Mailing Tubes
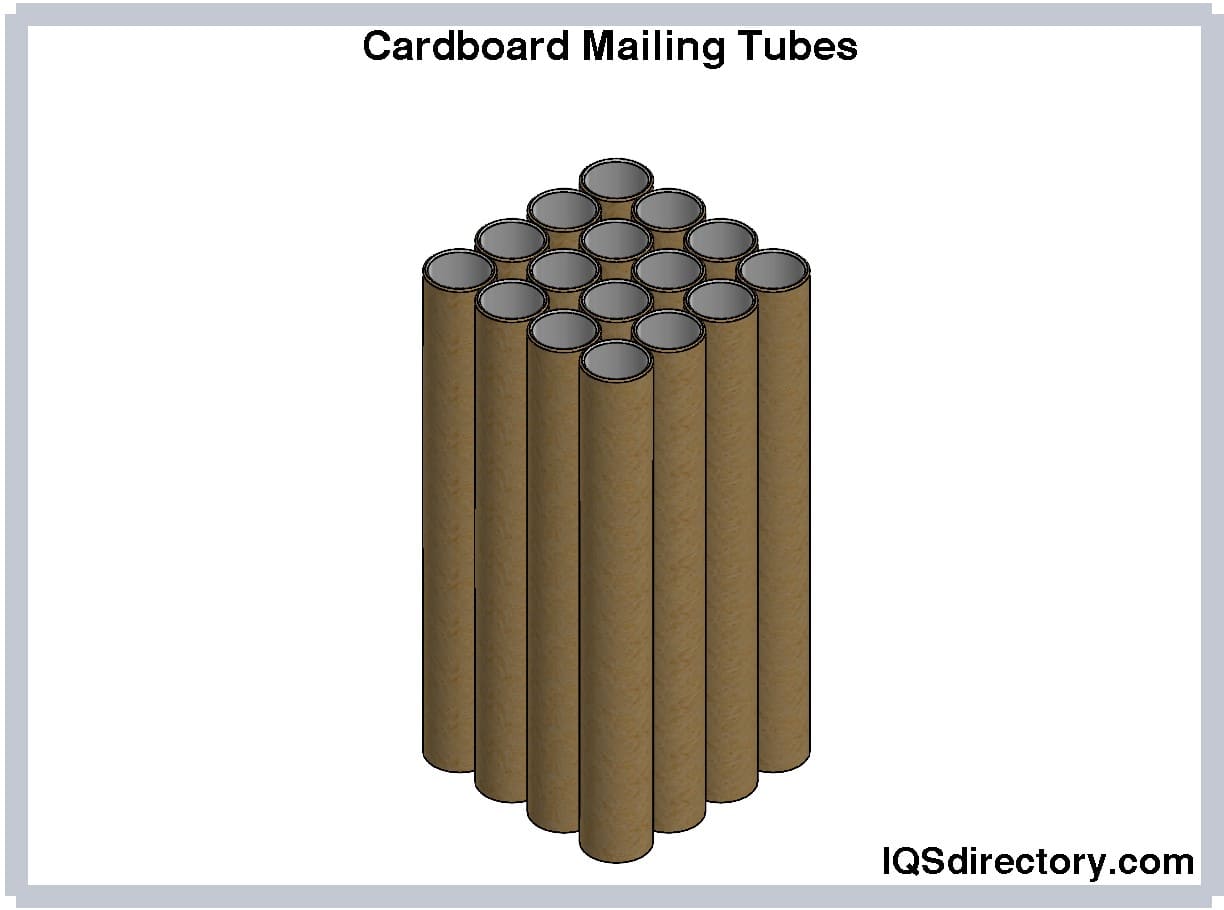
A mailing tube is a sturdy, solid, and durable cardboard container designed for shipping long slender devices and products or rolled up maps, banners, and posters. The indestructible exterior of mailing tubes...
Please fill out the following form to submit a Request for Quote to any of the following companies listed on
This article provides comprehensive information about paper tubes, paper core and composite cans. You will learn how these paper and paperboard products are made and their materials of construction as well as paper tube applications, advantages and drawbacks.
Read further to answer questions like:
Paper tubes are constructed by winding multiple layers of paper or paperboard together, forming robust, hollow, usually cylindrical forms. These layers are adhered together using laminating or bonding adhesives. The wall thickness of these tubes can differ, depending on the number of layers incorporated during the creation process.
Commonly known as paper cores, paperboard tubes, paper cans, fiber drums, fiber tubes, paper tubing, wound tubes, composite cans, coreboard tubes, and sometimes erroneously as cardboard tubes, these are used in a variety of applications. The term "cardboard tube" is technically inaccurate, as true cardboard is made up of three layers of kraft paper with a corrugated middle layer.
While paper tubes, Paper cores and related products are made from wound layers of paper or paperboard. Paper tubes or cores can be constructed from one, two, or multiple layers of brown kraft paper or paperboard.
The innermost layer, known as the liner, and the outermost layer, called the wrap, can be made from various materials such as foil, film, or specialized paper. These materials can offer features like water resistance, graphics or labeling, and specific colors.
The two main types of paper tubes and cores are spiral wound and convolute (or parallel wound) paper tubes. Convolute wound tubes are used in applications that require high bend strength, crush resistance, and dynamic durability.
In a spiral wound tube, the paper layers are wrapped around the tube at an angle relative to its axis. In convolute tubes, the edges of the paper strips are wrapped parallel to or at a 90-degree angle to the tube's axis.
Paper tubes have thinner walls and are widely used as containers or packaging for products.
A paper core is essentially a heavy-walled paper tube. The thicker walls of paper cores make them suitable for winding webs or sheets of flexible material into rolls during converting operations.
Paper machines produce very large rolls, also known as machine rolls, jumbo rolls, tambour rolls, or mother rolls. These large rolls are either rotary slit or converted into multiple narrower rolls using a winder with a paperboard core. Similar large rolls are also used in plastic film, foil, textile, and coated abrasive plants.
You might be surprised to learn that not all paper tubes are designed for packaging. Paper cores can also serve as machine components. For instance, paper cores used for winding large rolls in paper mills or plastic film production require extremely high-strength paper cores, often convoluted, to handle the demands of these industrial applications.
Paper cores used for retail or small-diameter rolls of adhesive tape, labels, foil, paper, tissue, or plastic film are designed for packaging and dispensing. These cores are typically thinner and are often spiral wound.
The paper tube material is cut either by rotary or saw methods to produce various products, including paper cans, composite cans, shipping tubes, push tubes, pyrotechnic tubes, display poles, converting cores, concrete piling forms, and other paper tube items.
Large fiber or composite drums, as well as paper straws, are produced using a similar winding process. Convolute winders are commonly used for making composite drums, offering a more eco-friendly alternative to steel drums. Paper straws, on the other hand, are spiral wound at very high speeds.
Most paper tubes are cylindrical or round in cross-section, but they can also be made in custom shapes such as square, oval, hexagonal, or triangular using specialized winding mandrels. Custom shapes help to precisely fit the tube to a specific part or product, reducing wasted space and eliminating the need for additional spacers or packing materials.
Tapered paper tubes or paper cones are created using a cone-shaped mandrel. Paper cones are commonly used as yarn carriers in the textile industry.
For specific applications, you might need your paper tubes slit or cut lengthwise to create half-shells, which can be used to cover large rolls for protection. These half-shells can be reconnected with tape or H-profiles. Covering a paper roll or coiled steel roll with half-shells is often easier than sliding the roll into a large protective paper tube.
Paper tube and core manufacturing is a converting process that involves web slitting, web winding, and lamination or adhesive bonding. Multiple layers or plies of paper or paperboard are wrapped around a steel mandrel in several revolutions, creating rigid, high-strength tubes or fiber cores through lamination.
Based on my experience, plies generally range from 2 to 10 inches (50 to 250 mm) in width, although some can be as wide as 20 inches (500 mm). The thickness of each ply typically falls between 0.008 and 0.050 inches (0.2 to 1.3 mm). The total number of plies can vary from 1 to over 50, but cores with 3 to 30 plies are more frequently encountered.
The strength of a paper core depends on several factors: the bond strength of the paperboard plies, the thickness of the plies, the bond area or overlap, and the adhesive bond strength. What's particularly interesting is that paperboards can be produced either through a single, thicker papermaking process or by bonding multiple plies together. As a result, some paper tubes are made up of laminated plies or layers.
Process Steps in Manufacturing Paper Tubes | |
---|---|
Machinery Utilized | Paper Tube, Paper Core and Paper Tube Product Manufacturing Process Steps |
OffRotary Slitting Machine | Jumbo Roll Unwound and Slit into Narrow Paper Strips or Plies |
Winder / Unwinder | Winding of Narrow Paper Strips or Plies |
Fork Lift Turk, Carts or Material Handler | Stacks of Paper or Paperboard Rolls Moved to Winder |
Winder - Unwinder or Unwinding Stands | Multiple Rolls of Narrow Paper Strips Loaded on to Unwinder Spindles/Shafts |
Winder - Adhesive or Glue Applicator | Adhesive Applied to Narrow Paper Strips |
Winder - Wrapping & Forming Mandrel | Paper Ply Strips Wrapped on to Mandrel to Continuously from Spiral Tube |
Inline Printing & Labeling Unit | Labeling Wraps with Printed Graphics Applied to Paper Tube in Inline Process |
Inline Cutter | Spiral Paper Tube Cut into Shorter Lengths |
Tube Drying Oven | Spiral Paper Tube Lengths Cured or Dried in Oven |
Offline Printer or Label Wrap Applicator | Labeling Wraps with Printed Graphics Applied to Paper Tube in Offline Process |
Recutter or Offline Cutter | Longer Tubes Cut in to Required Smaller Lengths for End Use |
Conveyors, carts or Material Handler | Cut to Length Paper Tubes Moved to Secondary Finishing Cutting and Closeure Operations |
Tube Finishing Machinery | Deburring, De-dusting, and Polishing or Skiving when Smoother Surface Finish Requited |
Punching or Die Cutting Equipment | End Notching, Slotting, Window Cutting, Perforating, Embossing |
Tube End Forming and Capping Equipment | End Forming, Plug Insertion, Capping or Flanging & Capping |
Conveyors, Carts or Material Handler | Finished Tube Moved to Palletizing and Packaging Machines |
Palletizer & Packaging Machines | Paper Tubes Stacked and Packaged on Pallets, in Boxed or On Steel Carts |
Loading Docks and Trucks | Packaged Paper Tube Products Loaded onto Trucks and Shipped to Customers |
I find that reviewing related patents and technology definitions on the USPTO website can offer a deeper understanding and more detailed insights into the paper tube manufacturing process.
Subclass B31C in the United States Patent and Trademark Office (USPTO) provides cooperative patent classification (CPC) and technology definitions for paper and wound tube manufacturing processes. Specifically, B31C 9/00 refers to the "Simultaneous forming of cylindrical and conical shapes by winding separate webs, such as in the production of bottles."
The paper tube manufacturing process can involve winding, folding, and bending, depending on the desired shape of the final product, such as round, square, or conical.
In the spiral paper tube or core manufacturing process, jumbo rolls of paper, paperboard, and lining materials are first converted into narrower ribbons through a rotary slitting operation. These paper ribbons are then rewound into narrow rolls using rewinding stands.
The narrow paper ribbon rolls are stacked in what resembles large "poker chip" piles. These "poker chip" stacks are then transported and loaded into the tube manufacturing machine.
Narrow paper webs or ribbons from several rolls are guided and attached, adhered, or taped to a steel mandrel. They are arranged either in an overlapping fashion or with spacing between the leading edges. This festooning or spacing allows the ribbons to feed smoothly without interfering with each other.
By attaching the leading edge of the ribbon obliquely, or at an angle less than 90 degrees to the axis of the mandrel, a spiral formation occurs during winding.
The outer diameter of the steel mandrel determines the inner diameter of the finished paper tube. The wall thickness of the tube depends on the thickness of the paper or paperboard ribbons, the adhesive thickness, and the number of ribbons used in the process.
Adhesive or glue is applied to each paper ribbon or ply before it is wound onto the steel mandrel. In my experience coating webs of paper, cloth, vulcanized fiber, and plastic film, a variety of web coaters can be used to apply the adhesive to the plies, including:
What’s fascinating is how the paper tube belt twists into a helical shape, continuously forming and bonding the paper tube plies together. The flexible belt wraps around the paper layers, applying pressure to ensure proper adhesive bonds between the ribbons. Additionally, the fabric-reinforced rubber belt advances the tube along the mandrel.
I can imagine that the stresses and performance demands on the paper tube forming belt are immense. These belts are endless or seamless to prevent marking, boasting high tensile strength and high friction to grip and move the tube efficiently. Additionally, they are easy to clean. Some suppliers of tube forming belts include Nitta, Passaic, and Rainbow.
Next, as additional paper plies are added to one end of the paper tube forming mandrel, the formed or laminated paper tube slides off the other end and is cut to length using rotary blade slicing or offline sawing operations. Depending on the end-use, additional deburring of the tube end edge may be performed.
Another fascinating aspect of the paper tube manufacturing process is the ability to produce a vast array of highly customized paper tube products or material combinations by using different material plies.
Liner or lining layers are applied to the inner diameter (first ribbon) or outer diameter (last ribbon) of the tube to enhance water, moisture, or grease resistance. These liners can be made of metal sheets, foil, coated paper (wax, silicone, or plastic), plastic film, and other protective materials.
If your current application is not satisfied with existing paper tubes, a custom paper tube manufacturer can engineer a new combination of liners, plies, and wraps to meet the specific needs of your specialized application, provided the order volume is sufficient.
One notable feature of paper tube manufacturing is the capability to enhance branding through labeling or printing, both inside and out. If printed or decorative graphics are needed on the paper tube, printable paper ribbons or materials can be used for the first and last ribbons. For example, a white paper or paperboard can be used for the outer layer, while stronger brown kraft paper can be used for the inner layers.
In the parallel or convolute paper tube or core manufacturing process, jumbo rolls of paper, paperboard, and lining materials are slit into wider ribbons, unlike the very narrow ribbons used in spiral tube manufacturing. In this process, the leading edge of the ribbon is aligned parallel to the axis of the paper tube mandrel, resulting in a single seam or flap running along the length of the paper tube.
An external metal roll can be used to apply pressure instead of a belt, which helps to eliminate voids or air pockets and ensures better adhesive contact, resulting in a stronger bond between paper plies. Because the paper web is wider, higher pressures and tensions can be applied during the convolute winding process. These higher pressures and tensions contribute to the production of tubes with greater strength compared to spiral wound tubes.
Convolute paper cores have greater beam strength than spiral wound cores, making them highly desirable for web manufacturing and converting. Convolute paper tube processes are employed to create high-strength, heavy-duty cores for winding and unwinding large jumbo rolls of flexible webs, such as:
When considering a paper core, it’s useful to think of it as a rotating component similar to bearings, gears, chucks, and shafts. In heavy-duty converting operations, paper cores function as machine parts rather than just packaging products, as they play a critical role in the operation and integrity of web manufacturing and handling machines. Spiral wound paper cores are suitable for lighter-duty applications, such as packaging and dispensing smaller rolls of labels, tape, foil, tissue paper, paper, or plastic film.
The spiral and convolute tube manufacturing processes are combined to produce some tubes. For instance, a spiral wound tube made of kraft paper could have an outer white paper or plastic layer with graphics and labeling wound around the outside of the tube using a convolute winding process.
You use paper cores and related products every day in your daily life without ever recognizing it. Paper towels, tissue, aluminum foil, plastic wrap are all wound on a paper tube for easy dispensing. If you open up your kitchen cabinet, you will see a wide variety of paper canisters, composite cans, and other paper tube containers. Fiber drums, straw making, and paper cups are made using similar technology.
Fiber drum machines, straw making machines, paper cup machines and composite can machines use process technology similar to paper tube winders.
Additionally, paper tube manufacturers and machinery OEMs have developed patented and proprietary processes for paper tube manufacturing. These specialized methods are designed to produce tubes and cores with enhanced strength, reduced weight, or other unique properties and functions. For example, PAKEA has designed and patented the SIRPAK® linear tube forming system to improve the production of non-round composite cans.
After a paper tube is formed on a spiral or convolute winder, it is cut into shorter lengths using both in-line and offline cutters. As the laminated spiral tube slides off the mandrel, it is continuously produced. The spiral tube material may be cut to the finished length with an in-line cutter or into longer sections, which are then processed by an offline recutter or recutting machine. During this process, the intermediate lengths might receive an outer wrap of protective film or foil, printed graphics, labeling, or a surface treatment before being cut to the final length. In-line cutting is performed using rotary blade cutters.
If you require very clean cuts and consistent lengths, rotary blade cutting is the ideal choice. Rotary cutting blades or saws are used for offline cutting. Rotary blade cutting typically produces cleaner, sharper edges and tighter tolerances. Saw cutting can be effective for very thick-walled tubes, but it generates burrs and dust that need to be removed from the paper tube or core. Blade cutting offers tighter cut-to-length tolerances, while saw-cut lengths can vary by as much as 1/16” (0.062”).
As discussed, the various permutations of ply materials can lead to numerous paper tube product possibilities. Even more variations can be achieved through surface treatments, coatings, dips, impregnations, and offline convolute wraps.
Paper tube surface treatments may involve dipping or impregnating the tubes with wax, silicone, or other waterproofing coatings to enhance their water resistance.
For specific winding applications, the inner or outer diameters of the tube are polished and burrs on the outer edges are removed to ensure the paper core can be smoothly loaded onto machinery and move freely.
Printing graphics and applying labeling wraps to the tube for packaging can be done either inline or offline. Both convolute and spiral wrapping processes are used for applying labels.
If the paper tube is intended for use as a spacer, concrete form, mask, or pole, the cut-to-length tube may be complete and ready for packaging and shipment. However, if the tube is for packaging purposes, additional processes such as slotting, die-cutting, flanging, sealing, capping, end rolling, or end forming are needed to create a shipping tube, paper canister, or composite can.
You’ll also recognize the benefits of value-added secondary operations like embossing, notching, slotting, slitting, and die-cutting windows. For instance, paper cores may have notches cut into their ends to assist with the winding and unwinding of converted film, tape, cloth, or other roll stock materials.
Openings can be cut into the side of a paper tube container, and a plastic film applied to the inner diameter to create a viewing window for the packaged goods inside. Embossing adds a raised pattern to the surface of the tube. Functional embossing, with raised bumps on the paper core's surface, can enhance the grip of web materials during winding.
A closure feature can be added to a paper tube to create a paper can, mailing tube, or other tubular composite packaging material. Paper tube closures can be achieved by rolling or forming the end of the tube to create rounded edges and inserting a paper disc, by using a plug or cap, or by combining end forming with capping techniques.
The closure on the end of a paper tube can be permanent or removable. Permanently closed ends include:
Paper tube containers can also have an open metal seamed end, which accepts a removable metal friction plug.
One type of paper tube closure that I find particularly appealing for its simplicity and functionality is the snap-loc closure. Tucked, crimped, or snap-loc end closures are among the easiest to produce and use. Crimped end closures, also known as EZ open crimp, "snap-seal," or "self-seal" ends, involve bending two edges of the paper tube inward. The snap-loc flaps can be easily pinched open and snapped closed by the end-user.
Tubes can also be star crimped and used as plugs inside the ends of cores to provide extra support and prevent collapse or crushing. Star-crimped paper tubing features crimps that run parallel to the tube's axis. A similar crimping technique is commonly used on round metal ducting for assembling ductwork.
Storage, shipping, and mailing tubes often use plastic, wood, or metal plugs to close the ends. While friction-fit plugs generally provide a secure fit, some applications may require additional tape or stapling through the tube wall to prevent the plug from becoming dislodged and to ensure the tube remains securely closed during shipping or handling.
Another option is using two caps that fit over the outside ends of the tube. These caps can be made from plastic, metal, or paper. Specialized plugs and caps are available for specific applications: slotted caps for coin or ticket collection, sifter caps with perforations for dispensing powders and dry goods, and plugs or caps with square exteriors or tabs to prevent rolling.
Paper tube containers can be made using telescoping paper tubes, where an inner tube has an outer diameter slightly smaller than the inner diameter of the outer tube. These containers can be constructed as two-piece or three-piece telescoping designs, typically featuring rolled ends with paper or wooden disc plugs.
While you probably think a paper tube-based product is only suitable for dry goods, surprisingly I have found that this is not the case. In packaging applications of a wet or frozen product such as frozen orange juice, flanging, sealing and capping of the paper tube is required to create a sealed, leak-proof package. Typically, “tin end” or metal seamed ends are used where a flange is created in the end of the tube and metal cap with additional sealant inside the joint.
I've noticed that the final step in manufacturing—packaging—is often given insufficient attention. However, packaging is crucial because inadequate protection can lead to damage that undermines a lot of hard work if the product is not safeguarded during transport and storage at the customer’s site.
The final step before shipping finished paper tubes, paper cores, and other paper tube products is palletizing and packaging to ensure they are not damaged during transport. The packaging method can vary based on customer requirements, but paper tubes and cores are often packed in:
Additionally, some paper tube manufacturers offer filling and sealing services, or can package their customers' products directly into paper tube containers.
You will find that the majority of paper tubes and paper cores are constructed from kraft paper and paperboard. Paper and paperboard are both derived from pulp, cellulose or plant fibers. Paperboard is generally 12 points or 0.012 inches or thicker, while paper is less than 12 points according to TAPPI definitions. ISO standards define paperboard as a paper with a grammage above 250 g/m².
Kraft paper Kraft paper is the most commonly used type of paper for making paper tubes due to its strength. Made from softwood pulp with long fibers, kraft paper is stronger than white or other types of paper. The term "kraft" itself comes from German and Swedish words meaning strength.
Coreboard paper is a specialized type of paperboard designed for manufacturing paper cores, and is typically made from 100% recycled materials. Uncoated recycled paperboard (URB) is also commonly used for making paper tubes and cores.
Paper tube consist of one to many plies consisting of three types:
Paper cores can be constructed using only kraft paper or paperboard in every ply, or by combining different materials for the liner and wrap. For example, the liner might be made of metal foil to provide a moisture barrier, the intermediate ply could be kraft paper for added strength, and the outer wrap might consist of white paper for printed labeling. A variety of material combinations can be used for the liner, intermediate, and wrap layers.
Liner and wrap materials can include:
By taking advantage of the ability to include unique non-paper layers during paper tube manufacturing, you will find that some very interesting and high-performance materials can be made.
For electrical insulation, waterproofing, thermal insulation, mechanical strength, and other properties for specialized applications, paper tubes can be manufactured from webs of non-paper materials.
The engineered materials can be wound in addition to or in place of conventional pulp or cellulose-based paper webs to provide specialized characteristics for specific applications. For example, specialized tubes can include:
Specialty ply materials include:
Typically, adhesives for paper tubes are based on water-based polymers, polyvinyl alcohol, dextrin, or hot melt polymers. Some adhesives may be modified with clay or other fillers. If specialty non-cellulose papers or nonwovens are used in the construction of paper tubes, specialty adhesives or thermoset resins may be required to bond the plies. Additionally, paper tubes can be impregnated with wax, resins, silicone, or other polymers to enhance water resistance or modify mechanical and electrical properties.
Paper tubes are measured and specified based on their inner diameter (ID), wall thickness, and length. For packaging or containment applications, the ID and length should correspond to the dimensions of the product being packed.
The product being packed should fit snugly within the tube to prevent movement during shipping, while still allowing enough clearance between the product and the tube's inner diameter (ID) to ensure easy insertion.
For products such as powders, granules, chemicals, or grease, the required volume per paper tube canister will determine the necessary dimensions. The outer diameter is less critical for mailing tubes or any paper tube canisters.
In summary, the wall thickness of a paper tube affects its flat crush resistance. It should be thick enough to prevent crushing during shipping, handling, and storage, but not so thick that it increases costs and reduces the lightweight benefits of using a paper tube.
Paper cores used in heavy converting usually need thicker walls to endure the stresses from winding. The required wall thickness depends on the width and diameter of the web materials being wound. For example, a narrow adhesive tape roll for retail packaging can use a thinner wall, while a paper core for winding a large roll of tape, film, paper, or cloth converted from a jumbo roll requires a thicker wall.
The dimensions of concrete form or piling tubes are determined by the required diameter of the concrete piling or support. Typically, large inner diameter (ID) paper tubes are specified for these applications.
Dimensional tolerances are also an important consideration. Tight tolerances should only be specified if truly necessary for the application, as over-specifying them can unnecessarily increase costs. Fortunately, paper tubes and cores are formed on a steel mandrel, which provides excellent control over the tube's inner diameter (ID).
Paper tubes and cores can absorb and release moisture over time, leading to shrinkage, expansion, or changes in their dimensions. Dimensional stability depends on the tube's resistance to moisture absorption or drying out.
Blade-cut tubes can maintain much tighter tolerances than saw-cut tubes, which is important when the paper tube is used for spacing, masking, or protecting threads, shafts, spindles, and other mechanical components. The difference between smooth blade-cut edges and rough saw-cut edges is evident in the image.
Dimensional Manufacturing Capability of Several Leading Paper Tube Suppliers | ||||||
---|---|---|---|---|---|---|
Leading Manufacturers of Paper Tubes and Cores | ID Range (inches) | Wall Thickness Range (inches) | Length Range (inches) | |||
Min | Max | Min | Max | Min | Max | |
Ace Paper Tube Corporation | 0.25 | 10 | - | 0.5 | - | - |
Chicago Mailing Tube | - | - | 0.025 | 0.75 | 0.25 | 350 |
Heartland Products Group LLC | 0.375 | 20 | 0.03 | 0.0725 | 0.5 | 60 |
Paper Tubes & Sales | 0.51 | 30 | 0.03 | 0.75 | 0.25 | 53 |
Valk Industries, Inc. | 1 | 16 | 0.018 (2 piles) |
0.75 (23 piles) |
0.375 | 50 |
Wes-Pac Inc. | 0.5 | 10 | 0.025 | 0.5 | 0.25 | 300 |
Western Container Corp. | 0.31 | 24 | 0.024 | 0.75 | 0.25 | 300 |
Understanding the capabilities of paper tube manufacturers can help determine what sizes are available and feasible. The table above reviews the manufacturing capabilities of several leading paper tube and core suppliers. Here is a summary of the dimensional manufacturing capabilities of these top suppliers:
While the table shows the range of available sizes, it is essential to contact the manufacturer to confirm whether they can produce a paper tube with your specific dimensions on their winders and cutters. For example, a paper tube with an inner diameter of 0.25 inches, a wall thickness of 0.75 inches, and a length of 0.375 inches may not be feasible.
Even if your project falls outside a manufacturer’s current capabilities, new tooling or machinery can be acquired and amortized for high-volume projects with sufficient annual order quantities. Paper tube tooling is generally less expensive than tooling for other manufacturing processes, such as injection molding or extrusion.
When ordering paper tubes, paper cores, or other paper tube products, it is crucial to discuss the end-use or application with the manufacturer. Their engineers and experts can recommend the appropriate materials and strength requirements (such as flat crush, radial crush, dynamic, or burst resistance), as well as any additional features or modifications needed to meet your specific application demands.
For instance, paper concrete form tubes must support the weight of the liquid concrete. If you are pouring concrete to a greater depth, the wall thickness and strength of the tubes must be adequate to handle the increased pressure.
Typically, commercial-grade form tubes can support concrete pours up to 20 feet in depth, while contractor-grade tubes are suited for pours up to 12 feet. Concrete form tubes are available in diameters as large as 60 inches, but the most common sizes are 6, 8, 12, 15, 16, 18, 20, 24, and 36 inches.
Paper cores for converting or winding web materials are commonly available with inner diameters of 3 or 6 inches, and come in various performance or strength levels. Higher-strength or higher-grade cores are suitable for larger finished roll sizes, heavier weight rolls, and higher winding or unwinding speeds.
The table below displays the paper core grades from the Graphic Communications Association (GCA) and the Composite Can and Tube Institute (CCTI). It outlines the minimum performance requirements for each grade. Additionally, CCTI offers Automated Paper Mill Core guidelines in an Excel spreadsheet to help determine the recommended core grade for your specific application.
GCA and CCTI Paper Core Grades and Test Performance | ||||||
---|---|---|---|---|---|---|
Paper Core Inside Diameter(ID) (inch) | Paper Core Grade | Minimum Test Performance for the Grade Code | ||||
GCA Code | CCTI Code | Harmonized or Combined Code | Flat Crush(lbs./4 inch.) | Dynamic or Cyclic Load Test(KN/10cm) | Flexural Stiffness or Bend Strength Test (kN-sq.m) | |
3 | L | 4 | 3-L4 | 600 | 15 | 6 |
3 | M | 6 | 3-M5 | 850 | 25 | 10 |
3 | F-Fiber | 9 | 3-F9 | 850 | 25 | 10 |
3 | H-Hight Strength | 12 | 3-H12 | 1000 | 35 | 12.5 |
3 | X-Extra High Strength | 14 | 3-X14 | 1200 | 42 | 15 |
3 | U-Extra High Strength | 16 | 3-U16 | 1400 | 50 | 17.5 |
6 | L | 4 | 5-L4 | 350 | 25 | 32 |
6 | M | 6 | 6-M6 | 400 | 35 | 35 |
6 | F-Fiber | 9 | 6-H12 | 750 | 60 | 55 |
6 | H-Hight | 12 | 6-H12 | 750 | 60 | 55 |
6 | X-Extra High Strength | 14 | 6-X14 | 800 | 70 | 60 |
6 | U-Extra High Strength | 16 | 6-U16 | 850 | 80 | 65 |
In addition, a paper tube or core inquiry or request for quote (RFQ) should include an estimate of the number of paper tubes or cores required and how often they will be reordered. Many custom paper tube manufacturers have minimum order quantities.
Moisture adsorption and water resistance can be important properties for many applications. Cobb testing is typically used to measure the moisture absorption properties of paper. A paper tube’s dimensional stability due to the resistance to moisture absorption or release (drying out) is another important property.
Shrinkage or swelling can cause paper products to warp or distort, which would be troublesome in paper core applications where the material is being wound up. A bent, warped or out-of-round tube would generate wrinkles and other defects in a web material such as adhesive tape, paper, plastic film or foil.
A TAPPI survey indicated 50% of the web breaks in paper mills were the result of roll or core defects. A large run of material could quickly turn into waste if the paper core straightness, roundness, and strength are not within the specifications required for the application.
Smoothness and the grooves from the spiral winding process can create wrinkles during web winding. External burrs from saw cutting could also generate a wrinkle. To reduce wrinkles, you might want to request that your outer paper core surfaces are skived and polished to increase smoothness.
A low-quality paper core can result in web breaks and exploding rolls, which can cause a paper mill or plastic film plant thousands of dollars and possibly damage equipment and harm workers. Several different mechanical tests are used to measure the strength and suitability of paper tubes and core for specific applications including flat or side-to-side crush, radial crush, flexural or bend, ring, and dynamic load testing.
The industrial test methods in this standard are divided into two parts. Part one determines the flexural modulus and Bending Stiffness of a paper using modal analysis and three-point bending testing procedures. Part two provides a method for calculating the theoretical critical speed of paper cores used on printing presses and high-speed web converting machinery.
Tests for performance under bending stresses and roll vibrations during winding and unwinding of web materials. Flexural stiffness is also a predictor for resistance to core explosions. Flexural strength or bend strength tests measure the resistance to a paper core sagging under an applied load to the center of a length. Sagging or distorted cores can cause vibration and misshapen rolls.
Tests for crushing performance of a paper tube or core during handling and transportation of a roll wound around a paper core. Flat crush strength tests push two flat plates or anvils against the outer walls of a tube to measure the crush strength. Flat crush strength is useful for paper tubes and composite cans for packaging applications.
For paper cores, the radial crush test better simulates the load conditions during winding.
Tests for performance under cylindrical loading during winding and unwinding in paper mills, plastic film plants and other web making facilities. Dynamic strength testing measures the maximum roll weight a core can support between core chucks in terms of lifetime or number of revolutions.
In my experience, I have found that materials often fail at lower stresses or loads when cyclic loading conditions versus static loads. Dynamic load or dynamic strength testing simulates the effect of cyclic loads generated by tension and the high-speed revolutions of the roll during winding.
Large rolls of paper, film and other materials generate an enormous amount of momentum during winding. When rolls are accelerated or braked the torque is transferred to the core through the core chucks and the tension of the web, which eventually results in core chewout or tearing apart of inner diameter of the core by the chuck. I believe that chewout is an area requiring improved test methods.
Two standards organizations, International Standards Organization (ISO) and Composite Can and Tube Institute (CCTI), provide test methods for flat crush testing: ISO 11093-6:2005 Paper and board — Testing of cores — Part 6: Determination of bending strength by the three-point method and Core Compression (Side-to-Side Flat Crush, CCTI T108). Composite Can and Tube Institute (CCTI) provides standards on measuring the dimensions of composite cans, tubes and core. CCTI also has standards for dimensional stability, water vapor permeability (moisture resistance), and warpage measurement.
The Technical Association of Pulp and Paper Industries (TAPPI) provides standards for the paper raw materials such as paper and paperboard used to manufacture paper tubes, paper cores, paper discs, paper caps, paper end caps and paper spools.
A wide variety of industries consume paper tubes to meet several different end use functions including:
Containing and packaging is probably the largest application segment for paper tubes. Mailing or shipping tubes are used to package large documents with folding such as maps, posters, prints of artwork, original paintings, blueprints or engineering drawings and architectural plans.
Powder tubes are designed for holding dry goods and granulated materials. They frequently feature rotary shaker or sifter tops to aid in dispensing, similar to disposable salt and pepper shakers.
Frozen lemonade and cookie dough are packaged in food-grade paper tube cans, which include liners and sealed ends to ensure the safe containment of the food products. Telescopic tubes are commonly used for packaging wine bottles, perfumes, and cosmetics.
Push-up tubes with oil-resistant liners are ideal for dispensing lip balms, lubricating grease, caulks, adhesives, deodorants, and repair compounds.
Chemicals, active pharmaceutical ingredients, pesticides, and fertilizers can be packaged in paper tube cans and composite drums by first lining the container with a plastic bag.
Another application that I find particularly intriguing is the use of paper tubes in construction. Large-diameter, spiral-wound paper tubes are employed to form concrete pilings by pouring concrete into the tube, which often includes rebar and remesh for reinforcement. Smaller-diameter paper dowel sleeves are used to create voids or channels within cast concrete, allowing space for communication cables, electrical wiring, and plumbing. Additionally, some architects have explored using paper tubes as framing materials for emergency or temporary shelters.
Paper tubes naturally dampen vibrations thanks to the fibrous structure of the paperboard. Additionally, they offer superior thermal insulation compared to metal tubing.
Specialized dielectric crepe or kraft papers can be used to create electrically insulating or dielectric paper tubes. Engineered papers and saturation with specially formulated resins can enhance either thermal conductivity or insulation properties.
Paper tubes are utilized to safeguard various mechanical components, including spindles, bolt threads, polished shafts, end mill teeth, plug gauges, and drill bits. By covering spindles or bolt threads with a protective tube, you can prevent impacts from other metal parts that might otherwise nick or distort the threads.
Paper tube masks are slid over threads or shafts to enable the targeted application of coatings or adhesives while protecting the areas covered by the mask from being coated.
Paper tubes serve as display poles to support signs in stores and exhibits. They are also used as spacers in packaging to prevent movement and protect products from damage. For example, paper tube spacers are employed to position and safeguard automotive wheel hubs during shipment. Additionally, paper tube spacers can function as reinforcing corner posts and supports within various packages.
Paper cores, paper cones, and paper spools are commonly used for winding, carrying, and dispensing materials such as wires, cables, tubing, foils, yarn, rope, and other roll stock. A paper spool typically features a paper core with two chipboard flanges. In the agricultural industry, paper cores are even utilized to roll up sod.
Paper tubes and cores have several advantages compared to plastic or metal tubes:
Paper tube and cores have drawbacks compared to similar products made from metals, plastic or glass:
Paper Packaging Has Low Density | |
---|---|
Packaging Material | Density (Ib/ft³) |
Kraft Paper | 43 |
Aluminum | 168 |
Glass | 157 |
PET Plastic | 87 |
Industries are increasingly adopting eco-friendly and sustainable packaging solutions, like paper tubes, to lower their carbon footprint and enhance their image with customers. Many consumers favor eco-friendly packaging, which can influence their purchasing decisions.
The marketing, consumer acceptance, and cost benefits of paper tubes in packaging and product selection are evident. Additionally, using paper tubes can help lower costs associated with complying with environmental regulations for plastics and metals, as they are free from volatile organic compounds (VOCs) and heavy metals, which are often regulated.
Customers purchasing paper tube products should have to be as concerned with compliance to:
Paper tube and core manufacturing is a very eco-friendly and sustainable process for several reasons:
Collection and Reuse Programs - Many paper tube manufacturers have a paper tube and core collection and re-use programs to facilitate the gathering of used cores from their customers as well as paper and paperboard scrap from their communities.
Natural / Eco-safe Material – Paper tubes and cores are made from natural plant materials and are ecologically safe because they do not contain any toxic chemicals or heavy metals. Paper tubes buried in the earth will compost in 1 to 2 months and add nutrients back into the soil.
A mailing tube is a sturdy, solid, and durable cardboard container designed for shipping long slender devices and products or rolled up maps, banners, and posters. The indestructible exterior of mailing tubes...
A poster tube is a cylindrical, triangular, or rectangular hollow prism that is commonly used to transport rollable, unframed art, important documents, or long and slender materials. They also carry objects like...
A shipping tube is a long container used for mailing long items that are rolled or folded to fit in the tube. They are constructed of various types of materials with Kraft paper being the most common and widely...
A Sonotube® is a cardboard concrete forming tube made of waxed paper or lamination that is wound into a tube into which concrete is poured to create supports, columns, and supports for posts. Sonotube® is a registered trademark owned by SPC RESOURCES, INC...
A tape and label core is a thick durable tube that forms the center of a label or tape roll with the same shape as that of a toilet paper or paper towel core but is sturdier and more resilient. Although the shape of tape and...
Pressure-sensitive adhesive tapes consist of a backing material film coated with an adhesive intended for relatively low-stress applications. Light pressure, usually done by the fingertips, is applied to initiate the binding. In the sticking process, the fluid properties...
A cardboard box is a shipping container made of thick heavy duty paper known as paperboard, which is more than 0.01 inch or 0.25 mm thick. The term cardboard is used as a generic descriptor for various types of solid firm papers used to produce boxes
Carpet tape is a double-sided tape designed for securing carpets or rugs to the floor. It's made of strong, durable, and adhesive material that can hold the carpet in place and prevent it from sliding or wrinkling. Carpet tape is used in
A corrugated box is a disposable container whose sides are made up of layers of material that include an inside layer, outer layer, and middle layer. The middle layer, between the outer and inner layers, is fluted, which are rigid wave shaped arches that provide cushioning...
One kind of pressure-sensitive self-adhesive tape is foam tape. It has one of several different backing materials and is made of foam. It may have adhesive on one or both sides. Foam tapes are, at their most basic level, tapes that are applied to uneven or
Masking tape is pressure sensitive, thin and very adhesive, easy to tear paper that is used in various tasks ranging from masking off areas that are not to be painted or as insulation for electric wires among other...
PTFE stands for polytetrafluoroethylene and is a synthetic fluoropolymer used widely in many industries and many other applications. PTFE is also commonly referred to as thread seal tape, teflon tape, and plumber‘s tape...