Deburring
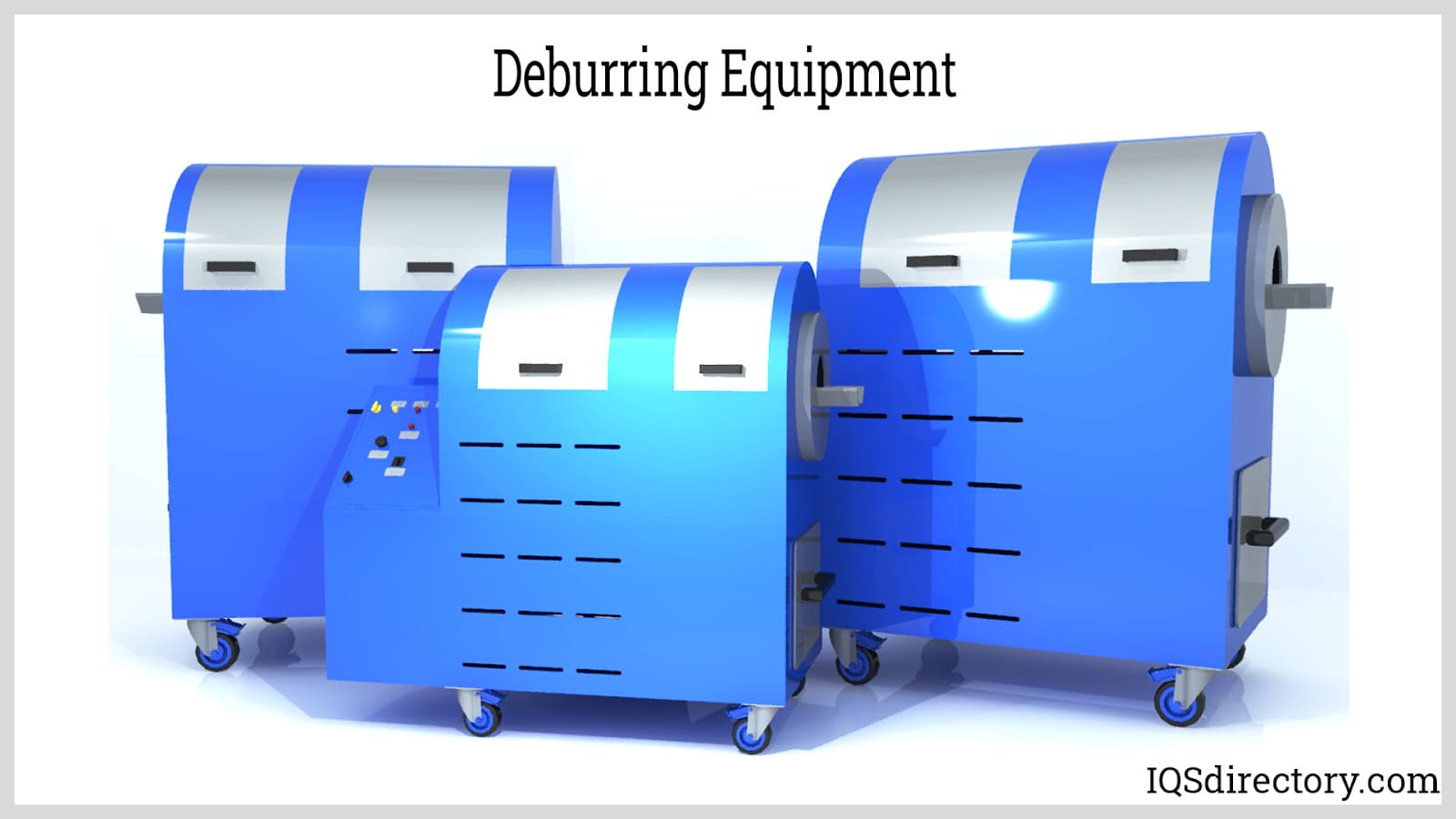
Deburring is a secondary operation of a machining process that enhances the final quality of the product by removing raised edges and unwanted pieces of material, known as burrs, left by the initial...
Please fill out the following form to submit a Request for Quote to any of the following companies listed on
This article will take an in-depth look at tumbling machines.
The article will bring more detail on topics such as:
This segment delves into tumbling machines, outlining their components, operation, and the complete process they encompass.
A tumbling machine is a durable piece of equipment designed for deburring and polishing metals, making it perfect for finishing either large components or many smaller ones. Known also as a barreling or mass-finishing machine, it functions by rotating parts inside a multi-faceted, urethane-coated barrel filled with processing media and a liquid compound, efficiently deburring parts through its tumbling motion.
The operation occurs as the media's top layer continually slides down the incline formed by the spinning barrel. Tumbling machines are extensively used in the jewelry industry for processes such as stone tumbling, jewelry polishing, and deburring metal parts. The rotary barrel tumbling machine and the vibratory tumbling machine are the most prevalent types used.
A tumbling machine consists of several essential components, including:
This includes components like the vibratory tub, motor, electric control panel, and a spring system. These parts work together to create the vibratory motion essential for the finishing process.
Water plays a vital role in the wet deburring process, significantly reducing friction between parts and media (discussed below). It also helps in removing dirt and grease by washing away the scrap, resulting in clean parts.
Media, made of various abrasive materials, are added to the bowl along with the parts to optimize the polishing or deburring process. The effectiveness of deburring is determined by the abrasive content in the media.
Compounds are mixed with media to enhance polishing or other specific functions. Usually in liquid form, sometimes as a paste, certain compounds can also act as corrosion inhibitors.
Tumbling machines have barrels filled with media, abrasives, and the items to be processed. The machine induces a consistent rotation in the barrel, filled with these elements. The friction from this movement grinds, smooths, and polishes the surfaces of the items handled.
Each material requires a different cycle based on its properties. Hard materials need specialized media and abrasive compounds, distinct from those used for softer materials. The surface treatment is mechanical; the tumbler creates friction depending on the type and amount of deburring media, whether it uses vibration or rotation.
A vibratory deburring machine features a circular tumbler lined with polyurethane (PU) to accommodate the parts and media mixture. A motor powers the machine, and springs provide stability. Activating the machine makes the bowl vibrate, initiating the parts' finishing process.
Within the bowl, the media rubs against the parts, aiding in their finishing. The vibratory motion helps deburr the parts, while the toroidal movement ensures comprehensive cleaning, deburring, and polishing.
Tumbling is employed on an industrial scale to eliminate surface imperfections resulting from prior processing. Additionally, it is used to polish the surfaces of various materials, enhancing their finish and appearance.
Such tumbling and vibratory finishing processes are normally employed for the polishing of metal alloys, plastics, natural materials, and precious metals.
The vibratory tumbling process is used by tumbling machines to effectively create smooth and polished surfaces on plastic as well as metal parts. This type of process works by combining the water and abrasive media in a machine called a vibratory tumbler. This form of tumbling has been used for years. It has been used by many companies for providing incredibly smooth surfaces on even the most fragile plastic and metal parts.
This tumbling machine generates rapid vibrations to facilitate strong collisions among the parts, water, and abrasive media. Vibratory tumbling is a preferred finishing method, with vibratory tumblers available in various sizes, from small to large.
The high-energy tumbling process, also known as centrifugal barrel finishing, is akin to vibratory tumbling. It utilizes water and abrasive media to achieve exceptionally smooth surfaces. This method is faster than vibratory tumbling and is often chosen when time is limited.
High-energy tumbling involves sealed barrels filled with the parts to be finished, water, and abrasive media. These barrels are mounted on a carousel that spins in one direction, creating centrifugal force while pushing the barrels in the opposite direction. Like vibratory tumblers, high-energy tumbling machines come in various sizes, from large to small, accommodating both large and small batches efficiently.
When choosing between vibratory tumbling and high-energy tumbling, several factors should be considered. Time management is crucial, as high-energy tumbling often requires more manual intervention and can take longer to complete. In contrast, vibratory tumblers are designed for optimal automation, making automated processes more efficient and cost-effective compared to those requiring manual handling.
Complexity is also an important factor to consider. The machinery for vibratory tumbling can be more complex and, therefore, more expensive. However, both vibratory and high-energy tumbling are highly effective in producing smooth, durable, and polished surfaces, enhancing the longevity of metal and plastic parts.
The tumbling-vibro finishing process consists of four key steps: grinding, smoothing, polishing, and shining. This method aims to achieve a flawless, shiny, and smooth surface. Grinding is the initial step, focusing on removing the most pronounced imperfections from the parts.
The second stage in the process is smoothing, where minor imperfections and remnants from the grinding phase are addressed. Following this, the tumbling process moves to polishing, which prepares the surface for the final step. The last stage is shining, where the treated piece achieves a brilliant, mirror-like finish, with a flawless surface.
A variety of materials can be processed using tumbling machines, including the following:
Different types of tumbling machines include:
The centrifugal barrel tumbler operates similarly to a Ferris wheel, with smaller baskets mounted on the edges of a large wheel. This tumbler features four barrels, each akin to a seat on the Ferris wheel, and a large flywheel. As the flywheel rotates, each barrel completes a full turn, generating extremely high centrifugal forces due to the flywheel's rapid spinning speed.
These forces can be 15 to 20 times greater than gravitational force, causing the contents to slide against each other under high pressure. This intense pressure enables rapid processing of metal parts and produces smooth, consistent finishes. The operator can adjust the tumbling speed, allowing for fine finishing and polishing at lower speeds or more aggressive deburring and edge smoothing at higher speeds.
Centrifugal tumbling machines are highly effective at removing significant burrs and blending lines left by machining. They excel in polishing and burnishing applications as well. When used with various ceramic and organic media, these machines can achieve a wide range of finishes, from super-fine surface finishing to thorough burr removal.
These tumbling machines are industry workhorses, used with a variety of metals such as aluminum, brass, chrome, steel, titanium, and stainless steel. However, they are not suitable for deburring plastic parts, as plastic is too pliable for this process.
Typical configurations of centrifugal barrel tumbling machines are:
A barrel divider enables the operator to split each barrel into smaller compartments. This helps prevent part-on-part contact and damage during processing.
This option is commonly used in larger systems to separate tumbling media from metal parts after processing. Without a separator, operators must manually pick out parts from the media, which can be very time-consuming for smaller components. The separator uses a vibratory screen to separate parts from media, with interchangeable screens available to handle different sizes of media and parts.
This option is commonly used in smaller systems to trap sediment from the tumbling process. A cascading feature removes the sludge from the processing table and traps it, while a sump pump expels the water from the tank. The sludge accumulates over time and needs to be cleaned out regularly.
An industrial parts tumbler operates in three categories of smoothness, starting with the deburring process. This step removes sharp edges or burrs left on metal surfaces after machining. A common example is rounding off sharp corners on a metal piece.
The second category of work involves blending machining lines, which is similar to deburring. This process smooths the finish on a metal piece by removing machine lines left from milling and cutting the metal to the desired shape and size.
The third category of action is the polishing process, also known as burnishing. This step elevates the smoothness of the part, making it shiny and capable of achieving a mirrored finish.
A vibratory tumbler is a large, donut-shaped drum. It consists of parts that rotate in a circular direction while the drum is shaking at a high speed. This motion causes the tumbling media and the parts to scrub against each other which results in the removal of burrs from, and the abrading of, the parts treated within. After this production step, the tumblers empty into a conveyor belt and the contents are sent through a dryer and cleaner. The dryer and cleaner contain rust inhibitor ingredients that serve to extend the shelf life of plain finish parts.
The shelf life of these parts can be negatively impacted by environmental factors, improper handling, and storage. It's important to avoid dropping parts from high distances to prevent edge damage. Additionally, handling with bare hands should be avoided as skin oils and impurities can harm the finish. Personnel should wear gloves when handling parts with a plain finish.
A drum tumbling machine features rubber-lined strips and an adjustable drum tilt to control the frequency of collisions between items. Its operation relies on the impact of workpieces with similar hardness against each other. The drum’s diameter is determined by the required productivity levels.
Drum tumbling machines may come with automated systems for both loading workpieces and transferring finished products. These systems streamline the process by loading finished pieces directly onto pallets for packaging. To prevent dust buildup, which can age the finished products or potentially harm the machine, a dust removal system can be installed. Regular maintenance to remove dust after each use is also recommended to keep the machine in optimal condition.
Linear tumbling machines come in various configurations and differ from drum tumbling machines in their operation. Instead of relying on drum rotation for collisions between products, linear tumblers use crank-type drives or chains as beaters to strike the surfaces of the items. This method results in a different finishing action compared to the tumbling action within a rotating drum.
One drawback of linear tumbling machines is that the beaters tend to wear out and need frequent replacement. In contrast, the rubber lining in drum tumblers is highly durable and lasts longer. However, a key advantage of linear tumblers is their ability to finish only one surface of a product, preserving the edges and corners of other surfaces. This feature makes them ideal for finishing surfaces like paving or facade tiles.
Barrel tumblers use rotary motion combined with abrasive media to create sliding friction, which facilitates polishing or deburring as parts slide against the media and each other. Centrifugal barrel tumblers enhance this process with additional centrifugal force, intensifying the tumbling effects. Vibratory tumbling machines, on the other hand, employ a side-to-side motion to shake a bowl or tub in a circular path, akin to the rock-polishing kits used by children. This method achieves finishing through a scrubbing action as parts and media shear against one another.
For general-purpose polishing, light to heavy deburring, and rapid metal removal, ceramic tumbling media is highly recommended. It excels with harder metals such as steel and stainless steel, though it can also be used on softer metals like aluminum. Ideal for very heavy parts, ceramic media is cost-effective, durable, and versatile, making it the most popular choice in mass finishing. This media is crafted from ceramic material, silica, and other minerals or abrasives, which are combined and fired to produce an effective grinding and finishing agent suitable for a variety of workpieces.
This formulation results in a very hard, cement-like product. Ceramic shapes, such as stars, triangles, and ellipses, are extruded and then cut to the desired size. The density of these shapes is influenced by the amount of abrasive material included in the mix prior to firing. A higher concentration of abrasives increases the density, making the ceramic tumbling media more aggressive and faster-wearing on workpieces.
Carbon steel tumbling media is employed for both burnishing and polishing metals. Its high bulk density applies substantial pressure on parts, achieving a high shine in a minimal amount of time. Additionally, carbon steel media is used for surface work-hardening, enhancing the wear resistance of parts. Available in various sizes and shapes, this media is known for its efficiency, resulting in very short cycle times.
High-density ceramic tumbling media is more robust and durable compared to standard ceramic media. It is ideal for applications requiring faster cycle times and minimal residue. This media accelerates both deburring and polishing processes across various tumbling equipment. Notably fracture-resistant, it offers a rapid cutting action, enhancing overall product throughput.
Premium ceramic tumbling media is engineered for tasks demanding precise deburring and polishing. Its finer sizes are perfect for detailed finishing work, delivering exceptionally smooth surface finishes. It is available in various shapes and sizes, including fast-cutting options, to cater to diverse finishing requirements.
Hardwood tumbling media is selected and cut for dry tumbling applications to ensure optimal performance. It works effectively with finishing creams for tasks such as surface smoothing, deburring, and polishing, particularly on plastic parts. This media can achieve nearly mirror-like finishes without the need for water and is known for its durability and longevity.
Plastic tumbling media is used for a range of finishing tasks including general metal deburring, precision deburring, burnishing, and polishing. It is suitable for softer metals like brass or aluminum, as well as for threaded parts.
This chapter will explore the various applications and advantages of tumbling machines.
Tumbling machines find application across diverse industries. They are commonly used in the production of buttons, eyewear, and jewelry. Additionally, these machines play a crucial role in treating the surfaces of small metal components and fashion accessories, including hair ornaments and costume jewelry.
In the medical device industry, customers demand consistent, high-quality finishes on metal components, particularly those with intricate geometries. Centrifugal barrel tumbling machines are renowned for their efficiency in polishing and deburring tasks. They excel in processing materials such as titanium, cobalt-chrome, and stainless steel, making them ideal for treating implants and surgical instruments. Additionally, these machines are used to polish dental implants and dental tools, ensuring a superior finish.
In the aerospace industry, achieving metal smoothness is critical for the high performance of components. Hand deburring of aerospace parts is often impractical and costly. As a result, manufacturers rely on centrifugal barrel tumbling machines to efficiently handle this task. This method is particularly advantageous for processing turbine blades and jet engine components, where precision and performance are essential.
The automotive industry is another type of business that benefits from centrifugal barrel tumbling machines for smoothing metal parts surfaces. In particular, the automotive industry employs centrifugal barrel parts tumblers for polishing engine heads, fasteners, and gears.
At these shops, centrifugal barrel tumbling machines deliver fast, cost-effective performance for polishing as well as deburring metal parts.
Other benefits include:
The tumble finishing process can be completed in a remarkably short time, ranging from just a few minutes to several hours, depending on the size and type of the workpieces. This method is significantly faster than traditional technologies and ensures a consistent and repeatable finish.
Tumbling machines used for deburring offer a precise approach to removing sharp edges, cleaning drill holes, and enhancing the overall surface smoothness of parts.
Previously, smoothing and polishing metal and plastic materials required complex and costly equipment. Modern tumbling machines have revolutionized this process by making it both efficient and cost-effective. Vibratory deburring machines improve the reliability and longevity of parts, ultimately reducing costs for manufacturers.
Modern tumbling machines are designed to be low-maintenance, offering high reliability with minimal need for frequent repairs or cleanings. This leads to increased uptime, cost savings, and the capacity to handle more orders efficiently.
Many tumbling machines are capable of handling both large quantities and very small items simultaneously. This versatility helps to save both time and money, making the process more efficient.
Vibratory tumbling machines offer exceptional versatility, as they can polish a wide range of materials including ceramics, plastics, steel, stainless steel, aluminum, and copper. Additionally, these machines can be tailored to meet specific user requirements, enhancing their adaptability.
The vibratory finishing process relies on high friction to effectively clean and deburr parts. It is particularly suited for delicate materials that might break or lose their shape easily. Vibratory tumbling machines provide a smooth finish while preserving the integrity of the product.
In mass production, achieving uniformity is crucial. Metal parts often come off the production line with imperfections that can affect consistency. Barrel tumbling machines provide an effective solution for smoothing out these imperfections, ensuring a more consistent batch. Compared to hand polishing, mass metal finishing with these machines delivers far more consistent results.
Some of the factors to include when working with industrial tumbling machines include:
One must be aware that centrifugal barrel tumbling machines generate a significant amount of heat within each barrel. For example, at a speed of 150 rpm, a 120-liter (32 gallons) centrifugal barrel tumbling machine can boil water in 15-20 minutes. Operators must keep this level of heat in mind for safety reasons and also for how it impacts the surface-finishing process. Due to the heat generated, very long cycle times are usually categorized as 5-15 minutes for many parts. A cycle that goes beyond an hour is considered an extremely long one and is not recommended.
Placing too many parts in a tumbler’s barrels will result in part-on-part contact, which can damage the parts. For cosmetically-sensitive parts, barrel dividers can be employed as a solution. Other important factors to consider are the part-to-media ratio in each barrel, as well as utilizing an appropriate amount of water and cleaning compound.
A typical barrel centrifugal tumbling machine has four barrels. Filling only one barrel must be avoided, as this practice can be hard on the bearings; the same is true when loading three of the four barrels. It can cause the machine to be off-center. If an odd number of barrels must be used, the empty barrel(s) opposite the loaded one(s) must be counterbalanced. If nothing else, the opposite barrel(s) should be filled with water to help counterbalance the machine.
A tumbling machine is a machine that is utilized for the finishing processes of parts. There are different types of tumbling machines that are used including the vibratory tumbler, centrifugal barrel tumbler, parts tumbler, drum tumbler, linear tumbler, etc. These machines are utilized for smoothing and polishing products. The process utilized by these machines is called the tumbling process. There are also different types of tumbling media used by tumbling machines in the tumbling process. These media include ceramic media, hardwood media, stainless steel media, carbon steel media, plastic media, etc. Tumbling machines have different applications in a wide range of industries. For example, a tumbling machine is used in the aerospace industry for smoothing jet engines, as well as blades. In the automotive industry, tumbling machines are also utilized for polishing engine heads and gears. Tumbling machines also help produce a number of other items with great consistency. These machines are an efficient, durable, low- cost, low-maintenance solution for the deburring, polishing, and finishing of numerous parts.
Deburring is a secondary operation of a machining process that enhances the final quality of the product by removing raised edges and unwanted pieces of material, known as burrs, left by the initial...
Finishing machines are machines used for metal finishing, which is the last stage of the metal fabrication process; the stage encompasses the use of machines in finishing the metal surface...
Vibratory tumbler is the equipment used in a vibratory finishing process, one of the most common methods in mass finishing. But how does a vibratory tumbler work...
Industries worldwide utilize abrasive blasting for various purposes, including cleaning rust and oil, removing surface coatings like paint and pollutants, preparing surfaces for paint and coatings, reinforcing metal surfaces and...
An aqueous part washer is an automated or semi-automated machine manufactured to clean, remove tough grease, and dry large or small parts before distribution or surface treatment. The washing is necessary since...
Automated parts washers are mechanical devices designed to efficiently remove grit, oil, grime, dirt, paint and other contaminating substances from parts with minimum manual supervision. These substances are removed...
A parts cleaner is a cleaning device that uses various types of solvents, cleaning agents, and processes to remove grease, grime, and contaminating materials from manufactured parts prior to shipment or movement for further processing...
A parts washer is a mechanical device designed to remove grit, grime, oil, miscellaneous debris, dirt, paint, and other contaminating substances from parts in preparation for their use in assembly operations, packaging, or coating...
Sandblast cabinets include systems or machinery and components for projecting blast media against a part‘s surface to abrade, clean, or modify the surface. Sand, abrasive, metal shot, and other blast media are driven or propelled using pressurized water, compressed air, or a blast wheel...
Sandblasting equipment includes systems or machinery, and components for projecting blast media against a part‘s surface to abrade, clean, or modify the surface. Sand, abrasive, metal shot, and other blast media are driven or propelled using pressurized water, compressed air, or a blast wheel...
Shot peening equipment includes systems or machinery and components for projecting shot peening media against a part‘s surface to modify the surface or surface engineer the part...
An ultrasonic cleaner is a type of sonic cleaner or sonic cleaning machine that uses cavitation to remove unwanted material. The cleaning effect is created by the compression and refraction of a cleaning medium. Miniscule vibrations propagate throughout the...
Ultrasonic cleaning is a type of cleaning process which uses cavitation induced by alternating compression and rarefaction cycles at ultrasonic frequencies. Ultrasonic frequencies are sound waves vibrating at 20 kHz or higher...
A wastewater evaporator is a method of removing water from water-based waste by converting the water in the waste to a vapor and leaving contaminants. The function of a wastewater evaporator is to reduce the volume of waste materials...
Parts washers are designed for cleaning, degreasing of equipment, and drying of mass quantities of small or large parts in preparation for surface treatment, assembly, inspection, or shipment...