Beryllium Copper
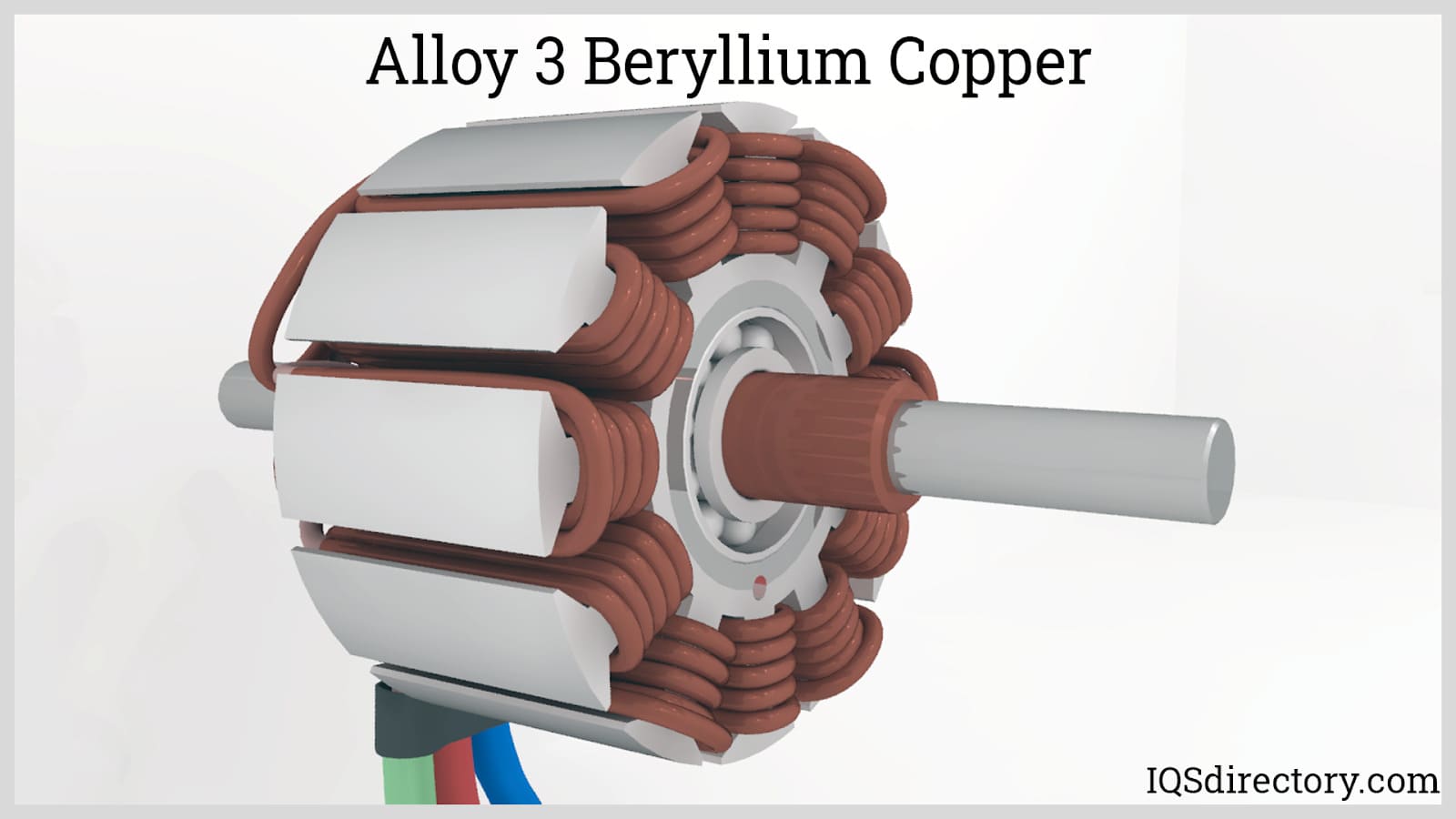
Beryllium Copper is a versatile copper alloy that is valued for its high strength and hardness, combined with good electrical and thermal conductivity. It is a non-ferrous, non-magnetic, and non-sparking metal alloy...
Please fill out the following form to submit a Request for Quote to any of the following companies listed on
This article will give detailed information about brass metal.
The article will give details on the following:
Brass is a term applied to a range of copper-zinc alloys renowned for their durability, strength, and resistance to corrosion. Altering the copper-to-zinc ratio in brass adjusts its mechanical, corrosion-resistant, and thermal characteristics for various purposes. Generally, brass includes between 60% and over 80% copper, while zinc constitutes less than 10% to above 40% of the mixture.
An alloy of brass with more than 30% zinc is labeled high brass. This type is less malleable, more brittle, and tougher to form. A higher zinc content can make brass more susceptible to corrosion, as zinc interacts with air and water, forming a zinc oxide layer.
Brass comprising more than 85% copper is termed red brass or gunmetal, noted for its exceptional malleability, ductility, resistance to corrosion, and ease of shaping. It is highly machinable, simplifying processes like cutting, forming, and drilling. However, the significant copper content also makes red brass more costly.
Lead is integrated into brass alloys with copper and zinc to act as a stabilizer, enhancing malleability and machinability. Yet, owing to health hazards related to lead exposure, the lead content within brass is tightly controlled. Typically, lead levels should remain below 2%, and in some regions, even stricter limits are enforced.
The Unified Numbering System (UNS) for Metals and Alloys designates a unique code to each metal type, comprising a letter and five digits. This identifier specifies its chemical composition, rather than mechanical attributes. The first three digits stem from existing number systems.
For brass alloys, the UNS code begins with "C" followed by five digits. Classifications include C20000 to C29999 for yellow brass, C30000 to C39999 for leaded brass, C40000 to C49999 for tin brass, and C87300 to C87900 for cast silicon brass. Red brass, with an 85% copper content, holds the designation C23000.
The zinc content in brass influences its malleability. If zinc levels exceed 45%, the alloy becomes challenging to work with. In brazing applications, a coarse type called white brass is utilized, important in die casting despite lacking economic significance.
Brass varieties with under 40% zinc are pliable and suitable for cold working. Alpha brass, less than 37% zinc, is named for its unique crystal structure, while alpha-beta brass or duplex brass contains zinc levels between 37% and 45%, having both alpha and beta structures.
Copper and zinc are principal components of brass, although other elements like lead are incorporated to bolster physical or mechanical properties and boost corrosion resistance. Naval brass, an alpha-beta type, contains 59% copper, 40% zinc, 1% tin, and traces of lead, with the tin enhancing resistance to marine corrosion.
Different brass types are identified by their crystal structures, either face-centered cubic (FCC) or body-centered cubic (BCC). Brass with high copper content bears an FCC structure similar to pure copper, while brass with higher zinc content adopts a BCC configuration.
Brass can have diverse colors like reddish-gold, silvery-white, or striking gold. More zinc in the alloy adds a silvery sheen, while greater copper content imparts a rose hue.
Compared to bronze and zinc, brass exhibits higher malleability.
Brass alloys are favored in metalworking for their toughness and corrosion resistance. The properties and characteristics of brass vary based on the copper-to-zinc ratio and the addition of other alloys. Elements such as tin, aluminum, iron, and lead enhance the deformability, machinability, and tensile strength of brass.
Alpha brass, while remaining a monophasic alloy, presents a distinct yellowish tint compared to red brass. Despite its susceptibility to degradation under certain environmental conditions and temperatures, its functionality remains unaffected. Alpha brass offers superior mechanical strength and ductility relative to other brass types, making it particularly well-suited for various forming applications.
Alpha brass, known as "cartridge brass," is used for ammunition cartridges, heat exchanger tubes, evaporators and automotive radiators, fire extinguishers, rivets, bolts, and screws. It is named for its homogeneous alpha crystal structure and its less than 37% zinc content.
Combining zinc with copper results in a solution that forms an alpha crystal structure with a uniform composition. Alpha brasses are noted for their softness, ductility, and malleability, which makes them ideal for cold working, welding, rolling, drawing, bending, and brazing. This type of brass is commonly known as 70/30 brass due to its composition of 70% copper and 30% zinc.
Alpha brass is known for its blend of durability and adaptability, making it suitable for cold drawing processes. Its higher zinc percentage enhances its resistance to corrosion. It is commonly utilized for manufacturing electrical socket springs and various fasteners such as wood screws. Alpha brass retains its shape well and is less susceptible to dezincification, a phenomenon where zinc gradually deteriorates over time.
Alpha-beta brasses, known as "duplex brasses" or "hot-working brasses", have an alpha-grain structure and a beta-grain structure with a zinc content between 37% and 45%. They are atomically comparable to pure zinc with the zinc content determining the alpha-phase to beta-phase brass ratio. Alloys, such as aluminum, silicon, or tin, can enhance the quality of beta-phase brass.
Alpha-beta brass, which is more common than alpha brass, offers greater toughness and strength but has reduced cold ductility. This type of brass is more cost-effective due to its higher zinc content but is also more susceptible to dezincification corrosion.
Although alpha-beta brasses are less malleable at room temperature compared to alpha brasses, they are much more workable at elevated temperatures. These brasses also exhibit resistance to cracking, even when lead is added to improve machinability. Typically, alpha-beta brass is processed through methods such as extrusion, stamping, or die casting.
An example of alpha-beta brass is Muntz metal, developed by George Frederick Muntz in 1830 as an alternative for wooden ship hulls. This alloy has a 60:40 ratio of copper to zinc and contains small amounts of lead, making it highly durable. While still used in shipbuilding, Muntz metal is now also utilized in the production of various fittings, pipes, and springs.
Beta brasses are known for their strength and toughness, making them ideal for casting applications. They are characterized by their bright appearance and less golden hue, attributed to their higher zinc and lower copper content. With a beta crystal structure, these brasses exhibit greater hardness and strength compared to alpha and alpha-beta brasses. Due to this structure, they can only be processed through hot working methods.
Beta brasses represent the third category of brass alloys and are the least commonly used. With a zinc content of 45%, they offer enhanced toughness and strength due to their beta crystal structure. Various forms of beta brass include machining brass, high tensile brass, naval brass, dezincification-resistant brass, cold working brass, and casting brass.
Incorporating lead into brass improves its machinability by serving as both a chip breaker and a lubricant. Since lead does not dissolve in brass, it remains as free particles along the grain boundaries. This addition not only enhances the strength of brass but also boosts its corrosion resistance. Lead content in brass can be as high as 3.5%, and the brass can be categorized as high, medium, or low leaded based on the amount of lead present.
There are two primary types of leaded brass: alpha (α) and alpha-beta (α+β). Alpha (α) leaded brass is typically cold-formed or hot-extruded due to its limited plasticity at elevated temperatures. In contrast, alpha-beta (α+β) leaded brass retains sufficient plasticity at high temperatures, making it suitable for forging processes.
Grades such as C34500 and C35300 represent high leaded brass, while C38000 is classified as low leaded brass. High leaded brass is commonly used for manufacturing pinions, gears, valve stems, flare fittings, and adapters. Low leaded architectural brass, on the other hand, is employed in the production of thresholds and frames for doors and windows.
Lead brass is available in forms such as pipes, bars, and tubes, and can be customized to meet specific application requirements. However, due to its lead content, it is considered hazardous and must be handled with caution.
As regulations on lead use in products tighten, brass manufacturers have turned to alternative alloys to replicate the properties previously achieved with lead. New alloys, such as those containing silicon and bismuth, offer similar machinability and excellent pressure tightness as leaded brass.
Even with the shift to lead-free brass, trace amounts of lead, up to 0.25%, are still allowed. This amount represents a significant reduction, being 32 times less than the levels used in the past.
Grade C87600 is an example of lead-free silicon brass that maintains excellent machinability and pressure tightness while resembling leaded brass in appearance. Lead-free brass valves and connectors are marked with an “LF” designation on their bodies and a plastic tag. Current regulations prohibit the installation of leaded brass in homes unless it contains 0.25% or less lead.
Lead-free brass is primarily composed of zinc and copper, with the ratio adjusted to meet specific application requirements. High copper content is preferred for machining applications, whereas high zinc content is beneficial for strength. Additional elements such as aluminum and manganese may be incorporated to achieve desired properties.
Adding tin to brass enhances its heat resistance and makes it more resistant to corrosion from seawater, earning it the name "naval brass." Tin integrates well into copper-based alloys, reinforcing their structure.
As the tin content increases, the alloy can become brittle (CuZnSn complex) and less suitable for plastic deformation. The tin content in tin brass ranges from 0.5% to 1.5%, with common types including HSn70-1, HSn62-1, and HSn60-1.
HSn70-1 is known for its excellent plasticity, allowing it to be formed by both hot and cold pressing, making it suitable for pipe manufacturing. In contrast, HSn62-1 and HSn60-1 exhibit α and (α+β) two-phase structures with a minimal α phase, resulting in reduced plasticity at room temperature and requiring high temperatures for deformation.
Tin brass, or naval brass, is primarily used in marine applications such as boat and ship construction, with a typical composition of 59% copper, 40% zinc, 1% tin, and minor amounts of lead. Besides shipbuilding, it is also utilized in components exposed to moisture and humidity.
Architectural bronze is considered a type of brass due to its zinc content, distinguishing it from traditional bronze, which is primarily composed of tin and copper. This alloy typically contains 55% to 59% copper, 2.5% to 3.5% lead, and 0.35% iron, with small amounts of zinc. Its combination of affordability, durability, and corrosion resistance makes it well-suited for industrial uses.
Architectural bronze can be shaped using various techniques, including hot forming, bending, brazing, soldering, butt welding, and machining. The material is hot-formed at temperatures ranging from 1150°F to 1350°F (621°C to 732°C) and is annealed at temperatures between 800°F and 1100°F (426°C to 593°C).
Manganese brass is an alloy primarily consisting of copper and zinc, with a 3% manganese content. It is capable of withstanding substantial loads and high-speed applications. Known under UNS grade C86300, it is commonly called manganese bronze. The alloy's exceptional strength and durability make it well-suited for heavy load bearings, hydraulic cylinder components, and large valve stems.
The key features of manganese brass include its remarkable strength and resistance to corrosion. The addition of manganese, ranging from 1% to 4%, significantly enhances the properties of brass due to manganese’s high solubility in the alloy. Manganese brass typically exhibits both alpha and alpha-beta crystal structures and can be processed using either hot or cold working methods.
With a Rockwell hardness rating of B95, manganese brass is available in bar and rod forms. Both forms are highly resistant to wear and maintain their strength over time thanks to their superior fatigue resistance. It is particularly valued for applications requiring corrosion resistance, anti-seizing characteristics, and high strength.
Manganese brass is employed in various demanding applications, including those involving heavy loads and requiring high shaft hardness in non-abrasive environments. Its use is prevalent in the aerospace industry for components such as landing gear parts, bearings, bushings, gears, and screw nuts, where it provides robust performance in challenging conditions.
Iron brass features an alpha-beta crystal structure and contains less than 1.5% iron. This alloy has a silvery appearance and combines toughness and strength with good plasticity at elevated temperatures. Its composition typically includes 50% to 61% copper, 17% to 19% zinc, 21% to 30% nickel, and up to 1.5% iron.
During production, iron is introduced into a molten blend of copper, zinc, and nickel. Iron brass exhibits an alpha-beta (α+β) crystal structure and tends to become less ductile in colder environments.
Iron brass is represented by alloys such as Alloy 280 (Muntz Metal) and Alloy C360 (Free Machining Brass). Both alloys consist of 60% copper and 35% to 40% zinc. Muntz Metal, with its minimal iron content, is commonly used for ship hulls. Free Machining Brass, which contains lead along with iron, is known for its ease of machining.
The addition of iron enhances the hardness of these alloys. For Muntz Metal and Free Machining Brass, iron contributes to their increased hardness and forgiability, which is not achievable with pure copper or many of its alloys.
Nickel brass exhibits a gold-like color that varies with the nickel content and remains resistant to discoloration and tarnishing over time. The incorporation of nickel into brass raises its recrystallization temperature and results in a finer grain structure. Nickel significantly enhances the alloy's resistance to corrosion from both air and seawater.
Nickel brass is primarily made from copper and zinc, similar to other brass types. However, instead of the typical 60% copper and 40% zinc ratio, nickel brass usually consists of 60% copper, 20% zinc, and 20% nickel. The nickel content affects the color of the alloy, which is why nickel brass is also known as nickel silver or German silver due to its silvery appearance.
While nickel brass shares general corrosion resistance properties with other brass alloys, its higher nickel content imparts additional benefits such as superior tarnish resistance and enhanced protection against stress corrosion cracking.
Nickel brass is commonly used in the production of coins due to its difficulty to counterfeit and its distinctive electromagnetic signature, which is useful for coin validation systems. It is also widely used in the manufacture of musical instruments, valued for its durability and tonal qualities.
Single-phase brass is created when zinc is dissolved in copper at levels below 35% zinc. This type of brass is typically deformed through cold rolling and is known for its high ductility and flexibility, thanks to its low zinc content.
Double-phase brass, which contains both alpha (α) and beta (β) phases, has a zinc content ranging from 36% to 46%. The higher zinc content in the beta phase reduces plasticity but increases tensile strength. This type of brass is often processed using high-pressure techniques.
In double-phase brass, the alpha phase consists of a copper-zinc solution, whereas the beta phase has a higher zinc percentage. This combination imparts double-phase brass with notable corrosion resistance, strength, and excellent machinability. The tensile strength and overall performance of double-phase brass are significantly enhanced by increasing the zinc content.
Bolts, nuts, washers, springs, and structural components for electrical equipment use double-phase brass. Single-phase brass is cold form due to its flexibility while double-phase brass is hot formed because of its high zinc content.
Brass is well-suited for decorative uses due to its attractive appearance, while its strength, durability, and resistance to corrosion make it valuable for mechanical applications. Its low friction properties also make brass an excellent choice for manufacturing fasteners, connectors, tools, and ammunition components.
Brass's low friction coefficient makes it an ideal material for manufacturing gears, locomotive axle boxes, and marine engines. Its robust durability and strength contribute to the longevity of tools, reducing the need for frequent honing, repairs, or maintenance. Brass is preferred for applications subject to continuous use and stress because of its excellent wear resistance.
The automotive industry relies on brass components for the production of radiator cores, tubes, and tanks. Brass radiators are replacing aluminum radiators in trucks due to their low cost, easy processing, and reduced scrap. They are made of solder coated brass tubes and copper fins, which are joined by tin lead solder.
Brass is frequently used for connectors and fasteners due to its resistance to corrosion and water damage. Brass nuts are known for their durability, attractive appearance, and availability in various sizes. Brass washers, valued for their aesthetic appeal, are employed by the military, aviation industry, and gas companies.
Brass is commonly utilized in electrical components due to its good conductivity. It is used to connect electrical lines and manufacture a variety of parts, including panel board accessories, wiring components, switch gears, and light fittings. Brass is also used to attach lamps or lights to lampshades and is available in both raw and polished or plated finishes.
Brass is highly valued for its suitability in pipe and fitting applications due to its advantageous properties. It effectively combats corrosion from water, gas, and various fluids, making it a reliable choice for plumbing. Its resistance to corrosion, heat, and pressure ensures that brass is well-suited for demanding plumbing environments.
Plumbing often involves the challenge of fitting pipes into tight or awkward spaces, which requires bending and shaping. Brass's malleability allows it to be easily shaped to accommodate these tricky installations. Moreover, once bent and formed, brass maintains its strength and resilience, avoiding issues like cracking, breaking, or rupturing.
In the early 19th century, brass was initially employed to replace wooden ship hulls, which were prone to decay and worm infestations. Brass's resistance to corrosion, combined with its strength and durability, made it an ideal substitute for wood in these applications.
Although brass has been superseded by more advanced materials for ship hulls, it remains in use for various ship components due to its corrosion resistance. Today, shipbuilders use brass for valves, propellers, fittings, and pipes because of its ability to withstand stress and its long-lasting properties.
Brass, thanks to its copper content, is highly regarded for its superior conductivity, making it ideal for electrical components. Brass is a fundamental material in electrical installations, found in various connectors, circuit breakers, and terminal blocks.
Typical brass electrical components include:
Brass is commonly chosen for its visual appeal and decorative attributes. It can be enhanced with various finishes to increase its attractiveness. Beyond its aesthetic qualities, brass is valued for its strength, durability, and long-lasting nature, making it a practical choice for decorative applications as well.
Brass can be finished with a bright, polished look for a modern and fresh appearance. Alternatively, its long history of use allows it to develop an aged, antique-like patina, which is often desired for achieving a classic or vintage look in various applications.
Brass is favored for items like lamps and dishwasher fittings due to its attractive appearance and resistance to microbial growth. Its visual appeal enhances the quality of various decorative and functional objects, including candle holders, sculptures, trophies, and plaques. Additionally, brass is used in a diverse range of products such as lighting fixtures, doorknobs, furniture, bathroom fixtures, and cabinet hardware.
Brass is frequently used in architecture for its durability and resistance to corrosion. It is commonly applied in architectural fascias, trimmings, and hedges. Due to its long history of use, brass alloys are also employed in the renovation and restoration of historical buildings, helping to return them to their original appearance.
Architects often select brass for cladding due to its ability to withstand weathering and its elegant, lustrous finish. Over time, brass develops a patina that transitions from its original gold hue to a more subdued yellow or pink. Despite these color changes, brass retains its durability throughout its aging process.
Brass handrails are preferred for many projects because of their antibacterial properties, derived from their copper content. Given that handrails are frequently touched by many people, the antibacterial nature of brass helps to keep them sanitary and provides an additional layer of protection, which is increasingly important in today's health-conscious environment.
Brass is also widely used as a decorative element to accentuate various features of buildings or structures. With its range of available colors—such as gold, dull yellow, amber brown, chocolate brown, and black—brass offers architects the versatility to design unique and striking appearances, enabling creative freedom in architectural design.
Brass is a key component in both plumbing and electrical systems commonly found in homes. In electrical systems, various parts of sockets and switches incorporate brass alloys. Similarly, in plumbing, brass is widely used in components such as valves and various pipe fittings, including elbows, plugs, and couplings.
The material used to create a musical instrument greatly influences the quality of its sound. While silver, bronze, plastic, and platinum have been utilized for various instruments, brass has proven to be exceptionally durable for producing sustained vibrations. Brass cymbals are a prime example of this durability, thanks to the metal's ductility and malleability. Thin brass sheets or plates can be formed without cracking or breaking, making brass a preferred choice for many instruments.
Brass instruments have a unique advantage in that they can sustain sound quality even when dented or impacted. Unlike some other metals that may lose their tonal properties when damaged, brass instruments can be repaired effectively, preserving their sound quality and performance.
Cartridge brass is specifically used for manufacturing cartridge casings. It is initially produced in large coils, which are then cut into narrower strips for processing. These strips are fed into a cupping press to create thick-walled, wide-diameter cups. These cups are subsequently drawn through several stages before being pinch-trimmed and shaped to form the final shell casings.
Brass is chosen for cartridge production due to its compressive strength and high melting point, while remaining softer than the barrel's bore and rifling. Its high friction coefficient also provides lubrication, ensuring that it is durable yet smooth enough to avoid damaging the gun's rifling.
Brass bars are thick, elongated rectangular or square sections commonly employed in construction and engineering projects. Like other brass products, they are valued for their exceptional strength and resistance to corrosion.
Brass bars are primarily functional rather than decorative, though they can be polished and finished for improved appearance. Their ductility and malleability allow them to be cut, shaped, and formed for various applications. Brass bars can be brazed, drilled, butt-welded, and soldered to meet specific requirements.
In contrast, brass strips are thin, flat sheets known for their electrical conductivity and resistance to corrosion. Due to their flexibility, brass strips are used in the manufacture of electrical components, jewelry, and a variety of decorative items.
Brass angle trim features a bright, brushed polished finish and is available in a range of sizes with a mill finish. It is commonly used for edging on steps, wall corners, frameworks, and other areas that require both protection and precise, trimmed edges.
Brass is typically hot worked at temperatures ranging from 750°C to 830°C (1382°F to 1526°F). Annealing is performed at temperatures between 520°C and 650°C (968°F and 1202°F), with low-temperature annealing occurring between 260°C and 270°C (500°F and 518°F).
Brass is used to manufacture a variety of components, including heat exchangers, pipes, equipment, and electronic parts, thanks to its plasticity, high strength, excellent machinability, weldability, and resistance to corrosion.
Typical Specifications for Brass:
Brass angles, or "L" shaped bars, are created by rolling and bending brass bars. These angles provide excellent structural support and are valued for their strength. While brass angle bars are not typically used in heavy construction due to their cost, they are ideal for supporting shelving and cabinetry.
Smaller sizes of brass angles are employed for reinforcing and protecting edges and corners. Their durability, stability, and appealing appearance make them suitable for crafting items such as side tables, chairs, and bed frames.
Solid brass has been utilized for thousands of years across various applications, from swords and firearms to other weaponry. In contemporary times, it is commonly used in items such as door knockers, fireplace tools, cabinet hardware, light fixtures, and decorative statues and figurines.
Solid brass is often valued for its traditional appeal, owing to its long history. It is a popular choice for home decor that embraces antique aesthetics, with many items and accents highlighted by its distinctive qualities.
Brushed brass features a matte finish achieved by creating abrasions and scratches along its surface, which reduces its shine and imparts a subdued, textured appearance. Unlike the bright, golden luster of polished brass, brushed brass has a more muted and soft quality. This finish is often used for faucets, light fixtures, and cabinet pulls.
Brass sheets offer the same longevity, strength, and durability as solid brass and are employed in a variety of industrial applications. According to the American Society for Testing and Materials (ASTM), there are five primary types of brass used for manufacturing brass sheets.
The types of brass used for making brass sheets include:
Brass sheets combine lightweight, malleable, and robust properties, making them suitable for use in architectural features and interior design accents. Despite being easier to shape compared to solid brass or rods, brass sheets maintain the same essential qualities as solid brass. This makes them a popular choice for crafting musical instruments and decorative items.
Brass sheets are valued for their resistance to corrosion and high tensile strength, which makes them ideal for applications such as radiator cores, automotive grilles, heat exchangers, and electrical components.
For millennia, brass has been a key material in various projects and components due to its durability, long-lasting performance, and visual appeal. Its historical significance and reliability continue to make it a preferred choice in numerous applications.
Brass is a versatile metal that can be shaped into various forms to suit different applications. Its widespread use is attributed to its excellent electrical conductivity and malleability, allowing it to be utilized in numerous projects, including piping, tubing, and flanges. This adaptability, combined with its strength, makes brass a favored material for demanding and complex applications.
Brass wire offers enhanced resistance to corrosion and lower electrical conductivity, combined with remarkable ductility. It finds extensive use in applications such as scientific equipment and instrumentation, largely due to its impressive strength. Brass's durability allows it to endure harsh conditions where other metals might quickly deteriorate.
Despite brass's conductivity being only 28% that of copper, its specific properties make it suitable for certain applications where lower conductivity is beneficial. Brass wire comes in various forms, including riveting, free cutting, lead-free, flat, zipper, stitching, brazing, and forging types. Each variant is tailored for particular uses and is made from different brass grades. For instance, brass grade C37700 is preferred for forging wire due to its favorable hot working properties.
The diverse grades of brass wire enable it to be used across a broad spectrum of applications and conditions. Grade C36000 is a free-cutting wire ideal for high-speed machining. Grades C26000 to C28000 are chosen for zipper and stitching wire due to their finish and color. Brass wire grade C38100 is used in brazing applications due to its low fuming, which makes it suitable for welding.
Brass sheets are utilized in various applications depending on their thickness and composition. Historically, they have been employed for decorative purposes, such as panels, window frames, and cladding, thanks to brass's attractive gold-like appearance.
Brass's low electrical conductivity makes it an effective shield against electromagnetic interference (EMI). As a result, brass sheets are used to shield medical devices, electrical contacts, connectors, relays, and RF connectors. The choice of brass sheets for shielding applications is due to their wear resistance, high-temperature tolerance, and ease of machining and forming.
Brass foil is utilized in the production of various types of brass products, including those for books, albums, and leather goods. It conducts heat evenly and quickly, which helps in creating crisp images at lower temperatures. Brass foil's hardness ensures long-term durability without deformation. Although it is the most costly among hot stamping types, its extended lifespan justifies the expense.
A very common use for brass is as fasteners and connectors. Part of the reason for their use is their positive appearance, which can enhance a piece of furniture, cabinet, or installation. Although this is a beneficial aspect of brass fasteners, their greater value comes from their strength, durability, and resilience in the face of difficult and harsh conditions. This characteristic of brass fasteners is the reason for their use in mariner applications and the auto industry.
Brass fasteners are valued for their excellent performance, machinability, and formability, coupled with their low friction properties. They are widely used across industrial, commercial, and residential applications. Brass fasteners come in various types, including bolts, screws, nuts, washers, and spacers. These fasteners are produced from a range of high-quality brass grades, such as UNS C22000, C26000, C27000, C27400, C36000, and C69400, each offering specific advantages for different applications.
Brass is commonly used for piping due to its resistance to corrosion and rust. In plumbing, brass is particularly valued for its strength and ability to withstand variations in pressure, making it ideal for producing fittings used in applications involving chemicals and gases.
Brass pipe fittings come in various forms, including couplings, adaptors, nipples, tees, gate valves, and end plugs. While brass pipes and fittings are more expensive than alternatives like PVC, cast iron, and steel, their longevity and durability offset the higher initial cost, as they typically do not need to be replaced.
A notable application of brass piping is in brass gate valves, or sluice valves, which control the flow of non-shock cold water, oil, gas, or air in compressed air systems by adjusting a wedge or gate. These valves are rated for pressures up to 200 psi and are available in a wide range of standard and custom sizes.
Brass flanges are crucial components in piping systems, used to create secure and leak-proof connections between brass pipes and fittings. Known for their strength, durability, and corrosion resistance, brass flanges offer a long service life and are available in various sizes. Custom sizes can also be made to fit unique or unusual pipe dimensions.
Brass flanges are manufactured from different grades of brass to meet specific application needs. They are essential for connecting equipment that cannot be joined directly and provide support for piping or tubing carrying heavy loads.
The primary advantage of brass flanges is their ability to form a tight seal, which is critical for preventing leaks and contamination. The choice of flange type depends on the application. Brass flange types include weld neck, slip-on, and threaded flanges. Weld neck flanges are suited for high-pressure applications, while slip-on flanges are typically used for lower pressure scenarios.
Brass plate is valued for its machinability and ability to withstand both hot and cold pressure processing. It is commonly used in structural components such as gaskets and linings for cutting and stamping applications. Brass plates are manufactured from various brass grades, making them suitable for marine applications and conduits for steam and oil.
Many brass parts, including pins, bolts, washers, nuts, and radiator components, start as brass plates. The popularity of brass plate is attributed to its plasticity in both cold and hot states, as well as its ease of brazing or welding. UNS C26000 is a commonly used brass grade for plates due to its strength and low thermal conductivity.
Brass plates are available in various sizes and can be custom-made to meet specific needs. They come in standard preformed sizes or can be tailored to unique dimensions. UNS C28000 brass plates are noted for their low friction coefficient, which helps reduce wear on moving parts.
Brass rods serve as fundamental materials for manufacturing brass tools, fasteners, and various products. Due to their high melting point, brass rods can be used as a substitute for solder in joining metal pieces. In production processes, brass rods are cut to specific or custom lengths and then transformed into finished products. They are available in various cross-sectional shapes, including round, triangular, square, hexagonal, round hollow, D stock, and rectangular, which are created through extrusion.
After extrusion, the brass rods are cooled and treated with an acid bath to remove oxidation. They are then cold drawn to meet the dimensional requirements of the application and to achieve the desired mechanical properties. Selecting brass rods that closely match the shape of the final product helps minimize waste.
Brass rods are used to manufacture components such as valves, fasteners, gears, connectors, and handles. Brass brazing rods, which have a higher melting point than solder due to their copper content, are particularly useful for joining metal pieces that will be subjected to stress or pressure.
Beryllium Copper is a versatile copper alloy that is valued for its high strength and hardness, combined with good electrical and thermal conductivity. It is a non-ferrous, non-magnetic, and non-sparking metal alloy...
Copper is a ductile, malleable, and reddish-gold metal with the capacity to effectively conduct heat and electricity. Brass and bronze, two commonly used alloys, are created when copper is combined with...
The copper sheet is a highly malleable and workable metal with outstanding electrical and thermal conductivity and corrosion resistance. Copper (Cu) is a reddish, very ductile metal that belongs to Group 11 of the periodic table...
Aluminized steels are steels that have been hot-dip coated with pure aluminum or aluminum-silicon alloys. This hot-dip coating process is termed hot-dip aluminizing (HAD)...
Aluminum 1100 is the softest of the aluminum alloys, which makes it easy to shape and form into a wide range of products for industrial and home use. It can be cold and hot worked but is frequently shaped by...
The term "aluminum coil" describes aluminum that has been flattened into sheets where their width is significantly higher than their thickness and then "coiled" into a roll. Stacks of individual aluminum sheets are difficult to...
Aluminum piping and tubing is silvery-white, soft, and ductile. The metal belongs to the boron group. Aluminum is the third most abundant element present on earth. Aluminum has low density. When exposed...
Metals are a group of substances that are malleable, ductile, and have high heat and electrical conductivity. They can be grouped into five categories with nickel falling in the category known as transition metals...
Stainless steel grade 304 is an austenite stainless steel that is the most widely used and versatile of the various grades of stainless steel. It is a part of the T300 series stainless steels with...
Stainless steel is a type of steel alloy containing a minimum of 10.5% chromium. Chromium imparts corrosion resistance to the metal. Corrosion resistance is achieved by creating a thin film of metal...
Stainless steel grades each consist of carbon, iron, 10.5%-30% chromium, nickel, molybdenum, and other alloying elements. It is a popular metal used in various products, tools, equipment, and structures that serve in many industrial, commercial, and domestic applications...
Steel service centers are companies that specialize in procuring steel directly from mills and manufacturers and supplying them to the customers. They are fundamental to the steel supply chain...
Stainless steel can be fabricated using any of the traditional forming and shaping methods. Austenitic stainless steel can be rolled, spun, deep drawn, cold forged, hot forged, or stippled using force and stress...
Stainless steel tubing is a multifaceted product that is commonly utilized in structural applications. Stainless steel tubing diameters and variations vary greatly based on the application requirements and are...
Titanium metal, with the symbol Ti, is the ninth most abundant element in the earth‘s crust. It does not occur in large deposits, yet small amounts of titanium are found in almost every rock...
Tungsten is a rare naturally occurring chemical element on earth. It is known to be one of the toughest metals on the earth. It is usually a tin white or a steel gray metal. Tungsten is common for its high tensile...
Aluminum is the most abundant metal on the Earth’s crust, but it rarely exists as an elemental form. Aluminum and its alloys are valued because of their low density and high strength-to-weight ratio, durability, and corrosion resistance...