Fasteners
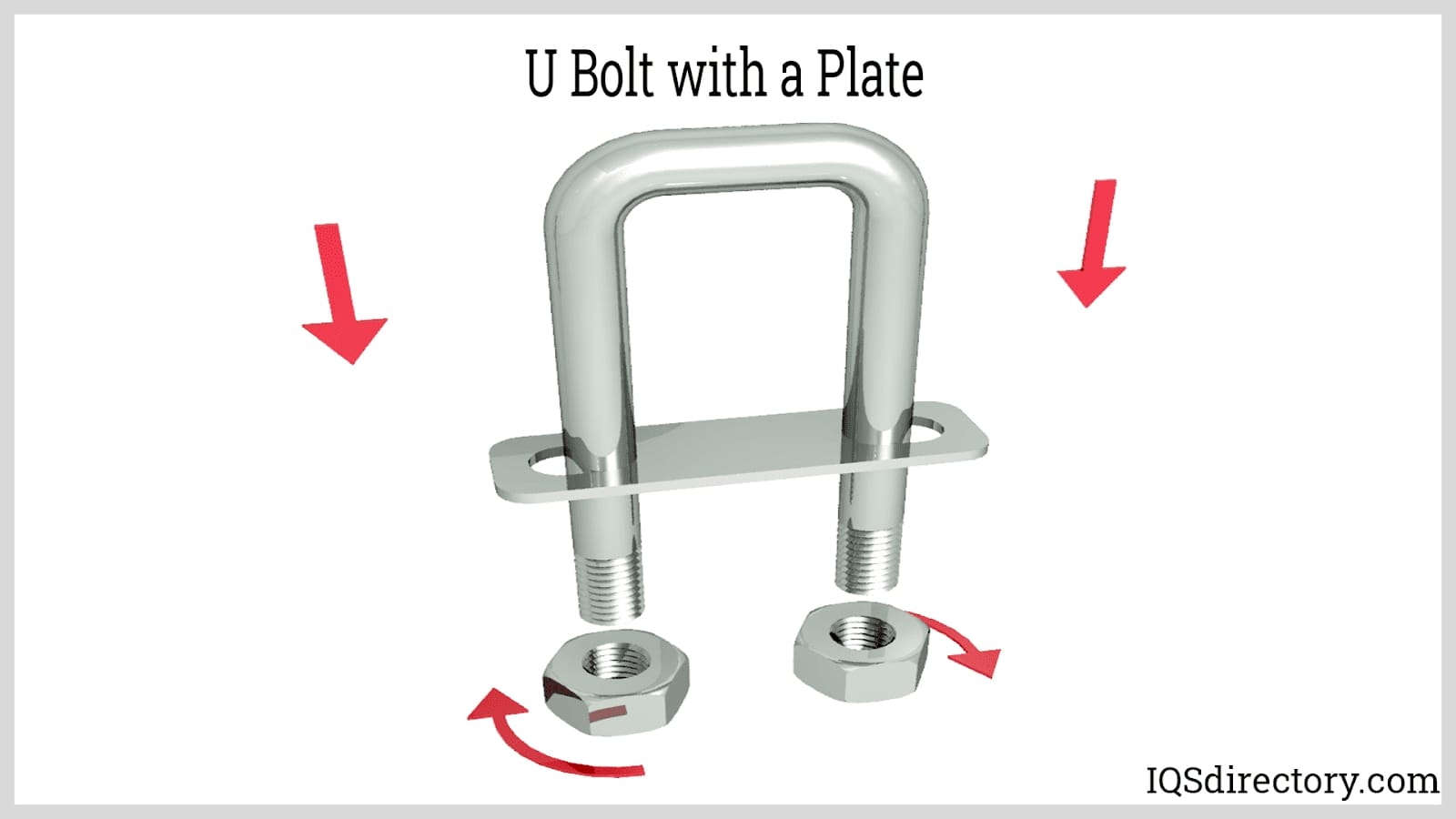
A fastener is a non-permanent or permanent mechanical tool that rigidly connects or affixes two surfaces or objects together. Non-permanent fasteners can easily be removed without damaging the joined materials...
Please fill out the following form to submit a Request for Quote to any of the following companies listed on
This article will take an in-depth look at cold heading and cold forming.
The article will bring more detail on topics such as:
In this chapter, we delve into defining cold forming, the types of materials utilized, and the different tooling methods employed in this production technique.
Cold heading, also known as cold forming, is a manufacturing technique where metal wire is shaped into specific forms without heating. This method uses high-speed hammers, dies, and punches to continuously form the metal.
The cold forming process begins by cutting a slug from a wire or coil, which is then crafted by a cold heading machine using a series of intense hammers and dies. This procedure involves exerting force from a punch onto the end of a metal blank within a die, requiring the force to exceed the metal’s yield strength to trigger plastic flow.
Viewed as a forging process absent of heat, cold heading encompasses operations like blank rolling, piercing, pointing, thread rolling, sizing, and trimming. It is pivotal for crafting metal threaded fittings and fasteners industry-wide.
As a swift forging technique, cold heading slices a wire to precise lengths at ambient temperature and under specific pressure. The cut wire then passes through consecutive die and tooling stages, transforming into a designated product, allowing shifts in feedstock diameters and lengths with operations such as piercing and trimming performing minute material adjustments in an efficient, non-stop procedure.
Originally designed for simple fastener creation, cold heading has evolved into a high-speed, automated, and multi-station method that allows for cost-effective production of composite fasteners and components. Modern cold heading accommodates tougher metals like high-temperature alloys and stainless steels.
Cold headers implement unique methodologies for slicing and gauging wire coil segments. The feeding and cutting techniques vary by machine manufacturer and utilize a cut-off knife to sever the wire from a specific angle. This process requires several components in addition to the cut-off knife.
Dies, larger than punches, sustain significant loads and are positioned on the stationary half of the cold header, typically composed of multiple pieces. The working die tool comprises three to four segments forming the whole working unit. These segments endure elevated pressure within a curved container, known as the casing, preserving the die’s lifespan over multiple cycles.
The die faces immense radial pressure per blow. Proper support averts premature failure, with the die forced tightly into the larger casing, which absorbs and spreads the pressure, ensuring die longevity through reuse before replacement.
Each die has a centered hole for part alignment. To counteract high-pressure part ejection, a knock-out pin array at the die’s rear holds the part early in the stroke, releasing it post-forming stroke. This precision system secures part removal after complete shaping.
Punches, attached to the movable section of the cold heading machine, handle less pressure than dies and are encased in punch casings despite their smaller size, managing significant loads.
Punches mold or form the screw heads, with typically one for initial and another for final impact. They also support pins pushing parts into the die, aiding trapped extrusions or recess pin accommodation, facilitating recessed part backward extrusion.
The transfer system is pivotal in cold forming, particularly in multi-die headers requiring multiple transfers. Components, like custom-designed fingers, secure parts in transit between dies, crucial for large or complex parts to avoid production defects such as head upset or shoulder droop.
Operators must precisely time the transfer to ensure secure part handling before it exits the die completely, refining this process through developed expertise.
Cold heading machines turn a metal blank into precise shapes via a reciprocating ram driving a hammer into a preformed die, often called stamping machines in manufacturing. Unaltered raw materials are then shaped as per design needs.
These machines feature bevel gears on one crankshaft end, paired with a cam gear, featuring a scissors slider on the roller shaft. The utility model fixes prior deficiencies, ensuring minimal cutting mechanism impact forces, quieter operation, and better productivity and quality.
Employing automated high-speed equipment like cold headers or part formers, the cold heading process converts simple wire into intricate components with accuracy, capable of producing up to 400 parts per minute with minimal waste.
Cold heading maintains the material’s volume, rearranging metal to form precisely designed components, ensuring efficient resource use and minimized scrap.
Recent innovations in cold forming machinery have amplified capabilities considerably. New machines with multiple dies streamline short and long part production, allowing for singular adjustments and quick setup via CNC controls. These enhancements optimize production efficiency while minimizing downtime courtesy of multi-station headers.
Contemporary cold forming merges diverse techniques for superior efficiency, and advancements in metallurgy permit forming stronger materials. Alloy producers rigorously refine compositions to meet demands for robust, corrosion-resistant parts, with controlled manufacturing of specific AISI grades for enhanced cold formability and further processing ease. Durable tool steels significantly extend die life, while versatile alloys prove valuable for machining and heading alike.
Cold heading equipment generally falls into two primary categories:
Both types of cold heading equipment utilize horizontal reciprocating rams and stationary bolsters. Cold heading machines can range from single-die setups to those with up to seven dies in sequence, accommodating various cut-off sizes. The capability of a manufacturer in cold heading largely depends on the number and types of machines they have in operation.
The cold heading tooling process primarily involves two key components: dies and punches. Punches apply the necessary force from the machine to the material, ensuring precise dimensional control of the part features. Meanwhile, dies guide and shape the material into the desired form and dimensions.
The term "cold heading" originates from the upsetting process used in the technique.
Cold heading is the technique employed to form a head on a bolt or screw. Upsetting refers to the process of consolidating material into a specific area of the component, like a collar or head. In essence, this process enlarges the diameter in the areas being worked. In cold heading terminology, manufacturers often refer to this as "the maximum number of diameters that can be upset."
Although it looks and sounds much more complex, upsetting is a simpler way of forming. It is a simple cylinder that is cut or removed from the lengthy continuous wire coil that is put inside the machine. For the parts that will become bolts and screws, or the externally threaded ones, the cylinder is much longer than its diameter. It is possible to break the cylinder down into different sections where each section is the same diameter and height. Each division is called a diameter. Some parts are very long and skinny, such as screws and bolts, with each beginning piece of wire consisting of multiple diameter sections.
Engineers have discovered that only a limited amount of material can be manipulated or compressed in one go before it risks bursting or cracking. In cold heading processes, this limit is generally about two percent of the diameter per strike. Given that many bolt heads or screws contain more than two diameters' worth of material, multiple strikes are necessary to achieve the desired result.
There is a constraint on how much material can be upset in a single blow under controlled conditions. For forming complex parts where more metal needs to be moved, the process is often conducted in two stages or blows. This explains the prevalence of single-die and double-stroke headers. Upsets are typically calculated based on wire diameters, dividing the total length of the metal blank by the wire diameter.
For instance, a 5-inch metal blank made from 1/2-inch wire corresponds to ten diameters in length. On a solid die header, the maximum dimension of wire that can be upset in a single blow is approximately 2 1/4 diameters. Thus, around 1 inch of the 5-inch metal blank can be used to form the required fastener head. Generally, single blow heading falls within the range of 1 to 1 1/4 diameters.
In a two-blow heading process, up to 4 1/2 diameters can be upset. During the initial contact between the metal blank and the punch, any part of the blank extending unsupported out of the die may bend if struck, leading to a cold shut defect. Attempting to upset a length of 3 inches, equivalent to six diameters, may be unmanageable.
However, there are exceptions to this rule. Advanced headers with sliding punches can accommodate up to 6 1/2 inches in diameter for two-blow upsets. In multi-station headers, the total diameters that can be upset are only limited by the number of available dies. Properly matching the wire diameter to the machine’s capabilities is crucial, as incorrect calculations can lead to mismatches and ineffective forming.
In the context of cold heading, "extrusion" refers to several distinct processes. There are primarily three types of extrusion: forward extrusion (which includes trapped and open extrusion), and reverse extrusion. In forward extrusion, the material is pushed forward through the die, either moving out in front of the tool (trapped extrusion) or extending outward in an open manner. Reverse extrusion, on the other hand, involves the material being forced backward, against the tool’s direction.
For instance, in forward extrusion, a metal blank is pushed into a die with a significantly smaller diameter than the blank itself, leading to an increase in length and a reduction in diameter. Conversely, in backward extrusion, the metal blank is subjected to high pressure from a punch at an angle. With no other path available, the material is forced along the edge of the punch and moves backward.
Forward extrusion is typically employed for producing items such as screws, stepped shafts, or bolts, while backward extrusion is commonly used for creating various cylindrical shapes like sleeves, nuts, and rivets. Similar to upsetting, extrusion alters the shape of the metal blank without wasting material. The extrusion process can be classified as either open or contained.
In open extrusion, the blank is driven into a die, whereas in trapped extrusion, the blank is entirely enclosed within the die. The effectiveness of controlled upsetting processes is influenced by the wire diameters, while extrusion processes depend on the reduction of the blank's area, often expressed as a percentage and determined by the extrusion angle.
A general guideline for open extrusion is that the area reduction in a single blow should not exceed 30 percent. It’s important to remember that the diameter measurements before and after extrusion are not used for calculating the area reduction directly.
In open extrusion, the part isn't confined by tools, allowing the extruding section of the tool to be positioned near the top of the die. This setup maximizes the length of material that can be extruded from the part.
However, open extrusion has its drawbacks. It requires substantial pressure to force the material through the extruding tool. Without adequate support from the tools, excessive pressure can lead to buckling, which can cause the process to fail.
Trapped extrusions, in contrast to open extrusions, involve completely enclosing the part within the tool before it is pushed through the extruding section. This method allows for a significant reduction in diameter, up to about seventy-five percent, due to the increased pressure that can be applied.
However, a limitation of trapped extrusion is that it requires a substantial portion of the tool to be occupied to create sufficient space for the extrusion. As a result, the length of the extruded part tends to be shorter and more restricted compared to open extrusion. Trapped extrusion, also known as contained extrusion, is crucial for producing complex parts in headers.
The radial extrusion die is often preferred for contained extrusion of the cold headed parts. This is because this form of die decreases die pressure and improves the pattern of flow of the wire as it is driven through the die. With almost all contained extrusion dies, the best results are obtained by making wire that has a larger diameter than the shank that is finished.
The wire gauge is chosen with precision to ensure that the resulting head dimensions are approximately twice the diameter of the original wire. The wire is then extruded to match the diameter of the shank and upset to achieve the specified head dimensions using standard techniques.
Reverse extrusion is primarily used to create hollow components like bushings and nuts. In this process, a pin is pushed into the material inside the die. There is considerable clearance between the pin's outer diameter and the die walls, allowing the material to flow backward along the pin. This results in the formation of an outer shape and the beginning of an internal channel or hole.
Reverse extrusion is also employed to create internal drive recesses in various screw heads. The final stages in cold heading include trimming and piercing, though not all parts undergo these processes. In fact, many externally threaded screws do not require trimming.
Both trimming and piercing involve shearing techniques where tools apply force, design, and speed to remove material from the targeted area. Trimming is generally reserved for finishing touches on collars or head shapes, such as creating a hex head. For internally threaded components, the reverse extrusion process is typically used on all sides, resulting in a blank with holes that do not extend fully through the part, separated by a thin web of material.
The piercing process follows, where a pin is driven into the hole, completely shearing the web to create a continuous hole through the part. In both cases, whether trimming an external part or piercing an internal part, the resulting scrap is minimal. This offal represents only a tiny fraction of the total material used in cold heading.
This chapter will discuss the applications and benefits of cold heading forming.
The cold heading process manufactures fasteners with high efficiency and good quality, saving costs and materials. However, this process requires high quality raw materials.
Cold heading utilizes a specific grade of steel known as cold heading steel, ideal for producing fasteners and joints. Additionally, this process can be applied to tempered alloy steels, structural steels, and ferritic-martensitic duplex steels.
Cold forming offers several key benefits, including:
Cold forming is known for its rapid production capabilities, with some manufacturers achieving output rates of up to 100 parts per minute. This high-speed process ensures uniform quality and accuracy in the finished parts.
Cold forming enhances the strength of the part by maintaining the material's inherent properties. Since the material is shaped without cutting or heating, its original grain structure aligns with the part’s contours, resulting in increased durability and strength.
Unlike hot forging, the cold forming process does not require extra energy to heat the material, making it more energy-efficient.
There are several limitations associated with cold heading, including:
As the diameter of a fastener increases, the pressure needed to shape the material also rises. While large machines are capable of producing fasteners of any size, they are often not practical for such tasks. For extremely large fasteners, machining is typically the more suitable method.
Not all materials are equally suited for cold forming. While various metals can be used, selecting the most appropriate types will yield superior results and enhance the quality of the final products.
Over the years, the process of cold heading has greatly helped with improving technology and producing higher-quality machining results. Thus, when selecting cold forming for a particular process, it is vital to understand its applications, benefits, and how each cold heading approach functions.
A fastener is a non-permanent or permanent mechanical tool that rigidly connects or affixes two surfaces or objects together. Non-permanent fasteners can easily be removed without damaging the joined materials...
Powder metallurgy is a manufacturing process that produces precision and highly accurate parts by pressing powdered metals and alloys into a rigid die under extreme pressure. With the development and implementation of technological advances...
Screw machined parts are complex pieces that are typically cylindrical and threaded and a screw machined product is a family of automatic lathes for small to medium-sized components...
A self-drilling screw is a type of tool that has the same design features as a drill bit or cutting tool. As the name implies, self-drilling screws do not require a pilot hole in order to perform as a fastener...
Swiss screw machining is a process for producing high precision parts in high volume using an automatic lathe that is programmed to perform every aspect of the cutting process. The method used for...
Thread rolling is a type of threading process which involves deforming a metal stock by rolling it through dies. This process forms external threads along the surface of the metal stock...
Bolts are tools used to fasten and secure the faces of assemblies using a nut. They are threaded and come with a matching nut. Their purpose is to connect aligned unthreaded holes by being placed through...