EDM Machining
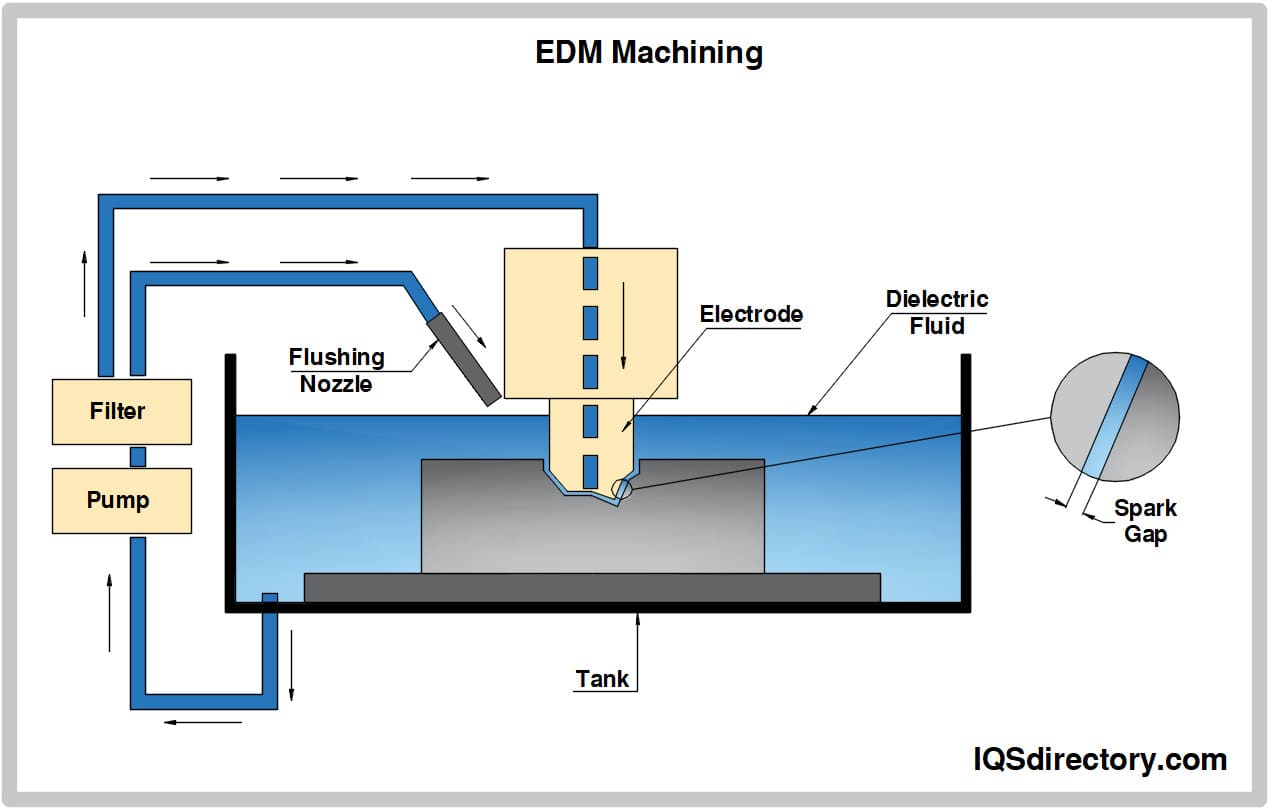
EDM machining is a contemporary machining method based on the removal of material from a part using thermal energy. The material is removed by local melting or vaporizing small areas on the surface of the part being machined...
Please fill out the following form to submit a Request for Quote to any of the following companies listed on
This article will give a detailed discussion on wire electrical discharge machining (EDM)
It is expected that after reading, one should understand;
Electrical discharge machining (EDM) is a high-precision machining process that employs thermal energy rather than mechanical force to remove material from a workpiece. Wire EDM, a specialized form of EDM, utilizes an extremely fine metal wire, typically brass or copper, as the cutting tool electrode. This method uses deionized water, which not only conducts electricity but also prevents rust accumulation. In wire EDM, the slender wire electrode maneuvers along a pre-set course to cut or shape the workpiece. Electrode wire diameters usually range from 0.004 to 0.012 inches (0.10mm to 0.30mm), although different sizes are available. The wire is continuously supplied from two spools, ensuring that the active segment of the wire remains unworn during use.
Wire electrical discharge machining (EDM) is effective for machining parts that resist traditional machining processes, provided they are electrically conductive. Commonly machined metals include non-ferrous alloys like steel, titanium, super alloys, and brass. The EDM method generates small chips by melting or vaporizing the material to achieve precise cuts, rather than through cutting. This versatility allows EDM to be widely used in the industry, handling strong metals efficiently without occupying excessive space.
Wire EDM is renowned for its efficiency and cost-effectiveness when machining conductive and challenging materials. The process enables fast and precise cutting of complex designs while adhering to tight tolerances. As a non-contact cutting method, it is ideal for machining hard, brittle, or delicate materials without deforming them.
Wire EDM involves meticulous cutting, trimming, and removal of material from the workpiece. The process creates an electrical discharge between the wire electrode and a conductive material, causing sparks that remove material from both the workpiece and electrode. Given its properties, wire EDM is specially suited for machining tough, conductive materials. A non-conductive fluid or dielectric is utilized to avoid electrical shorting and help remove debris, allowing the process to continue uninterrupted.
Before wire machining begins, a starting hole needs to be drilled in the workpiece, or the process can commence from an edge. Each discharge during machining produces a tiny crater on the workpiece while marking the electrode. The wire's angling capability allows for creating tapered or varying profiles on different surfaces. The electrode and workpiece avoid physical contact. Depending on the precision and surface finish needed, the workpiece might undergo cutting, roughing, and subsequent skimming. Typically, the wire penetrates through the solid material in one pass before a slug or scrap piece is extracted. While this method can suffice for some applications, a final skim pass often ensures optimal accuracy.
In wire EDM, pulses of voltage difference are applied between the electrode and workpiece. This causes electrons to travel from the negatively charged electrode to the positively charged workpiece, affecting the deionized water molecules. As ions and electrons accumulate between the electrode and workpiece, an electric current forms, with ions rushing towards the workpiece and electrons moving to the electrode.
When this electric current flows, the temperature can soar to nearly 10,000°C, resulting in the melting and vaporizing of the material closest to the electrode. When the current ceases, the flowing dielectric fluid expels or cleans away the molten matter. The precision of the wire EDM process is largely dictated by the cutting parameters and speed. Higher speeds may slightly bend the wire, affecting accuracy. For maximum precision, lower power and speed settings are suggested. With reduced settings, tolerances can achieve +/- 0.0002 inches, while higher speeds generally result in tolerances of +/- 0.001 inches.
EDM wire diameters range from 0.0008 to 0.013 inches. Smaller wires necessitate lower power settings and slower cutting speeds. The 0.010-inch diameter plain brass wire is utilized for over 80% of EDM applications. It is important to choose a wire that matches the material being machined for optimal results.
The geometry of a design is a crucial factor in determining its suitability for wire EDM. It influences the complexity of manufacturing the component and whether wire EDM can effectively produce the desired features. Not all geometric designs are compatible with EDM, and some may present challenges such as wire erosion, inconsistent surface finishes due to varying material thicknesses, and limitations in achieving precise tolerances. Engineers and designers should evaluate the geometry as early as possible in the design phase to ensure the part can be manufactured effectively.
When designing a product for wire EDM machining, it is essential to carefully evaluate the required surface finish. Wire EDM can achieve surface finishes with precision as fine as 3 microinches. However, not all components need such high precision. Only a few parts require this level of accuracy and smoothness. Therefore, designers should assess the acceptable tolerance range for the part. Setting appropriate minimum specifications will have a significant impact on the overall cost of the final product.
Design considerations for cost efficiency, project timeline reduction, and part repeatability are crucial in wire EDM machining. For instance, achieving higher surface finishes in wire EDM necessitates tighter tolerances, which in turn increases the cost due to longer cutting times. Additionally, the choice of material and the height of the part can affect machining accuracy. Taller components require more force to remove material, which can impact both precision and surface finish. Thus, these factors must be carefully evaluated during the design process.
When evaluating a project design, it is important for the designer to discuss material choices with the client. Selecting the appropriate conductive material is crucial for meeting design specifications and ensuring suitability for wire EDM. Choosing the right material can help lower the cost of the final product, particularly if the part requires specific hardness, dimensional accuracy, or tight tolerances. Each aspect of the part design should be carefully examined and optimized to achieve both optimal functionality and cost efficiency for wire EDM machining.
Time is a crucial factor in manufacturing, especially when designing parts for optimal manufacturability. EDM machining can be time-consuming, so it's important to consider that customer orders often require rapid turnaround times.
The success of the wire EDM process depends heavily on precise programming. The numerical control (NC) program dictates the operations of the machine tool, and its accuracy is essential for achieving the correct shape and precision. Once programming is completed, the CNC program must be thoroughly reviewed and validated to ensure it is error-free before the cutting begins. The wire EDM machine's numerical control system includes a verification feature to check for syntax errors and ensure that the program adheres to the specified processing contour.
The components of a wire EDM machine collaborate to precisely shape materials. Each part plays a crucial role, and their coordinated function is essential for the machine's operation.
In wire EDM, the wire functions as the cathode, while the workpiece acts as the anode in the machine's electrode setup. During the cutting process, the servo motor regulates the wire electrode to prevent it from touching the workpiece.
The wire feed system manages the electrode wire's speed and tension, controls its back-and-forth movement, and ensures that the wire coils onto the drum properly without overlapping.
The wire acts as the electrode for generating electrical discharges. Consequently, the thickness and shape of the workpiece influence the required diameter of the wire.
The workpiece is secured on the work table, which is moved by two stepper motors. The interaction between the moving table and the cathode wire enables the wire EDM process. The high-speed wire feed EDM machine features X and Y axis slides on its work table, utilizing advanced linear guideways and ball screws for movement. The XY cross structure, a time-tested design, provides robust mechanical rigidity and precision control. This design is now well-established and commonly employed in the manufacturing of various machine tools.
CNC systems rely on high-precision stepper motors that feature robust coupling and programming capabilities. These systems are crucial for managing the complete wire EDM machining process. They automate the cutting operation and manage the sequencing of the wire path to ensure accurate results.
The tank for the wire-cut EDM process must be filled with dielectric fluid. This fluid prevents tiny particles from sticking to the wire electrode during machining. Deionized water is commonly used because it cools the operation and helps achieve a smooth surface finish on the workpiece.
The power supply unit sends pulses between 100V and 300V to the wire electrode and the workpiece. The electrical charges that flow through the wire electrode to interact with the workpiece are also controlled in frequency and intensity. Therefore, a highly-developed power supply unit is required to deliver the right kind and quality charges during wire EDM machining.
Deionized water is pumped from the tank, filtered to eliminate impurities, and then channeled through separate nozzles before returning to the tank via another filter. If the quality of the working solution or the effectiveness of the filter affects the cutting process, they should be replaced.
Due to their high conducting qualities, brass is the most popular material for EDM wires. It is a copper and zinc alloy, and the wire cuts more quickly the more zinc there is in the alloy. There should be a balance, though, as brass wire's corrosion rate is decreased when the zinc concentration exceeds 40%.
These wires are named for their surface coating of pure zinc or zinc oxide. Zinc-coated wires are favored by manufacturers because they enhance the machining speed.
Initially, copper was the wire of choice for wire EDM due to its availability and excellent conductivity. However, as generators became more powerful, copper's slow cutting speed and limited tensile strength became evident. Consequently, copper wire is now rarely recommended, except for use with older equipment that specifically requires it.
The diffusion annealing process allows for the creation of wires with a higher zinc content by applying multiple layers of pure zinc coating. These wires are versatile for machining different materials and are well-suited for high-volume production.
Molybdenum wires are known for their exceptional tensile strength. Despite having high melting and vaporization temperatures, which make them less ideal as electrode material, molybdenum wires are beneficial for maintaining precise wall straightness and reducing the occurrence of wire breaks, which is common with finer brass wires, thanks to their strength.
This wire features a carbon steel core that offers excellent strength and resistance to fractures, while being coated with a thick layer of zinc-rich, diffusion-annealed brass to enhance cutting efficiency.
When attempting to address a challenging application, tungsten wire is frequently one of the last options considered. Sometimes this wire is the only option for an EDM issue, despite being very expensive, cutting poorly, and difficult to deal with. It is the least effective wire electrode in cutting performance, with even greater melting and vaporization temperatures than moly. Of all EDM wires, however, tungsten wire has the highest tensile strength. This quality enables it to define and sharply carve very small, straight-walled details.
Determining the tensile strength of EDM wire is essential. The wire feed system of the machine, including components like the wire tensioner, roller guides, and both upper and lower feed contacts, exerts tension on the wire even if it doesn’t touch the workpiece during cutting (where the electric current is applied). This preloaded tension can be adjusted for different cutting tasks. The tensile strength of the wire influences its ability to endure stress during cutting; a lower tensile strength means the wire is more prone to breaking.
Wire with lower tensile strength can still cut angles without breaking. The U-V axis wire guides can be adjusted or offset to achieve significant tapers and angle cuts up to 45°. Using the U-V axis to control the perpendicularity of vertical walls allows for tighter stretching of stronger wire. For rough cutting, lower wire tension facilitates faster machining without causing wire breakage. In contrast, skim cuts require slower speeds and reduced power to ensure optimal surface finish and accuracy.
Rather than rating fracture resistance directly, it may be more precise to describe an EDM wire's ability to endure as its toughness or resilience. This is because the wire must withstand the highly dynamic conditions within the spark gap.
Conductivity gauges a substance's electrical current-carrying capacity. More power can be transmitted to the workpiece during EDM if the wire's conductivity is higher. Increased cutting speeds are frequently the result of more efficient conductivity.
To achieve rapid vaporization, a wire with a low melting point is ideal. This allows the wire surface to evaporate quickly and convert into gases, preventing contamination of the gap with resolidified debris.
Tensile strength is often mistaken for hardness. Hardness refers to a wire's ability to withstand stretching or deformation. EDM wires are categorized as either soft or hard. Hard wires generally perform better on closed-guide machines, providing more reliable threading, whereas soft wires excel at taper-cutting. Additionally, hard wires usually offer more consistent auto-threading performance.
Once the appropriate material for the workpiece and the correct wire have been chosen based on the provided guidelines, the machinist should proceed with the following steps:
Before initiating online cutting, it is necessary to prepare wire holes for processing closed holes and certain punches. The location of the threaded hole must align with the starting point designated for the machining process during programming.
Select the appropriate clamping method to position the workpiece according to its size, shape, and processing needs. Depending on whether you are working with plate parts, rotating parts, or block components, you may use specialized or custom fixtures for clamping. Once clamped, the workpiece must be adjusted. This typically involves checking the perpendicularity and flatness of the clamping and correcting the axial parallelism between the machine tool and the workpiece's reference plane.
Before starting the wire EDM process, it's crucial to accurately position the wire electrode at the cutting coordinate's initial location. Adjustment methods include automatic alignment, the spark method, and visual inspection. Modern CNC wire-cutting machines often feature contact sensing, automated edge detection, and automatic center finding, which enhance alignment precision. Despite these advancements, operation can vary between different machines.
Wire EDM programming is central to the entire process, with CNC software controlling the machine tool's operations. The accuracy and shape of the machining are directly affected by the correctness of the program. For production, automatic programming methods are typically utilized.
Once programming is complete, it is essential to review and confirm the CNC program's accuracy before commencing any cutting operations. The numerical control system of the wire EDM machine offers various verification methods for this purpose. If the CNC program is verified to be accurate, the machining process can proceed as planned.
Once the machining is complete, the tool moves back to its initial position. The machinist can then remove the finished workpiece from the clamps.
While both wire EDM and traditional EDM operate on similar principles, wire EDM represents an advancement over conventional EDM. Here are the differences between the two:
Traditional EDM requires electrodes to be shaped into various forms, which is a time-consuming process before machining can start. In contrast, wire EDM is ready for use as soon as the wire is installed, making it ideal for projects that need to be completed quickly.
In wire EDM machining, the wire itself acts as the electrode, allowing for greater accuracy compared to traditional EDM methods. This precision enables the wire to cut materials as thin as approximately 0.004 inches. Furthermore, wire EDM is particularly well-suited for machining complex shapes and intricate designs, whereas conventional EDM is generally used for heavier cuts.
In wire EDM, a thin, heated wire serves as the electrode during cutting. This differs from conventional EDM, where electrical charges are generated using electrodes made from highly conductive materials such as copper or graphite. The shape and size of these electrodes affect the surface finish, with circular electrodes producing the smoothest surfaces, followed by diamond, square, and triangular shapes. When these electrodes are applied to the workpiece, they create a "negative" mold of the desired shape.
Wire EDM machining is utilized across various industries due to its versatility in cutting both ferrous and non-ferrous metals. Its adaptability extends to handling components of varying sizes and shapes, from long sections to highly intricate parts. Despite this, the thickness of the wire electrode plays a crucial role in its application, which means that traditional EDM methods might be more suitable for processing tougher and thicker materials.
To be effective and efficient, a wire EDM machine should have several critical features. Precision and accuracy are the most important, with the machine needing to achieve exact tolerances and maintain consistent dimensional precision throughout the machining process. High repeatability is also essential, ensuring that the machine can reliably produce identical shapes and features. Speed and cutting efficiency are vital, with the machine needing to perform quickly while maintaining high-quality results. The machine's stability and rigidity are crucial, as they help it endure the forces of the EDM process, reduce vibrations, and ensure accurate positioning. Lastly, advanced control systems and software, including CAD/CAM integration and adaptive machining, enhance the machine's versatility, ease of operation, and overall effectiveness.
Considering these attributes, the following five wire EDM machine manufacturers are noted for their prominence and strong reputation in North America:
Mitsubishi Electric is a renowned name in wire EDM machine manufacturing, distinguished by its precision, dependability, and cutting-edge technology. Their machines are known for high-speed cutting performance, exceptional surface quality, and precise accuracy. Additionally, Mitsubishi Electric is celebrated for its intuitive CNC controls and software, which streamline programming and operation.
The MV series from Mitsubishi Electric, including models like the MV1200S and MV2400R, has garnered positive feedback in the industry. These machines feature cutting-edge technologies such as non-contact cylindrical drive systems and smart automatic wire threading, which significantly boost both productivity and dependability.
Makino stands out as a leading name in the wire EDM machine industry. Their equipment is praised for its robustness, reliability, and outstanding performance. Makino's wire EDM machines frequently feature sophisticated control systems, rapid machining speeds, and advanced automation functionalities. They are renowned for their precision in achieving tight tolerances and maintaining high accuracy in intricate machining tasks.
Among Makino's notable wire EDM machines is the U6 H.E.A.T. Extreme. This model employs high-energy applied technology to deliver both efficient and precise machining outcomes. It is particularly valued for its capability to manage complex geometries, uphold tight tolerances, and produce exceptional surface finishes.
Sodick is well-known for its high-precision wire EDM machines. Their equipment is celebrated for its remarkable cutting speed, accuracy, and surface quality. By integrating advanced technologies like linear motor drives, Sodick ensures high responsiveness and efficiency. Additionally, their sophisticated control systems and user-friendly software interfaces are designed to improve both convenience and operational productivity.
The AG series from Sodick, featuring models such as the AG400L and AG600L, has become popular within the wire EDM industry. Beyond their standard advantages, these machines come equipped with smart control systems, sophisticated wire threading technology, and easy-to-use software interfaces. Users are drawn to Sodick’s wire EDM machines for their dependability, efficiency, and capability to manage intricate machining tasks.
GF Machining Solutions provides a diverse selection of wire EDM machines suited for different applications. Their machines are known for their accuracy, adaptability, and dependability. Featuring smart technologies like automatic wire threading, adaptive machining, and sophisticated tooling options, GF Machining Solutions’ machines offer high cutting speeds, enhanced energy efficiency, and advanced automation features.
GF Machining Solutions' AgieCharmilles CUT series, including models like the CUT E350 and CUT P550, is highly esteemed in the industry. These machines are known for their adaptability, accuracy, and cutting-edge automation features. The CUT series also includes smart technologies such as automatic wire changing, collision avoidance systems, and advanced tooling capabilities. Users appreciate GF Machining Solutions' wire EDM machines for their exceptional performance, versatility, and efficiency in maximizing productivity.
Fanuc is a prominent name in the CNC machine industry, including wire EDM machines. They focus on providing user-friendly controls and straightforward programming, enabling operators to efficiently set up and manage the machining operations. Fanuc's machines are also known for their precision, operational efficiency, and durability over time.
Fanuc's Alpha C600iA is a widely recognized wire EDM machine celebrated for its sturdy build, consistent stability, and dependable performance. It delivers impressive cutting capabilities, high precision, and is designed for ease of use. The Alpha C600iA integrates Fanuc’s CNC control systems, facilitating smooth programming, monitoring, and management. It is particularly valued by users for its precision, robustness, and user-friendly features.
Choosing the right wire EDM machine is contingent on various factors, including the desired level of repeatability, accuracy, cutting speed, and budget constraints. It is also beneficial to review industry reports, stay updated on market trends, and consult with industry experts or suppliers before finalizing your decision.
The wire EDM process is ideally suited for intricate designs, complex geometries, and components requiring precise geometric angles that cannot be achieved through traditional manufacturing methods.
The automotive industry favors wire EDM cutting over traditional methods because it delivers precise molding and drilling for larger components. Additionally, the EDM process results in more durable and long-lasting materials, which is highly valued in this sector.
The medical industry heavily depends on wire EDM services due to its superior performance compared to traditional manufacturing methods. Medical devices often require components that are highly specialized, miniature, and exact. For instance, hand tools used by doctors and surgeons must have precisely straight edges, which are critical for ensuring the equipment's effectiveness during procedures.
Wire EDM services are also utilized by manufacturing firms for dental and orthodontic tools. These dental instruments require the same level of precision as medical devices. Wire EDM is commonly used for crafting the tiny components essential for braces.
Wire EDM cutting services are commonly employed in aerospace technology. This technique is used to produce components for engines, fuel systems, landing gear, and other high-stress, high-temperature systems, as these parts must withstand the extreme heat and pressure needed for reliable operation.
Wire-cut EDM is extensively used for machining various molds, such as punch dies, squeeze dies, powder metallurgy molds, bend molds, and plastic molds. By adjusting different compensation settings, wire EDM can efficiently cut terrace dies, punch plates, stripper plates, and other materials.
EDM machining is a contemporary machining method based on the removal of material from a part using thermal energy. The material is removed by local melting or vaporizing small areas on the surface of the part being machined...
Sinker Electrical Discharge Machining (EDM) is a metal machining process used to create molds, dies, and parts using electrical sparks to erode material from a workpiece. It is preferred over other machining processes due to...
The normal functioning of CNC machines is done along the three Z, X, and Y axes. The five axes machines have two more axes accessible, which are namely A and B. The addition of the two extra axes makes it easy to cut complex and intricate parts...
CNC machining is an electromechanical process that manipulates tools around three to five axes, with high precision and accuracy, cutting away excess material to produce parts and components. The initial designs to be machined by CNC machining are created in CAD...
The CNC process was developed in the 1950‘s and took a leap forward in the 1980‘s with the addition of computerization. Unlike other production processes, CNC begins with a rendering by a computer, which creates a two or three dimensional representation of the part to be produced...
G-code is the name of a plain text language that is used to guide and direct CNC machines. For most modern CNC machines, it isn‘t necessary to know the meaning of G-codes since CAD and CAM software is translated into G or M codes to instruct a CNC machine on how to complete a process...
Computer numerical control (CNC) is a fundamental part of modern manufacturing. The majority of machines operate using instructions and guidelines that have been downloaded using a CNC program controller...
Water jet cutting is a manufacturing process that uses high pressure jets of water provided by pressurizing pumps that deliver a supersonic stream of water to cut and shape various types of materials. The water in water jet cutting is...
Machining is a manufacturing process used to produce products, parts, and designs by removing layers from a workpiece. There are several types of machining that include the use of a power driven set of machining tools to chip, cut, and grind to alter a workpiece to meet specific requirements...
The CNC process, computer numerical control, is a method of manufacturing where programmed software directs the operation of factory tools and machinery. It is designed to manage a wide range of complex machines from grinders and lathes to mills and routers...