Band Heaters
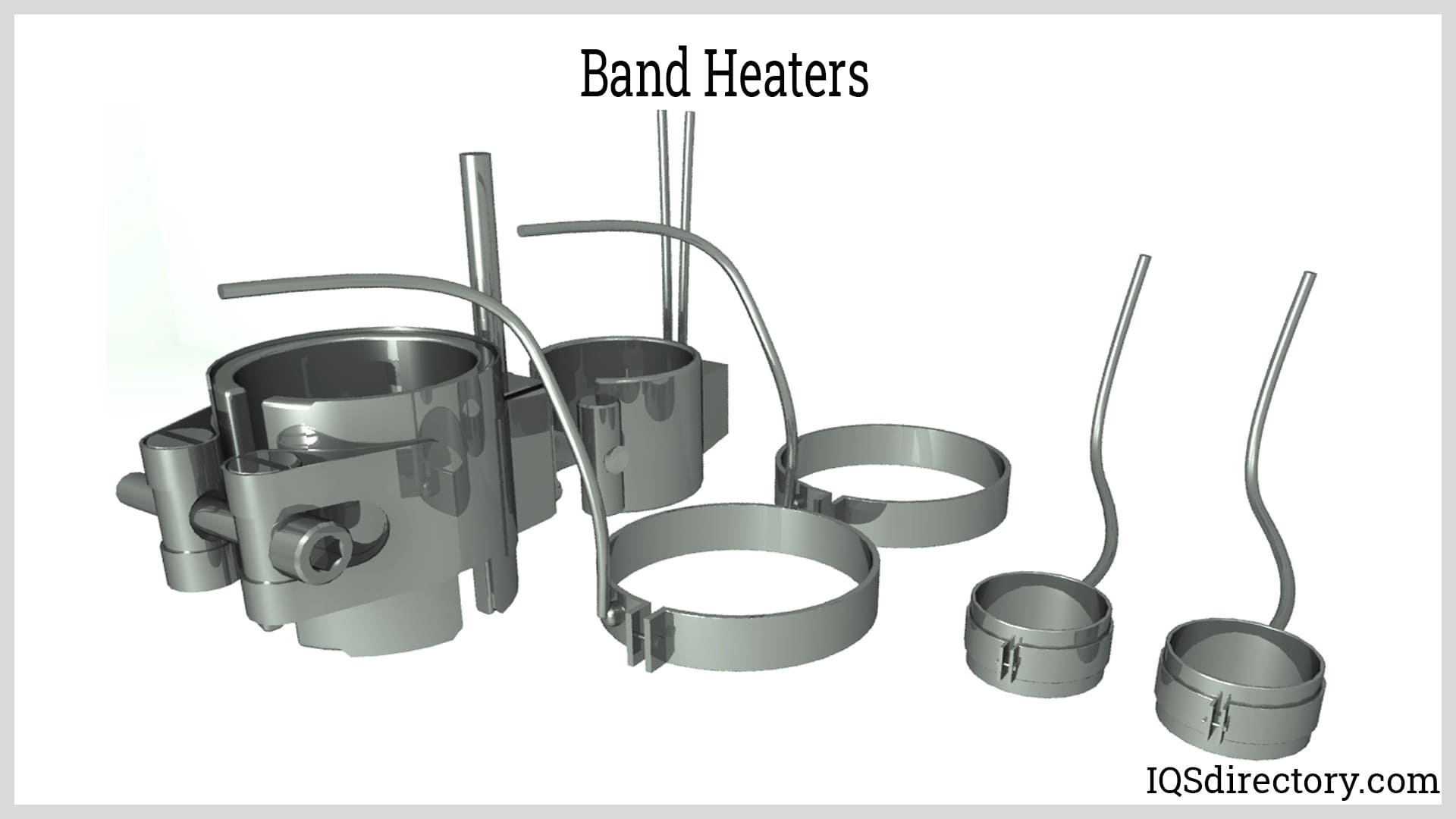
A band heater is a heating device that clamps onto objects to provide external heat using radiant and conductive heating. The different mounting methods of band heaters makes it possible to secure them tightly and...
Please fill out the following form to submit a Request for Quote to any of the following companies listed on
This article contains everything you will need to know about flexible heaters and their use.
You will learn:
Flexible heaters are crafted from materials capable of bending, stretching, and conforming to numerous surfaces needing heat application. These versatile heaters are available in various forms, such as polyimide films, silicone rubber, tape, rope, and customized designs for specific uses like tank enclosures or gas cylinder heating. Typically, their construction features chemically etched, screen-printed, or wire-wound elements, allowing them to adapt closely to the curves of different surfaces.
Renowned for their durability, reliability, precision, and efficiency, flexible heaters stand out as an ideal option for various heating needs. They can easily adhere to numerous substrates and play a vital role in industrial, commercial, and military environments due to their lightweight nature and ability to endure harsh conditions.
The emergence of flexible heaters arose from the necessity to tackle complex heating challenges where conventional heaters fell short. These applications required heaters that could seamlessly alter their form to fit diverse surfaces and conditions. Consequently, a wide variety of flexible heaters was developed, specifically designed to efficiently provide heat across multiple environments and situations.
Each flexible heater is designed with unique features tailored to specific applications, allowing it to adapt to various conditions. Despite the diverse designs and functionalities of flexible heaters, they share common characteristics, such as the use of single-layer circuits. This feature is a key differentiator from other heating devices and is fundamental to their adaptability.
Flexible heaters transfer heat using highly conductive metals like copper and resistive alloys such as Inconel or Cupro-nickel. These materials are chosen for their excellent thermal conductivity and their ability to maintain a thin, flexible form. Heat is generated by high-resistance conductors, which then transfer energy to different substances, fluids, and materials. The dimensions of the conductors are carefully selected to provide the desired resistance based on the applied voltage.
Flexible heaters come in a variety of types, styles, and shapes, but they typically feature one of three main configurations: etched foil, screen printed, or wire wound. Each of these configurations utilizes distinct manufacturing techniques and methods for delivering electrical energy to the heater.
Etched foil flexible heaters are crafted using precision etching techniques on a thin substrate. This process involves chemically etching a specific pattern to create a circuit-like structure designed for resistive heating. Etched foil heaters are ideal for applications requiring precise control of heat distribution and temperature, ensuring uniform and efficient heating.
When an electric current flows through the foil, resistance generates heat due to the Joule heating effect. As the voltage increases, so does the resistance, leading to higher heat output. This mechanism allows for precise regulation of heat production within the resistive foil.
Etched foil heaters feature a highly accurate conductor layout, enabling the design of complex heating patterns. This precision ensures that heat is applied exactly where needed, avoiding both cold and hot spots. The primary advantage of flexible heaters, including etched foil types, is their ability to deliver consistent and uniform heat, a critical factor in many heating applications. Etched foil heaters are specifically engineered to maximize this benefit.
Wire wound flexible heaters are constructed with evenly spaced laminated wires sandwiched between layers of a flexible insulating material, typically silicone rubber. Similar to etched foil heaters, wire wound heaters are designed to distribute heat uniformly across their fabric cover, which provides insulation and protection.
Nickel-chromium (nichrome) wire is commonly used in wire wound flexible heaters due to its high electrical resistance, making it well-suited for heating elements. Nichrome’s durability allows it to withstand repeated flexing and bending, which is essential for the longevity of wire wound heaters.
Despite their robustness and resilience, wire wound flexible heaters generally have a slower warm-up time, which can delay the heating process. However, they are cost-effective and capable of heating larger surfaces, which contributes to their overall efficiency.
Screen printed flexible heaters are produced by applying conductive ink onto a flexible substrate using screen-printing techniques. The substrates used can include various polymers such as polyester (PET), polyimide (PI), polycarbonate, and others. These heaters come in different types, including self-regulating versions that maintain a consistent temperature once reached, and fixed resistor versions.
Screen printing, a process that has been around for many years, originally served to imprint images, patterns, or designs on fabrics. In the mid-20th century, this technique expanded to include the creation of printed circuits. The process involves mixing ink and using a tool to push the ink through a stencil with a circuit pattern onto the fabric surface.
The stencil with the circuit pattern dictates the placement of heating traces and heat distribution. The design of the pattern allows for precise heating in specific areas, with power density adjusted by modifying the stencil pattern.
Manufacturing screen-printed flexible heaters is efficient and can be done using methods such as flatbed screen printing, rotary screen printing, or roll-to-roll processes. The choice of manufacturing technique depends on the type of heater and the materials used.
Polyimide flexible heaters are primarily made from polyimide, a versatile polymer known for its wide temperature tolerance. Polyimide can withstand temperatures as low as -200°C (-328°F) and as high as 260°C (500°F), making it suitable for extreme conditions. This material combines the desirable attributes of flexible heaters with superior mechanical properties, providing both flexibility and durability.
Polyimide polymers are known for their ability to endure high temperatures while maintaining excellent electrical insulation. The flexibility of polyimide makes it an ideal material for manufacturing flexible heaters. Its structural properties allow for the creation of complex and intricate designs that ensure uniform heat distribution across the heater's surface.
Polyimide heaters are prized for their lightweight nature, versatility, and superior thermal performance. They retain their shape while effectively transferring heat to various applications. Their thin profile allows them to fit into tight or limited spaces, making them suitable for a wide range of applications.
These heaters are highly customizable, allowing adjustments to meet specific voltage, wattage, shape, and size requirements. This flexibility enables engineers to design polyimide heaters to precise specifications. Additionally, polyimide heaters offer excellent dielectric strength and chemical resistance, contributing to their durability and longevity under diverse conditions.
Silicone rubber flexible heaters come in two main types: wire wound and etched foil. Wire wound flexible heaters feature resistance wires laminated between layers of rubber, providing both uniform heating and structural strength. They are typically used in applications that require large-sized, low-volume heating solutions.
The heating performance of wire wound flexible heaters depends on the type of wiring used. Nickel-chromium (nichrome) wire is commonly employed due to its high resistivity and resistance to oxidation, enabling it to reach temperatures up to 1250°C (2280°F). This type of wiring is ideal for applications requiring high-temperature heating.
Another type of wiring used in silicone rubber flexible heaters is copper-nickel wire. This wire offers medium-range electrical resistivity and a low temperature coefficient of resistance. Copper-nickel wired heaters are typically used for applications where the maximum temperature requirement is around 600°C (1110°F).
Iron-chromium-aluminum wire is also used in silicone rubber flexible heaters. This high-resistance material provides excellent form stability and durability, with an operating temperature up to 1400°C (2550°F). Heaters made with iron-chromium-aluminum wire are known for high surface loading, high resistivity, and low density, allowing for material savings and reduced weight.
Etched foil silicone rubber flexible heaters are made by chemically etching circuits that are then laminated between thin sheets of silicone, facilitating rapid and even heat transfer. These heaters feature wider widths and closer element spacing, which allows for higher output wattage and multiple heating zones on a single unit. The etched foil can be made from materials such as aluminum, stainless steel, nickel-chromium, or copper, enhancing versatility and performance.
Polyester flexible heaters, also known as polyester film heaters or polyester foil heaters, are constructed with conductive ink sandwiched between layers of polyester. These heaters typically come in sizes up to 600 mm x 1000 mm (2 ft x 3 ft) and are capable of withstanding temperatures up to 90°C (194°F), with a maximum resistance temperature of 100°C (212°F). However, predicting the exact temperature of these heaters can be challenging due to the numerous variables affecting the heating process.
Conductive ink is used to ensure even heat distribution across the polyester layers, allowing for localized low-power heating. Polyester flexible heaters come in various forms, including fixed self-adhesive foil types and versions wrapped in PVC for applications involving liquids.
These heaters are produced using screen printing technology, which involves applying silver-based conductor tracks in conjunction with conductive ink. The diversity in polyester flexible heaters can be attributed to the wide range of conductive inks available, with ongoing improvements in formulations. Adjustments to heating performance can be made by altering the conductive ink used, which helps reduce tooling costs.
Flexible heaters come in a wide range of configurations, shapes, sizes, types, and designs. Despite their diversity, most flexible heaters share common core elements aimed at ensuring durability and long-lasting performance.
The three primary types of flexible heaters are etched foil, wire wound, and screen printed. These types differ in their resistor materials, heat transfer mechanisms, and the substrates used for applying electrical resistance. Each method has been developed and refined over the years, with distinct production processes tailored to their specific applications. While their fundamental purpose remains consistent—providing effective and reliable heating—the techniques for manufacturing each type vary significantly.
The choice of substrate is a critical factor in the production of etched foil flexible heaters. It must be flexible enough to bend, shape, and conform as needed. Polyimide and silicone rubber are commonly used substrates that support the foil and act as dielectric layers protecting the heating element.
Stage One – The initial phase involves selecting the appropriate type of foil and laminate. These choices are made based on the specific resistance requirements of the heater.
Stage Two – The next step is to choose a substrate and apply a thermoset adhesive that bonds the foil to the substrate. This adhesive must be compatible with both materials and form a strong, durable bond. This bond needs to withstand both the chemical etching process and the stresses encountered during the heater's final application.
Additional considerations for the adhesive include minimizing outgassing, ensuring UL flame retardance, and providing mechanical flexibility. The bonding process involves applying increased pressure and temperature to achieve a flat, unstressed laminate with a robust bond.
Stage Three – To maintain proper alignment of the layers during fabrication, registration holes are drilled into the base laminate. These holes serve as guides to ensure that the different layers of the heater do not shift or move during the chemical etching process.
Stage Four – The fourth stage involves applying a pattern for the conductive element onto the laminate. This begins with coating the foil and polyimide with a photoimageable resist. A mask, which outlines the dimensions and shape of the heater element, is placed over the resist. This setup is then exposed to UV light, curing the resist and preparing it for chemical etching. The cured resist protects the desired heating pattern, while the uncured resist is removed.
Stage Five – In the fifth stage, the heater element is etched into the foil by subjecting it to a sequence of chemical etching, stripping, and cleaning processes. These steps remove the unprotected foil, requiring precise control to ensure the heater element meets the required thickness and width. The chemicals used in this process vary depending on the type of foil being used.
After the etching process is completed and the chemicals are washed away, the heater's resistance is tested before applying the final top dielectric lamination.
Stage Six – The final step involves applying the top dielectric lamination, which includes a dielectric film or coverlay with a thermoset adhesive on one side. This lamination also features pre-drilled holes for alignment with the laminate and access points. These access points are crucial for wire connections, sensor integrations, and component mounting, ensuring that all necessary connections and fixtures can be properly installed.
The fundamental element in the construction of wire wound flexible heaters is the choice of resistance wire. Unlike the more intricate processes used for screen printed and etched foil flexible heaters, the manufacturing of wire wound heaters is relatively straightforward, as it does not involve chemical treatments. The primary components of the process are the resistance wire and the overlay, which is typically made from silicone rubber or other flexible materials.
Wire – For wire wound flexible heaters, resistance wires such as nickel chrome (nichrome) are commonly used. Nichrome is composed of approximately 80% nickel and 20% chromium. The wire's diameter is carefully selected to optimize heater performance. Nichrome wire is favored for its high resistivity and excellent oxidation resistance at elevated temperatures, making it ideal for use in these heaters. Various gauges of nichrome wire provide flexibility in heater design and efficiency.
Fiberglass Cord – The resistance wire is encased in a fiberglass cord, which adds flexibility and support. This cord acts as both insulation and protection, and it can endure temperatures up to 801°C (1475°F), which is why it is chosen for wire wound flexible heaters.
Pattern – Similar to etched foil flexible heaters, the pattern of the wiring in wire wound flexible heaters is crucial for ensuring even heat distribution. The pattern is meticulously designed based on the wire's diameter and the desired heat output. It specifies the arrangement of the wires within the enclosing material and the spacing between them, which affects how heat is distributed.
The wire is arranged according to this pattern to guarantee uniform heating and to match the size and shape of the enclosing material. This careful patterning process helps prevent the formation of gaps or cutouts and dictates where the heat will be most concentrated. Lead wires and cord sets are added during this stage, typically through soldering, to complete the wiring setup.
Attaching to the Substrate – The finalized pattern is embedded into a neoprene or silicone rubber substrate, which is reinforced with nylon for added durability. The combined thickness of the substrate, wires, and lead wires is approximately 0.813 mm (0.032 in). This thin profile allows the heater to be installed in tight or confined spaces, maintaining flexibility and efficiency in various applications.
While the screen-printing process for flexible heaters shares similarities with the etched foil process, such as creating a pattern overlay, it differs significantly in its use of materials. Unlike etched foil heaters, which involve chemical etching, screen-printed heaters use specially formulated inks as the conductive elements.
Step One – The process begins with defining the shape and form of the substrate based on the geometric pattern outlined in the engineering drawing. The chosen substrate must be capable of accepting the printed pattern and enduring the mechanical stresses associated with flexible heater applications.
Step Two – The substrate for screen printing is typically a polymer such as polyimide or polyethylene terephthalate (PET), selected for its thin profile, durability, and resilience. The chosen substrate is prepared to accept the conductive ink pattern through various screen-printing techniques.
Step Three – In this step, the ink formulation is critical. The ink, often a paste or liquid, is prepared by mixing conductive materials like carbon or silver with a solvent to achieve a paste-like consistency. The goal is to create a homogeneous mixture through microscopic dispersion, ensuring the ink effectively transfers the conductive pattern onto the substrate.
Step Four – The stencil, designed with the conductor pattern dimensions, serves as a template for the screen-printing process. It allows ink to pass through only the intended areas, blocking it from regions where no imprint is desired. Stencils may be framed or frameless; framed stencils are used for high-volume production due to their durability, while frameless stencils are more cost-effective and easier to store.
The stencil used in screen printing is typically made from a thin sheet of plastic or metal with the pattern cut into it. This material must be strong enough to endure the high-pressure printing process.
Step Five – The pattern is printed onto the substrate using the screen-printing method, one of the oldest and most versatile printing techniques. This step involves forcing the paste or ink through the stencil onto the substrate. The screen-printing process is known for its simplicity, flexibility, and cost-effectiveness. For flexible screen-printed heaters, the conductive pattern is directly applied to the substrate. This process allows precise control over the thickness and width of the heating element, which in turn affects the heater’s resistance, wattage, watt density, and uniformity of heat distribution.
Step Six – After the pattern is printed, it is adhered to the substrate through a heating process that removes any remaining liquid. This heating step bonds the ink to the substrate, forming a permanent heating element. The curing process not only strengthens the bond but also enhances the mechanical strength and flexibility of the heater.
Step Seven – The final step involves applying a dielectric insulating layer over the heating element. This layer can be made from another polymer or an epoxy, which may be printed, coated, or sprayed on. As with other flexible heaters, terminations are connected to the dielectric layer using epoxy or silicone, ensuring reliable electrical connections and protection.
Flexible heaters have become indispensable across various industries due to their adaptability, durability, and efficiency. Their ability to be shaped and customized to fit diverse applications—whether large or small—makes them a versatile solution for heating needs. Designed to endure a wide range of environments and conditions, the materials, substrates, and elements of flexible heaters ensure reliable performance and resilience in demanding situations.
In industries where equipment frequently transitions between warm and cold conditions, parts can experience significant shrinkage and expansion. This temperature fluctuation can lead to physical changes such as cracks, stress, and wear, ultimately resulting in part failure and damage. Flexible heaters are crucial in these environments, as they provide consistent thermal control to maintain parts at a stable, even temperature. This steady warmth helps to mitigate the effects of expansion and contraction, thereby extending the lifespan of the equipment and reducing the risk of damage.
Security cameras, night vision equipment, surveillance systems, and mirrors often face challenges such as humidity, moisture, temperature fluctuations, fog, and mist, which can obscure their lenses and hinder performance. Flexible heaters are installed directly onto these devices to address these issues by removing moisture and preventing lens fogging. By keeping the surface of the lenses warm and dry, flexible heaters ensure optimal visibility and functionality, whether the component is stationary or in motion.
Outdoor equipment with moving parts can suffer from malfunctions due to moisture accumulation caused by inclement weather. In cold climates, this moisture can freeze, forming ice clogs that render the equipment inoperable. To avoid costly repairs and ensure reliable operation, flexible heaters are used to prevent moisture buildup and subsequent damage. Their flexibility, compact size, and precise temperature control make them well-suited for this task, effectively protecting equipment from weather-related issues.
One of the most significant applications of flexible heaters is the stabilization of product viscosity. Unlike traditional heating elements, flexible heaters can be positioned directly with the product, making them invaluable for industries where precise temperature control is crucial. Chemical producers, food processors, cosmetic manufacturers, and oil companies rely on flexible heaters to keep their products or ingredients flowing smoothly, ensuring they are easily dispensed and processed.
Many fluids experience changes in viscosity based on environmental conditions, production processes, and their inherent properties. Flexible heaters address this issue by maintaining consistent temperatures, thereby stabilizing the viscosity and thickness of liquids. This capability ensures optimal performance and reliability across various applications.
During the processing of various products, changes in temperature or environment can significantly affect their characteristics and texture, impacting the final product's quality. For instance, melted chocolate used in candy production or pastry batter for doughs and confections can undergo changes that alter their flow, texture, and properties, potentially leading to product defects.
Maintaining a stable and controlled environment is crucial to preserving product quality. For example, prepared foods must be kept at safe temperatures to prevent bacterial growth, while medical laboratories need consistent temperatures to ensure the integrity of specimens and cultures.
Flexible heaters play a vital role in these scenarios by providing even and reliable temperature control. They help prevent damage and ensure the desired properties of products are maintained. By stabilizing temperatures, flexible heaters contribute to cost savings, minimize waste, ensure high quality, and prevent the development of unwanted properties.
Sensors are essential components in many environments, used to detect and respond to various types of input. They play a crucial role in monitoring both outdoor and indoor activities at remote locations, which often exposes them to low temperatures.
Flexible heaters are employed to keep sensors warm without disrupting their functionality. By providing consistent and adequate heat, these heaters ensure that sensors continue to operate effectively and accurately, even in cold conditions. This helps prevent signal failures and maintains reliable performance.
The finishing process for products often involves glue, sealants, laminates, or bonding agents that need to cure or set properly. In mass production, allowing products to sit idle while these substances set is impractical, especially with large batches. Flexible heaters are used to maintain a consistent temperature, ensuring quick and efficient curing and bonding without any temperature fluctuations.
Electronics can suffer damage from cold temperatures, even in the absence of moisture. Semiconductors and circuits may experience signal interruptions or failures under such conditions. Conversely, excessive heat can degrade batteries and lead to failure, while extreme cold can have similar detrimental effects. Flexible heaters provide consistent temperature regulation, preventing extreme temperature fluctuations that could otherwise harm electronic components.
In vacuum environments, the lack of atmospheric conditions and minimal temperature changes can challenge the safe operation of equipment. Flexible heaters, being direct heaters, can offer the necessary stability and consistent temperature control required for equipment in such settings, including clean rooms and vacuum chambers.
Screen-printed flexible heaters have the ability to heat a variety of fabrics, including automotive seats and clothing. In vehicles, they provide comfort through heated seats and instrument panels. Additionally, they are utilized in heating pads, blankets, and therapeutic equipment to offer warmth during patient recovery and injury treatment. Flexible heaters are also essential in incubators, where they ensure a steady, constant, and consistent heat for newborns.
The output wattage of a flexible heater is crucial to its design, as it ensures the heater has the right resistance, voltage, and current to generate sufficient heat. The wattage is calculated by multiplying volts by amps, resulting in watts.
Wattage is typically expressed as watts per square inch (wpsi). Using Ohm's Law helps ensure that a flexible heater operates within the permissible tolerances for its application. Each type of flexible heater has specific limitations that need to be understood before selection to ensure it meets the application's requirements.
Ohm's Law describes the relationship between voltage, wattage, amperage, and resistance. It helps calculate the load that a thermostat or digital controller will switch and ensures the appropriate application of charge for the given resistance, since resistance can't be measured in an open circuit. By knowing any two of the three factors—voltage, current, and resistance—one can calculate the third.
Ohm’s Law is crucial for validating static values of circuit components, current levels, voltage supplies, and voltage drops. This knowledge is essential for correctly using a flexible heater and matching it to the intended application.
The formula for Ohm’s Law is: Current (I) = Voltage (V) / Resistance (R). In flexible heaters, determining the current strength involves calculating amperage as wattage divided by voltage. Ohm's Law is integral to flexible heater design, helping determine the resistance, measured in ohms, which is converted into heat—represented by watt density. Unlike traditional electronics, which aim to minimize heat to avoid damage, flexible heaters are designed to have higher resistance to generate more heat for the application.
Flexible heaters, made from silicone rubber or polyimide, can withstand the temperatures produced by electrical resistance. Silicone rubber endures temperatures from 221°C to 260°C (430°F to 500°F), while polyimide withstands temperatures from 149°C to 199°C (300°F to 390°F).
A band heater is a heating device that clamps onto objects to provide external heat using radiant and conductive heating. The different mounting methods of band heaters makes it possible to secure them tightly and...
A cartridge heater is a cylindrical tubular heating device that provides concise and precise heating for various forms of materials, machinery, and equipment. Unlike an immersion heater, a cartridge heater is inserted into a hole in the item to be heated to furnish internal radiant heat...
Ceramic heaters are electric heaters that utilize a positive temperature coefficient (PTC) ceramic heating element and generate heat through the principle of resistive heating. Ceramic materials possess sufficient electrical resistance and...
Electric heating is produced by using a known resistance in an electric circuit. This placed resistance has very few free electrons in it so it does not conduct electric current easily through it. When there is resistance in...
An immersion heater is a fast, economical, and efficient method for heating liquids in tanks, vats, or equipment. Known as bayonet heaters, they have heating elements that can be directly inserted into a container of water, oil, or other material in order to heat the entire contents...
Infrared heating is a heating method used to warm surrounding bodies by infrared radiation. Thermal energy is transferred directly to a body with a lower temperature through electromagnetic waves in the infrared region...
The idea of an electric heater seems to be out of place in modern society since most buildings have a sophisticated central heating system. That may be true, but electric heaters can be a helpful way of saving energy while providing efficient heating...
A heating element is a material or device that directly converts electrical energy into heat or thermal energy through a principle known as Joule heating. Joule heating is the phenomenon where a conductor generates heat due to the flow of electric current...
Radiant heaters are systems that generate heat internally and then radiate it to the nearby objects and people. The sun is a basic example of a radiant heater. When we feel warm on our bodies on a sunny day...
An AC power cord is a detachable way of providing an alternating current of electric energy from a mains power supply to an electrical appliance or equipment. Serving industries like...
Electrical plugs, commonly known as power plugs, are devices responsible for supplying and drawing current from a receptacle to the circuitry of an electrical appliance...
A NEMA connector is a method for connecting electronic devices to power outlets. They can carry alternating current (AC) or direct current (DC). AC current is the typical current found in homes, offices, stores, or businesses...
A power cord is an electrical component used for connecting appliances to an electrical utility or power supply. It is made from an insulated electrical cable with one or both ends molded with connectors...
Thomas Edison developed the power distribution system in 1882. He wrapped a copper rod in jute, a soft shiny fiber from plants, as an insulator. The jute wrapped copper rod was placed in a pipe with a bituminous compound...