Air Cooled Chillers
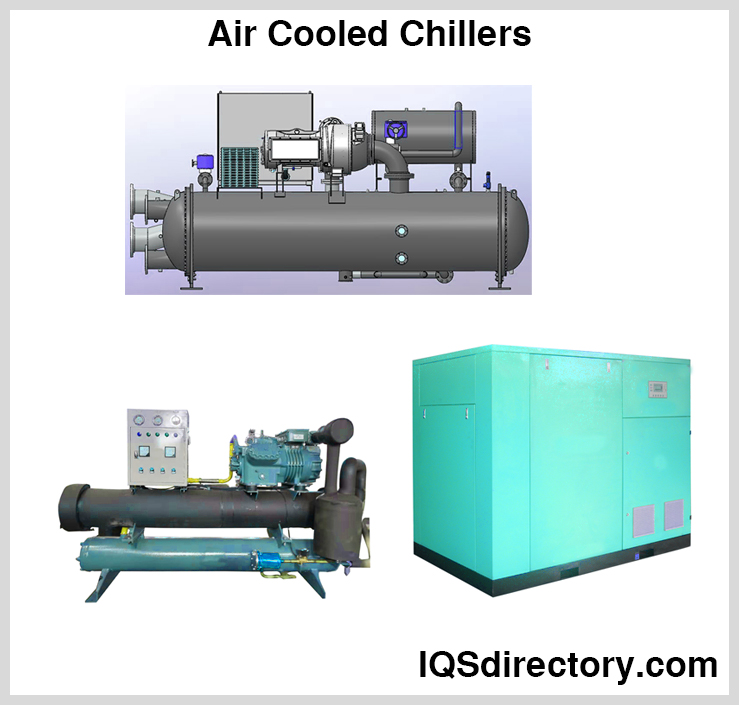
Air cooled chillers are refrigeration systems that cool fluids and work in tandem with the air handler system of a facility. Air cooled chillers are types of chillers that rely on the use of fans to reject heat outside the...
Please fill out the following form to submit a Request for Quote to any of the following companies listed on
This article contains information on chillers, their different types, and their work.
You will learn:
A chiller serves as a cooling mechanism, specifically designed to extract heat by moving a refrigerant through several components where the thermal energy is transferred and expelled. The essential parts of an industrial chiller comprise a compressor, condenser, expansion valve, and evaporator. These components collaborate to circulate the refrigerant efficiently, allowing for the thorough removal of heat from processes, operations, or environments.
There are several types of industrial chillers, each utilizing unique methods for heat extraction. They either employ air or water as a cooling medium. For example, an air-cooled industrial chiller uses fans to disperse the heat. In contrast, a water-cooled chiller leverages a cooling tower to circulate water, facilitating heat elimination.
Besides their cooling methods, industrial chillers are categorized by the type of compressor utilized. Even though all compressors have the fundamental role of compressing the refrigerant to elevate its temperature and pressure before reaching the condenser, they employ diverse designs and operational mechanisms to accomplish this compression.
Industrial chillers operate on the principles of vapor compression or absorption technology. They are specifically engineered to provide a continuous supply of coolant to maintain desired temperatures. This consistent temperature regulation is achieved through a constantly circulating fluid system, which effectively decreases temperatures by extracting heat.
Industrial chillers operate on the principle of vapor compression or absorption. They are engineered to deliver a continuous flow of coolant, maintaining a set temperature. This is achieved through a constantly circulating fluid system that lowers temperatures by removing heat.
Technological advancements, starting in the 1950s and extending into the twenty-first century, have led to the development of cooling and heat removal equipment that can achieve temperatures suitable for processes like laser cutting and die casting. What began as simple water baths in the mid-20th century has evolved into a critical component of contemporary manufacturing.
Industrial operations generate heat through friction, high-powered machinery, and the use of furnaces or ovens. To extend the lifespan of heavy-duty equipment and ensure optimal efficiency and productivity, an industrial chiller circulates cooled liquid through the equipment.
On the manufacturing floor, temperatures can rise rapidly when equipment is in full operation, creating an unsuitable working environment. To protect employee safety, industrial operations use industrial chillers to keep working conditions at the proper temperature. With the addition of an air handling unit, industrial chillers can cool work areas with chilled air, much like an air conditioner. Depending on the building, air cooling chillers can be on top or inside of the building.
Plastic is highly sensitive to temperature and can be damaged if it gets too hot, making proper cooling essential. The cooling temperature of a mold directly affects the quality of the final product. Industrial chillers provide a cooling bath that helps maintain the quality of plastic products. During the extrusion process, a heat exchanger separates the cooling water from the extrusion process to ensure effective temperature control.
In the metal plating industry, high-temperature electroplating or electroless processes generate significant heat during the coating of metals. To manage these extreme temperatures and ensure effective cooling, heavy-duty industrial chillers are used to dissipate the heat from the plated metal.
The food industry enforces strict regulations on the storage temperatures of ingredients and products. Industrial chillers used in this sector function similarly to traditional cooling systems, ensuring that food items are kept at the required temperatures.
Power plants produce substantial amounts of heat during electricity generation. Chillers help manage this by absorbing the heat generated by various components and processes, effectively cooling them down.
Medical equipment demands precise temperature control. MRI scanners, CT scanners, and LINAC machines generate heat that must be managed and dissipated. Industrial chillers offer a consistent cooling source to ensure the efficient operation of these critical devices.
The production of medicines involves the use of chilled water and requires precise temperature control. Industrial chillers are designed to provide the accuracy and precision needed for this chilling process and can be either central or compact process chillers. The four main types of pharmaceutical industrial chillers are reciprocating, screw-driven, centrifugal, and absorption.
Laser Industrial chillers are designed to cool laser equipment or laser processes. For a laser to perform at peak efficiency, it has to maintain an optimal wavelength. CO2, high-power exciters, and ion lasers have to be precise and accurate. They depend on an industrial chillers water cooling system.
Nearly half of all major construction projects rely on rented temporary HVAC systems for heating, ventilation, and cooling. These systems are installed, operated, and maintained to meet the project's short-term needs. Builders and contractors leverage the flexibility of temporary HVAC systems to secure contracts and efficiently manage their projects.
There are three common reasons for the use of a temporary HVAC system, which include:
The portable industrial chiller shown below is an example of a temporary unit suitable for use at a project site. This model is available in both air-cooled and water-cooled versions and includes features that ensure outstanding performance.
Despite the variety of industrial chillers available, most operate on the same fundamental principle for heat removal. A crucial component of this process is the coolant or refrigerant, which absorbs more heat than air and helps maintain stable temperatures. The core concept behind an industrial chiller is that cooling involves removing heat from a process and releasing it into the air.
All industrial chillers are equipped with a condenser, compressor, expansion valve, and evaporator, which circulate a fluid or refrigerant. The operation of an industrial chiller involves transforming the refrigerant from a liquid to a vapor and then back to a liquid. In its vapor state, the refrigerant absorbs heat from the process. As the refrigerant is compressed and condensed back into a liquid, it recirculates through the system to capture and remove heat from the process or operation.
The compressor takes refrigerant at low pressure and low temperature and compresses it into a high-pressure, high-temperature gas. There are three main types of compressors: centrifugal, turbocor, and screw.
The compressed gas passes through coils in the condenser, where air or water flows over the coils to dissipate heat from the refrigerant. As the refrigerant loses heat, it condenses into a liquid.
In the evaporator, the refrigerant reverts to a gas, becomes very cold, and absorbs heat. This is where the refrigerant interacts with the fluid, removing heat from the fluid and transferring it to the refrigerant. Common types of evaporators include copper coil, shell and tube, and plate.
The expansion valve, also known as a thermostatic or electronic expansion valve, regulates the flow of refrigerant between the condenser and evaporator, adjusting the flow according to the cooling load.
The fluid circuit, or cycle, transports the processed fluid to the item being cooled, directly lowering its temperature.
The pumping system circulates cool water or a water/glycol solution from the industrial chiller to the cooling system.
The filter is designed to capture contaminants, dirt, and particles that may enter the chiller fluid. It is also an integral component of the air intake system.
An external heat exchanger for chillers is used for materials that must not come into direct contact with the industrial chiller. Types of external heat exchangers include submersible cooling coils, plate heat exchangers, shell and tube heat exchangers, and jacketed tanks.
While the condenser functions as a heat exchanger, some systems incorporate an additional heat exchanger as part of the fluid cycle, depending on the system's design.
Chillers use significant amounts of electrical power during the chilling process, and their efficiency is assessed by comparing the energy consumed to the refrigeration output. The Coefficient of Performance (COP) and the Energy Efficiency Ratio (EER) are the two primary methods for measuring this efficiency. A high COP indicates that the system is operating at peak efficiency, which also applies to the EER. However, many companies inaccurately claim that their units operate at 100% EER or COP, which is not feasible as these figures do not account for the chiller's load.
The Integrated Part Load Value (IPLV) is a more accurate measure of a chiller's efficiency, as established by the Air Conditioning, Heating, and Refrigeration Institute (AHRI). Since chillers often operate below full capacity, the IPLV provides a calculation that reflects their performance under typical conditions.
The IPLV rating takes into account that most chillers operate below their design capacity most of the time. By evaluating the chiller's performance at four different load levels, the IPLV provides a more accurate representation of a chiller’s overall efficiency.
As one of the largest electricity consumers in commercial enterprises, it's crucial for purchasers to understand how to measure a chiller's efficiency. An efficiently operating chiller reduces operating costs, resulting in substantial savings for the company.
Industrial chillers are categorized based on how the refrigerant releases absorbed heat and the type of compressor used. Additionally, there are specially designed chillers that serve unique and specific functions. Due to ongoing technological advancements and changes in chiller designs, it is not feasible to compile a comprehensive list of all types of industrial chillers.
Water-cooled industrial chillers are typically paired with a cooling tower and utilize a condenser water treatment system to eliminate mineral deposits. The cooling tower supplies water to the chiller, where it is then cooled.
An air-cooled industrial chiller is employed where heat discharge is not a concern. It absorbs heat from the circulating water and transfers it into the air. First, the evaporator absorbs heat from the chilled water, and then the condenser releases this heat into the air as the refrigerant condenses.
Screw industrial chillers, available in both water-cooled and air-cooled versions, utilize a helical rotor to compress and circulate refrigerant vapors.
Screw industrial chillers, which come in both water-cooled and air-cooled versions, use a helical rotor to compress and circulate refrigerant vapors.
Centrifugal industrial chillers employ compression to transform kinetic energy into static energy, thereby increasing the temperature and pressure of the refrigerant. The impeller blades draw in the refrigerant and compress it.
In an absorption industrial chiller, a generator utilizes steam or hot water to convert the refrigerant into vapor. This vapor then moves to the condenser before returning to the absorber. In the absorber, the refrigerant vapor is absorbed by a solution, which subsequently condenses to release heat.
Reciprocating industrial chillers use pistons and a chamber to generate pressure in the refrigerant. They can be either sealed or open in design, with sealed units housing all components within a single enclosure. Because reciprocating chillers operate similarly to automobile engines, they require regular maintenance.
Explosion-proof industrial chillers are built for heavy-duty applications and must adhere to specific National Fire Protection Agency (NFPA) guidelines during construction. They feature a specially reinforced structure to safeguard against flammable materials and must be custom-ordered. Designed primarily for the protection and safety of workers, these chillers operate on the same principles as standard chillers but with enhanced reinforced protection.
Low-temperature industrial chillers are for industries that operate below freezing and require chillers that can produce temperatures at –40°F (-40°C). They are used for ice rinks, petrochemical cooling, chemical extraction, and medical, pharmaceutical, and food processing industries as well as product testing labs.
An evaporative industrial chiller utilizes the process of evaporation to cool air. As water evaporates, it turns into gas, carrying away high-energy particles and causing a significant drop in the surrounding air temperature. This cooling effect can be experienced when mist is introduced into a room. An evaporative chiller amplifies this natural evaporation process using advanced technology.
An evaporative industrial chiller operates using a water reservoir, a fan, and thick pads. The fan pulls in hot air, which then flows through the moist pads that absorb water from the reservoir. As the hot air passes through the pads, the surface water evaporates, resulting in a temperature drop of nearly 20 degrees Fahrenheit.
Thermoelectric coolers (TECs) utilize the Peltier effect, which generates a heat flux at the junction of two different materials when a DC current is applied. In this setup, positive and negative semiconductors are arranged parallel in the thermal path and in series along the electrical path. When voltage is applied, electrons transport heat to one side, cooling the other side. The heat is then absorbed by a heat sink and expelled into the ambient air by fans.
A TEC assembly can be mounted directly onto a cold plate or used to cool a refrigerant liquid. TECs are typically employed in applications where the cooling requirement is less than 400 watts.
The term "laser" stands for Light Amplification by Stimulated Emission of Radiation. A laser is produced when electrons in the atoms of optical materials—such as glass, crystal, or gas—absorb energy from an electrical current. This energy excites the electrons, causing them to move from a lower to a higher energy state and emit electromagnetic radiation.
In ordinary light, light waves travel in various wavelengths and directions, each wavelength corresponding to a different color with distinct peaks and valleys. To the naked eye, this light appears white. In contrast, a laser beam consists of coherent light, with all the waves moving in the same direction and synchronously aligned peaks and valleys. The concentrated light energy in a laser produces a substantial amount of heat.
When laser light is aimed at a surface, its light energy converts into heat, which can cut, melt, or burn the material. This process generates heat that must be managed to maintain the laser’s efficiency and prevent damage. Industrial lasers employ various chillers and cooling methods to keep the temperature constant.
Laser chillers are designed to dissipate heat generated during the laser process, helping to maintain the laser's wavelengths and ensure beam quality. High-powered lasers typically require robust water-cooled chillers, while lower-powered lasers can be effectively cooled using other methods, such as different types of fans.
Cold plates are essential for cooling lasers and are used in conjunction with recirculating chiller systems. They come in various forms, such as tubed and aluminum vacuum-brazed designs.
Cold plates can be mounted on the laser and receive cooling liquids from a chiller. The heated liquid from the process is then returned to the chiller. In some cases, the cold plate can also be designed to function as the electrodes in a laser system.
Vapor compression industrial chillers use a refrigerant that circulates through an evaporator, compressor, condenser, and expansion valve. This process is highly efficient for cooling high-wattage loads while consuming less energy. In a laser system, a vapor compression chiller can be employed by adjusting the evaporator cycle. Alternatively, other cooling methods involve running the refrigerant directly through the cold plate.
The vapor-compression style of liquid chiller is the most commonly used cooling method for high-powered lasers. These chillers can cool up to 10 kW and are compatible with all types of lasers.
The miniature rotary compression system has become a popular method for cooling lasers. Advances in rotary compressors have enabled the miniaturization of compression systems to handle heat loads of up to 100 watts. This compact design is widely used with lasers due to its efficiency and space-saving advantages.
Miniature rotary compressor chillers are portable and offer precise temperature control. They provide cooling capacities ranging from 3 kW to 140 kW and operate within temperature ranges of 20 °F to 80 °F (-6.6 °C to 26.6 °C).
In a direct expansion chiller system, the refrigerant flows directly through the cold plate and is driven by the compressor, eliminating the need for a water cooling loop and simplifying the system. This design removes the requirement for a secondary coolant loop. During this process, the refrigerant undergoes an isothermal phase change, providing exceptional temperature control across the cold plate.
Direct expansion systems include the standard components of a compressor, condenser, expansion valve, and evaporator, which absorb heat directly. They offer a compact cooling solution with a miniature rotary compressor. The key advantage of this system is its precise temperature control. Direct expansion cooling systems are specifically designed for high heat flux applications, such as laser cutting and burning.
Although the fundamental operation of industrial chillers is consistent across different types, regular maintenance is essential to ensure optimal performance. Like any industrial equipment, scheduled monitoring and inspections are crucial. Manufacturers strongly recommend adhering to their guidelines for maintaining and checking chiller components to ensure they operate according to specifications.
Heat transfer is a crucial aspect of a chiller’s operation. Condenser coils can become clogged or obstructed, affecting the free passage of air.
An industrial chiller's performance is heavily reliant on the refrigerant. Incorrectly charged refrigerants can significantly affect the chiller's efficiency and operation.
Water used in cooling towers must meet specific flow parameters. Debris, dirt, solids, and contaminants can disrupt water flow and adversely affect the chiller’s performance.
To ensure optimal performance from a chiller, all reservoirs should be regularly checked to confirm they have an adequate supply of fluids.
Chillers perform optimally at 50 °F (10 °C). Unmonitored temperature fluctuations can negatively impact their operation. To achieve the best results, regularly checking the glycol inlet and outlet temperatures helps identify potential issues early.
All equipment accumulates dirt and dust during the manufacturing process. To maintain peak efficiency, regularly clean the exposed parts of the chiller and replace filters to prevent clogging.
Air cooled chillers are refrigeration systems that cool fluids and work in tandem with the air handler system of a facility. Air cooled chillers are types of chillers that rely on the use of fans to reject heat outside the...
A glycol chiller is a chilling system that uses a percentage of glycol mixed with water to create extremely low temperatures far beyond the freezing point of water. The two types of glycol are ethylene glycol based or propylene glycol based...
Laser cooling is a multi-process that includes a number of techniques in which atomic and molecular samples are cooled down to a temperature near absolute zero. These techniques depend on...
A water chiller, or chilled water system, is a type of refrigeration system which uses water as a secondary refrigerant. They are used for larger, more complex, heating, ventilating, air conditioning, and refrigeration (HVACR) applications...
Cooling towers are specialized heat exchangers that remove heat from water mainly by means of latent heat loss from evaporation while coming into contact with an airstream. Aside from evaporative cooling, water is also cooled by sensible heat transfer due to the temperature difference between air and water...
Heat exchangers are pieces of equipment used to transfer heat between two or more fluids. This process usually involves abundant working or utility media such as water or air that rejects or absorbs heat from a more valuable fluid such as crude oil, petrochemical feedstocks, and fluidized products...
Open loop cooling tower makes use of direct contact with the air in order to cool down the water. It is essentially a heat exchanger. In these types of cooling towers, there is the partial heat transfer due to heat exchange between...
A plate heat exchanger (PHE) is a compact type of heat exchanger that utilizes a series of thin metal plates to transfer heat from one fluid to the other. These fluids are typically at different temperatures...
A shell and tube heat exchanger (STHE) is a type of heat exchanging device constructed using a large cylindrical enclosure, or shell, that has bundles of perfectly spaced tubing compacted in its interior. Heat exchanging is the transfer of heat from one substance or medium to a similar substance or medium...