Force Calibration
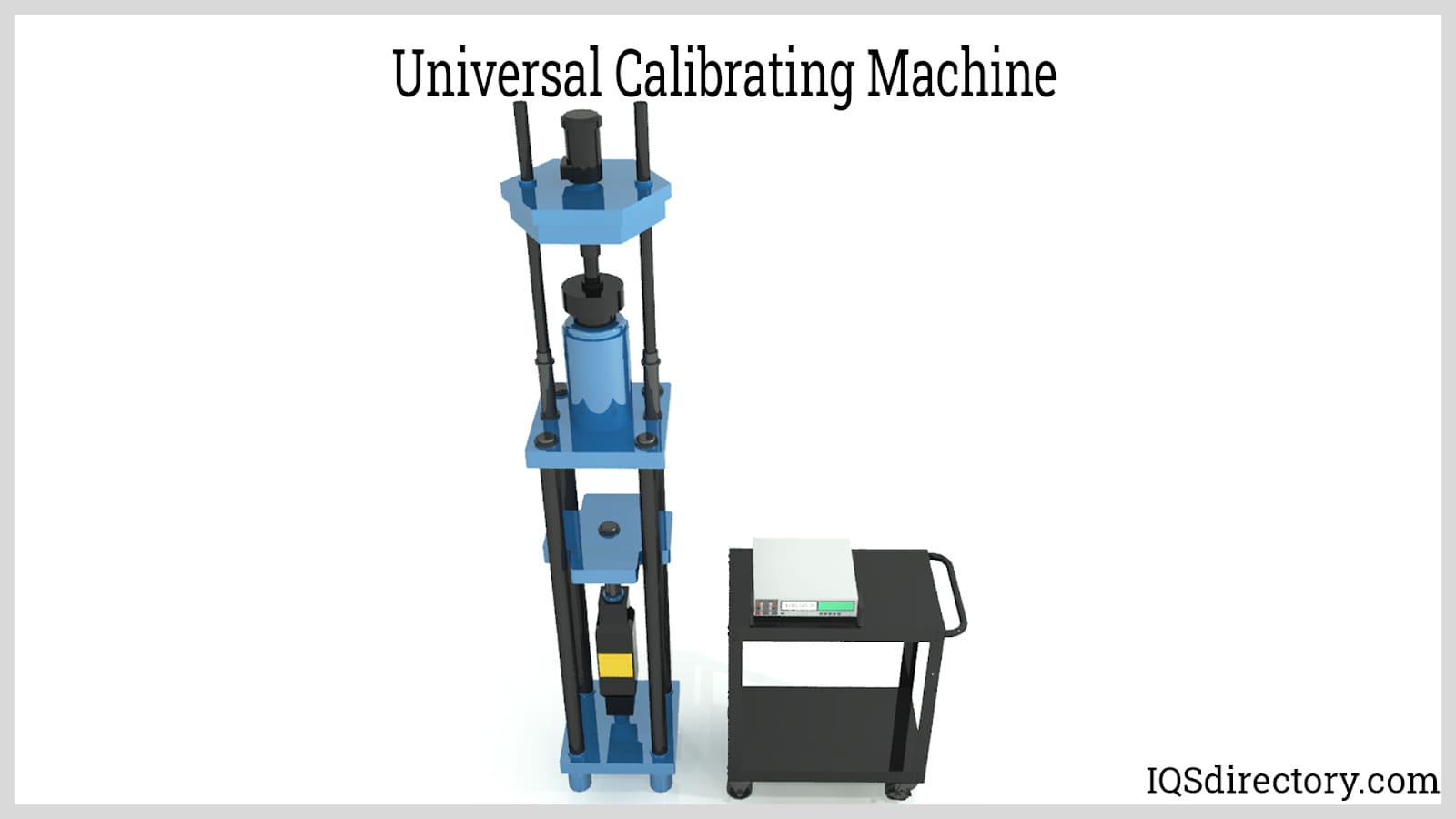
Force calibration is a necessary process used for testing materials used for manufacturing equipment, machines, and other devices. All forms of metals and other materials can expand and contract during their use...
Please fill out the following form to submit a Request for Quote to any of the following companies listed on
This article provides a detailed look at.
Read further to answer questions like:
Calibration services are specialized in detecting inaccuracies and uncertainties within measurement instruments or equipment. In the calibration process, the device under test (DUT) is meticulously compared to a recognized reference standard to determine the extent of deviation from the accurate or ideal measurement value. This deviation is termed as an error. Upon identifying this error, the DUT can be adjusted to enhance its measurement precision. However, this correction process, which aims to fine-tune or trim the device, is carried out separately.
Calibration must be executed as a formal procedure within a certified and controlled calibration laboratory environment. Some providers offer on-site calibration services, facilitating the process for clients by avoiding disruption of operations as equipment is calibrated directly at the point of use.
Upon completion of the calibration, the service provider delivers a detailed certificate to the client organization. This certificate includes the specific calibration results, tailored to the instrument, which is essential for accurate documentation and traceability. Additionally, a calibration label might be attached to the equipment to clearly indicate that the device has undergone calibration.
The International System of Units (SI) is a globally recognized and standardized measurement system. Originating from the French term "Système International d'Unités," the SI system is more broadly known as the metric system. Designed for accuracy and consistency, SI units provide a universal method for expressing and comparing physical quantities in a manner that fosters clear communication and collaboration. Standardized measurement is a critical foundation for science, engineering, manufacturing, pharmaceuticals, and a wide variety of industrial quality assurance processes.
The SI system was established in 1960 by the 11th General Conference on Weights and Measures (CGPM, Conférence Générale des Poids et Mesures). It operates under the authority of the Bureau International des Poids et Mesures (BIPM), an international organization based in Paris, France, which has the mandate to maintain global measurement uniformity and consistency in physical measurements, regulatory compliance, and laboratory calibration services.
The SI system comprises seven fundamental base units from which all other derived units are formed, covering essential measurement categories such as length, mass, time, electric current, temperature, amount of substance, and luminous intensity. For example, the most stable reference for length is the distance traveled by light in a vacuum over 1/299,792,458 of a second, which is precisely one meter. This modern definition leverages natural constants, ensuring reproducible and highly accurate length standards for advanced scientific research and industrial applications. The base units are periodically reviewed and updated based on the latest international standards, definitions, and advances in metrology. By combining these base quantities, a total of 22 SI-derived units are established. The following table outlines the modern base quantities and their units:
Name of Physical Quantity | SI Unit |
---|---|
Length (l) | meter (m) |
Mass (M) | Kilogram (kg) |
Time (T) | Second (s) |
Electric Current (I) | Ampere (A) |
Thermodynamic Temperature (S) | Kelvin (K) |
Amount of Substance (N) | Mole (mol) |
Luminous Intensity (J) | Candela (cd) |
SI prefixes such as kilo-, milli-, and micro- are appended to base units to indicate various orders of magnitude, enabling effortless scaling and conversion of measurement units. This system supports practical applications across industries—whether calibrating laboratory instruments, conducting process validation, ensuring product specifications, or establishing traceable measurement results in quality-controlled environments.
Metrological traceability, sometimes referred to as measurement traceability, is a vital aspect of quality infrastructure in science, industry, and commerce. Defined by the International Vocabulary of Metrology, traceability is the “property of a measurement result that allows the result to be related to a reference through a documented, unbroken chain of calibrations, each contributing to the measurement uncertainty.” This principle ensures that measurements and instrument calibrations conform to internationally recognized standards of measurement and quality assurance guidelines. Measurement traceability is required for ISO/IEC 17025 accredited laboratories, compliance with regulatory requirements, and for facilities adhering to Good Manufacturing Practices (GMP) and Good Laboratory Practices (GLP).
To better understand the concept, refer to the measurement traceability pyramid illustrated below:
The calibration traceability chain begins with working standards or high-accuracy process calibrators used on devices under test (DUTs). Within any facility, these instruments are considered the most precise tools available. Before utilization, these working standards must themselves undergo calibration in an accredited calibration lab—often one with ISO 17025 accreditation. Here, they are compared against secondary standards with even greater precision. Ultimately, this chain leads to National Metrology Institutes (NMIs) such as the National Institute of Standards and Technology (NIST) in the United States. NMIs maintain primary standards, providing the highest-level reference for traceable measurements worldwide.
At the top of the traceability pyramid are SI units, serving as the foundation for all measurement standards, certified reference materials, and calibration practices. Each link in the calibration hierarchy must report its associated measurement uncertainty, ensuring transparency and comparability across industries, test labs, and regulatory bodies. Collaboration among the BIPM, NMIs, and global standards organizations ensures that the definitions and realization of SI units remain consistent, up-to-date, and universally accepted. As traceability moves down from primary to secondary to working standards and down to daily-use measurement devices, uncertainty increases slightly at each level, emphasizing the need for robust calibration and periodic verification schedules.
Measurement traceability is critical for risk mitigation, regulatory compliance, and market acceptance—particularly in sectors such as aerospace, pharmaceuticals, automotive, energy, and food processing. A traceable measurement enables manufacturers and laboratories to demonstrate integrity, support product claims, and facilitate international trade by aligning with recognized standards. Reliable traceability helps reduce product recalls, disputes, and costly errors caused by inaccurate measurements or undocumented testing methods.
For a measurement to be considered traceable, the following three criteria must be strictly met:
Note: In the United States, the National Institute of Standards and Technology (NIST), part of the U.S. Department of Commerce, serves as the national metrology institute (NMI). NIST provides calibration services, reference materials, and authoritative measurement methods to ensure SI traceability and support industrial competitiveness.
When selecting a calibration services provider, look for accredited calibration laboratories with a demonstrable track record and the capability to provide NIST-traceable calibration. Always verify the scope of accreditation, typical measurement uncertainties, and customer support policies to ensure that your instruments meet accuracy and traceability requirements for your specific industry.
There's a saying: "If you can't measure it, you can't improve it." Accurate measurement is fundamental to ensuring quality assurance, safety compliance, operational efficiency, and overall progress. Numerous industries—including manufacturing, aerospace, automotive, pharmaceuticals, energy production, research laboratories, and healthcare—depend on precise measuring instruments to enhance product quality, reduce process variation, and ensure optimal performance. The primary objective of calibration services is to minimize measurement errors, maintain traceability to recognized standards, and increase confidence in the reliability and accuracy of measurements.
Factors such as harsh environments, temperature fluctuations, humidity, mechanical impacts, frequency of use, and improper handling can increase measurement uncertainty and lead to instrument drift or error. Therefore, timely calibration and routine maintenance of measuring devices—such as pressure gauges, flow meters, balances, spectrometers, and electrical testers—is essential to ensure ongoing reliability. By systematically calibrating instruments, organizations maintain the repeatability and reproducibility of the data produced, supporting robust quality control processes.
However, it is important to note that not all instruments inherently deteriorate at the same rate. Those that remain stable over many years can serve as excellent reference standards, particularly if their long-term stability and well-documented uncertainty are verified. While these reference instruments might not represent the absolute true value, their predictable performance makes them valuable for metrology and lab calibration comparisons.
Calibration becomes critically important when a measuring instrument significantly impacts the accuracy and validity of testing procedures, an essential factor in regulated industries and test laboratories. The credibility of data generated by laboratories, especially in fields such as medicine, medical device manufacturing, environmental analysis, and legal testing, directly depends on the traceability and reliability of calibrations performed on equipment.
The ISO/IEC 17025 standard—often referenced as the General Requirements for the Competence of Testing and Calibration Laboratories—comprehensively outlines the competencies and procedures required for laboratory accreditation. This includes measurement uncertainty analysis, instrument traceability, and documented calibration intervals. Many laboratories and testing companies face challenges in consistently applying these requirements, yet adherence provides not only technical benefits but also numerous intangible advantages, such as enhanced reputation, customer trust, and streamlined audit processes for accredited testing facilities.
Calibration services are also necessary when a measurement device is critical for detecting variations in industrial or laboratory processes that could significantly impact product quality, environmental safety, and operator health. Reliable and traceable measurements empower engineers, scientists, and quality managers to identify and mitigate assignable causes of variation in production lines or research experiments, facilitating preventative action and early detection of deviations.
Minimizing variation is essential for organizations striving to meet international product specifications, regulatory requirements, and compliance mandates. Large measurement deviations can introduce severe risks to both process safety and end-user well-being, particularly in highly regulated sectors such as aerospace, automotive, food processing, pharmaceutical manufacturing, and petrochemicals, where even minor discrepancies can jeopardize structural integrity, product efficacy, or consumer health.
Beyond compliance, instrument calibration ensures geographical consistency and interoperability in measurements, aligning with international standards and bilateral agreements. This is crucial for global and domestic trade, where discrepancies in measurement directly impact company revenues, tax calculations, and logistical operations. For example, a cubic meter of gasoline exported must be accurately measured and matched by the receiving country to maintain fairness in transactions and tax assessments. Reliable calibration and metrology practices provide the foundation for dependable trade, scientific research, and technological advancement.
When planning calibration intervals and practices, consider factors such as instrument criticality, usage frequency, environmental conditions, and regulatory requirements. Establishing a robust calibration management program not only enables preventative maintenance and cost savings through early fault detection but also strengthens quality assurance, regulatory compliance, customer satisfaction, and overall process optimization. By embracing comprehensive calibration strategies, organizations demonstrate a commitment to excellence and sustained competitive advantage in their respective industries.
The BIPM defines calibrators as the "measurement standard used in calibration." These calibrators can be high-accuracy instruments used to calibrate a device under test (DUT), a source, or a Certified Reference Material (CRM).
A source is an instrument that generates a known and precise output. The DUT measures this output, and the settings of the source equipment are considered the true values.
A Certified Reference Material (CRM) is a type of standard characterized by a metrologically validated procedure with a known exact measurement value. Each CRM sample must be stable and accompanied by a certificate verifying its authenticity. CRMs are commonly used in analytical and clinical chemistry.
The typical procedure for calibrating a process parameter involves the following steps:
When comparing measurements from the DUT and the calibrator, there are two possible outcomes:
Common metrics used to determine calibration results include the Test Accuracy Ratio (TAR) and Test Uncertainty Ratio (TUR). Many calibration laboratories aim for a TAR or TUR of 4:1. This implies that the DUT's accuracy is at least 25% of the reference standard's accuracy, or the reference standard is four times more accurate than the DUT.
Test Accuracy Ratio (TAR): TAR is the ratio of the DUT tolerance to the tolerance of the reference standard. While it provides a basic pass-or-fail assessment in calibration, it does not account for measurement uncertainties associated with the calibration process.
Test Uncertainty Ratio (TUR): TUR is the ratio of the DUT tolerance to the estimated calibration uncertainty. Unlike TAR, TUR considers various factors that can impact measurement accuracy, such as environmental conditions, process variations, technician errors, and the instruments used. The estimated calibration uncertainty is usually expressed with a confidence level of 95% or 99%.
Source calibrators are devices that generate a known and precise output for the parameter being calibrated. These instruments are commonly used in calibration and metrology laboratories to assist personnel in verifying the accuracy of measuring instruments.
Electrical calibrators are devices designed to provide or measure electrical signals such as current, voltage, frequency, pulses, and resistance. Examples of electrical calibrators include multifunction process calibrators, oscilloscope calibrators, and power calibrators.
Dry block calibrators are employed for calibrating temperature measuring devices. They feature a metal block housed in an insulated container, which is accurately heated or cooled to a specified temperature. Once the temperature is stable, it is maintained, and the temperature readings are taken by inserting the probes into the dry block calibrator's vessel.
Calibration baths are another method for calibrating measuring devices. While similar in concept to dry block calibrators, calibration baths use an insulated container filled with a liquid that is precisely heated or cooled to a specific temperature. Once the temperature within the liquid has stabilized, probes are inserted into the bath to obtain readings.
Calibration baths provide greater temperature stability and precision, making them suitable for calibrating devices that require high sensitivity.
Pressure calibrators are instruments used to measure, apply, and regulate pressure to a device under test (DUT). The DUT then measures the pressure generated. Examples of pressure calibrators include digital pressure controllers and pressure comparators.
A deadweight tester is a specialized pressure calibrator that uses calibrated, traceable weights along with a piston and cylinder assembly to apply known pressures to a device under test (DUT). The DUT then measures and records the applied pressure.
Humidity calibrators feature a chamber that is precisely set and maintained at a specific relative humidity or dew point. The device under test (DUT) then measures the relative humidity and dew point within the chamber.
Flow calibrators are designed to regulate the flow rate to a known and precise value, allowing a device under test (DUT) to measure it. They are commonly used to calibrate flow meters and flow controllers in liquid and gas distribution systems.
Laser interferometry employs a laser and electronic controls to assess machine components for straightness, parallelism, and flatness. This method can measure extremely small dimensions and is frequently used to calibrate machine tables, slides, and axis movements. It relies on the interference of light waves and their interaction with various materials to perform measurements.
The interferometer process involves splitting a single light beam into two separate beams that then create an interference pattern when recombined. Due to the short wavelengths of light, even minute differences in the path lengths of these beams can be detected with high precision. Although the basic technique has been around for over a century, the advent of laser interferometers has significantly improved the accuracy of this calibration method.
The choice of calibration equipment depends on the specific type of service being performed. There are numerous calibration services available, including:
Pressure calibration services focus on calibrating devices that measure pressure, including pressure switches, pressure transmitters, relief valves, and barometers used in gas and liquid systems operating at various pressures, whether above or below atmospheric levels.
Temperature calibration services are designed to calibrate devices that measure temperature, such as thermocouples, RTDs, thermistors, PRTs, bi-metal thermometers, thermal cameras, and infrared meters. This calibration is carried out in a controlled environment to ensure accuracy.
Humidity calibration services involve calibrating instruments that measure humidity, such as humidity recorders, probes, sensors, psychrometers, and thermohygrographs. During humidity calibration, parameters like relative humidity and dew point are assessed, similar to temperature calibration, in a controlled environment.
Flow calibration services are intended to calibrate volumetric and mass flow meters as well as flow controllers used in gas and liquid distribution systems. Regular calibration is crucial as it directly affects the quality and safety of the fluids flowing through process equipment and pipelines.
For calibrating machines that handle helium or hydrogen, the leak standard should be traceable to NIST, with calibration ranges of 2 x 10-10 atmcc/sec or higher for helium, and other gas leak standards should be 1 x 10-8 atmcc/sec or higher.
Pipette calibration services are used to ensure the accuracy of single-channel, multi-channel, and electronic pipettes in dispensing precise liquid volumes. These pipettes are commonly used in analytical laboratories.
Pipette calibration is performed by weighing a liquid dispensed by the pipette at a known temperature. The volume dispensed is calculated by multiplying the weight of the liquid by its density, and this value is compared to the theoretical volume to verify accuracy.
Electrical calibration services are designed to calibrate instruments that measure electrical parameters, including voltage, resistance, current, inductance, and capacitance. This service typically covers devices such as oscilloscopes, multimeters, data loggers, and clamp meters.
Dimensional calibration services focus on calibrating instruments that measure dimensional properties like length, volume, flatness, and angle. This includes devices such as micrometers, calipers, and height gauges, among others.
Force calibration services are conducted to calibrate devices that measure force-related parameters such as weight, torque, and both tensile and compressive forces. This involves comparing the force measurements of the device under test (DUT) to a calibration standard. Adapters are used during calibration to ensure that the applied force is accurately centered on the DUT, minimizing measurement errors.
Traceable deadweights serve as the standards for force calibration, which is carried out in a controlled environment. Instruments commonly calibrated in this service include tensiometers, load cells, scales and balances, force gauges, compression and tensile testers, force dynamometers, hardness testers, and proving rings.
Once calibration is completed by an accredited service provider, a calibration certificate is issued. This certificate provides a detailed summary of the calibration process, including the procedure followed and the results obtained. Essential information included in the certificate typically consists of:
A calibration sticker is affixed to the equipment to indicate the status and validity of its calibration. It typically displays the equipment's serial number and the date when the next calibration is due. While the sticker provides a convenient visual reference for checking the calibration status, it does not substitute for the authenticity and traceability provided by a calibration certificate.
Unaccredited calibration refers to methods used by owners or in-house teams to calibrate instruments. This is often called commercial calibration, standard calibration, quality assurance calibration, or NIST traceable calibration. Such calibration is conducted following the standards set by a calibration laboratory but lacks formal endorsement by an official accrediting body. The accompanying calibration certificate outlines the basic equipment and standard traceability used, but it does not provide official accreditation or legal documentation.
While unaccredited calibration services may be more affordable or convenient, they lack adherence to formal calibration regulations, are not subject to audits, and generally do not meet the rigorous standards of accredited services. This can result in inaccurate measurements, poor quality assurance, and unreliable results, potentially leading to process errors, fines, or product recalls.
When evaluating a calibration certificate, consider the following key details:
Calibration correction refers to the discrepancy between the measurements obtained by the DUT during calibration and the exact value of the reference standard. This information is detailed on the calibration certificate. The calibration correction value is applied to future measurements taken by the DUT to adjust its readings. This adjustment helps the DUT approach the true value more closely, thereby enhancing its accuracy.
Expanded uncertainty represents the range specified in the calibration report within which the true values are expected to fall with a certain level of confidence. This value is calculated statistically and encompasses all sources of uncertainty. A lower expanded uncertainty indicates higher precision in the measurements of the DUT.
The coverage factor, or K-factor, reflects the confidence level associated with the expanded uncertainty. Commonly used K-factors are 2 or 3 in most industries.
A K-factor of 2 corresponds to a 95.45% confidence level, meaning that 95.45% of the time, the measurements are expected to fall within the expanded uncertainty range. Similarly, a K-factor of 3 corresponds to a 99.73% confidence interval. Higher K-factors are used for devices performing critical measurements, where measurement errors can be costly and potentially hazardous.
A crucial aspect of calibration acceptance is measurement decision risk, which is assessed through metrics such as false accept risk and false reject risk. These metrics are used to evaluate the quality of the calibration process.
False accept risk is categorized into two types: unconditional and conditional. Unconditional false accept refers to the risk of equipment being out of tolerance but incorrectly classified as within tolerance. Conditional false accept, on the other hand, acknowledges the potential for equipment to be out of tolerance, but this is considered within the context of the measurement decision. High false accept risk can lead to significant negative consequences for the performance of the equipment.
False reject risk occurs when equipment that is actually within tolerance is incorrectly deemed out of tolerance. This can result in unnecessary costs from adjustments, repairs, re-calibrations, and more frequent recalibrations, potentially impacting operational efficiency and increasing overall expenses.
Force calibration is a necessary process used for testing materials used for manufacturing equipment, machines, and other devices. All forms of metals and other materials can expand and contract during their use...
A dynamometer is a measuring device used to determine the torque, force, speed, and power required to operate the drive on a machine or motor, which can be measured by evaluating the torque and rotational speed of a motor simultaneously...
An engine dynamometer is a device used to test an internal combustion engine that has been removed from a car, ship, generator, or any other accessory that uses one. The goal is to verify performance before reinstalling the engine in the equipment...
Force sensors are transducers that transform mechanical input forces like weight, tension, compression, torque, strain, stress, or pressure into an electrical output signal whose value can be used to...
A load cell is a transducer which converts mechanical energy (tensile and compressive forces) into electrical signals. There are different transducer operating principles that can be utilized to convert forces...
A load pin is a sensor utilized to measure force or weight in various research, control, measurement and testing applications. The load pin force sensor converts a force into an electrical signal. The load pins provide...
Machine vision systems are assemblies of integrated electronic components, computer hardware, and software algorithms that offer operational guidance by processing and analyzing the images captured from their environment. The data acquired from the vision system are...
An optical comparator is a measurement system that offers extremely accurate and repeatable measurement data. Optical measuring tools include optical comparators. This gadget employs the principles of optics by utilizing...
A platform scale is a scale that measures the weight of objects loaded on a flat platform. The function of the platform is to transmit the weight of the object to the internal measuring device and to support the object during weighing...
A strain gauge, or strain gage, is a sensing device used for measuring strain experienced by an object. It is made from a long, thin piece of conductor bonded to an elastic backing material called a carrier...
At the heart of every weighing device is a sensor called a load cell. When an item is put on a load cell, it senses the force of the gravitational pull of the weight, which an electronic circuit processes to display...