Belt Conveyors
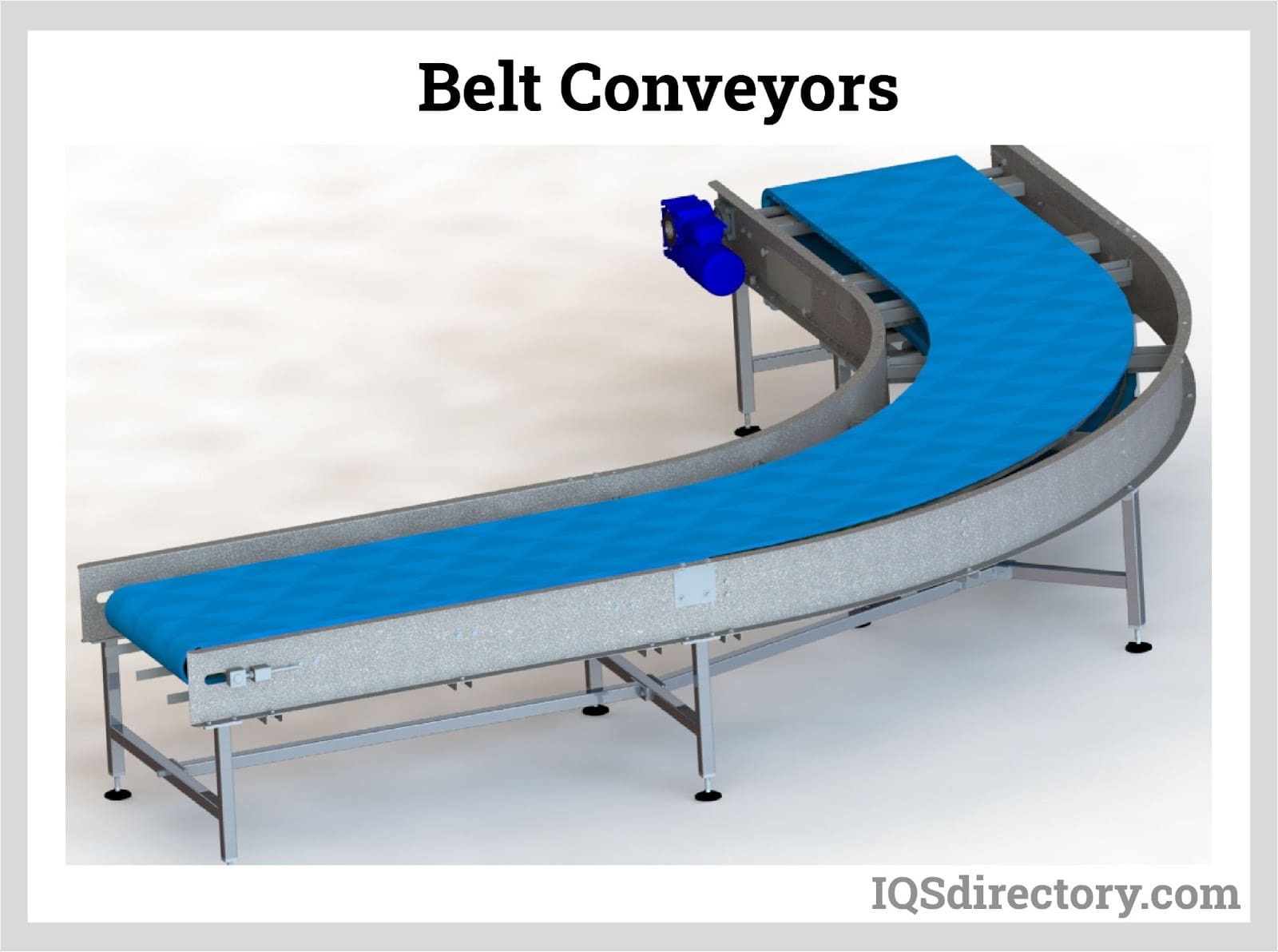
A belt conveyor is a system designed to transport or move physical items like materials, goods, even people from one point to another. Unlike other conveying means that employ chains, spirals, hydraulics, etc...
Please fill out the following form to submit a Request for Quote to any of the following companies listed on
This article will take an in-depth look at bucket elevators/conveyors.
By reading this feature, you will understand more about topics such as:
Bucket elevators, alternatively known as grain legs, serve the purpose of transporting bulk materials efficiently. Primarily utilized in industries such as commercial agriculture and mining, these systems are meticulously crafted and supplied by specialized manufacturers.
Bucket conveyors are equipped with dual-strand roller chains designed to transport materials both horizontally and at an incline. With a sturdy build and energy-efficient operation, these conveyors excel in handling hot and abrasive materials. Importantly, the buckets maintain a stable position without tilting to release the cargo.
Frequently called bucket conveyors, these apparatuses are engineered to transfer materials upward between various levels in a facility. While "elevator" and "conveyor" are terms often used interchangeably, they describe distinct bucket transportation system layouts.
These machines, commonly referred to as bucket elevators, facilitate the vertical lifting of goods using a series of buckets propelled by centrifugal force.
Conversely, bucket conveyors are implemented to move materials along an inclined path, closely resembling vertical conveyors. A notable distinction is that bucket conveyors are simpler and are optimal for handling delicate items and products.
Designed to efficiently scoop up materials, the buckets feature scooped edges and maintain an upright position to prevent spillage. A bucket elevator might commonly be used for transporting materials such as ore, fertilizer, or grain. In a straightforward vertical bucket elevator system, bulk materials are elevated to the top, discharged, and the empty buckets return to the bottom to collect a new load. The discharged materials navigate a chute to storage bins, packaging, or further systems. The operation is largely automated, with minimal human oversight beyond monitoring and adjusting. Advanced systems can be programmed for periodic unloading. Safety protocols are essential to protect operators and bystanders from moving components, especially in chain-driven systems where loose clothing or hair poses potential hazards.
Bucket conveyors employ reciprocating buckets for the vertical transport of materials, commonly aggregates or bulk items. Structurally, the system consists of interconnected troughs or buckets that ascend while maintaining a steady level to avoid spillage. Material is introduced at the "boot," or front end, with each bucket mechanically emptying at the discharge point. This approach to vertical transportation is swift and automated. Proper construction ensures durability and effectiveness, tailored to the specific material and transport height required. Ideal for dry, light, or powdered materials, these conveyors typically avoid wet or sludge-like substances to prevent discharge interference.
Bucket elevators are built for continuous operation, akin to other industrial machinery. Frequent stops and starts heighten spill risks, can cause damage, and reduce efficiency. Operational schedules might range from specific daily hours to near-continuous use, depending on processing demands. Equipped with emergency stop features, the bucket elevator allows immediate shutdown when issues occur. Advanced models may include sensors to detect and halt operations if obstructions are sensed.
Style AA: The centrifugal elevator bucket of style AA features a robust cast iron design. This bucket is reinforced with a strong rear wall and durable corners and lips. It is commonly used for handling materials like stone, sand, gravel, coal, fertilizer, clay, salt, limestone, and concrete. The AA bucket is well-suited for challenging and abrasive industrial applications.
Style MF: The MF style (medium front) steel elevator bucket is designed with a reinforced rear wall, sturdy corners, and thickened lips. It is typically used for handling materials such as pellets, clay, alumina, and fertilizer. The MF bucket is ideal for materials that flow easily or require gentle handling.
Style AA Ductile Iron Buckets: The Style AA ductile iron (DI) elevator buckets are built to exceed the requirements of rigorous industrial environments. These buckets feature enhanced durability, with thicker walls and a reinforced front lip, making them ideal for high-impact and abrasive applications.
These buckets are constructed with reinforced walls and a fortified front lip, enhancing their durability and lifespan in challenging industrial conditions. Ductile iron offers superior impact and abrasion resistance compared to malleable iron, ensuring that buckets made from ductile iron provide extended service life and more efficient operation.
Welded AA Buckets: A welded AA bucket generally consists of three main sections, with end caps either attached to the sides or continuously welded. The bucket's sides are usually straight, and the front features a reinforced wear lip designed for added strength.
Welded MF Buckets: For welded MF buckets, a front plate is generally inserted between a press-formed body and welded continuously to the body at the outer seams, which are typically made up of two sections.
The most common areas of wear on an elevator bucket are the front lip, edges, and sidewalls. Buckets that engage in digging actions at the boot area experience accelerated wear. To address this, a digger bucket can be used. A welded MF digger bucket is designed to endure the additional stress of digging operations and is slightly larger than standard buckets, which helps minimize wear on adjacent buckets and the surrounding area.
Belting is a critical component of bucket elevators, and selecting the appropriate belt for your specific needs is essential. In industries such as grain handling, belts must be designed to be static-conductive, resistant to oil, and flame-retardant to meet safety and performance standards.
Proper traction is vital for ensuring that the belt operates smoothly. Adjustments can be made to the take-ups in the boot to influence traction. Additionally, the head pulley must feature effective slide lagging to grip the belt securely and prevent slippage. A crown on the head and boot pulleys helps maintain the belt's alignment, with a typical crown of 1/8 inch for every 12 inches of belt width.
New belts often experience an initial stretch of 1.5–2% within the first few days or weeks. It may be necessary to adjust the belt tension during this period. Over time, belts can stretch again, indicating that internal cords are aging and could lead to eventual belt failure.
Repeated stretching of the belt suggests that the internal cords are deteriorating, which could result in a breakdown. Regular inspection for signs of wear or cover loss is crucial. Loss of belt cover reduces static conductivity and traction, and increases the risk of fire or explosion if the belt fails to discharge static electricity properly.
PVC belting is characterized by its single-ply construction with a woven cloth carcass at its core. This design provides flexibility, allowing it to navigate smaller pulleys. However, PVC belting offers moderate resistance to oil, which may limit its suitability for some applications.
Rubber Belting: Multi-ply rubber belting has a woven fabric carcass and moderate-to-superior oil resistance. Rubber is an excellent option for feed products that contain fat.
Continuous bucket conveyors are designed to transport lightweight or delicate materials without gaps between the buckets, which helps prevent spillage. These conveyors operate at slower speeds, typically between 3 and 5 feet per second. The system fills each bucket individually, eliminating the need for digging, and relies on gravity to discharge the material. This design is particularly effective for handling fragile or easily breakable products, as it minimizes aeration and potential damage. Continuous bucket conveyors can be configured in various shapes such as S, Z, or C, and are available in different capacities. They are ideal for heavy-duty tasks in industries like mining, plastics, and other sectors where minimal agitation is required.
Positive discharge conveyors utilize an extra sprocket to eject material from the discharge end, distinguishing them from other centrifugal conveyor types. These conveyors operate at lower speeds, ranging from 2 to 4 feet per second, which helps reduce spillage and prevent damage to the material. To compensate for their slower speed, the buckets used are typically larger, a design feature that varies by manufacturer. These conveyors are particularly beneficial for applications where preserving the quality of the product is crucial, such as with cereals, nuts, dried fruits, and similar items. Despite their advantages, they tend to be more costly compared to other bucket conveyor systems and come in a variety of configurations and sizes.
Free-flowing material is moved by centrifugal force using centrifugal bucket conveyors. To optimize centrifugal force, evenly spaced buckets on a chain gouge into the material at the inlet before throwing it out of the discharge throat, usually directly after the top turn of the chain. Any material left over will fall back down, and the conveying process will start again since these buckets are enclosed in a metal enclosure that prohibits material from exiting anywhere other than the discharge end. They can run up to 350 feet per minute and have a capacity of up to 100 pounds per cubic foot. They are capable of both low and high speeds. Some centrifugal elevator versions can travel up to 1000 feet per minute, although these are only appropriate for lighter materials. Centrifugal bucket conveyors are a desirable option for grain, mineral, sugar, and chemical applications because they perform best with fine materials and are suitable for higher-speed applications.
Chain bucket elevators are effective for handling dry materials, even though they include various components that are prone to wear and breakage. To maintain efficiency and minimize the effects of grit, these systems require lubrication with thick grease. The capacity of these elevators is mainly determined by the size of the buckets they can accommodate. Some models can function both as elevators and conveyors, offering the flexibility to receive or discharge material at multiple points along their trajectory. The integration of a conveyor belt enhances their ability to handle heavy loads and lift materials vertically. Additionally, the design of the buckets provides excellent stability and reduces the likelihood of spillage.
In a chain bucket elevator, two chains are employed to transport the buckets from one location to another. Any material that is rejected during this process is subsequently lifted and returned to the main flow by the elevator.
In a chain bucket elevator, rejected material is elevated and redirected back into the primary flow following a C-shaped path.
The Z lift mechanism of the bucket chain elevator utilizes a Z-shaped trajectory to reintegrate the rejected material into the main flow.
An entrance hopper, a vibration feeder, buckets, a gear-motor drive, inspection hatches, and an outlet chute make up the chain bucket elevator. A geared motor continuously moves the buckets around while placed on a chain. The buckets are poured into an output chute at the top of the apparatus. In the lowest part, there is a drawer that makes cleaning simple. The chain can be adjusted manually.
Belt bucket elevators are widely used for lifting both wet and dry ores. They offer an advantage over chain-bucket elevators in wet conditions because they don’t require complex or costly lubrication and have fewer surfaces prone to wear and friction. The capacity of a belt bucket elevator is limited by how well the belt adheres to the head pulley, though this can be improved by using a less slippery material for wrapping the pulley. These elevators occupy less floor space compared to inclined conveyors and are capable of handling thin slurries. When maintenance is necessary, it is important to have a method for emptying the elevator's boot, ideally in a location where the material can be easily rinsed or transferred to another system.
The bucket lifter (BL) is designed to transport materials from one location to another using one or multiple buckets. It is specifically suited for handling smaller materials compared to chain or belt bucket elevators. The bucket lifter provides a straightforward and cost-effective solution for moving items between points.
A gear motor, one or more buckets, a chain or belt, and a steel frame make up the bucket lifter. A loading station at the bottom ensures the exact dosage of the bucket(s). When tilted, the bucket(s) are raised to the top and emptied. The bucket tilts back to the bottom after a certain amount of time, ready for the next filling. If there are multiple buckets on the bucket lifter, they are all returned to the bottom part after being emptied one at a time. The bucket lifter is made of stainless steel or painted steel and has a sturdy frame construction.
Using multiple-discharge bucket conveyors, a product can be elevated and transported to numerous locations, such as nearby feeding numerous bagging or packaging machines. This bucket conveyor design also allows for many infeed points, making it a more affordable option than multiple conveying machines.
Indexing bucket conveyors feature a unique design and functionality. These conveyors are timed to deliver a precise amount of product to each bucket, which then transfers the goods into a packaging machine.
Skid steer conveyor buckets are designed to handle tasks such as replenishing bedding material, spreading mulch, or applying sand in landscaped areas. They often come with side discharge options and are available in different diameters to fit various skid steer models. These buckets vary in width and can be used with materials like sand or sawdust, with the sawdust variant also suited for mulch. Each of these attachments provides distinct benefits and is operated using the joystick controls within the cab, integrating seamlessly with the machine's hydraulic system.
Skid steers are agitators with a hydraulic motor in a sand arrangement. Three direct drive motors that are all operated by standard flow hydraulics and each individually controlled by the stroller switch in the side of the cab are installed on the side discharge buckets. Depending on where the material needs to go, the operator can eject the material left or right. A 12-inch wide heavy-duty belt in this sand model ejects the material, in this case, out the left side. The flow of material onto a bed, the side of a home, or a barn stall can also be adjusted using an ejector limiter, an adjustable plate that moves up and down. The frame shields the hydraulic motor. This hydraulic motor is the agitator motor, running continuously while the other two hydraulic motors power the belt. The material loading out front can also be done using these buckets. The cutting edge can feature a weld that the user can utilize to load mulch, sand, sawdust, or straw. The side discharge buckets include replacement wear pads by the belt and bolts on normal flow hydraulics. The material accumulates and wears on these bolts on replaceable plates due to the belt's constant rotation. Both the straw and sawdust configurations have a leveler or equalizer that enables the material to cascade down onto the belt equally and then be expelled into the desired location. The sand design has an agitator.
Unlike traditional elevators, horizontal elevators do not use cables. Instead, they employ linear motor technology, similar to that used in magnetic levitation trains, to operate their ropeless systems. This allows multiple cabins to travel in a continuous loop, ascending one shaft and descending another, much like trains moving along a rail network. A key advantage of this approach is that horizontal elevator systems can carry up to 50% more weight per shaft compared to conventional lifts.
Bucket elevator design influences the lubrication and tensioning processes. Heavy chains using bucket elevators require regular lubrication and tensioning. In summary, bucket conveyors have an excellent conveying capacity and require less maintenance.
Bearing Lubrication: Bucket elevators have four key lubrication points: two at the head bearings and two at the boot take-up bearings. Each point should be lubricated at least once a week under standard operating conditions. The equipment manual provides recommendations for bearing lubricants based on typical temperature ranges. For detailed maintenance and lubrication practices, refer to the manufacturer's guidelines.
Chain and Sprocket Drive Lubrication: Despite the chain drive being splash lubricated, it is essential to check the oil level before each operating shift. The oil level can be monitored through the sight gauge located on the drive guard's side. If the oil level is low, top it up as needed. For specific lubrication instructions, consult the bucket elevator manual.
Periodically inspect the oil for contaminants. If pollutants are detected, drain, flush, and refill the oil. Additionally, the chain should be dipped in a nonflammable solvent to remove debris, dirt, or water from the bushings, rollers, and sidebars. Clean the sprockets as well, and use compressed air to dry both the chain and sprockets thoroughly.
Regularly examine the drive chain and sprockets for signs of wear or damage. Remove the upper drive guard and rotate the sprockets and chain slowly to check for issues. This method is the most effective for inspecting these components. Replace any parts showing significant wear or damage. Additionally, verify sprocket and shaft alignment, and check chain slack to ensure proper drive alignment. For more details on these procedures, refer to the bucket elevator manual.
Splice: The splice is a critical element that affects belt performance and can lead to belt failure if installed incorrectly. Ensure that the splices match the belt width precisely. A template is provided to guide the placement of holes for the splice installation. Use a power punch, rather than a standard drill, to create these holes.
Throat Plate: Although it may be overlooked, the throat plate plays a vital role in the efficiency of your bucket elevator system. Properly installed and maintained, it prevents material from falling back into the boot pit and ensures proper discharge from the elevator. Position the throat plate as close to the buckets as possible for optimal performance. Mechanically-made splices can provide a more secure fit.
>Venting: Proper ventilation can significantly enhance bucket performance. Venting facilitates the removal of air from the bucket during filling, which improves material handling. It also allows air to enter the bucket during discharge, promoting the smooth exit of material. Different venting patterns are available for various applications.
Bolts: Bolts come in a wide variety with various characteristics. The industry standard is the No. 1 Norway elevator bolt, which has a square shoulder and a flat back. It is the most prevalent and affordable elevator bolt. However, Norway bolts should be tightened again over time because vibrations can cause them to loosen. The fanged elevator bolt is another popular variety; it has teeth that stick into the belt to keep it in place. Fanged bolts can be used with a resistant nylon lock nut because they are non-rotating. In some applications, fanged bolts are preferred to Norway bolts despite being more expensive because they are far less prone to loosen due to vibration.
A belt conveyor is a system designed to transport or move physical items like materials, goods, even people from one point to another. Unlike other conveying means that employ chains, spirals, hydraulics, etc...
Processing equipment for holding and moving bulk bags is known as bulk bag equipment. This bulk bag equipment is typically used at the front end of the production process to hand off product to...
A conveyor belt is a material handling system designed to move supplies, materials, and components using an efficient and effortless process that saves on time, energy, and cost. The design of conveyor belts includes two motorized pulleys with the conveyor material looped over them...
A conveyor system is a method for moving packages, products, supplies, parts, and equipment for production, shipping, or relocation. The different types of conveying systems include pneumatic, screw, belt, and roller. The construction of individual systems depends on the materials...
Flat belts are power transmission belts that are flat and made of rubber, synthetic composites, or leather. They are used to transfer rotational power in industrial equipment and conveyor systems. Flat belts have a low profile with a positive grip, which...
A metal conveyor belt is a conveyor belt that uses metal in the form of flat sheets or woven wire mesh as its belt surface. The use of a metal surface enhances the ability of a conveyor to handle parts and...
Pneumatic conveying is a method for transferring bulk materials, like powders and granules, using compressed gas or air, from one processing center to another. Material is moved through an enclosed conveying line or tube using a combination of pressure differential and airflow from a blower or fan...
Screw conveyors, or auger conveyors, are industrial equipment used in transporting bulk quantities of granular solids (e.g., powder, grains, granules), semi-solids, liquids, and even non-flowing materials from one point to another...
A timing belt is made of rubber with hard teeth capable of interlocking with camshafts and crankshafts cogwheels. It is an integral component of an internal combustion engine responsible for...
Roller conveyors are a type of conveyor belt that allows objects to skate on its surface by using rollers, which are equally spaced revolving cylinders. They transport stuff from one location to another...
A vertical conveyor is an engineered mechanical method for moving goods, products, supplies, parts, and components from a lower level to a higher level or from a higher level to a lower level. They are...
Vibratory conveyors are material-handling equipment used to transport fine to coarse-grained bulk materials. These vibratory conveyors are strong conveying equipment utilized for bulk commodities with fine to coarse graininess...
A v-belt is a flexible machine element used to transmit power between a set of grooved pulleys or sheaves. They are characterized as belts having a trapezium cross-section...
Vacuum conveyors are suctioning machines that utilize air pressure in order to move materials through an enclosed pipeline. Vacuum conveyors have broad applications throughout the industrial and...