Cardboard Balers
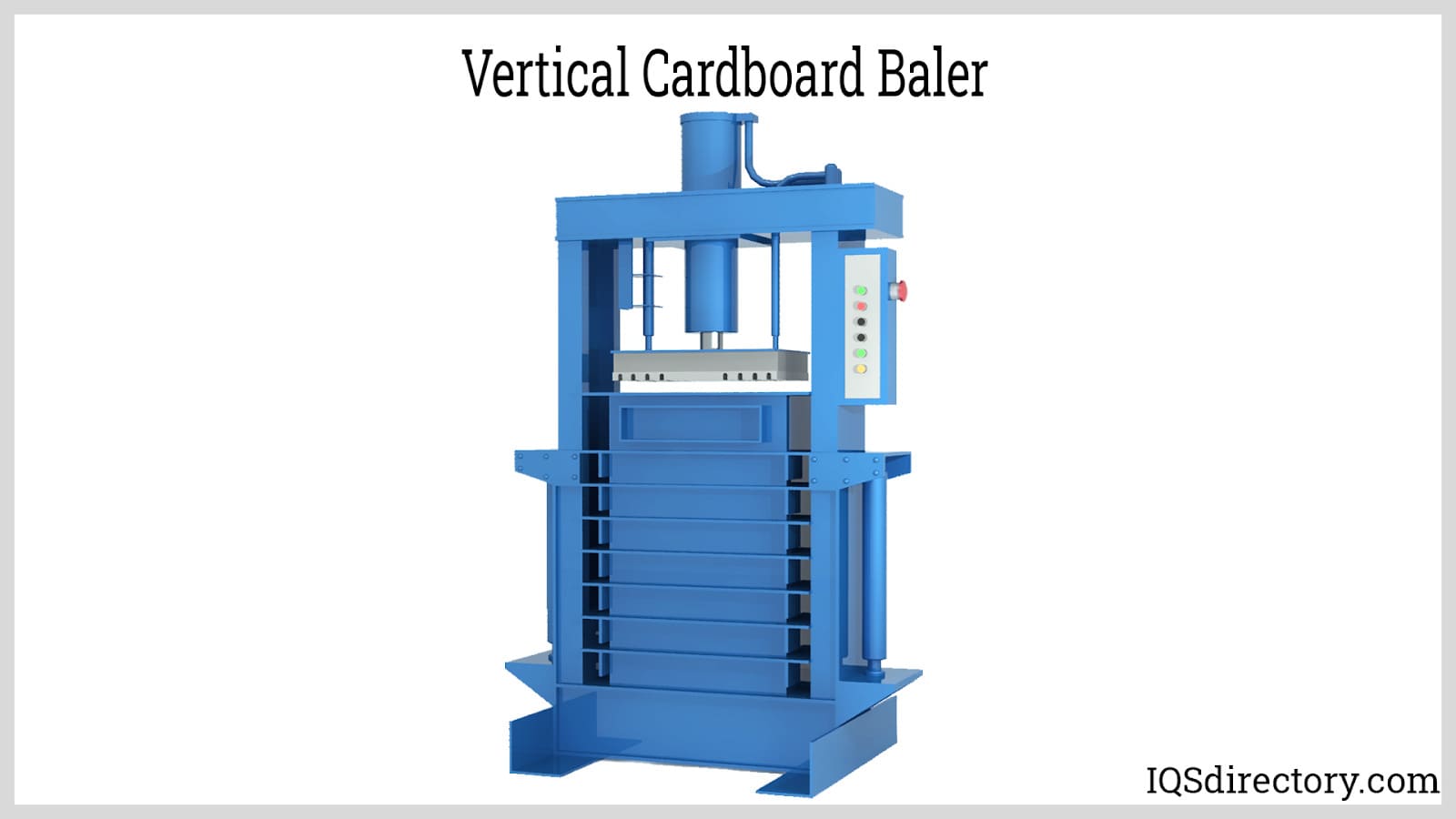
A cardboard baler is a mechanism that uses a metal plate driven by a hydraulic ram to apply tremendous pressure and force to crush, compact, and compress pieces of cardboard into tightly formed and easy to transport cubes and...
Please fill out the following form to submit a Request for Quote to any of the following companies listed on
This article provides a detailed look at baling machines.
You will learn:
A baler machine is a piece of equipment that compresses various materials into rectangular bales using a ram mechanism, making them ideal for transportation, storage, recycling, or further processing. These machines are built to handle both homogeneous and heterogeneous waste, converting materials into easily manageable sizes, thereby optimizing space utilization and enhancing asset efficiency.
Baling agricultural products and waste helps preserve their value and facilitates proper disposal or their use as raw materials. Animal feed, such as hay, grass, and straw, is essential for livestock nutrition, needing to maintain high energy and protein content. Because fodder is bulky and prone to decomposition, it requires drying and forming to avert spoilage. Moreover, decomposition produces heat, posing a risk of spontaneous combustion if not correctly managed.
The baling process is vital for managing moisture levels in animal feed. If moisture is too low, hay becomes dry and less nutritious, while excessive moisture increases the risk of spoilage and combustion. To mitigate these issues, fodder bales are frequently wrapped in plastic film or covers to maintain ideal moisture content.
In industrial environments, balers are instrumental in material management, especially in recycling operations. They compact materials into more dense and stackable bales, enhancing transportation efficiency and significantly cutting transport costs. Recycling these compacted bales streamlines material handling, leading to improved throughput, reduced operational costs, and increased economic gains.
Balers were first introduced in the 1930s to help farmers manage haystack sizes more effectively. Prior to automatic balers, hay was cut manually and gathered into stacks using rakes and forks. It was understood that haystacks needed to be of an optimal size—neither too large to avoid heating and combustion, nor too small to prevent drying and degradation.
The first automatic balers, known as round balers, were introduced in 1947 by Allis Chalmers under the name Roto-Balers. Since then, various types of balers have been developed, including rectangular and small square balers, all of which have been widely adopted in agriculture.
Early scrap material balers were in the form of compactors patented by MS Wells in 1941 as a means for compacting oil cans. Come the 1970s, these were further developed to compact household wastes by using hydraulic pressure from water lines.
Balers are chosen depending on the type of material to be baled, material loading methods, required purity, required dimensions for transport and milling, and throughput. Since the main point of using balers is to produce an economic advantage, it is important to keep in mind the difference between the baler’s investment and operating costs against the savings produced from storage and transportation cost reductions. Selecting a large, high-throughput baling machine may not be the best option. There are many baling machines available on the market that serve particular materials and specifications.
Vertical balers, also known as downstroke balers, compress materials using a vertical, downward force. These machines are typically employed for recycling materials such as cardboard, plastics, metals, and foam. The compression chamber is positioned on the side of the machine, elevated for efficiency. The ram, powered by either hydraulics or an electric motor, moves downward to compress the materials once the chamber is filled.
Vertical balers are more space-efficient than horizontal balers, making them ideal for smaller-scale applications such as supermarkets and retail stores. Their compact design not only reduces their footprint but also makes them more cost-effective, often priced significantly lower than horizontal balers. Vertical balers can handle a wide range of recyclable materials, offering versatility in what they process. However, they have limitations in output consistency, as their compaction force and bale sizes are less standardized. This inconsistency can make transportation less efficient and add extra processing steps for recycling mills, potentially complicating the sale of bales. Some manufacturers address these issues with heavy-duty vertical balers equipped with powerful pistons and high-power reciprocating pumps, designed to produce dense, standard-sized bales.
Horizontal balers use horizontal force to compress the materials. Unlike vertical balers, the materials are not loaded directly into the chamber but are collected by a hopper on top of the machine, where the material sits on top of the ram. Conveyor, sorting, and shredding systems can be integrated to aid in loading, making them more convenient and less labor-intensive for operators. For the process to be efficient, the loaded materials must be prevented from jamming, clogging, or preventing the movement of the ram.
Horizontal balers are generally larger than vertical balers, allowing them to handle high volumes of material. They generate greater compaction forces, producing dense bales that can weigh up to half a ton. This results in uniform bales that are more suitable for transport and further processing.
To address issues with jamming and maintain smooth production, baler manufacturers continually develop solutions for horizontal balers. One effective method is the use of anti-jamming devices, such as shear blades, which cut material efficiently and help keep the baling process moving. Shear blades trim excess material that can obstruct the ram, preventing jams and ensuring a consistent compression stroke.
Unlike horizontal balers, vertical balers cannot utilize shear blades due to their design. As a result, materials for vertical balers must be pre-cut before being loaded into the machine. Horizontal balers benefit from shear blades—whether saw-toothed or staged—which improve processing efficiency and minimize delays.
Single ram balers use a single hydraulic cylinder to generate compression and are among the most common types of balers for material recycling. They can be either horizontal or vertical, depending on the ram's orientation. Horizontal single ram balers are further categorized into closed-end and open-end extrusion balers.
Closed-end (closed-door) balers compact materials using a single ram against the chamber door. After compaction, a chamber door opens to release the bale. Automatic ejection rams are also added to aid in releasing the compacted bale.
Horizontal closed-end balers are the standard for the industrial baler industry. They allow businesses to make larger and heavier bales regardless of the types of materials being baled. Their main feature is the closed-off baling chamber, which is smaller in comparison to open-end auto tie balers. Waste material is compressed using a single ram that uses the weight of its force to compact the material.
Closed-end balers operate automatically and do not require an operator. They activate when their chamber is filled to capacity and continue operation until the material is compressed. Closed-end balers may repeat compaction multiple times until the chamber is completely full and the ram can no longer move.
Open-end balers compress the materials through a long extrusion chamber. This is often called continuous horizontal baling. The ram compresses the bale against the side of the previous bale formed in the extrusion chamber. It is a faster process than closed-end balers and eliminates the need for other parts, such as ejection rams and separation doors. A common feature of open-end extrusion balers is their automatic tying mechanism, which is useful for high-rebound products such as cardboard, rubber, and textiles.
As with closed-end balers, open-end balers operate automatically but continuously without ever stopping due to their open-end design and tying mechanism. They are a highly dependable tool for companies that have a high volume of waste and multiple shifts.
An open-end baler is a heavy-duty extrusion-type baler that quickly and efficiently compresses a huge volume of waste material. Regardless of their constant motion and high-end operation, open-end balers are economical and energy-saving due to the design of their single ram.
Open-end balers come with one or two rams, with the two ram type being able to work quickly and compress a wider range of materials. The chamber of an open-end baler is under constant tension due to the continuous pressure it applies. The increased tension ensures that the bales produced are tight, secure, uniform, and dense. To prevent damage to the mechanism, the baling cylinder releases tension between bales.
Two-ram balers, also known as two-cylinder balers, use a primary ram for compressing material and a secondary ram for controlling and removing the compressed material. They can be configured as either vertical or horizontal balers. The primary ram compresses the material, while the secondary ram manages the ejection process. These machines are particularly effective for handling high-rebound materials like rubber and are designed to compact large and dense materials. The dual-ram setup allows for better management and containment of the rebound effect during compression.
Another common configuration for two-ram balers is the L-shaped design. In this setup, the material is compressed along one axis initially, and then along the perpendicular axis for further compression. This design allows for a larger feed opening, accommodating bulkier materials more easily. The increased opening size facilitates quicker loading and reduces the likelihood of material bridging in the hopper, thus improving overall efficiency.
Another advantage of two-ram balers is reduced tie wire usage. These balers produce denser bales, which require less wire to secure their shape. The higher compaction pressure forces materials into plastic deformation, meaning they do not revert to their original shape. As a result, the bales maintain their dimensions over time, reducing the need for stronger ties and contributing to overall cost savings.
Liquid extraction balers, as their name implies, not only compact materials but also drain liquid from them. This feature is particularly valuable for handling rejects from food production, bottled goods, and brewed products. Unlike other balers, liquid extraction balers are constructed with nearly 90% stainless steel to withstand liquid exposure, while the remaining parts are coated with anti-wear and corrosion-resistant paint. They also include a closed-loop catch system to collect the extracted liquid efficiently, ensuring a clean and effective discharge process.
Ferrous balers are primarily used in scrap metal processing and are designed to handle heavy materials like metals. These balers come in two or three-cylinder configurations. The two-cylinder ferrous baler features a pressing lid or wing door that compresses metals alongside the main ram. In contrast, the three-cylinder ferrous baler compresses metals from all directions. It uses a pressing lid to pre-compress the metals to the desired size, while the remaining two rams complete the compression process, similar to the operation of an L-shaped two-ram baler.
Ferrous balers, like two-ram balers, are equipped with large openings that facilitate the feeding of more material. These openings are designed to accommodate materials without being restricted by the bale dimensions, and material feeding is typically handled by cranes.
Ferrous balers are distinguished by their lack of automatic tying systems. Metals, which undergo plastic deformation during compression, generally maintain their shape after baling, reducing the need for additional tying.
A track baler is mobile, enabling it to be positioned directly at the scrap location, thereby reducing the amount of handling required for baling scrap material. This reduction in handling not only cuts costs and saves time but also enhances overall efficiency. The size of a track baler allows it to handle several tons of scrap, compressing and shearing it effectively. The movement and compression of a track baler are controlled remotely.
In this machine, materials are compressed into a log-shaped, compacted form which is then cut to length either by shearing or further compacting to create a bale. This "logging" action serves as a preliminary pressing operation. Due to their capability to produce sheared logs in addition to high-density bales, these machines are also referred to as scrap shears.
SBLs excel in portability. They are typically transported via trailer trucks and feature hydraulic landing gears, facilitating easy on-site installation. This makes them highly beneficial for small junkyards, demolition projects, and site cleanup activities.
Round balers are utilized for baling agricultural products and are typically towed by a tractor that gathers forage from the field. The forage is conveyed into the baling chamber, where a series of rollers and belts compress the materials. Once the desired density and dimensions are achieved, an automatic wrapping mechanism wraps the rolled material in mesh netting. After wrapping, the baler opens to release the round bale.
Round balers are designed for baling agricultural products and are typically towed by a tractor, which collects forage from the field. As the forage is gathered, it enters the baling chamber where rollers and belts compress the materials. Once the desired density and dimensions are achieved, an automatic wrapping mechanism wraps the material in mesh netting. After wrapping, the baler opens to release the round bale.
A basic baler typically includes a ram, chamber, material feeding gate, and a mechanism to generate compressive force. These fundamental components are further refined to enhance compression force and processing speed. Additional features like hoppers and wire-tying mechanisms are often incorporated to automate processes and reduce manual labor. Below are the key components found in a typical baling machine.
Hydraulic Cylinder: This part exerts the required force to compress the material. The working fluid is pressurized by positive displacement pumps to achieve the required compression. Scrap metal baling requires tough and durable hydraulic cylinders. They must also be able to withstand shocks and side loading. Proper maintenance such as condition monitoring and lubricating is essential.
Control System: This is where commands are entered by the operator. The hydraulic system is usually controlled by programmable logic circuits or PLCs by manipulating the opening and closing of the valves. This is also where parameters such as pressure, bale dimensions, and temperature are monitored. For advanced systems, the machine is equipped with diagnostic and fault detection systems.
Conveyors: Conveyors are used for material feeding at a lower elevation. This eliminates the need for larger cranes that are usually needed to reach the height of the hopper. Loader trucks dump the materials onto the conveyor, which lifts and transports the material into the hopper.
Ejection Rams or Arms: After compression, ejection rams remove the baled material from the chamber. Fully ejecting the bale and other materials that did not form together helps to minimize contamination.
Bale Ties: These are wires or straps that wrap around the bales to prevent them from becoming loose after compaction. Bale ties must have sufficient strength to counter the rebound or expansion of the materials. There are different types of bale ties according to material, finish, and loop. Below are the most common types.
Balers are predominantly used in scrap material recycling. Below are the most common uses of balers and the recommended types for each application.
Balers are used for compacting steel cans, aluminum cans, steel sheets, radiator caps, copper wires, and clips. For lighter metals such as cans and sheets, a two ram baler is enough. But for compacting heavier, thicker metals, ferrous balers consisting of three hydraulic cylinders are more suitable.
Balers are used for materials such as cardboard, office papers, magazines, newspapers, and so forth. An average office worker produces about 2 pounds of paper products per day. Mixed paper makes up an estimated 70% of office total waste. Large recycling plants use horizontal single ram balers with automatic tying mechanisms. For small to medium-scale storage and recycling, standard mill-size balers and stand-alone vertical baling machines are sufficient.
This includes PET and HDPE bottles, plastic films, rigid PP containers, rigid and flexible PVC materials, as well as electronic and automotive plastic scraps. Prior to feeding these materials to a recycling facility, sorting should be conducted based on type, origin, and characteristics. When baling multiple types of plastics, it's crucial to prevent cross-contamination between batches to meet the standards of the recycling facility.
Foams are lightweight materials with low densities that occupy significant storage space. Certain foams, like many polyurethane foams, are thermosetting plastics, meaning their properties change irreversibly upon curing. This characteristic makes recycling such foams challenging, often leaving incineration or landfill disposal as the primary disposal methods. Balers assist in reducing the space taken up by compressing weights exceeding a thousand pounds into a volume of approximately 45 cubic feet.
This category encompasses used clothing, carpets, rugs, wool, and other fibrous materials. Baling textiles differs from baling materials like steel and plastic because it requires less force but demands cleanliness and freedom from stains throughout the process. The primary goal of baling textiles is to minimize space during hauling and enhance transportation efficiency. Vertical balers are commonly used for handling textiles.
Balers are employed to compress animal fodder, aiding in moisture control and nutrient retention, as previously discussed. Initially developed for bundling and storing haystacks, the concept was later adapted for handling scrap materials. Round balers are widely used for baling animal forage.
Balers play a crucial role in compacting animal fodder to regulate moisture levels and preserve nutrients, as discussed previously. Originating as a solution for bundling and storing haystacks, this concept was later adapted for handling scrap materials. Round balers are widely used for baling animal forage.
A cardboard baler is a mechanism that uses a metal plate driven by a hydraulic ram to apply tremendous pressure and force to crush, compact, and compress pieces of cardboard into tightly formed and easy to transport cubes and...
A Trash compactor is a machine or device designed to compress, reduce, and compact a variety of materials through hydraulic, mechanical, or pneumatic force. The initial steps in the compacting process are the collection of the material to be compacted...
Modern balers are descendants of hay presses, invented in the mid-nineteenth century, that made it easier to gather and stack hay. The earliest hay presses were stationary units built into a barn and extending two to three stories into the hayloft...
A cardboard shredder is a machine designed to turn cardboard boxes and sheets into small shards or strips. Specialty cardboard shredders are configured to convert cardboard into flexible perforated material for packaging...
A bowl feeder is a mechanism for supplying small parts and components to a production line or for sorting bulk items for rapid use. A self contained bowl feeder system has a bowl that sets on a spring loaded base that moves vertically...
An industrial shredder is a piece of heavy duty equipment designed to shred dense and light materials to prepare them for recycling or for the destruction of unusable products. They are an environmentally sound device that...
Scrap metal must be processed to be effectively recycled and ready for reuse. Metal shredders are machines used to process a variety of metal scraps. Metal shredders are frequently used to reduce metal debris to...
A shredding machine is equipment utilized for shredding. Shredding machines are used to reduce the size of materials. While most online sources define the shredding machine as...
Tire shredders are a type of recycling equipment used to reduce the volume of tires to scrap using high torque shredding systems. The various types of tire shredders are capable of handling large loads of...
Vibratory conveyors are material-handling equipment used to transport fine to coarse-grained bulk materials. These vibratory conveyors are strong conveying equipment utilized for bulk commodities with fine to coarse graininess...
Vibratory feeders are short conveyors used to transport bulk materials utilizing a controlled vibratory force system and gravity. The vibrations impart a combination of horizontal and vertical acceleration through tossing, hopping, or sliding-type of action to the materials being handled...
A vibratory screening is a process that separates bulk solid materials from solids and slurries using inertial vibration that causes various sizes of particles to pass through openings in a screen or...