Plastic Corrugated Boxes
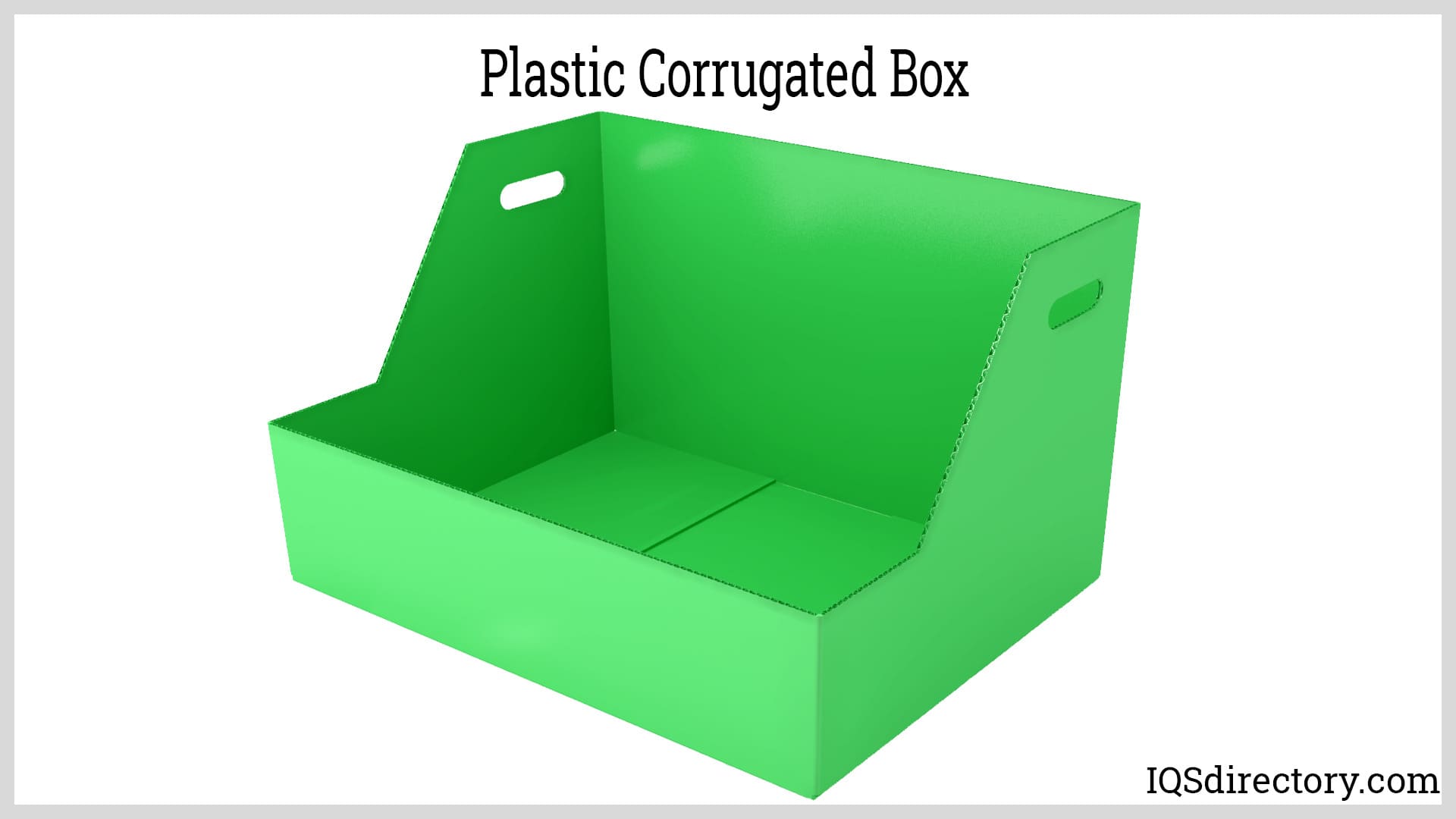
A plastic corrugated box is a disposable container with three layers of material consisting of an inner layer, an outer layer, and a middle layer on its sides. Corrugated plastic is known by various names, including...
Please fill out the following form to submit a Request for Quote to any of the following companies listed on
This article will give a detailed discussion of plastic corrugated boxes.
It is expected that after reading, one should understand the following:
Transporting goods to multiple destinations often causes significant wear and tear on cardboard boxes. They can tear easily, are susceptible to leaks, and may allow exposure to chemicals, moisture, and dust, potentially damaging the contents and disrupting production. Corrugated plastic boxes offer a durable, reusable solution that helps save time, money, and resources.
A plastic corrugated box is a versatile container made from three layers: an inner layer, an outer layer, and a middle layer. This material, often referred to by names such as polyflute, flute plastic, twin wall plastic, or corflute, is typically constructed from polypropylene. These boxes are designed to offer robust protection for goods during storage, handling, stacking, and transportation. Made from high-quality polyethylene or polypropylene, they usually have thicknesses ranging from 2mm to 25mm (almost an inch). Plastic corrugated boxes are fully recyclable and reusable, contributing to reduced waste and cost savings. They are also resistant to chemicals, dust, and water, and are lightweight to ease handling and transport.
Plastic corrugated boxes offer a compelling packaging solution due to their robust material and durability. Their design makes them some of the most portable, shock-resistant, and lightweight plastic options available. Made from polypropylene, a highly durable thermoplastic polymer with a neutral pH, these boxes can withstand a range of environmental conditions, including varying temperatures and weather. They provide effective protection for goods during transport and storage by minimizing damage from external impacts. Additionally, plastic corrugated boxes excel at guarding against moisture and maintaining structural integrity, even when handling heavy items.
When selecting a packaging solution, people seek materials that are lightweight, visually appealing, secure, and cost-effective. Choosing the right packaging is crucial to ensure that products reach their destination safely, economically, and without damage. Fortunately, there are many types of plastic corrugated boxes available, each tailored to meet specific needs and requirements.
Before selecting the right plastic corrugated box, it's important to consider the mode of transportation for the items inside. For example, a box intended for land transport should be designed to withstand rough road conditions, whereas a box for air transport should be adapted to handle changes in atmospheric pressure and temperature.
Packaging can be exposed to moisture during warehouse storage, maritime shipping, or accidental contact with rain. Paper-based materials, such as corrugated cardboard, are prone to water absorption and may fail to protect products if they become wet. In such scenarios, corrugated plastic offers a more resilient alternative. However, it is important to ensure that the adhesive used to assemble the plastic sheets is moisture-resistant to avoid potential damage.
When choosing packaging materials, it’s essential to consider the weight, size, and shape of the product being packed. This is why plastic corrugated boxes come in a wide range of sizes and thicknesses, allowing them to be tailored to fit various products and requirements.
Products are often shipped to a wide range of climates globally. It is crucial to consider these potential temperature variations when selecting shipping options. Plastic corrugated boxes, for example, are capable of enduring significant temperature fluctuations.
Containers are essential for protecting valuable items, so choosing the right one is crucial. Corrugated plastic boxes are designed with three layers: an inner liner, a middle fluted section, and an outer liner. This construction allows them to support various product weights, offer excellent dimensional stability, and come in a wide range of sizes to ensure secure storage. The value of the product should also influence the choice of plastic strength; for high-value items, opting for thicker plastic is advisable to provide additional protection.
Unlike more durable items, delicate products such as crystals, mirrors, and chinaware need extra protection. Therefore, selecting the right container is crucial to prevent damage during storage or shipping. Plastic corrugated boxes are designed to shield their contents from being crushed or broken. For added protection, options like double-walled boxes with partition inserts are available. Additionally, plastic corrugated boxes can be custom-built to address specific handling requirements.
While the exterior of a packaging container is important, its interior is equally crucial. To minimize the risk of damage to items, it's essential to use cushioning materials such as air pads, paper pads, foam, or loose fill to fill empty spaces. For electronics, additional considerations include preventing electrostatic discharge (ESD) and providing corrosion protection. Plastic corrugated boxes are well-suited for these needs, offering solutions for both cushioning and protection.
As discussed in Chapter One, plastic corrugated boxes are designed to address various requirements, but their manufacturing process remains consistent. These boxes are made from three layers of thin polypropylene plastic, often referred to as plastic cardboard. The production of corrugated plastic boards and the formation of corrugated boxes are achieved through specific machine processes, detailed below.
A corrugator is a set of machines designed to continuously produce single, double, or triple-wall boards. The operation of a corrugator machine is relatively straightforward. The process involves two main stages: the containerboard combining process and the box manufacturing process. In the first stage, one or more fluted plastic sheets, which are designed to provide strength and cushioning, are bonded to flat layers of plastic linerboard. The second stage involves assembling these corrugated plastic sheets into boxes. Corrugating machines are equipped with interchangeable rolls that vary in flute size, allowing for adjustments in the width of the corrugated medium.
During the containerboard combining process, a roll of plastic material is fed into the corrugator. The machine's large, electrically powered rollers move the material through preheating rollers and corrugating rolls, which shape the plastic into flutes. A second liner roll is then aligned with the corrugated rolls, and once the fluted material is formed, it is brought into contact with another flat layer of plastic at a section of the machine known as the bridge. Here, the fluted plastic is glued to the solid layer to create a durable wall of the corrugated plastic board.
A corrugated box can be classified based on the number of walls it has: single-wall, double-wall, or triple-wall, depending on the layers of corrugated plastic used. After a wall is formed, the corrugated edges of the plastic are carefully coated with starch adhesive at a glue station to bond it to an adjacent wall. Finally, the layered sheets move across plates heated by steam as they
At the end of the corrugator, the plastic board is cut and separated into sheets, known as box blanks, by a slitter-scorer. Once the box blanks are produced, they are transferred to an automatic stacker and placed onto a large rolling platform. A folding machine then shapes the blanks into boxes along pre-defined score lines. After the boxes are properly formed and trimmed, adhesive is applied to the sections that will be joined to finalize the box assembly.
Plastic corrugated boxes come in various types, each offering specific advantages for different applications. These include:
Plastic Profile Board - This type of board provides a lightweight yet rigid material, available in various weights and thicknesses.
Triple-Wall - As indicated by its name, triple-wall corrugated plastic boxes feature three layers of flutes. Each layer contains flutes of different sizes to enhance stability. The additional layers increase compression strength and cushioning capabilities.
Double-Wall - A double-wall box features an additional layer of fluting compared to a single-wall corrugated plastic box. This extra layer enhances its ability to support heavier and larger items.
Single-Wall - This basic corrugated design consists of a single outer layer with an inner layer of fluting in between. It is also referred to as double-face corrugated plastic.
Honeycomb - Honeycomb corrugated boxes feature a unique honeycomb pattern within the corrugation. This design makes honeycomb corrugated plastic flexible and suitable for creating lightweight boxes ideal for transporting non-fragile materials.
Here are the top five flute profiles used in plastic corrugated boxes:
The A-flute profile is the original flute design used in corrugated plastics. It features approximately thirty-three flutes per linear foot and has a thickness of about a quarter inch.
B-flute corrugated plastic boxes, which have around 47 flutes per linear foot and a thickness of 1/8 inch, are commonly used for packaging canned products.
C-flute corrugated plastic, commonly used for shipping cartons, has a thickness of 5/32 inch and approximately 39 flutes per foot.
E-flute corrugated plastic features approximately 90 flutes per linear foot and has a thickness of 1/16 inch.
F-flute corrugated plastic, used for small retail packaging, has around 125 flutes per foot and a thickness of 1/32 inch.
Multiple flute profiles can be combined in a single composite board. For example, a triple-wall board might feature two layers of C-flute medium and one layer of A-flute medium. By mixing flute profiles, designers can adjust the overall thickness
This corrugated plastic box features partitions, allowing it to hold materials in separate compartments. The partitions are custom-designed to match the size of the individual items. Besides offering enhanced organization, these boxes are thin, strong, and cost-effective, making them an ideal choice for storing, protecting, or shipping delicate, non-waterproof items.
A double-cover plastic corrugated box features a body constructed from square or rectangular tubing with interchangeable telescopic covers. These boxes are stored flat and can be easily assembled as needed. The top and bottom pieces slot together to provide a secure fit, offering enhanced protection for valuable items. The interlocking design of the double-cover box ensures a snug and stable fit, with reinforced flanges on both the covers and tubes to strengthen the structure. This design is particularly suited for shipping large or bulky items such as appliances and heavy machinery.
These plastic corrugated boxes are engineered for improved handling and ease of carrying, featuring an integrated plastic handle. They are commonly used when transporting fragile components to provide added convenience and protection.
Corrugated plastic mailers, also known as corrugated plastic shipping boxes, are designed to safeguard items during delivery. Available in various colors for enhanced visual appeal and branding, these boxes can be customized to reflect a business's identity. They are often used for subscription box packaging and e-commerce, accommodating either a single large item or multiple smaller products.
Slotted boxes are crafted from corrugated plastic that is pre-scored and slotted. This slotted style is the most prevalent and widely utilized form of corrugated plastic boxes. These boxes are versatile, used for shipping or storing a variety of items, chemicals, and components. Several common slotted box designs exist. A regular slotted box features four equal-length flaps that, when folded, meet at the box's center, with the outer flaps being half the width of the box. The half-slotted box is similar but lacks a top set of flaps. Another variation is the overlap slotted box, where the outer flaps overlap and are stapled together to form the box, with a longer length than width. The full overlap box, where top and bottom flaps overlap, offers additional support for larger items. Finally, for a box with a center slot, the inner and outer flaps differ in length and meet in the middle.
A telescoping corrugated plastic box features a two-piece design, with the lid being larger than the bottom section. This design allows the lid to extend partially or fully over the tray's sides, enhancing stacking strength and making it easier to open. These boxes are widely used across various industries for displaying products, as well as for secure packaging, transporting, and shipping items. Heavier or bulkier items are often packaged and shipped in sturdier telescoping boxes, which still allow for easy access to the contents inside.
A rigid corrugated plastic box consists of two end panels and a central section. The self-erecting version of this box is made from a single sheet of scored corrugated plastic, which can be folded into either a slotted or telescoping container.
Folder-style boxes have a solid base, with overlapping flaps that are notched to allow for easy folding or wrapping around a product. These boxes are commonly used for transporting smaller items, such as books and printed materials. Their one-piece construction includes a flat bottom, with side flaps extending to create the sides, ends, and top. There are versions available with either five or four panels. The five-panel design includes a top flap, while the four-panel version does not. In the five-panel design, the second and fourth panels serve as the top and bottom, while the fifth panel forms a side in the one-direction folding setup.
The tuck-top corrugated plastic box is designed for quick, efficient, and easy closure. The tuck flap fits into the box's body, with the top flaps closing securely over the top when extended. This design flattens the bottom of the box and allows the sides to open up, simplifying the process of loading items. A variation of this is the tuck-top snap-lock bottom box, where the bottom consists of four interlocking flaps instead of being pre-glued, differing from the tuck-top auto bottom version.
Plastic corrugated boxes are commonly used to package office supplies and stationery.
Consumers planning a move and considering hiring a moving company should opt for plastic corrugated boxes to transport their belongings. These boxes are durable enough to protect fragile items that might be damaged if packed in cardboard. One of the key advantages of plastic corrugated boxes is their ability to withstand heavy loads without breaking, ensuring the safety of possessions and making the moving process smoother.
Plastic corrugated packaging has been a significant advancement for the supply chain. These boxes are widely available, easy to pack and unpack, and ensure the safe delivery of various products. They are ideal for transporting a wide range of industrial goods with efficiency.
Available in various sizes and designs, plastic corrugated boxes are ideal for transporting a diverse range of textiles.
Auto components vary greatly in size and shape, requiring meticulous planning for storage and shipping. It is crucial to use sturdy, weight-bearing, and cushioned packaging to protect these parts from damage. Plastic corrugated boxes are well-suited to meet these needs.
Medications require secure delivery within specific temperature ranges, making plastic corrugated boxes an ideal choice. These boxes naturally regulate temperatures and can accommodate multiple items simultaneously with the help of dividers or partitions, ensuring that contents remain undamaged. Plastic corrugated boxes are particularly well-suited for transporting several small items between locations.
Electronic devices are generally quite fragile and require careful packaging to prevent damage during shipping. Additionally, the packaging must protect against static electricity. Fortunately, plastic corrugated boxes are a good choice for this purpose, as they do not conduct electricity and provide the necessary protection for electronic components.
In e-commerce, presentation plays a key role. Customizing plastic corrugated boxes with unique designs, aesthetics, and brand elements can enhance marketing and branding efforts. By personalizing these boxes, you can effectively promote your business and make a memorable impression.
Plastic corrugated boxes are made from materials that comply with FDA food storage regulations and are built to withstand a range of temperatures. This ensures that food remains fresh during transport or temporary storage.
Storage, transportation, and distribution are vital functions across many industries. Packing items effectively requires meeting both customer and business needs. Key considerations include convenience, portability, and the protection of goods. While cardboard boxes are commonly used for packing, plastic corrugated boxes offer several advantages over cardboard, which we will explore in detail.
A plastic corrugated box is a disposable container with three layers of material consisting of an inner layer, an outer layer, and a middle layer on its sides. Corrugated plastic is known by various names, including...
Plastic crates are containers used for moving or transporting goods from point A to point B. They are also used for storage and are made of exclusively or partially plastic material. The basic material is plastic...
A plastic tote is a box type portable storage container that is made of resilient and durable plastic that is capable of withstanding heavy duty use in industrial and residential settings. They come in...
A cardboard box is a shipping container made of thick heavy duty paper known as paperboard, which is more than 0.01 inch or 0.25 mm thick. The term cardboard is used as a generic descriptor for various types of solid firm papers used to produce boxes
Pressure-sensitive adhesive tapes consist of a backing material film coated with an adhesive intended for relatively low-stress applications. Light pressure, usually done by the fingertips, is applied to initiate the binding. In the sticking process, the fluid properties...
Carpet tape is a double-sided tape designed for securing carpets or rugs to the floor. It's made of strong, durable, and adhesive material that can hold the carpet in place and prevent it from sliding or wrinkling. Carpet tape is used in
One kind of pressure-sensitive self-adhesive tape is foam tape. It has one of several different backing materials and is made of foam. It may have adhesive on one or both sides. Foam tapes are, at their most basic level, tapes that are applied to uneven or
A mailing tube is a sturdy, solid, and durable cardboard container designed for shipping long slender devices and products or rolled up maps, banners, and posters. The indestructible exterior of mailing tubes...
Masking tape is pressure sensitive, thin and very adhesive, easy to tear paper that is used in various tasks ranging from masking off areas that are not to be painted or as insulation for electric wires among other...
Paper tubes consist of paper or paperboard sheet layers wound together to form strong, hollow, and usually cylindrical shapes. The paper layers are laminated or bonded together using adhesives. The wall thickness of the tube can vary depending on the number of layers wrapped during manufacturing...
A plastic tank is a large capacity liquid or granular storage unit that can be vertical, horizontal, below or above ground, as well as movable. They are designed to hold several gallons of a variety of substances for long periods without experiencing wear, weathering, or deterioration...
A plastic water tank is a large capacity container designed to store water for household, agricultural, irrigation, and industrial manufacturing use. There are various types of water tanks produced to meet the needs of specific applications, with...
A poly tank is a plastic storage tank used to store, transport, and collect water, other liquids, and granular or powder materials. They are made of polyethylene or polypropylene and are a cost effective, lightweight, and easy to handle...
PTFE stands for polytetrafluoroethylene and is a synthetic fluoropolymer used widely in many industries and many other applications. PTFE is also commonly referred to as thread seal tape, teflon tape, and plumber‘s tape...
A Sonotube® is a cardboard concrete forming tube made of waxed paper or lamination that is wound into a tube into which concrete is poured to create supports, columns, and supports for posts. Sonotube® is a registered trademark owned by SPC RESOURCES, INC...