Air Cooled Chillers
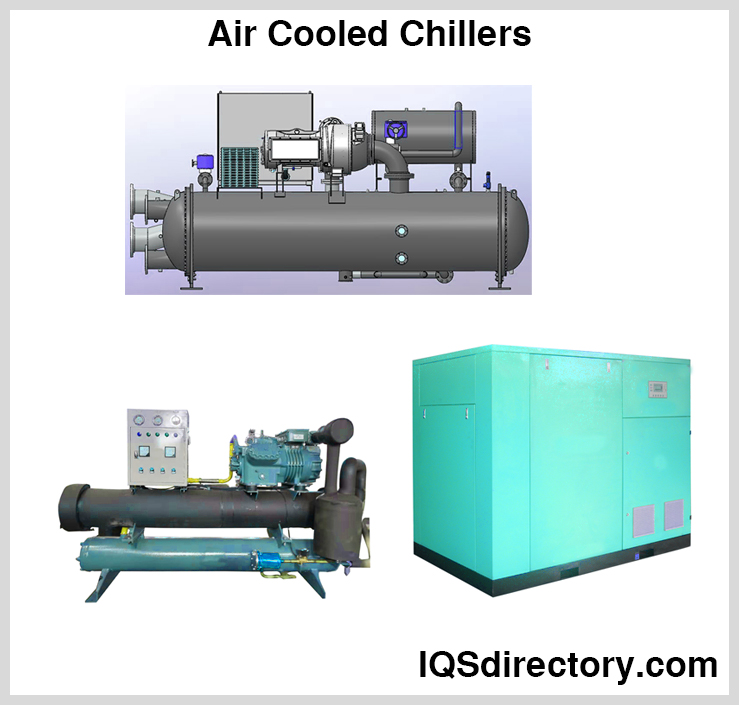
Air cooled chillers are refrigeration systems that cool fluids and work in tandem with the air handler system of a facility. Air cooled chillers are types of chillers that rely on the use of fans to reject heat outside the...
Please fill out the following form to submit a Request for Quote to any of the following companies listed on
An explanation of process chillers and their use with a list of manufacturers
You will learn:
A process chiller is a cooling unit that circulates water to remove heat from industrial processes. Using a closed loop system, process chillers absorb heat by transferring it from circulating water to a refrigerant. The wide use of process chillers is due to their high efficiency and reliability in removing heat generated during manufacturing applications. Heat removal protects equipment and products and ensures the optimum performance of industrial equipment and increases equipment longevity.
Normal operation of a process chiller includes a pumping system for circulating cooling water or a glycol solution. As fluid is pumped through equipment, it absorbs heat, which is returned to the chiller, where the absorbed heat is transferred from the circulating fluid to refrigerant. The absorbed heat is carried by the refrigerant to a compressor, condenser, and evaporator that complete the heat removal process.
The type of refrigerant used by process chillers varies in accordance with the temperature required for a process. The refrigerant goes through a set of phases that changes it from a liquid to a gas and back to a liquid. In order to complete the heat removal process, every process chiller has basic components that move and handle the refrigerant. The basic components of a process chiller are a compressor, evaporator, condenser, and expansion valve, which are the essential for the closed loop cycle.
The different types of chillers begin with water cooled and air cooled, which are the methods used to collect and dissipate heat. Further division of process chillers is in regard to their type of compressor that can be screw, scroll, or reciprocating. Each type of process chiller is designed to perform cooling functions for specific applications and industries. The varieties of process chillers enable manufacturers to provide solutions for any process, product, or industrial application. Each type is carefully designed using complex intricate systems for cooling equipment, spaces, and assisting in maintaining the proper temperature for operational efficiency.
The two general classes of chillers are water cooled and air cooled, which vary in regard to how collected heat is expelled into the atmosphere. Both classes of chillers are differentiated by their type of compressor that have different methods for compressing the refrigerant that carries the heat collected by circulating water.
Compression methods are divided into positive displacement and dynamic, both of which are used in residential HVAC systems and industrial grade chillers. The emphasis on compressors is due to their importance in a chiller’s processing of collected heat, a factor that determines a chiller's capacity.
Engineers use either of these methods in the designing of process chiller compressors. The compression method that is chosen is dependent on several factors including the required temperature, refrigerant volume, and the capacity of a chiller.
Water cooled process chillers use water to collect heat from a process and bring the collected heat back to the chiller where refrigerant takes the heat from the water. When the water leaves the chiller, it has a temperature of 6°C (42.8°F). A pump forces the chilled water into equipment. As the water leaves the equipment, it carries the heat that it collected back to the chiller where the refrigerant absorbs the heat.
The refrigerant, with the collected heat, passes through the condenser, which has a water loop that is connected to a cooling tower where heated water is sent to release the collected heat into the atmosphere. The exchange of heat in the condenser, between the water and refrigerant, is completed through a pipe wall by heat transfer.
In the water tower, fans make direct contact with the water and send the heat into the atmosphere. The cooled water returns to the condenser to continue the cycle. Cooling towers take several forms including cross flow, counter flow, natural draft, and mechanical draft.
Air cooled process chillers operate in a manner that is similar to water cooled chillers but without pumps and cooling towers. Water is circulated from the chiller to equipment where it absorbs heat and returns to the chiller. As with water cooled chillers, in the chiller, the water releases the collected heat into the refrigerant that carries heat to the condenser where powerful fans blow across tubes containing the refrigerant to dissipate the heat into the ambient atmosphere.
The components of air cooled chillers are very similar to those of water cooled chillers with the main difference being how absorbed heat is removed from the chiller. The simplicity of air cooled chillers is one of their main selling points since they do not require pumps or cooling towers. They are affordable and easy to install due their uncomplicated component structure. Since air cooled chillers do not require large amounts of water and are self-contained units, they can be installed outdoors, regardless of the type of environment. Air cooled chillers are known for their cooling capacity and their ability to meet the needs of different industrial processes. They are capable of meeting the requirements of high demanding applications.
The unique feature of scroll process chillers is how they compress the refrigerant. The compression process is performed by two interleaving scrolls where one scroll is stationary while the other orbits around the stationary one. The process creates pockets that compress and move refrigerant gas to the condenser where absorbed heat is released. The cooled refrigerant goes from the condenser into the expansion valve that reduces the refrigerant’s pressure and temperature before it enters the compressor.
Scroll process chillers operate quieter than reciprocal chillers but are more expensive. They are included in air cooled and water cooled chiller systems. The design of scroll chillers makes them less susceptible to breakdowns or failure, which lowers maintenance costs. They are exceptionally efficient and have a higher capacity than that of reciprocal process chillers.
The unique feature of screw process chillers is in regard to how their compressor works. Referred to as helical compressors, screw chillers have helical slotted rotors with a convex flap and concave groove. Refrigerant gas is compressed through volume reduction as it passes between the rotors. The progression of the liquid refrigerant, through the compressor rotors, transforms it from a liquid to a gas vapor with suction, compression, and discharge being completed linearly and efficiently.
Screw chiller compressors have sliders that regulate the compression path. They have the same structure as scroll, piston, and centrifugal chillers with the key difference being how the compressor is used. Screw chiller tonnage varies between 30 to 400 or more tons, which is several times more than scroll chillers. To increase the efficiency of a chiller, screw chillers can have one or two rotating screws to apply force and compress refrigerant.
Certain types of industrial equipment are susceptible to explosions, which necessitates the use of chillers that can withstand such occurrences. Explosion proof process chillers are specially designed using materials that protect components from combustible materials. A select number of chiller manufacturers specialize in the manufacture of explosion proof chillers. They provide detailed information regarding the capabilities of their equipment and how the construction of their chillers protects workers and the work environment.
Explosion proof chillers can be air or water cooled and have scroll or screw compressors. A chiller’s components are not the factors that determine whether a chiller is explosion proof. Motor design, sealed conduits, and several other seals work together to provide explosion proofing. The classification of explosion proof is in reference to the system design standards established by the National Electric Code (NEC) in regard to hazardous environments. A site is determined to be combustible if it contains flammable gases, vapors, dust, or other combustible materials.
The term explosion proof refers to electrical equipment and machinery that can contain and endure explosions within their structure. Industries that bear the hazardous area classification are oil and gas, chemical processing, and mining. Adherence to the standards of the NEC is for the protection of personnel and assets in order to reduce the potential disasters.
Although all chillers are designed to lower the temperature of industrial equipment, some processes require extremely low temperatures. To address such conditions, chiller manufacturers design and produce chillers that can yield temperatures between 0°C and -31.67°C (32°F and -25°F). Typical chillers have one stage of refrigeration generated by their components and operate above freezing. Low temperature chillers that operate below freezing have multiple refrigeration stages.
Unlike a typical chiller, low temperature process chillers use different refrigerants at each stage to drastically lower the temperature. Low temperature chillers are designed to be durable, efficient, and include high strength components to be able to withstand the demanding temperatures. Compressors, valves, tubing, pumps, and condensers are robust and exceptionally strong.
In order to reach the lower temperatures, low temperature chillers use a variety of fluids that are superior to single stage chiller refrigerants. The types of heat transfer fluids include silicone oil, inert fluorinated fluids, hydrofluoroethers, and alkylated aromatic fluids. As with all forms of chillers, low temperature chillers can be air or water cooled.
The name for glycol chillers is derived from the use of a glycol water mixture as a coolant. Glycol is an organic compound from the alcohol family that is capable of drastically slowing the rate of freezing. A glycol water mixture is typically 60% glycol and 40% water, a mixture that has antifreeze properties for rapid cooling. It is used as the refrigerant in glycol process chillers and collects heat from circulated water using a thermal heat exchanger.
The types of glycol are ethylene and polyethylene, which are chosen in accordance with the requirements of an application. The deciding factor is the toxicity of ethylene glycol, an issue that prevents it from being used with food products. Polyethylene glycol is non-toxic and is used in food production, breweries, and dairies. The United States Pharmacopeia (USP) provides information on the various grades of glycol to ensure whatever glycol that is chosen meets required safety standards.
The main factor that differentiates glycol from other forms of refrigerants is its consistency and reliability. In the food industry, the cooling properties of glycol enables the production of better tasting and higher quality food products. The variation in the temperature of glycol chillers is the narrowest of all types of process chillers at +/- 1°.
Reciprocating process chillers are an older form of process chiller that uses a piston in the compressor to compress the refrigerant. The components of reciprocating chillers are the same as those for other types of process chillers with the design of the compressor being the distinguishing feature.
The compressor for reciprocating process chillers is positive displacement due to its use of a reciprocating piston to compress the refrigerant. When the piston moves, it creates a vacuum in its cylinder that forces the intake valve open and allows the refrigerant to be sucked in. After the piston reaches the end of the cylinder, it returns to its initial position, which closes the intake valve trapping the refrigerant. The return movement of the piston compresses the refrigerant and increases its pressure. As the pressure on the refrigerant increases, the exhaust valve for the compressor opens and the refrigerant leaves the piston’s cylinder.
The three types of reciprocating compressors are hermetic, semi-hermetic, and direct driven. Hermetic and semi-hermetic compressors are tightly sealed in a housing that contains a motor and the compressor. Components for these compressors cannot be accessed for repair. If a compressor fails, it is removed and replaced. Hermetic and semi-hermetic compressors are not commonly used with high volume process chillers due to their low capacity. Direct drive reciprocating compressors are an older form of compressor that has been replaced with technologically advanced modern compressors.
The process chillers and compressors described above are types of chillers that have the structure and design that is capable of withstanding the harsh environments of manufacturing and industrial operations. Each of the components of a process chiller are selected in accordance with their ability to endure an industrial environment and have longevity. The importance of process chillers necessitates that they be dependable to avoid process and application shutdowns. In all cases, the essential part of process chillers is their compressor, which is the central and essential feature.
Each of the components of a process chiller undergoes a thermodynamic process when a chiller is removing heat and providing cooling. All chillers contain an evaporator, compressor, condenser, and expansion valve. The phases of the cooling process are completed within each of these components. It is critical, with process chillers, that the four phases of the cooling process be completed efficiently and quickly in order to maintain the preprogrammed temperature of a process.
The first phase takes place in the evaporator of a process chiller. It is where heat is absorbed, collected by the circulating water and is removed from the water by heat transfer and absorbed by the refrigerant. The process of the evaporator boils the refrigerant and converts it from a low-pressure liquid to a low-pressure gas or vapor.
The purpose of the evaporator, in phase one, is to act as a heat exchanger. Although there is an absorption of the heat, the refrigerant and water never make contact. The exchange of heat is completed through the walls of tubes, coils, or plates. At the completion of the heat absorption process, the process water or coolant is lowered.
The primary types of evaporators are coil, shell and tube, and plate. The function of each type is the same but is performed differently. Coil evaporators are mostly found in home air conditioning units where warm air is cooled as it passes over coils. Many process chillers use shell and tube evaporators where collected heat is transferred between two fluids. Plate evaporators have rising and falling plates where thin liquid film passes over the plates to complete the evaporation process.
The refrigerant, in the form of a low-pressure gas, leaves the evaporator to enter the compressor, which is a component that defines a chiller and determines the nature of the work that a chiller can perform. The main job of the compressor is to increase pressure on the refrigerant gas using various mechanisms such that the gas reaches a high enough temperature to release its heat in the next phase, which is the condenser.
All types of compressors are designed to apply pressure to the refrigerant gas. The compressor for a chiller system determines the cooling capacity of a system. Choosing the right compressor for a chiller system optimizes the performance of the system. High volume process chillers require the most efficient, durable, and economical form of chiller. It is this aspect of their function that necessitates that they be carefully chosen.
The third phase of the chiller process involves the condenser where the removal of the heat from the refrigerant takes place. This aspect of its function is critical to the performance of a chiller in that it prepares the refrigerant gas or vapor for the next part of the initiation of the heat removal process. In essence, the condenser is a heat exchanger that transitions the refrigerant from a gas to a liquid. The change of the refrigerant prepares it for the next chiller cycle.
As with the other elements of a chiller, the condenser influences the performance of a chiller and affects a chiller’s efficiency. The three forms of condensers are air cooled, water cooled, and evaporative, which combines the principles of air and water cooled. When the gas or vapor from the compressor enters the condenser, it is immediately cooled and releases heat causing it to change back to a liquid.
The fourth and final phase of the chiller process involves the expansion valve, which is a form of metering device. The function of the expansion valve is to lower the pressure of the refrigerant. As the pressure drops, the temperature of the refrigerant drops as well and the refrigerant becomes a liquid gas mixture before entering the evaporator.
The majority of expansion valves are thermal expansion valves, thermostatic expansion valves, and electronic expansion valves. Although the function of all expansion valves is the same, each of them is differentiated by how they complete the process. The purpose of the expansion valve is to control the amount of refrigerant that enters the evaporator.
The definition of an expansion valve as being a controlling device comes from its ability to vary the flow of refrigerant in accordance with changes in the cooling load. When extremely low temperature requirements are necessary, electronic expansion valves (EEVs) are used due to their ability to provide tight superheat control. EEVs have a stepper motor that regulates the valve’s position.
When the refrigerant, in liquid form, enters the evaporator, the heat collection cooling process repeats. The proper performance of each of the elements of a process chiller is essential to a successful cooling process and production efficiency. Chiller manufacturers work with their clients to design and provide a cooling process that meets the needs of a product and application. Experts in the field provide insight and guidance as to the type, style, and form of chiller required for a process.
The purpose of HVAC systems and process chillers is to lower the temperature with distinctly different objectives. Aside from their very different structure, the distinguishing feature that separates HVAC systems from process chillers is their function. HVAC systems or heating, cooling, and ventilating systems heat and cool indoor spaces and maintain indoor temperatures at a comfortable level. Process chillers have a specific function, which is to remove heat from a process.
Process chillers are designed to cool an industrial or manufacturing process in an environment where there are extreme fluctuations in temperature. They are required to operate at a high level 24 hours a day to meet the demands of industrial processes. This aspect of their function radically differentiates them from HVAC systems that do not have to endure such requirements.
Although HVAC systems are a necessary part of industrial operations, they do not have the specific functions related to process chillers. An HVAC system is designed to maintain the temperature in a work area. They keep the ambient air comfortable for workers to perform their jobs. The cooling provided by a HVAC system is not sufficient to cool specific processes since cooling from HVAC systems is a surface cooling.
Process chillers, using a piping system, are directly connected to processes to remove heat. They have more resilient components capable of withstanding the demands of manufacturing. In essence, process chillers perform a function that is similar to air conditioning in a car. Unlike the movement of air in an automobile’s AC system, process chillers move a liquid through a machine to remove heat that is the result of production.
The main focus of an HVAC system is to maintain a programmed temperature. They achieve this through a system of ducts installed throughout a space. During summer months, when the temperature is high, HVAC systems cool the internal temperature to provide a comfortable environment. Large HVAC systems use the mechanisms of process chillers to achieve the proper internal temperature.
During winter months, when the temperature decreases, HVAC systems switch from cooling the environment to heating it. This is achieved in different forms depending on the design of the system. The ducting system that previously pumped cool air into a building delivers warmth at a pre-programmed temperature. In many cases, buildings have systems that maintain the same temperature year-round, which is provided by a well-designed HVAC system.
The amount of stress and strain placed on a HVAC system is far less than the constant demand placed on a process chiller, which has to constantly adapt and change in accordance with the demands on the equipment it is servicing. Although HVAC systems have a certain amount of stress and continually operate, their mechanism does not have the demands of a process chiller.
HVAC systems are less expensive than process chillers due to their design but have high operational costs. Process chillers have high installation costs due to being designed for a specific function. Their constant operation requires regular maintenance and monitoring, which is similar to the maintenance of an HVAC system.
Although the purposes of HVAC systems and process chiller systems are the same, how they are designed to perform their functions and their components are vastly different. HVAC systems remove heat from a building, industrial space, or environment by removing and filtering the air of a space. Their function varies in accordance with the external environment.
Process chillers are a focused device designed to remove heat from a specific piece of equipment or device. Unlike HVAC systems that have a ducting system, process chillers have a set of pipes or tubes that connects them to the equipment they are cooling. Heat is removed by transfer using a refrigerant.
Choosing the right chiller for an industrial application is an important operational decision that can improve production, efficiency, and increase profitability. Industrial manufacturing requires the cooling benefits from process chillers, which are designed to keep equipment cool regardless of the amount of excessive heat. When selecting a process chiller, the first consideration is whether to purchase an air or water cooled chiller. Both types have positive features and provide exceptional service.
Air cooled chillers use ambient air to remove heat from processes using a condenser. They are a cost-effective solution that efficiently completes the cooling process. The medical industry, breweries, research laboratories, and injection mold production rely on the dependability of air cooled chillers.
Water cooled chillers use water from a cooling tower to dissipate heat from the condenser. They are the most common form of process chiller due to the ruggedness of their components and are widely used for industrial operations.
Once the choice is made between an air or water process chiller, there are other factors that have to be considered prior to negotiating with a process chiller manufacturer. Understanding the various aspects of a process chiller will assist in making a sound decision and help manufacturers in providing the best chiller for a device or application.
The selection of a process chiller involves balancing technological needs with process and practical needs. Working with a reputable process chiller manufacturer can assist in the selection process and provide the perfect solution. Their expertise and experience can serve as a guide and reliable source of information. In most cases, process chiller manufacturers become partners that help with upkeep, maintenance, and monitoring of the performance of a process chiller.
Process chillers are an essential part of a variety of industrial operations that rely on process chillers to remove heat for the protection of products and personnel. Manufacturers of process chillers work closely with their clients to develop process chillers that match the requirements and details of heat producing applications. The precision and efficiency of process chillers has made them the perfect production solution.
Brewery process chillers are used for cooling the wort sugar solution, clarifying brite tank temperature control, fermentation, crash cooling, pre-packaging, and product storage. The demands of the brewing industry require process chillers that can meet the heavy duty performance, tighter temperature controls, round the clock operations, compressor modulation, and refrigeration technology that is necessary to produce a well crafted beer.
The quality of milk products requires the removal of heat from processing equipment during pasteurization in order preserve the quality of dairy products. Proper chilling and heat removal ensure product safety, shelf life, and quality. Process chillers are chosen for their able to meet the demands of dairy operators. Their easy maintenance, exceptional performance, tight temperature controls, and durability have made process chillers the perfect tool for dairy product processing.
Food processing is a tightly regulated industry, which requires equipment and machinery that can meet federal regulations. Process chillers serve several functions in food processing that are similar to the dairy industry. For many years, ice was the cooling method used to preserve the quality of food products. The introduction of process chillers has been a revelation that has lowered costs and made ice production more efficient. As with other industrial processes, the food industry requires precision temperature control to meet the unique requirements of various foods. High performance process chillers, with their technologically advanced controls, are able to meet food processing parameters.
The accuracy and maintenance of medical equipment are necessary for the protection of patients. Medical devices provide data as to a patient’s medical condition. As with other forms of equipment, medical equipment produces heat when scanning, imaging, and providing data, which has to be dissipated to avoid equipment failure. Process chillers provide the necessary temperature control, reliability, and efficiency required to produce accurate data for patient diagnosis.
Cannabis production has become a new and ever growing industry. With the changes in regulations, cannabis growers are found in every part of the United States. Although cannabis has been grown illegally for years, modern cannabis production has expanded into large facilities that require high volume temperature control. The key to the successful production and growing of cannabis is precision temperature control due to the delicacy of the cannabis plant. The commercial cannabis industry relies on process chillers and their 24 hour daily operation to preserve cannabis plants and the quality of the final product.
A unique type of process chiller is the extreme low temperature process chiller that produces temperatures that are well below freezing. These well designed durable process chillers are used for underground excavations, aerospace, energy production, automotive production, product testing, and ice where extremely low temperatures are a necessity. Precision designed highly durable low temperature process chillers are capable of meeting these extreme temperature conditions.
The difference between HVAC chillers and process chillers is most evident in manufacturing, where the quality of a product depends on precision temperature control and 24 hour operation. Plastic molding, pharmaceutical production, and chemical synthesizing depend on durable process chillers to ensure product quality. ln addition, process chillers are found
in commercial printing, metal finishing, laser cutting, machine tooling, die-cutting, and the semiconductor industry due to process chillers' ability to provide scalability, tight temperature control, continuous operation, and oil chilling.
Process chillers are a cooling system designed to remove heat from an industrial process using chilled circulating water. They are a direct cooling device that focuses on the cooling of machinery, processes, and critical equipment.
A process chiller uses a closed loop system to remove heat from a specific process by drawing the heat away and dispersing it into the atmosphere.
Air cooled and water cooled are the two general types of process chillers, which are differentiated by how they release heat into the atmosphere.
The central and critical component of a process chiller is its compressor, which can take different forms. It is a part of process chillers that assists in releasing heat from a process chiller’s refrigerant and changes the refrigerant’s pressure and temperature.
Process chillers are essential parts of manufacturing processes. In many cases, they are referred to as mission critical due to their importance to a process. Process chillers are industrial grade devices that are required to provide peak performance 24 hours of every day.
Air cooled chillers are refrigeration systems that cool fluids and work in tandem with the air handler system of a facility. Air cooled chillers are types of chillers that rely on the use of fans to reject heat outside the...
A chiller is a cooling mechanism designed to produce fluids that can lower temperatures by removing heat from the fluid. The type and use of a chiller depends on the required temperature and kind of refrigerant, which can be a liquid or a gas...
Laser cooling is a multi-process that includes a number of techniques in which atomic and molecular samples are cooled down to a temperature near absolute zero. These techniques depend on...
A water chiller, or chilled water system, is a type of refrigeration system which uses water as a secondary refrigerant. They are used for larger, more complex, heating, ventilating, air conditioning, and refrigeration (HVACR) applications...
Cooling towers are specialized heat exchangers that remove heat from water mainly by means of latent heat loss from evaporation while coming into contact with an airstream. Aside from evaporative cooling, water is also cooled by sensible heat transfer due to the temperature difference between air and water...
Heat exchangers are pieces of equipment used to transfer heat between two or more fluids. This process usually involves abundant working or utility media such as water or air that rejects or absorbs heat from a more valuable fluid such as crude oil, petrochemical feedstocks, and fluidized products...
Open loop cooling tower makes use of direct contact with the air in order to cool down the water. It is essentially a heat exchanger. In these types of cooling towers, there is the partial heat transfer due to heat exchange between...
A plate heat exchanger (PHE) is a compact type of heat exchanger that utilizes a series of thin metal plates to transfer heat from one fluid to the other. These fluids are typically at different temperatures...
A shell and tube heat exchanger (STHE) is a type of heat exchanging device constructed using a large cylindrical enclosure, or shell, that has bundles of perfectly spaced tubing compacted in its interior. Heat exchanging is the transfer of heat from one substance or medium to a similar substance or medium...