Air Cooled Chillers
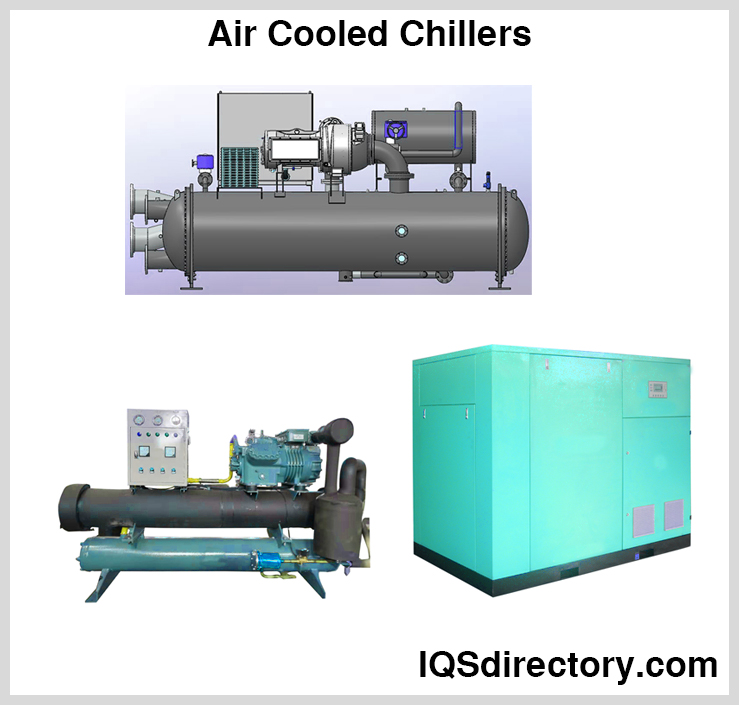
Air cooled chillers are refrigeration systems that cool fluids and work in tandem with the air handler system of a facility. Air cooled chillers are types of chillers that rely on the use of fans to reject heat outside the...
Please fill out the following form to submit a Request for Quote to any of the following companies listed on
Here is the most complete guide on the internet about
You will learn:
This article takes an in depth look at glycol chillers.
You will learn more about topics such as:
A glycol chiller is an industrial cooling device that employs a blend of glycol and water to reach temperatures far below the natural freezing point of water. The glycol used in these systems can either be ethylene glycol or propylene glycol. Glycol's antifreeze capabilities ensure the coolant remains liquid at these chilly temperatures. Generally, the mixture found in most chiller systems comprises 60% glycol and 40% water.
Increasing the glycol concentration within the mixture enhances its antifreeze efficiency, which is particularly advantageous for achieving swift cooling. This improvement significantly boosts heat transfer efficiency, which is vital for maintaining specific temperatures. Such precision is often crucial for successful industrial and production processes.
Industrial chillers using glycol-water coolant circulate the mixture through heat exchanger systems, where heat is absorbed from diverse industrial applications. Once the coolant is warmed, it passes through the chiller for cooling before being recycled to absorb more heat from various industrial operations. Glycol chillers are extensively utilized because they consistently maintain frozen food quality and facilitate food processing systems.
Glycol, an organic alcohol compound, is commonly known for its antifreeze properties. Its key feature is its superior ability to transfer heat, which makes it particularly effective for cooling and chilling applications. Glycol mixtures in industrial chillers are adept at rapidly removing substantial amounts of heat, which is essential for maintaining reaction stability during chemical processes. Due to their rapid heat transfer capabilities, glycol chillers are crucial in scenarios where quick temperature control is necessary.
There are two primary types of glycol chillers: ethylene glycol and propylene glycol. Despite both being glycol compounds, they should not be mixed due to their distinct properties related to fluid characteristics, toxicity, and heat transfer efficiency. Mixing them could lead to system malfunctions or inefficiencies.
Ethylene glycol serves as an antifreeze in industrial cooling systems, offering protection against freezing and acting as a rust inhibitor. The concentration of ethylene glycol in a water mixture is based on the lowest expected outdoor temperatures and the specific temperature requirements of the application. With a high flashpoint of 240°F, ethylene glycol is suitable for various industrial processes. However, its toxicity prevents its use in food processing applications.
Propylene glycol, known for its low toxicity, is a food-grade antifreeze often used in environments where safety is a priority. It is more environmentally friendly than ethylene glycol and readily biodegradable. Propylene glycol chillers are suitable for use in the food industry and refrigeration systems where direct contact with the substance might occur. Despite being a synthetic compound, propylene glycol mixes well with water. The Food and Drug Administration has deemed it safe for use in maintaining moisture in medicines, cosmetics, and food products.
Portable glycol chillers are small, compact, and self contained, with all of their components included in the unit. They have a capacity of 1 to 40 tons of cooling and are ideal for small loads or where special fluids, flows, pressure, or temperature are necessary. Due to the compact size of portable glycol industrial chillers, they can be used for test applications or positioned for temporary use.
A modular glycol industrial chiller system consists of multiple chillers connected to create a comprehensive cooling solution. This setup is highly adaptable, allowing for the addition of more chillers as demand grows. The system is designed to ensure uninterrupted cooling, even during maintenance periods.
Modular glycol industrial chillers feature oversized processing pumps and large glycol reservoirs with extra ports for system expansion. As new modules are added, the chilling capacity of the system increases significantly. This design is particularly advantageous for industries that cannot afford downtime, as it allows for backup chillers to take over if one unit fails.
One notable advantage of modular glycol industrial chiller systems is their ability to operate partially during periods of low heat load, which saves costs and enhances control. While the term "modular glycol industrial chiller" encompasses a broad range of designs, these systems are available in various configurations to suit different industrial needs.
When selecting a glycol industrial chiller, several crucial factors must be taken into account. Their distinctive performance characteristics and high efficiency have made them a preferred choice for cooling critical production processes.
Process cooling systems are crucial for industrial applications, where heat accumulates during material blending, mixing, or chemical reactions. A cooling system helps maintain stable temperatures, allowing other manufacturing processes to proceed efficiently.
One significant advantage of a glycol industrial chiller is its precise temperature control. Glycol's antifreeze properties prevent pipes from freezing, with both ethylene and propylene glycol being suitable for cooling systems but not interchangeable due to their differing properties.
Glycol is an effective additive in cooling systems because of its compatibility with water. While the freezing point of water is 32°F, which can hinder or damage a cooling system, glycol lowers the freezing point to –60°F, enhancing the system's operational temperature range.
The lower temperatures achievable with glycol allow a cooling system to remain effective longer than with water alone. These benefits have made glycol a crucial component in modern cooling systems.
Glycol industrial chillers operate as closed-loop systems, where the coolant continuously circulates without exposure to the environment. This closed system keeps the glycol coolant clean and uncontaminated, preventing fouling or scaling and eliminating water loss from evaporation. As a result, closed-loop systems are exceptionally efficient and durable.
Closed-loop systems also require less pumping power, which helps lower installation costs. The glycol coolant is circulated through tubing connected to the input and output sections of the chiller.
The heat exchanger allows the transfer of heat between the glycol water coolant and the refrigerant gas. It uses the flowing glycol to collect heat from the refrigerant and move the heat away from the area being cooled. The heat exchanger and glycol pipes are small since glycol is capable of removing more heat.
The low viscosity of glycol is why high-powered pumps are not required for operating a glycol chiller. Small pumps are essential for circulating the glycol and maintaining a consistent cool temperature. Depending on the chiller unit's design and the application's needs, the cooling system may require multiple pumps.
The compressor takes low pressure and temperature refrigerant and compresses it into high pressure and temperature. There are several different types of compressors that a glycol industrial chiller can use with ones designed to fit the needs of the chiller and the applications for which it was developed. The different types of compressors include positive displacement, screw, diaphragm, screw, diaphragm, rotary, and centrifugal.
The condenser absorbs the excess heat from the chiller's compressor, which it has received from the evaporator. This heat is transferred to water circulating around the condenser, which then releases the heat into the surrounding air.
Water plays a crucial role in glycol systems, as glycol must be mixed with water for the system to function effectively. Key factors in the process include the type and quantity of water used, which can vary. Although city water can be used in a glycol industrial chiller, it is generally not recommended.
Manufacturers recommend the use of distilled or reverse osmosis water to mix with glycol. Deionized water can initiate the chiller process but should be replaced since it can attack metals in the chiller and damage other components. Reverse osmosis or hyperfiltration removes contaminants through the use of pressure that forces water through a semipermeable membrane. The process can be seen below.
Several factors must be considered when determining the ratio of water to glycol. The primary consideration is the location of the chiller and the ambient temperature of the environment. Indoor chillers, which are less likely to experience freezing conditions, typically require less glycol.
For systems operating at very low temperatures, such as below 20°F, the glycol-to-water mixture should be adjusted similarly to that of an outdoor chiller system, corresponding to the saturated suction temperature in the evaporator or 10°F below the chiller's setpoint temperature.
Determining the correct ratio of water to glycol depends on the coldest temperature the glycol system will encounter during operation. It is crucial to get this ratio right, as excessive glycol can lead to inefficiency, while insufficient glycol can cause the system to freeze or burst pipes.
Once the appropriate type of water and glycol are selected, the chart below provides an approximate percentage of water to glycol for both outdoor and indoor glycol chiller applications.
Glycol Chiller Applications | |||
---|---|---|---|
Applications | Percent of Water to Glycol | Freeze Protection | Burst Protection |
Indoor | 30% to 70% | 5°F or -15°C | -20°F / -29°C |
Outdoor | 50% to 50% | -35°F or -37°C | -60°F / -60°C |
Maintaining clean water and proper glycol content are critical factors in regard to the life of the cooling system as well as an important part of reducing downtime. To keep the water and glycol free of suspended solids, it is important to have a filtration system as part of the chiller.
Automatic self-cleaning screen filters act as a barrier to suspended solids and are energy-efficient, although they can result in some coolant loss.
A commonly used filtration method for glycol chillers is the side stream filter. This system removes a portion of the fluid flow to filter out solids and contaminants before returning the cleaned fluids to the system. Side stream filtration is effective in controlling suspended solids and helps maintain the integrity of the glycol and water mixture.
Glycol industrial chillers are highly regarded for their efficiency in cooling systems, thanks to the precision control they offer and the low temperatures they can achieve. They are commonly used in beverage production, where maintaining specific cooling levels is crucial for ensuring the quality of the final product.
Maintaining products at a consistently low temperature can be costly and necessitate frequent monitoring. The introduction of glycol systems in various sizes has streamlined the process, making it more affordable to produce high-quality products without the need for constant oversight of the cooling process.
A common concern with refrigeration systems is the risk of leaks that can lead to temperature increases and potential crop damage. This issue is mitigated with glycol chillers, as glycol contains inhibitors that make the system resistant to corrosion, scaling, and rust, thereby reducing the likelihood of leaks and damage to pipes.
Propylene or ethylene glycol acts as an anti-freeze, preventing freezing inside the coils. The glycol and water mixture also helps protect the chiller from the buildup of algae and bacteria.
Another safety feature of glycol chillers is their low maintenance requirements. These chillers can store and keep products cool for extended periods without the need for expensive upkeep. They are designed to last for years, delivering exceptional performance with minimal maintenance needs.
Glycol industrial chiller pipes are capable of running longer distances, servicing multiple processing locations from a single cooler and pump package. These pipes come in various types, with PVC80 being a common choice. Proper installation is crucial, and using a reverse return method helps balance the flow across the equipment by ensuring that the cooling medium travels the same distance to and from the chiller. The size of the piping is determined by the flow requirements of the equipment, considering factors like pressure drop and velocity.
The economizer feature in glycol industrial chillers leverages cold ambient air for cooling when the temperature is suitable. A control switch deactivates the compressor and utilizes the chilled environmental air to meet the thermostat's setpoint. This feature enhances efficiency and reduces operating costs by integrating ambient air into the cooling process.
Glycol industrial chillers can operate at temperatures well below the freezing point of water, with control over these temperatures achieved by adjusting the glycol mixture percentages. For example, a 10% ethylene glycol mixture freezes at 26°F, whereas a 60% mixture freezes at -60°F. Glycol's antifreeze properties ensure that the coolant remains in a fluid state, even at extremely low temperatures.
Opting for a glycol industrial chiller can be significantly more cost-effective compared to multiple self-contained refrigeration units. A single glycol chiller unit, which includes a chiller compressor to cool the glycol and water, often costs less than half of what it would cost to purchase several separate refrigeration units.
Over the years, cooling systems have evolved significantly, moving away from outdated and harmful methods. The chiller manufacturing industry has become more environmentally conscious, developing cooling solutions that comply with environmental agency regulations.
These advancements in cooling technology have expanded their use across various industries and provided solutions for applications that previously lacked effective cooling options. A key aspect of this progress is the incorporation of glycol as an additive in cooling systems, which has enhanced their efficiency and versatility.
With increasing environmental safety restrictions, grocery stores need chilling units that meet eco-requirements while providing long-lasting and durable solutions. Propylene glycol industrial chillers, which are food grade, are ideal for frozen food chiller cases. They are specifically engineered to efficiently remove heat while being robust enough to withstand constant use.
Maintaining the freshness of fruits and vegetables is crucial in the produce packing industry. Failures, downtimes, and maintenance delays can ruin a shipment of products. Like grocery stores, cooling units must comply with food grade requirements while being robust enough for continuous use. Propylene glycol industrial chillers are engineered to meet the stringent demands of the produce shipping industry, making them an ideal choice for ensuring reliable and effective cooling.
One of the areas where glycol industrial chillers are used the most is the brewing industry, which requires precisely controlled temperatures and conditions. The maintenance of temperature has to be consistent since any fluctuations can have extremely negative effects on the quality of the final product. It is for these reasons that propylene glycol industrial chillers help to precisely regulate and maintain container temperatures.
Engineering an outdoor ice rink in a warm climate presents unique challenges. However, glycol chillers, which can cool below the freezing point of water, make it feasible. In such installations, glycol is pumped through mats placed beneath the ice rink surface. Water sprayed over these mats then freezes upon contact, allowing the rink to maintain ice even in warmer temperatures.
Similar to breweries, the quality of dairy products heavily depends on an effective cooling system, as inadequate or unsuitable systems can lead to bacterial growth. Consistent temperature control throughout the dairy manufacturing process is essential. Milk is pumped directly from cows into cooling units, which store it until further processing.
Maintaining a stable temperature at every stage of the process is crucial to prevent spoilage and bacterial growth in raw milk.
The few examples of glycol chiller applications provided are just a fraction of their extensive uses. Any industry where heat is a factor in the process relies on glycol chillers to effectively remove and dissipate heat.
There are specific actions and considerations to avoid in order to keep a glycol chiller operating at peak performance. Failing to follow these guidelines can result in damage or complete system failure. Glycol chiller manufacturers provide clients with essential information during installation to ensure the system performs optimally.
While automotive antifreeze contains similar chemicals to glycol coolants used in chillers, it is formulated differently. Using automotive antifreeze can lead to reduced flow rates, pressure issues, and a significant decrease in heat transfer efficiency.
Inhibited glycol contains additives that protect against corrosion, scale, and rust, unlike uninhibited glycol. For effective protection, glycol must be used in concentrations of 25% or higher to ensure that the inhibitors are present in sufficient quantities.
Manufacturers strongly advise against mixing ethylene and propylene glycol or different brands of glycol. The incompatibility of various formulations can result in clogged filters, strainers, and pumps, as well as problems with transfer properties.
Different states, counties, and cities have varying regulations regarding the use of glycol and antifreeze to protect water tables, drainage systems, and fluid disposal. It is crucial to check with local authorities before installing a glycol chiller to ensure compliance with municipal regulations.
The ratio of glycol to water must be regularly checked and tested to maintain the correct percentages and prevent corrosion issues.
Glycol chillers perform best when using distilled or reverse osmosis purified water, as city water often contains contaminants that can interfere with the glycol-water mixture. Other pure water options include demineralized water, which eliminates the unpredictability associated with municipal water.
Air cooled chillers are refrigeration systems that cool fluids and work in tandem with the air handler system of a facility. Air cooled chillers are types of chillers that rely on the use of fans to reject heat outside the...
A chiller is a cooling mechanism designed to produce fluids that can lower temperatures by removing heat from the fluid. The type and use of a chiller depends on the required temperature and kind of refrigerant, which can be a liquid or a gas...
Laser cooling is a multi-process that includes a number of techniques in which atomic and molecular samples are cooled down to a temperature near absolute zero. These techniques depend on...
A water chiller, or chilled water system, is a type of refrigeration system which uses water as a secondary refrigerant. They are used for larger, more complex, heating, ventilating, air conditioning, and refrigeration (HVACR) applications...
Cooling towers are specialized heat exchangers that remove heat from water mainly by means of latent heat loss from evaporation while coming into contact with an airstream. Aside from evaporative cooling, water is also cooled by sensible heat transfer due to the temperature difference between air and water...
Heat exchangers are pieces of equipment used to transfer heat between two or more fluids. This process usually involves abundant working or utility media such as water or air that rejects or absorbs heat from a more valuable fluid such as crude oil, petrochemical feedstocks, and fluidized products...
Open loop cooling tower makes use of direct contact with the air in order to cool down the water. It is essentially a heat exchanger. In these types of cooling towers, there is the partial heat transfer due to heat exchange between...
A plate heat exchanger (PHE) is a compact type of heat exchanger that utilizes a series of thin metal plates to transfer heat from one fluid to the other. These fluids are typically at different temperatures...
A shell and tube heat exchanger (STHE) is a type of heat exchanging device constructed using a large cylindrical enclosure, or shell, that has bundles of perfectly spaced tubing compacted in its interior. Heat exchanging is the transfer of heat from one substance or medium to a similar substance or medium...