Boiler Rentals
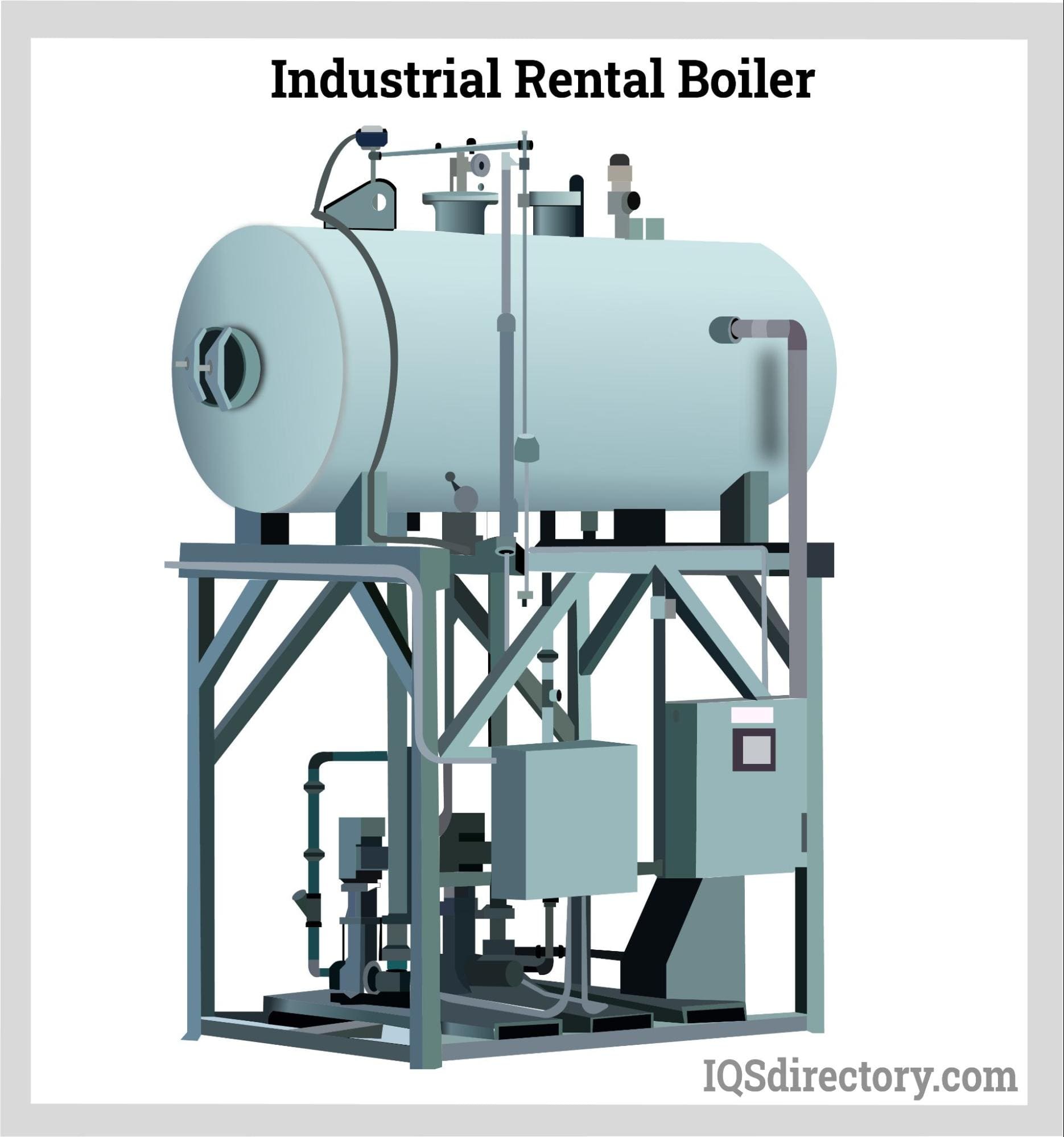
Boiler rental is a service that is offered by boiler manufacturers to assist customers in times of emergency, high usage, or as a cost effective permanent solution. Every type and size of boiler is available for rental from ones...
Please fill out the following form to submit a Request for Quote to any of the following companies listed on
This article contains information and details regarding high pressure boilers and their use.
You will learn:
A high-pressure boiler operates at pressures of 80 bars or more and is typically utilized in thermal power plants for electricity generation. This type of boiler transforms water into steam via thermal energy within tubes filled with water, housed in a durable metal enclosure. The generated steam is then employed to operate various machinery.
The hallmark of a high-pressure boiler is its ability to produce significant pressure, distinguishing it from other boiler variants. This pressure and steam are generated by burning fuels like coal, natural gas, or oil. Heated gases circulate either through natural convection or are propelled by a pump. Utilizing a centrifugal pump for forced circulation increases the evaporation rate to 210 kPa (kilopascals) per square centimeter, as natural convection alone is insufficient for producing the high pressures required.
High-pressure boilers come in diverse types, such as steam generators and electric boilers, and in various designs, including vertical, horizontal, gas, water-tube, and fire-tube configurations. A shared characteristic of these boilers is the implementation of small-diameter tubes, which boost the heating surface area and enhance heat transfer efficiency.
In a fire-tube boiler, hot gases travel through tubes immersed in water, raising the water's temperature to create steam, as depicted in the accompanying image below.
Most boilers operate on the fundamental principle of converting heated water into steam. The differences among various types of boilers lie in their geometric orientation, the placement of the fire (external or internal), pressure levels, water circulation methods, number of tubes, and gas circulation mechanisms.
The geometric orientation of a boiler can be horizontal or inclined, with the fire positioned either inside or outside the boiler, depending on its design. Boilers are classified based on pressure: those producing pressures above 80 MPa are considered high-pressure boilers, while those with pressures below 80 MPa are classified as low-pressure boilers.
Water circulation can be either forced or natural. Forced circulation involves pumping the water, while natural circulation relies on convection. Gas circulation is influenced by the type of tubing used: in fire-tube boilers, hot gases pass through tubes submerged in water, whereas in water-tube boilers, water flows through the tubes, heated by surrounding gases.
Boilers can have either single or multiple tubes. For example, the traditional Cornish boiler features a single fire tube, while modern designs often incorporate multiple tubes to improve efficiency and performance.
The Lamont boiler is a forced convection water-tube boiler that uses a pump to circulate water. It features an economizer to enhance energy efficiency, along with a boiler drum, superheater, evaporator, and air preheater. In this system, water is pumped through the economizer and preheater before entering the boiler drum.
The boiler drum acts as a steam separator. The pump directs water to a distributor header with nozzles that distribute the feed water into the evaporator tubes located in the boiler walls, maximizing surface heating.
In the boiler drum, water and steam are separated. The steam is then routed to the superheater, which raises the temperature of the saturated steam to prevent water droplets from reaching the turbine. The superheated steam is then directed to the turbine for power generation.
The Benson boiler shares several features with the Lamont boiler but operates without a steam separator and functions under critical pressure. It is a water-tube, forced circulation boiler in which feed water is compressed to supercritical pressure. This compression prevents the formation of bubbles in the water tube by increasing the density of the water, making it equal to the density of the steam. As a result, the latent heat in the water is effectively reduced to zero, facilitating easier conversion to steam.
Like the Lamont boiler, the Benson boiler includes an air preheater, economizer, superheater, evaporator, and combustion chamber. However, in contrast to the Lamont boiler, the combustion chamber in a Benson boiler can be mounted horizontally.
The Loeffler boiler was designed to address a problem encountered with the Lamont boiler: salt and sediment buildup on the water tube surface, which reduced heat transfer efficiency. Similar to the Benson boiler, the Loeffler boiler circulates water under high pressure within the water tubes.
The Loeffler boiler features both radiant and convective superheaters to effectively distribute steam to the turbine. The radiant superheater uses radiant energy from the burning fuel to heat the saturated steam, providing the primary heat transfer. The steam then moves to the convective superheater, which is heated by flue gases, further increasing the steam temperature before it is sent to the turbine.
The Velox boiler is a forced circulation water tube boiler that uses high velocity to rapidly produce steam. The principle of the Velox boiler is built on the velocity of the gas, which moves faster than the speed of sound and increases the rate of heat transfer.
The Velox boiler features a gas turbine compressor that delivers compressed air into the combustion chamber, where it facilitates additional heat release. This increased rate of heat release boosts the velocity of the flue gases to near the speed of sound. The flue gases travel from the fire tubes at the bottom of the combustion chamber and envelop the water-filled tubes.
Water is forced from the economizer to the circulating pump at high speed, which accelerates the heat transfer from the gases to the water. The heated water and steam then move to the water separator and proceed to the superheater. Similar to the Loeffler boiler, the superheater in the Velox boiler is heated by the flue gases.
The Cornish boiler is one of the simplest types of boilers. It is a fire-tube boiler featuring a long, horizontal tube with a single flue containing the fire. The cylindrical shell of a Cornish boiler typically ranges from one to two meters in diameter and four to seven meters in length.
Fuel for a Cornish boiler is loaded onto a grate through a door, where it burns to generate hot gases. These gases then pass through the fire tube, which is surrounded by water, heating the water to produce steam.
The Babcock and Wilcox boiler is a horizontal water-tube boiler that uses natural draft circulation and features multiple tubes. Water enters the tubes through a downcomer header, is heated by hot flue gases, and moves in a zigzag pattern due to baffle plates. The steam generated in the tubes then flows to an uptake header, where it is collected in a boiler drum. An anti-priming pump removes any water droplets from the steam, ensuring that only dry steam is sent to the superheater. The superheater increases the steam temperature, and the steam is either collected or directed to the turbine for power generation.
High pressure boilers offer distinct characteristics and features that make them ideal for generating energy and power. Key factors that set high pressure boilers apart from other energy production methods include their fuel type, emissions, and efficiency. Each of these factors impacts the equipment's performance and cost. The following information highlights some of the essential features of high pressure boilers.
Water expands approximately 1,600 times to form steam, which is capable of carrying large amounts of heat. This makes water an economical and ideal medium for generating heat and power. High-pressure boilers heat water to produce steam at pressures exceeding 15 psi, with water pressures often surpassing 160 psig.
Combustion efficiency refers to how effectively the fuel is used during combustion, distinct from stack loss, which is the heat lost through flue gases and moisture. High-pressure boilers are highly efficient, operating with 15 to 20% excess air, ensuring that nearly all of the fuel is converted into thermal energy.
Thermal efficiency measures the heat exchanger's ability to transfer heat from the heating process to water or steam, excluding radiation and convection losses. Most high-pressure boilers achieve a thermal efficiency of around 95%.
Fuel-to-steam efficiency, measured by the ASME Power Test Code, is the ratio of BTU output to BTU input. This ratio reflects the efficiency of the boiler in converting fuel into steam. The higher the ratio, the more efficient the boiler. Typically, high-pressure boilers achieve a thermal efficiency of about 95%.
Stack temperature is the heat lost from the combustion process in a boiler.
Minimizing stack loss is crucial for efficient boiler operation. Effective heat transfer is indicated by a low stack temperature, which means less heat is wasted. High-pressure boilers manage air flow to avoid excessive air that can contribute to stack loss. The specific air requirements are determined by the type of fuel utilized in the boiler.
Burners typically require 15 to 20% excess air for complete combustion. Minimizing excess air improves the efficiency of a high-pressure boiler. Excess air is indicated by increased flue gas temperatures. An economizer, which recovers heat from the flue gases, can help mitigate some of this heat loss.
Radiation and convection losses vary based on the boiler’s type, size, and pressure. These losses occur because the boiler operates at much higher temperatures than its surroundings. While it is impossible to completely eliminate these losses, they can be reduced through proper insulation of the piping and boiler body.
The American Boiler Manufacturers Association (ABMA) provides a standard radiation loss chart to measure radiation losses. The extent of these losses is directly proportional to the boiler's surface area.
The efficiency of a boiler increases with more heating surface area per horsepower. Typically, boilers are designed to produce 5 to 7.5 lbm/hr of steam per square foot of heating surface, though this can vary between models.
The number of flue gas passes through the boiler before exiting is a key factor in efficiency. As flue gases circulate, they cool and decrease in volume. More passes improve heat transfer efficiency and increase the gas velocity.
The efficiency of a boiler heavily depends on the performance of the burner, controller, and the boiler system as a whole. For optimal efficiency, the burner must effectively use the air supply and minimize excess air. The burner’s efficiency is crucial to controlling operational costs, with proper air levels ensuring effective combustion.
High pressure boilers are categorized based on their fuel type, which significantly influences operating costs. The choice of fuel can also impact environmental compliance depending on local regulations. Understanding the different fuel options available can aid in selecting the most appropriate high pressure boiler for specific needs and location.
One current trend in high pressure boiler selection is opting for models that can operate on multiple fuels, such as natural gas, propane, or #2 fuel oil. This flexibility allows for adjustment in fuel usage as prices fluctuate, providing a key advantage in managing fuel costs effectively.
Coal has been used as a fuel source for boilers for over a century. In many contemporary boilers, coal is pulverized into a fine powder to improve combustion efficiency. Among the various types of coal, anthracite is known for its high heat output and cleaner burning properties, as it produces more heat and less smoke compared to other coal types.
Biomass, an organic fuel, is becoming increasingly popular due to its eco-friendly nature and low emissions. Biomass fuels come in various forms, which are described below. To facilitate handling, feeding, combustion, transportation, and storage, biomass is often processed into pellets or briquettes for greater efficiency.
Rice husks are increasingly used as a biomass fuel due to their abundant availability as a byproduct of rice production. Utilizing rice husks not only addresses disposal issues but also offers the advantage of the ash produced, which is rich in silica. Additionally, rice husks are a low-maintenance fuel that does not contribute to corrosion, fouling, or sintering problems.
Wood chips are created by processing wood through a chipper, which sizes them appropriately for use as fuel. Boilers designed to operate on wood chips are known as multifuel boilers, as they can also burn pellets made from various crop production wastes. These boilers are equipped with a feeding mechanism that ensures a continuous supply of fuel.
Gas boilers can operate on either propane or natural gas. In these systems, gas is ignited in a combustion chamber to heat the heat exchanger. Gas boilers are among the most common and cost-effective options, both in terms of installation and operation.
Oil boilers have the same operating principle as a gas boiler. The fuel is ignited in a combustion chamber and heats the heat exchanger that heats the water. Oil boilers are not eco-friendly since oil burning produces CO2. Although there are problems with oil boilers, they can be more efficient, depending on their model and design. They are also more expensive to operate because of the changing prices of crude oil.
Electric boilers utilize electric heating elements to directly heat water. While they produce no emissions and are relatively straightforward to operate, they are less efficient and significantly more expensive compared to other boiler types. They are, however, an excellent choice for situations with stringent emission regulations.
Understanding the purpose of a boiler—primarily to generate steam from water—is crucial for effective boiler construction. In industrial settings, high pressure boilers are mainly used to produce energy and power to operate equipment and machinery.
While different types of boilers feature varied designs and geometric orientations, most share common components, including the burner, combustion chamber, and heat exchanger.
To ensure efficient energy production, boilers are equipped with essential accessories and mountings. Accessories typically include economizers, superheaters, feed pumps, controllers, and air preheaters. Key mountings consist of feed check valves, steam stop valves, fusible plugs, blow-off cocks, critical safety valves, and water level indicators.
The burner serves as the primary heat source for the boiler. It operates based on signals from a thermostat that controls heat production. For liquid fuels, such as oil, the burner uses a nozzle to atomize the fuel into vapor, which is then ignited. For solid fuels like wood, coal, and biomass, these materials are fed into a grate within the combustion chamber, where they are ignited to produce heat.
The combustion chamber, also known as the firebox, is where the fuel is burned. Constructed from cast iron or steel, it can withstand extremely high temperatures. The chamber is sealed to retain heat between firing cycles, enhancing efficiency. Heat generated in the combustion chamber is transferred to the heat exchanger.
The grate is a platform within the combustion chamber where solid fuels, such as wood and coal, are placed to burn. It features bars spaced to allow airflow, essential for sustaining combustion and efficiently burning the fuel.
The heat exchanger's role is to transfer heat from the combustion gases to the water without direct contact. In a boiler, this involves the transfer of heat through pipes from the heated gases produced in the combustion chamber. The heat exchanger is crucial for converting water into steam in the boiler.
The steam drum functions as a separator for the steam-water mixture. Steam exits the steam drum at the top and is directed to the superheater, while water is removed from the bottom. The separation process occurs in two stages: primary and secondary. The primary stage separates most of the steam from the water, while the secondary stage, using a separator scrubber, captures any remaining water droplets to ensure the steam is as dry as possible.
Boiler accessories are not mounted on the boiler but are necessary for the boiler to operate efficiently.
The economizer is where water enters the boiler and its temperature is increased by the flue gases. It is an energy-saving device that enhances system efficiency by preheating the water, thereby reducing fuel consumption and lowering operating costs.
Steam produced by a boiler is often wet or saturated, containing harmful water droplets. The superheater’s role is to further heat the steam to eliminate these droplets, ensuring that the steam is dry and superheated for optimal performance.
Boiler feed pumps supply the boiler with water at a rate that matches the amount of steam being produced. In contemporary boilers, centrifugal pumps are commonly used for this purpose.
Boiler controllers oversee the operation of the boiler, detecting abnormalities and ensuring proper function. They manage the aquastat to regulate water temperature, preventing excessive firing. Additionally, controllers monitor water levels and the feed rate to avoid low water levels, which could lead to overheating and frequent firing.
The air preheater (APH) utilizes recovered flue gases to heat incoming air, enhancing the boiler's thermal efficiency. As the flue gases cool after transferring heat to the air, they are directed into the gas stack. Air preheaters come in two types: recuperative and regenerative.
Boiler mountings are crucial for ensuring the efficient operation and safety of a boiler. As the name suggests, these components are attached directly to the boiler.
The water level indicator is a crucial safety device that shows the current water level inside the boiler. Typically, boilers are equipped with two water level indicators for redundancy. Each indicator consists of a glass tube and three cocks: the first connects the tube to the steam, the second to the water, and the third verifies that the first two cocks are clear and functioning properly.
The pressure gauge monitors and displays the internal pressure of the boiler, providing crucial information for safe operation.
Every boiler must be equipped with a pressure gauge, which can be installed on either the front or side of the unit. High pressure boilers typically utilize a Bourdon gauge, renowned for its precision in measuring high pressures.
The safety valve safeguards the boiler by releasing steam when the internal pressure exceeds safe levels, preventing potential overpressure hazards. It helps manage extreme pressure by venting excess steam, and its loud discharge serves as an audible warning to nearby personnel. Common types of safety valves include lever, dead weight, high steam-low water, and spring-loaded varieties (as illustrated below).
A stop valve regulates the flow of steam, with the capability to fully halt its passage. It controls the steam supply to different parts of the system and can be operated either manually or as part of an automated control system.
A fusible plug is a safety device used in firetube boilers to prevent overheating. Under normal conditions, the fusible plug remains submerged in water, which keeps it intact. If the water level drops, the plug becomes exposed, causing its fusible metal to melt. This action allows water to flow in and extinguish the fire, thereby protecting the fire tubes from damage.
The blow-off cock is utilized to eliminate unwanted deposits that accumulate at the bottom of the boiler or to drain excess water. When opened, the cock allows these deposits to be expelled under pressure.
The feed check valve regulates the flow of water into the boiler and prevents it from flowing back if there is a pump failure or insufficient pressure. Also known as a no-return valve, it is installed just below the water level in the boiler.
High pressure boilers are crucial for energy production and power generation, but they also pose significant risks. Despite their advanced safety features, failure to manage pressure can lead to catastrophic explosions, releasing both metal debris and superheated steam.
Certain conditions can lead to dangerous boiler failures.
Melt-down occurs when the boiler metal melts due to a low water supply. While it may not cause an immediate explosion, it can severely damage the boiler. If not addressed, the risk of an explosion remains.
Thermal shock happens when cold water is introduced to an overheated surface. The sudden expansion of cold water into steam can cause an explosive reaction.
Combustion explosions result from ignited gas and can occur either inside or outside the boiler.
Maintaining proper steam pressure is essential for boiler safety. All boilers must have effective safety measures to manage and monitor steam pressure.
The boiler log provides a detailed record of all boiler operations and is updated regularly. It includes crucial information on safety inspections and any operational malfunctions.
Maintaining the correct water level is essential for boiler safety and efficiency. There are two primary methods for monitoring water levels: using the gauge glass, which is the simplest approach, and checking the cocks if the gauge glass is not functioning properly.
During blowdown, the gauge glass should refill rapidly when the blowdown valve is closed. If refilling is slow, it may indicate a blockage in the water flow.
A safety valve's capacity is rated in pounds per hour, and it must be equal to or exceed the boiler’s pounds per hour rating. The valve's performance is tested using the try lever; once the lever is released, the valve's disk should return to the closed position.
Modern boilers include a flame safeguard within their control systems. This system monitors the burner and shuts off the fuel supply if no fuel is detected. A flame scanner assesses the flame’s flicker and intensity by scanning visible, infrared, and ultraviolet light to ensure proper combustion.
Rust and corrosion are significant issues in boiler systems. Corrosion can weaken the metal and cause pitting in tubes, piping, and other components. Proper water treatment is essential to maintain boiler efficiency and prolong its lifespan.
Carryover occurs when water droplets enter the steam line due to high water levels, water impurities, or high surface tension. Managing these factors is crucial to prevent carryover.
During blowdown, the boiler should operate under a light load and maintain a normal water level. Open the valve slowly and cautiously to avoid injury.
When opening a steam valve, always wear safety glasses or shields and gloves. Open the valve very slowly to balance the pressure and warm the downstream equipment. Ensure that traps are also drained.
Pumps are generally low-maintenance, but their bearing temperatures should be regularly monitored, and any vibrations should be checked. Routine maintenance should include lubricating the pump bearings and inspecting the flexible couplings and pump seals.
Steam traps can lead to a feedwater pump becoming steambound, where feedwater turns to steam due to excessive heat. To resolve this issue, the pump needs to be cooled.
The measures outlined above are essential for managing high pressure boilers. Adhering to specific safety standards set by organizations and manufacturers is critical.
Organizations must comply with stringent safety guidelines and regulations for high pressure boilers as defined by the Occupational Safety and Health Administration (OSHA) and the National Fire Protection Association (NFPA).
The organizations overseeing boiler standards and regulations include OSHA, NFPA, and the American Society of Mechanical Engineers (ASME). OSHA and NFPA have established safety protocols and regulations to ensure proper handling and operation of high pressure boilers under various conditions.
OSHA's boiler regulations aim to prevent serious injuries and establish standards tailored to specific industry conditions.
Pressure devices must undergo inspections to ensure safe installation and must be regularly tested and inspected.
Boilers are deemed compliant if they possess a current, valid certification from a qualified inspector.
Requirements for different types of pressure devices and equipment are detailed in Subparts F and O of the OSHA standards.
NFPA 85 outlines safety and preventive measures to address uncontrolled fires, explosions, and implosions in Section 1.1. It sets forth requirements for the design, installation, operation, training, and maintenance of boilers and pressure devices.
The ASME Boiler Code is a national standard that enhances public safety, product reliability, and industrial efficiency. It supports research in industrial sectors and strengthens contractual relations and certification, serving as an international benchmark for accreditation programs.
Boiler rental is a service that is offered by boiler manufacturers to assist customers in times of emergency, high usage, or as a cost effective permanent solution. Every type and size of boiler is available for rental from ones...
A steam boiler is a steam producing heating system. It creates energy by heating water to get steam. It is a heat exchanger that makes steam for outside usage and has a combustion chamber and water container. The several varieties of steam boilers include...
A water tube boiler is a boiler that has a set of tubes through which water circulates and is heated by heated gasses from its furnace or combustion chamber that is located below the tubes. Fuel, burning in the...
A conveyor oven is a continuous flow oven; it‘s an oven that is open on opposing sides and has a conveying system running from one end of the oven to the other. Designed like a batch oven, conveyor ovens have the additional benefit of keeping products moving while providing continuous and uniform heat...
A furnace is a direct fired device used to provide heat for industrial processes that require heat in excess of 400° C (752° F). Any industrial application that relies on heat to create a reaction or heat materials for production uses an industrial furnace...
A curing oven is thermal processing equipment used by thermal specialists to improve or enhance the strength and durability of materials. Many factory processes such as baking, drying, heating, cooking, and curing require...
An industrial oven is a device used to create extremely high temperatures to heat treat parts, condition metals, and cure metal coatings. Common functions for industrial ovens include drying, curing, testing, and coating of parts and products...
An infrared oven is an oven that heats objects or cooks food using infrared radiation instead of conventional conduction or convection heating. People can use infrared ovens in commercial kitchens, homes, or...
A normal function of an industrial furnace is to heat treat metals for annealing, tempering, or carburizing and pre-treat materials for forging. Though metal is a common material to be treated using an industrial furnace, other materials are also...
Industrial ovens are thermal processing machines used as heating chambers for drying, curing, and baking of foods, parts, and components. The main industries that use industrial ovens are chemical and food processing and electronics manufacturing...