Automatic Screwdrivers
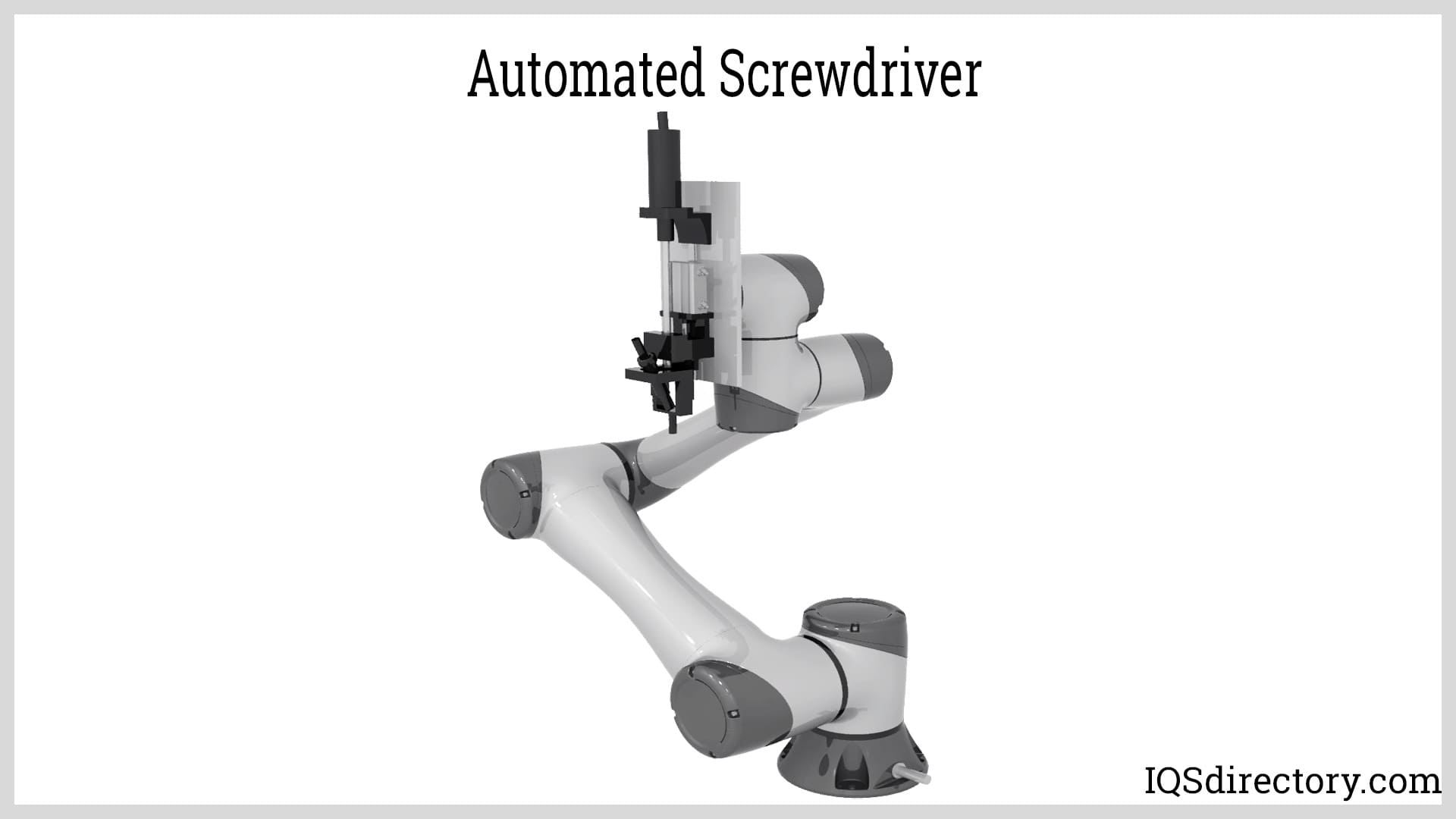
An automatic screwdriver is a piece of equipment that automatically inserts screws into a product during assembly and production. Since every production operation is unique and requires a...
Please fill out the following form to submit a Request for Quote to any of the following companies listed on
This article will give an in-depth discussion about collaborative robots.
The article will bring more understanding about:
In this chapter, we delve into the world of collaborative robots, highlighting crucial factors to consider when choosing the appropriate cobot for your specific applications.
Collaborative robots, commonly known as cobots, symbolize a breakthrough in robotic advancements, redefining automation by operating alongside human workers. Unlike conventional robots, cobots are fitted with sensors that enable environmental awareness. This technology allows them to work safely with humans, transitioning into a protective mode if any disturbance or safety threat is detected, thus minimizing risks associated with traditional robots lacking these safety features.
Collaborative robots are a specialized category within automation equipment, a comprehensive range of machinery facilitating automated production processes. This category also includes automation cells, conveyors, industrial robots, and niche equipment like turn-over machines and lifters.
Cobots utilize tools akin to those used by traditional robots, adaptable to diverse positions and applications. Manufacturers worldwide are investing in creating specialized tools for cobots, enhancing their task learning capabilities and versatility. These tools encompass Vision systems, End of Arm Tooling (EOAT), Grippers, Software, Range Extenders, Supply components, and Safety Systems.
Vision systems provide collaborative robots with the ability to perceive and decode their environment. Utilizing 3D or 2D cameras, cobots can detect and locate objects, identify patterns, and scan barcodes. This flexibility allows for efficient product handling; unlike traditional systems requiring organized layouts, vision-equipped cobots base actions on visual data. These systems support optical inspections, like detecting product flaws, and their capabilities are further boosted by Artificial Intelligence, offering sophisticated functionalities and improved efficiency.
In the realm of vision systems for collaborative robots, different options exist, tailored to various applications based on adaptability, cost-effectiveness, and ease of operation. Key choices include 3D and 2D camera setups, selected based on the task-specific needs envisioned for the collaborative robot.
While more economical than 3D cameras, 2D cameras have limited functionalities. They can measure an object's width and length but not its height.
3D cameras offer capabilities to measure an object's width, height, and length, making them highly versatile, although at a higher cost. Their ability to measure height is ideal for dealing with objects of varying elevations or stacked items, proving useful in packing or palletizing operations.
End of Arm Tooling (EOAT) includes a spectrum of tools attachable to collaborative robots, such as sanders, screwdrivers, sensors, tool changers, glue dispensers, welding apparatus, and soldering tools. Recent advancements in these tools have greatly enhanced their potential, enabling cobots to play a more integral role in amplifying production capacities for various companies.
EOAT presents vast opportunities for training cobots on new tasks. The continuous advancement of these tools will allow cobots to tackle a wider array of applications in the coming future. Below are some examples of the diverse EOAT tools available:
A dispenser is used to affix a glue or sealant syringe to a cobot’s end, allowing precise path-following and glue application with consistency, reducing wastage by precisely controlling glue quantity.
Screwing machines enable cobots to execute fastening tasks independently or alongside human operators. Screwing is monotonous and repetitive, making it ideal for cobots, which can efficiently manage this task over extended durations.
Armed with a sander, a cobot can proficiently sand, polish, or deburr surfaces. Integrated sensors ensure consistent pressure application for uniform results, and user-friendly software allows easy programming for specific paths.
Collaborative robots come with integrated sensors enhancing their capability to work safely with humans. For tasks demanding extra precision, additional sensors, such as an external force torque sensor, can further improve sensitivity.
Soldering and welding demand a high precision level, making cobots an excellent match due to their accuracy. Equipping a cobot with a soldering iron or welding torch allows for effective automation of these tasks.
Grippers enable collaborative robots to manipulate items by lifting and positioning them in different locations. A variety of grippers exist, including vacuum, magnetic, and finger grippers, designed for specific use cases such as vacuum grippers for boxes or soft grippers for delicate goods. Specifications such as gripping width, force, and payload capacity are crucial for selection.
Grippers vary according to material and task type. Selection should consider the weight and material of items to be handled.
Electric grippers suit complex tasks with their ability to fine-tune parameters like finger positioning and grip strength.
Pneumatic grippers, driven by air, handle simpler tasks. They're lighter, cost-effective, and offer a significant grip force, useful for varied applications.
For high-precision work, three- or two-finger grippers are optimal, adapting to objects' shapes to ensure secure handling.
Numerous resources exist for programming and designing applications for cobots, each robot coming with intuitive software to match its function. Simulation tools aid in development and refinement before implementation.
Traditional robots typically require extensive programming time and expertise, generally performing limited predefined actions. Cobots, however, are designed for ease of programming, learning new tasks swiftly with intuitive software and mobile apps. This simplicity allows for quick deployment and the ability to perform a wide variety of tasks.
RoboDK is an affordable, robust robot simulation tool, featuring over 500 robot arms in its library. Its user-friendly interface requires no programming experience, allowing rapid setup for simulations. Supporting offline programming, RoboDK facilitates cobot program development and testing outside production settings, suitable for machine tending, pick-and-place, welding, packaging, and palletizing applications.
Range extenders augment cobots' potential by expanding their horizontal and vertical operational reach, thereby enhancing automation capabilities. Typically constrained to their base axis, cobots gain increased mobility with range extenders, which also enhance productivity. For instance, in palletizing, robots can handle higher, more efficient box stacking, and navigate in front of large machinery, executing complex workflows.
Collaborative robots are praised for their ease of application and swift installation. With range extenders, they become even simpler to integrate, aided by user-friendly software for seamless cobot communication setup.
Safety measures include tools ensuring safe human-robot interaction, such as barriers and sensors that detect human proximity to the robot.
Supply systems comprise tools providing cobots with materials for manipulation. For instance, a tool can place screws in specific positions for cobot access, while screw-feeding systems collect and deliver them for assembly processes. Vibrating plates assist in sorting and organizing mixed items.
Enhanced cobot versatility arises from various automatic tool changers available on the market. These allow autonomous switching between tools, enabling multiple operation performance. In assembly tasks, a cobot might use a gripper to position components before switching to a screwdriver for final assembly, boosting productivity and return on investment.
Several points should be assessed when selecting a collaborative robot:
Cobots are ideally suited for tasks that are perceived as dirty, boring, dangerous, or physically exhausting. Typical uses include assembly, handling materials, inspection, and packaging. These robots are engineered with qualities like reach, precision, and payload capability for efficient human collaboration. While not as fast or powerful as traditional industrial robots, cobots excel in safety and adaptability, filling in workforce gaps and enabling human employees to focus on more strategic tasks.
The ISO 10218-1 and ISO 10218-2 outline four crucial cobot features: stops, hand guiding, speed and separation monitoring, and force and power limitations. These characteristics ensure safe, efficient operation across various applications. Speed and separation monitoring support tasks involving close human-robot interaction, while force and power limits are crucial for delicate operations. These standards facilitate safe, effective cobot integration in diverse settings.
Implementing a cobot demands ample expertise. Evaluate whether your team can manage the process or if a systems integrator is needed. Systems integrators offer valuable insights from varied client experiences, providing customized solutions and avoiding the hurdles of starting anew. Their expertise can often ensure cost-effective and smoother cobot integration.
Significant expertise is crucial when integrating a cobot. Determine if your internal team possesses the required skills and time or if you should consult a robotic integrator. These integrators, also called systems integrators, analyze your operations and advise on what would work best based on their extensive experience. They bring cost-effective solutions by preventing the need to create from scratch.
Risk assessment is a vital component when deciding on cobot usage. Despite built-in sensors designed to stop motions and avert injuries, cobots still pose potential risks. Ensuring full safeguarding is essential to secure safe, effective operation for staff protection.
Open communication is critical for successful cobot implementation. It's essential to engage all involved parties, from top-level executives to employees interacting with the cobot. Ensuring all stakeholders are knowledgeable and aligned can significantly streamline the integration process.
Collaborative robots, also known as cobots, represent a groundbreaking advancement in industrial robotics and smart manufacturing. These innovative automation solutions are engineered to work safely and efficiently alongside human workers in a shared workspace. The main types of collaborative robots differ in their design, safety mechanisms, and levels of required human-robot interaction, making them adaptable to a wide range of industrial automation and assembly applications. By understanding the differences between these cobot types and the technology driving their development, manufacturers and businesses can make informed decisions on selecting the optimal solution for improved productivity, safety, and return on investment.
In most conversations about collaborative robots, Power and Force Limiting (PFL) cobots are the primary focus. These collaborative robots are engineered with advanced safety features, including torque sensors, soft materials, and rounded edges, all contributing to direct human-robot collaboration without the need for traditional safety fences, external light curtains, or complex guarding systems.
To further advance operator safety, these force and power limiting cobots utilize collision detection sensors and safety-rated monitored stop functions that instantly halt operation upon making contact with a human. Due to these robust safety protocols, they are excellent for light payload tasks such as electronic assembly, machine tending, laboratory automation, precision inspection, and packaging in industries demanding flexible automation and human-machine interaction.
Although PFL collaborative robots are typically intended for lighter-duty applications, ongoing advancements in robotics technology are rapidly expanding their capabilities, enabling more diverse use cases across manufacturing, logistics, healthcare, and research environments.
Safety Monitored Stop collaborative robots integrate conventional industrial robot arms with safety monitoring systems such as presence detection devices, interlock gates, and emergency stop sensors. These cobots are ideal for manufacturing processes that require occasional human intervention for quality checks, tool changes, or equipment maintenance.
When a human worker enters the robot’s workspace, the cobot immediately suspends all motion, ensuring compliance with ISO/TS 15066 and other relevant industrial safety standards. Restarting the process is quick and user-friendly, allowing for minimal downtime and improved workflow continuity on automated production lines.
This type of collaborative robotics solution is frequently used in applications such as automotive manufacturing, CNC machine tending, material removal, and applications where a balance of throughput, safety, and periodic manual intervention is essential.
Speed and Separation collaborative robots—often described as “fenceless automation solutions”—are designed for environments with fluctuating human presence and a need for unrestricted access to equipment. These cobots employ safety laser scanners, intelligent vision systems, and virtual safety zones to dynamically adjust the robot’s operating speed based on a person’s proximity.
When an operator enters the defined safety zone, the cobot slows operation, switching to safe-mode or stopping entirely as required. Once the area is clear, the cobot resumes its programmed speed, maximizing both workplace safety and operational efficiency. This technology is particularly promising for warehousing, logistics automation, and large-scale material handling systems where flexible interaction and adaptive safety are vital.
Because speed and separation cobots offer exceptional adaptability, they can often replace traditional industrial robots in scenarios where safety, efficiency, and collaboration are equally important.
Hand guiding, or “lead-through teach,” collaborative robots feature safety-rated handles or end effectors that allow human operators to guide the robot arm manually for intuitive programming of complex paths, workflows, or pick-and-place operations. This user-friendly programming interface eliminates the need for advanced coding skills, enabling rapid deployment and task reconfiguration even by non-technical staff.
Hand-guided cobots are instrumental for applications that require frequent reprogramming, variation in production, or custom assembly operations—such as prototyping, low-volume manufacturing, or mobile workstations within dynamic environments.
Each of these four categories of collaborative robots offers unique benefits and levels of direct interaction between humans and robots. Cobots are designed to minimize the risk of accidents and injuries, leveraging the latest in robotics safety standards and smart automation features. As the rapidly evolving robotic automation industry continues to innovate, new types and advanced models of cobots will emerge, further shaping the future of smart factories, Industry 4.0, and intelligent manufacturing.
Selecting the best collaborative robot for your unique operation involves evaluating several key factors, including workplace safety requirements, payload demands, integration with existing automation systems, and the degree of required human-robot collaboration. Modern cobot manufacturers and leading robotics suppliers offer expert consultation, risk assessments, and customized automation solutions tailored to your needs. Investing in the right cobot technology can help streamline production, lower costs, improve workplace safety, and increase overall equipment effectiveness (OEE).
For organizations seeking to implement robotics in manufacturing, assembly, material handling, or laboratory environments, understanding the latest innovations in collaborative robotics is essential to maximizing ROI, productivity, and workforce satisfaction.
This chapter will explore the various applications and advantages of collaborative robots.
Tasks such as packing goods, restocking inventory, and assembly line work are often repetitive and monotonous. These types of tasks can lead to Repetitive Strain Injury (RSI), a condition resulting from the repeated performance of the same movements.
When robots take over repetitive tasks, human workers can focus on more complex and creative responsibilities, such as quality control or maintenance.
Assigning workers to solution-oriented and creative tasks not only enhances their job satisfaction but also fosters personal growth. This approach encourages flexibility and diversity, contributing to a more positive work environment. Such factors help workers find greater meaning in their roles, leading to increased engagement and productivity.
Collaborative robots, equipped with various tools and intuitive software, are capable of handling a wide range of tasks. Their versatility allows them to integrate multiple functions into a single automated process. While theoretically, a cobot can be trained for numerous applications, certain tasks are commonly automated, as outlined below.
Tasks like sanding, polishing, or deburring require precise control. Thanks to built-in sensors, a collaborative robot can follow designated paths while applying a consistent force on the surface, ensuring uniform quality. This makes them ideal for processing wooden, stainless steel, or metal surfaces.
Repetitive screwing tasks are well-suited for cobots. With the right tools and software, a cobot can be programmed to align objects with precision, apply consistent force, and maintain accuracy over long periods. This is challenging for humans but manageable for a cobot operating continuously throughout a workweek.
Pick-and-place tasks involve picking up objects from bins and arranging them on conveyors. While this application is straightforward, it can become more complex with additional tools, such as double grippers or adjustable grippers for different materials and sizes.
Bin picking is similar to pick-and-place but involves retrieving items from a non-standardized arrangement. Using vision systems and intelligent software, cobots can identify and pick items from bins one by one, and can also supply items to conveyor belts.
Machine tending involves placing parts into machines like CNC lathes or bending equipment. By automating this task, operators are freed up to focus on more complex activities, enhancing safety and productivity while allowing for extended operational hours and increased output.
Collaborative robots can significantly streamline the palletizing process. Using an electric vacuum gripper, a cobot can efficiently pick up boxes and place them onto pallets. Advances in technology have eliminated the need for external air supplies and hoses, simplifying integration and reducing costs.
Cobots are highly effective in performing quality control and inspection across various industries. They can handle tasks like placing items in testing equipment and sorting them based on visual inspections, thanks to advanced vision technology.
Gluing and sealing are ideal tasks for collaborative robots. By attaching a glue or sealant syringe to the cobot, it can follow a specified path and apply the adhesive consistently, ensuring uniform application.
Soldering and welding require high precision, making collaborative robots an excellent choice for these tasks. Cobots offer consistent quality and precision in welding and soldering applications, surpassing human capabilities.
Collaborative robots are highly adaptable and can be utilized across various industries. Their versatility allows them to be effectively integrated into many sectors, each with its unique requirements and challenges.
Automation in the food industry has increased due to factors such as higher demand and stricter safety regulations. While automating food handling presents challenges, advances in cobots and gripper technology have addressed these issues, enabling effective integration.
The plastics industry is characterized by low-volume, high-mix production, which presents challenges for automation due to frequent changes in production processes. Collaborative robots, with their flexibility and ease of reprogramming, have adapted well to these requirements.
As the demand for customized packaging solutions grows, collaborative robots are increasingly used for tasks like packing products into boxes and stacking them on pallets. Cobots can handle physically repetitive tasks, improving both production efficiency and worker satisfaction.
In the electronics industry, where precision and careful handling of small components are crucial, collaborative robots equipped with advanced sensors are well-suited for tasks like quality control and testing. Their sensitivity and accuracy make them ideal for these applications.
The pharmaceutical industry benefits from automation due to its need for high accuracy and low error margins in large-scale production. Collaborative robots excel in maintaining consistent performance, reducing errors, and improving overall efficiency.
The automotive industry has long utilized industrial robots for assembly. With increasing demands for customization and small production runs, collaborative robots are now becoming valuable for various automotive applications.
In the metal industry, where low-volume, high-mix production is common, collaborative robots are advantageous due to their adaptability. They can perform tasks such as soldering, welding, and loading CNC machines efficiently, meeting diverse production needs.
Collaborative robots offer several advantages, including:
Compact – Cobots are compact and can be integrated into production environments without occupying significant space.
Installing and Programming – Cobots are easy to install and program. With user-friendly software for both desktops and smartphones, they can be up and running quickly.
Flexible – Cobots can be easily programmed to perform new tasks, making them versatile for various stages of the production process.
Mobile – Lightweight and easily movable, cobots can be placed on mobile workstations to perform different tasks in various locations within a facility.
Consistent and Precise – Cobots deliver consistent actions with precise force, ensuring uniform quality and accurate component placement.
Positive Impact on Employees – By handling dangerous or monotonous tasks, cobots allow employees to focus on more creative and meaningful work, enhancing job satisfaction.
Reduction of Costs of Production – The efficiency and increased production capabilities provided by cobots contribute to cost savings and improved profitability.
Collaborative robots may require a restricted working area to ensure worker safety. Initial setup costs can be high, and safety measures might slow down operations. Cobots may need to stop when a person enters their workspace, impacting workflow. Additionally, some cobots are designed to slow down or shut down completely in the presence of humans, which could necessitate costly safety measures. Since they rely on human supervision, they cannot operate entirely independently.
To achieve effective integration, significant investment in safety and operational measures may be required. Collaborative robots' dependence on human oversight means they cannot function without continuous human support.
The RIA ISO/TS 15066 technical specifications and ISO 10218 safety standards provide guidelines on the safety performance and functionality of collaborative robots. Published in 2016, the RIA TR15.606-2016 Cobots document outlines safety requirements for robot systems and collaborative robots, reflecting the U.S. adoption of ISO/TS 15066. Under TS 15066, collaborative robots' speed and force limits are configured based on human contact areas, application data, and workspace hazards.
The RIA TR15.806-2018 Guidance on Testing Force and Pressure in Collaborative Robot Applications offers guidelines for measuring device conditions, test measurements, and testing methods. It includes metrics and methods for evaluating forces and pressures associated with both transient and quasi-static contact in collaborative applications.
Cobots have leveled the playing ground for small to medium-sized industries. For years, large industries have had the benefits of automation by utilizing traditional industrial robots. But these expensive, complex and large robots were made for high volumes, low volume, and constant production operations, opposed to the high-mix production typical of smaller manufacturers.
Collaborative automation has turned into an adaptive, affordable, and user-friendly technology which allows companies of just about any size (and any level of technical capability) to improve productivity, better quality, and respond more rapidly to varying customer demands.
An automatic screwdriver is a piece of equipment that automatically inserts screws into a product during assembly and production. Since every production operation is unique and requires a...
An automation system is an integration of sensors, controls, and actuators designed to perform a function with minimal or no human intervention. The field concerned in this subject is called Mechatronics which is an...
An industrial robot is an autonomous system of sensors, controllers, and actuators that executes specific functions and operations in a manufacturing or processing line. They operate continuously through repetitive...
Robotic system integrators are companies that provide assistance in automating a wide range of applications. They help design robotic technologies that best suit the needs of an operation for a company and solutions as...
Warehouse automation is the process of replacing repetitive tasks with systems that are automated. The main goal is to remove labor-intensive duties that consume time. As a result, the workers can focus more on...
An AGV forklift is a driverless self-operating robotic device that has the ability to carry, lift, retrieve, and place loads for easy transfer from one location to another. An automatic guided vehicle (AGV) forklift is a computer controlled mechanism that...
Automated guided vehicles (AGV) or mobile robots are types of guided robotic systems that are not bounded by a fixed range of motion. Rather, it is self-contained and can move along a line, surface, or space...
An autonomous mobile robot (AMR) is a self-propelled self-powered mechanism designed to perform repetitive tasks or organizational functions using an internal guidance system. They are able to navigate their...
A belt conveyor is a system designed to transport or move physical items like materials, goods, even people from one point to another. Unlike other conveying means that employ chains, spirals, hydraulics, etc...
A bowl feeder is a mechanism for supplying small parts and components to a production line or for sorting bulk items for rapid use. A self contained bowl feeder system has a bowl that sets on a spring loaded base that moves vertically...
A conveyor system is a method for moving packages, products, supplies, parts, and equipment for production, shipping, or relocation. The different types of conveying systems include pneumatic, screw, belt, and roller. The construction of individual systems depends on the materials...
Palletizing is the process of putting items on a pallet. The process of emptying the loaded objects in the reverse pattern is known as depalletizing. A pallet is a flat, square-shaped platform used to transport and...
A pallet stacker is a machine designed to assist the user in lifting, moving and handling palletized materials with ease. A pallet itself is a flat and horizontal structure used to support goods in a sturdy fashion...
A palletizer is an automated material handling machine used to stack and orient several individual products into a single load for a more convenient and economical method of handling, storage, and shipment. Palletizers are usually part of a bigger packaging process...
Pneumatic conveying is a method for transferring bulk materials, like powders and granules, using compressed gas or air, from one processing center to another. Material is moved through an enclosed conveying line or tube using a combination of pressure differential and airflow from a blower or fan...
A robotic palletizer is a type of palletizer that employs a robotic arm to pick, orient, and place individual products and arrange them into a single stack of load. They are the next generation of palletizers, and they will supersede conventional palletizers...
Roller conveyors are a type of conveyor belt that allows objects to skate on its surface by using rollers, which are equally spaced revolving cylinders. They transport stuff from one location to another...
Screw conveyors, or auger conveyors, are industrial equipment used in transporting bulk quantities of granular solids (e.g., powder, grains, granules), semi-solids, liquids, and even non-flowing materials from one point to another...
Vibratory conveyors are material-handling equipment used to transport fine to coarse-grained bulk materials. These vibratory conveyors are strong conveying equipment utilized for bulk commodities with fine to coarse graininess...
A vertical conveyor is an engineered mechanical method for moving goods, products, supplies, parts, and components from a lower level to a higher level or from a higher level to a lower level. They are...
Vibratory feeders are short conveyors used to transport bulk materials utilizing a controlled vibratory force system and gravity. The vibrations impart a combination of horizontal and vertical acceleration through tossing, hopping, or sliding-type of action to the materials being handled...
In 1954, when Arthur "Mac" Barrett, of Barrett Electronics Corporation, unveiled the first AGV, he named it Guide-o-Matic and described it as a driverless vehicle...