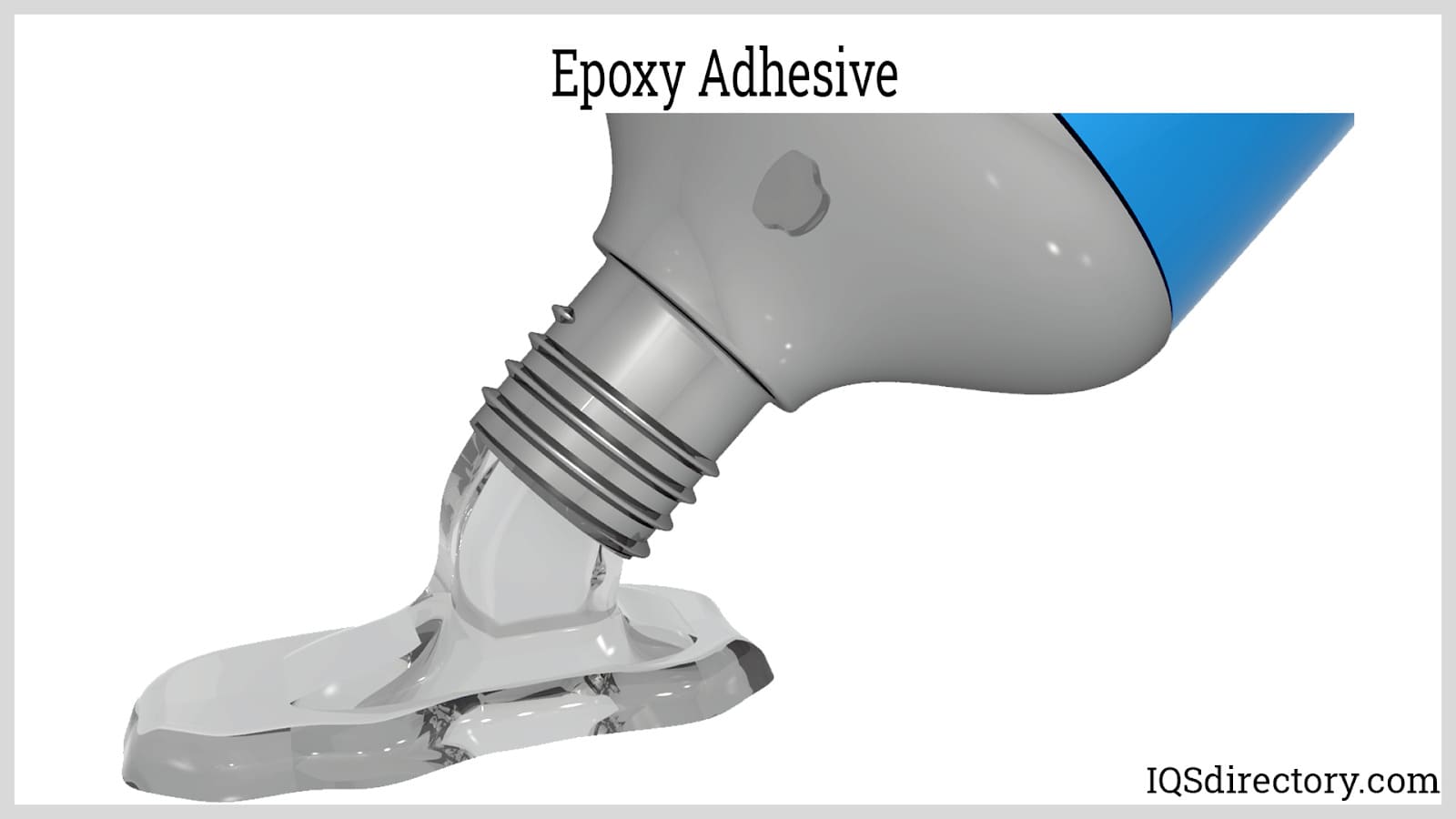
Epoxy: Epoxy glue is a thermosetting adhesive made up of a resin or epoxy polymer and a hardener that is used to adhere or join a range of surfaces together with a strong, permanent, and robust bond that can...
Please fill out the following form to submit a Request for Quote to any of the following companies listed on Hot Melt Adhesives .
This article will take an in-depth look at hot melt adhesives.
The article will bring more detail on topics such as:
This chapter delves into the details of hot melt adhesives, examining their production process and how they function.
Hot melt adhesives, commonly known as glue adhesives, are thermoplastic polymers that remain solid at room temperature but become liquid when heated beyond their softening threshold.
These adhesives have a relatively low softening temperature compared to other packaging materials, allowing them to be used across various industries. Turning into liquid upon heating, they become active and enable bonding between surfaces.
In solid form, hot melt adhesives come in shapes like beads, blocks, pellets, chips, pillows, or glue sticks. Depending on their application, they might be extruded through a nozzle, sprayed, or rolled onto surfaces.
The makeup of a hot melt adhesive affects its cost, performance, functionality, and availability. A typical hot melt comprises a polymer mixed with various additives, each serving different purposes.
Common additives include antioxidants, resins, plasticizers, and waxes, with other chemicals added to enhance specific properties of the adhesive.
Polymers are vital components of hot melts. Being long chains of specific molecules, polymers determine most physical traits of hot melt adhesives, such as heat resistance, flexibility, and strength.
The type of polymer, its molecular weight, and concentration influence properties like shear and impact resistance. Higher polymer content raises the viscosity, which refers to the thickness of the liquid, and enhances the adhesive's toughness and flexibility.
Resins crucially determine the tack, which refers to the stickiness and persistence of the adhesive after application. They also affect wetting properties, which control how the adhesive behaves in its liquid state on surfaces.
The choice of resin—based on factors like its softening point and compatibility with the primary polymer—affects the adhesive's performance. Resins such as rosin, its derivatives, and hydrogenated hydrocarbons are commonly used.
A higher resin content generally reduces tack and shortens drying time, while a lower resin content results in a more aggressive and durable hot melt.
Waxes primarily control the open time and set speed of hot melt adhesives. Open time refers to how long it takes to establish a bond, and set speed measures the quickness in achieving a sufficiently strong bond.
These parameters need to match production line requirements. Waxes also affect heat resistance and sub-ambient adhesion. Common waxes include synthetic, microcrystalline, and natural waxes, which vary by molecular weight, crystallinity, and melting point.
A lower wax content leads to higher viscosity, resulting in a more flexible and aggressive adhesive, while a reduced wax content lowers viscosity, decreases aggressive bonding, and accelerates setting.
Antioxidants prevent degradation in hot melts over time and include aromatic amines, phenols, BHT, phosphites, and phosphates. Mixed with stabilizers, these antioxidants do not change the adhesive's physical properties but protect it during its molten state and throughout compounding.
Plasticizers, used alongside resins and polymers, are crucial additives in hot melts. Acting as secondary base polymers, they boost toughness and flexibility. Typically, plasticizers are hydrocarbon oils that lower melt viscosity, enhancing wetting abilities with minimal aromatic content.
Beyond the main components, hot melts can incorporate various additives for specific applications, like biocides for bacterial inhibition, fillers to increase strength and decrease costs, or pigments, flame retardants, and even glitter for desired visual effects.
This chapter will cover the production process and characteristics of hot melt adhesives, providing insight into how these versatile industrial adhesives are made, the science behind their adhesive properties, and why they are widely chosen in various manufacturing and packaging sectors.
Hot melt adhesives are thermoplastic bonding agents that become pliable or plastic when heated and solidify as they cool, creating instant and durable bonds. Since hot melt glue contains no water or solvents, it delivers rapid curing times and reduces the risk of warping substrates. The essential raw materials for producing hot melt adhesives include resins, polymers (such as EVA copolymers, polyolefins, and polyamides), plasticizers, waxes, tackifiers, and antioxidants. Each ingredient contributes unique properties, like adhesion, flexibility, open time, and set speed, essential for meeting rigorous industry requirements.
During the hot melt adhesive manufacturing process, these raw materials are precisely weighed and blended in heated vessels to form a homogeneous molten mixture. Depending on the application—packaging, woodworking, automotive, nonwoven assembly, bookbinding, or product assembly—different hot melt formulas may be used. Common types of hot melt adhesives include polyurethane (PUR), metallocene-based polymers, ethylene-vinyl acetate (EVA), and polyethylene hot melts. These formulas are selected for their adhesive strength, fast setting characteristics, and compatibility with specific substrates.
Once blended, hot melt adhesives are discharged and cooled into various forms such as pellets, chips, blocks, slats, or sticks for hot melt glue guns, ensuring easy handling and accurate dosing during application. In many industrial settings, bulk hot melt is supplied in solid forms and melted on demand in heated tanks or melter systems that are integrated with automated dispensing equipment.
Hot melt adhesives are then heated until they reach a liquid state, making them ideal for both manual and automated adhesive application systems. This liquid is applied to the desired surface using methods such as spraying, rolling, bead dispensing, slot coating, or extrusion. Following application, the adhesive is allowed a short open time to achieve optimal wetting before being pressed together with the bonding substrate. Pressure—applied by rollers, clamps, or manual force—ensures a robust and consistent hot melt bond. The hot melt cools and solidifies rapidly, forming a resilient link ideal for high-speed production lines.
Hot melt adhesives exhibit a combination of performance properties that make them a preferred choice for industrial bonding and assembly applications. Understanding these properties helps in selecting the right hot melt glue formulation for specific uses across the packaging, woodworking, labeling, automotive, and textile industries. In comparison to solvent-based or water-based adhesives, hot melts offer advantages like lower VOC emissions, faster handling strength, and greater versatility.
Viscosity: Viscosity measures the thickness of a liquid and its resistance to flow, which is essential for precise hot melt adhesive dispensing and coverage. Liquids with high viscosity, such as oil, move slowly, whereas those with lower viscosity flow more easily. The viscosity of hot melt glues is influenced by the application temperature, typically between 250 and 350°F (121 to 176°C). Shear rate is a key factor in determining viscosity. Various instruments, such as capillary rheometers, Brookfield Thermosel, and dynamic mechanical analyzers, are used to assess viscosity, which is measured in poise. Proper viscosity ensures compatibility with a wide range of dispensing equipment and application methods.
Molten Color: The color of hot melt adhesives, often evaluated using numerical scales and both quantitative and subjective methods—including Hunter, Gardner, Saybolt, and the yellowness index—can be important for ensuring adhesive appearance in end uses like bookbinding, product packaging, or woodworking, where color consistency is essential.
Peel Strength: Peel measures the force required to separate bonded surfaces. It is quantified in pounds per inch and can be tested at various angles and on different surfaces. High peel strength is important for substrates that may experience flexing or dynamic movement during their service life.
Failure Temperature: Failure temperature—sometimes called heat resistance or service temperature—is the point at which a hot melt adhesive ceases to perform effectively. It is divided into peel adhesion failure temperature and shear adhesion failure temperature. Peel adhesion failure occurs when bonded surfaces can be easily separated at high temperatures, while shear adhesion failure involves the force applied as one surface slides over another. The strength of the adhesive is tested by mounting a specimen vertically, applying weight, and observing how long it takes for the surfaces to part. Selecting the right adhesive ensures the bond can withstand operating conditions.
Softening Point: The softening point is the temperature at which the hot melt begins to flow. It is influenced by the transition temperature of the base polymer and the type of wax used. Common methods to determine the softening point include the ring and ball test and the Mettler method. A higher softening point is often preferred for demanding applications such as packaging or automotive bonding, where exposure to high temperatures is possible.
Substrate-Specific Adhesion: This property varies depending on the material used. Bond strength characteristics are assessed using actual substrates and can be tested at ambient, elevated, and sub-ambient temperatures. Versatile hot melt adhesives are formulated to bond a wide array of materials, helping manufacturers meet the requirements for multi-substrate applications.
Thermal Stability: Thermal stability indicates how well a hot melt can endure various temperatures without degrading. This is assessed by heating the hot melt to its application temperature. A hot melt with high thermal stability remains stable at extreme temperatures, showing no significant decomposition. The test evaluates changes in viscosity, the formation of charring, skin, edge rings, color shifts, and gel formation. Good thermal stability is critical for minimizing downtime and equipment maintenance during high-volume production runs.
Cold Crack Formation: Cold crack formation tests determine at which low temperatures hot melts may develop cracks. Rubber-based hot melts typically show cracking in temperatures between 10 to 30°F (-12 to -1°C), while other types of hot melts can crack at temperatures ranging from 15 to 45°F (-9 to 7°C). Low-temperature flexibility is crucial for cold storage and freezer packaging applications.
Loop Tack: Loop tack is used for evaluating pressure-sensitive hot melts that bond only when pressure is applied. This test measures the adhesive’s aggressiveness, with results expressed in ounces. A higher force needed to remove the hot melt indicates greater aggressiveness. Pressure sensitive hot melts are common in labeling, tapes, and product assembly.
Mechanical Properties: Mechanical properties are crucial for evaluating a hot melt's performance. Key properties include the yield point, which is the stress level at which the hot melt begins to deform permanently, and tensile strength, which measures the force required to break a sample. These attributes influence the adhesive’s ability to hold up under loading and mechanical stress, relevant for structural applications and manufacturing environments.
Many advanced hot melt adhesives comply with regulatory standards, including FDA food packaging requirements and environmental sustainability directives, meeting the needs of industries seeking safe and eco-friendly bonding solutions.
Hot melt adhesives are favored for their flexibility, ease of application, immediate bonding capability, and lower melting points relative to other adhesive types. Their solvent-free nature and rapid set time make them highly suitable for automated manufacturing, ensuring minimal processing delays. These properties make hot melt adhesives highly effective and safe for use on a wide range of substrates and materials, even for difficult-to-bond plastics or slick surfaces where traditional glues may fail. Typical uses span case and carton sealing, furniture assembly, product labeling, bookbinding, automotive trim attachment, textile lamination, and more.
Hot melt adhesives are versatile enough for both manual application using glue guns and bulk dispensing in large-scale automated production lines. Their adaptable formulas can be customized to bond low-energy surfaces or to resist extreme environmental conditions. For users evaluating adhesives for purchase, it’s important to consider application method, adhesive strength, open and set time, temperature resistance, and substrate compatibility to ensure optimal performance for your specific industrial or commercial use case.
If you need guidance on selecting the best hot melt adhesive for your project or require custom formulations for unique manufacturing challenges, reach out to an experienced hot melt adhesive manufacturer or supplier. They can provide technical support, product samples, and recommendations tailored to your process, ensuring consistent quality and efficient production outcomes.
Hot melt adhesives, often referred to as hot glue, are versatile bonding agents widely used across many industries due to their fast-setting, flexible, and solvent-free properties. These adhesives are available in a range of formulations designed to meet specific bonding needs—offering solutions for manufacturers, packaging professionals, and product assemblers alike. Understanding the different types of hot melt adhesives is critical for selecting the best adhesive for your application and ensuring strong, reliable bonds in industrial and commercial projects.
Ethylene vinyl acetate (EVA) serves as an industry-standard polymer base and is one of the most common types of hot melt adhesives, especially in the packaging and bookbinding sectors. EVA hot melt adhesives deliver strong adhesion, rapid set time, and cost-efficiency, making them ideal for carton sealing, case packing, and paper-product assembly. These industrial adhesives are valued for their broad performance range, compatibility with automatic glue machinery, and ability to bond a wide variety of substrates. EVA adhesives are suitable for both standard and low-temperature applications, offering flexibility and ease of use even in low-temperature hot melt systems. Additionally, EVA’s versatility allows it to be formulated for food-safe and freezer-grade adhesives, meeting regulatory requirements for specific markets.
Polyethylene-based hot melt adhesives are especially effective in tray sealing, case closure, and other carton applications. These packaging adhesives are characterized by their low odor, light color, and easy release from metal surfaces, making cleanup and machinery maintenance simpler for manufacturers. Polyethylene adhesives also exhibit good chemical resistance and stable performance at traditional hot melt application temperatures. However, they are less suitable for direct bonding of difficult substrates such as certain plastics and metals, so they are typically reserved for applications involving paper, cardboard, and other porous materials. When selecting polyethylene hot melt, users benefit from straightforward processing, minimal equipment downtime, and product consistency, all of which contribute to lower operational costs and higher productivity in high-volume packaging environments.
Metallocene-based hot melt adhesives represent a newer generation of polymer adhesives, engineered for superior thermal stability and performance. First developed decades ago, metallocene polymers were added to hot melt formulations to reduce charring, enhance pot life, and minimize degradation from repeated heating and cooling cycles. Metallocene adhesives offer excellent storage temperature stability across both hot and cold environments, making them ideal for sensitive electronic components, medical device assembly, and food packaging. Their clean running properties significantly decrease equipment maintenance and downtime, reducing total cost of ownership for manufacturers. While these specialty adhesives tend to have a higher initial cost compared to conventional EVA glue, they offer exceptional bonding strength, longevity, and overall value. Today, varied metallocene hot melt adhesive formulations are available to meet the unique requirements of high-speed manufacturing, automated assembly, and even specialty labeling.
Amorphous poly alpha olefins (APAO) adhesives are chosen for applications that require a combination of tackiness, flexibility, and extended open time—ideal for product assembly, bookbinding, and automotive interior component bonding. APAO hot melt adhesives are known for their soft texture, low density, and strong adhesion to plastics and nonwoven substrates, including adding foam inserts to corrugated packaging or bonding corrugated plastic containers. Their moisture and chemical resistance expands their use to hygiene products, construction, and specialty tapes. With exceptional creep resistance and ability to maintain tack over longer periods, APAO adhesives provide manufacturers with greater process flexibility and adaptability for a variety of assembly operations. These adhesives are also compatible with a range of hot melt applicators and can often be customized with additives such as tackifiers, antioxidants, and plasticizers to further tune performance.
Polyamide adhesives are high-performance hot melt adhesives formulated for demanding applications that require resistance to heat, chemicals, solvents, and oils. These adhesives are widely used in wood bonding, filter assembly, textile lamination, and electrical product manufacturing due to their quick-setting, high-tensile strength, and flexibility in both low and high temperature environments (up to 400°F / 204°C). Polyamide hot melt is ideal for bonding substrates that experience exposure to harsh environments or challenging operating conditions. While they provide superior bond performance and high-temperature resistance, polyamides may exhibit less thermal stability during prolonged heat exposure compared to newer polymer technologies. When selecting a polyamide adhesive, consider the specific heat and chemical resistance requirements of your process to ensure optimal long-term performance and durability in your finished goods.
Choosing the Right Hot Melt Adhesive: When selecting a hot melt adhesive for your industrial or manufacturing application, it’s essential to consider substrate compatibility, required open and set times, operating temperature ranges, and any specific performance criteria such as food safety or chemical resistance. Whether you require quick bond strength for high-speed packaging or versatile adhesives for diverse materials, understanding the differences between EVA, metallocene, APAO, polyethylene, and polyamide adhesives ensures optimal product performance, cost savings, and streamlined production processes. Speak with an adhesive specialist or materials supplier to identify the best formulation for your needs and to ensure compliance with industry standards and regulatory requirements.
This chapter will explore the various applications and advantages of hot melt adhesives.
Hot melt adhesives find widespread use across various industries. Here are some key sectors that benefit significantly from these adhesives:
Spraying hot melt adhesives is an efficient and rapid method for application. This technique involves directing a continuous stream of adhesive to create specific patterns using compressed air. To maintain machine efficiency and avoid operational problems, it's important to oversee the application process carefully to prevent issues such as:
The process of cooling and setting hot melt adhesives starts with a spray nozzle designed for hot melts. This technique is especially effective for covering extensive surface areas.
Hot melt slot coating involves applying a layer of hot melt adhesive onto a substrate before it solidifies and cools. This method is typically used for adhesives that are pressure-sensitive, especially on thin substrates.
In the process of creating a hot melt bead or line, the nozzle dispenses a specific amount of adhesive before stopping momentarily and then restarting. This technique is mainly used when an adhesive needs to be applied precisely to a particular location and quickly compressed. Like with spray applications, the adhesive begins to cool immediately after being dispensed. Adhering to the recommended speed is essential to prevent any issues with bonding during this application.
While the benefits of hot melt adhesives can differ across various industries, there are several common advantages that are widely recognized. Some of these universal benefits are outlined below.
Hot melts are created from a variety of materials, leading to significant differences in cost, effectiveness, and the final characteristics of the adhesives. This diversity highlights the range of performance and functionality among different hot melt products.
Hot melts used for labels and tapes are typically pressure-sensitive. The labeling industry requires customizable products that offer a wide range of tack levels. A smaller tack range can be used for tapes, although they need a high level of shear resistance. Pressure-sensitive hot melts are now being used in place of solvent-based ones, mainly because they have a greater plasticizer and heat resistance.
Hot melts are commonly utilized in packaging, heat sealing, tray molding, and container labeling. Key attributes of these adhesives include extended pot life, adaptability in adhesion, minimal odor, lower application temperatures, and cost-efficiency. Specialized hot melts are employed for flexible packaging, such as small containers and lids.
In the graphic arts industry, hot melts are predominantly based on EVA and are typically applied at temperatures between 325 and 350 degrees Fahrenheit (163 to 176°C). These adhesives are known for their quick setting and reliable performance within a temperature range of 20 to 120 °F (-6.6 to 48.8 °C). They feature a unique property where they do not snap shut if released, akin to a mouse trap index. Additionally, graphic art hot melts resist ink solvents. Applying these adhesives requires precision, often using specialized tools, with the hot glue gun being the most frequently utilized.
Hot melt adhesive cleaners are very important to maintain and keep equipment running efficiently. There is a wide variety of hot melt cleaning systems and fluids from different manufacturers. Hot melt cleaners are offered for thermoplastic, polyurethane-based, polyamide-based, and polyolefin adhesives.
This adhesive exhibits excellent resistance to both extreme cold and heat. It offers robust bonding strength and superior vibration resistance, enhancing production efficiency and achieving peak strength more quickly than silicone alternatives.
Primarily used for laminating foam and mattresses, this adhesive cures rapidly, making it ideal for swift production. It features strong initial adhesion and good heat viscosity, along with excellent weather resistance.
Designed for bookbinding, this adhesive is suitable for binding reports, magazines, and hardcover books. It provides high bonding strength, weather resistance, and flexibility, ensuring the book remains flat.
This adhesive is highly effective for fabrics, offering strong adhesion, resistance to washing, and stability.
These adhesives are formulated to withstand high humidity and aging, making them suitable for various wood types and other materials.
Specifically intended for multi-layered materials, this adhesive provides strong, flexible bonding and long-lasting durability.
This adhesive is suitable and mainly used for laminating materials like aluminum boards, calcium silicate, bright PVC, etc.
This adhesive is ideal for bonding clear containers made of OPP and PVC. It features excellent adhesion, strong initial bonding, and impressive resistance to aging.
Electronic assembly adhesive is designed for use with various plastic materials in product assembly. It provides strong water resistance and ensures an airtight seal.
Hot melt adhesives find applications across diverse industries, including functional clothing, furniture laminating, and medical protection laminating adhesives.
Hot melt adhesives are also known as glue adhesives. They are thermoplastic polymer adhesives that, at room temperature, are in a solid state. Hot melt adhesives liquefy if they are heated at a temperature that is above their softening point. The use of hot melt adhesives has been of great impact on humanity. They are much safer and not hazardous for operators to use as compared to many other adhesives and thus make them a suitable and appropriate alternative.
Epoxy: Epoxy glue is a thermosetting adhesive made up of a resin or epoxy polymer and a hardener that is used to adhere or join a range of surfaces together with a strong, permanent, and robust bond that can...
Silicone adhesive is a versatile water resistant polymer whose primary ingredient is silica, a common form of sand found in quartz. The term silicone refers to a group of polymers that have a siloxane bond with organic compounds. The production of silicone adhesives begins...
Pressure-sensitive adhesive tapes consist of a backing material film coated with an adhesive intended for relatively low-stress applications. Light pressure, usually done by the fingertips, is applied to initiate the binding. In the sticking process, the fluid properties...
Carpet tape is a double-sided tape designed for securing carpets or rugs to the floor. It's made of strong, durable, and adhesive material that can hold the carpet in place and prevent it from sliding or wrinkling. Carpet tape is used in
One kind of pressure-sensitive self-adhesive tape is foam tape. It has one of several different backing materials and is made of foam. It may have adhesive on one or both sides. Foam tapes are, at their most basic level, tapes that are applied to uneven or
Industrial coatings are a type of substance that is spread over a surface of various derivatives like concrete or steel. They are engineered chemically to give protection over industrial products that include pipelines and...
Labels are an important aspect of product packaging, identification, presentation, and traceability. They are a way of communicating the manufacturer to the customers and the rest of the world. Labels promote the brand of the product and...
A mailing tube is a sturdy, solid, and durable cardboard container designed for shipping long slender devices and products or rolled up maps, banners, and posters. The indestructible exterior of mailing tubes...
Masking tape is pressure sensitive, thin and very adhesive, easy to tear paper that is used in various tasks ranging from masking off areas that are not to be painted or as insulation for electric wires among other...
Paper tubes consist of paper or paperboard sheet layers wound together to form strong, hollow, and usually cylindrical shapes. The paper layers are laminated or bonded together using adhesives. The wall thickness of the tube can vary depending on the number of layers wrapped during manufacturing...
A poster tube is a cylindrical, triangular, or rectangular hollow prism that is commonly used to transport rollable, unframed art, important documents, or long and slender materials. They also carry objects like...
PTFE stands for polytetrafluoroethylene and is a synthetic fluoropolymer used widely in many industries and many other applications. PTFE is also commonly referred to as thread seal tape, teflon tape, and plumber‘s tape...
A shipping tube is a long container used for mailing long items that are rolled or folded to fit in the tube. They are constructed of various types of materials with Kraft paper being the most common and widely...
A Sonotube® is a cardboard concrete forming tube made of waxed paper or lamination that is wound into a tube into which concrete is poured to create supports, columns, and supports for posts. Sonotube® is a registered trademark owned by SPC RESOURCES, INC...
A tape and label core is a thick durable tube that forms the center of a label or tape roll with the same shape as that of a toilet paper or paper towel core but is sturdier and more resilient. Although the shape of tape and...