Plastic Caps and Plugs
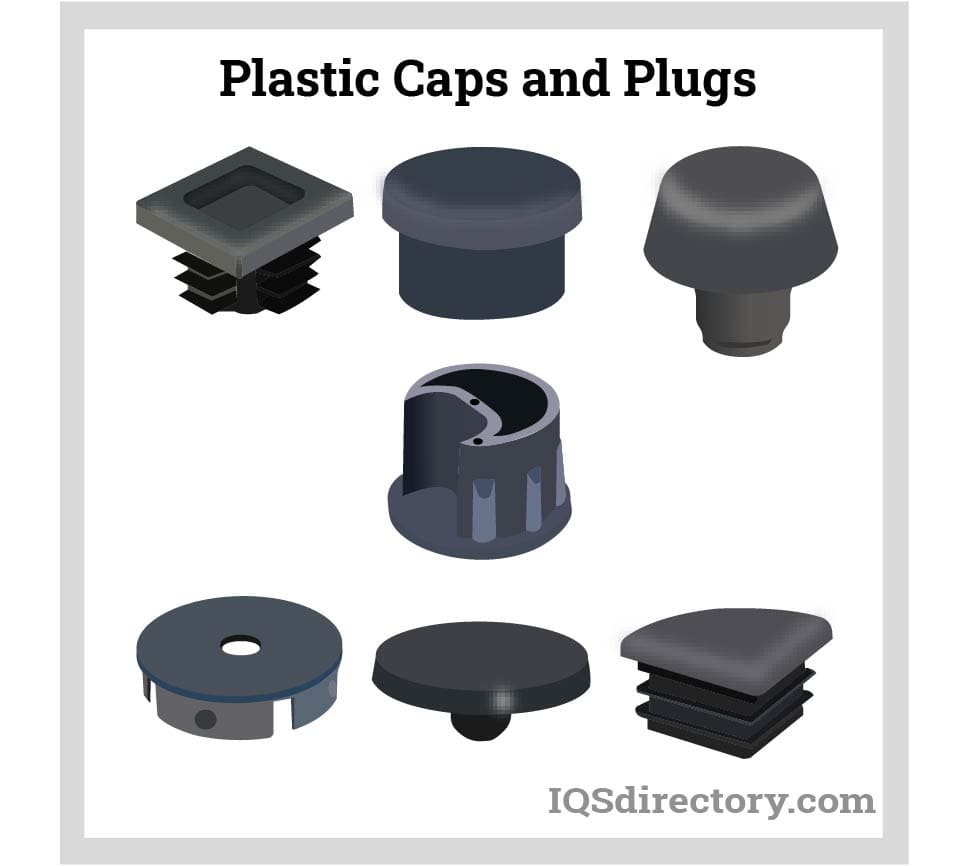
Plastic caps and plugs are two distinct ways for sealing the ends, tops, and openings of tubes and containers. Caps are placed over the opening, and plugs are placed in the opening. Due to the many varieties of...
Please fill out the following form to submit a Request for Quote to any of the following companies listed on Plastic Coating .
Information about plastic coatings and dip molding with a list of leading manufacturers.
Plastic coating involves the application of liquid polymers or plastics onto a component using methods such as dipping or immersion. This technique forms a strong plastic layer that provides both protection and visual appeal. It significantly enhances the material's resilience against scratches, abrasions, corrosion, and environmental wear. By reinforcing metal parts, plastic coatings extend their operational life. Furthermore, these coatings deliver practical advantages like enhanced grip and user insulation.
Plastic coatings are prevalent on hand tools, grips, and handles. As an example, pliers typically come with plastic-coated handles that elevate user convenience and improve handling by making the tool more comfortable to use and durable. This type of coating also benefits a multitude of other products by offering extra strength and protection, such as shopping carts, baskets, forceps, covers, caps, plugs, and numerous other items.
Plastic coatings serve effectively as thermal and electrical insulators. They are often applied to hand tools like tongs and spatulas to ensure safety when dealing with hot objects. These coatings are also essential in the electronics sector, insulating components like wires, cables, and digital meter probes.
The method of attaching a plastic coating to an existing metal item is referred to as dip molding. During this process, the metal component acts as a mold for the polymer. The component is initially treated and warmed before being submerged in a liquid polymer. The polymer adheres to the metal and solidifies as it cools, resulting in a durable plastic layer.
Dip molding resembles dip coating but includes an added phase for extracting the molded part. This approach produces single, hollow, and double-walled components, reducing the requirement for additional processes like trimming or deflashing. By limiting these subsequent stages, dip molding conserves materials. Examples of dip molded goods include latex gloves, accessories, cups, plastic caps, and components used in sports equipment.
Common polymers used for coating include plastisol, latex, neoprene, polyurethane, and epoxy. An important feature of these polymers is that they should be available in a liquid state at room temperature without requiring extra preparation. Additionally, for effective dip coating and dip molding, the liquid polymer needs to have a sufficient viscosity to prevent it from dripping off the mold surface. This ensures that the polymer stays in place until it sets and cures.
Plastisol is a widely used polymer in both dip molding and dip coating. It consists of finely ground polyvinyl chloride (PVC) resins suspended in a liquid plasticizer. Upon heating, plastisol transforms into a soft, flexible material with a rubber-like texture as it cools. Known for its durability, resistance to corrosion, and impact strength, plastisol is also valued for its high dielectric properties, making it ideal for electrical applications. To achieve desired finishes, colorants can be incorporated into the plastisol.
Latex is a dispersion of tiny polymer particles, with a significant portion consisting of rubber. It serves as a foundational material for producing both natural and synthetic rubber. While this polymer is widely accessible and safe for most users, there are concerns about allergic reactions that can arise when the latex degrades into a powdered form, which has led to a decrease in its popularity among some users.
Neoprene, created through the polymerization of chloroprene, serves as an alternative to latex. It is recognized for its resistance to chemicals and its flexible properties.
Polyurethane consists of urethane groups connected through carbamate linkages. It is celebrated for its flexibility and exceptional resistance to deformation.
Epoxy is a thermosetting polymer that, once its molecular chains are cross-linked, creates coatings with high strength, and resistance to chemicals and heat.
As discussed earlier, dip coating and dip molding share a similar operational principle. This chapter will explore the procedures involved in both processes.
Pre-treatment is essential for effectively applying plastic coatings to metal substrates. These steps are crucial for ensuring proper adhesion in both dip coating and dip molding processes.
In dip coating, pre-treatment is more intricate compared to dip molding because the polymer must permanently adhere to the metal, which serves as the mold. The pre-treatment procedure includes the following steps:
Impurities can hinder the polymer’s ability to bond with the mold or part, creating weak spots where damage may begin and spread.
Oils and greases on the metal substrate surface can act as contaminants, reducing water resistance and hindering the proper adhesion and application of the plastic coating. These contaminants are typically removed through alkali or acidic washes, or by thermal degreasing.
When re-coating parts that have already been coated, it is essential to completely remove the existing layer before applying a new one.
In addition to cleaning the surface, various properties can be added to achieve specific desirable traits. These enhancements may benefit both the dip coating process and the final application of the product.
Phosphating, also known as phosphate conversion, involves applying a thin layer of phosphate before applying the plastic coating. This phosphate layer enhances the substrate's corrosion resistance, particularly in situations where the plastic coating may be damaged. Common types of phosphate layers used in dip coating include zinc phosphate, iron phosphate, and tricationic phosphate.
Shot peening involves bombarding a surface with spherical particles to induce cold working. This process creates compressive residual stress on the substrate's surface, which helps to strengthen it and alleviate any pre-existing residual stress. Such stress can lead to microcracks, which may be exacerbated by subsequent processes.
Blasting alters the substrate surface by creating tiny cavities, which enhances the surface area available for adhesion of primers, undercoats, and plastic coatings. Common blasting techniques include sandblasting, metal grit blasting, glass bead blasting, and plastic bead blasting.
De-embrittlement is a heat treatment process designed to eliminate hydrogen that has diffused into the metal substrate, reducing the risk of brittle fractures under stress. This hydrogen often comes from previous pre-treatment steps, such as acidic washes and phosphate applications.
The following treatments are applied to the substrate surface to enhance the quality of the coating:
Primers act as a preparatory layer that enhances adhesion between the substrate and the plastic coating. They also provide extra protection to the substrate being coated.
Undercoats are additional layers that impart specific properties to the final product, such as UV and scratch resistance. Typically, undercoats are not used independently but function effectively when combined with the primary plastic coating.
In the dip molding process, a mold release agent is applied to the mold's surface to facilitate the removal of the molded part. Common mold release agents include silicone and permanent polytetrafluoroethylene (PTFE).
After completing the pre-treatment steps, the mold is dried to eliminate any moisture. Retained moisture can lead to expansion when exposed to heat during subsequent steps, causing the formation of voids or bubbles in the finished product.
The mold is heated in an oven to a specific temperature for a set duration. The heating temperature is a key factor in determining the coating thickness of the part. The effectiveness of heat distribution is influenced by the mold's design and the airflow within the oven. Uniform heating is crucial to ensure an even coating thickness throughout the material.
The heated mold is either partially or fully dipped into the liquid polymer, allowing the polymer to adhere to its surface. The outer dimensions of the mold define the internal shape of the part. The dwell time, or the length of time the mold remains submerged in the liquid polymer, is a crucial factor in determining the final coating thickness. Longer immersion times result in thicker coatings.
The speed at which the mold is immersed and withdrawn from the liquid polymer is another crucial factor, influenced by the properties of the polymer used. These rates are optimized by manufacturers during the process development phase. Generally, these movements should be slow to regulate the flow of the polymer and achieve a smooth finish. Rapid withdrawal after the dwell time can cause surface irregularities, while overly slow immersion and withdrawal can result in an excessively thick coating.
Some advanced facilities use a fluidized bed of fine polymer powder as an alternative to traditional liquid polymer solutions. In this method, the process is similar to conventional techniques: the fine powder melts and bonds to the heated mold surface upon contact.
Any excess liquid polymer is allowed to drain off the mold's surface. To achieve a thicker coating, multiple dipping cycles may be used, or a specialized coating may be applied.
The coating is cured in an oven to set the polymer more thoroughly and completely evaporate the excess moisture, solvents, and additives. In this step, the final mechanical properties of the polymer such as rigidity and flexibility are acquired. In thermosetting polymers, the curing step allows the polymeric chains to become completely cross-linked.
The cured coating is cooled either by immersing the mold in a water tank with temperatures ranging from 122 to 1112°F (50 to 600°C) or by using forced or natural air convection. The cooling rate is generally less critical compared to other molding processes.
Once the coating is cured, the finished parts are taken out of the frame. For dip molding operations, the plastic-coated part is separated from the mold either manually or using mechanical methods. This process yields a finished plastic component or part.
The dip molded plastic or the plastic coating may undergo additional finishing steps such as notching, punching, printing, and decorating.
Dip coating and dip molding processes share similar machinery. In a dip coating or dip molding operation, several machines and components are used to produce dip molded plastic.
Dip molding is an alternative to traditional molding. Parts are seamless and made using inexpensive tooling, which makes the process ideal for cost effective prototyping. The process for dip molding is similar to candle making. A heated metal mold is dipped into a tank of liquid material, which can be a form of plastic or rubber.
The material in the tank may be completely melted or be at ambient temperature. The mold remains in the dipping tank for varying times depending on the required thickness of the molded product. Once a sufficient amount of time has passed, the molded product is removed from the tank, cured, and stripped from the mold.
As with the manufacture of candles, the metal mold for dip molding may be dipped several times to increase the number of layers of the molded product. In addition, the mold may be dipped in different materials to create varying effects. Handles for tools may be dipped in a hard plastic to create a tight fit and durability. They may then be dipped in a softer material to form a comfortable grip.
Unlike dip coating, where the material remains attached, dip molded products are demolded during the final step of the molding process. Dip molding produces single wall, hollow, and double wall products, which eliminates the need for trimming and deburring. Gloves, clothing, cups, lids, and equipment and parts are produced using dip molding.
The dip molding process includes the use of:
A key factor in regard to dip molding is following the steps of the process to ensure the quality of the final molded product. Each step, from dipping to finishing, is adhered to such that the desired shape is achieved.
Finishing - As with the design of all dipped molded products, finishing improves the appearance of a product and involves the use of different processes that can include coatings and washing, each of which makes it easier to work with a product.
Rotary-type configuration - Several mechanical arms equipped with carrier frames are mounted on a rotating wheel, similar to a carousel. As the wheel turns, each arm is indexed to dip the mandrels into different depths of the solution.
The dip molding process is restricted to plastics or rubbers that form well around the mandrel under high temperatures. The most commonly used dip molding material is polyvinyl chloride (PVC), due to its affordability and ease of use. Other types of materials are various thermoplastics including polythene, polypropylene, polystyrene, polyamide and polycarbonate. Also available are natural latex rubber, neoprene, nitrile (Buna-n), and silicone, which are processed in a similar manner as plastics but require different types of curing and heating treatments.
Dip molding manufacturers provide their customers with an array of material choices for the forming of their products. Although plastic is a popular choice, various forms of rubber are ideal and provide highly durable and flexible products.
The choice of a polymer for the dip molding process involves ones that are available in liquid form without the need for additional processing. Polymers considered have sufficient viscosity to prevent run off.
Although the materials listed above are commonly used for dip molding, there is a long list of varying materials used for the process. Each type of material requires some form of accommodation in order to be adapted to dip molding.
Plastic coating machines play a crucial role in modern industries by applying protective, insulating, or decorative plastic layers to a variety of products. This enhances their durability, functionality, and appearance across sectors such as manufacturing, construction, automotive, and electronics. Below, we explore several top brands of plastic coating machines available in the United States and Canada, highlighting specific models and their distinctive features, functions, and capabilities:
Features: The Nordson Encore LT is a manual powder coating system engineered for precision and efficiency in plastic coating. Its user-friendly operation and control make it ideal for small to medium-sized applications. The system utilizes advanced electrostatic technology to ensure a consistent, high-quality finish and includes a lightweight, ergonomic gun design for ease of use. The Encore LT also supports rapid color changes and promotes effective powder utilization.
Features: The WAGNER PEM-X1 is a manual liquid coating system known for its precision and dependability in plastic coating applications. It provides adjustable coating parameters to accommodate a range of needs. The system is equipped with advanced atomization technology for a smooth and consistent coating distribution. Its user-friendly control panel offers intuitive settings and monitoring options. The PEM-X1 also facilitates quick material changes and simplifies maintenance.
Features: The Reliant Finishing Systems PC601 is a conveyorized powder coating system tailored for high-volume applications. It provides a continuous coating process with efficient use of materials. The system boasts a sturdy conveyor for smooth and consistent movement of parts and employs advanced powder application technology for even and durable coatings. Additionally, the PC601 features automated controls and customizable options to maximize productivity.
Features: Graco provides a range of electrostatic liquid coating systems designed for plastic coating tasks. These systems deliver efficient, high-quality finishes with excellent transfer efficiency. They incorporate advanced electrostatic technology to ensure even coverage and minimize overspray. Users benefit from precise control over coating parameters such as flow rate and atomization. Graco's electrostatic liquid coating systems are recognized for their reliability, durability, and user-friendly operation.
Features: The Dymax UVC-6 is a conveyor system engineered for UV-curable plastic coating applications. It provides precise control over UV exposure and curing times, ensuring effective coating performance. The system includes multiple lamp heads to guarantee even and complete curing. It also features adjustable conveyor speed and height for added flexibility and customization. The UVC-6 is compatible with other Dymax equipment and offers user-friendly controls.
Note that model availability and features may change over time. For the most current information on models that meet your needs, please contact the manufacturers or their authorized distributors.
Dip coating and dip molding offer several advantages to manufacturers, thanks to their straightforward concepts and versatile applications. Here are some key benefits of using these methods:
These processes do not result in shrinkage, allowing for precise achievement of the desired internal dimensions. Additionally, unlike other molding methods, the cooling rate is less critical and does not require stringent control.
Dip coating and dip molding effectively create seamless, double-walled components. Unlike parts joined from multiple pieces, which can have stress points at the seams that compromise durability, these methods ensure a continuous and robust construction.
Dip plastic casting allows for the production of large plastic components by encapsulating sizable metal pieces through dip molding. Producing similar large plastic parts using injection or blow molding would necessitate large tooling and become a costly process. The primary constraints of dip molding are the dimensions of the tool, the capacity of the pre-heat and curing ovens, and the size of the polymer solution tank.
Additionally, dip coating and dip molding are capable of creating intricate designs with severe undercuts and angles.
Designers can easily add extra details to the final product, as the tooling material can be readily modified. Additionally, different coating materials and thicknesses can be achieved using the same tooling by adjusting the formulation of the polymer solution.
Dip coating and dip molding are well-suited for short runs and laboratory-scale production due to their straightforward equipment requirements. Unlike injection and blow molding, which necessitate complex machinery and extensive floor space, these processes involve simpler setups. Additionally, the tooling for dip molding is cost-effective as it does not require high pressures to operate.
In dip coating and dip molding, excess solution drains back into the dipping tank, making it possible to reuse it. This is in contrast to other molding methods, where excess polymer material often results in cut-outs and runners that need additional processing for recycling. Dip coating also offers advantages over spray coating, as some of the spray material typically ends up on the walls of the coating chamber or equipment, leading to waste.
However, there are limitations to these processes where other molding methods may offer advantages. The following are some of the disadvantages:
While the internal dimensions achieved with dip coating and dip molding are precise, obtaining an exact coating thickness can be challenging. This is because it depends on various factors, including dwell time, tooling temperature, immersion rate, withdrawal speed from the polymer solution, and the properties of the polymer solution itself. These variables can also make it difficult to achieve uniform coating thickness distribution.
Dip molding is a time-consuming process due to the extended heating, dipping, and cooling cycles required.
Plastic coatings have become an integral part of manufacturing, used to enhance the appearance and functionality of cars, tools, appliances, sports equipment, and handrails. Their adaptability and versatility make plastic coatings a valuable addition to a wide range of products. In today’s market, plastic coatings are essential for ensuring the longevity and durability of both commercial and industrial items.
The demand for plastic coatings can be summed up in three key attributes: longevity, durability, and safety. Modern producers are continually seeking methods to extend product life while ensuring safety and reliability. These critical factors drive the development of new products, influencing every
Years ago, customers expected that new products would eventually need replacement, a principle that manufacturers relied on to sustain their market share. However, with technological advancements and the increasing complexity and cost of products, consumer expectations have shifted towards durability and long-term performance. In response, manufacturers have developed techniques to extend the lifespan of their products.
As component design and capabilities have advanced, a range of exceptionally strong plastic polymers has been developed to suit the needs of modern devices. These polymers contribute significantly to the longevity of electronics, such as televisions and computers, by providing unmatched durability under challenging conditions. When used as coatings, these polymers create a protective layer around commercial and industrial tools, enhancing their durability and extending their useful life.
In both commercial and residential settings, protective coatings are essential to prevent injuries from uncovered corners or exposed edges. In industrial environments, where tools can be complex and hazardous, plastic coatings play a crucial role in safeguarding workers from dangerous materials and equipment. Plastic-coated safety walls, gates, and enclosures act as shields, providing crucial protection and reducing the risk of harm.
Moreover, plastic-coated tools offer several benefits when used with moving parts, electrical circuits, and controls. Ensuring worker safety is a core principle of modern manufacturing, and plastic coatings contribute significantly to this goal by enhancing the safety and functionality of tools and equipment.
Vibrations are an inherent byproduct of operating heavy machinery and industrial equipment. To ensure the longevity of their products, facilities work diligently to minimize and manage these vibrations. A key component of this effort involves using plastic coatings, which help to prevent direct contact between machinery parts and reduce overall vibration.
Despite numerous efforts to reduce noise in production environments, it remains a significant aspect of manufacturing due to the high forces involved in producing large quantities of products. In addition to addressing vibrations, plastic coatings are also employed to mitigate noise. They are used in various applications such as separators, gaskets, shields, controls, and enclosures to help dampen and control sound levels.
Reducing friction in industrial processes enhances efficiency and ensures smoother operation across various production tasks. Friction can cause equipment wear, abrasions, and electromagnetic interference (EMIs), all of which can be detrimental to machinery. Applying plastic coatings to different components significantly lowers friction, thereby improving safety and boosting productivity.
Modern industrial machinery often includes insulation to safeguard both workers and products. Plastic coatings are commonly used due to their durability, ease of application, and long-lasting performance. These coatings help to reduce electromagnetic fields (EMFs), prevent direct contact between metal components, and ensure the smooth operation of equipment.
Applying protective plastic coatings provides additional protection and value to industrial processes. This investment helps reduce wear, damage, and the need for frequent replacement of critical machinery, while also significantly enhancing worker safety.
Plastic caps and plugs are two distinct ways for sealing the ends, tops, and openings of tubes and containers. Caps are placed over the opening, and plugs are placed in the opening. Due to the many varieties of...
Blow molding is a type of plastic forming process for creating hollow plastic products made from thermoplastic materials. The process involves heating and inflating a plastic tube known as a parison or preform. The parison is placed between two dies that contain the desired shape of the product...
Industrial coatings are a type of substance that is spread over a surface of various derivatives like concrete or steel. They are engineered chemically to give protection over industrial products that include pipelines and...
Plastic bottles are bottles made of high or low-density plastic, such as polyethylene terephthalate (PET), polyethylene (PE), polypropylene (PP), polycarbonate (PC), or polyvinyl chloride (PVC). Each of the materials mentioned has...
Reaction injection molding or RIM molding is a molding process that involves the use of two chemical elements with high reactivity and low molecular mass that collide and mix before being injected into a closed mold. High pressure pumps circulate isocyanate and...
Thermoforming is the process of heating thin plastic sheets to its forming temperature and stretching it over a mold which takes its shape. After cooling and setting of the molded plastic sheet, each part will be separated from its batch to form a single unit or product...