Aluminum Coil
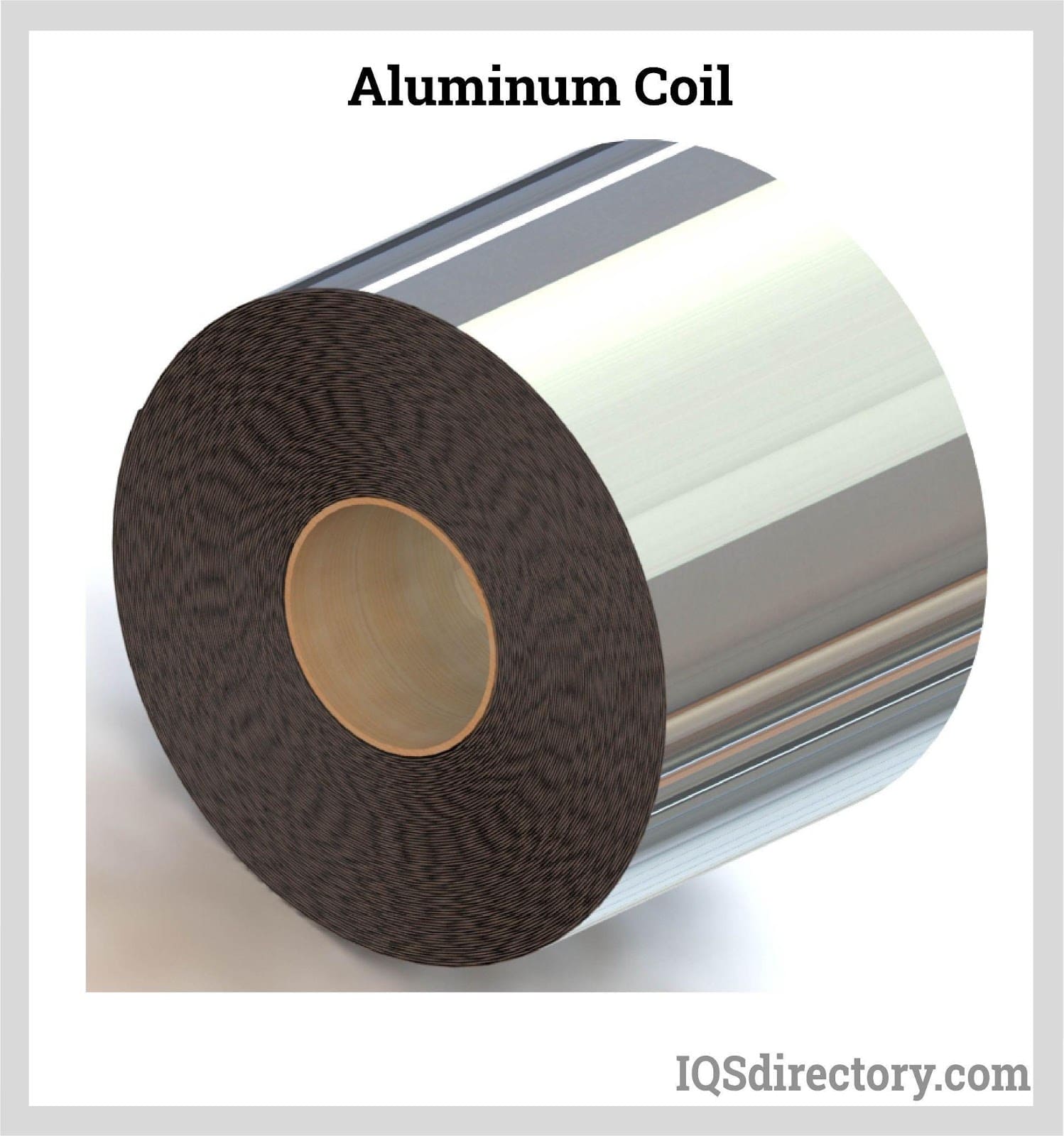
The term "aluminum coil" describes aluminum that has been flattened into sheets where their width is significantly higher than their thickness and then "coiled" into a roll. Stacks of individual aluminum sheets are difficult to...
Please fill out the following form to submit a Request for Quote to any of the following companies listed on
This article will provide you with everything you need to know about aluminum 1100 and its use.
You will learn:
Aluminum 1100 stands as the most pliable of the aluminum alloys, which makes it perfectly suited for a wide spectrum of industrial and domestic uses. It can undergo both cold and hot work processes, but is primarily formed using techniques such as spinning, stamping, forging, and drawing. Belonging to the 1000 series, Aluminum 1100 is composed of 99% aluminum, with the remaining 1% made up of trace elements like copper, iron, magnesium, manganese, silicon, titanium, vanadium, and zinc. Its softness results in smooth work hardening, allowing for easier shaping and forming.
The excellent workability of Aluminum 1100 is ideal for producing intricate and complex shapes. It is frequently utilized in the food processing and chemical industries due to its favorable characteristics. Moreover, Aluminum 1100 possesses the highest thermal conductivity among aluminum alloys and demonstrates significant electrical conductivity. Its outstanding resistance to corrosion and attractive, polished finish make it highly sought after for decorative purposes.
Available in sheets, plates, wire, and various thicknesses of foil, Aluminum 1100 remains a versatile material in the manufacturing sector.
As with all types of aluminum, aluminum 1100 comes in various forms—or tempers—defined by the changes in the types and amounts of alloying elements added and their overall aluminum content. The distinguishing feature of all variants of the 1100 series is the extraordinary purity of their aluminum content, commonly used in applications where high workability and corrosion resistance are vital. This purity makes aluminum 1100 highly malleable, offering significant advantages in manufacturing and fabricating processes across multiple industries, from industrial production to food packaging and electrical applications.
Aluminum 1100 is the purest of all commercial aluminum alloys, possessing a minimum aluminum content of 99%. The nominal trace elements that make up the other 1% are carefully controlled, resulting in a soft, highly ductile, and workable material. Despite its relatively low strength, aluminum alloy 1100’s exceptional formability, excellent weldability, and impressive corrosion resistance make it a popular choice for intricate forming operations and deep drawing processes.
Of the various aluminum alloys, aluminum 1100 is ideal for cold working due to its exceptional ease of fabrication. It can be processed using virtually all standard forming techniques, including bending, drawing, spinning, stamping, and rolling. This flexibility allows manufacturers to produce a wide variety of shapes and products such as billets, coils, aluminum sheets, ingots, and foil, all derived from melting and casting raw aluminum. Unlike heat treatable alloys like 6061 or 7075, aluminum 1100 is non-heat treatable, which underscores its inherent softness and superb malleability. Its moderate strength and superior surface finish also make it ideal for applications such as heat exchanger fins, chemical equipment, and architectural trim, where appearance, corrosion resistance, and workability are essential.
Industries such as HVAC, signage, cookware, and reflectors often select aluminum 1100 for its high thermal conductivity and ability to be anodized for enhanced surface protection. Additionally, its superior electrical conductivity leads to widespread use in electrical bus bars, transformers, and conductive components.
Properties of Aluminum 1100 | |||
---|---|---|---|
Properties | Conditions | ||
T (°C) | Treatment | ||
Density (x1000 kg/m2) | 2.71 | 25 | |
Poisson's Ratio | 0.33 | 25 | |
Elastic Modulus (GPa) | 70-80 | 25 | |
Tensile Strength (MPa) | 110 | 25 | H12 |
Yield Strength (MPa) | 105 | ||
Elongation (%) | 12 | ||
Reduction in Area (%) | |||
Hardness (HB500) | 28 | 25 | H12 |
Shear Strength (MPa) | 69 | 25 | H12 |
Fatigue Strength | 41 | 25 | H12 |
Thermal Expansion (10-6/°C) | 23.6 | 25 | |
Thermal Conductivity (W/m-k) | 218 | 25 | H18 |
Electric Resistivity (10-9 0-m) | 30 | 25 | H18 |
Aluminum alloy 1145 contains slightly more aluminum than alloy 1100, with a composition of 99.45%. This higher aluminum content boosts its electrical and thermal conductivity compared to the standard 1100 alloy, making it an excellent choice for electrical and heat transfer applications. Additionally, aluminum 1145 is chemically similar to alloy 1235, which is frequently used as an alternative for increased availability.
Aluminum 1145 is commonly specified for the production of cold-rolled aluminum foil and is widely used in packaging for food, pharmaceuticals, medical devices, and cosmetics. Due to its reflective surface and excellent barrier properties, aluminum 1145 foil is highly valued in the flexible packaging industry to protect products from moisture, light, and contaminants. In construction, this grade serves as a material for thermal, hydro, and sound insulation, leveraging its ability to reflect heat and sound waves efficiently. These properties also position aluminum 1145 as a preferred choice for producing transformer windings, cable wraps, and insulation products.
The superb purity of aluminum 1145, combined with malleability and corrosion resistance, makes it appropriate where contamination must be minimized. Furthermore, 1145 alloy is well-suited for light gauge, high-purity applications and can be processed using all major forming techniques such as rolling, stamping, and embossing.
Elements in Aluminum 1145 | |
---|---|
Elements | Content (%) |
Aluminum, Al | 99.45 (m) |
Copper, Cu | 0.05 |
Manganese, Mn | 0.05 |
Magnesium, Mg | 0.05 |
Zinc, Zn | 0.05 |
Titanium, Ti | 0.05 |
Silicon, Si + Iron, Fe | Remainder |
Specifications in Aluminum 1145 | |
---|---|
Specifications | |
ASTM Standards | B209 |
Finish | Standard Finishes |
QQA Standards | 1876 |
Temper | Standard Tempers |
Thickness | 0.0005 to 0.064 in |
Width | 0.375 to 60 in |
Density | 2.6-2.9 g/cm3 |
Elastic Modulus | 70-80 GPa |
Poisson's Ratio | 0.33 |
Aluminum 1199 stands out among the 1xxx series alloys as the highest purity option, offering an outstanding 99.99% aluminum content. Its extremely low density and unmatched purity are key contributors to the alloy's selection for advanced applications such as aerospace, scientific apparatus, and specialized electronics. In industries where strict control of contamination is essential—such as the food processing, chemical, and healthcare sectors—aluminum 1199 is sought after for equipment manufacturing, cookware, and pressure vessels. Its superior resistance to oxidation and atmospheric corrosion provides excellent long-term durability, even in aggressive environments.
The unrivaled electrical and thermal conductivity of 1199 aluminum makes it the benchmark choice for electrical conductors, capacitor foils, heat exchanger components, and sensitive instrumentation. Its abundance and cost-effectiveness, compared to less common specialty metals, explains its popularity for high-volume production where both cost savings and high-purity performance are crucial. Industries such as telecommunications, energy, and scientific research rely on aluminum 1199 in cable sheathing, cathode foils, and other precision applications where the highest purity and conductivity are desired. Alloys with such elevated aluminum content often find use as reference materials and calibration standards due to their predictable and consistent properties.
Elements in Aluminum 1199 | |
---|---|
Elements | Content (%) |
Aluminum, Al | 99.99 min |
Silicon, Si | 0.006 max |
Magnesium, Mg | 0.006 max |
Zinc, Zn | 0.006 max |
Iron, Fe | 0.006 max |
Copper, Cu | 0.006 max |
Gallium, Ga | 0.005 max |
Vanadium, Va | 0.005 max |
Manganese, Mn | 0.002 max |
Remainder (each) | 0.002 (each) |
Properties of Aluminum 1199 | ||
---|---|---|
Properties | Metric | Imperial |
Tensile strength | 115 MPa | 16700 psi |
Yield strength | 110 MPa | 16000 psi |
Poisson's ratio | 0.33 | 0.33 |
Elastic modulus | 62 GPa | 8990 ksi |
Shear modulus | 25 GPa | 3630 ksi |
Elongation at break (@tickness 1.60 mm/0.0630 in) | 5% | 5% |
Shear strength | 74 MPa | 10700 psi |
Hardness, Brinell (@load 500kg with 10.0mm ball) | 31 | 31 |
Thermal Conductivity | 25°C |
Aluminum 1100-H14 is recognized as a commercial-grade aluminum alloy that blends excellent formability with moderate strength and exceptional resistance to chemical and environmental corrosion. Its “H14” temper designation indicates that the alloy has been strain-hardened to a half-hard condition, optimizing its mechanical properties for sheet metal fabrication while retaining its signature malleability and ductility.
The H14 temper is particularly important in applications demanding both moderate strength and flexibility. In this state, aluminum 1100-H14 is often specified for use in architectural facades, signage, appliance panels, light reflectors, and heat exchanger fins. The balance of rigidity and workability means it is suitable for bending, rolling, and light forming while maintaining a high-quality surface finish.
In aluminum alloy nomenclature, the first digit following “H” identifies the method of strain hardening, while the second digit specifies the relative degree of hardening. For example, "H1" signifies strain-hardened only, and the "4" denotes half-hard; higher numbers represent increased hardness within the alloy family. It's important to note that the 1xxx aluminum series, including 1100-H14, is non-heat treatable—meaning mechanical properties are enhanced exclusively by cold working rather than by heat treatment, unlike alloys such as 6061-T6.
Beyond its renowned formability, 1100-H14 delivers high reflectivity, excellent electrical and thermal conductivity, and is easy to weld or braze. It meets stringent ASTM and other industry standards for quality and consistency, making it suitable for demanding applications that require both reliable performance and ease of fabrication.
When selecting between types of aluminum 1100 and their respective tempers, consider the intended application, required mechanical strength, formability, corrosion resistance, and conductivity. For buyers and engineers seeking a balance of low weight, durability, and versatility in non-heat-treatable aluminum alloys, the 1xxx series—especially 1100 in its various tempers—often provides an optimal solution.
Elements in Aluminum 1100-H14 | ||
---|---|---|
Element | Value | Condition |
Aluminum | 99.00% | H14 |
Copper | 0.05 - 0.2% | H14 |
Manganese | 0.05% | H14 |
Zinc | 0.10% | H14 |
Mechanical Properties of Aluminum 1100-H14 | ||
---|---|---|
Mechanical Properties | Value | Condition |
Bending Fatigue Strength | 50.0 MPa | H14 |
Elastic modulus | 69.0 GPa | H14 |
Hardness, Brinell | 32.0 [-] | H14 |
Plane-Strain Fracture Toughness | 22.0 35.0 MPa.√m | |
Poisson's ratio | 0.33 [-] | |
Shear modulus | 25.9 GPa | |
Tensile strength | 110.0 - 145.0 MPa | H14 |
Density | 2.71 g/cm3 |
Aluminum 1100, recognized for its excellent corrosion resistance and high thermal conductivity, is primarily made from bauxite—an abundant sedimentary rock with a high concentration of aluminum oxide, typically between 45% and 60%. The production of aluminum 1100 starts with the extraction of aluminum compounds from bauxite, separating impurities like iron oxide, silica, and other trace metals using a refined industrial process. As a highly sought-after material in the aluminum alloys market, understanding its detailed manufacturing process is essential for both manufacturers and customers seeking quality, purity, and versatility in their aluminum products.
Bauxite ore can present as hard rock or soft, easily mined material, influencing mining techniques and operational efficiency. Over 70% of the world’s aluminum supply originates from bauxite mines concentrated in just a few countries, contributing to global supply chain dynamics and pricing in the aluminum market. However, a significant environmental issue remains: the generation of red mud byproduct during aluminum extraction. Responsible waste management and advances in sustainable aluminum production now play a key role in reducing environmental impact and meeting industry regulations for green manufacturing.
The extraction of aluminum from bauxite—commonly called alumina production—was revolutionized by Austrian chemist Karl Josef Bayer in the late 1880s through what is now known as the Bayer process. This technologically advanced method utilizes a systematic four-step approach, involving chemical treatment and pressurized conditions, to effectively purify aluminum oxide (alumina) from bauxite ore. The resulting alumina serves as the critical intermediary for producing pure aluminum, including alloy grades such as aluminum 1100, widely used in the fabrication of heat exchangers, electrical conductors, chemical storage tanks, and food processing equipment.
To fully refine bauxite into a usable form for aluminum manufacturing, two integral processes are employed: the Bayer process, which isolates alumina, and the Hall-Héroult process, which extracts pure aluminum metal from alumina. These advanced metallurgical procedures form the backbone of global aluminum refining, allowing manufacturers to meet stringent quality standards across industries—including aerospace, automotive, and electronics—that require high-purity alumina and premium-grade aluminum sheet, foil, and extrusions.
In the digestion stage, mined bauxite is ground and crushed into fine particles to maximize surface area. The pulverized ore is then mixed with a concentrated sodium hydroxide solution to produce a high-pH slurry. This mixture is fed into a high-pressure digester where heat and pressure facilitate the reaction between sodium hydroxide and alumina, forming soluble sodium aluminate. Impurities like iron oxides and silicates do not dissolve and accumulate as insoluble red mud—a central waste management issue for the aluminum refining industry.
The caustic slurry from the digester is then transferred through a cascade of pressurized blow-off tanks for clarification. As pressure drops to atmospheric levels, solid red mud particles are separated from the soluble sodium aluminate using cyclonic sand traps and industrial thickeners. Efficient clarification is key to minimizing impurities, optimizing yield, and ensuring the resulting aluminum oxide meets strict performance and durability requirements. The residue is collected, thoroughly washed to recover any remaining sodium aluminate, and then responsibly disposed of or repurposed for building materials.
The clarified sodium aluminate solution enters tall precipitation tanks, where temperature is carefully controlled to maximize crystallization of aluminum hydroxide (also called hydrate). By seeding the solution with recycled aluminum hydroxide crystals, the process promotes the formation of larger, more easily filtered agglomerates. Settling and filtration yield a high-purity aluminum hydroxide, with process efficiency impacting the purity and particle size distribution critical for downstream processing of aluminum 1100 and other industrial grades.
The washed aluminum hydroxide is transferred to the calcination stage. Here, rotary kilns or fluidized bed calciners heat the material to over 960°C (1750°F), driving off chemically bound water to create a fine, anhydrous, white powder known as alumina (Al2O3). High-quality alumina is essential for successful electrolytic reduction into primary aluminum. Consistency in calcination promotes equipment longevity, enhances energy efficiency, and ensures the resulting aluminum ingots—including aluminum 1100—meet specifications for machinability, ductility, and formability.
The Hall-Héroult process is a cutting-edge electrolytic technique co-invented by Charles Hall and Paul Héroult and remains the predominant method for refining pure aluminum from alumina. This energy-intensive process takes place in specially designed reduction cells—large iron tanks lined with heat-insulating carbon that acts as the cathode. Carbon anodes are immersed in a molten bath containing dissolved alumina and cryolite (sodium hexafluoroaluminate), which lowers the melting point of alumina to around 950°C (1742°F), reducing overall energy demand and enhancing process control.
During the electrolytic reaction, a strong electric current passes through the molten bath, breaking the chemical bonds of alumina. Pure aluminum metal settles at the tank bottom, while oxygen released at the carbon anodes forms carbon dioxide. This process achieves aluminum of up to 99.99% purity—a critical attribute for manufacturers targeting high-performance and food-grade applications. Aluminum 1100’s exceptional purity results from this precise smelting process, making it the material of choice for products requiring excellent workability and corrosion resistance.
Due to the significant power requirements, electricity costs constitute a major share of total aluminum manufacturing expenses. This has led to the concentration of aluminum smelters in regions with reliable access to low-cost and renewable energy sources, enabling the industry to pursue more sustainable smelting practices and reduce carbon footprint. Innovations in carbon capture and alternative anode materials continue to shape the future of environmentally responsible aluminum production.
After reduction, primary aluminum is tapped from the reduction cell, transported to furnaces, and optionally alloyed with additional metals such as copper, magnesium, or manganese, creating specialized aluminum alloys with tailored mechanical properties. Aluminum alloys are engineered for demanding sectors, including aerospace, automotive, and construction. Purification through fluxing removes residual impurities to ensure the highest product quality before casting into ingots, billets, or other forms for further hot or cold working, extrusion, rolling, or precision machining.
Distinctively, Aluminum 1100—characterized by its minimal alloying elements and high purity—is typically formed directly into ingots or billets without needing further modification. Its consistency and softness make it ideal for deep drawing, spun hollowware, and applications where malleability and finishing are critical evaluation criteria for buyers and specifiers.
Key Considerations When Selecting Aluminum 1100:
When evaluating options for purchasing Aluminum 1100, it is recommended to compare leading suppliers based on quality certifications, traceability, available stock forms, and value-added processing services to ensure optimum performance in your application.
Aluminum 1100, one of the most widely used aluminum alloys, is transformed into various products through several cold working processes. After smelting, the sheets, ingots, and billets of aluminum 1100 are typically shaped by drawing, spinning, stamping, forging, and rolling, although it can also be hot worked if needed.
Cold working can significantly enhance the strength of aluminum 1100 by increasing the number of dislocations, or defects, within the metal's atomic structure. As the number of dislocations rises due to cold working, the metal's strength improves. At room temperature, aluminum 1100 has a yield strength of approximately 4 ksi (30 MPa). After cold working, its yield strength can increase to about 24 ksi (165 MPa).
Rolling aluminum transforms slabs into usable forms, such as aluminum cans and containers for takeout food. The process begins with a slab or billet of aluminum 1100, which hardens and strengthens during rolling. A roller mill applies force to the top and bottom of the slab, gradually reducing its thickness to the desired level.
After rolling, aluminum is classified based on its thickness. If the thickness is 0.25 inches (6.3 mm) or more, the material is classified as plate, which is often used in aerospace applications for wing structures and other components. Thicknesses between 0.008 inches (0.2 mm) and 0.25 inches (6.3 mm) are classified as aluminum sheet, making it a versatile form used in various applications. Rolled aluminum that reaches a thickness as thin as 0.008 inches (0.2 mm) is classified as foil, commonly used for packaging and insulation materials.
The extrusion process involves pushing an aluminum billet through a die under high pressure to form a specific shape. Although aluminum 1100 is not commonly used in extrusion, its high formability makes it well-suited for creating intricate and unique profiles. During extrusion, the billet is heated to soften the aluminum, facilitating its passage through the die. Because aluminum 1100 is relatively soft, it requires less heating compared to other alloys to achieve successful extrusion.
Spinning, or spin forming, is a process where a disc or tube of aluminum is rotated at high speed on a lathe. A form block is positioned on the lathe, and a properly sized disc of aluminum is clamped against this block with a pressure pad. As the aluminum disc and form block spin, force is applied to the workpiece, causing it to conform to the shape of the block. This force can be applied using one or multiple tools to ensure a smooth, wrinkle-free final product.
Aluminum spinning is typically used for low to medium volume production due to the time required for the process. It is often preferred over stamping when tooling costs for stamping dies are prohibitive or when producing shapes that cannot be easily achieved with stamping. This method provides versatility for creating complex shapes and detailed designs.
Annealing is a heat treatment process that enhances the properties and formability of aluminum 1100. In this process, aluminum 1100 is heated to a specific temperature and then cooled slowly. Annealing helps to relieve internal stresses, increase ductility, and improve the metal's workability. The process can be categorized into three types: homogenization, recrystallization, and heterogenization.
Annealing enhances the formability of aluminum 1100 beyond its typical limits. While various work hardening methods can shape and deform aluminum, they can eventually lead to the metal's grain structure becoming too stressed, causing breaking, cracking, or warping. To address these issues, aluminum 1100 is subjected to annealing, a heat treatment process that resets the grain structure and allows for further shaping and manipulation.
The forging process for aluminum is similar to the forging processes for other metals, which includes the use of pressure using a press or hammers. The process of forging requires several steps in order to reach the appropriate tolerance for the completed part. Although forging is a force and pressure method, it still requires proper planning and preparation.
The forging process of aluminum 1100 begins with selecting the appropriately sized slab or billet, which must be cleaned to remove any debris or impurities. After cleaning, the billet is heated to soften the aluminum, making it easier to shape. This heating is precisely controlled to ensure the aluminum 1100 reaches the correct temperature for forging. For aluminum 1100, the forging temperature is relatively low, ranging between 371°C and 510°C (700°F and 950°F).
During forging, force is applied using either a press or hammer. The process includes upsetting, drawing out, and finishing. Upsetting is used to widen and shorten the billet's end, while drawing out stretches the workpiece to the desired length. Finally, finishing refines the shape and removes excess material.
Forging exerts significant stress on the aluminum, necessitating controlled cooling to room temperature to prevent thermal shock. As the size of the workpieces increases, the cooling time extends accordingly.
The final step in forging involves machining the product, which includes drilling holes, cutting off waste, polishing, and coating. Proper machining is crucial for ensuring the quality and performance of the finished part, resulting in a precisely produced component.
Several processes can be used to weld aluminum, including stick welding, though it is generally not recommended due to its messiness. The most common methods for welding aluminum are tungsten inert gas (TIG) welding and metal inert gas (MIG) welding. Other techniques include laser welding, resistance welding, and shielded arc welding.
TIG welding uses alternating current (AC) and argon gas as the shielding gas. The filler material is manually fed into the weld pool and does not require a feeding wire. This method is known for its cleanliness and minimal contamination. MIG welding, on the other hand, is faster and uses a spool gun or other feeding mechanism to supply welding wire. However, MIG welding can potentially contaminate the weld, so it's crucial to ensure that both the base material and filler are clean, dry, and adequately shielded.
Despite the challenges associated with welding aluminum 1100, it remains widely used across various industries due to its lightweight, conductivity, corrosion resistance, recyclability, and attractive appearance.
Aluminum 1100 is used to produce a wide range of products thanks to its favorable properties, ease of workability, and machinability. The sheets, slabs, billets, and plates of aluminum 1100, cast or rolled during production, are sent to manufacturers who use various processes to create marketable products. Its versatility makes aluminum 1100 popular in both industrial applications and home products.
Aluminum 1100 is commonly used in radiator manufacturing due to its excellent heat dissipation properties. Its versatility allows it to be formed and shaped to meet various design requirements. Radiator fins, which must be thin yet durable, benefit from aluminum 1100's ability to rapidly dissipate heat thanks to their thin profile and the material's inherent thermal conductivity.
Aluminum 1100 is used to manufacture pots, pans, cooking tools, and other cookware because of its excellent heat conductivity and resistance to corrosion. Its key feature is its ability to distribute heat evenly across the entire surface of a pot or kettle, ensuring that food is cooked uniformly.
Aluminum 1100 is frequently used as a roofing material for commercial, industrial, and residential buildings. The thickness of aluminum 1100 roofing varies by application: residential roofing typically ranges from 0.030 inches to 0.032 inches, while commercial roofing can be as thick as 0.063 inches. Aluminum 1100 roofing is suitable for various environments, including coastal areas, hurricane-prone regions, heavy snowfall zones, and high-temperature locations.
One of the most recognizable uses of aluminum 1100 is in aluminum cans, which are ubiquitous. Concerns about aluminum's environmental impact have been raised due to the widespread use of these cans. However, advancements in technology and efforts by manufacturers have shown that aluminum 1100 is among the easiest forms of aluminum to recycle and repurpose.
The production of aluminum cans is a rapidly growing industry due to their effectiveness in preserving beverages until opened. Aluminum cans are stackable, cost-effective, quick to fill, printable, and make efficient use of shelf space.
The brief list of aluminum 1100 products provided here is just a small sample of its many applications. Aluminum 1100 is used in a variety of items, including heat exchangers, electrical conductors, reflective surfaces, chemical processing equipment, signage, aircraft components, heat shields, soundproofing materials, and decorative pieces. Its numerous benefits and superior qualities make aluminum 1100 an ideal material for a wide range of products.
Aluminum has become a key material in the manufacturing of many modern products, particularly with the surge in popularity of cellphones, laptops, tablets, and other handheld devices. Its resilience, longevity, lightweight nature, and strength make aluminum an ideal choice for producing contemporary appliances.
When exposed to air, aluminum forms a thin oxide layer on its surface that protects the metal from corrosion. If this oxide layer is damaged, it quickly repairs itself when exposed to oxygen. This self-healing property is a major advantage of aluminum alloys. When stored in stable environments without significant temperature fluctuations or moisture, aluminum 1100 can last indefinitely without requiring additional surface treatment.
Aluminum is widely used in heat sinks due to its thermal conductivity, although it's not as high as copper's. The choice of aluminum over copper is attributed to its lightweight nature, versatility, lower cost, and ease of forming and shaping. Aluminum 1100 stands out with its exceptionally high thermal conductivity among aluminum alloys, making it the preferred choice for applications requiring both strength and efficient heat dissipation.
Aluminum 1100's low density makes it incredibly lightweight, which is a significant advantage over other metals in applications demanding strength, durability, and reduced weight. Its lightweight nature, combined with other beneficial properties, makes aluminum 1100 ideal for modern products where ease of handling and convenience are essential.
While reflectivity might not always be the foremost feature of aluminum 1100, its mirror-like finish provides notable photometric qualities and light control. This reflectivity makes aluminum 1100 particularly effective for signs, enhancing visibility at night. Beyond street signs, its reflective properties are utilized in advanced scientific instruments, including those used for sterilization.
Modern industrial practices emphasize sustainability, focusing on preserving and protecting the environment through efficient use of resources. Aluminum 1100 plays a crucial role in these efforts due to its high recyclability. When its useful life ends, aluminum 1100 is sent to recycling facilities where it is processed and reused, contributing significantly to environmental conservation and sustainability.
The high purity of aluminum 1100 gives it an attractive appearance, making it popular in architectural applications to accentuate building features. Its light weight not only enhances the aesthetic of structures but also provides additional benefits such as sun protection and insulation. Aluminum 1100's appealing look and functional qualities make it a valuable choice for both visual and practical applications.
The term "aluminum coil" describes aluminum that has been flattened into sheets where their width is significantly higher than their thickness and then "coiled" into a roll. Stacks of individual aluminum sheets are difficult to...
Aluminum piping and tubing is silvery-white, soft, and ductile. The metal belongs to the boron group. Aluminum is the third most abundant element present on earth. Aluminum has low density. When exposed...
Aluminum is the most abundant metal on the Earth’s crust, but it rarely exists as an elemental form. Aluminum and its alloys are valued because of their low density and high strength-to-weight ratio, durability, and corrosion resistance...
Aluminized steels are steels that have been hot-dip coated with pure aluminum or aluminum-silicon alloys. This hot-dip coating process is termed hot-dip aluminizing (HAD)...
Beryllium Copper is a versatile copper alloy that is valued for its high strength and hardness, combined with good electrical and thermal conductivity. It is a non-ferrous, non-magnetic, and non-sparking metal alloy...
A variety of copper-zinc alloys are referred to together as brass. Different ratios of brass and zinc can be used to create alloys, which produce materials with various mechanical, corrosion, and thermal properties...
Copper is a ductile, malleable, and reddish-gold metal with the capacity to effectively conduct heat and electricity. Brass and bronze, two commonly used alloys, are created when copper is combined with...
The copper sheet is a highly malleable and workable metal with outstanding electrical and thermal conductivity and corrosion resistance. Copper (Cu) is a reddish, very ductile metal that belongs to Group 11 of the periodic table...
Metals are a group of substances that are malleable, ductile, and have high heat and electrical conductivity. They can be grouped into five categories with nickel falling in the category known as transition metals...
Stainless steel grade 304 is an austenite stainless steel that is the most widely used and versatile of the various grades of stainless steel. It is a part of the T300 series stainless steels with...
Stainless steel is a type of steel alloy containing a minimum of 10.5% chromium. Chromium imparts corrosion resistance to the metal. Corrosion resistance is achieved by creating a thin film of metal...
Stainless steel grades each consist of carbon, iron, 10.5%-30% chromium, nickel, molybdenum, and other alloying elements. It is a popular metal used in various products, tools, equipment, and structures that serve in many industrial, commercial, and domestic applications...
Steel service centers are companies that specialize in procuring steel directly from mills and manufacturers and supplying them to the customers. They are fundamental to the steel supply chain...
Stainless steel can be fabricated using any of the traditional forming and shaping methods. Austenitic stainless steel can be rolled, spun, deep drawn, cold forged, hot forged, or stippled using force and stress...
Stainless steel tubing is a multifaceted product that is commonly utilized in structural applications. Stainless steel tubing diameters and variations vary greatly based on the application requirements and are...
Titanium metal, with the symbol Ti, is the ninth most abundant element in the earth‘s crust. It does not occur in large deposits, yet small amounts of titanium are found in almost every rock...