Air Pollution Control Equipment
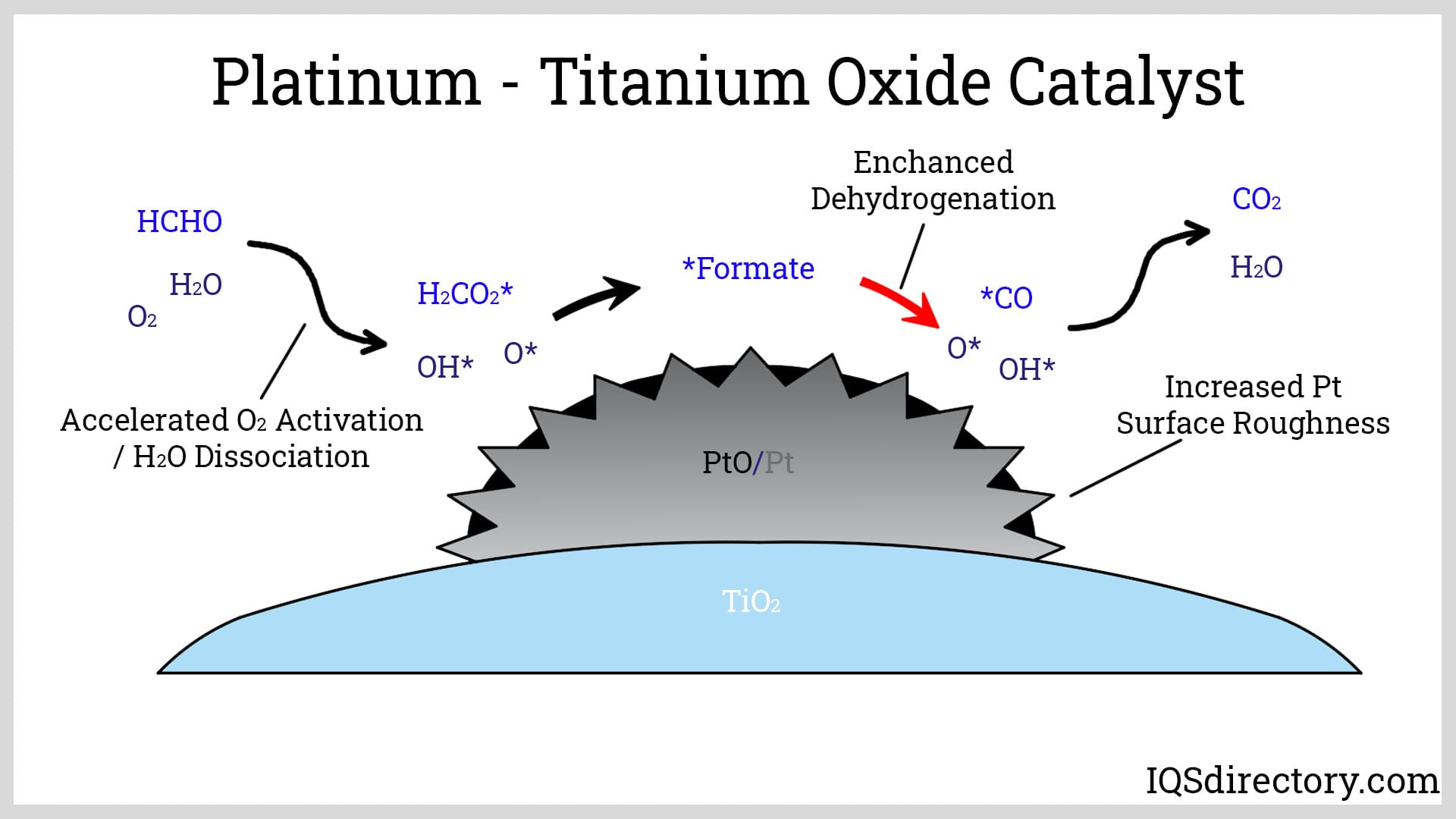
The term "air pollution" is used so frequently that many of us believe we have a complete understanding of its meaning. Scientists and environmentalists have made so many predictions of the negative effects...
Please fill out the following form to submit a Request for Quote to any of the following companies listed on
This article takes an in depth look at electrostatic precipitators.
This article will look at topics such as:
An electrostatic precipitator, or ESP, is an air pollution control device that utilizes electrical charges to eliminate airborne contaminants in solid, droplet, gaseous, or liquid states. It operates without the need for conventional filtration systems, efficiently capturing pollutants emitted from industrial processes, factories, and power plants.
As exhaust such as smoke or gas emerges from a burner or furnace, it traverses through wires or plates within the electrostatic precipitator that impart a static charge to the exhaust. This charged smoke or gas is then collected on an oppositely charged plate, where the pollutants are effectively trapped. Electrostatic precipitators can be customized to meet the specific requirements of pollutant conditions while using minimal electric power.
Many industrial sectors depend on fossil fuels for their production activities, which produce smoke containing soot, ash, and uncombusted carbon dioxide. ESPs deploy electric charges to cleanse these pollutants from the smoke, ensuring that only purified air is emitted into the surroundings. The removal of these detrimental particles is vital to prevent damage to buildings, protect the environment, and minimize health hazards to humans.
Electrostatic precipitators are engineered to extract particulate matter from polluted air, such as dust, smoke, soot, ash, and fumes, achieving up to 99% efficiency for particulates 1.0 μm or larger in diameter. The performance of an electrostatic precipitator typically remains high regardless of the size of the particulates. Nonetheless, those with extremely high or low resistivity may pose challenges, as ESPs operate optimally with particulate matter that possesses moderate resistivity.
Air pollution refers to the presence of harmful particles, gases, and contaminants in the atmosphere that degrade environmental quality and pose significant health risks to living organisms, including humans, animals, and plants. Common air pollutants such as nitrogen dioxide (NO2), sulfur dioxide (SO2), carbon monoxide (CO), carbon dioxide (CO2), ozone (O3), and fine particulate matter (PM2.5 and PM10) are known contributors to air quality degradation. These air contaminants can be toxic, causing serious health issues such as asthma, chronic respiratory problems, cardiovascular diseases, and various forms of cancer. In addition to threatening public health, air pollutants drive major environmental concerns by intensifying smog formation, acid rain, and the greenhouse effect, which accelerates climate change and global warming.
Sources of air pollution fall into two main categories: anthropogenic (human-made) and natural origins. Major human-generated sources include emissions from vehicles, industrial facilities, power plants, manufacturing factories, air conditioners, and refrigerators, all of which release volatile organic compounds (VOCs), hydrocarbons, and greenhouse gases into the atmosphere. Natural sources of air pollution encompass wildfires, volcanic eruptions, dust storms, and gases escaping from underground mines or natural gas reserves. If air quality management and pollution control strategies are not implemented effectively, these sources compound and cause severe consequences for both human health and the Earth’s protective ozone layer. To help reduce these environmental impacts, there are numerous types of advanced air pollution control equipment designed to minimize and mitigate emissions in various industrial and commercial settings.
Today, public awareness has grown regarding the urgent need for clean air, environmental stewardship, and the adoption of sustainable practices. The Environmental Protection Agency (EPA), under mandates like the Clean Air Act (CAA), actively regulates air pollutants and sets air quality standards to safeguard both the environment and public health. The CAA divides air contaminants into three primary groups:
Air pollutants are generated throughout every stage of industrial operations, from the extraction and processing of raw materials to production, distribution, and consumption. Industrial air pollution control is particularly important as these activities release a vast range of pollutants, including gases, dust, mists, chemical vapors, and particulates. Implementing effective air quality control technologies and equipment allows facilities to minimize emissions, meet regulatory compliance requirements, and reduce environmental impact. The most common air pollution control systems utilize fans or industrial blowers to move contaminated air into specialized filtration and purification systems that clean the air through various advanced methods:
Specialized air pollution control devices and systems are vital for industrial emission control. Common equipment used in the air filtration and pollutant removal process includes:
When selecting a pollution control system, it is important to consider factors such as pollutant type, concentration, industry-specific regulations, energy efficiency, maintenance requirements, and long-term environmental impact. Solutions such as air quality monitoring systems, stack emission monitoring, and continuous emissions monitoring systems (CEMS) are also critical for compliance, reporting, and proactive air quality management.
Flue gas is a byproduct of fuel combustion processes that occur in industrial boilers, furnaces, steam generators, and power plants. This exhaust stream, often called emissions or stack gas, is released through pipes or chimneys. If not effectively treated, flue gas will introduce harmful substances into the environment, negatively impacting air quality and public health.
Flue gas contains an array of pollutants, including fine particulate matter (PM), carbon monoxide (CO), nitrogen oxides (NOx), sulfur dioxide (SO2), volatile organic compounds (VOCs), and sometimes heavy metals or dioxins, depending on the fuel source. These components contribute directly to the formation of smog, acid rain, and ground-level ozone pollution. Water vapor, produced from the combustion of hydrocarbons, also makes up a noteworthy portion of flue gas and is often visible as smoke or steam from industrial smokestacks.
Effective flue gas treatment is required to protect the environment as well as meet local, state, and federal air quality regulations. Treatment technologies include wet, dry, and semi-dry scrubbers, selective catalytic reduction (SCR) units, and electrostatic precipitators, each designed to capture or neutralize specific contaminants. The choice of flue gas treatment method depends on the industry, fuel composition, regulatory requirements, and the targeted removal efficiency for pollutants such as sulfur oxides, nitrogen oxides, mercury, and acid gases.
Proper air pollution control and flue gas management not only reduce harmful emissions but also help industries maintain legal compliance, avoid costly penalties, and improve community relations. As regulations continue to evolve and air quality standards become stricter, investing in modern, energy-efficient, and high-performance air pollution control solutions has never been more crucial for sustainable industrial growth and protecting public health.
Many industries—including power plants, cement manufacturing, steel mills, and chemical processing facilities—require high-efficiency electrostatic precipitators (ESPs) to control industrial emissions and particulate matter due to their use of fossil fuels, which results in the emission of harmful chemicals, dust, and flue gases into the atmosphere. The effective operation and design of an electrostatic precipitator rely on several essential components, each playing a critical role in efficient air pollution control, particulate collection, and environmental compliance:
These are the fundamental components and subsystems of an electrostatic precipitator:
The diagram above illustrates the position and operation of each critical component in an industrial electrostatic precipitator. An alternating current (AC) supply is directed to the precipitator's control cabinet, where the voltage is increased by a high-voltage transformer and then rectified (converted) by a diode within the rectifier unit. This vital process transforms AC current into direct current (DC), which is then delivered to the discharge electrodes. A reliable DC supply is essential for establishing the strong electric field needed for effective dust collection and particulate removal.
At this stage, flue gases containing suspended particulate matter, fine dust, and industrial pollutants pass through the zone between the discharge electrodes and collecting plates. The gas stream is subjected to an intense electrical field, which ionizes the particles. The ionized particles, which now have a charge of opposite polarity to the collecting electrodes, are attracted to and adhere to the collecting plates or tubes. Over time, these dust particles accumulate on the plates and are periodically dislodged, falling into the hopper below, from which they are efficiently removed and discharged as collected waste. This process delivers high collection efficiency even for submicron particles, making ESPs one of the most effective particulate control devices.
The discharge electrodes in electrostatic precipitator designs are typically composed of thin copper wires, which are welded and annealed for improved electrical conductivity and durability. These vertically suspended wires generate a substantial corona discharge when energized with high-voltage DC. The principal function of these electrodes is to create a strong electrostatic field within the clean air chamber that ionizes particles present in flue gas streams. The collecting electrodes or plates, often made from rigid steel or other conductive materials, serve as the surface for particle adhesion and removal, further optimizing filtration performance and promoting consistent air quality in emissions control systems.
Rapper coils, also referred to as magnetic impulse gravity impact rapper coils (MIGI), perform a critical cleaning function in modern ESP air pollution control systems. They impart a strong shearing or vibrational force to the collecting plates and electrodes, effectively dislodging accumulated dust, ash, fly ash, smoke, and sticky particulate contaminants. The vibrations produced by rapper coils are powerful enough to release even hardened and caked particles, ensuring maximum efficiency in dust removal and minimizing the potential for re-entrainment in the cleaned gas stream. For applications with especially sticky or adhesive dust, water spray nozzles are sometimes integrated to assist the cleaning process and maintain optimal operational efficiency.
This automated cleaning mechanism reduces maintenance downtime and supports continuous operation of electrostatic precipitators in industrial processes with variable gas flows and particle loads.
The transformer rectifier (TR) unit is an integral part of ESP design, serving to convert the standard AC voltage supplied to the electrostatic precipitator into the high-voltage DC current necessary for efficient particle charging. By generating a stable and adjustable DC voltage (often up to 100 kV), the TR unit ensures a continuously strong electrical field across the discharge and collecting electrodes. This negative electrical field imparts a strong negative charge to dust and particulate contaminants within flue gases, facilitating their migration to the positively charged collecting plates. Effective voltage regulation and power supply stability are paramount to ensure consistent particle collection and emission reduction, especially in systems subject to fluctuating loads or harsh industrial environments.
The hopper in an electrostatic precipitator system is an inverted pyramidal container specifically engineered for efficient collection and storage of particulate matter. As dust accumulates on the collecting electrodes following the ionization and precipitation processes, the rapper coils periodically dislodge it, causing the particles to fall into the hopper below. The hopper’s design supports easy evacuation of ash, dust, and other collected pollutants—either manually or with automated discharge mechanisms. Mounted vibrators on the hopper walls prevent the formation of dust bridges and promote uninterrupted discharge, significantly reducing the risk of blockages or buildup during high-volume operation. Ensuring proper dust handling and disposal in the hopper is key for safe, environmentally responsible particulate control.
When designing an electrostatic precipitator for industrial emission control, it is crucial to consider factors such as gas flow rate, particle size distribution, required collection efficiency, system voltage and power requirements, and space constraints. Advanced ESP designs also focus on optimizing the spacing between electrodes, selecting materials resistant to corrosion and high temperatures, and ensuring ease of maintenance and part replacement to minimize downtime. Control systems with real-time monitoring and automation can further improve electrostatic precipitator efficiency, facilitate regulatory compliance with air quality standards, and reduce operating costs over the system's lifecycle.
Modern ESPs are often selected based on specific process conditions, the type of pollutant to be controlled (such as fly ash, cement kiln dust, or chemical mists), energy consumption, and local emission regulations. A thorough understanding of these parameters ensures that the system will effectively reduce particulate emissions, protecting both workplace safety and the surrounding environment.
An electrostatic precipitator, also known as an electrostatic air cleaner, is designed to purify air emitted from industrial chimneys. Flue gases generated by the combustion of solids in industrial processes contain harmful pollutants that are dangerous to both human health and the environment. It is essential to remove these pollutants from the air released by industrial chimneys.
To achieve this, an electrostatic precipitator is installed between the furnace and the chimneys. It captures particulate matter from the flue gases, effectively removing pollutants and releasing cleaner, less harmful gases into the atmosphere.
Electrostatic precipitation operates by generating an electrostatic force that ionizes the particles in the flue gas. It involves two types of electrodes: a positive electrode, typically in the form of plates, and a negative electrode, usually consisting of mesh wire. These electrodes are arranged vertically and alternately within the precipitator.
The negative electrode is connected to the negative terminal of a DC voltage supply, while the positive electrode is connected to the positive terminal. To enhance the negative charge on the negative electrode, the positive terminal may be occasionally grounded. The spacing between the DC voltage supply, the negative electrode, and the positive plate is carefully adjusted to maintain a high voltage gradient. This setup ionizes the air between the negative electrodes and the adjacent positive plates, creating a corona discharge that surrounds the electrodes and establishes a negatively charged environment.
The area between the electrodes becomes fully ionized, resulting in a high concentration of free electrons and ions. The electrostatic precipitation process occurs within a metallic container, which has an inlet for flue gas and an outlet for clean, pollutant-free gas. As the flue gas enters the precipitator, dust particles are captured by the free electrons and ions. These particles become negatively charged and are attracted to the positively charged plates through electrostatic forces.
Once the negatively charged dust particles adhere to the positive plates, the excess free electrons are removed from the plates, and the particles fall off due to gravity. The precipitator includes hoppers that collect the dust particles from the collecting plates. Clean air is then discharged from the outlet into the atmosphere. Additionally, water sprays are used at the top of the precipitator to facilitate the rapid removal of dust particles from the plates.
In some systems, electrostatic precipitators are paired with denitrification units to remove harmful air pollutants like nitrogen dioxide and sulfur dioxide. These precipitators are often marketed as air purifiers or cleaners, serving as alternatives to traditional furnaces in various industries. While they prevent bacterial growth, the plates can be challenging to clean and may generate ozone or nitrogen oxides. Special filters are used to address these issues, and soak-off cleaners are available to ensure thorough removal of dust particles.
Regular and constant use of an electrostatic precipitator can lead to performance issues, which may arise from operational errors or quality problems. Proper maintenance is crucial for maintaining the efficiency and effectiveness of an electrostatic precipitator (ESP). Many performance issues can be prevented with careful planning and regular inspections.
If flue gas is introduced into the chamber at an excessively high rate, dust particles can accumulate in the electric field, leading to the formation of dust masses. This accumulation can make it difficult to remove particulate matter from the gas effectively.
The distribution of air flow significantly impacts the performance of the precipitator. Efficiency is higher in areas with low air flow, where dust removal occurs more rapidly. In contrast, areas with high air flow experience reduced efficiency due to the effects of high-speed smoke compared to low-speed smoke.
The efficiency of a precipitator is influenced by the specific resistance of the dust particles. For optimal collection, the specific resistance should be between 10,000 and 10,000 Ω·cm. If the specific resistance is too low, particles may move and escape through the outlet with the gas stream, reducing efficiency. Conversely, if particles are too large, they may not escape. To address this, it is necessary to vibrate the dust particles effectively, ensuring they are retained by the device for proper purification.
In the operation of negative pressure of dust collection air leakage will be a cause to produce secondary dust flying. Due to air leakage the smoke speed of the gas increases which results in the short residence time of the flue gas in the device. Air leakage also decreases the temperature of the flue gas that may lead to condensation and even corrosion.
The efficiency of dust removal increases when the temperature of the flue gas is between 110-130°C. At higher temperatures, the specific resistance of the dust particles decreases, the viscosity reduces, and the gas flow speed increases, which can lead to lower dust removal efficiency. Conversely, if the temperature is too low, humidity rises, ionization weakens, corona discharge may close, and dust removal efficiency decreases. Generally, the optimal flue gas flow rate is between 0.8 and 1.2 m/s.
High soot concentration increases the amount of dust particles in the electric field. Excessive soot concentration can lead to corona discharge closure, preventing current from passing through the electric field and reducing the precipitator's efficiency. If the flue gas has high soot concentration, it should be pretreated. The soot concentration in the flue gas should be kept below 5 g/m³.
Dust accumulation can lead to the complete failure of an ESP system. It is crucial to keep the charge plates, hopper, and rectifier clean and regularly checked. Regular maintenance is essential to avoid system failures or operational shutdowns. Neglecting the cleanliness of the ESP can undermine its effectiveness and expose companies to fines for inadequate pollution control.
Rapper coils play a critical role in the cleaning process by providing vibrations to remove buildup on collection plates or wires. Failure of the rapper coils can result in excessive buildup on the collection plates, reducing their efficiency and ability to capture charged particles. If not addressed, this buildup can eventually cause the system to stop functioning.
Electrostatic precipitators come in various types to meet specific functional requirements and economic considerations. Below, we explore the different types of electrostatic precipitators and their respective applications in detail.
Electrostatic precipitators come in various types to meet specific functional requirements and economic considerations. Below, we explore the different types of electrostatic precipitators and their respective applications in detail.
Plate Wire Precipitator - Plate wire electrostatic precipitators are used with boilers, paper mill incinerators, and basic oxygen furnaces. In this type of precipitator, the flue gas flows between the metal sheets that are placed parallel to each other and have high voltage electrodes.
The electrodes are hung in between the plates or supported by a rigid frame. Gas flows horizontally from vertically placed plates. As it flows, it passes through each wire in the arranged order. Plate wire electrostatic precipitators are used for large volumes of gas.
Flat Plate Precipitator - Flat plate precipitators are used to increase the surface area for particle collection and provide a strong and increased electrical field. Since corona cannot be produced on its own in flat plate electrostatic precipitators, corona producing electrodes are placed behind and ahead of the collecting electrodes. Flat plate precipitators can be operated with little or no corona current flowing from ionized particles. They can be used for particles that have high resistivity but are small in diameter. Fly ash is captured and collected by flat plate electrostatic precipitators.
Tubular electrostatic precipitators feature tubes arranged in parallel, with high voltage electrodes running along their axes. These tubes can be configured in various shapes, such as circular, square, or honeycomb, and the gas can flow either upward or downward through them. Tubular precipitators are single-stage units, meaning that all the gas passes through the tubes without any leakage.
Plate electrostatic precipitators, on the other hand, are more commonly used. They are particularly effective in handling wet or sticky particulate matter because they can be tightly sealed to prevent leakage. While tubular precipitators are ideal for controlling hazardous gases, plate precipitators offer versatility and reliability for a wider range of applications.
Dry electrostatic precipitators are designed to collect particulate matter from dry environments. Similar to rapper coils, these precipitators periodically vibrate to dislodge dust particles from the collector plates and discharge electrodes, directing the dust into a collection hopper. However, these vibrations can occasionally release small particles back into the air stream. Dry precipitators are generally not effective at capturing submicron particles and are primarily used for collecting ash or cement.
Wet electrostatic precipitators are designed to remove pollutants from wet gas streams, such as resin, oil, tar, and paint. They utilize a continuous water spray to collect dust particles from the gas. At the inlet of the precipitator, a fine mist of water and air conditions the particulate matter for collection. High voltage corona electrodes and collection tubes charge and separate the particles. The collected solid materials and liquid from the spray are then drained out of the precipitator.
Wet electrostatic precipitators are particularly effective for capturing wet, sticky, flammable, and high-resistivity solids and can capture smaller particles compared to dry precipitators. They typically have a tubular shape and are more costly than dry precipitators. Given their reliance on water, these precipitators are constructed from corrosion-resistant materials. The collected particulate matter is removed as a slurry, which is flushed from the system.
Most electrostatic precipitators are single-stage devices. These precipitators operate at very high voltages to charge and collect particles. In a single-stage system, the electrodes and collecting plates are arranged parallel to each other and function in the same direction. Both the charging and collection processes occur within the same section of the precipitator.
Single-stage electrostatic precipitators can have either tubular or plate configurations and typically use rapping coils or a liquid film to remove the collected particles. The charging wires and collection plates are positioned close together in the same area of the precipitator. This contrasts with two-stage electrostatic precipitators, where the charging and collection processes are separated into different sections.
Two-stage electrostatic precipitators are arranged in series rather than in parallel. This configuration allows particles to spend more time being charged and reduces the likelihood of back corona. They are designed to handle smaller particles and are often used as air purifiers in conjunction with air conditioning systems. Two-stage precipitators are typically used for low-volume and smaller-scale applications.
The term "air pollution" is used so frequently that many of us believe we have a complete understanding of its meaning. Scientists and environmentalists have made so many predictions of the negative effects...
An air scrubber is an air purification system that removes particulate matter from the air through the use of moisture or by cooling or filtering the airstream as it enters the scrubber...
Oxidizers, or incinerators, are pieces of equipment used to treat waste gas or plant emissions that contain harmful pollutants by thermally decomposing them into simpler, many stable compounds...
Air filters are devices used to remove airborne particles, pollutants, and microorganisms hazardous to health and the ecosystem. In industrial facilities, air filters preserve the quality of products and materials and protect critical equipment from damage...
A baghouse is a pollution control device that uses tubes, envelopes, or cartridges to remove, capture, and separate dirt, particulate matter, and dust from the air of a manufacturing or processing facility. The main components of a baghouse are the media or bags used to filter the particles from the air as it passes through the system...
A central vacuum system is a cleaning mechanism that is built into a building for ease of use, access, and maintenance. Vacuum and pressure are created by a centrally located motor to remove dirt, dust, and debris...
A dust collection system is a system that removes particulate contaminants from the air in production facilities, workshops, and industrial complexes. The system cleans air by forcing it through a series of airtight filters...
Explosion-proof vacuums are vacuum systems that use compressed air, electricity, and cyclonic motion to prevent the ignition of gasses or vapors and operate at temperatures that will not ignite a possibly flammable atmosphere. Replacing motors with...
A HEPA filter is a high efficiency pleated air filter capable of capturing extremely small particulate matter down to particles that are the size of a micron (µ), or a micrometer, which is 1/1000th of a meter...
An industrial vacuum cleaner is a heavy duty piece of cleaning equipment designed to remove debris, industrial waste, construction refuse, and matter that remains after a manufacturing process or construction project...
A jet dust collector is a suction filtration unit that pulls dust ladened air into a filtration system that collects particulate matter and releases clean air. The filters of jet dust collectors are cleaned by compressed air that uses...
During the Industrial Revolution, when companies began producing high volumes of industrial waste like fine dust, wood dust, and other particles, an American, in 1852, S.T. Jones, applied for the first dust collector patents, a single bag filter...
Vacuum cleaners use suction to collect dirt, dust, waste products from industrial processes, and other debris for disposal, recycling, or reuse. They are mainly used for building maintenance and cleaning of industrial space...