Brass
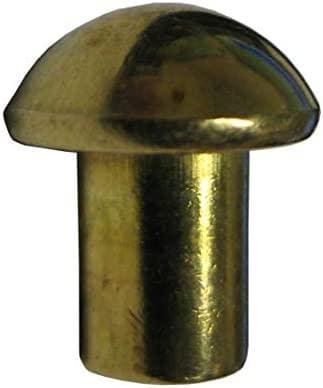
A variety of copper-zinc alloys are referred to together as brass. Different ratios of brass and zinc can be used to create alloys, which produce materials with various mechanical, corrosion, and thermal properties...
Please fill out the following form to submit a Request for Quote to any of the following companies listed on Beryllium Copper .
This article presents all the information you need to know about Beryllium Copper. Read further and learn more about:
Beryllium copper (BeCu) is an alloy, heat-treated to provide outstanding strength alongside its non-magnetic and non-sparking qualities. It's crafted by alloying copper with 0.5% to 3% beryllium, creating a material markedly stronger than other copper-based alloys. The beryllium content determines its specific grade, influencing both its strength and electrical conductivity. This differentiation highlights the unique advantages and characteristics of the various grades of beryllium copper.
While beryllium copper is a more modern advancement in metallurgy, it stands in stark contrast to ancient alloys like brass and bronze, recognized for centuries. Beryllium itself was isolated in 1828 using a reaction between beryllium chloride and potassium. The first beryllium copper applications, notably conductive springs, emerged in 1920 for telephone switchboard relays. By the 1970s, the alloy found significant usage in automotive and telecommunications industries.
Nowadays, beryllium copper is extensively applied in diverse fields including energy (tools aiding oil and gas extraction, and coal mining), power production, and electronics (connectors), as well as cryogenics and the automotive sector (components like valve seats, guides, and systems preventing brake locking). Its uniform tonal quality and resonance make it suitable for musical instruments such as triangles, trumpets, bells, and tambourines. Moreover, due to its robustness and resistance to marine environments, thanks to its anti-fouling properties, it is used in harsh conditions. Beryllium copper is also employed in MRI machines to circumvent issues related to magnetic ferrous components.
An alloy consists of a metal combined with other metals or non-metal elements to enhance its properties for specific industrial and manufacturing applications. Among the most widely used copper-based alloys are beryllium copper, brass, and bronze, each offering a unique set of physical and mechanical characteristics suited to different types of engineering, electrical, and decorative uses. Copper acts as the primary component or "solvent" in these alloys, imparting intrinsic benefits such as superior corrosion resistance, minimized biofouling, and exceptional thermal and electrical conductivity—characteristics that make these alloys valuable for electrical components, marine fittings, and high-performance parts across diverse industries.
Brass: Brass is an alloy primarily composed of copper and zinc. It is renowned for its good mechanical strength, impressive ductility, and excellent workability, all attributed to the proportion of zinc alloyed with copper. Brass exhibits greater malleability than bronze, allowing it to be easily shaped into complex forms without fracturing. This versatility has made brass a material of choice since prehistoric times, first identified around 1,400 B.C.E., and often referred to as "yellow copper" due to its distinct coloration ranging from dull yellow to reddish hues, depending on zinc content.
Common uses for brass include the fabrication of musical instruments (such as trumpets and trombones), high-quality plumbing fixtures, cartridge cases for ammunition, electrical terminals, and ornamental hardware. Its corrosion resistance makes it suitable for marine applications, while lighter brasses are popular in jewelry and decorative accents as affordable gold alternatives. Because brass is non-magnetic and possesses good acoustic properties, it remains a go-to material in both art and industrial manufacturing.
Bronze Bronze is a robust alloy formed by combining copper with tin—the principal additive—alongside elements like phosphorus, manganese, and sometimes nickel or aluminum for specialized grades. Discovered earlier than brass (dating back to 3,500 B.C.E.), bronze has played a significant role in tools, armor, coinage, and sculpture throughout history. Physically, bronze tends to be harder and more brittle than brass, with a higher melting point and a signature reddish-gold color that distinguishes it visually from other copper alloys.
Due to its superior strength, low friction properties, and high wear resistance, bronze is favored for components exposed to recurrent motion and stress, such as bearings, bushings, gears, and springs. It is also commonly used for architectural hardware, electrical connectors, marine fittings, and premium sculptures. Phosphor bronze and aluminum bronze variants offer enhanced corrosion resistance, making them highly suitable for applications in seawater environments and demanding industrial conditions. The durable and aesthetic nature of bronze supports its ongoing popularity for both functional and artistic uses.
Beryllium Copper: Beryllium copper, often referred to as beryllium bronze, is a high-performance copper alloy composed of copper and about 0.5–3% beryllium, with occasional additions of cobalt or nickel for enhanced properties. Beryllium, found in over 30 different mineral species, imparts exceptional strength and hardness to copper, creating an alloy with tensile strength and electrical conductivity that outperforms most other copper alloys. The resulting material has a steel-gray appearance, combining a low density with remarkable durability and fatigue resistance—even at elevated temperatures.
Beryllium copper is uniquely valued for its non-sparking, non-magnetic qualities, making it a critical choice for use in hazardous environments (such as oil and gas, aerospace, and defense industries). It is frequently used to manufacture precision springs, electrical connectors, electronic switches, mold tooling, and components for instrumentation where both electrical and mechanical performance are required. Its excellent corrosion resistance and machinability also make it a top choice for high-reliability applications that demand longevity and consistent performance under stress. Further chapters will explore in-depth the distinctive characteristics, advantages, and industry-specific use cases for beryllium copper alloys.
Comparative Overview of Beryllium Copper, Brass, and Bronze: When considering which copper alloy best suits your needs, it is important to analyze application-specific requirements such as mechanical strength, electrical or thermal conductivity, machinability, corrosion resistance, and cost. For instance, brass is often selected for its workability and decorative appeal, bronze for its wear resistance in frictional applications, and beryllium copper for environments demanding a combination of high strength, electrical reliability, and safety where non-sparking tools or components are essential.
Understanding these distinctions helps engineers, purchasing managers, and manufacturers choose the optimal alloy for custom parts, electrical systems, marine hardware, and more. For further guidance on sourcing high-quality copper alloys, consider exploring brass suppliers and bronze suppliers to compare product specifications, certifications, and lead times for your industry application. Selecting the right material pays dividends in performance, safety, and long-term value.
Beryllium copper, also known as BeCu or beryllium bronze, is a unique copper-based alloy that offers a valuable combination of high strength, electrical conductivity, and corrosion resistance. Beryllium copper can be manufactured in various forms such as plates, rods, strips, and wires, using either wrought or cast production methods. Wrought beryllium copper alloys are typically shaped through hot or cold working techniques to achieve precise mechanical properties. In contrast, cast beryllium copper is created by pouring or injecting molten metal into molds. Following the forming process, the material often undergoes age hardening (precipitation hardening) to achieve desired levels of strength, hardness, and machinability.
Beryllium copper alloys are categorized into two main types based on their chemical composition and the physical properties they deliver. These properties are influenced primarily by beryllium content, the addition of other alloying elements (such as cobalt and nickel), and the specific heat treatment processes used during production. Understanding these distinctions helps engineers, designers, and purchasers select the ideal beryllium copper grade for demanding industrial applications requiring non-sparking, non-magnetic, high performance specialty metals.
High-strength beryllium copper alloys, containing between 1.6% and 2.05% beryllium, are engineered for mechanical strength, durability, and resistance to fatigue and deformation. Their exceptional strength arises from the age hardening or precipitation hardening process, a metallurgical technique in which beryllium atoms precipitate from a supersaturated solid solution of copper as the alloy is heat treated and cooled.
During this heat treatment, the solubility of beryllium in copper declines—especially between 392°F and 860°F (200°C to 460°C)—causing beryllide particles to form. These nanostructures create coherency strains at the matrix-precipitate interface, resulting in significant increases in tensile strength and hardness. Age-hardened beryllium copper also exhibits high resistance to stress relaxation, which is critical for components subjected to repeated loading, such as industrial springs, electrical connectors, and non-sparking hand tools. Additional characteristics include exceptional corrosion resistance, machinability, and the ability to be formed into complex shapes.
Notable high-strength beryllium copper alloys include:
C17200, recognized as Alloy 25, stands as the most widely used high-strength beryllium copper alloy. Featuring 2% beryllium content, it achieves tensile strengths exceeding 200 ksi and a Rockwell hardness rating of C45, rivaling hardened steel. With a minimum electrical conductivity of 22% IACS, Alloy 25 delivers a rare blend of electrical and mechanical performance. Its high fatigue strength, stress relaxation resistance at elevated temperatures, and excellent dimensional stability make it ideal for critical oil & gas, aerospace, and defense sector components.
In plastic injection molding, C17200 is the premier choice for mold inserts and cores thanks to its remarkable thermal conductivity—up to four times higher than standard mold steel. This property facilitates faster, more uniform cooling of molded parts, reducing cycle times, minimizing warpage, and improving product quality. The alloy's non-magnetic, non-sparking nature also supports use in potentially explosive or corrosive industrial environments.
C17300, known as Alloy M25 or "leaded beryllium copper," incorporates 0.2% to 0.6% lead for enhanced machinability. The lead addition decreases tool wear and chipping during high-speed cutting operations, earning C17300 a reputation as a top choice for machining complex precision parts in the electronics, automotive, semiconductor, and aerospace industries. Besides its ease of fabrication, Alloy M25 offers superior fatigue and wear resistance, as well as high-strength performance metrics similar to Alloy 25.
With high thermal conductivity, corrosion resistance, polishability, and the ability to be forged or welded (excluding Oxy-Acetylene), C17300 is often used in the production of springs, fuse fasteners, connectors, spot welding electrodes, seam welding rollers, die casting heads, and injection mold tooling. These features make C17300 indispensable for manufacturers seeking reliable, high-performance copper alloy solutions for advanced applications.
C17000, or Alloy 165, features a lower beryllium content compared to C17200, resulting in slightly reduced strength but improved cost efficiency. This high-strength, age-hardenable copper alloy maintains robust mechanical properties even at cryogenic temperatures, combining hardness, ductility, and thermal stability. C17000 is favored in the production of industrial tools, fasteners, bearings, bushings, resistance welding components, and applications demanding a balance between strength and conductivity.
Offering enhanced machinability, mill-hardening capability, and resistance to galling in threaded connections (to itself or stainless steel), C17000 can be soldered, brazed, arc welded, spot welded, and butt welded, but is not recommended for Oxy-Acetylene welding. Its balanced electrical conductivity and high fatigue strength support use in electronic connectors, relays, and moving mechanical assemblies, addressing user intent for a reliable, versatile beryllium copper alloy option.
High-conductivity beryllium copper alloys contain lower concentrations of beryllium (typically 0.2%–0.7%) with additions of cobalt and nickel to further enhance electrical and thermal conductivity. These copper alloys are engineered for applications where efficient energy transfer, excellent formability, and moderate mechanical strength are key. While increased beryllium generally enhances alloy strength at the expense of electrical conductivity (a trade-off observed in other copper alloys like brass and bronze), these grades deliver an optimal balance for high-performance electrical and electronic components.
Common high-conductivity beryllium copper alloys include:
C17510, or Alloy 3, incorporates 0.2%–0.6% beryllium and 1.4%–2.2% nickel, resulting in high thermal and electrical conductivity while maintaining moderate strength and resistance to thermal fatigue. Alloy 3 is commonly specified for use in power and signal cables in offshore oil and gas operations, as well as switchgear, relay contacts, and battery connectors where reliable current transmission and durability under repeated stress are required.
With a tensile strength of 140 ksi, Rockwell hardness of B100, and electrical conductivity ranging from 45%–60% IACS (International Annealed Copper Standard), C17510 exhibits strong performance in spot and seam welding electrodes for joining high-resistance materials. Its form factors include wire, strip, and bar—making it an essential high-conductivity beryllium copper alloy for mission-critical, high-reliability electrical and mechanical assemblies.
C17500, known as Alloy 10, includes 0.4%–0.7% beryllium and a higher cobalt content of 2.4%–2.7%. This alloy offers mechanical and physical properties similar to C17510, but with enhanced hot and cold workability, making it especially effective for casting and molding tooling. Although slightly lower in thermal conductivity than Alloy 3, C17500 is preferred in specialized applications where performance at elevated temperatures and resilience under heavy-duty mechanical stresses are essential.
C17500's capabilities—tensile strength up to 140 ksi, Rockwell hardness B100, and 45%–60% IACS conductivity—satisfy rigorous demands for welding electrodes, industrial contacts, and heavy-duty switchgear. All C175-series beryllium copper alloys contain cobalt, while Alloy 3 includes nickel, giving engineers design flexibility for electrical and mechanical performance requirements.
Alloy 10X is a proprietary beryllium copper alloy composed of copper, cobalt, beryllium, and zirconium, engineered specifically for robust high-temperature performance. It maintains excellent strength and ductility up to 806°F (430°C), combined with superior resistance to thermal cracking and fatigue. These attributes are ideal for demanding automotive powertrain applications, such as exhaust valve seats and pre-ignition chambers, where reliability in extreme temperature conditions is crucial.
Alloy 310, a blend of copper, beryllium, nickel, and cobalt, represents the best features of both C17500 and C17510. With outstanding electrical and thermal conductivity in combination with high strength and hardness, Alloy 310 is a frequent choice for welding electrodes, non-ferrous casting dies, nozzles, and plunger tips. Its superior resistance to thermal fatigue and excellent cost-performance ratio make it widely used in manufacturing industries where tool longevity and part integrity are top priorities.
The unique synergy of physical properties and affordability sets Alloy 310 apart for users seeking durable, high-conductivity, specialty copper alloys for metalworking and joining processes.
Beryllium copper is renowned for achieving the highest strength among copper alloys, while also retaining excellent thermal and electrical conductivity. These key features make it highly valued. High-strength beryllium copper alloys can have a tensile strength exceeding 200 ksi (approximately 1,400 MPa). This remarkable strength and hardness are achieved through a heat treatment process known as precipitation hardening, which involves precipitating beryllium from the alloy mixture.
Additional unique properties of beryllium copper that differentiate it from other metals include:
One of the most notable features of beryllium copper is its ability to prevent frictional sparking when struck against other metals. This makes it an ideal choice for tools used in environments prone to fire and explosion, such as oil rigs and coal mines. If a particle of beryllium copper becomes dislodged and hot, it cools quickly and is unlikely to ignite nearby flammable materials.
Galling refers to a form of mechanical wear on metal surfaces resulting from adhesion and friction, particularly when lubrication is absent. It typically occurs when two metals slide against each other under compressive forces, such as in threaded connections. Beryllium copper is resistant to such wear, exhibiting minimal friction and surface damage even under heavy loads and continuous vibration. Additionally, it offers excellent abrasion resistance.
As a non-ferrous metal, beryllium copper is inherently non-magnetic. This means that magnetic fields do not interfere with the performance of beryllium copper components. Unlike some other metal alloys, beryllium copper does not exhibit magnetic behavior or become magnetized during machining and forming processes.
Beryllium copper's tensile strength and toughness are maintained at temperature extremes, even at long exposure times. Beryllium copper can be used in cryogenic conditions, wherein steels become brittle at very low temperatures. The performance of beryllium copper at elevated temperatures is above average compared to other copper alloys. This and its inherent hardness are why beryllium copper is commonly used in molding tools and welding electrodes.
Beryllium copper is highly resistant to corrosion in harsh environments, does not easily tarnish, and is protected against biofouling. Unlike stainless steel, which can suffer from stress corrosion cracking due to high chloride conditions, beryllium copper remains unaffected by chlorine. This makes it an excellent choice for use in saline environments and in oil and gas industries.
Beryllium copper is suitable for handling various chemicals such as glycols, ketones, hydrocarbons, and esters on a regular basis. However, the presence of impurities like sulfides, acids, and salts in these substances can accelerate its corrosion. Additionally, fumes released during the curing of polyvinyl chloride and room temperature vulcanized silicone can also lead to corrosion of beryllium copper components.
Beryllium copper is relatively easy to machine. It is typically shaped and worked before undergoing the hardening process. Prior to hardening, beryllium copper has moderate hardness and high ductility, which facilitates its fabrication.
Additionally, beryllium copper is resistant to hydrogen embrittlement, a condition where hydrogen atoms become trapped in the metal's microstructure during processes like welding, hot forming, or electroplating. Parts affected by hydrogen embrittlement can become prone to cracking under stress. Beryllium copper’s resistance to this phenomenon helps maintain its integrity and performance in various applications.
The age precipitation process for beryllium copper enhances its strength and hardness significantly, leading to improved dimensional stability during stamping and cutting operations. This heat treatment effectively relieves internal stresses, ensuring that the metal piece maintains its shape and precision under various mechanical processes.
Heat treatment of beryllium copper involves a precise sequence of heating and cooling cycles, which imparts desirable mechanical properties to the material. This treatment significantly enhances the strength, durability, and machinability of beryllium copper. It is applicable to both wrought and cast beryllium copper alloys.
The physical states of beryllium copper at various temperatures and concentrations are depicted in the binary phase diagram below. This diagram is a valuable resource for understanding the heat treatment process. The thermal properties of beryllium copper, such as its melting and boiling points, are influenced by the beryllium content.
The heat treatment process for beryllium copper consists of two main stages: solution annealing and age precipitation.
Solution annealing is usually done at the supplier‘s side and prepares the beryllium copper piece for age hardening. At this stage, the beryllium precipitates are dissolved in the copper matrix to form a supersaturated beryllium copper solution, through the diffusion of beryllium atoms in the alpha phase. It also ensures a uniform concentration of beryllium on the alloy system and regulates its grain size. Depending on the alloy composition, the beryllium copper is heated slightly below the solidus temperature, which varies around 1450⁰F (790⁰C) for high strength alloys and 1652⁰F (900⁰C) for high conductivity alloys until a solid homogeneous mixture is present. At the solidus curve (curve BC) in the binary phase diagram, the solid and liquid phases of beryllium copper coexist. The solidus temperature decreases with increased beryllium concentration. The annealing temperature and time are controlled to prevent undesirable grain growth and melting.
After the annealing process, to preserve the supersaturated structure at room temperature, the beryllium copper is quickly cooled by quenching in water. This rapid cooling results in a soft and ductile metal that can be easily cold worked through processes such as forming, drawing, or rolling.
Age hardening, also known as precipitation hardening, involves heating the annealed beryllium copper to a temperature below the solvus point, followed by slow cooling. This process typically takes place in a furnace at temperatures ranging from 392-752°F (200-400°C) for an hour or more. In the binary phase diagram, below the solvus temperature, beryllium and copper form distinct solid phases. The solvus temperature increases with higher beryllium content. Age hardening is carried out after the beryllium copper has been formed and shaped.
The strengthening of beryllium copper is due to the precipitation of beryllium from the solution, which occurs during the slow cooling process. As the temperature decreases, the solubility of beryllium in the copper matrix reduces, leading to the formation of beryllide phases along the grain boundaries. This precipitation enhances the material’s hardness and strength.
The heating temperature and duration are crucial factors in age hardening, influencing the material's physical properties such as strength and conductivity. The specific age-hardening conditions can be tailored based on the intended application of the beryllium copper component. Typical age-hardening conditions include:
During the age hardening process, beryllium and copper oxides can develop on the surface of the metal. This oxidation is unavoidable, even in pure hydrogen atmospheres or under vacuum conditions, but it does not negatively impact the material's performance. However, for applications that involve plating or soldering, it is crucial to remove these surface oxides to ensure proper bonding and functionality.
Beryllium copper, like other metal alloys, can present health hazards. The ways it can enter the human body and its potential health effects include:
Beryllium is known to be a human carcinogen. Workers involved in beryllium copper production have a high risk of developing lung cancer.
To minimize health risks when handling beryllium copper and to protect workers from exposure to toxic dust and fumes, the following industry practices are recommended:
The exceptional properties of beryllium copper have led to its adoption in a diverse range of industrial and commercial applications. Ongoing research, testing, and experimentation have revealed many uses beyond its initial role as a highly durable conductive material. A significant advantage of beryllium copper is its elasticity, which provides it with twice the strength of other copper alloys.
Engineers and designers are continually discovering new and inventive applications for beryllium copper's unique characteristics. Its reliability, durability, and exceptional strength, combined with its consistent performance, make it an ideal choice for sustainable and dependable applications.
A variety of copper-zinc alloys are referred to together as brass. Different ratios of brass and zinc can be used to create alloys, which produce materials with various mechanical, corrosion, and thermal properties...
Copper is a ductile, malleable, and reddish-gold metal with the capacity to effectively conduct heat and electricity. Brass and bronze, two commonly used alloys, are created when copper is combined with...
The copper sheet is a highly malleable and workable metal with outstanding electrical and thermal conductivity and corrosion resistance. Copper (Cu) is a reddish, very ductile metal that belongs to Group 11 of the periodic table...
Aluminized steels are steels that have been hot-dip coated with pure aluminum or aluminum-silicon alloys. This hot-dip coating process is termed hot-dip aluminizing (HAD)...
Aluminum 1100 is the softest of the aluminum alloys, which makes it easy to shape and form into a wide range of products for industrial and home use. It can be cold and hot worked but is frequently shaped by...
The term "aluminum coil" describes aluminum that has been flattened into sheets where their width is significantly higher than their thickness and then "coiled" into a roll. Stacks of individual aluminum sheets are difficult to...
Aluminum piping and tubing is silvery-white, soft, and ductile. The metal belongs to the boron group. Aluminum is the third most abundant element present on earth. Aluminum has low density. When exposed...
Metals are a group of substances that are malleable, ductile, and have high heat and electrical conductivity. They can be grouped into five categories with nickel falling in the category known as transition metals...
Stainless steel grade 304 is an austenite stainless steel that is the most widely used and versatile of the various grades of stainless steel. It is a part of the T300 series stainless steels with...
Stainless steel is a type of steel alloy containing a minimum of 10.5% chromium. Chromium imparts corrosion resistance to the metal. Corrosion resistance is achieved by creating a thin film of metal...
Stainless steel grades each consist of carbon, iron, 10.5%-30% chromium, nickel, molybdenum, and other alloying elements. It is a popular metal used in various products, tools, equipment, and structures that serve in many industrial, commercial, and domestic applications...
Steel service centers are companies that specialize in procuring steel directly from mills and manufacturers and supplying them to the customers. They are fundamental to the steel supply chain...
Stainless steel can be fabricated using any of the traditional forming and shaping methods. Austenitic stainless steel can be rolled, spun, deep drawn, cold forged, hot forged, or stippled using force and stress...
Stainless steel tubing is a multifaceted product that is commonly utilized in structural applications. Stainless steel tubing diameters and variations vary greatly based on the application requirements and are...
Titanium metal, with the symbol Ti, is the ninth most abundant element in the earth‘s crust. It does not occur in large deposits, yet small amounts of titanium are found in almost every rock...
Tungsten is a rare naturally occurring chemical element on earth. It is known to be one of the toughest metals on the earth. It is usually a tin white or a steel gray metal. Tungsten is common for its high tensile...
Aluminum is the most abundant metal on the Earth’s crust, but it rarely exists as an elemental form. Aluminum and its alloys are valued because of their low density and high strength-to-weight ratio, durability, and corrosion resistance...