Boiler Rentals
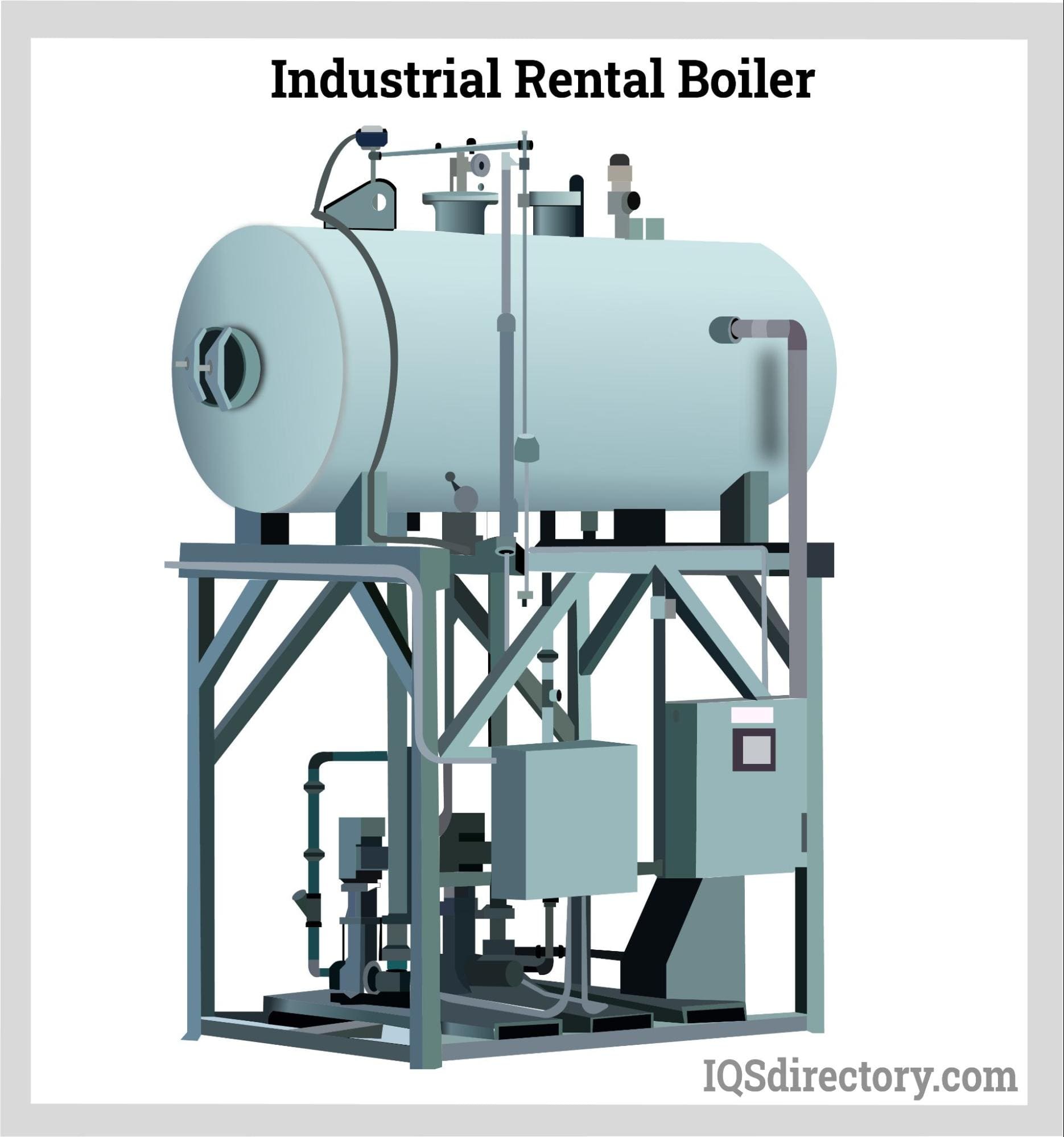
Boiler rental is a service that is offered by boiler manufacturers to assist customers in times of emergency, high usage, or as a cost effective permanent solution. Every type and size of boiler is available for rental from ones...
Please fill out the following form to submit a Request for Quote to any of the following companies listed on Steam Boilers .
This article provides a detailed look at.
Read further to answer questions like:
A steam boiler is an apparatus designed to produce steam by heating water. It acts as a heat exchanger, transforming water into steam for a variety of external uses. The boiler typically contains a combustion chamber alongside a water reservoir. Steam boilers are available in different sizes, from compact units to sizable versions capable of undertaking more intensive operations.
A steam boiler facilitates steam production by burning fuel to raise the temperature of water. This process utilizes three heat transfer methods: radiation, convection, and conduction.
Steam boilers are classified based on their construction, portability, tube type, fuel type, and operating pressure. Early boilers were as efficient as modern ones but lacked sufficient control mechanisms, making them hazardous. The size, fuel, and dimensions of a boiler vary according to the specific task and industry requirements. Common fuel types include electricity, wood, natural gas, coal, and fossil fuels, each differing in cost, environmental impact, and efficiency. With the growing demand for electricity and power, alternative fuels such as biomass and refuse-derived fuel have been developed.
Hot water boilers are tanks designed to transfer heat to water, which is then circulated for heating purposes. Constructed from materials like stainless steel, cast iron, aluminum, and steel, these boilers can withstand high temperatures and pressures.
Hot water boilers are classified by their tube systems, which can be either fire tube or water tube. In fire tube boilers, tubes immersed in water carry the heat, which then heats the surrounding water. In water tube boilers, water circulates inside the tubes, which are heated from the outside.
Electric boilers use electric elements to generate heat, providing a faster and more efficient heating method. As an eco-friendly and cleaner system, they do not require fuel combustion. Electric boilers are more durable, require less cleaning, and are virtually maintenance-free. However, it is important to manage the buildup of scaling in the water reservoir.
Gas steam boilers Gas boilers, powered by natural gas or propane, are more efficient than standard boilers. The fuel is piped directly into the boiler from an external source. Heat distribution from a gas steam boiler depends on its specific configuration. Gas steam boilers are suitable for both industrial purposes and low-pressure applications.
Low pressure steam boilers transfer heat at pressures between 10 and 15 psi with a temperature of 300°F (149°C). This type of boiler is ideal for applications requiring consistent temperatures with minimal need for rapid changes. Low pressure steam boilers are popular because they deliver steam much faster than high pressure steam boilers.
High pressure steam boilers create excessive pressure to power equipment and machinery. The force and power of a high pressure steam boiler is produced by a pump that forces the steam at high pressure into the circulation system. To be classified as a high pressure steam boiler, a boiler must be able to produce pressure between 15 psi and 800 psi at temperatures that exceed 250°F (121°C).
For safety and efficiency, high pressure steam boilers are regularly monitored for their pressure and temperature. Their high pressure loads are classified as either batch or continuous: batch loads are used for short-term demand, while continuous loads are suited for long-term demand.
Oil steam boilers operate similarly to gas boilers, but use oil instead of gas in the combustion chamber. The burning oil heats the exchanger, which then heats the water. Oil steam boilers can achieve efficiency rates of over 90%. Although they are more expensive than gas steam boilers, they typically have twice the lifespan.
One concern with oil boilers is the requirement for an oil tank, either inside or outside, that must be refilled regularly to ensure a constant supply of fuel.
Water tube boilers circulate water through tubes within the boiler. The fire from the combustion chamber burns around the outside of these tubes, heating them and, in turn, heating the water inside. This design generates high pressure steam by utilizing tangential pressure, or hoop stress, applied to the circumference of the tubes. This stress is similar to the pressure exerted on the bands of a wooden barrel as it fills.
Various types of water tube boilers have been used since the invention of the first boiler, evolving and improving over the centuries.
La Mont, Benson, and Loeffler steam boilers employ forced circulation and draft fans to generate large quantities of steam with high efficiency. Water is pumped through small-diameter, closely spaced tubes by a centrifugal pump. Their efficiency is enhanced by an economizer, which preheats the water using flue gases or pipe gases from the combustion chamber.
In a fire tube steam boiler, the tubes are heated while water circulates around them. The heat inside the tubes is generated by gases from burning coal or oil, which transfer thermal energy to the water, producing steam. Fire tube steam boilers are typically used for low pressure steam. The three main types of fire tube steam boilers are Cochran, locomotive, and Lancashire.
A fire tube steam boiler can be fitted with an economizer to enhance its efficiency and heat recovery system.
Shell boilers feature heat transfer surfaces enclosed within a steel shell. Various tube layouts are employed, which affect the number of times heat passes through the system before being discharged. Also known as flue boilers, shell boilers have a long, cylindrical water tank and utilize fire tubes. Heat from the furnace or combustion chamber flows through these fire tubes to warm the water.
The earliest version of this type of boiler was the Cornish boiler, characterized by a long cylinder with a single large flue or pipe containing the heat or fire. It was later replaced by the Lancashire steam boiler, which featured two flues for the fire.
Shell steam boilers, also called shell and tube boilers, are one of the simplest boiler designs, known for their efficient and economical steam production.
A steam boiler absorbs heat generated from combustion, transferring it through radiation, convection, or conduction. The efficiency of heat transfer depends on factors such as the type of steam, the fuel used, and the characteristics of the transfer surfaces.
Radiation is the transfer of energy through electromagnetic waves emitted by all elements and bodies. In a steam boiler, the tubes absorb radiant heat from the flame in the combustion chamber. The effectiveness of radiant heat transfer depends on the rate at which the electromagnetic waves are absorbed by the surfaces.
Convection is the transfer of heat within a liquid or gas as it heats up. When a liquid or gas is heated, it becomes lighter and less dense, causing it to mix with cooler, denser liquid or gas. In a steam boiler, convection occurs when the heated fluid becomes lighter and rises, allowing cooler, heavier fluids or air to move in. This process creates a continuous cycle of heating and mixing, as the hot fluid is replaced by cooler fluid.
Conduction is the process of heat transfer through direct contact between surfaces. In metals, heat moves through the material to warm anything it touches. In a steam boiler, conduction occurs when the outer part of the tubing is heated, and this heat transfers through the tubing to the inner surface and the cooler water inside.
A steam boiler heats water in a manner similar to a teapot, but on a larger and more complex scale. While specific designs vary, all steam boilers share common elements: a burner, combustion chamber, heat exchanger, expansion tank, steam temperature control, safety relief valve, and low water cutoff.
The designs and types of steam boilers widely vary depending on their construction and purpose.
The burner’s function is to deliver fuel and air into the combustion area. Fuels such as oil, gas, or pulverized coal need to mix thoroughly with the air. Dampers regulate the airflow to the burner, and an impeller distributes the air evenly around it. Fuel is introduced into the boiler via pipes known as spuds and is ignited by an igniter.
The combustion chamber facilitates the reaction between fuel and air to generate heat for steam production. To maximize efficiency, the chamber must be well-insulated to prevent heat loss through radiation. It contains tubes with water and steam that pass through the chamber, which houses the burner and controls. Efficient combustion is crucial for proper boiler operation, as the heat generated is absorbed by the boiler surfaces at the top of the combustion chamber.
The heat exchanger facilitates the transfer of heat between fluids without allowing them to mix. It consists of a long coiled pipe submerged in the fluid to be heated. Gas or a heated liquid flows through the pipe, transferring heat to the surrounding water. Heat exchangers are constructed from various materials, with stainless steel being the preferred choice due to its resistance to corrosion and rust.
The expansion tank helps regulate and maintain boiler pressure by providing a space for water to expand and absorb pressure changes. It features a diaphragm that separates the tank into two sections: one side receives water from the boiler, while the other side is managed by an air valve to control pressure. The air valve adjusts pressure by pushing against the water in the other section until normal pressure levels are achieved.
Steam temperature control is essential to prevent thermal stress and ensure precise temperature regulation. Effective control of both pressure and temperature helps keep fuel costs low. Steam temperature is typically managed by spraying water onto the first and second stage superheaters using an attemperator or desuperheater.
Other methods for controlling steam temperature include using flue gas circulation, flue gas bypass, or adjusting the tilt angle of the burners in the furnace. The most straightforward approach is to monitor the steam temperature as it exits the boiler and adjust the position of the spray water valve accordingly.
The pressure relief valve The pressure relief valve is a crucial safety measure for steam boiler operation. It helps prevent catastrophic failures by relieving excess pressure buildup. The valve opens when pressure exceeds a critical level and closes once the pressure returns to normal.
A low water cutoff automatically shuts off the burner or fuel supply to a steam boiler when the water level falls below a specified point. This prevents damage such as rupture or significant failure due to a dry-fired boiler. Low water cutoffs are essential safety features integrated into steam boilers and hydronic systems to protect against damage and ensure safe operation by shutting down the boiler if water is lost.
Traditionally, steam boilers are used for central heating in homes, offices, businesses, hospitals, and other facilities. Despite their diverse applications, all boilers operate with the same fundamental functions and mechanisms, involving a contained combustion process to generate heat.
A range of fuels can be used to generate heat in a boiler and ignite the burner. The heat produced is then circulated through the system using pumps and heat exchangers. To tailor the steam boiler’s function to specific needs, additional control mechanisms are often incorporated.
Aquariums utilize steam boilers to manage their operations. The numerous tanks in an aquarium require precise regulation of water temperature and conditions to safeguard the diverse species on display. Gas-powered steam boilers, coupled with heat exchangers, are used to control both fresh and saltwater tanks and to generate water currents and surges, simulating ocean-like environments.
Pasteurization involves heating products to specific temperatures to eliminate pathogens. Precise temperature control is essential, as any deviation can affect the taste of the final product. Brewers and distillers use low pressure steam heat to produce consistent batches cost-effectively. Dairy producers rely on steam boilers for cleaning and sanitization.
College laboratories often use exhaust air during experiments and testing. To replace the exhausted air, outside air, which can be cold, is brought in and needs to be heated. Given the large and spacious nature of laboratories, significant heating is required. To meet this demand, universities and colleges typically use low pressure steam boilers.
Heating multi-story skyscrapers demands a robust energy production system designed for continuous operation. Due to their immense size, skyscrapers require multiple boilers to ensure efficient and effective heating. Steam boilers used for this purpose can weigh up to 165 tons and consume 3,000 liters of fuel per hour, which is sufficient to heat around 2,000 private residences.
Using water and steam for heating skyscrapers is highly practical and effective due to their ease of transport and widespread availability.
Beer is brewed in large kettles, which are heated and sanitized using steam boilers. After each brewing cycle, the kettles must be thoroughly cleaned and sanitized to remove any contaminants. When designing a brewery, the choice of boiler is a critical factor to ensure the kettles remain clean and functional.
The spent grain from the brewing process can be repurposed as fuel for steam boilers, offering both ecological benefits and cost savings.
A key function of a steam boiler is to drive turbines for electricity generation. A large and powerful boiler can produce up to 225,000 pounds of steam per hour at 900 psi, potentially generating 20 megawatts of electricity. Advances in technology and design have enabled steam boilers to be optimized for energy efficiency while still producing power.
In the lumber industry, low pressure steam boilers are employed to power kilns for drying specialty lumber products. Hardwoods for furniture and cedar planks for cooking both require kiln drying. Low pressure steam boilers enable producers to carry out this drying process safely and efficiently, enhancing the quality of the wood products. Their manageable and consistent heat makes them well-suited for this drying application.
Like all industrial equipment, the production and operation of steam boilers are governed by codes, regulations, and standards set by regulatory agencies, voluntary organizations, and the U.S. government. The American Society of Mechanical Engineers (ASME) publishes the most widely accepted codes for boilers and pressure vessels in its Boiler and Pressure Vessel Code guide.
The codes most pertinent to boilers were published in 2013 and are organized into different sections:
Section VIII Guidelines for Pressure Vessels of which there are three types:
The ASME also has additional codes and standards for boiler systems, including the B31 series for piping and the CSD series for controls and safety equipment.
OSHA's primary focus is worker safety. Steam boilers are considered potentially hazardous and must be operated only by trained, experienced, and authorized personnel. OSHA mandates regular and frequent inspections of boilers to ensure they are free of leaks, that combustion is functioning correctly, and that all safety devices and gauges are operational.
Older steam boilers insulated with asbestos coatings, wraps, or lagging should be inspected for leaks, damage, flaking, or deterioration. Any damaged asbestos materials must be safely removed and replaced.
Founded in 1888, the ABMA is the longest-running trade association in the United States. Initially established to address prevalent safety concerns at the turn of the century, the ABMA has been instrumental in implementing numerous safety measures for steam boilers, advancing their use into the 21st century.
The modern ABMA's mission is to lead and unify the boiler industry through education, awareness, and a commitment to addressing steam boiler issues and challenges. The ABMA represents manufacturers across all areas of the industry, from heavy-duty steam boilers for power plants to those used in the utility sector. The association covers all devices that produce steam and hot water.
Boiler rental is a service that is offered by boiler manufacturers to assist customers in times of emergency, high usage, or as a cost effective permanent solution. Every type and size of boiler is available for rental from ones...
A high pressure boiler is a shell and tube heat exchanger that use boiled water to create steam or high pressure hot water. Using water filled tubes in a metal tank or enclosure, they create power by converting water into steam through thermal energy, which is used...
A water tube boiler is a boiler that has a set of tubes through which water circulates and is heated by heated gasses from its furnace or combustion chamber that is located below the tubes. Fuel, burning in the...
A conveyor oven is a continuous flow oven; it‘s an oven that is open on opposing sides and has a conveying system running from one end of the oven to the other. Designed like a batch oven, conveyor ovens have the additional benefit of keeping products moving while providing continuous and uniform heat...
A furnace is a direct fired device used to provide heat for industrial processes that require heat in excess of 400° C (752° F). Any industrial application that relies on heat to create a reaction or heat materials for production uses an industrial furnace...
A curing oven is thermal processing equipment used by thermal specialists to improve or enhance the strength and durability of materials. Many factory processes such as baking, drying, heating, cooking, and curing require...
An industrial oven is a device used to create extremely high temperatures to heat treat parts, condition metals, and cure metal coatings. Common functions for industrial ovens include drying, curing, testing, and coating of parts and products...
An infrared oven is an oven that heats objects or cooks food using infrared radiation instead of conventional conduction or convection heating. People can use infrared ovens in commercial kitchens, homes, or...
A normal function of an industrial furnace is to heat treat metals for annealing, tempering, or carburizing and pre-treat materials for forging. Though metal is a common material to be treated using an industrial furnace, other materials are also...
Industrial ovens are thermal processing machines used as heating chambers for drying, curing, and baking of foods, parts, and components. The main industries that use industrial ovens are chemical and food processing and electronics manufacturing...