Air Scrubber
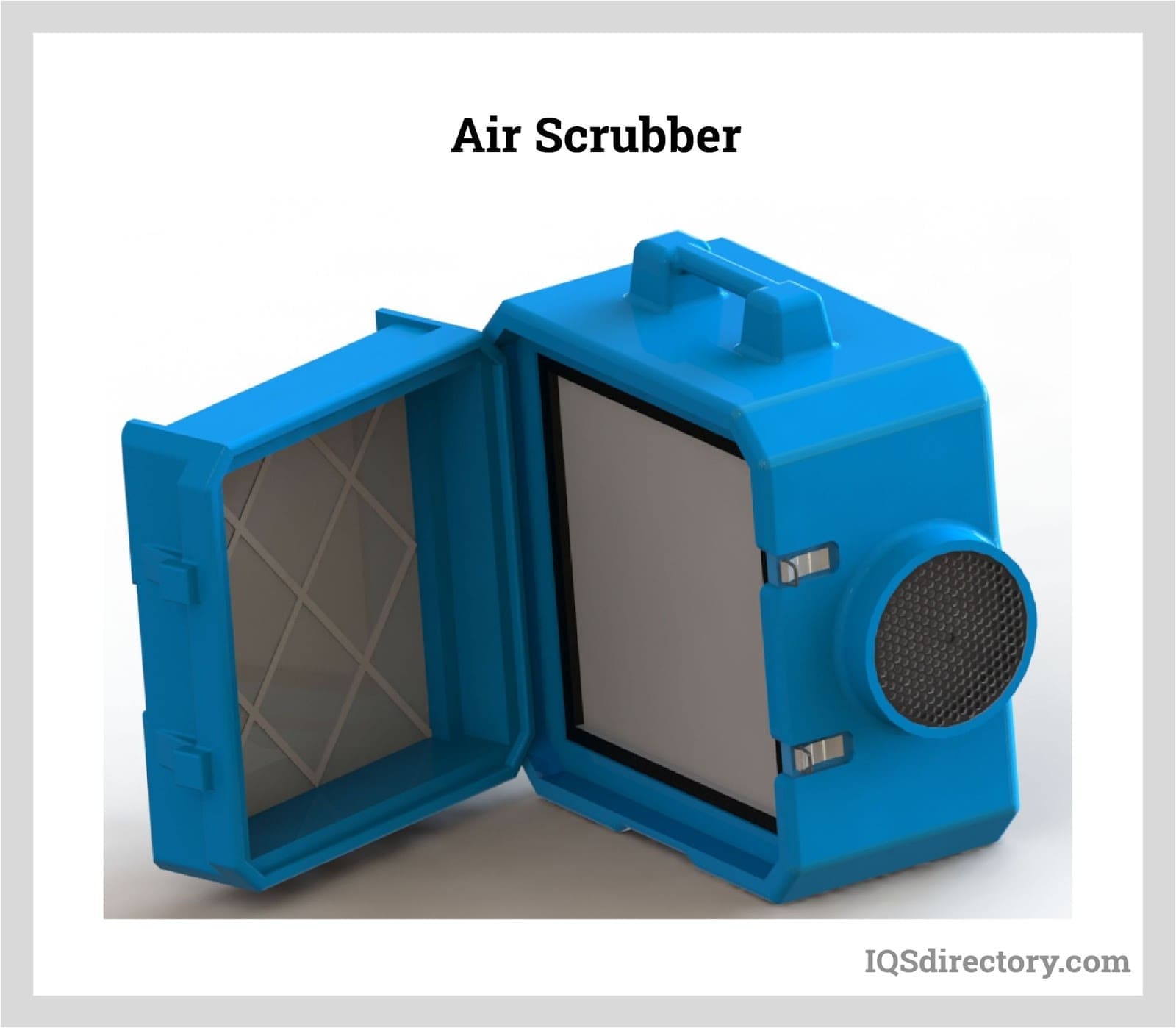
An air scrubber is a purification system designed to remove particulate matter from the air. It achieves this by using moisture or by cooling and filtering the airstream as it passes through the scrubber.
Please fill out the following form to submit a Request for Quote to any of the following companies listed on
This article will take an in-depth look at air pollution control equipment.
You will learn about:
The term "air pollution control equipment" refers to advanced systems used to curb the discharge of various solid and gaseous pollutants into the atmosphere, primarily originating from industrial emissions via exhaust stacks or chimneys. These systems are classified into two main categories: those that target acidic gas emissions and those designed to manage particulate matter emissions effectively.
Air pollution control technologies primarily function through three core methods:
Considering that operational conditions and environments vary substantially across different facilities, choosing suitable monitoring equipment or methodologies involves more complexities than merely comparing performance metrics and costs. Each facility and installation has specific monitoring needs, influenced by several critical factors.
These factors collectively assist in acquiring the monitoring equipment best suited for specific operational requirements.
One consequence of the Industrial Revolution was a significant rise in air pollution from the fuels burned in industrial processes. Additionally, as industries expanded, there was excessive exploitation of natural resources like wood, coal, water, and land.
By the mid-20th century, the adverse effects of unchecked industrialization became increasingly evident. For example, in 1948, severe air pollution in Donora, Pennsylvania, reached deadly levels, resulting in the deaths of 20 people and illnesses affecting 7,000 others. In 1952, London experienced "The Great Smog," a dense, choking fog caused by sulfur particles combined with coal-burning gases, leading to the deaths of 12,000 people and harming animals during the five-day event. In 1984, an air pollution disaster at the Union Carbide factory in Bhopal, India, resulted in the illness or injury of between 150,000 and 600,000 residents and the deaths of nearly 4,000 workers.
In response to these devastating incidents, governments worldwide introduced various clean air regulations. For instance, the UK government passed the first Clean Air Act in 1956, which prohibited coal burning in cities. Similarly, the United States enacted its Clean Air Act in 1970.
Following the enactment of clean air legislation, companies began adopting various pre-existing air pollution control technologies. One such technology was the electrostatic precipitator, initially developed by German mathematician Dr. M. Hohlfeld in 1824. Approximately 80 years later, in 1907, Professor Frederick Gardner Cottrell patented the first mass-producible electrostatic precipitator. At that time, this device was used to capture, treat, and remove sulfuric acid.
The Clean Air Act of 1990 required regular monitoring of specific pollutants from various stationary sources. Monitoring equipment is vital for complying with legal requirements and regulatory standards. This equipment collects data on particulate matter and gaseous pollutants, which is essential for auditing and obtaining licenses for new and existing facilities. Additionally, emissions monitoring evaluates the effectiveness of pollution control systems and ensures health and safety within a facility.
The dedication of many individuals has led to a substantial reduction in VOC and HAP emissions in recent years. However, with global climate change highlighting carbon emissions as a major issue, policymakers and environmentalists are collaborating to develop legislation aimed at significantly cutting carbon emissions. In response to these new and forthcoming regulations, manufacturers may need to explore alternatives to traditional incinerators and oxidizers. Potential alternatives include filtering system components such as mist collectors, wet scrubbers, dry scrubbers, and electrostatic precipitators.
As sustainability and pollution control concerns increase, almost every industrial operation now uses some form of pollution control system to reduce emissions of volatile organic compounds (VOCs), hazardous air pollutants (HAPs), and greenhouse gases (GHGs). Regular inspections, certifications, and government regulations mandate and enforce the use of these systems.
Air pollution control equipment manufacturers offer a wide array of solutions customized to the unique conditions and environments of their clients' installations.
Another type of air pollution control equipment is the carbon adsorber. It filters polluted air as it passes over or through an activated carbon bed. The carbon bed captures and retains VOCs from the air, releasing only clean air.
Carbon absorbers can utilize a range of processes and materials, including lithium hydroxide, sodium hydroxide, amines (such as monoethanolamine), minerals, and zeolites (e.g., serpentinite).
It is an air purification system that filters or cools the airstream as it enters the scrubber to remove particulate matter from the air. Wet and dry air scrubbers are distinguished by how they remove particles. An air scrubber's main purpose is to purify the air after it has been polluted with harmful gasses, chemicals, fumes, and pollutants.
Wet air scrubbers use liquid solvents to eliminate pollutants, whereas dry scrubbers rely on solid materials. Both types effectively remove odors and gas contaminants from industrial exhaust streams. Wet air scrubbers typically achieve higher pollutant removal rates compared to dry scrubbers. They are essential for preventing pollutants from entering the outside air and are commonly used in industrial manufacturing and wastewater treatment facilities. Available in various shapes and sizes, wet air scrubbers are adaptable to any industry that emits air pollutants.
Wet air scrubbers function by utilizing water or a water-based solvent to absorb contaminants from the air. Contaminated gas enters the scrubber from the bottom, moves upward through a packed bed, and interacts with downward-spraying solvent. Before leaving the scrubber, the gas passes through a mist eliminator to capture any residual droplets. The contaminants are trapped in the solvent droplets. The liquid solvent, contained in a metal or composite vessel, interacts with the gas stream as it flows through. The scrubber releases clean gas while the solvent absorbs the pollutants.
The effectiveness of a solvent in removing impurities is largely determined by its composition, especially its electric charge. The solvent’s charge—whether positive, negative, or neutral—affects its capacity to bond with various inorganic contaminants.
Dry air scrubbers tackle specific contaminants by quickly spraying chemicals into the exhaust stream. The reaction between the chemicals and pollutants causes the contaminants to precipitate out of the air stream. These scrubbers are environmentally friendly because the collected particles and chemicals are either incinerated by the heat of the air stream or captured in a filter.
A dry air scrubber eliminates the need for wastewater removal or storage, making it a cost-effective solution. Dry scrubbers are mainly employed to capture solvents and acidic vapors.
These filterless devices remove solid, droplet-shaped, gaseous, or liquid particles from the air using an electric charge. It is a tool for reducing air pollution that filters pollutants out of the smokestacks of factories, manufacturing facilities, and power plants. The electrostatic precipitator collects smoke or gas as it exits a burner or furnace by passing the gas or smoke over wires or plates. This process gives the gas or smoke a static charge, which is then collected on a second plate with a negative charge, where the pollutant particles are held. With only a small quantity of electrical energy, electrostatic precipitators can be precisely tuned to meet the requirements of the pollution circumstances.
Most businesses rely on fossil fuels for manufacturing, which produces smoke containing soot, ashes, and unburned CO2. Electrostatic precipitators (ESPs) use an electric charge to remove these pollutants from the smoke, releasing clean air into the atmosphere. Removing these harmful particles is crucial due to their potential risks to human health, the environment, and infrastructure.
Electrostatic precipitators eliminate particulate matter from polluted air, such as dust, smoke, soot, ashes, and fumes.
Oxidizers utilize thermal decomposition, also known as incinerators, to treat waste gasses or plant emissions that include dangerous chemicals. The preheated waste gas is oxidized in oxidizers, which resemble burners or reactors and operate at temperatures of up to 1832 °F (1,000 °C).
Thermal oxidizers convert hazardous air pollutants (HAPs) and volatile organic compounds (VOCs) into carbon dioxide and water. In the combustion chamber, a high-draft fan introduces air to support the combustion of flammable substances and ensure complete burning. This air also dilutes the waste gas stream to safe levels. To ensure safe operation, the lower explosive limit (LEL) in the combustion chamber should not exceed 25%, unless a concentration monitoring system permits up to 50%. Exceeding this limit could cause explosions in the chamber or vent system.
To ensure safe operation, the concentration of combustible gases in the combustion chamber should not exceed 25% of the lower explosive limit (LEL). In certain cases, upstream monitoring may allow deviations of up to 50%. The waste gas stream is ignited in the chamber after being diluted with air, using a guided burner or igniter. Due to the dilution, the heat produced is minimal. If the combustion is not self-sustaining, additional auxiliary fuel is added to maintain the necessary chamber temperatures.
Some oxidizers can operate continuously without additional fuel. For instance, catalytic oxidizers use catalyst media—substances that speed up chemical reactions without being depleted—to drive the process. This results in lower fuel consumption and reduced operating temperatures compared to thermal oxidizers. Furthermore, air-to-air heat exchangers can improve energy efficiency by preheating incoming air with the hot, treated exhaust gas from the system's output.
Another method to increase the temperature inside the chamber while minimizing extra fuel consumption is to harness the exhaust heat from the chamber. If the heat energy from the exhaust gases were to be released immediately, it would be wasted. Instead, heat exchangers transfer heat from the incoming air stream to the outgoing exhaust stream. This reduces the amount of heat required to ignite the preheated air entering the chamber. Additionally, ceramic media within the combustion chamber can be used to further warm the air.
The ceramic media absorbs heat from the previous reaction and transfers it to the incoming gas stream.
Exhaust gases are released into the atmosphere through a stack, which is designed to facilitate the natural flow of air from the combustion chamber. Sample-taking probes are arranged along the stack to collect data, and emission monitoring systems analyze these samples.
Additional downstream or auxiliary equipment is necessary to handle the potential presence of acid-forming substances and particulate debris in the waste gas stream. Wet scrubbers, in particular, are commonly used to remove acid vapors.
Wet electrostatic precipitators (WESPs) use a powerful electric field to control particulate matter by charging and collecting particles and droplets on a collection surface. In this method, a discharge electrode imparts a negative charge to the particles as the gas stream flows through the collection section. This negative charge attracts the particles to the grounded surface of the collection electrode. Operating at low-pressure drops, WESPs effectively remove over 90% of the collected material.
Catalytic oxidizers use high heat or elemental additions to burn VOCs.
Thermal oxidizers remove volatile organic compounds (VOCs) by treating contaminated air with platinum or palladium. This process breaks down the VOCs into non-toxic byproducts such as nitrogen and oxygen.
Both processes can be either regenerative or recuperative. This capability allows companies to recycle heat and reduce costs, making it beneficial for industrial manufacturing facilities across various sectors—such as agriculture, mining/geochemistry, pharmaceuticals, and automotive—that face significant expenses from operating pollution control systems.
Regenerative thermal oxidizers (RTOs) utilize ceramic heat transfer beds to recover up to 90% to 95% of the energy emitted during the oxidation process. The procedure begins with directing the incoming waste gases through control valves to heat them from ambient temperatures to near-combustion levels. As the gases absorb heat, the ceramic bed cools down, reducing heat transfer efficiency. The control valves then redirect the flow to a different heated ceramic bed. Meanwhile, the cooled ceramic bed undergoes a heat regeneration phase using the exhaust gases to prepare it for the next heating cycle.
In contrast, recuperative oxidizers warm-up polluted gas in an energy recovery chamber using shells, tubes, plates, or another type of traditional heat exchanger. By using the energy released by oxidized VOCs, they can sustain themselves. Through the heat exchanger, the operation begins by raising the temperature of the incoming waste gas. After burning, the mixture of waste gas and the air is released to the stack after passing through the other side of the heat exchanger. Next, the heat exchanger increases the intake temperature by recovering heat from the exhaust. The two types of heat exchangers are plate and shell and tube. Thermal oxidizers with plate heat exchangers have higher thermal efficiency at lower operating temperatures and need less capital investment. On the other hand, heat exchangers with shells and tubes are favored at higher operating temperatures.
The simplest thermal oxidizers are direct-fired thermal oxidizers (DFTOs), often called afterburners. These units do not employ preheating or heat recovery methods when introducing the waste gas stream into the combustion chamber. Instead, the hot air remains in the firing chamber for a set period, known as the residence or dwell time, before exiting.
When the desired thermal destruction rate efficiency (DRE) is obtained, the firing chamber operates at 1800 °F to 2200 °F (982-1204 °C) with airflow rates of 500 cu ft to 50,000 cu ft. Emissions are controlled during this time. Safe air and water vapor are released once the DFTO has processed the emissions. The least amount of capital is required to achieve emission compliance with DFTOs, which have a 99% efficiency rate for destroying hydrocarbons.
This thermal oxidizer uses specially created non-catalytic ceramic beds with good thermal and flow dispersion qualities. Unlike other thermal oxidizers, this one premixes the air and waste gasses before introducing them to the combustion chamber. Burners or earlier processes preheat the combustion. When the air and gas mixture enters the combustion chamber, the high temperatures cause them to ignite. Burners and electric heaters are used to heat ceramic media to operational temperatures when the exothermic reaction of the air and gasses is insufficient.
Mist collectors, also known as mist or moisture-eliminator filters, are air pollution control devices designed to remove moisture and vapor from gas streams, including smoke, oil, and mist. These collectors use fine mesh filters to separate liquid droplets from the gas. The collected droplets are then gathered in a separate chamber for processing, with the potential for recovery and reuse.
With some types delivering 99.9% efficiency for particles with a diameter of less than 0.3 mm, mist collectors maintain high filtration efficiencies for submicron liquid particles. Mist collectors can process caustic and acidic gas streams. However, they cannot process gas streams with large particulates because they could clog the collector's filter. Additionally, they are not employed in applications where the temperature exceeds 120 °F (48 °C).
Cyclones, also referred to as cyclone dust collectors, are air pollution control devices that remove dry particulate matter from gaseous pollutants without relying on filtration media. Instead, they use centrifugal force. In a cyclone, gas streams enter and spiral through a cylindrical chamber. This swirling motion propels larger particles against the chamber wall, reducing their inertia and causing them to drop into a collection hopper below for further processing and disposal. The cleansed gas then exits the cyclone and continues upward.
The efficiency of cyclones varies with particle size; larger particles are removed more effectively than smaller ones. To capture the smaller particles that cyclones can't effectively handle, additional filtering devices such as baghouses are often used in conjunction with cyclones in air pollution control systems.
Selective Catalytic Reduction (SCR) systems, also known as catalytic reactors, are widely employed to reduce nitrogen oxide (NOx) emissions from fossil fuel combustion in industrial settings. In these systems, industrial exhaust and pollutants are first treated with ammonia, which reacts with NOx molecules to produce nitrogen and oxygen. Catalytic reactors use various catalysts to facilitate the breakdown of remaining gaseous pollutants, allowing for further combustion and reduction. A common example of catalytic reactors is the three-way catalytic converter used in automotive exhaust systems, which reduces NOx, carbon monoxide (CO), and volatile organic compounds (VOCs) in engine emissions.
SCR systems can achieve over 90% efficiency in reducing and removing NOx, and can attain 99.99% efficiency for other gaseous pollutants with less energy than incinerators. Despite their high efficiency, SCR systems are not suitable for all applications due to their high cost and their inability to handle emissions and exhaust that contain particulates.
Biofilters utilize microorganisms, such as bacteria and fungi, to reduce and remove water-soluble chemicals from air pollution. Unlike incineration systems, which produce byproducts like NOx and CO, biofilters decompose gaseous pollutants such as VOCs and organic HAP without generating harmful byproducts. These filters can achieve over 98% efficiency in eliminating pollutants from industrial emissions and exhaust.
Industrial air pollution control equipment is crucial and must be prioritized. Almost every industry contributes to environmental pollution through its operations. Sectors such as petroleum, oil, coal, metal, chemical, and waste management are among the major contributors to toxic emissions.
Industrial activities—including raw material extraction, product manufacturing, site and machinery maintenance, and transportation—inevitably generate pollution. Burning fossil fuels releases volatile hydrocarbons, while the use of wood and coal as fuel results in carbon dioxide and sulfur dioxide emissions. Additionally, automobiles contribute significantly to harmful carbon emissions. Each industrial process emits pollutants that contaminate the air, soil, or water.
Non-industrial air pollution control technologies are also used in homes, cars, and other mobile environments. For example, home air conditioners often feature filtration systems that remove impurities such as pet dander, allergens, mold spores, and dust.
Additionally, precision filtration systems help reduce vehicle emissions from engines, exhaust systems, and air conditioning units.
Many facilities use continuous emissions monitoring systems (CEMS) to track, manage, and report emissions. These systems utilize various instruments to measure the concentration of particulate matter and gaseous chemicals at specific points, often in stacks or ducts. They also assess physical properties of waste gas streams, such as opacity. The New Source Performance Standard (NSPS) and the New Source Review (NSR) require emissions monitoring at major pollution sources, and certain EPA regulations also mandate continuous emissions monitoring.
In addition to parametric monitoring, continuous emissions monitoring helps technicians comply with Compliance Assurance Monitoring (CAM) regulations.
Parametric monitoring measures emissions by tracking key parameters related to the operation of process or air pollution control equipment. This method uses pollutant emission levels and monitored control parameters to assess compliance. The adoption of CAM regulations has increased the acceptance of parametric monitoring, as it offers a more flexible and cost-effective approach to demonstrating compliance.
An air scrubber is a purification system designed to remove particulate matter from the air. It achieves this by using moisture or by cooling and filtering the airstream as it passes through the scrubber.
Air pollution refers to any unwanted particles in the air that contaminate the environment and harm the health of living organisms. These particles can be toxic and may lead to a range of serious health issues, including...
Oxidizers, also known as incinerators, are devices used to treat waste gases or emissions from industrial processes by thermally breaking down harmful pollutants into simpler, more stable compounds.
Air filters are devices used to remove airborne particles, pollutants, and microorganisms hazardous to health and the ecosystem. In industrial facilities, air filters preserve the quality of products and materials and protect critical equipment from damage...
A baghouse is a pollution control system designed to remove, capture, and separate dust, particulate matter, and dirt from the air in manufacturing or processing facilities. It utilizes filters in the form of tubes, envelopes, or cartridges. The primary components of a baghouse are the filter media or bags, which trap particles as air flows through the system.
A central vacuum system is a cleaning mechanism that is built into a building for ease of use, access, and maintenance. Vacuum and pressure are created by a centrally located motor to remove dirt, dust, and debris...
A dust collection system is designed to remove particulate contaminants from the air in production facilities, workshops, and industrial complexes. It cleans the air by directing it through a series of airtight filters.
Explosion-proof vacuums are designed to safely handle potentially flammable environments. They use compressed air, electricity, and cyclonic motion to prevent the ignition of gases or vapors. These vacuums operate at temperatures that avoid igniting a potentially explosive atmosphere, and their motors are replaced with specialized, safety-certified components to ensure safe operation.
A HEPA filter is a high-efficiency, pleated air filter designed to capture very small particles, down to the size of a micron (µ), which is 1/1,000th of a meter.
An industrial vacuum cleaner is a robust cleaning device engineered to handle debris, industrial waste, construction refuse, and residual materials left over from manufacturing or construction activities.
A jet dust collector is a suction filtration unit that draws dust-laden air into a filtration system, capturing particulate matter and expelling clean air. The filters in jet dust collectors are cleaned using compressed air, which helps maintain their effectiveness.
During the Industrial Revolution, as industries started generating large amounts of industrial waste, including fine dust and wood particles, S.T. Jones from America applied for the first dust collector patents in 1852. His invention was a single-bag filter designed to address these issues.
Vacuum cleaners employ suction to gather dirt, dust, waste products from industrial processes, and other debris for disposal, recycling, or reuse. They are primarily used for maintaining and cleaning industrial spaces.