Types of Metal Finishing
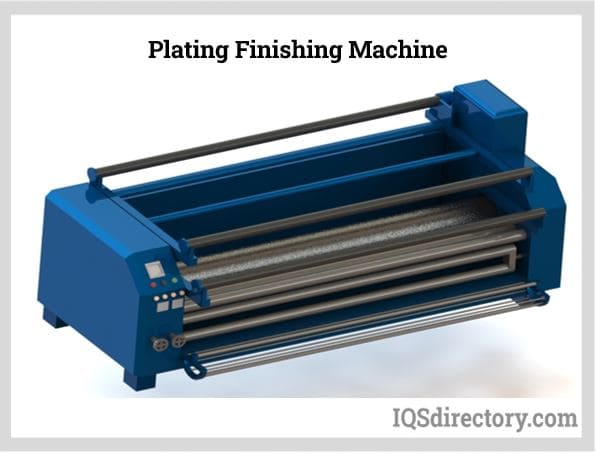
Metal products are found everywhere in our houses at work. In its raw form, plucked from nature, metal is hard, crude, and unattractive. To make the best use of it, it needs to be finished, polished, and...
Please fill out the following form to submit a Request for Quote to any of the following companies listed on
This article will take an in-depth look at industrial coatings. It will bring more understanding on topics such as:
This chapter delves into the foundational principles behind industrial coatings and their varied applications.
An industrial coating acts as a protective shell applied to surfaces, designed to shield them from damage while also enhancing appearance. The main goal of these coatings is to protect surfaces against environmental threats and other potential damage. They can be applied to an array of surfaces, such as concrete, wood, metal, plastic, glass, rubber, leather, mortar, and asbestos.
Industrial coatings are available in many types, each possessing unique traits and benefits. Selecting the appropriate coating depends on the environment and the qualities of the surface in question. Coating manufacturers provide expert guidance on the best practices for application.
These coatings are crafted to deliver both visual appeal and durability. Multiple options are available, such as Xylan dry film lubricants, resins, and xylene.
The coverage of industrial coatings extends widely, with their chief function being to protect equipment from corrosion. The aesthetic value is also crucial for particular equipment and settings. These coatings are commonly applied to safeguard materials like concrete or steel.
Furthermore, industrial coatings play a role in boosting materials' resistance to fire and other hazards. They are used to line water tanks and reservoirs, ensuring a safe environment for potable water and preventing corrosion.
Polymers are the most prevalent materials for industrial coatings, including epoxy, moisture-cure urethane, polyurethane, and fluoropolymer coatings.
Several elements are critical when applying industrial coatings, including the following:
To ensure adhesion, the substrate—or base material—receiving the protective layer must be cleaned beforehand. Most coatings rely on either a mechanical or physical bond to adhere to the substrate's surface. Chemical bonding may also form a strong layer. A surface not properly cleaned of dust, chemicals, or contaminants may lead to premature coating failure.
Proper substrate surface preparation is vital for the successful application of industrial coatings. Before the coating application, the surface should be thoroughly cleaned of moisture, dry contaminants, and salts using methods such as heating, blasting, or chemical cleaning. Effective cleaning mitigates issues like fisheyes, blistering, adhesion failure, alligatoring, bubbling, and cissing.
Priming is a critical step in any industrial coating process, ensuring the coating and sealant adhere well to the substrate for lasting performance. Primers enhance compatibility between various substrates and coatings, improving final appearance by evening out surface imperfections.
With the primer applied, the substrate is primed for coating. Different coating methods are employed, each aimed at thoroughly covering the substrate's surface. The method chosen often depends on the substrate's size and complexity. Popular coating processes include dip, brush, roll, spray, spin, and flow coating.
The curing and drying practices influence coating performance. Incorrect procedures can undermine coating quality. Each product should come with detailed instructions for ideal drying and curing procedures to maximize results.
Proper curing requires maintaining the right temperature for a specified time on the substrate, not just the oven. Thus, bake times can differ based on the part's thickness.
Upon completing the coating process, parts should be inspected to meet specific standards. Industrial coatings must meet precise thickness requirements to provide full coverage and reflect all details. Effective inspection policies help ascertain coating projects remain within acceptable thickness ranges.
Choosing a fitting industrial coating requires careful consideration of both the equipment and coating materials. A robust coating setup demands components like durable pump seals, clean filters, and routinely flushed air lines. Poor maintenance may produce suboptimal results.
Suppliers work alongside customers to assess procedures, ensuring workplaces are clean, followed by routine equipment maintenance.
Consider these factors for a custom industrial coating solution:
Picking the right formulation hinges on the substrate, often needing materials such as urethane, acrylic, or epoxy. Manufacturers must also factor in the types of materials and when the application takes place during production.
Certain substrate and coating pairings can be matched using suitable primers or additives to bolster binding and other attributes. Specifications, like corrosion resistance or adhering to food safety norms, influence material selection choices.
Various application steps and materials yield different outputs depending on the substrate's condition. Some substrates, like plastic, need a heat cure to keep the coating intact without causing deformation.
Environmental factors must be weighed when selecting coatings. A steady, clean setting with controlled temperature and humidity is crucial. Environmental inconsistencies may cause uneven finishes. Temperature shifts and fluctuating humidity can result in thermal shock.
During application or drying, chemical changes might occur due to exposure to splashes, fumes, or contaminants, impacting efficacy. Parts require shielding from abrasion, UV exposure, and physical harm during curing.
The desired coating outcome is shaped by the application process details. Thoroughly planned techniques—like spraying, brushing, or dipping—should offer precise thickness oversight. There's also a need to consider substrate prep, post-cure cleanup, baking and curing methods, spatial requirements, and controlled drying conditions.
Industrial coatings entail distinct characteristics. Epoxy and urethane are both resistant to numerous chemicals and physical forces, but epoxies falter with outdoor exposure and can both be compromised by nitric acid. Water-based variants, although safer for application, might heighten the risk of base material corrosion. The functional and visual properties of a coating primarily depend on its makeup and application technique. Important properties for consideration include flexibility, smoothness, gloss retention, color stability, moisture resistance, and conductivity or solderability for further processing. At every formulation stage, the part’s intended function should direct the necessary coating properties for peak performance.
Some of the different coating techniques are:
A cost-effective process provides high quality coating that is uniform on substrates of different shapes or sizes including large surface areas. Dip coating can be carried out manually or automatically for application productions of high volume.
Parts are immersed in a tank filled with liquid polymer and then withdrawn at a controlled rate under regulated temperature or atmospheric conditions. The coating's thickness is influenced by factors such as the viscosity of the coating, the rate of withdrawal, the number of dipping cycles, and the duration of immersion. Solidification typically happens at high temperatures within an oven.
To ensure surfaces are free of contaminants, it is essential to clean them before dipping. For effective process control and to maintain consistent quality standards, the flow and runoff properties are crucial. Deep coating allows for simultaneous coating of both internal and external surfaces.
For durable protection against abrasion, water, corrosion, humidity, extreme temperatures, wind, and UV light, it is essential to choose Master Bond eco-friendly liquid polymeric formulations. These formulations come in a variety of colors and enhance appearance. Special coating grades offer additional benefits, such as optical clarity, toughness, resistance to solvents and acids, low friction, vibration and impact resistance, and exceptional electrical insulation properties.
E-Coat is a hybrid process between plating and painting that involves immersing a part in a water-based solution containing a paint emulsion. An electric current is applied to both the solution and the part, causing the paint emulsion to deposit and form a coating over the part. This process ensures that the part is coated both internally and externally. Any metal surface accessible to the solution or exposed is coated.
The E-Coat process offers superior protection against corrosion and rust while also improving the appearance of parts. It is highly durable, providing resistance to salt spray, dielectric interference, and acids. Compared to powder coatings and solvent-based spraying, E-Coat delivers complete coverage and consistent thickness. Additionally, parts can be processed either wet or dry with E-Coat.
Due to its exceptional durability, E-Coat is extensively used in industries such as oil and gas, HVAC systems, water and wastewater management, and aerospace. It can be applied to a wide range of substrates, including castings, stampings, structural iron, pipes, springs, and aluminum castings, among others.
Achieving excellent leveling and uniform distribution of liquid polymer requires skilled personnel and the appropriate brush or bristles. Multiple coats might be necessary to reach the desired film thickness.
The bristles of the brush, whether synthetic or natural, must be compatible with the product being applied. When coating irregular substrate surfaces such as corners, edges, bolt heads, piping, and welds, it is important to consider the brush's shape, size, and angle. Brushes should be clean before use. Although brushing is slower compared to other coating techniques, it has a short setup time. Benefits of brushing include low capital cost, minimal wastage, and economic efficiency for production runs.
Roll coating involves applying a base, intermediate, and topcoat to flat substrates using rollers. One common method employs three rollers: a soft application roll, a polished steel roll, and a metering or doctor roll. As the material passes through these rollers, each performs a specific function in the coating process. Roll coating can be carried out manually or with an automatic conveying system.
For high-volume production, automated roll coating equipment, such as gravure coating and direct roller coaters, can efficiently apply liquid polymeric coatings with consistent thicknesses to flat surfaces. Key parameters for selecting the appropriate machine include the thickness or width of the substrate, the type of substrate, the speed of operation, and the overall or partial cost.
Roll coaters come in various configurations, offering reliability, cost-effectiveness, and high-quality finishes that meet diverse requirements. This technique is widely used for its continuous energy efficiency and reduced labor needs. It also provides benefits such as reduced waste, excellent weight control, efficient coating transfer, and design flexibility.
A specialized form of roll coating is gravure roll coating, where adhesives are applied to the substrate using a roll or applicator ball etched to control the amount of coating. The size of the gravure roll determines the dimensions of the finished coating.
Gravure coating methods include direct and offset variations. In the direct method, the steel roll features the engraving pattern, and a blade removes excess adhesive. The offset method, a variation of direct coating, employs an offset roll placed between the gravure roll and the coating material to apply the coating, providing an additional layer of control between the applicator and the gravure roll.
Spraying is an economical and versatile coating process suitable for parts of various types, sizes, and shapes, including large surface areas. It can be performed manually or automatically and is effective for both viscous and non-viscous liquid coatings. This method offers high transfer efficiency, ensuring uniform quality finishes.
The desired film thickness is achieved using various types of spray guns and equipment, including air atomized conventional sprays, airless sprays, and air-assisted airless sprays. This equipment optimizes material usage and meets specific requirements such as finish quality, film thickness, edge build-ups, overspray reduction, reliable performance, and minimizing waste.
A crucial factor in using spraying as an application method is the quality of the compressed air, which is assessed based on the size and concentration of solid particles, water vapor content (measured by the pressure dew point temperature), and oil concentration. These factors are influenced by the compressor, dryer, and filtration system.
When using a compressed air system, it's important to determine the type of air needed for the spraying application. Since all air contains moisture, the water content increases as air is compressed. If dry air is required, drying equipment should be used to remove the moisture. Oil-lubricated air compressors require filters to reduce oil content, with different grades of filters available to achieve varying levels of air quality.
Spraying offers the advantage of being performed from a vertical angle, contributing to a safer work environment. However, common drawbacks include uneven spraying, sagging, orange peel, pinholes, overspray, and spluttering. To optimize performance and flow, careful control features must be adhered to.
To achieve defect-free coatings, high standards for spray application techniques are essential, facilitating effective transfer efficiency. For smooth finishes, it is important to determine the optimal spray distance, angle, and pattern.
Thermal spray coating involves using heat to melt metallic or ceramic materials, which are then applied to the surface of a workpiece. This process is employed to enhance the appearance of new components or to restore damaged ones. It adds protective qualities and improves the visual appeal of parts and components. The amount of heat used varies depending on the properties and characteristics of the coating material.
This technique is suitable for applying coatings to a diverse range of materials, parts, and components. It provides resistance to wear, erosion, cavitation, corrosion, abrasion, and heat. Additionally, thermal spray coating enhances product properties by offering conductivity, insulation, lubricity, and chemical resistance.
In all forms of thermal spray coating, small particles of metal or ceramic material are sprayed onto a clean, prepared surface, where they adhere to form a coating layer. The thermal process and kinetic energy cause the particles to flatten onto the surface and bond with each other, creating a cohesive layer. While all thermal spray coating methods share this basic principle, they differ in specific aspects of the process.
The factors that differentiate thermal spray coating processes include the type of heat, temperatures, velocities, coating materials, and the type of bonding. Thermal spray coating processes use unique ways to produce heat with some using arc welding heat while others use gas flames. Included in the type of heat is the temperature reached by the gas stream and the velocity of the coating process. As with all forms of plating and coating methods, the types of materials to be coated on a substrate vary according to their properties, which has an impact on the thermal spray coating method.
Thermal spray coating involves applying molten material, heated to a high temperature, to the surface of a metal to create a strong and secure bond. While the overall goal of thermal spray coating remains consistent, the methods used to achieve this can vary. Plasma and oxy-fuel are two primary heat sources used in these processes.
Flame spray was developed over 100 years ago and uses a welding torch with a high velocity spray to place molten metal on the substrate. The coating feedstock is in the form of a wire or powder. Flame thermal spraying is limited to materials with low melting points and do not strongly adhere to the substrate
HVOF is a flame thermal spray process that creates a combustion jet using a gas, such as hydrogen, propane, or propylene, to reach temperatures of 2500°C up to 3100°C (4500°F up to 5600°F). The produced coating is very dense with low porosity that is hardened and wear and corrosion resistant.
Two wire electric arc spray uses electric conductivity created between two wires to heat and melt the material for deposition. It has similar combustion as flame spraying. Once the material is heated by the two wires, compressed air distributes it. Two wire electric arc spray is a cost effective method that uses aluminum or zinc as the coating material and has the highest rate of deposition of thermal spray methods.
The plasma spraying process uses an inert gas, such as argon or an argon hydrogen mixture, to heat a DC current arc. The interaction between the DC electric arc and the gas forms a plasma jet. Powder material is injected into the flaming plasma at the nozzle. The rapid expansion of the gas and powder pushes the powder particles onto the surface of the workpiece. The key to the process is the velocity at which the molten material strikes the substrate to form a tight bond.
VPS is a form of plasma spraying that takes place in a low pressure atmosphere chamber with a pressure level below 0.1 mbar to prevent oxygen and hydrogen from affecting the coating process. Under the unique conditions, spraying is completed in the same way as regular plasma spraying. The VPS atmosphere prevents metal particles from oxidizing. The plasma spray has a larger diameter and longer length as convergent and divergent nozzles create greater speed. The coatings from the process are denser and more adherent due to lower oxide in the atmosphere.
With detonation spraying, a long water cooled barrel that has inlet valves for gases and powder has oxygen and fuel fed into the barrel with the powder. The mixture of gas and oxygen is ignited to reach a temperature of 4000° C (7232° F) by a spark that heats and accelerates the powder to supersonic speeds. The kinetic energy of the powder particles hits the substrate to form a dense coating. Once the barrel is purged by nitrogen, the process repeats every few seconds.
Thermal spray coating can be applied using various types of coating materials, each offering distinct properties and characteristics to enhance a product's quality and performance. Most thermal coatings are resistant to abrasion, corrosion, erosion, and rust.
Thermal spray coating can be applied using over 80 different types of metals and coating materials, including:
In spin coating, a coating is applied to the center of a substrate, which is then spun at high speed by centrifugal force. The spin coater continues to revolve until the desired film thickness is achieved. Key parameters that influence the process and help meet specific application requirements include the spinning rate, resin materials, substrates, surface tension, acceleration, and viscosity.
Spin coating is highly effective for achieving thin, uniform coatings with consistent quality and repeatability. The process is straightforward, rapid, and suitable for substrates of various sizes. However, potential issues during processing can include uncoated areas, streaks, comet-like patterns, swirl marks, and films that are either too thin or too thick.
Flow coating is a straightforward, quick, and dependable technique for applying liquid coatings, either manually or automatically. It is particularly recommended for large, flat horizontal sheets and panels that are difficult to dip coat. This method allows for achieving high coating thicknesses with just a single application.
Flow coating is a space-efficient, low-waste, and cost-effective method with high transfer efficiency. In this process, coatings are dispensed onto the upper part of the workpiece, flowing down to cover the flat surface areas completely. The controlled flow is influenced by the viscosity of the compound. The final finish and uniformity can be affected by curing conditions such as temperature and humidity. However, flow coating is not suitable for parts with holes or protrusions.
Slot die coating is a pre-metered method where the final coating thickness depends on the rate at which the coating is applied. In this process, material is delivered through a narrow slot positioned over the surface to be coated, creating a thin film on the substrate. Slot die coating can be integrated into various types of operations.
The slot die coating mechanism consists of several systems: metering, distribution, head positioning, and substrate movement. The metering system controls the flow of the coating material, while the distribution system ensures an even spread. The head positioning system maintains the correct orientation of the coating head relative to the substrate, and the movement system advances the substrate past the slotted head.
PVD coating, or Physical Vapor Deposition, also known as thin film coating, involves vaporizing solid materials in a vacuum and applying them to a substrate. This process deposits material atom by atom, creating a thin metal or metal-ceramic layer that enhances the component's appearance, durability, and functionality. The result is an extremely thin, environmentally friendly coating.
The PVD coating process consists of four main steps: ablation, transport, reaction, and deposition. The two primary types of PVD coating are sputtering and thermal deposition. Thermal deposition uses high temperatures and vacuum pressure for vaporization, while sputtering employs a vacuum chamber with a high-energy source.
Sputtering, though slow and complex, yields a pure and uniform coating. Thermal deposition offers high throughput and efficiency but requires additional tooling.
PVD requires precision timing for the vaporized atoms to bond with the target material. Reactive or inert gasses, such as oxygen or nitrogen, assist in forming a strong bond between the coating and substrate. The final step in the process involves rotating the substrate while monitoring the rate of deposition using various tools. The process can be automated using conveyor belts placed before the vaporized arc for a specified length of time.
The PVD coating process is utilized across various industries, including food packaging, medical devices, optics, cookware, and plumbing fixtures. It is particularly effective for inorganic solid materials with high melting points.
The various types of industrial coatings include:
What properties do these types of coatings offer, and how do they compare to other materials? For example, Teflon coatings are known for their excellent dielectric stability, low coefficient of friction, near-total chemical inertness, and heat resistance.
Teflon coatings are the original non-stick finishes. Industrial products made out of Teflon coatings or fluoropolymer resins exhibit exceptional high temperature resistance and are also resistant to chemical reactions, stress cracking, and corrosion. These industrial coatings can be used on aluminum, carbon steel, stainless steel, brass, steel alloys and magnesium as well as on non-metallic like glass, plastics, and fiberglass.
What are the characteristics of Teflon coatings?
Only a few solid substances can adhere to a Teflon finish. Most materials release easily from Teflon surfaces, although tacky substances may exhibit some adhesion.
The coefficient of friction for Teflon ranges from 0.05 to 0.20, varying based on factors such as sliding speed, load, and the specific type of Teflon coating used.
Teflon surfaces are both oleophobic and hydrophobic, making them resistant to wetting. This property facilitates easy and thorough cleaning, as these surfaces are often self-cleaning.
Teflon industrial coatings can continuously operate at temperatures up to 500°F (260°C) or 1112°F (600°C) with proper ventilation.
Most Teflon industrial coatings can endure extreme temperature variations without compromising their physical properties. They can be used effectively at low temperatures as low as -454°F (-270°C).
Teflon industrial coatings remain unaffected by chemical environments.
Teflon exhibits a low dissipation factor, high dielectric strength, and very high surface resistivity across a wide range of frequencies.
While Teflon coatings offer many benefits, there are important considerations when working with them, particularly during the curing process. Teflon coatings emit toxic phosgene gas when cured, which poses significant hazards. It is crucial to consult with coating manufacturers for guidance on safely managing these risks and handling Teflon coatings properly.
Excalibur coatings are widely regarded as the toughest, most durable, and longest-lasting non-stick coatings available. Unlike other coatings, Excalibur is a complete coating system rather than just a layer applied over an existing substrate.
The Excalibur system starts with the arc-spraying of stainless steel onto a component, integrating it seamlessly. Following this, the stainless steel matrix is infused with premium non-stick coatings. This process results in a coating system that combines the durability of stainless steel with the superior release properties of non-stick surfaces.
The application of Excalibur Coating involves the following steps:
When the surface properties of an ideal material in engineering construction are unsuitable, these coatings become essential. Xylan coatings, applied as a thin film, are particularly effective at binding to surfaces that do not readily accept other PTFE coatings. They provide controlled friction, wear resistance, non-stick and release properties, lubrication, and corrosion prevention.
These coatings were developed to offer a wide range of valuable performance attributes. Single coat thin films of fluoropolymer provide excellent corrosion resistance and chemical resistance. Additional benefits include resistance to galling, electrical resistance, abrasion resistance, non-stick and non-wetting properties, and reduced friction. OEM components coated with fluoropolymer tend to have a longer lifespan before needing replacement.
These coatings offer a distinctive blend of surface-enhancing properties that stand out in the industry. They are engineered to withstand extreme temperatures, feature exceptional surface hardness, resist galling, and provide anti-friction benefits. Among high-performance options, Nitro coat is the preferred choice.
Nitro coat barrier coatings are chemically applied using cutting-edge technology. These coatings are effortlessly applied to most metallic substrates, resulting in thin, extremely uniform, and dense layers. Components coated with the Nitro coat process consistently exhibit outstanding performance under both extreme field conditions and rigorous laboratory testing.
These coatings are primarily designed to enhance material performance by increasing operating temperature, load-bearing capacity, and friction coefficient. They provide effective lubrication across a wide range of loads, often exceeding 250,000 psi. By transferring lubricant between mating surfaces, moly coatings offer sacrificial lubrication, which helps reduce both friction and wear.
Molybdenum coatings combine high-performance resins with molybdenum disulfide lubricant. The coating is thermally cured to ensure a strong bond with the base metal of the coated part.
These high molecular weight coatings are expertly formulated to provide exceptional corrosion resistance in various environments. They serve as effective abrasion-resistant coatings while delivering superior barrier protection against alkaline compounds, harsh chemicals, solvents, and caustic solutions.
These coatings are designed to protect metal surfaces from oxidation caused by high temperatures, as well as from acids, water, and other corrosive agents. They are commonly used in offshore, military, and chemical processes, delivering significant performance benefits. By safeguarding steel engine components, these heat and corrosion-resistant coatings can notably extend their lifespan.
These coatings are two-coat non-stick systems consisting of a primer and a topcoat. They offer the highest operating temperature tolerance among fluoropolymers, along with excellent abrasion and chemical resistance, and an exceptionally low coefficient of friction. Capable of withstanding temperatures up to 600 degrees Fahrenheit, these coatings are typically applied with a thickness of 1-3 mm.
These coatings are resin-bonded polymer systems known for their exceptional resistance to chemical reactions and thermal degradation. They remain virtually unaffected by solvents up to 500°F (260°C), making them a popular choice in the chemical processing industry. PPS coatings can be used alone for excellent corrosion and chemical resistance or as a primer beneath a topcoat. In addition to their thermal and chemical benefits, PPS coatings offer outstanding abrasion and wear resistance.
PVDF is a pure fluoropolymer known for its exceptional strength, purity, and resistance to acids, solvents, heat, and bases. It also generates minimal smoke during fires. At high temperatures, PVDF can dissolve in polar solvents like amines and organic esters, making it ideal for corrosion-resistant coatings and durable architectural finishes for building panels.
PVDF can be easily melted for extrusion or injection molding applications. It is widely used in high-purity semiconductor markets, the paper and pulp industry, nuclear waste processing, water treatment, and chemical processing. Additionally, PVDF meets the stringent specifications required by the food and pharmaceutical processing industries.
These coatings offer exceptional chemical resistance and reliable electrical properties. ECTFE coatings are ideal for applications requiring superior thermal and chemical resistance beyond what PVDF can provide.
These coatings are applied as free-flowing dry powders and do not require solvents to bind the components. Powder coatings are typically applied using a fluidized bed or an electrostatic spray. To fuse the particles and ensure adhesion to the surface, the parts are heated both before and after application. These coatings are primarily used for metals, but can also be applied to some thermoplastics and thermosets.
Metallized coatings, also known as thermal spray coatings, are applied in a molten or semi-molten form to provide corrosion protection by spraying metals onto steel or concrete surfaces. Common metals used for these coatings include aluminum, zinc, and their alloys.
These coatings are favored for their long service life, immediate curing, and lack of volatile organic compounds (VOCs). They can be applied in various conditions, with the metal being heated prior to application. Metallized coatings are particularly suited for outdoor use due to their enhanced resistance to impact and UV rays.
Hard coat refers to a fast setting urethane or polyurea elastomer. It works well on wood or other materials, with some forms having UL-tested fire ratings. Hard coat forms a solid finish on surfaces such as styrofoam and urethane foam. They contain no solvents and are volatile organic compounds that can serve as vapor barriers.
Hard coat formulations offer a range of properties, from soft and rubbery to hard and rigid. While hard coat can be tinted to a base color, it typically lacks UV stability unless it has an aliphatic formulation. Often, hard coat is applied without color and then painted. To ensure stable adhesion, especially in extreme or harsh conditions, a primer is necessary. As with many industrial coatings, proper surface preparation is crucial for achieving the best results with hard coat applications.
Low friction coatings offer friction coefficients ranging from 0.2 down to 0.05, with polytetrafluoroethylene (PTFE) providing the lowest coefficient. The choice of coating type depends on the specific application, as each offers different wear resistance and hardness characteristics.
Applying a low friction coating can reduce high static friction coefficients between mating parts, thereby minimizing the forces involved. Additionally, these coatings help prevent foreign substances from adhering to treated surfaces. Beyond metals, low friction coatings are also effective on elastomers and rubber, reducing their friction values.
This chapter will explore the applications and benefits of industrial coatings. It is crucial for workers to adhere strictly to the manufacturer’s guidelines to ensure the success of the coating process and the safety of those involved. Manufacturers provide detailed instructions for the safe handling of coating materials and offer contact information for any questions about the application process.
There are many diverse types of industrial coatings with many different characteristics. For instance, the PVDF coating is highly reactive and is used in applications where highest strength is required. Each coating provides many benefits to the equipment on which it is applied; for instance, by improving the equipment’s wear resistance or strength. Therefore, when selecting a coating for equipment, one must be cautious of the properties of the coating material and the environment in which the equipment is going to be used. The bottom line is that industrial coatings are there to protect equipment from harsh weather or environmental conditions that end up damaging the equipment, ultimately prolonging its lifespan.
Metal products are found everywhere in our houses at work. In its raw form, plucked from nature, metal is hard, crude, and unattractive. To make the best use of it, it needs to be finished, polished, and...
Anodized aluminum is aluminum that has undergone an anodizing process to create an exceptionally durable, corrosion-resistant, and highly aesthetic surface. Anodizing creates a stable aluminum oxide layer fully integrated with...
Plastic coating is the application of liquid polymers or plastic on the surface of a workpiece by dipping or immersion. The result is a thick plastic finish for protective and decorative purposes. This gives the material additional resistance against...
Metal plating refers to a process where a thin layer of metal coating is placed on the surface, or substrate, of a metal part, component, or product. The process can consist of electroplating, which deposits...