Finishing and Polishing Machines
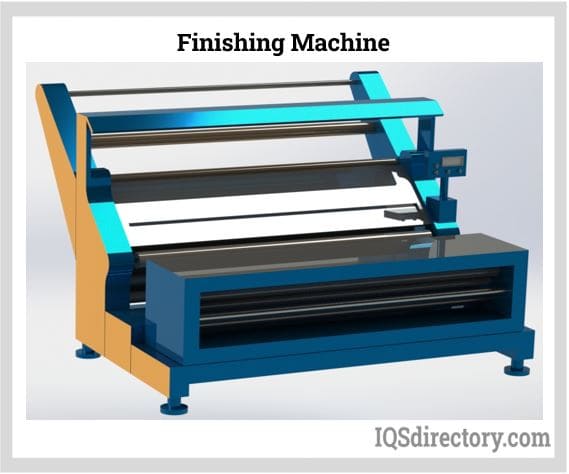
Finishing machines are machines used for metal finishing, which is the last stage of the metal fabrication process; the stage encompasses the use of machines in finishing the metal surface...
Please fill out the following form to submit a Request for Quote to any of the following companies listed on
This article gives you a complete guide to the deburring process and deburring machines. You will learn about:
Deburring is a secondary machining process aimed at improving the final quality of a product by eliminating raised edges and unwanted material remnants, known as burrs, that result from initial machining operations. Burrs are typically formed through shearing, bending, cutting, piercing, and compressing materials, and are most commonly found on soft and ductile materials. Deburring machines use various methods—including mechanical, electrochemical, and thermal techniques—to effectively remove these burrs.
When materials are subjected to shearing or bending forces up to their failure point, they undergo plastic deformation. This causes regions along the edges to become bent, elongated, and extruded. These elongations and extrusions are particularly noticeable at the entrance, sides, and exit of the cutting tool. The formation and size of burrs are difficult to predict and quantify, making deburring efficiency largely empirical. It often requires multiple production trials to refine and perfect the process.
Deburring can be accomplished through various methods, many of which are "global," meaning they affect the entire product. Since global deburring processes impact the whole surface, they can inadvertently alter the final dimensions or introduce chemical and abrasive residues. Therefore, it is crucial to carefully select and control deburring methods to maintain the product's desired characteristics.
Deburring can represent a significant portion of manufacturing costs, particularly in high-precision applications. For example, deburring accounts for about 30% of the manufacturing cost for high-precision parts in aerospace applications, and approximately 15 to 20% for automotive parts. Despite its cost, deburring does not add intrinsic value to the product, highlighting the importance of efficient and controlled deburring processes.
Despite the challenges and associated costs, deburring remains a crucial part of the production process for the following reasons:
Edge quality significantly impacts the form, performance, and longevity of a product. Burrs and raised edges can affect the precise fit and assembly of machine parts, which is crucial for precision components in aerospace, automotive, and electronics industries. For mating parts such as gears, rollers, and other sliding surfaces, burrs can cause interference and potential damage.
Parts with burrs generally have a reduced fatigue life compared to burr-free components. Machining processes often introduce residual stresses due to work hardening along sheared and bent edges, which alter the mechanical properties of these regions. Features like holes, slots, and notches concentrate stress, and the irregular profile of burrs at the edges can act as crack initiation sites.
Thermal and roll-over burrs can create crevices that facilitate localized corrosion. Corrosive materials such as water and electrolytes can accumulate in these crevices, and improper coating application can lead to thinner coatings on raised areas, exacerbating corrosion.
Burrs also pose safety hazards, as sharp edges can damage pressurized lines, electrical cables, and potentially injure personnel. To mitigate these risks, sharp edges are often chamfered or radiused to prevent cuts and other injuries.
The most effective way to prevent burr formation is to use less ductile materials, which are less likely to produce burrs. However, this is not always feasible due to material requirements for specific applications. For ductile materials, burr formation is often unavoidable. In such cases, non-conventional methods like chemical etching and laser machining may be considered, though they come with limitations on workpiece thickness and high investment costs.
Finishing, deburring, and tumbling are terms used in secondary machining operations. Finishing is a broad term that consists of operations such as deburring, blasting, polishing, grinding, coating, plating, and so on. Deburring is a type of finishing for removing burrs, irregular edges, and flashes. One method of deburring is through mechanical equipment. Mechanical deburring machines create abrasion imparted by an abrasive media placed together with the part inside a chamber. The chamber is agitated by vibration or tumbling. Thus, tumbling is a deburring process that uses abrasive media and the rotation of the chamber, known as a barrel, to scrape part burrs.
Burrs can be classified based on their formation mechanism, in addition to their cutting direction. The four types of burrs are: Poisson, roll-over, tear, and cut-off burrs.
The term "Poisson" is derived from the Poisson effect, which refers to the expansion in directions perpendicular to the applied stress. When compressive forces are applied to the material, the edges in contact with the force plastically deform and elongate, resulting in burrs. During cutting, as the tip of the cutting tool strikes the workpiece, the edges of the cut become deformed due to the compressive and shearing forces. These deformations, known as entrance burrs, occur at the entry point of the cutting tool.
Roll-over burrs are formed from chips that are bent rather than sheared off by the cutter. As the cutting tool exits the cut, some material rolls along with the tool. This material folds towards the feed and along the cut edge. If the material is sufficiently ductile, the chip may not easily separate from the part. Additionally, the depth of cut influences the formation of roll-over burrs, as a greater depth causes the chip or roll to become thicker.
Tear burrs are side-burrs that arise when the material is plastically deformed rather than fully sheared during cutting. This phenomenon is commonly observed in punching processes, where a sharp, jagged edge is left along the contour of the punched hole. Essentially, tear burrs result from the material tearing away from the workpiece.
A cut-off burr occurs when leftover material remains as the cut part separates or falls away from the main piece. These burrs can be either positive or negative and are commonly seen in saw cuts and automatic screw machine parts. To prevent cut-off burrs, it is important to support both sides of the material properly until the cut is complete.
These types of burrs are commonly known as slags, spatters, or dross. Slags are produced from hardened molten metal during processes like welding, plasma cutting, and laser cutting. Due to residual stresses from heating and uncontrolled cooling, slags have different mechanical properties compared to the base metal. While slags can often be removed by manual brushing, grinding may be necessary in some cases.
Deburring can be accomplished through various methods, depending on factors such as material, part geometry, size and location of burrs, product volume, and cost. Conventional deburring methods include manual and mechanical operations, while non-conventional techniques such as electrochemical, thermal energy, and cryogenic processes are used for specific applications. Below are some common deburring processes, along with their advantages and applications.
This method is used for finishing large quantities of parts or components and can be performed using batch or continuous systems, either dry or wet, depending on the material. Mass finishing requires an initial investment in time and materials to develop the precise finishing recipe for your needs. However, it ultimately saves time, money, and manual labor. Examples of mass finishing equipment include rotary vibrators, continuous flow installations, drag finishing machines, high-energy disk systems, and tub vibrators.
This method involves deburring using hand-held or mechanized tools, such as deburrers, grinders, brushes, files, and sanders. It is a "localized" process, meaning it does not affect the entire part. Manual deburring is used in areas where high tolerance for dimensional variations is acceptable, as the parameters for manual deburring cannot be perfectly controlled. While in-house time standards are commonly established by fabricators and manufacturers, they do not fully address the consistency of the process. This method is generally slow and is typically performed at the end of the production line, making mistakes costly. Below are some types of manual deburring methods.
Brushes made of metal filaments or thin wires attached to a rotating disc are used to scrape off burrs along the edges of the cut. This is a fast and relatively low-cost method but is limited by the consistency of the deburring action. Intensity depends on filament diameter, free length configuration, texture, density, material type, disc width, angular velocity, and contact.
This method employs abrasives like aluminum oxide, silicon carbide, and zirconia, which are bonded into sheets, belts, pads, wheels, and discs. The mechanized reciprocating or rotating action of these abrasives removes raised material from the surface of the workpiece. Abrasives come in a range of grades, from coarse to exceptionally fine, depending on the amount of material to be removed, the desired surface finish, and the specific application.
Sheet metal edging machines use small grinding wheels or pinch rolls to smooth the edges of sheet metal with thicknesses ranging from 0.025 to 0.25 inches. These machines are stationary, with sheet metal being fed either manually or automatically. Some models can deburr both the top and bottom surfaces and can create chamfers or fillets. When using multiple rollers, the pressure applied by each roller pair progressively forces burrs and raised edges to be flattened or displaced. However, it is crucial to carefully control compressive forces, especially on soft and malleable materials, to prevent warping or buckling under the roller pressure.
This method involves using a chamfering, grinding, or deburring tool mounted on a robotic arm. The main disadvantages of manual deburring—such as inconsistency, slow turnover, and labor intensity—are addressed by robotic deburring, which eliminates human error. Robots are capable of performing repeatable movements consistently and quickly. With CNC programming, operators can set predefined movements and parameters such as force and tool speed. Although the initial investment is higher, robotic deburring proves beneficial in the long run due to reduced operating costs and increased safety compared to manual processes.
Mechanical deburring involves using machines to perform general deburring on workpieces. Unlike manual deburring, operators have less control over the aggressiveness and localization of the deburring action. Manual, robotic, and waterjet deburring are also considered mechanical methods due to their abrasive nature. Examples of mechanical deburring machines include the following.
Barrel tumblers are among the most cost-effective deburring machines in terms of operating expenses. These machines not only remove burrs but also polish the surfaces of parts. The process involves loading parts into a chamber or "barrel" along with abrasive media and, if necessary, special compounds tailored to the material and desired surface finish. Barrel tumbling can be performed as a batch operation or, in some cases, as an in-line or single-pass process. It is categorized into wet and dry tumbling.
In wet tumbling, water is used as a lubricant to enhance deburring efficiency and wash away residues. The amount of water influences processing speed and surface finish quality. Compounds designed for ceramic or plastic media are added to the water to provide corrosion resistance, cleanliness, a cosmetic finish, and shine. These compounds also improve the deburring process by removing oils, extending the life of the abrasive media, and reducing foaming from plastic and synthetic media.
While the use of water and liquid compounds offers numerous benefits, it also presents challenges such as wastewater contamination and potential uncontrolled reactions with fluids used in upstream processes.
Dry tumbling uses only dry media, such as sand and organic materials. Sand not only aids in polishing but also functions similarly to water in wet tumbling by carrying residues away and preventing them from embedding in the part's surface. Organic materials, being more absorbent than sand, effectively remove dirt and oils. Examples of organic materials used include corn cob grits, walnut shell grits, and wood pegs.
Using dry media avoids the disadvantages associated with wet tumbling compounds, but the process is relatively slow. Heavier abrasive compositions can reduce processing time, but dry abrasives are generally lighter than their liquid counterparts and take about twice as long to achieve the same deburring effect. Consequently, dry tumbling is less suited for large-volume production.
A specialized version of the barrel tumbler is the centrifugal tumbler, which features an array of two or four tumblers mounted on a rotating turret. The turret rotates in one direction, causing the barrels to rotate in the opposite direction. Each full rotation of the turret equates to one rotation of the barrels. By increasing the turret’s rotation speed, centrifugal forces exceed gravity, resulting in greater abrasive forces and faster deburring times.
Vibratory deburring machines are similar to deburring barrel tumblers where the parts are loaded into a chamber along with the abrasive media and other additional compounds. Their main difference is the movement of the chamber. While tumblers rotate to generate agitation inside the chamber, this type of machine vibrates to generate motion. The chamber is mounted on springs or dampers which isolates its movement from the foundation. An off-center revolving weight is attached which shakes the contents of the chamber. Various configurations are available such as tubs, circular bowls, or trough machines. Choosing the configuration depends on the geometry of the part and its application.
This process uses the impact force of high-velocity water jets to remove burrs and debris from the workpiece. Waterjets are CNC-controlled, similar to robotic systems with tooling. Waterjet deburring operates at lower pressures compared to waterjet cutting, which helps prevent damage to the part and is effective only for removing thin and loosely attached burrs. Larger burrs are difficult to remove without risking damage to the edges. The main advantage of waterjet deburring is its ability to access features that are difficult for traditional deburring systems to reach. Additionally, it ensures the final product is free of oils and debris.
This deburring process utilizes the principles of electrolysis. Electrolysis is accelerated in areas with small gaps between electrodes and inhibited in areas with insulation. The cathodic tool, shaped as a negative of the workpiece, focuses electrolysis on the burr regions. The workpiece serves as the anode in the circuit. An electrolyte is used to transfer charge between the tool and the workpiece, and portions of the tool are insulated to prevent dissolving unintended surfaces. This method is particularly effective for deburring complex geometries and materials that are difficult to machine but conductive. Additionally, there is no tool wear. However, a significant drawback is the challenging wastewater treatment, as the process involves environmentally harmful chemical compounds.
This process, also known as the thermal energy method, involves exposing the workpiece to hot corrosive gases for a very short duration. A thermal shockwave is generated, which rapidly vaporizes the burrs. The rest of the workpiece remains unaffected due to its low surface-to-mass ratio and the brief exposure time. Small amounts of metal, such as burrs and raised edges, sublimate because they cannot dissipate the intense heat quickly enough. Thermal deburring is particularly effective on materials with low thermal conductivity that are prone to oxidation.
Cryogenic deburring is primarily used for precision plastic parts with inherent impact toughness. In this process, liquid nitrogen is introduced into a chamber containing the parts to be deburred. The rapid cooling lowers the chamber temperature close to the glass transition temperature of the plastic material, causing the burrs to become brittle. This embrittlement makes the burrs easier to remove without altering the properties of the rest of the part. The part, along with abrasive media, is then tumbled within the chamber.
This process involves impacting the surface with abrasive media to remove any surface irregularities. Abrasive blasting is used to remove larger burrs and to create a required texture and surface roughness usually for equipment used in fluid shearing applications. Micro-abrasive blasting is more precise in creating smoother surfaces without damaging or changing the dimensional accuracy of the part. This process uses very fine abrasive media such as aluminum oxide, glass beads, and plastic media and a miniature nozzle to produce a controllable abrasive jet that can target and remove microns of material. Micro-abrasive blasting is used for high-value precision parts.
A variety of abrasive media types are available on the market, including ceramic, steel, plastic, and organic compounds. These materials come in various shapes and sizes to accommodate different part geometries. In addition to scratching and cutting, the deburring media also serves as a cushion, preventing the parts from impacting each other.
Ceramics are suitable for deburring various metals and plastics. Their composition, density, and geometry affect the surface finish and cutting speed. Due to their inherent hardness, ceramics are particularly durable and effective for deburring hard metals.
Steel media are employed for light deburring and burnishing. Despite their high initial cost, they are widely used due to their minimal attrition rate and exceptional cleanliness.
Synthetic abrasives consist of 50 to 70% abrasive material by weight, which can include alumina, emery, and silicon carbide. These abrasives are embedded within a softer matrix. As the softer material wears away, the abrasive particles are exposed and perform the deburring of the part.
Plastics can be formulated for specific applications and come in different densities. Low-density plastics are used for general-purpose deburring, while high-density plastics are designed for deburring both ferrous and non-ferrous metals.
Examples of these are walnut and corn cob. Organic media are used for drying purposes since they can easily absorb water and oil.
There is a wide range of deburring tools available, from basic hand tools like files and chisels to more complex equipment such as grinders, saws, and countersink tools. Essentially, there is a deburring tool suitable for every situation. The purpose of deburring is to remove unwanted fragments and imperfections from a finished part or component, resulting in a smooth and even surface. This process is a crucial final step in manufacturing.
Although deburring might seem like a straightforward task of removing small metal fragments, each edge and surface is unique and requires a specific deburring tool. The variety of deburring tools is extensive, encompassing both common tools and more specialized, unique options.
Files – Of the many varieties of deburring tools, files are the most common. They are available in an array of sizes to precisely fit the types of material and edge design. Part of the selection process for files is the grit of the teeth since they come with varying aggressive grits. For the deburring process, it is advised to use a file with fine and double cut teeth.
The shape of a file makes it possible to smooth and shape a straight flat surface. Files are rough tools and incapable of precision or delicate work but have the ability to work rapidly to remove unwanted materials. Swiss patterned files have exceptionally fine teeth and are made using CNC machining.
Hand Deburring Tools – Hand deburring tools, also referred to as burr whips, are a form of small power tool that has different detachable blades that are available in differing sizes, materials, and shapes. They can be used on flat surfaces and internal curves but are not designed for round curved surfaces. Hand deburring tools can deburr drills, slots, and edges with rotatable blades that adapt to the contour of the surface of the workpiece. They have different hand grips, blade holders, and are simple to operate.
Countersink Tools – As the name implies, countersink tools are designed to deburr the edges of drilled holes that may have fragments, particles, or chips left from the countersinking process. Deburring a countersink hole can be completed by hand or by using a power tool attachment, as seen in the image below. Countersink tools are ideal for smoothing holes in steel and aluminum.
Wheel Grinders – Wheel grinders are a very aggressive method for deburring and have to be used carefully. They are designed for heavy duty deburring of heavy materials. Wheel grinders come with a variety of grinding wheels from very fine to high grit for rough cutting. The use of a wheel grinder requires precision control of the grinding process with appropriate contact force.
Finishing machines are machines used for metal finishing, which is the last stage of the metal fabrication process; the stage encompasses the use of machines in finishing the metal surface...
A tumbling machine is a durable deburring and metal-polishing machine designed for finishing large parts or batches of smaller parts. A tumbling machine is also known as a barreling machine or a mass-finishing...
Vibratory tumbler is the equipment used in a vibratory finishing process, one of the most common methods in mass finishing. But how does a vibratory tumbler work...
Industries worldwide utilize abrasive blasting for various purposes, including cleaning rust and oil, removing surface coatings like paint and pollutants, preparing surfaces for paint and coatings, reinforcing metal surfaces and...
An aqueous part washer is an automated or semi-automated machine manufactured to clean, remove tough grease, and dry large or small parts before distribution or surface treatment. The washing is necessary since...
Automated parts washers are mechanical devices designed to efficiently remove grit, oil, grime, dirt, paint and other contaminating substances from parts with minimum manual supervision. These substances are removed...
A parts cleaner is a cleaning device that uses various types of solvents, cleaning agents, and processes to remove grease, grime, and contaminating materials from manufactured parts prior to shipment or movement for further processing...
A parts washer is a mechanical device designed to remove grit, grime, oil, miscellaneous debris, dirt, paint, and other contaminating substances from parts in preparation for their use in assembly operations, packaging, or coating...
Sandblast cabinets include systems or machinery and components for projecting blast media against a part‘s surface to abrade, clean, or modify the surface. Sand, abrasive, metal shot, and other blast media are driven or propelled using pressurized water, compressed air, or a blast wheel...
Sandblasting equipment includes systems or machinery, and components for projecting blast media against a part‘s surface to abrade, clean, or modify the surface. Sand, abrasive, metal shot, and other blast media are driven or propelled using pressurized water, compressed air, or a blast wheel...
Shot peening equipment includes systems or machinery and components for projecting shot peening media against a part‘s surface to modify the surface or surface engineer the part...
An ultrasonic cleaner is a type of sonic cleaner or sonic cleaning machine that uses cavitation to remove unwanted material. The cleaning effect is created by the compression and refraction of a cleaning medium. Miniscule vibrations propagate throughout the...
Ultrasonic cleaning is a type of cleaning process which uses cavitation induced by alternating compression and rarefaction cycles at ultrasonic frequencies. Ultrasonic frequencies are sound waves vibrating at 20 kHz or higher...
A wastewater evaporator is a method of removing water from water-based waste by converting the water in the waste to a vapor and leaving contaminants. The function of a wastewater evaporator is to reduce the volume of waste materials...
Parts washers are designed for cleaning, degreasing of equipment, and drying of mass quantities of small or large parts in preparation for surface treatment, assembly, inspection, or shipment...