Epoxy Adhesives
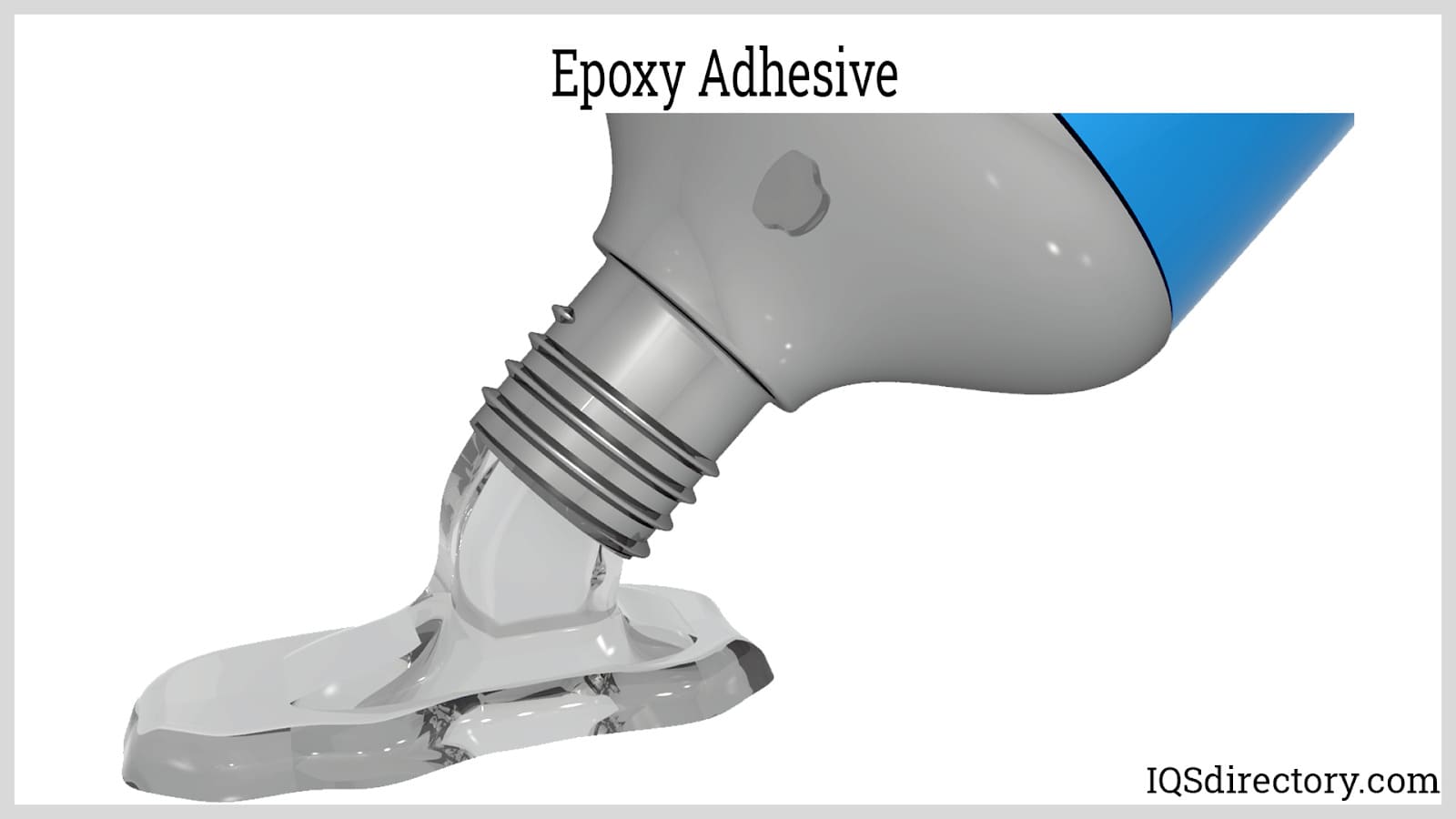
Epoxy: Epoxy glue is a thermosetting adhesive made up of a resin or epoxy polymer and a hardener that is used to adhere or join a range of surfaces together with a strong, permanent, and robust bond that can...
Please fill out the following form to submit a Request for Quote to any of the following companies listed on
This article takes an in depth look at Silicone Adhesives.
You will learn:
Silicone adhesive is a multifaceted, water-resistant polymer primarily made from silica, a prevalent form of sand found in quartz. The word "silicone" describes a category of polymers characterized by a siloxane bond, paired with organic compounds. The manufacturing process starts by extracting silicon from silica, often referred to as silicon oxide.
The numerous advantageous features of silicone adhesives have rendered them a favored choice in a wide array of applications. They present a non-toxic option distinct from conventional adhesives, being both inert and versatile. Silicone adhesives are extensively utilized across multiple industries as a reliable solution for fastening and bonding surfaces securely.
Thanks to their biocompatibility, silicone adhesives are often leveraged in the healthcare sector. They function as bandage adhesives that stick easily to the skin, forming a tight seal to avert infections while also being easy to remove without leaving behind any residue. Their durability is due to their remarkable chemical stability and resistance to environmental conditions and humidity. Whether applied to metals or skin, silicone adhesives deliver a robust, lasting bond.
The distinct characteristics of silicone make it an extraordinarily resilient adhesive. Its elasticity and other properties remain consistent over a broad temperature spectrum. Silicone adhesives are frequently employed for bonding metals due to their flexibility, thermal resistance, and competence in adhering to diverse substrates.
The principal ingredient in silicone adhesive is silica, a widely available mineral found abundantly in sand, soil, granite, and rocks. Silica is a core raw material, making up about one-fourth of the Earth's crust and serving as an essential building block in the production of high-performance silicone adhesives. Commonly found in forms such as emerald, quartz, clay, and glass, silica provides the basis for manufacturing industrial-grade sealants, caulks, and specialized silicone glues used in various industries such as electronics, automotive, medical, and construction.
Silica, also referred to as silicon dioxide (SiO2), is a compound of silicon and oxygen atoms. The three main forms of silica are quartz, tridymite, and cristobalite, with lesser-known forms including celestite, keatite, and lechatelierite. Beyond adhesive manufacturing, silica is widely utilized in numerous applications including concrete production, industrial abrasives, semiconductors, and advanced ceramics. Recognizing the diverse utility of this mineral enhances our understanding of its importance in producing both standard and specialty silicone-based bonding materials.
The manufacture of premium-grade silicone adhesives begins by isolating elemental silicon from silica. Silica, plentiful in quartz and sand, serves as the foundation for synthesizing high-purity silicon necessary for industrial adhesives and sealants. The extraction of silicon is a technically demanding process due to its very high melting temperature, necessitating advanced thermal and chemical engineering methods.
Quartz ore, containing both quartz and silica sand, is the primary source of high-quality silica. To extract the silica, the quartz ore is first crushed to a size of roughly 25 mm and then finely ground. After thorough grinding, the material undergoes scrubbing, washing, and flotation to further purify and separate the high-purity quartz sand. Screening follows to remove impurities, ensuring that the feedstock used for silicone production meets stringent industry standards for cleanliness and performance.
The final step in isolating silicon is to heat the purified quartz sand. As silicon has an extremely high melting point, the sand must be heated to temperatures exceeding 1800°C in an electric arc furnace, a critical step for electronics-grade and high-performance adhesive manufacturing. This reduction process produces metallurgical-grade silicon, which, after cooling, is ground into a very fine powder. This powder is then ready for subsequent chemical conversion steps that ultimately produce versatile silicone polymers and high-strength silicone rubber adhesives.
To produce silicone, the pure silicon powder is combined with methyl chloride and heated in the presence of a copper catalyst. This heating process triggers a key chemical reaction, resulting in the formation of various methyl chlorosilanes. Among them, dimethyldichlorosilane is the most critical precursor for silicone manufacturing. The mixture, containing dimethyldichlorosilane and other organosilicon compounds, is then separated and purified via fractional distillation at controlled temperatures, isolating the optimal base material for silicone resin and adhesive production.
During the next phase, water is carefully added to the dimethyldichlorosilane, initiating a controlled hydrolysis process. This leads to the generation of disilanol and hydrochloric acid as by-products. The disilanol undergoes condensation, often facilitated by hydrochloric acid, resulting in the formation of polydimethylsiloxane (PDMS). PDMS contains the characteristic siloxane (Si–O–Si) backbone, renowned for its flexibility, chemical inertness, and thermal stability. At this stage, formulators can tailor the molecular weight and cross-link density through advanced polymerization techniques, allowing for the customization of silicon-based adhesives for applications demanding flexibility, weather resistance, electrical insulation, or high bond strength.
Modern manufacturers may further blend additives, catalysts, fillers, or coloring agents with the silicone polymer to engineer adhesives with enhanced performance characteristics, such as UV resistance, improved adhesion to challenging substrates, or biocompatibility for medical-grade products.
Silicone adhesives and sealants are the result of polymerizing high-purity silicone compounds, producing advanced bonding solutions vital to many industrial, automotive, electrical, and construction projects. In their uncured state, silicone adhesives present as viscous gels or liquids, offering exceptional versatility for a wide range of substrates—including metal, glass, plastics, and ceramics. As a chemically inert and non-toxic compound, silicone adhesive is widely chosen for safety-critical and precision applications, including medical device assembly and electronics encapsulation.
The end product of the silicone adhesive manufacturing process is a robust, flexible, and heat-resistant bonding agent. These unique characteristics make silicone adhesives highly sought after for applications requiring long-term durability, resistance to extreme temperatures, moisture, chemicals, and environmental exposure. For example, in the automotive industry, silicone sealants are integral for engine gasketing and vibration damping; in electronics manufacturing, they are essential for potting, circuit board protection, and thermal conductivity; in construction, silicone caulks ensure watertight and weather-proof seals for windows, doors, and façades.
With advancements in adhesive technology, the latest silicone-based formulations provide superior performance, offering rapid curing, low VOC emissions, and compatibility with automated dispensing equipment. This makes silicone adhesives an indispensable component for efficient assembly lines, green building practices, and high-reliability product design.
Several types of silicone adhesives and sealants—including silicone bond, high-temperature silicone adhesives, room temperature vulcanizing (RTV) silicone, and silicone rubber sealants—are widely used across various industries. Thanks to their tight, flexible, and durable seals, silicone adhesives have become the preferred bonding and sealing solution for applications in construction, automotive, electronics, aerospace, and marine environments. Their reliable weatherproofing, thermal resistance, and chemical stability make them highly effective for demanding industrial and commercial requirements.
Among the broad range of silicone-based adhesives, two predominant categories exist: single-part (one-component) and two-part (two-component) systems. The fundamental difference lies in the arrangement of the curing agent, significantly impacting the workflow, application method, and drying or curing time. This allows professionals to choose the right product formulation for fast assembly lines, high-strength bonding, structural adhesive use, or flexible substrate attachments.
High temperature silicone adhesive is specifically engineered to withstand extreme heat, enduring continuous temperatures exceeding 600°F (315°C) and resisting aging, vibrations, and mechanical shock. These adhesives are commonly used in gasket bonding, oven and fireplace sealing, high temperature automotive repairs, and sealing industrial heating equipment. Classified as a type of RTV silicone, this gel-like liquid adhesive requires a curing period of 24 to 48 hours, depending on application thickness and environment. Its performance makes it a preferred choice for thermal insulation, electrical insulation, and as a heat-resistant sealant for metal-to-metal and metal-to-ceramic bonds.
RTV silicone adhesive is a versatile, gentle adhesive forming a strong, gasket-like bond between surfaces. Known for its cushioned texture and excellent elasticity, RTV silicone is favored in the electronics industry for electrical insulation and in construction for gap filling and weatherproofing. Its resistance to moisture, chemicals, UV rays, and temperature fluctuations make it suitable for both indoor and outdoor applications. Unlike other silicone adhesives, RTV begins curing on contact with air, which significantly reduces downtime during assembly or repairs. To prevent premature polymerization, it is stored in airtight containers. Additionally, RTV silicones serve as reliable sealants for automotive assembly, appliance repair, and HVAC installations.
Silicone rubber adhesive features many of the hallmark characteristics of silicone adhesives—such as flexibility, heat resistance, and exceptional waterproofing. It is frequently utilized in marine environments for sealing seams and windows on boats, as well as in bathroom and kitchen installations for waterproofing against leaks. Its capacity to create a durable, long-lasting, watertight seal resists cracking, degradation, and microbial growth, extending the lifespan of joined surfaces. Silicone rubber adhesive is especially suitable for bonding materials exposed to constant moisture or vibration.
Single-component silicone adhesive systems offer a convenient, ready-to-use solution that eliminates the need for mixing. These adhesives deliver consistent performance and retain flexibility across a wide range of operating temperatures, making them a preferred choice for manufacturing, household repairs, and product assembly. With a selection of hardness levels, viscosities, and even grades offering optical clarity, one-part silicone adhesives can address custom application requirements—such as electronics potting, glass bonding, and electrical sealing. Like other silicone adhesives, curing times depend on application thickness and environmental conditions, allowing for tailored production schedules.
Two-part silicone adhesives feature separate components for the adhesive base and curing agent, which are precisely combined prior to use. This system offers greater control over the curing rate and end properties, making it well-suited for high-performance manufacturing, structural bonding, and large-scale industrial assemblies. Once mixed, the cross-linking reaction begins immediately, gradually increasing the adhesive's viscosity until it fully sets. Two-part silicones are often chosen for applications requiring custom cure profiles, precise working times, or enhanced mechanical properties in aerospace, automotive, and electronics engineering.
Fluorosilicone adhesive is formulated with trifluoropropyl groups, amplifying its resistance to aggressive chemicals—including solvents, fuels, oils, acids, and bases—outperforming standard silicone adhesives in hostile settings. Its robust mechanical properties and multi-surface adhesion capabilities make it ideal for aerospace, automotive fuel systems, and environments where chemical exposure is unavoidable. Available in single-component and dual-component versions, fluorosilicone adhesives cure in patterns similar to traditional silicones, either through air exposure or component mixing. Their high performance and specialty formulation address critical bonding needs for aircraft, automotive gaskets, and chemical processing equipment.
Pressure sensitive silicone adhesives (PSAs) are constructed from high-quality synthetic elastomers engineered for strong, flexible adhesion to a wide variety of substrates, including plastics, metals, cloth, and low-energy surfaces. PSAs are extensively used for label application, protective films, and industrial tapes due to their capacity for instant tack and reliable, residue-free removal. Their formulation incorporates polymer chains with high molecular weight and repeating monomer units, promoting stability under extreme temperature fluctuations, harsh weather, or demanding environments.
The advanced properties of PSAs make them adaptable to different industries: from automotive masking tapes and electronic component protection films to masking tape and medical device assembly. Their packaging versatility (including rolls, sheets, or die-cut shapes) allows custom solutions. Silicone PSAs bond efficiently even to "hard-to-wet" surfaces and provide chemical resistance against solvents and oils, with minimal loss of tack or flexibility—making them highly valued in electronics assembly and healthcare sectors.
In the medical industry, pressure-sensitive silicone adhesives are preferred for sensitive skin applications such as wound dressings, surgical tapes, and transdermal patches. Their biocompatibility, hypoallergenic characteristics, and non-invasive removal protect the skin while reducing infection risk and optimizing patient comfort. PSAs can be engineered to inhibit bacterial growth, offer moisture transmission, and maintain adhesion throughout the healing process.
Despite performing similar bonding functions, PSAs display a variety of adhesion levels and tack properties that can be precisely formulated using different polymer blends, curing technologies, and substrate preparations. Modifications in coating techniques and chemical composition allow for targeted performance—satisfying the specific requirements of automotive, medical, packaging, and electronics industries. This degree of customization highlights the versatility and broad application scope of silicone-based pressure-sensitive adhesives.
Silicone PSAs are not only valued for their strong adhesion and reliable sealing properties, but also for long-term resistance to UV radiation, oxygen, heat, and chemicals. These features ensure the adhesives maintain their integrity in demanding settings, supporting a wide spectrum of industrial and commercial requirements.
In industrial and commercial manufacturing, silicone adhesives must often cure quickly to accommodate fast-paced production workflows. Modern silicone adhesives offer outstanding elastomeric properties, broad operating temperature ranges, resistance to chemicals such as fuels and oils, minimal shrinkage, and low shear stress—making them vital for high-stress environments and rapid assembly lines. Depending on formulation and curing system, the entire silicone adhesive curing process can finish in as little as ten minutes, dramatically improving efficiency, reducing production downtime, and providing strong, flexible bonds for high-performance applications.
Ultra-violet cured silicone adhesive is equipped with photo-initiators that activate curing upon UV light exposure. Once the photoinitiator absorbs light at the correct wavelength and intensity, a rapid polymerization reaction triggers, curing the silicone adhesive in mere seconds. This solvent-free curing method is ideal for cleanroom environments, electronics assembly, and medical device manufacturing where fast processing and contamination control are essential. Consistent UV exposure is crucial, as the curing process will stop immediately if the light source is removed.
Fast-curing silicone adhesives utilize a two-part, platinum-catalyzed system that can cure rapidly without the need for atmospheric moisture. Constructed from a vinyl-functional silicone polymer, a platinum catalyst, cross-linker, and inhibitor, this advanced adhesive system delivers efficient polymer network formation. The addition of the cross-linker initiates the curing sequence, typically reaching full strength and elasticity in about 24 hours. These high-speed systems are particularly valued for automotive manufacturing, electronics potting, encapsulation, and medical device assembly where a reliable, quick set is required.
LED curing systems offer a cutting-edge alternative to traditional UV curing for silicone adhesives. LEDs can be precisely calibrated to deliver exact wavelengths—from UV (365 nm – 395 nm) to visible light (405 nm – 460 nm)—matching the photoreactive components of modern silicone formulations. Advantages of LED curing include energy efficiency, low heat emission, environmental friendliness, and consistent illumination, ensuring dependable, even polymer cross-linking. These attributes have made LED light curing increasingly popular for electronics manufacturing, display assembly, and specialty bonding applications.
Aquarium silicone adhesive is specially formulated to maintain a waterproof, airtight bond for glass and acrylic fish tanks. It is essential for constructing and repairing aquariums—sealing seams, affixing decorative elements, and ensuring leak prevention under constant hydrostatic pressure. This marine-grade silicone adhesive dries to a clear, flexible finish—providing maximum visual appeal and lasting strength in submerged or continuously wet conditions. Its outstanding adhesion and elongation properties resist mold, algae, and chemical breakdown, maintaining aquarium safety. While the full cure may take up to seven days, it creates a strong, reliable seal that stands the test of time for hobbyists and professional aquarists alike.
Silicone adhesives are popular for their exceptional properties, notably their ability to maintain a strong bond across a broad temperature range. They effectively manage thermal stress between materials with varying expansion and contraction rates.
One of the key advantages of silicone adhesives is their durability in diverse environmental conditions. This longevity makes them particularly suitable for a wide range of applications, including those in medical fields.
Ceramic materials are known for their durability and non-metallic, inorganic nature. They exhibit high resistance to wear, corrosion, and thermal changes, as well as exceptional strength and effectiveness as electrical insulators. Ceramics are used in a variety of products and are a key material for engineers. Silicone adhesives are particularly useful for bonding ceramics to other substrates that may have chemical properties that make them challenging to bond with ceramics.
Glass presents a unique bonding challenge due to its smooth and non-porous surface. Most glass bonding applications do not require load-bearing but need to create a bond that remains effective under various environmental conditions, often invisibly. The adhesive used must be strong enough to form a watertight seal while also flexible enough to withstand multi-directional stress without breaking. Silicone adhesives are commonly chosen for glass bonding and sealing because they meet these requirements effectively.
Though not as fragile as glass, bonding rubber is a time consuming process that requires significant surface preparation using expensive and hazardous materials. For the bond to hold tight and firm, the surface has to be primed and roughed before applying the adhesive. Elastomeric technology has made it possible to bond many types of rubber. Silicone adhesives are a major development in the ability to bond and seal rubber, expanding its usefulness and number of applications. One part or two part systems can be used with two part systems ideal for rubber since they cure in thick layers.
Silicone adhesives are highly effective for bonding metals due to their versatility in joining different substrates. Unlike other adhesives, which often require specific formulations for metal bonding, silicone adhesives can effortlessly bond various metals. Both one-part and two-part silicone adhesives are suitable for this purpose. The curing time for silicone adhesives may vary based on the amount used and the types of metals being joined.
Silicone adhesive is particularly well-suited for bonding wood, allowing for direct application. Its strong bonding properties mean that only a small amount is needed, focusing on key areas where the pieces connect. This is especially beneficial when working with smaller wood components, as minimal adhesive is required.
Renowned for its strength and versatility, silicone adhesive offers a reliable grip while maintaining flexibility and sealing properties. Its resistance to UV radiation, temperature changes, and moisture further enhances its suitability for use with wood.
Silicone adhesive is a highly favored bonding agent due to its numerous advantageous properties. The production of silicone's raw material occurs in large quantities, facilitating the manufacturing process of the adhesive. Its prevalence spans across various industries, from aerospace to window installations.
The fundamental component of silicone production is silica, which ranks as the fourth most abundant mineral on the planet. Silica's widespread presence in diverse mineral forms simplifies the synthesis of silicone.
One essential attribute for adhesives is their ability to maintain bonding strength despite temperature fluctuations. This characteristic is a major reason for the widespread use of silicone adhesives in industrial settings. Silicone's capacity to adhere to any material further highlights the importance of this feature.
While silicone adhesive creates a strong and secure bond, it remains flexible and does not become rigid. Flexibility is crucial for many applications since materials often expand or contract with environmental changes. Silicone adhesive starts as a clear gel and cures into a flexible adhesive over time.
Silicone adhesive's durability under challenging conditions makes it an ideal choice for industries such as aerospace and extreme weather environments. Unlike other adhesives, silicone can endure conditions that might cause other adhesives to fail. It is essential for manufacturing and industrial processes that adhesives withstand production demands and offer long-lasting performance.
Although silicone adhesive requires several hours to cure, it becomes nearly invisible once fully set. This transparency makes it suitable for bonding applications like windows and aquariums. Engineers appreciate silicone adhesive for its ability to bond effectively without compromising the aesthetic of a design.
The ability of silicone adhesives to repel water is evident in their use in marine environments. Once applied, silicone acts as a sealant and remains unaffected by water or moisture. This property contributes to its use in aerospace, transportation, and window sealing applications.
Adhesive application often involves concerns about harmful fumes and complex preparation processes. Silicone adhesives stand out for being user-friendly, as they bond effectively with any materials regardless of their composition, without extensive preparation.
Contemporary manufacturing and production processes increasingly focus on reducing environmental impact and minimizing their ecological footprint. There is a heightened emphasis on sustainability in product development, driven by society's growing awareness of the adverse effects of harmful substances.
Silicone adhesives, derived from natural materials, have a minimal environmental impact. They are resistant to a broad range of chemicals and do not react chemically, further underscoring their environmental friendliness.
Engineers meticulously plan every facet of a project, including the choice of adhesive. In industrial settings, the materials used must be robust and resilient to withstand demanding conditions.
Silicone adhesives are preferred in many industries due to their exceptional strength, durability, and lack of chemical reactivity.
The extreme conditions of outer space impose significant stress and strain on spacecraft materials. The challenges of pressure, atmospheric conditions, and sealing demands necessitate the use of robust adhesives. Silicone adhesives have proven to meet these rigorous requirements effectively.
In the film industry, prosthetics are used to create various illusions on actors' skin. Various adhesives and bonding agents have been tested over the years, with some proving to be harmful. Recently, silicone adhesives have emerged as the optimal choice for applying and securing prosthetics. These adhesives are odorless and gentle on the skin. The curing process begins once the prosthetic is pressed into place.
Silicone adhesives are highly elastic, making them perfect for use in dentistry. Their chemical inertness ensures safety when used for placing prosthetic appliances in the mouth. Typically, dentists apply the adhesive to the appliance, position it, and then cure it using ultraviolet light.
There is a wide array of materials used in the automotive industry, which includes plastics, aluminum, steel, stainless steel, and various fabrics. In many cases, unlike materials need to be tightly joined and have a secure bond. It is for these reasons that silicone adhesives are used. They offer excellent adhesion to a variety of substrates and are long lasting.
Automobile manufacturers favor silicone adhesives for several reasons: they are durable, weather-resistant, waterproof, impact-resistant, and do not crack or peel. Additionally, they create a flexible bond that meets the demands of automotive applications.
Medical products have several intricate parts that have to be permanently joined and tightly sealed. Silicone adhesives are used due to their ability to bond and adhere unlike surfaces. Medical products are made using polycarbonate due to how easily it can be shaped and molded. Also, polyamide, or nylon, is used for tubing and catheters as well as titanium, which is used for implants like pacemakers, cochlear implants, hydrocephalus shunts, and infusion pumps.
Medical products must adhere to rigorous standards set by the American Medical Association (AMA) and the Food and Drug Administration (FDA). Silicone adhesives are well-suited for medical applications due to their inert nature and ability to create a strong, durable seal, which is crucial for medical devices.
Food grade silicone adhesive is free from toxic substances and chemical fillers, making it a safer alternative to conventional adhesives. It provides an exceptional bond and is highly durable, with resistance to temperature fluctuations, moisture, ozone, vibrations, and weathering.
Epoxy: Epoxy glue is a thermosetting adhesive made up of a resin or epoxy polymer and a hardener that is used to adhere or join a range of surfaces together with a strong, permanent, and robust bond that can...
Hot melt adhesives are also known as glue adhesives. They are thermoplastic polymer adhesives that are solid at room temperature. Hot melt adhesives liquefy if heated to a temperature above their softening point...
Pressure-sensitive adhesive tapes consist of a backing material film coated with an adhesive intended for relatively low-stress applications. Light pressure, usually done by the fingertips, is applied to initiate the binding. In the sticking process, the fluid properties...
Carpet tape is a double-sided tape designed for securing carpets or rugs to the floor. It's made of strong, durable, and adhesive material that can hold the carpet in place and prevent it from sliding or wrinkling. Carpet tape is used in
One kind of pressure-sensitive self-adhesive tape is foam tape. It has one of several different backing materials and is made of foam. It may have adhesive on one or both sides. Foam tapes are, at their most basic level, tapes that are applied to uneven or
Industrial coatings are a type of substance that is spread over a surface of various derivatives like concrete or steel. They are engineered chemically to give protection over industrial products that include pipelines and...
Labels are an important aspect of product packaging, identification, presentation, and traceability. They are a way of communicating the manufacturer to the customers and the rest of the world. Labels promote the brand of the product and...
A mailing tube is a sturdy, solid, and durable cardboard container designed for shipping long slender devices and products or rolled up maps, banners, and posters. The indestructible exterior of mailing tubes...
Masking tape is pressure sensitive, thin and very adhesive, easy to tear paper that is used in various tasks ranging from masking off areas that are not to be painted or as insulation for electric wires among other...
Paper tubes consist of paper or paperboard sheet layers wound together to form strong, hollow, and usually cylindrical shapes. The paper layers are laminated or bonded together using adhesives. The wall thickness of the tube can vary depending on the number of layers wrapped during manufacturing...
A poster tube is a cylindrical, triangular, or rectangular hollow prism that is commonly used to transport rollable, unframed art, important documents, or long and slender materials. They also carry objects like...
PTFE stands for polytetrafluoroethylene and is a synthetic fluoropolymer used widely in many industries and many other applications. PTFE is also commonly referred to as thread seal tape, teflon tape, and plumber‘s tape...
A shipping tube is a long container used for mailing long items that are rolled or folded to fit in the tube. They are constructed of various types of materials with Kraft paper being the most common and widely...
A Sonotube® is a cardboard concrete forming tube made of waxed paper or lamination that is wound into a tube into which concrete is poured to create supports, columns, and supports for posts. Sonotube® is a registered trademark owned by SPC RESOURCES, INC...
A tape and label core is a thick durable tube that forms the center of a label or tape roll with the same shape as that of a toilet paper or paper towel core but is sturdier and more resilient. Although the shape of tape and...