Air Dryers
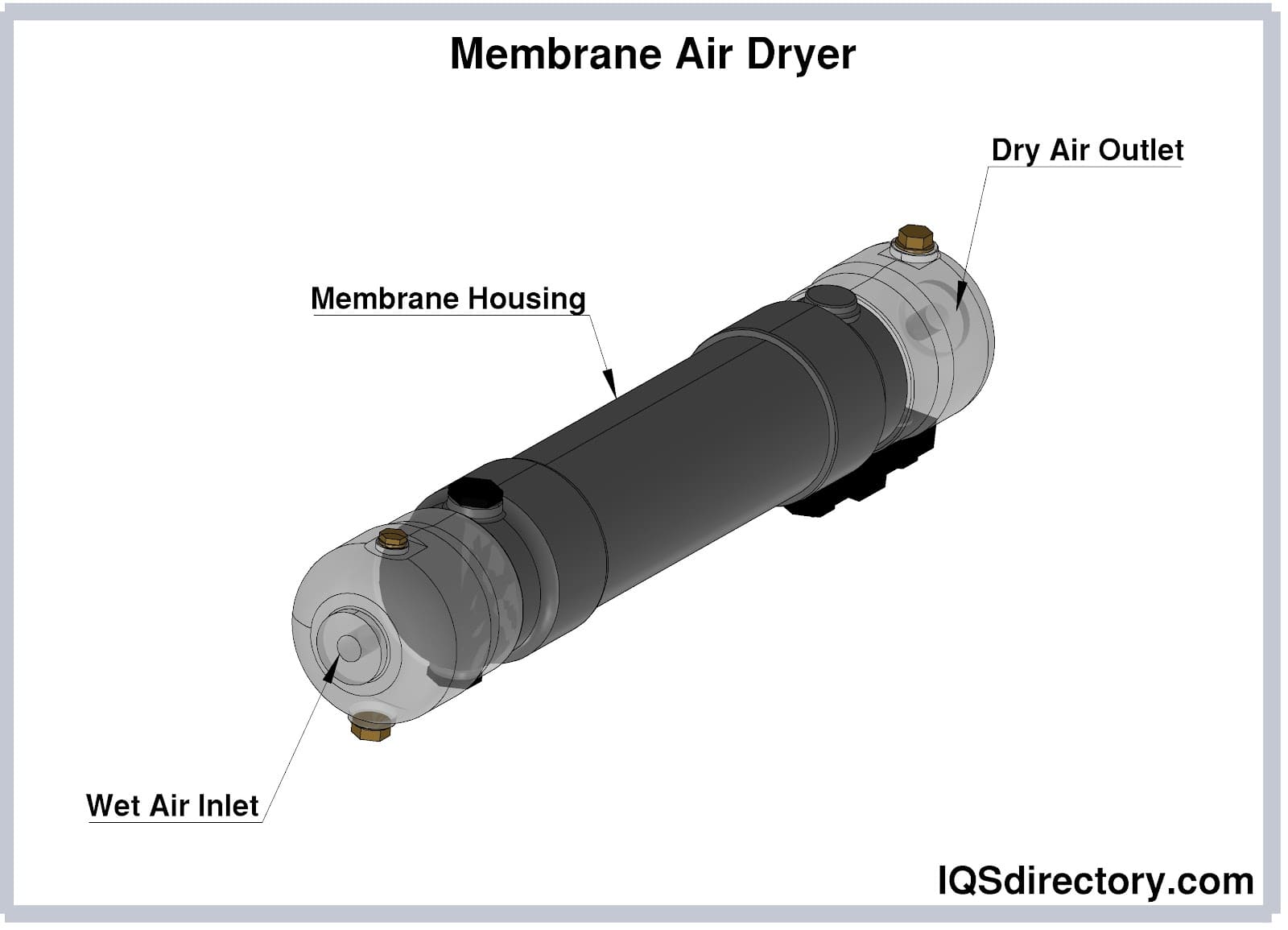
An air dryer is a system or piece of equipment that is used to remove moisture present in the air, particularly compressed air. Ambient air typically has a relative humidity of around 30 to 50%. Compressing air packs higher...
Please fill out the following form to submit a Request for Quote to any of the following companies listed on
This article takes an in-depth look at types of industrial dryers.
Read further and learn more about topics such as:
Industrial dryers are sophisticated, heavy-duty machines engineered to remove moisture from diverse items such as machinery, raw materials, and foodstuffs. These efficient dryers are designed to process large volumes, providing precision control and durability essential for rigorous industrial use.
The term "industrial dryer" encompasses a wide range of drying machines, each employing its own unique operational mechanism. Generally, industrial dryers are tailored to fit specific products or manufacturing processes. Among these are freeze dryers, chemical drying systems, air bar dryers, continuous tray dryers, oven dryers, and pan dryers.
Drying is the process of reducing moisture in wet materials by vaporizing it. This process involves both heat and mass transfer operations. Essentially, heat is applied to the material, which causes the moisture to evaporate. The evaporated moisture is then carried away with air or an inert gas.
As the drying process continues, the moisture content in the surrounding air rises. Though the weight of the material decreases, its dry weight remains unchanged. The drying process is crucial for several reasons, including:
Industrial dryers have applications across multiple sectors, including food production, pharmaceuticals, agriculture, sugar manufacturing, pulp and paper, textiles, woodworking, metallurgy, metal fabrication, and automotive industries.
Various types of dryers mainly differ in their methodology for moisture extraction, as well as their dimensions and capacities. Small-scale industrial dryers, typically utilized in research and development settings, are capable of removing minimal moisture amounts. Meanwhile, large-scale industrial dryers can manage tons of wet material per hour.
Given the vast selection of industrial dryers, choosing the appropriate one with the correct type, dimensions, and features for a specific use demands careful planning and evaluation. Each dryer type offers distinct functionalities that can impact the quality and productivity of the finished product.
In conductive heat transfer, materials are dried by heating them through a surface, object, or surrounding jacket. In contrast, convective heat transfer involves direct drying without the need for surfaces or coils. These processes are categorized as direct or indirect, with conductive heating being indirect and convective heating being direct.
Direct dryers use convection to transfer heat to the material being dried. In this method, the heat transfer medium makes direct contact with the material. Typically, hot air or an inert gas is used as the medium, which is circulated around and through the material. This hot air provides the latent heat needed to vaporize the absorbed moisture, which is then carried away by the air stream.
Direct and continuous dryers are widely used in industrial settings due to their high efficiency. They generally offer better heat transfer efficiency than indirect dryers. Nonetheless, these dryers tend to have higher operating costs and may experience greater energy losses.
Direct drying is further optimized by using lifting flights, which move the material through and over the stream of drying gases. These flights enhance heat transfer and significantly improve the overall efficiency of the drying process.
Air dryers are engineered to eliminate moisture from ambient air, particularly from compressed air systems. Ambient air typically contains 30% to 50% moisture. When air is compressed, its moisture content can rise to 100%. Excessive moisture in manufacturing environments can harm sensitive equipment and machinery, potentially causing process contamination, early equipment failure, wear, and corrosion. Therefore, removing this moisture is crucial.
An air dryer extracts moisture and impurities from ambient air, contributing to a cleaner and safer work environment. In areas with high humidity, air dryers are essential for maintaining continuous operations and avoiding downtime. Various methods are employed to dry the air, including adjusting temperature, increasing air pressure, and compressing the air substantially.
One air drying technique involves cooling the air and then reheating it. During the cooling phase, moisture condenses and is removed, resulting in drier air. Another approach uses absorbent materials to capture and remove moisture. A more expensive method entails compressing the air, cooling it to condense and remove moisture, and then returning the air to its original pressure.
Moisture build up is a natural result of filtering and compression processes, which cannot be prevented. The removal of the accumulated moisture is a necessity to avoid damage to the various processes. Air drying requires the selection of the best method for the application where the moisture is collecting. Air dryer manufacturers provide guidance and tools to safely and efficiently complete the process.
Conveyor dryers are a type of continuous drying system that transports products through multiple drying stages within a production or storage setup. Products travel on a conveyor belt through controlled hot air zones that regulate both accuracy and temperature. The conveyor belt, often made of mesh or web material, facilitates the flow of warm air either upward or downward onto the drying products. Typically, a conveyor dryer is designed to be around 60 feet in length and includes three or
Some conveyor dryer designs incorporate multiple passes, where products transition from one belt to another using gravity. The number of passes, which can range from two to three, depends on the specific product being dried. Multiple-pass conveyor dryers are often used in applications such as vegetable dehydration.
In a conveyor dryer, the heated air is precisely regulated for air velocity, temperature, and humidity. Multiple drying zones ensure that products are dried gently at a consistent feed rate and controlled temperatures. Turbine fans or nozzles direct heated air onto the products to accelerate the drying process, ensuring thorough moisture removal. Conveyor dryers are versatile and can handle materials of any viscosity.
The two key factors regarding food dryers are their ability to accurately control the temperature of the drying process, to avoid damaging the product, and the use of pure heat energy to avoid polluting the environment. All food dryers are designed with a stable heat source, powerful circulating fans, heat preservation, and efficient energy use of at least 90%.
Two popular types of food dryers are multi-layer mesh belt continuous dryers and heat pump dryers. The multi-layer mesh belt dryer utilizes heat and airflow to accelerate drying, making it suitable for processing large volumes of food products. Its belt, made from strip pellet material, ensures better ventilation, which is beneficial for items that cannot withstand continuous high temperatures.
Heat pump food dryers offer a rapid, automated drying process suitable for seafood, bacon, fruits, tobacco leaves, and paper. These dryers use forced ventilation combined with steam or electrical heat to ensure uniform drying. Proper temperature control is crucial to prevent microbial growth and avoid damaging the food products. In a heat pump dryer, food is placed on evenly spaced trays to ensure consistent exposure to heat throughout the drying process.
Rolling bed dryers, referred to by the German acronym WB-T, are specifically designed for drying large volumes of biomass. These dryers integrate bulk material flow with heat transfer and continuous motion to ensure effective drying. The system features a long, cylindrical drum that rotates around its vertical axis. Biomass is loaded into the drum and moves continuously through the cylinder. This constant rotation ensures that the material is evenly dried efficiently and cost-effectively.
Rolling bed dryers merge the benefits of drum and fluidized bed dryers to gently dry products at low temperatures. They offer an energy-efficient and uniform drying solution, particularly for biomass materials. These dryers are designed compactly to enhance heat exchange, minimize exhaust temperatures, and reduce heat loss. The airflow velocity is adjusted based on the drying requirements of the material. Additionally, rolling bed dryers utilize low-temperature exhaust air to optimize the drying process.
In contrast to more complex industrial dryers, rolling bed dryers feature a straightforward and efficient design, making them easy to operate. Their perforated bed facilitates airflow over the material. The drying process takes place primarily in the initial stage of the cylinder, with cooling occurring in the subsequent stages. Rapid drying is achieved through direct contact between the material and the heated air blown into the system.
Indirect dryers use conduction to transfer heat to the material. In this method, a conductive partition separates the heat transfer medium from the material. The material is placed inside a drying chamber and heated through the chamber walls. The latent heat needed to vaporize the absorbed moisture is conducted through these walls. The evaporated moisture is then removed by the surrounding air. Compared to direct dryers, indirect dryers require much less carrier air.
Indirect dryers are ideal for drying sensitive items like pharmaceuticals and combustible materials due to their low airflow, which reduces the risk of contamination. They are also suitable for batch drying processes with relatively low production volumes.
In direct drying, the process environment is tightly sealed and controlled, which is particularly beneficial when handling potentially combustible materials. The fuel used for drying does not come into direct contact with the materials, preventing any contamination of the dried products with the fuel.
In indirect dryers, the fuel used for drying is kept separate from the materials being dried, so there is no need for lifting flights or circulating mechanisms. The exhaust from the furnace in indirect drying is also isolated from the drying materials and process gases, eliminating the need to treat the exiting gas.
Radiant dryers use electromagnetic waves to transfer heat directly to the material being dried. These waves carry thermal energy that penetrates deeply into the material, causing the moisture to evaporate as it heats up. The heat is efficiently absorbed by the material with minimal loss to the surrounding air, making the process contactless and reducing the risk of contamination.
Similar to indirect dryers, radiant dryers require minimal airflow and may only use a small blower. They are considered cleaner and more environmentally friendly compared to convective and conductive dryers. Radiant dryers are commonly used for drying adhesives, paints, and coatings applied to surfaces.
Categories of radiant dryers include:
Microwave dryers utilize electromagnetic waves in the microwave frequency range of 300 MHz to 300 GHz to penetrate the material beyond its surface. These waves interact with the material’s molecules, generating heat internally rather than relying on external hot air. Unlike traditional hot air dryers, microwave dryers convert energy directly into heat through molecular interactions, with the material effectively heating itself via dipole rotation.
Dipolar rotation occurs when electromagnetic waves from a microwave dryer align the material's molecules from their relaxed state. As the molecules repeatedly shift between alignment and relaxation at millions of cycles per second, this constant movement converts stored energy into thermal energy. This rapid conversion heats the material quickly, facilitating efficient drying.
A microwave dryer system includes a microwave generator, applicators or wave guides, a microwave unit, and a control system. Being a non-contact, heat-free drying method, microwave dryers are versatile and suitable for various applications, from paper products to pharmaceuticals. They are available in different configurations, ranging from standalone units to large conveyor systems, each tailored to specific drying requirements.
Infrared dryers utilize electromagnetic radiation with wavelengths longer than visible light, ranging from 0.78 µm to 1000 µm. This type of radiation transfers thermal energy from a warmer object to a cooler one. The surface of the material being dried absorbs heat when the infrared emission spectrum of the radiator aligns with the material's absorption characteristics.
Infrared dryers heat the surface of a material, with this heat gradually penetrating inward. They are similar to microwave and RF dryers in that they are specialized for specific material types. However, what sets infrared dryers apart is their method of generating heat directly on the material's surface.
Infrared dryers utilize advanced infrared radiators as their heat source, offering high efficiency, quick response times, uniform heating, and low energy consumption within a compact design. Unlike other drying methods that depend on heated air or water, infrared dryers use radiation from a hot element in an infrared lamp to lower the temperature of the substrate. They produce high power densities in small areas, which allows for rapid cooling due to the reduced thermal mass of the heating element.
The term batch dryer is a general descriptor that covers several versions of high volume dryers capable of efficiently drying large numbers of parts in one single cycle. Batch dryers can have conveyor systems where parts pass through on webbed belts that allow heated air to flow around the parts through the webs in the dryer. Other forms of batch dryers have a drying chamber with brackets to hold baskets of parts. It is form of dryer that is manually operated but has a control system that monitors the drying chamber.
Certain batch dryers feature drying zones where components move through a series of heated sections, allowing for gradual and even drying. These dryers are automated, enabling robotic systems to unload the parts, which sets them apart from other drying methods.
Batch dryers handle a set volume of material over a specified drying period. The amount processed is constrained by the dryer’s capacity, as it can only accommodate a limited quantity at one time. Once drying is complete, materials are either manually or automatically unloaded to prepare for the next batch. Batch dryers are suited for lower production volumes and include types such as tray dryers, drum dryers, and rotary dryers.
A continuous dryer is engineered to dry a steady stream of products, such as grains, finished parts, pharmaceuticals, or various food items. These dryers come in various configurations, including transport chains, carts, rotary pumps, and conveyor belts. The drying process involves moving materials through a chamber divided into different zones, each offering specific chemical and physical drying processes.
In a continuous dryer, the initial zone elevates the temperature of the material to facilitate the diffusion of moisture from around the product. As the material progresses through subsequent zones, moisture continues to diffuse from the product's surfaces into the air within the dryer. Throughout this process, the temperature in each zone is meticulously regulated to avoid any damage to the product or material.
Continuous dryers are highly efficient and do not require cooling down at the end of a drying cycle, leading to production savings as batches can be introduced without adjusting the dryer controls. These dryers are equipped with gas burners, temperature and moisture sensors, moisture outlets, recuperative burners, and a control panel with a steering system.
Continuous dryers offer several advantages that enhance business efficiency. They provide a high throughput rate, allowing for the processing of large volumes of material in a short period. The effectiveness of the process is reflected in the low moisture content of the final products, enabling immediate shipment of the dried goods.
The various types of industrial batch dryers include:
Tray dryers feature multiple trays stacked within a drying chamber, each holding the material to be dried. Air, which acts as the heat transfer medium, is circulated by blowers. This air absorbs thermal energy from heating coils and is directed over the material, facilitating the diffusion and evaporation of moisture. Some of the moisture-laden air exits through the ventilation duct, while the remainder, along with a fresh stream of dry air, is recirculated within the chamber. The air's temperature and velocity can be adjusted based on the specific product and operational needs.
Tray dryers are among the most basic industrial dryers, characterized by their low initial cost and compact size. They are straightforward to operate and maintain. However, they generally require a longer drying time and may not be ideal for powdered solids.
Vacuum dryers work under reduced pressure to accelerate the evaporation of moisture or solvents from the material. By lowering the operating pressure, the boiling point of the absorbed liquid is decreased, allowing these dryers to function at lower temperatures compared to other industrial dryers.
Materials are placed in trays within the dryer, which features a vacuum pump to lower the chamber pressure. Heat is transferred to the material via conduction or radiation from the chamber walls, and some vacuum dryers include a steam jacket. The vacuum pump removes the vapor, which can be condensed and recovered for reuse if needed.
Vacuum dryers are ideal for processing heat-sensitive, hygroscopic, combustible, and granular materials. They are commonly used in the food and pharmaceutical industries to preserve nutrients by avoiding high temperatures. These dryers effectively remove significant amounts of moisture and offer rapid drying times.
Pan dryers feature an agitator or mill that stirs wet materials within a jacketed vessel. The slow rotation of the agitator or mill enhances the drying rate—moisture removal per unit time and area—by promoting even heat distribution and preventing material from adhering to the vessel walls. These dryers can operate under atmospheric or vacuum pressure and are suitable for drying heat-sensitive, viscous, and sticky substances.
Pan dryers are designed to integrate multiple drying operations within a single unit without exposing or removing the product. This batch-style dryer allows for automatic loading of wet materials into the top cylinder jacket, where the agitator rotates to facilitate drying. Once the material is dried, it is expelled through a pneumatically operated door. The cylinder and chamber of a pan dryer are built to handle the required pressures and ensure compatibility with the products being processed.
Pan dryers are tailored to meet the specific requirements of the products they are designed to dry. Each unit is custom-built and tested to ensure it adheres to the standards needed for the particular product. Additionally, scale-up data and working capacity details are provided to ensure that the pan dryer meets client specifications and requirements.
Freeze-drying, or lyophilization, involves freezing the material and then applying a vacuum to remove moisture. This method is used for products that deteriorate or change significantly at high temperatures, as it helps preserve their biological activity and chemical properties. It's commonly employed in the food and pharmaceutical industries to maintain nutrient content and active ingredients, and is also used for biological specimens such as blood, tissues, and proteins. However, freeze-drying is a time-consuming process.
Freeze dryers consist of refrigeration equipment, a drying chamber, holding trays, and a vacuum pump. The sample is first frozen to at least its melting temperature to convert the moisture and solvent within the material into a solid phase. The vacuum pump is then activated to decrease the pressure inside the chamber. Heat transfer under low pressure causes the solidified moisture or solvent to transform into vapor. The vacuum pump draws the vapor sublimed off the material. The freeze dryer will continue to run to drive off the moisture or solvent bound to the material.
Bin dryers are a type of batch dryer featuring a large cylindrical or rectangular chamber with a wire mesh bottom. Air is drawn in through the bottom and then blown upwards through the mesh to dry the material. The walls of the bin dryer are securely sealed to prevent the escape of heated air. The dryer door, which allows fresh air to enter for heating, can be fully or partially opened to control the circulation of warm air within the chamber.
The bin, or holding tank, features a perforated bottom plate. Air is blown through a heater and circulated upward through the perforations, drying the product. Materials are placed on shelves, with the most moisture-laden and heaviest items at the bottom. As the air moves upward carrying moisture, it exits the dryer. Ducting ensures consistent air velocity and keeps fine particles suspended until they settle at the bottom and are removed. Bin dryers are commonly used for drying agricultural and forestry products like wood, fruits, vegetables, grains, and bamboo. They typically lack a control system and may serve as pre-dryers.
In tunnel dryers, materials are placed on trays that are mounted on trolleys. These trolleys enter the dryer at one end and gradually travel through the drying tunnel, where a stream of hot air or gas is circulated. As the trolleys move through the tunnel, the materials are dried. The trays can move in conjunction with or opposite to the direction of the air stream:
The heater zone settings and trolley speed can be adjusted to optimize the drying process based on the type and volume of materials being processed, as well as the desired final moisture or solvent content.
Tunnel dryers are an advanced version of tray dryers, offering continuous entry and exit of materials during operation. As materials remain stable on the trolley while moving through the tunnel, these dryers are ideal for items that are prone to damage or deformation, such as automotive components, electronic parts, construction materials, glass, and large fruits, vegetables, and food products. Tunnel dryers are particularly effective for processing materials that require extended drying periods.
Rotary dryers are composed of a slightly inclined metal drum equipped with internal flights. Material is introduced at the upper end of the drum, which rotates slowly to lift and cascade the product. Hot air or gas is introduced either concurrently or countercurrently with the flow of material. The combined effects of rotation and internal tumbling promote even and efficient drying. The dried material exits from the lower end of the drum.
Rotary dryers can be categorized into direct-fired and indirect-fired types. In direct-fired rotary dryers, the hot gas comes into direct contact with the material inside the drum, which can be useful for applications like roasting food products. Conversely, in indirect-fired rotary dryers, heat is transferred to the material through the drum's walls, avoiding direct contact between the heating medium and the material.
Rotary dryers are suitable for drying granular and non-sticky materials. They are commonly used in drying products from a crystallization process. They are suitable for drying salts, minerals, grains, nuts, and animal feeds.
In fluidized bed dryers, wet material is introduced into a vessel via a screw feeder. Preheated air is blown upwards from the bottom of the vessel, keeping the particles suspended or fluidized. This airflow is perpendicular to the direction of material movement, and a horizontal air stream may also assist in moving the particles. The extensive interaction between the particles and air accelerates the drying process. Moisture-laden air exits through the top of the vessel, with any particles carried away being captured by a cyclone separator or bag filter. The dried material is then collected at a lower point in the vessel.
Vibrating fluidized bed dryers incorporate vibration to improve the fluidization of larger particles as well as sticky or difficult-to-move feeds.
Fluidized bed dryers are utilized for drying powdered and granular materials like grains and cereals. Certain models are specifically designed for batch drying processes.
Vacuum drying is a popular drying technique known for its efficiency in processing products and materials. At the heart of a vacuum dryer is a sealed drying chamber connected to a vacuum system via a condenser. The chamber is enveloped by a jacket through which different heating methods are applied to enhance the drying process.
When wet material is introduced into the drying chamber, the vacuum system reduces the chamber's pressure while the heated jacket provides heat. This indirect heating method safeguards the product and enhances drying efficiency. As the material dries through evaporation, the resulting vapor is extracted via a vacuum stack or pulse filter to the condenser, where it is condensed back into liquid form. The liquid is then directed to a holding tank for either reuse or disposal.
In an agitated vacuum dryer, moisture removal depends on the vacuum level, the exposure of the material’s surface, and the heat transfer efficiency of the jacket. Optimizing these factors improves the dryer’s performance. Agitator vacuum dryers are particularly useful for drying products sensitive to heat and air, and they are often positioned adjacent to filtration equipment.
Spray drying rapidly and efficiently converts slurries, suspensions, or pastes into fine, dried powders. Typically, the feed has a high moisture content and needs to be pumpable. This method is commonly used to produce a variety of products, including soaps, detergents, milk, coffee, tea, salts, polymer resins, flavorings, extracts, and pharmaceuticals.
The spray drying process includes the following stages:
This stage involves transforming the feed into a fine mist of droplets to facilitate rapid drying. The feed is continuously pumped to an atomizer positioned at the top of the drying chamber. Various techniques can be used for atomizing the feed:
A hot gas stream is introduced into the drying vessel from either the top or the bottom. Air is typically used for drying solids in aqueous solutions, while nitrogen is used for organic or flammable solvents. The atomized feed disperses over the gas, which removes moisture or solvents. The vessel has a large diameter to avoid particle adhesion to the walls, and the particles eventually settle at the conical bottom of the vessel.
Drying occurs in just a few seconds, making spray dryers ideal for processing thermally sensitive products that can degrade if exposed to heat for extended periods.
Particles are separated from the drying gas using a cyclone separator and a filter.
In flash drying, wet material is introduced into a stream of hot air that propels it through a drying duct. The airstream’s heat dries the material during its passage, after which cyclones or bag filters separate the dried particles. Scrubbers are then employed to ensure the final cleaning meets emission standards.
Flash dryers remove moisture from wet granular materials through high-velocity gas streams that keep the particles suspended while heat evaporates the moisture or solvents. Cyclonic action then separates the material from the gas stream. To enhance energy efficiency, some of the exhaust gas is recirculated back into the system.
Flash drying is a continuous process that can use either direct or indirect heating, depending on its configuration. This method allows for rapid processing of materials, enabling them to be immediately packaged for shipment upon exiting the dryer. Flash drying can be adjusted to temperatures ranging from 340°F (170°C) for heat-sensitive materials up to 1100°F (600°C) for materials that can withstand high temperatures. The short residence time and moisture evaporation result in evaporative cooling, which allows for higher inlet temperatures without harming the product.
Drum dryers, also known as roller dryers, are used to dehydrate liquid feeds into powders, flakes, or granules. These dryers feature one or two heated drums that rotate around their axis. Steam circulates within the drum, and heat is transferred through its walls. The feed is applied to the rotating drum's surface or between two drums. The liquid forms a thin film that dries on the heated surface. The amount of time the product stays on the drum is influenced by its initial and final moisture levels. A scraper is used to remove the dried material once it reaches the desired dryness.
Vacuum drum dryers operate within a chamber under reduced pressure. The low pressure lowers the boiling point of moisture or solvents, allowing them to evaporate at lower temperatures. This makes vacuum drum dryers ideal for drying products that are sensitive to heat.
Disc dryers feature several vertical rotating discs mounted on a shaft inside a horizontal cylinder. Heat is supplied to the shaft via steam or hot oil and transferred to the discs. As the discs spin, they dry the material indirectly. Wet feed, such as slurry or sludge, is introduced at one end of the cylinder. As the material comes into contact with the rotating discs, moisture or solvent evaporates while it moves through the cylinder. Scrapers inside the cylinder ensure even mixing and prevent material from adhering to the discs. The dried product is collected at the bottom of the cylinder, opposite the feed entry point.
Disc dryers are designed to enhance heat transfer to the product, resulting in quicker drying times. The gentle rotation of the discs helps protect delicate materials and maintain their quality. A major advantage of disc drying is its uniform drying process, facilitated by the continuous movement of the discs, which prevents uneven drying and moisture accumulation.
Disc drying features an advanced heat transfer mechanism that enhances energy efficiency and reduces operational costs. Disc dryers can handle a variety of materials and are utilized across numerous industries, including pharmaceuticals, food processing, and chemicals.
The RAMCO Industrial Hot Air Parts Dryer is known for its rapid drying capabilities without excessive heat. It features a process elevator that modifies airflow patterns, creating a dynamic drying effect that improves surface coverage, enhances evaporation, and accelerates processing times. The dryer utilizes electrically heated air, which is continuously recirculated and directed into the drying chamber via air knives. During operation, the elevator moves the parts load in and out of the heated air stream, optimizing the drying process. Available in standard models, the RAMCO dryer can also be customized to meet specific customer requirements.
The NPH and PGH drying hoppers are tailored for the drying and dehumidification of plastic resins. They feature a rail for hopper-mounted heaters, a slide gate shut-off, and an extended sight glass. Constructed from stainless steel and carbon steel, these hoppers are designed with large access doors for easy cleaning. The double-wall construction ensures a secure seal, high quality, and long-term durability. Most models come equipped with lifting lugs and include 12-foot silicone hoses with clamps.
The 801D Heated Hot Air Parts Dryer is designed to effectively eliminate spots on parts using heated air to dry basket loads. It features a stainless steel construction and includes digital timer and temperature controls. With a capacity of 29 gallons and dimensions of 36x14x14 inches, the 801D uses forced warm air that enters from the back and circulates over the baskets for drying and passivation. The dryer is a standalone unit with casters for portability and ease of movement.
The FM-D-LH3025 Hot Air Dryer features a front-loading design and employs vertical airflow for the drying process. Air is introduced at the top of the drying chamber and flows downward, exiting through a grate at the bottom. This design allows for the use of drying racks and can accommodate parts up to two feet tall. The downward airflow enhances drying speed and efficiency. Standard features include hanger rods, side wall brackets for multiple trays, and work rests. The vertical configuration supports high-capacity loading.
Drying small, nested parts, particularly those with cups that trap water, can be challenging with conventional hot air methods. Spin dryers address this issue by rapidly spinning a basket of parts, using centrifugal force to expel excess water. A turbine fan positioned below the spinning basket draws heated air through the parts from a heater mounted on the lid. This process ensures thorough drying of a basket load of parts in under sixty seconds, combining centrifugal force and fan action for efficient and damage-free drying.
Industrial dryers play a crucial role in product quality and must be selected to fit specific application and product requirements. Although they represent a significant investment, choosing the right industrial dryer can ensure long-lasting performance with minimal maintenance for several decades.
Before issuing a Request for Proposal (RFP), manufacturers and engineers typically have a well-defined understanding of the dryer type they need, based on thorough investigation and analysis. The following six criteria are key considerations engineers evaluate when preparing their RFP.
The particle size and density of the material influence the required drying process. For example, fine powders need different drying cycles compared to sludge, and large painted or coated parts have specific drying requirements of their own.
Drying materials of varying sizes and particulates within the same batch can add complexity to the drying process. The density of each item affects its movement through the dryer and may necessitate specialized conveyance methods to ensure effective and even drying.
Calculating both the starting and ending moisture percentages is essential. This involves testing the weight differences between wet and dry material to determine the water weight. Accurate calculations are crucial, as even minor errors can alter the water weight and lead to selecting an improperly sized dryer.
Materials also differ based on whether the moisture is surface water or absorbed, which greatly influences the drying method. Surface water and absorbed moisture require different vaporization techniques. Understanding whether moisture is internal or external helps determine if pre-drying steps are necessary.
Materials respond differently to heat; some may undergo chemical reactions at specific temperatures, while others might melt, burn, or even explode if exposed to heat for too long or at high temperatures. The heat source used can influence these reactions, making it crucial to control it carefully.
An item's reaction to heat affects the dryer size, the duration of heat exposure, and whether to use direct or indirect heating methods.
Material handling involves how the substance is loaded into the dryer. Wet or sticky materials might require forceful movement to avoid blockages. In such cases, dryers can be designed with nonstick surfaces or paddles and equipped with cleanable fittings to minimize potential buildup.
Many modern products are highly delicate and require careful handling to prevent damage and waste. Such materials need a conveyance method that is gentle and non-abrasive. Conversely, coarse or gritty materials can damage the dryer’s surface and reduce its lifespan, requiring more robust handling solutions.
Every industrial operation has production targets that must be met for each run. The size of an industrial dryer should align with the expected production volumes. It’s important to consider whether the dryer will operate continuously in an assembly line or handle batch processing. Undersized dryers can hinder production efficiency and may be overwhelmed by excessive demands.
Industrial dryers can function as standalone units used on demand or as integral components of an assembly process, requiring synchronization with production schedules. This aspect of the selection process involves determining the dryer’s placement to align with assembly and production requirements.
Industrial dryers are robust pieces of equipment essential for production and maintaining product quality. Their selection involves considering the same factors as other machinery, including the initial purchase cost and ongoing operating expenses.
While some industrial dryers may have a lower initial cost, they can become more expensive over time due to higher maintenance needs, inefficiency, improper matching to operational requirements, and shorter lifespan. These factors can lead to increased overall operating costs.
In the planning and research phases, engineers thoroughly assess the total investment in an industrial dryer, considering its efficiency, impact on product quality, and operational costs. The goal is to ensure that the dryer meets and surpasses the production needs, creating an optimal alignment between the dryer’s capabilities and the production requirements.
An air dryer is a system or piece of equipment that is used to remove moisture present in the air, particularly compressed air. Ambient air typically has a relative humidity of around 30 to 50%. Compressing air packs higher...
A conveyor oven is a continuous flow oven; it‘s an oven that is open on opposing sides and has a conveying system running from one end of the oven to the other. Designed like a batch oven, conveyor ovens have the additional benefit of keeping products moving while providing continuous and uniform heat...
A curing oven is thermal processing equipment used by thermal specialists to improve or enhance the strength and durability of materials. Many factory processes such as baking, drying, heating, cooking, and curing require...
An industrial oven is a device used to create extremely high temperatures to heat treat parts, condition metals, and cure metal coatings. Common functions for industrial ovens include drying, curing, testing, and coating of parts and products...
An infrared oven is an oven that heats objects or cooks food using infrared radiation instead of conventional conduction or convection heating. People can use infrared ovens in commercial kitchens, homes, or...
Industrial ovens are thermal processing machines used as heating chambers for drying, curing, and baking of foods, parts, and components. The main industries that use industrial ovens are chemical and food processing and electronics manufacturing...