Band Heaters
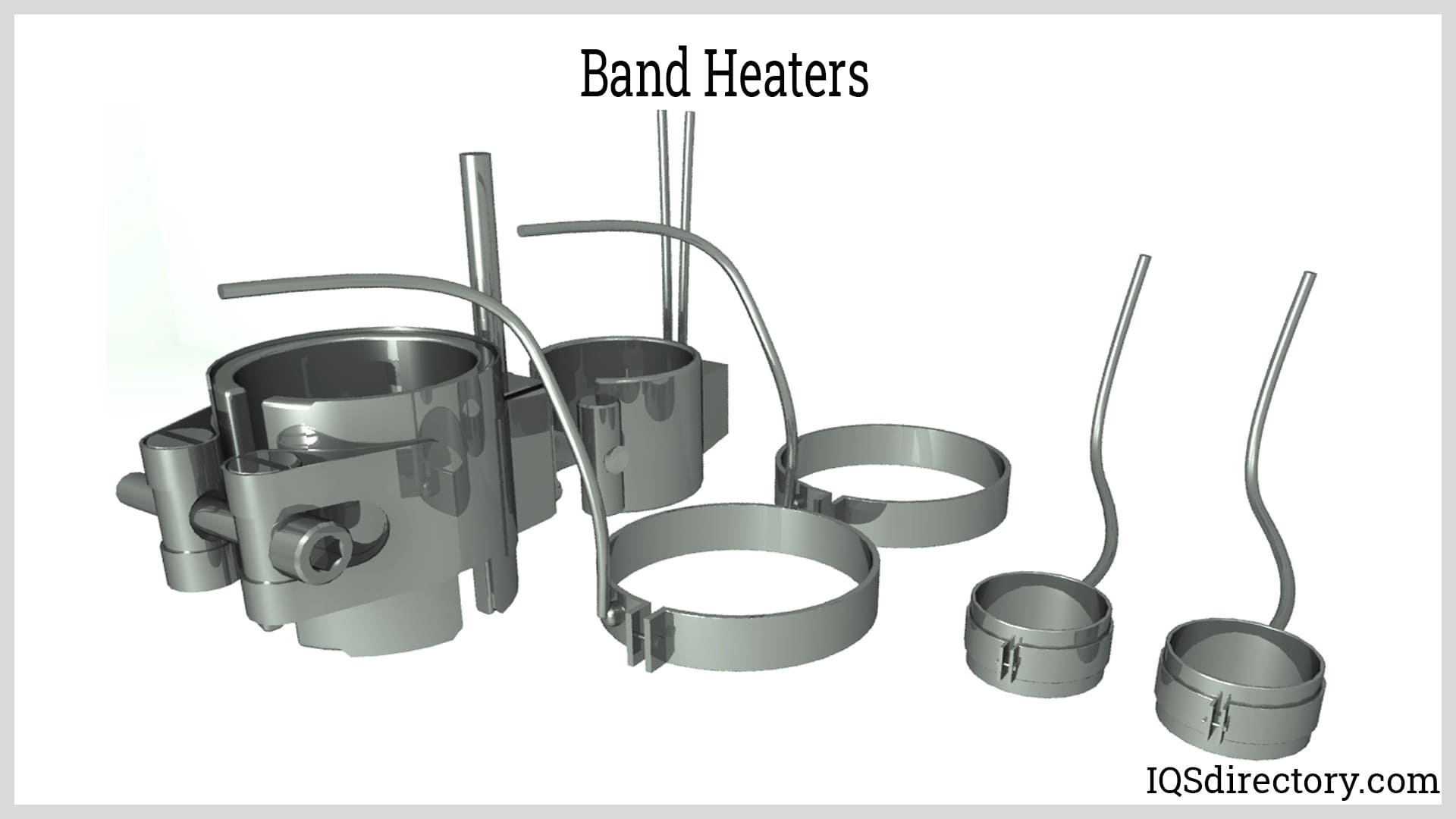
A band heater is a heating device that clamps onto objects to provide external heat using radiant and conductive heating. The different mounting methods of band heaters makes it possible to secure them tightly and...
Please fill out the following form to submit a Request for Quote to any of the following companies listed on
This article covers everything you need to know about immersion heaters.
You will learn:
An immersion heater is a fast, economical, and efficient method for heating liquids in tanks, vats, or equipment. Known as bayonet heaters, they have heating elements that can be directly inserted into a container of water, oil, or other material in order to heat the entire contents.
Immersion heaters use direct heat transfer to quickly bring liquids to the desired temperature. Composed of bundles of tubing, these heaters can be mounted on the side of a container or submerged directly in its contents. The heating coils within the heater transfer heat to the liquid, which then distributes evenly throughout the container.
Immersion heaters offer a cost-effective and environmentally friendly way to heat materials, providing a clean energy source without residual discharge or pollutants. In nuclear reactors, they are used to maintain a constant temperature of heated water for steam generation.
There are two types of immersion heaters: direct and indirect. Direct immersion heaters have their heating elements positioned directly in the liquid, while indirect immersion heaters use radiation or convection for heating. Over-the-side and in-line heaters are direct immersion heaters because their sheathed elements come into contact with the liquid. Pipe and infrared immersion heaters are classified as indirect, as they do not make direct contact with the liquid.
Immersion heaters feature an electrically resistant heating element enclosed in a protective sheath. When activated, the heating element warms the surrounding jacket, which in turn heats the sheath and subsequently the liquid. The heater's effectiveness relies on the thermal conductivity of both the jacket and the sheath.
Direct and indirect immersion heaters use two different methods for heating liquids. A direct immersion heater is inserted directly into the liquid at the top or in a fitting on the side. Its heating element comes in contact with the fluid to be heated. Once positioned, it is turned on and electricity runs through the heating element into the liquid.
An indirect immersion heater is placed inside a closed-end pipe that is then immersed in the liquid. The heating element warms the air inside the pipe, creating an oven-like effect that heats the surrounding liquid. The main advantage of this design is that the heater does not come into direct contact with the fluid, thereby preventing contamination and corrosion.
The time required to heat a material depends on both the quantity and power level of the immersion heater. Immersion heaters are designed to handle specific types of materials for optimal heating efficiency.
When examining an immersion heater, there are certain elements that have to be closely observed. They include:
Each of these factors are discussed below.
The most crucial factor regarding the sheath is the material or fluid that will come into direct contact with it, as different sheath materials respond differently to various liquids. The chart below serves as a brief guide to sheath materials. Manufacturers of immersion heaters often provide charts indicating which sheathing materials are suitable for specific applications.
Choosing the right sheath material is crucial, as its failure can result in significant problems. Corrosion is the most common type of failure, and most immersion heater manufacturers do not offer warranties against it.
Sheath Materials Selection Chart | |||
---|---|---|---|
Sheath Material | Max Sheath Temperature | Max WSI | Application |
Copper | 350°F | 55 | Clean water, water solutions non-corrosive to copper, boilers, cooling towers. |
Steel | 750°F | 22 | Immersion in oils, alkaline cleaning solutions, tars and asphalt, wax, petroleum, heat transfer mediums. |
304 Stainless Steel | 1200°F | 30 | Process water, Corrosive liquids, food processing equipment, soap, soluble cutting oils, hospital equipment. |
Incoloy | 1500°F | 40 | Air heating, radiant heating, cleaning and degreasing solutions, plating & pickling solutions, corrosive liquids, air or gas. |
Among the various sheathing materials, Incoloy, a nickel-based corrosion-resistant alloy, is the most widely used. It offers superior strength at high temperatures and is available in multiple alloy forms to accommodate a range of fluids, liquids, and chemicals.
The power density of an immersion heater must be calculated to match the specific liquid being heated. Incorrect power density can lead to overheating of the liquid and excessive heat buildup in the heater. A crucial factor is the liquid's ability to dissipate heat from the heater's element, which determines the appropriate power density.
Water effectively dissipates heat from a heating element, allowing for a higher power density. In contrast, substances like crude oil and molasses do not transfer heat as efficiently and require a lower power density, as illustrated in the power density chart below.
Typical Liquid Density | |
---|---|
Compound | Density, kg/m3 |
Drilling Mud | 1500-2000 |
Water | 1000 |
Diesel | 860 |
Gasoline | 725 |
Liquid Petroleum Gas (LPG) | 550 |
Liquefied Natural Gas (LNG) | 460 |
The next consideration is whether the heater can deliver sufficient heat to reach the desired temperature, which is determined by its wattage. Wattage is calculated based on three key factors:
This requires the greatest amount of wattage and is dependent on the method of heating such as conduction, convection, or radiation as well as the type of heater.
When the immersion heater has achieved start up, the amount of wattage required should remain constant and maintain continual heat flow.
Heat loss has to be factored into the operation of any heating device. In the case of an immersion heater, the enclosure for the liquid, the type of heater, and type of liquid determine the amount of heat loss, which can increase the required amount of wattage.
These three factors are influenced by the material and mass to be heated, the temperature difference required, and the time needed to achieve the desired temperature.
Immersion heater enclosures, casings, have normally been made from aluminum since the middle of the 20th Century. Plastic enclosures have become more popular because of plastic‘s moldability but have been of inferior quality. Most manufacturers have continued to use aluminum for its mechanical and thermal resistance.
For larger immersion heaters for uses such as atomic power plants, heavier denser metals are required.
The dark blue section in the above image is the enclosure that contains the wiring for the pictured pipe insert, indirect immersion heater.
The temperature range for immersion heaters is dependent on how it will be used. Most industrial heaters are designed to heat water to around 900° F or 482\° C. Depending on application requirements, the amount of heat will remain constant. Two key factors in the amount of heat produced are the voltage supply and resistance.
The heating element of an immersion heater is composed of a nickel-chrome alloy called nichrome, combined with refractory metals such as tungsten, molybdenum, or tantalum, and encased in stainless steel or titanium. Most heating elements are insulated with magnesium, which acts as a filler between the heating element and the sheath.
The composition of heating elements can vary based on the material being heated. For example, low alloy steels are commonly used in heating elements designed for heating oil or gas. The image below shows an immersion heater equipped with a stainless steel heating element, specifically designed for the brewing process.
Immersion heaters are employed to heat fluids for testing or to maintain materials at a desired temperature. They operate under various conditions without the need for an open flame. Electrical industrial immersion heaters have become the most prevalent heating devices used by manufacturers, largely due to environmental considerations and cost efficiency.
Freeze protection is required to keep materials from freezing in cold weather. Industries such as oil and gas, water treatment, transportation, agriculture, and mining depend on immersion heaters for that purpose. For oil based products, the problem isn‘t so much freezing but having products turning to gel or a thick wax.
Nuclear power plants utilize immersion heaters to maintain water pressure in reactors for steam production. The diagram below, provided by Wattco Manufacturing, illustrates the placement of immersion heaters in key locations within a nuclear power plant.
Low and freezing temperatures can lead to pipes at wastewater facilities becoming clogged or frozen. Immersion heaters help maintain water flow in the pipes and reservoirs, ensuring that operations continue smoothly.
Immersion heaters prevent gas and oil from solidifying into gel or wax in harsh, cold conditions. Typically, an over-the-side immersion heater is used, which can be installed without altering the existing infrastructure, as shown in the image below. These heaters are ideal for situations where insertion into the container wall is not feasible.
In the construction industry, immersion heaters are employed to accelerate the curing process. Similar to their use in heating oil and gas, over-the-side heaters are utilized to achieve faster and more consistent results.
Laboratory environments demand precise temperature control for processes such as pill drying and sterilization. Screw plug heaters are among the most commonly used, along with over-the-side versions. The image below shows a screw plug immersion heater.
In food processing, immersion heaters are primarily used to meet quality standards and government regulations. Proper moisture control is crucial to prevent the growth of bacteria and pathogens. Flange, over-the-side, and screw plug immersion heaters are used to provide heat for the sterilization of vats and containers. Immersion heaters are also commonly employed to heat vegetable oil, as illustrated in the image below.
In the chemical industry, immersion heaters are essential for maintaining chemicals at a controlled temperature and preventing freezing. Over-the-side, flange, screw-in, duct, and circulation heaters all contribute to keeping chemicals at a safe and stable temperature.
Immersion heaters are crucial for safety in the brewing industry, as they generate heat using electricity. Brewing involves the production of ethanol, which can be hazardous. Immersion heaters provide precise temperature control and are equipped with automatic shut-off features to prevent overheating. Their reliability and durability also offer significant cost savings over time.
Coatings are applied to metals to enhance their corrosion resistance. Immersion heaters support this process by delivering consistent and immediate heat, which is essential for maintaining the plating process. The image below shows a screw-in immersion heater used in the plating process.
Carbon tanks are utilized to purify water by eliminating contaminants such as chlorine, bacteria, pollutants, and other organic or chemical substances that can affect the water's smell and taste. To ensure the tanks remain free of foreign substances, an immersion heater heats the water for effective sanitization, as shown in the image below.
Starting with the basic classification of immersion heaters into direct and indirect types, they are further categorized based on their method of insertion into the material being heated. The most common types are screw plug, over-the-side, flange, and circulation heaters. Although these four are the most frequently used, advancements in technology and new innovations have led to a broader range of immersion heater varieties.
When selecting an immersion heater, it is crucial to choose one specifically designed for the material to be heated, as not all types are suitable for every solution, fluid, or material.
It is impractical to list every type of immersion heater due to the extensive variety and the constant introduction of new models. Below is a selection of some of the more common types, along with a brief description of their functions.
Pipe plug immersion heaters are intended for small to medium-sized containers with pressure ratings up to 3000 psi. They are installed by screwing directly into an opening in the tank wall and can feature sheaths made of copper, stainless steel, Incoloy, or steel. The choice of sheath material determines the types of materials they can effectively heat.
Quartz immersion heaters are designed for use in plating and acid finishing solutions, excluding those containing hydrofluoric acid or fluorides. They can tolerate a pH range of 0 to 9 and are resistant to sulfuric and hydrochloric acids. Some quartz immersion heaters come with an automatic shut-off feature that activates when a preset temperature is reached, depending on the supplier.
Circulation immersion heaters are suitable for a variety of applications, including water heating, freeze protection, heat transfer for oil, fuel oil heating, and heating of steam, air, and gas. They are designed to heat a flowing liquid through an inline or side piping setup. These units typically include a built-in heating element, heating chamber, sensor or thermostat, jacket, insulation, and inlet and outlet connections. Liquids or gases circulate through the system either by force or naturally.
Over-the-side heaters are used when through-the-tank-wall heaters cannot be installed or when heaters need to be removed for cleaning without emptying the tank. They are ideal for freeze protection, heating viscous materials, and applications in open tanks.
Flanged immersion heaters are designed for use in large containers, such as high-pressure oil storage tanks. They are attached to the unit via bolts or welds to a corresponding flange that is welded to the tank's outer wall, and they can feature either rectangular or round flanges. Flanged immersion heaters can be custom-built to accommodate specific watt densities and power ratings, and they offer a wide range of sheath materials.
Screw plug immersion heaters are perfect for situations with limited space or connection issues. They are used to prevent liquids from freezing in smaller tanks or reservoirs and come in various sizes. These heaters feature a tubular element with a threaded hex plug and some models include a thermowell for a temperature control sensor. They are installed directly through a threaded opening in the tank wall.
L-shaped immersion heaters, also known as over-the-side immersion heaters, are designed for high-temperature conditions with increased evaporation rates. They offer improved heat distribution and reduced exposure to the air. To prevent contact with the chamber walls and bottom, they are equipped with two-inch sludge legs.
Tank immersion heaters are used to heat resins and oils, helping them retain their viscosity and prevent crystalline precipitation, such as sodium hydroxide. These heaters are capable of producing temperatures up to 1000°F. The image below shows a tank heater from inside the tank.
Immersion heaters using solar power help to maintain the temperature in a water storage tank to ensure the temperature is consistent. They are a cost effective means for saving energy. The water heated by the system can serve as a hot water supply or as a means of heating, which can be seen in this diagram.
Drywell heaters are low watt density heaters designed for controlled temperature heating of temperature-sensitive materials. They can be installed in any above-ground tank and dissipate heat at as low as three watts per square inch on their sheath. These heaters help prevent coking or damage to materials that are sensitive to temperature.
Materials that benefit from drywell low watt density heating include asphalt, light and heavy fuel oils, diesel, biodiesel, glycerin, lubricating oils, hydraulic fluids, resins and epoxies, animal fats, and molasses, among others.
To install a drywell heater, follow these steps: Cut a rectangular opening near the bottom of the tank, slide the heating element and control panel assembly into position, and weld the unit into place to ensure a secure seal. The heater’s elements are housed within a sheath, allowing for maintenance without the need to drain the tank.
Another method for installing a drywell low watt heater involves inserting the heater into the tank's nozzle, serving as an alternative to the welded installation approach.
Drywell low watt electric heaters provide 100% energy efficiency, as all the energy is utilized for heating. Their flexibility allows them to be integrated and coordinated with other electrical components, enabling the reduction of heater load to a base rate. This helps prevent fluctuations in demand or peak usage, ultimately reducing consumption costs.
As environmental concerns increase, many companies are prioritizing the elimination of pollutants. Drywell low watt electric heaters help address this by eliminating the need for emission stacks, air quality monitoring, or boiler permits.
Heavy duty industrial heaters follow the same basic designs that can be found in heaters used for small vats and tanks. The main difference between heavy industrial heaters and those for other applications is their size, which can be seen in the image below from Liberty Electric Products.
This immersion heater is 240 feet long with a power rating of 2500 kW. It can be mounted using a flange and features sheath material tailored for the specific application.
Industrial immersion heaters can be installed either horizontally or vertically as inline electric heaters. They are used for a range of applications, including heating simple solutions, lubrication oil, thermal fluids, or process air. Typically, large, heavy-duty industrial immersion heaters are custom-made to meet specific customer specifications and requirements.
Regardless of a customer‘s configuration needs, industrial immersion heaters have fixed elements that use compression fittings that fit into heavy duty flanges. Terminal boxes and flanges are designed to meet customer applications.
Industrial immersion heaters are utilized in various conditions and applications, including chemical processing. They are essential for any industry that needs to regulate the temperature of materials.
While industrial immersion heaters and suction heaters serve similar functions, they apply heat differently. Suction heaters heat material as it is pumped out of the tank, whereas immersion heaters heat the container itself, making them ideal for maintaining large quantities of material at a consistent temperature.
Similar to smaller immersion heaters, industrial immersion heaters are designed to be installed in the storage tank. They feature bundles of tubing with coils that are open and immersed in the fluid.
Industrial immersion heaters differ from traditional heating devices in their design, shape, and size. The temperature controls, watt densities, and heating capacity vary depending on the type of heater and its elements.
The control box, shown in the photo, contains a thermostat and is located in a control room that oversees the system. This setup ensures safety and helps prevent malfunctions.
In manufacturing, heating is crucial for blending liquids, combining substances, or converting solids to liquids. Different industries employ various types of immersion heaters to meet their specific needs.
The fundamental structure of industrial immersion heaters is similar to that of smaller models. Below is a list of common types and the industries that utilize them.
Flanged heaters are used for water treatment, the petroleum industry, and the chemical industry.
Circulation heaters are found in the petrochemical, nuclear power plants, and the oil and gas industries.
Over-the-side heaters offer great flexibility and versatility, making them adaptable to containers of any size. Their adaptability makes them a cost-effective choice for a wide range of industries.
Screw plug heaters are utilized in the chemical industry, food and beverage production, and HVAC systems. They are effective for managing extremely cold conditions and protecting fluids.
Pipe heaters are used for low heat conditions such as wax, tar, and molasses storage. They are indirect and do not have contact with liquids.
Tank and reservoir heating is crucial for industrial product manufacturing. Immersion heaters provide essential heat to prevent fluids from freezing, maintain stability, ensure consistent flow, minimize loss or damage, and uphold safe conditions.
The cost-effectiveness of immersion heaters has made them vital for the storage, preservation, and production of products. As engineers seek ways to enhance product performance, they increasingly depend on the reliability of immersion heaters.
Listed below are some of the benefits that designers, production planners, and engineers consider when deciding to use an immersion heater.
Immersion heaters excel in heat transfer and energy efficiency. They provide a cost-effective solution for heating large volumes of liquids with minimal waste. Their basic design involves transferring energy directly into the medium, making them effective for preventing gelling and condensation.
High-temperature ceramic immersion heaters provide enhanced efficiency, capable of reaching temperatures up to 1200°C with a 98% heating efficiency in water..
Immersion heaters require minimal maintenance, making them a cost-effective choice. They operate continuously, ensuring facilities run smoothly without downtime for upkeep or repairs. With few moving parts, there is a reduced risk of mechanical failure and a lower need for cleaning and maintenance.
Cleaning an immersion heater involves the use of a pressure washer to remove sediment and do an inspection for corrosion. The process of cleaning is fast, easy, and effortless. The elements of the immersion heater below were not cleaned properly allowing build up on the heater‘s elements.
Over-the-side heaters can be removed for maintenance, eliminating the need to drain the tank to clean the heater.
Element splitting can occur during the final phase of an immersion heater’s use. Rapid corrosion of the resistor wire may break the element’s circuit, leading to slower heating. In such cases, replacing the element can be a cost-effective and efficient alternative to purchasing a new immersion heater.
Immersion heaters are versatile and can heat a wide range of materials. They offer a convenient solution for various industries, adapting easily to different conditions and materials. This flexibility and simplicity make immersion heaters widely used. Their adaptability, reliability, and durability often eliminate the need for replacement equipment when faced with unusual or unique conditions.
Immersion heaters are direct heating devices that come into direct contact with the medium they heat, making them the fastest heat transfer equipment available. They enable quicker and more efficient heating of tanks and reservoirs. Their compact design maximizes the contact surface area, thereby increasing the speed of heat transfer and distribution.
Direct heat transfer ensures that a substance quickly reaches its target temperature and maintains it with ease. The external parts and mechanics of immersion heaters facilitate easy integration into industrial settings. The placement of an immersion heater can be observed in the image below.
Immersion heaters offer greater accuracy and reliability compared to other heating options. Their direct heating capability allows them to precisely achieve the desired temperature. The even heat distribution ensures consistent temperature readings throughout the entire contents of the tank.
Temperature accuracy is crucial for mediums that must stay within a specific temperature range to maintain material usability and prevent damage or safety hazards. This is particularly important for flammable or combustible substances.
Accurate temperature readings help reduce energy consumption. For freeze protection, immersion heaters only need to operate when the temperature falls. The more precise the readings, the less frequently the immersion heater needs to run.
The ease of installation stems from their simple design, reducing the likelihood of failure or error and enhancing efficiency and reliability. This straightforward installation leads to shorter downtimes, minimizing losses and maintaining overall efficiency.
The easiest immersion heater to install is an over-the-side heater. These can be installed without halting operations and easily fit over the side of an open tank or reservoir. Additionally, they can be skid-mounted for use in multiple tanks.
Screw plug and flange immersion heaters require more effort to install. Flange heaters are welded into the tank, while screw plug heaters are screwed directly into the tank. Although this takes more time, it makes them ideal for closed tanks. Despite the additional work, the installation process remains quick and straightforward.
Existing equipment can be retrofitted with an immersion heater, enhancing efficiency and reducing operational costs without the need to replace the current equipment.
One of the main concerns for equipment installation is safety. Since immersion heaters do not have moving parts or an open flame, they don‘t produce exhaust or present a safety hazard.
When in operation, immersion heaters do not produce any sound and are far quieter than any other form of heating method.
Many heating methods rely on some form of fuel, but immersion heaters are powered by electricity and do not produce pollutants. Their lack of emissions and waste makes them eco-friendly. As the demand for fuel conservation and pollution reduction increases, many manufacturers are transitioning to immersion heaters as a more environmentally safe heating solution.
Immersion heaters have gained popularity in recent years due to rising fuel costs. Companies have had to seek cost-effective heating solutions, and immersion heaters have emerged as a top choice. They are the cleanest energy source, producing no residual discharge while delivering immediate and efficient heat transfer.
Thanks to their efficient energy use and long lifespan, immersion heaters offer a cost-effective and eco-friendly solution for heating applications.
A band heater is a heating device that clamps onto objects to provide external heat using radiant and conductive heating. The different mounting methods of band heaters makes it possible to secure them tightly and...
A cartridge heater is a cylindrical tubular heating device that provides concise and precise heating for various forms of materials, machinery, and equipment. Unlike an immersion heater, a cartridge heater is inserted into a hole in the item to be heated to furnish internal radiant heat...
Ceramic heaters are electric heaters that utilize a positive temperature coefficient (PTC) ceramic heating element and generate heat through the principle of resistive heating. Ceramic materials possess sufficient electrical resistance and...
Electric heating is produced by using a known resistance in an electric circuit. This placed resistance has very few free electrons in it so it does not conduct electric current easily through it. When there is resistance in...
A flexible heater is a heater made of material that can bend, stretch, and conform to a surface that requires heating. The various forms of flexible heaters include polyimide film, silicone rubber, tape...
Infrared heating is a heating method used to warm surrounding bodies by infrared radiation. Thermal energy is transferred directly to a body with a lower temperature through electromagnetic waves in the infrared region...
The idea of an electric heater seems to be out of place in modern society since most buildings have a sophisticated central heating system. That may be true, but electric heaters can be a helpful way of saving energy while providing efficient heating...
A heating element is a material or device that directly converts electrical energy into heat or thermal energy through a principle known as Joule heating. Joule heating is the phenomenon where a conductor generates heat due to the flow of electric current...
Radiant heaters are systems that generate heat internally and then radiate it to the nearby objects and people. The sun is a basic example of a radiant heater. When we feel warm on our bodies on a sunny day...
An AC power cord is a detachable way of providing an alternating current of electric energy from a mains power supply to an electrical appliance or equipment. Serving industries like...
Electrical plugs, commonly known as power plugs, are devices responsible for supplying and drawing current from a receptacle to the circuitry of an electrical appliance...
A NEMA connector is a method for connecting electronic devices to power outlets. They can carry alternating current (AC) or direct current (DC). AC current is the typical current found in homes, offices, stores, or businesses...
A power cord is an electrical component used for connecting appliances to an electrical utility or power supply. It is made from an insulated electrical cable with one or both ends molded with connectors...
Thomas Edison developed the power distribution system in 1882. He wrapped a copper rod in jute, a soft shiny fiber from plants, as an insulator. The jute wrapped copper rod was placed in a pipe with a bituminous compound...