Boiler Rentals
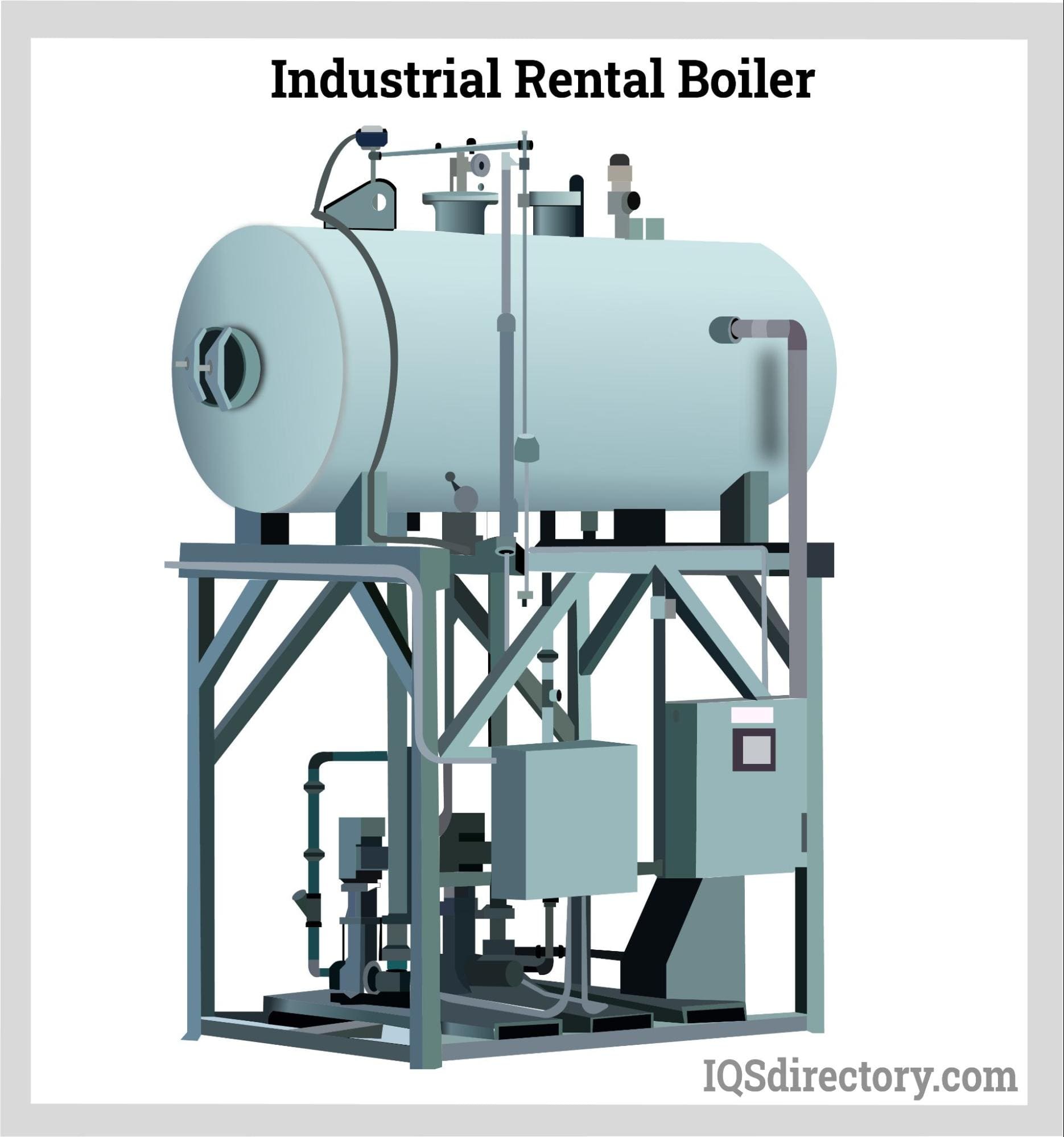
Boiler rental is a service that is offered by boiler manufacturers to assist customers in times of emergency, high usage, or as a cost effective permanent solution. Every type and size of boiler is available for rental from ones...
Please fill out the following form to submit a Request for Quote to any of the following companies listed on
This article contains everything you will need to know about water tube boilers and their use.
You will learn:
A water tube boiler is designed with a series of tubes that carry water, which is heated by hot gases originating from a furnace or combustion chamber located below these tubes. When fuel is burned in the furnace, it produces gases that transfer heat to the metal tubes, subsequently warming the water inside. This heated water ascends to a steam drum, where saturated steam is released.
The fuels used in a water tube boiler include natural gas, propane, coal, diesel fuel, or heating oil, which are combusted in the combustion chamber or furnace to generate hot gases, heating both the tubes and the water within them. Traditional boilers operated in the opposite manner, heating tubes immersed in water via a furnace utilizing coal or wood. As water temperature increased, it resulted in a time-intensive heating process. This inefficiency led to the innovation of the water tube boiler design, where water flows through the tubes for more effective heating.
Traditional water boilers, which heated both the water and the pipes, occupied significant space and were quite cumbersome. To ensure these conventional boilers were ready for heating or industrial use, designated staff had to start them up early each morning before the rest of the workers arrived, leading to inefficiencies and increased energy consumption in both commercial and industrial environments.
The drawbacks of the previous boiler design—including large spatial footprint, slow start-up times, and risk of boiler failure—prompted engineers to explore the use of robust, high-pressure materials for tubes that would hold water and be heated to produce steam. This research resulted in the creation of the water tube boiler, a cutting-edge technology in industrial steam boilers. Water tube boilers offer enhanced thermal efficiency, higher steam output, superior heat transfer capabilities, and reduced fuel consumption compared to traditional fire tube boilers. Furthermore, modern water tube boiler systems are designed for increased safety, easier operation, and a significantly smaller installation footprint, making them suitable for a range of applications from power generation plants to petrochemical industries.
In the early days of boiler technology, numerous catastrophic failures occurred due to pressure part malfunctions in the steam section of boilers. The materials used in the construction of early boilers were inadequate to withstand the steam pressure they generated, often resulting in dangerous explosions. Initially, municipal boilers for district heating or process heating were small and multiple units were needed to meet community demands. To address this inefficiency, larger industrial boilers capable of producing higher steam pressure and greater thermal output were developed for facilities such as factories, refineries, and electricity power plants. However, the materials used in these early larger boilers continued to struggle with pressure resistance and long-term durability until advances in metallurgy and design improved reliability.
Boilers are engineered to produce steam by heating water with a burner, leveraging water's remarkable heat transfer properties for numerous applications, including space heating, process hot water, and electricity generation. In a traditional fire tube boiler, the tubes are submerged in a water-filled tank. A furnace heats the tube walls, which in turn heat the water, converting it into hot water and eventually steam. Despite water's excellent heat transfer capabilities, conventional boilers consume a significant amount of energy due to the lengthy process of heating the tubes through water's heat transfer.
Conventional boilers for industrial use require substantial space, often necessitating a dedicated boiler room due to their size and maintenance requirements. This spatial requirement restricts their application primarily to large industrial, manufacturing, and institutional facilities, and makes conventional boilers less appealing for modern manufacturing processes that demand compact, modular, and energy-efficient heating solutions.
Water tube boilers have gained popularity across industries because of their engineered efficiencies, rapid startup, compact footprint, and low overall energy consumption. In this design, water is encased by hot gases from the combustion chamber or firebox. As these combustion gases pass through the boiler, they heat the water within the tubes, rapidly generating high-pressure steam that can be used for electricity production, process steam, district heating, and other power needs. Water tube boilers provide superior heat recovery and operate efficiently at high pressure and temperature ranges, making them the preferred choice for critical operations in thermal power plants, chemical processing, and petrochemical facilities.
A typical water tube boiler consists of four main components: the water drum (or mud drum), the upper steam drum, water tubes, the furnace, and either a superheater or an economizer (heat recovery unit). The water tubes link the two drums, allowing water to circulate by both natural and forced convection. As the cooler water descends through the downcomer tube, the heated water rises to the top of the boiler. This efficient circulation ensures consistent steam quality, which is vital for applications ranging from turbine drives to industrial autoclaves.
The steam drum is responsible for collecting both steam and water, where they are then separated. This critical component is a large, elongated cylinder constructed from flat metal plates and situated at the top of the boiler. Water from the economizer enters the steam drum, where a scrubber or demister separates the generated steam from the water. The dry steam is then released from the steam drum and distributed to power turbines, heat exchangers, or other steam-driven processes, while the separated water is recirculated back into the boiler via downcomers to be converted into steam again.
Cooler, denser water flows from the steam drum through large pipes called downcomers to the mud drum, or water distribution manifolds, located at the base of the boiler. This essential water movement can occur through natural circulation (common in smaller or lower-pressure boilers) or be enhanced by a multistage centrifugal pump in forced circulation systems (often used in high-pressure water tube boilers). Typically, water tube boiler steam drums are equipped with at least six downcomers to ensure adequate water flow for optimal thermal performance and to prevent overheating or tube failures.
Located at the base of the boiler, mud drums collect sediment, dissolved solids, and impurities, acting as a reservoir for boiler water treatment. Because of the substantial accumulation of material in the mud drum, regular cleaning and scheduled blowdown are necessary to remove these deposits and maintain efficient boiler operation, preventing scaling and corrosion in high-pressure steam systems.
There are three primary types of steam drums found in water tube boiler systems: single steam drum, bi-drum, and multi-drum. The bi-drum design is often employed in industrial boilers for both power generation and process steam production due to its reliable pressure containment and ease of maintenance. Single steam drum boilers, commonly used in large power plants, are capable of operating at higher pressures and temperatures, which is ideal for supercritical and ultra-supercritical power generation applications. Multi-drum boilers allow for increased flexibility and larger steam generation capacity for heavy industrial loads.
The economizer, also known as a flue gas heat recovery unit, is a critical energy-saving device mounted on the stack of a water tube boiler. Its primary purpose is to capture and transfer waste heat from exhaust flue gases to the boiler feed water, preheating it before it enters the steam drum. This process significantly increases the boiler’s overall thermal efficiency while lowering operational costs by reducing the amount of fuel required to bring water to operating temperature. Integrating an economizer into a modern boiler system is a recommended practice in energy management and sustainability initiatives for reducing a facility’s carbon footprint.
There are two main types of economizers: condensing and non-condensing. Condensing economizers are the most efficient, recovering not only sensible heat but also the latent heat from condensation of water vapor in exhaust gases. However, they require flue gases to be cooled below their condensation temperature, which can be challenging and may require corrosion-resistant materials—especially in boilers that use fuel oil or biomass. By cooling flue gases to below this point, a condensing economizer allows water vapor in the gases to condense, thereby releasing latent heat that is transferred to the feed water, improving energy recovery.
Shell-and-tube economizers are the most widely used configuration, consisting of a shell with a series of internal tubes. In this design, hot flue gases pass through the shell while boiler water circulates through the tubes. The heat from the flue gases is efficiently transferred to the feed water via the tube walls, making this type suitable for high-capacity power station boilers and large industrial plants.
Plate economizers, alternatively, feature a series of metal plates arranged in either a parallel or staggered configuration. Flue gases pass through channels between the plates, while feed water flows between adjacent plates. The heat from the flue gases is effectively transferred to the feed water through the plate surfaces, making this design ideal for compact, modular boiler systems and retrofits.
Boiler economizer maintenance is critical to prevent fouling and ensure long-term heat exchange efficiency. Routine inspections and cleaning maximize energy savings, minimize downtime, and support consistent, reliable boiler performance.
The mud drum is positioned at the base of a water tube boiler and is linked to the steam drum via tubes. It holds hot water and gathers solids, minerals, and other impurities that settle at the bottom. These unwanted impurities are eliminated through a process called boiler blowdown, which involves removing small quantities of boiler water at set intervals to decrease impurity concentration. Effective blowdown is essential for boiler water treatment, preventing scaling, corrosion, and efficiency losses.
Water treatment chemicals—such as oxygen scavengers, anti-foaming agents, and pH stabilizers—are introduced into the feed water for both the steam drum and mud drum to prevent fouling, corrosion, and boiler tube deterioration. The treated feed water enters the boiler from the economizer and flows into both the steam drum and mud drum. As the water travels through downcomer pipes, it absorbs intense heat from the firebox and furnace before being delivered to the mud drum. Riser tubes then transport water or steam from the mud drum to the steam drum, maintaining continuous water and steam circulation throughout the boiler system, which is vital for high steam purity and thermal stability.
Mud drum design and maintenance are key considerations in water tube boiler system reliability, as buildup can cause inefficient heat transfer or localized overheating, leading to potential boiler tube failure or costly unplanned shutdowns.
Water tube boiler burners feature a short flame and a wide diameter, optimized for clean and efficient combustion. There are different types of burners, including single and multiple flame versions, designed to handle a variety of industrial fuels. A single flame burner can utilize two types of liquid gas fuels, while a multiple flame burner is designed for just one type. These burners are equipped with a central ventilation system and a wind box to efficiently distribute combustion air, ensuring consistent burner performance in high-demand industrial and power plant settings.
The performance and emissions of a water tube burner are influenced by several key combustion factors: oxygen and nitrogen concentration levels, combustion reaction temperature, and the residence time of nitrogen oxides (NOx) in the flame environment. Nitrogen oxides—harmful pollutants regulated by environmental agencies—tend to form in high quantities at temperatures exceeding 2800°F (1540°C). To maintain regulatory compliance and minimize environmental impact, water tube boiler burner designs focus on reducing NOx emissions through various advanced combustion control strategies.
Optimal burner efficiency hinges on achieving complete fuel combustion, precise control of the fuel-to-air ratio, and proper air-fuel mixing, which maximizes boiler energy output while minimizing unburned hydrocarbons and carbon monoxide emissions. Adjusting this ratio and creating fuel-rich or staged combustion zones at the flame front helps minimize the conversion of nitrogen to NOx, thereby reducing its formation. The ideal stoichiometric ratios are 10:1 for natural gas, 12:1 for fuel oils, and 24:1 for liquefied petroleum gas (LPG), but real-world adjustments are required depending on the specific fuel and load profile.
In modern power stations and large industrial plants, water tube boilers are equipped with multiple burners—sometimes numbering 20 or more—to generate sufficient energy to heat water tubes effectively and meet demanding steam loads. The boiler furnace or radiant section is structurally designed to accommodate the flames from all these burners and ensure maximum heat absorption by the tube surface.
Burners are categorized based on their fuel type and operating mechanism. The primary types of water tube boiler burners include diesel, gas, and biomass burners. Diesel burners support various liquid fuels such as fuel oil, kerosene, vegetable oil, and biodiesel, all of which must be pressurized prior to combustion in the burner chamber for complete atomization and ignition.
Gas burners operate with a range of gaseous fuels, including propane, butane, natural gas, hydrogen, and lighting gas. Unlike diesel fuels, gas fuels ignite more easily, do not require pre-pressurization, and are favored for clean energy applications due to their lower carbon footprint and reduced soot formation.
Biomass or pellet burners are eco-friendly solutions, supporting renewable energy and sustainable heating. The term biomass refers to the natural, organic materials used to create boiler combustion, flames, and heat—such as pressed sawdust, wood pellets, bioethanol, agricultural waste, forest residues, fruit peels, and pits. The unique physical properties of biomass fuels require that they be stored in a fuel storage tank close to the water tube boiler. Biomass boiler systems are widely adopted in sustainability-focused industries seeking to reduce greenhouse gas emissions and reliance on fossil fuels.
The burner’s flame ignites within the industrial boiler furnace or radiant section, generating intense heat energy primarily through radiant heat transfer. This hot gas heats the water flowing through the steam-generating tubes. The furnace walls consist of water-filled tubes or risers, which absorb the radiant and convected heat. These riser tubes are supplied with water from the mud drum at the base of the boiler and are positioned along four walls of the furnace—a configuration commonly referred to as a “water wall” in modern water tube boiler designs.
The riser tubes feature extensive tube surface area designed for maximum heat absorption, playing a crucial role as the evaporator section of the boiler. When water within these tubes is exposed to radiant and convective furnace heat, it quickly turns into high-quality steam, ready for use in steam turbines, industrial process heat, or combined heat and power (CHP) systems. The efficiency of the furnace directly impacts the overall energy performance of water tube boilers, making advanced furnace design essential to modern thermal power plants and high-efficiency industrial steam systems.
Boiler tubes in a water tube boiler play a crucial role in efficient steam generation and heat exchange. Positioned within the furnace walls, these tubes contain the circulating water that is heated by the burner to produce steam. To endure the high operating temperatures and pressures typical of industrial boiler systems and power plants, water tube boiler tubes are typically seamless and constructed from high-strength materials such as carbon steel, chromium-molybdenum alloy steel, austenitic stainless steel, and, for the most demanding applications, nickel-base superalloy materials.
Water tube boiler tubes are engineered for maximum resistance to thermal corrosion and stress rupture, providing longevity and consistent performance in medium to high-pressure steam systems. These tubes must exhibit superior heat transfer, fatigue strength, and resistance to oxidation, creep, rupture, and pitting. The thermal conductivity of the tube metal is especially significant, as it directly impacts the boiler’s ability to deliver rapid, reliable, and consistent steam output for continuous industrial operation.
Riser tubes within the furnace walls absorb thermal energy from the furnace flame. In specific high-efficiency boilers, refractory furnace linings and tube surfaces are coated with welded studs and refractory material to withstand intense heat and further augment the lifespan of the pressure parts. Most industrial water tube boilers feature tubes joined together by fins or strips to increase heat transfer surface area. These exposed tubes are integral to the rapid generation of steam in both on-demand and continuous steam generation systems. For high purity and safe operation, regular inspection of boiler tubes for corrosion, scaling, and wear is paramount.
The windbox plays a crucial role in the combustion process occurring around the burner of a water tube boiler system. It is a chamber that encircles the burner and is equipped with powerful fans that introduce controlled air into the combustion chamber. An adjustable damper on the burner modulates and directs the airflow to maintain optimal combustion conditions and reduces noise emissions. Airflow through the windbox is continuously monitored using instruments such as pitot tubes, airfoils, or flow restriction devices located in the duct system leading to the windbox, supporting the precise control demanded by modern low NOx burner technologies.
Windboxes may also be positioned behind the water wall to supply additional combustion air, helping to minimize air pulsation, maintain stable flame characteristics, and ensure consistent, complete combustion of all types of boiler fuels. In large-scale coal-fired water tube boilers, there are both primary air and secondary air systems. The primary air system regulates the introduction and mixing of solid fuels, while the secondary air system promotes further combustion efficiency, facilitates effective mixing with gaseous fuels, and supplies air to the windboxes for total boiler system optimization. This advanced air control is essential for compliance with modern boiler emission standards and for supporting overall steam system efficiency.
Water tube boilers are industrial steam generation systems that are categorized based on the type of fuel they utilize—a critical factor that directly influences operating costs, boiler efficiency, and environmental impact. As the global drive for sustainability grows, many traditional fuels have been replaced with more eco-friendly alternatives. This transformation, especially prominent in the 21st century, has broadened the spectrum of available boiler fuels, allowing facility managers and process engineers to select energy sources that meet both regulatory standards and their operational needs. Today, water tube boiler fuels come in a variety of forms to match the evolving priorities of energy efficiency, carbon emissions reduction, fuel availability, and long-term cost savings.
Water tube boiler fuels are classified into four main categories: solid, liquid, gas, and agricultural biomass. The fuel type chosen not only impacts annual operating expenses but also determines combustion characteristics, emission profiles, and maintenance requirements. Advanced fuels aim to maximize heat energy output—measured in British Thermal Units (BTU)—to efficiently generate the required steam for industrial and commercial applications.
Coal is historically the most widely used fuel source for boiler operation, particularly in large-scale industrial steam boilers and electric power generation plants. Its ability to be burned in natural lump form or processed (crushed) enhances combustion efficiency within boiler fireboxes. However, coal combustion produces substantial air pollutants, including sulfur oxides (SOx), nitrogen oxides (NOx), mercury, as well as fly ash—key contributors to environmental and health concerns. Due to regulatory pressure, coal-fired boilers are being phased out in favor of cleaner energy sources; nevertheless, coal remains essential in applications where a high steam output and reliable supply are required. Types of coal used include anthracite, bituminous, and sub-bituminous, each differing in carbon content and calorific value.
Natural gas is a highly preferred boiler fuel for industrial and commercial facilities owing to its clean-burning characteristics, affordability, and reliable pipeline supply. Composed mainly of methane, with trace amounts of ethane, propane, butane, and inert gases, natural gas systems offer high combustion efficiency and ease of control within water tube boilers. Burning natural gas produces significantly fewer greenhouse gases—such as carbon dioxide (CO2), sulfur dioxide (SO2), and particulate matter—than coal or oil, thereby supporting compliance with strict environmental regulations. Its low carbon content and availability make natural gas ideal for industries prioritizing low operational costs, reduced carbon footprint, and minimal maintenance due to lower soot and residue formation.
Liquid propane (LPG) is another clean-burning fuel, valued for its high energy content and flexibility of storage in pressurized tanks. Frequently used in commercial and small-scale industrial boilers, propane offers emissions that are considerably lower than those produced by traditional carbon-heavy fuels, such as coal and heavy oil. The convenience of delivery and lower maintenance requirements further enhance its appeal. While it shares advantages with natural gas—such as efficient combustion and straightforward burner management—propane is generally not recommended for very large, industrial-scale boilers due to supply limitations and long-term cost considerations. Propane can be employed in gas boilers, but is best suited for facilities with moderate energy demands where sustainable supply chains exist.
Fuel oil-fired water tube boilers operate by atomizing and igniting oil within specialized burners, providing rapid and intense heat transfer to the boiler tubes. Compared to gas, oil boilers deliver highly efficient energy conversion as nearly all combustion heat is transferred without significant waste. Unlike gas boilers linked to a supply main, oil fueled boilers require on-site storage tanks, introducing considerations for logistics and fuel stock management. Although oil fuels deliver strong performance and are suited for backup power generation or remote locations, their environmental impact is higher due to NOx, SOx, and particulate emissions.
In oil-fired water tube boilers, combustion optimization is achieved via steam atomization—breaking oil into fine droplets for thorough mixing with combustion air, promoting efficient burning and ignition. Innovative technologies, such as flue gas recirculation (FGR), are integrated to lower nitrogen oxide emissions by redirecting a portion of flue gases back into the burner, thus moderating flame temperature and reducing pollutant formation. While FGR contributes to cleaner operation, it may require adjustment to burner performance and slightly impacts overall system efficiency.
The solid fuel category for water tube boilers is diverse, encompassing traditional resources and emerging alternatives focused on sustainability. Classic solid fuels comprise coal and wood, the original boiler fuels. Expanding the category are materials such as bagasse (sugarcane pulp residue), municipal solid waste, refuse-derived fuel, shredded tires, and a wide array of agricultural by-products (e.g., rice husks, coconut shells, and corn cobs). Low-emission solid fuels—when sourced responsibly—can meet renewable energy targets, making them an attractive option for facilities seeking to minimize their carbon footprint. Modern water tube boilers are engineered to burn these solid fuels efficiently, accommodating variable fuel sizes and moisture content. Depending on design, the steam generation capacity of these systems can range from 25,000 PPH (pounds per hour) up to 500,000 PPH, supporting even the largest industrial heating and process steam applications.
Biomass is at the forefront of renewable energy solutions for water tube boiler systems. Utilizing organic matter such as wood chips, wood pellets, sawdust, or agricultural residues, biomass boilers are particularly effective in reducing net carbon emissions since the CO2 released during combustion is largely offset by tree growth and plant photosynthesis. These renewable fuels are gaining traction in the food and beverage industry, dairy processing, pharmaceutical manufacturing, and district heating networks. Due to the bulkier nature, biomass boilers are sized larger than their fossil-fueled counterparts to accommodate combustion volume and ensure adequate heat release.
Modern biomass boiler systems include an automated feed hopper, enabling continuous, controlled supply of fuel to the combustion area and minimizing labor requirements. This automation increases operational efficiency, fuel consistency, and safety. Wood pellets are among the most widely used biomass fuels due to their high energy density, ease of bulk storage, and uniform quality. For facilities seeking LEED certification or compliance with renewable portfolio standards, advanced biomass-fired water tube boilers are a preferred investment.
The American Society for Testing and Materials (ASTM) has established rigorous technical specifications for fuel oil used in water tube and fire tube boiler systems. There are six recognized grades, each tailored for specific burner technologies and industrial operating conditions. Grade No. 1 oil is used in residential and small industrial burners, while Grades No. 2 through No. 6 serve larger atomizing burners and high-demand industrial boilers. These classifications reflect variations in viscosity, boiling range, API gravity, and typical heating value—all important considerations for selecting the optimal fuel for energy output, cost control, and emissions compliance.
Fuel Oil Grades | |||
---|---|---|---|
Grades | API Gravity | Density lb/gal | Heating Value Btu/gal |
1 | 38 to 45 | 6.950 to 6.675 | 137,000 to 132,900 |
2 | 30 to 38 | 7.296 to 6.960 | 141,800 to 137,000 |
4 | 20 to 28 | 7.787 to 7.396 | 148,000 to 143,100 |
5L | 17 to 22 | 7.940 to 7.686 | 150,000 to 149,400 |
5H | 14 to 18 | 8.080 to 7.890 | 152,000 to 149,400 |
6 | 8 to 15 | 8.448 to 8.053 | 155,900 to 151,300 |
Optimizing the air-to-fuel ratio is crucial for maximizing boiler combustion efficiency, reducing excess oxygen, and preventing equipment damage or heat losses, irrespective of the energy source. This proportion directly determines how effectively a given fuel (such as oil grades #2, #4, #6, diesel, gasoline, natural gas, propane, coal, wood, or biomass) is burned to achieve desired steam outputs. An imbalanced air-to-fuel ratio can lead to incomplete combustion, heightened emissions, elevated fuel consumption, and accelerated wear on boiler components. Industrial boiler operators rely on precise instrumentation and control systems to continuously monitor and adjust this ratio, achieving higher system reliability, lower emissions, and reduced operational costs.
Additional Considerations for Fuel Selection: When evaluating which fuel to use for a water tube boiler, decision factors include regional fuel availability, long-term price stability, regulatory emissions compliance, safety, required maintenance schedules, and integration with existing energy infrastructure. Steam system efficiency, life cycle costs, and sustainability objectives should also be weighed. Newer fuel technologies, including waste-to-energy, co-firing (combining biomass with fossil fuels), and even hydrogen are emerging, offering facilities even more flexibility in balancing energy needs with environmental stewardship.
By carefully considering fuel properties, combustion technology, boiler design parameters, and environmental impacts, organizations can select the optimal fuel solution to maximize performance, efficiency, and regulatory compliance for their water tube boiler installations.
Water tube boilers come in various types, including single pass vertical and bent tube designs. They are favored in industrial and utility settings due to their capability to handle design pressures up to 2000 psig, temperatures reaching 1000°F (537.78°C), and capacities of up to 500,000 pounds per hour (PPH).
Water tube boilers come in several types, including A Type, D Type, and O Type, named according to their shape. Other types include simple vertical, Stirling, and Babcock and Wilcox. Stirling boilers were developed during the first industrial revolution and later acquired by Babcock and Wilcox in 1906. Today, Babcock and Wilcox continues to build modern, technologically advanced boilers.
An A-type water tube boiler features two water drums connected by a shared header. In this design, evaporated water is transported upwards through risers into the steam drum and steam header. A-type boilers are known for their water-cooled furnace and vertical gas outlet, which reduce the boiler's footprint and allow for high steam capacity in a compact size. The triangular arrangement of the two water drums and the steam drum gives the A-type water tube boiler its name.
In an A-type water tube boiler, water fills the space between the drums, with the furnace positioned at the center. These boilers can be fired by coal or oil and feature multiple fire doors for stoking. Originally designed for battleships, A-type water tube boilers were created to deliver high power within a compact footprint.
D-type water tube boilers feature a large steam drum positioned at the top, connected to a mud drum at the bottom. Steam is generated in the tubes or risers and rises to the steam drum. The furnace includes water-filled tubes along its four walls, known as water walls. This design facilitates excellent water circulation, enabling rapid steam production and generation.
D-type water tube boilers are capable of generating steam at up to 1,000,000 PPH with pressures reaching 2000 psig. They are built for durability, endurance, and longevity, making them ideal for applications that require high-pressure superheated steam while maintaining a compact footprint.
In an O-type water tube boiler, the steam and mud drums are vertically aligned, one positioned above the other. They are connected by curved water pipes that form the shape of the letter "O." These boilers are fired by liquid burners, and the combustion chamber is situated between the curved convection tubes and the water wall tubes.
Similar to D type water tube boilers, O type water tube boilers are well-suited for conditions with limited space. Access to the O type boiler is available at both ends. These boilers are known for their durability and long service life. O type water tube boilers can achieve an output of up to 250,000 PPH with pressures reaching 900 psig.
Vertical water tube boilers differ from other types in that they are oriented vertically rather than horizontally. Historically, they were used to power vehicles such as early steam locomotives. In these boilers, water is heated within the cylindrical shell.
Fuel is placed onto the grate within the furnace of the vertical water tube boiler to generate hot gases that heat the vertical tubes. Ash residue from the fuel falls through the grate into an ash pit. The steam produced in the tubes is collected until it reaches a desired level and is then released to power machinery.
The firebox is tapered toward the top to facilitate the passage of steam to the top of the cylinder. The cross tubes are inclined to enhance their heat exposure and improve water circulation. An uptake tube extends from the top of the firebox to the boiler's chimney.
The Stirling boiler, a high-capacity bent tube boiler introduced in 1888 by Alan Stirling, can produce up to 50,000 kg/hr with pressures reaching 60 kgf per cubic meter. It is designed primarily for central power stations. This boiler features three steam drums positioned at the top and two mud drums located at the bottom. The steam and mud drums are interconnected by a network of bent tubes that are resistant to expansion under heat.
In keeping with 19th-century practices, the drum structure is encased in brickwork with a fire door at the base. A circulating tube links the steam drums, extending from the central drum, which gathers the steam. Positioned beneath the mud drums, the furnace heats the water contained in the mud drums. Steam from the steam drums is then converted into superheated or dry steam by a superheater.
The Stirling boiler is one example among many types of water tube boilers. As technology evolves, new designs and configurations are continually refined. However, all water tube boilers share the core principles of utilizing a fuel source, water, and tubes to produce steam.
Water tube boilers are widely utilized because they can manage both high pressure and temperature conditions effectively. Their exceptional efficiency in transforming fuel into valuable energy contributes to their broad application across various sectors. These boilers are favored for their dependable and secure operation.
Boilers primarily serve the purpose of generating power, which was why they were vital during the early days of the industrial revolution. The dependable performance of water tube boilers has solidified their role in power plants, where they generate steam to drive turbines and produce electricity.
The chemical and petrochemical sectors demand reliable power, flexibility to handle varying loads, and adherence to emission standards. Water tube boilers are capable of fulfilling these requirements due to their high efficiency and dependable operation. They are employed to generate steam for processes such as refining, distillation, and cracking.
Water tube boilers play a critical role in the pulp and paper industry by providing the necessary steam for drying paper, meeting energy needs, and cooking wood chips during the initial manufacturing phase in the digester. The steam generated ensures consistent heating, precise temperature control, and optimal efficiency throughout the process.
In the food and beverage industry, water tube boilers are essential for preparing food products consistently and efficiently. They produce large quantities of steam and hot water, which are crucial for mass production processes. The primary advantage of using water tube boilers is their capability to generate high volumes of steam and hot water, ensuring that food products are smooth, tender, and easily digestible. Additionally, these boilers contribute to maintaining the optimal environmental conditions within food processing facilities.
In the pharmaceutical sector, water tube boilers are subject to stringent demands, requiring precise temperature control for tasks such as drying, sterilizing, and purifying chemicals and equipment. A critical concern for all types of boilers in this industry is the generation of clean steam. Water tube boilers, with their advanced filtration systems, are particularly well-suited to provide the high-quality steam needed for pharmaceutical applications, ensuring both purity and efficiency in the production process.
In the textile industry, the primary requirement for water tube boilers is the ability to deliver rapid steam at temperatures of 265°F (129.4°C) for dyeing and finishing operations. Due to the variable demand in textile production, relying on fire tube boilers can be inefficient and expensive. Water tube boilers play a crucial role in the early stages of textile manufacturing, supplying the necessary energy for fabric pretreatment and facilitating precise heat control for printing processes.
For decades, water tube boilers have been a reliable choice for heating residential, industrial, and commercial spaces. Their widespread use in heating systems is due to their dependable performance and accurate temperature control. The even distribution of radiant heat from a water tube boiler ensures that buildings and work environments remain comfortably warm and conducive to productivity.
A flexible tube boiler, often referred to as a flex boiler, features a network of compact, curved tubes rather than the traditional long, straight tubes. Water flows through these smaller tubes and is heated by combustion gases. Because the tubes are smaller and more numerous, the flex boiler heats water more quickly. The design allows for greater surface area exposure to the hot gases, facilitating a faster conversion of water into steam.
The flexible tube boiler design offers several notable benefits. One of its key features is the arrangement where the fire is positioned outside the tubes while the water circulates inside. This design results in a low water volume and quick heating capabilities, allowing the boiler to reach 100 psi within ten minutes. The rapid heating reduces fuel consumption. Despite the bends in the tubing, the flexible tube boiler is resistant to thermal shock, as the tubing's flexibility helps mitigate the risk of damage from temperature fluctuations.
Flexible tube boilers are designed to reduce thermal stress while providing a rapid response in a compact and robust unit. Many models can achieve pressures of up to 500 psig or higher and maintain an efficiency rating of 90%. Their performance and reliability make them a preferred choice for institutions such as universities, hospitals, office buildings, and manufacturing facilities.
Water tube boilers are highly favored for their efficiency, as they experience minimal heat loss due to the direct interaction between water-filled tubes and combustion gases. This design allows them to quickly transform substantial amounts of fuel into valuable energy.
Boiler rental is a service that is offered by boiler manufacturers to assist customers in times of emergency, high usage, or as a cost effective permanent solution. Every type and size of boiler is available for rental from ones...
A high pressure boiler is a shell and tube heat exchanger that use boiled water to create steam or high pressure hot water. Using water filled tubes in a metal tank or enclosure, they create power by converting water into steam through thermal energy, which is used...
A steam boiler is a steam producing heating system. It creates energy by heating water to get steam. It is a heat exchanger that makes steam for outside usage and has a combustion chamber and water container. The several varieties of steam boilers include...
A conveyor oven is a continuous flow oven; it‘s an oven that is open on opposing sides and has a conveying system running from one end of the oven to the other. Designed like a batch oven, conveyor ovens have the additional benefit of keeping products moving while providing continuous and uniform heat...
A furnace is a direct fired device used to provide heat for industrial processes that require heat in excess of 400° C (752° F). Any industrial application that relies on heat to create a reaction or heat materials for production uses an industrial furnace...
A curing oven is thermal processing equipment used by thermal specialists to improve or enhance the strength and durability of materials. Many factory processes such as baking, drying, heating, cooking, and curing require...
An industrial oven is a device used to create extremely high temperatures to heat treat parts, condition metals, and cure metal coatings. Common functions for industrial ovens include drying, curing, testing, and coating of parts and products...
An infrared oven is an oven that heats objects or cooks food using infrared radiation instead of conventional conduction or convection heating. People can use infrared ovens in commercial kitchens, homes, or...
A normal function of an industrial furnace is to heat treat metals for annealing, tempering, or carburizing and pre-treat materials for forging. Though metal is a common material to be treated using an industrial furnace, other materials are also...
Industrial ovens are thermal processing machines used as heating chambers for drying, curing, and baking of foods, parts, and components. The main industries that use industrial ovens are chemical and food processing and electronics manufacturing...