Radiant Heaters
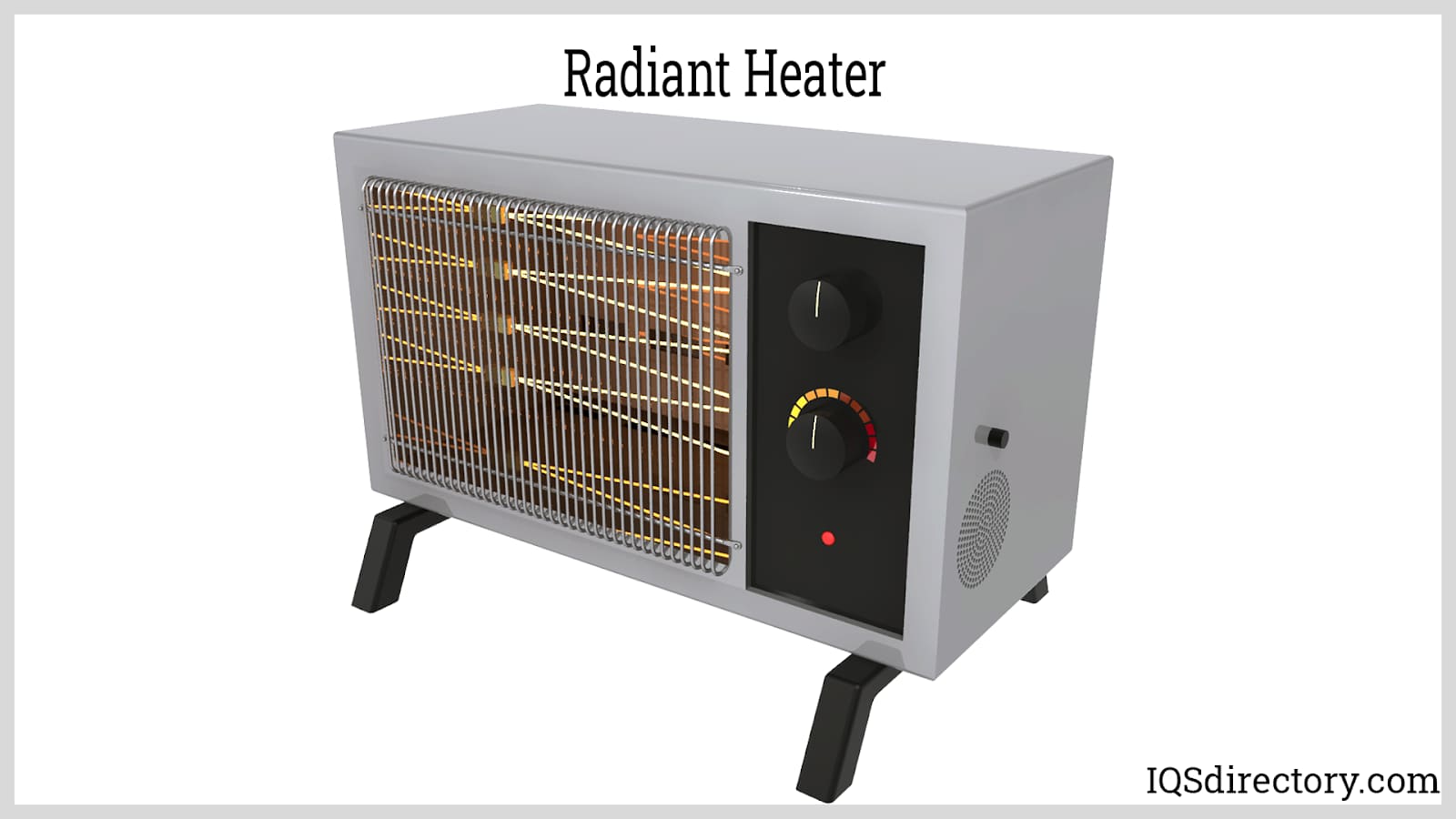
Radiant heaters are systems that generate heat internally and then radiate it to the nearby objects and people. The sun is a basic example of a radiant heater. When we feel warm on our bodies on a sunny day...
Please fill out the following form to submit a Request for Quote to any of the following companies listed on
This article presents all the information you need to know about infrared heaters.
Read further and learn more about:
Infrared heating employs electromagnetic waves to convey energy directly to materials, eliminating the need to warm the air between the infrared source and the target. The released infrared energy generally ranges from 0.7 microns (µ) to 6 µ. By choosing specific wavelengths, energy consumption is optimized, making the heating of the material more efficient.
This heating technique transfers heat directly into materials while keeping the surrounding air at a cooler temperature. Consequently, infrared heaters are appreciated for their energy efficiency, user convenience, and health advantages. They can be powered by electricity, natural gas, or propane, providing a cost-effective and efficient heating solution.
Infrared electromagnetic waves cover an extensive range of wavelengths, from 780 nm to 10 microns in various industrial settings. The shorter the wavelength, the higher the frequency and energy. Infrared heating can generate temperatures between several hundred degrees Celsius and up to 6,512°F (3,600°C).
Recent innovations have expanded the application of infrared heating technology. Today, modern infrared heaters come equipped with a wide array of features and designs to meet the varied demands of industrial, commercial, and residential settings. They are utilized for heating spaces such as homes, offices, garages, and warehouses. Industries leverage infrared heaters for operations such as drying, curing, printing, and thermoforming. In healthcare, infrared heaters are applied in physiotherapy to assist rehabilitation processes.
The infrared spectrum was initially identified by Sir William Herschel, a British-German astronomer, during the early Industrial Revolution (1760-1840). The concept of infrared heating was acknowledged but was not widely adopted until World War II. During this time, the military used infrared heating for drying paints and lacquers on equipment, finding it extremely efficient compared to fuel-intensive convection ovens, which were both costly and a drain on fuel resources.
Infrared heaters were prevalent in workshops and factories during the war. Nevertheless, their use declined after World War II as central heating systems gained popularity.
As focus shifted towards eco-friendly technologies, the development of infrared heaters picked up pace again from the late 20th to the early 21st century. This period saw a considerable expansion in the applications of infrared heating. Advances in design and configuration enabled the installation of infrared heaters across various environments, from residential homes and office spaces to large industrial plants. Technological progress and improved control mechanisms have facilitated the ongoing evolution and widespread acceptance of infrared heating solutions.
Infrared heat is a fundamental form of radiant heating that involves the direct transfer of thermal energy from an infrared heater to an object or material, bypassing the need to first warm the surrounding air. This heating method closely replicates the way the sun warms the Earth—delivering natural, efficient, and comfortable warmth to people, surfaces, and workspaces. As a result, infrared heating technology has become increasingly popular in both residential and industrial applications, including space heaters, patio heaters, and industrial process heating.
In an infrared heater, specialized heating panels or elements are heated to a temperature that allows them to emit infrared radiation. This radiation travels through the air until it strikes a solid object, such as furniture, people, or industrial materials, and directly transfers heat to that object. This process mirrors the way radiant heat is transferred between metals and coils using electromagnetic waves, ensuring rapid, targeted heating and minimal energy loss compared to convection-based systems.
Unlike traditional convection heating methods—which warm the air first before transferring heat to objects in the space—infrared heaters are engineered to project radiant heat directly to surfaces, people, or machinery. This approach enables infrared heating systems to quickly raise the temperature of surfaces with minimal energy consumption. As a result, businesses and homeowners benefit from energy-efficient heating, reduced operating costs, improved indoor air quality, and consistent warmth—making infrared heaters a cost-effective and highly efficient solution for a wide range of heating needs.
Electromagnetic waves are composed of oscillating fields that are perpendicular to one another: one is the electric field and the other is the magnetic field. These waves represent the underlying mechanism for infrared energy transmission and are fundamental to the operation of all infrared heating devices.
These waves are characterized by their wavelength and frequency. Wavelength refers to the distance between consecutive crests of a wave, and is measured in nanometers or angstroms within the context of the electromagnetic spectrum. Frequency, measured in Hertz (Hz), indicates the number of wave cycles per second and is used to categorize different types of electromagnetic waves, including ultraviolet, visible light, and infrared radiation.
There is an inverse relationship between wavelength and frequency: as the frequency increases, the wavelength shortens, and vice versa. A wave's energy increases with higher frequency and shorter wavelength. Therefore, high-frequency, short-wavelength waves deliver more energy and are more effective in heat transmission, while low-frequency, long-wavelength waves carry less energy.
Electromagnetic waves differ from mechanical waves in that they do not require a physical medium to travel; mechanical waves, such as sound waves, rely on media like air or water for propagation. In contrast, electromagnetic waves—including infrared rays—can traverse a vacuum. This explains why we feel the sun’s radiant heat across vast distances and experience temperature increases under direct sunlight. Infrared heaters leverage the same physical principles as solar heating to provide highly efficient warmth indoors and outdoors.
Infrared radiation occupies the segment of the electromagnetic spectrum situated between visible light and microwave radiation. The wavelengths of infrared waves span from 700 nanometers (approximately 430 terahertz) to 1 millimeter (about 300 gigahertz), covering a diverse range of energy levels. This positions infrared waves perfectly for heat transfer applications in both commercial and industrial settings.
The infrared spectrum encompasses several categories, each optimized for different infrared heating applications—such as near-infrared heating (NIR) for fast-response industrial processes, mid-wave infrared heating (MWIR) for drying and curing, and far-infrared heating (FIR) for space and comfort heating. Below is a classification table illustrating the main regions of the infrared spectrum, which helps guide material selection and heater design for specific projects:
Classification of Infrared Waves | |||||
---|---|---|---|---|---|
Region | Abbrevation | Wavelength(μm) | Frequency(THz) | Photo Energy(meV) | Temperature Range(°F) |
Near-Infrared | NIR | 0.75-1.4 | 214-400 | 886-1653 | 6495.8 to 3266.6 (3591-1797°C) |
Short Wavelength Infrared | SWIR | 1.4-3 | 100-214 | 413-886 | 3266.6 to 1279.4 (1797-693°C) |
Mid-Wavelength Infrared | MWIR | 3-8 | 37-100 | 155-413 | 1279.4 to 192.2 (693-89°C) |
Long-Wavelength Infrared | LWIR | 8-15 | 20-37 | 83-115 | 192.2 to −112 (89 - −80°C) |
Far Infrared | FIR | 15-1000 | 0.3-20 | 1.2-83 | −112.27 to −454.27 (−80.15 - −270.15°C) |
Infrared waves are leveraged in a variety of applications, including highly efficient radiative heating, infrared thermal imaging, remote sensing, and wireless communications. In heating, the type of infrared used can affect factors such as penetration depth, heating efficiency, speed of response, and suitability for materials processing.
When choosing an infrared heater—whether for residential underfloor heating, outdoor patio areas, industrial ovens, or drying processes—understanding the wavelength region is crucial to ensuring optimal performance and energy efficiency. For instance, far-infrared panels are well-suited for space heating and provide gentle, even warmth, while short-wave and near-infrared heaters are ideal for processes demanding rapid and intense heating.
Radiation is the process of heat transfer via the emission, absorption, and reflection of electromagnetic waves—including infrared radiation—from objects with a temperature above absolute zero (0 Kelvin or -459.4°F). All objects constantly emit some level of thermal radiation due to the molecular motions and collisions of their atoms, molecules, and subatomic particles such as protons and electrons.
The amount and wavelength of thermal radiation an object emits varies based on its temperature and surface properties, which helps explain the variety of specialized infrared heating systems for distinct uses. As temperature increases, objects radiate more thermal energy, making infrared heaters highly effective for quickly and directly delivering heat where needed. Radiant heating does not require heating air molecules, which enhances energy efficiency and provides instantaneous comfort.
Besides radiation, there are two other primary mechanisms for heat transfer: conduction and convection. Conduction involves the transfer of thermal energy through direct contact between molecules or atoms—common in solid materials. Heat flows from regions of higher to lower thermal or kinetic energy during conduction, making this method prevalent in metal objects and building structures.
Convection, by contrast, involves the transfer of heat through the movement of fluid or gas molecules. When part of a fluid (air or liquid) is heated, it expands and becomes less dense, causing it to rise and set up convection currents that transport heat throughout the environment. While convection is effective in large spaces, it is less precise and often leads to uneven heating—an issue that infrared heaters overcome by providing direct and targeted warmth.
Infrared heating systems are composed of two primary components: a heating element (often made of tungsten, quartz, or ceramic) that converts electrical energy or fuel-derived chemical energy into thermal energy, and a reflector that directs the emitted infrared waves toward targeted objects. This simple but effective design allows for both portable and fixed infrared heaters to deliver consistent, zoned heating solutions.
The efficiency and performance of an infrared heater depend heavily on the quality and design of the reflector. Reflectors with high reflectivity maximize the transmission of radiant heat while reducing heat loss and minimizing energy waste. Shapes, surface finishes, and materials are engineered to focus and channel infrared waves outward, maximizing coverage and minimizing hotspots. To withstand demanding environments, ideal reflectors must be highly resistant to corrosion, able to operate at elevated temperatures, and easy to maintain for long-term reliability.
Common materials used for reflectors include aluminum, stainless steel, ceramic, and quartz, each offering a blend of heat resistance, lightweight construction, and reflectivity. Advanced models may include gold or ruby coatings to further optimize reflectivity and concentrate the heat output for precision processes. The choice of heating element—such as carbon fiber, halogen, or quartz tube heaters—can also tailor performance for specific applications or industries.
For users evaluating infrared heaters for their specific needs, it’s essential to consider factors such as wattage, heater type (panel, tube, lamp), mounting options, coverage area, safety certifications, and compatibility with smart controls or building automation systems. Purpose-built heaters are available for a wide range of applications—from garage and workshop heating to commercial facility climate control, food processing, paint curing, and moisture removal. By understanding the underlying operating principles of infrared heaters and matching the technology to your environment, you can achieve energy savings, improved comfort, and reliable, targeted heating for any application.
Flameless heating is essential in a diverse range of industrial settings, supporting core processes such as drying, surface preparation, curing, and improving manufacturing workflow efficiency. These applications frequently require reliable, precise temperature control to ensure optimal product quality and minimize energy costs. As advanced thermal processing technologies continue to evolve, contemporary manufacturing increasingly depends on infrared heating systems for their ability to deliver controlled, uniform heat—meeting the stringent demands of modern production environments while boosting operational cost-efficiency and overall productivity.
Industrial infrared heating systems are engineered to rapidly and uniformly heat a variety of surfaces and materials. Once activated, these high-efficiency heaters emit targeted infrared energy—ideal for applications requiring instant, consistent heat, such as industrial stamping, metal pressing, plastic welding, and composite curing. By employing infrared heaters, manufacturers can significantly reduce operational costs through energy savings while reliably delivering the precise heating required for numerous specialized processes. Industries from automotive manufacturing and aerospace to electronics and plastics leverage the power of infrared heat for increased output with lower environmental impact.
Many industrial production lines employ coatings—ranging from paints and adhesives to powder coatings and protective chemical films—that are either sprayed, brushed, or electrostatically applied to metal, plastic, or composite parts. To ensure consistent coating adhesion, appearance, and durability, the method used to dry or cure these layers is critical. Infrared drying technology is widely implemented for both fast and uniform results across a broad range of material surfaces.
When working with liquid coatings, industrial infrared heaters play a key role by accelerating the drying process, promoting a flawless, bubble-free, and uniform surface finish. In powder coating operations, while traditional air drying is inefficient, infrared heaters enhance the crucial gel and cure phases—melting and bonding powder particles into a cohesive, durable layer—drastically shortening production cycles and improving throughput. This makes infrared drying and curing a preferred choice in sectors like automotive, appliances, and heavy machinery manufacturing. Additionally, advanced infrared systems can contribute to VOC (volatile organic compound) emissions reduction, helping organizations comply with rigorous environmental standards.
Infrared welding has become a standard technique for joining thermoplastic components in various manufacturing sectors. Used extensively to seal and assemble plastic parts—such as fan blades, housings, automotive components, and fluid-handling systems—infrared welding delivers a clean join by softening material surfaces for seamless bonding without introducing particulates, residue, or mechanical stress. This technique is especially valuable for manufacturing high-integrity plastic containers, ducts, and pressure vessels.
In certain plastic fabrication processes, infrared preheating is combined with vibration welding, which involves applying controlled vibration and pressure to weld parts together. By using infrared heat to prepare surfaces before vibration, manufacturers achieve superior weld strength, enhanced structural reliability, and significantly reduced risk of particle generation—a crucial benefit in industries like medical device production and food packaging where contamination control is essential.
For precision manufacturing applications such as embossing and laminating, controlled and uniform heating is critical to avoid material warping or surface defects, particularly at edges or on composite layers. Infrared heaters provide the exact, even heat necessary to condition surfaces, ensuring optimal process results and minimal material loss. Manufacturers in sectors such as automotive and consumer electronics depend on infrared technology for rapid and consistent preheating prior to embossing or laminating procedures.
Within the automotive industry and beyond, infrared laminating ovens efficiently fuse multiple layers of material—like plastic, vinyl, or specialty foils—to substrates, enhancing overall protection, durability, and surface aesthetics. Frequently, complex automotive components such as car doors, consoles, and dashboards are assembled with layered foils, and infrared heat ensures the adhesive bonds are strong and cycle times remain fast. The use of infrared heaters in these processes conserves energy, reduces product defects, and meets the growing demand for lightweight composite materials in industrial design.
Industrial infrared heaters are available in three primary types: quartz, ceramic, and metal-sheathed. Each type is engineered to produce electromagnetic infrared radiation for process heating, with devices capable of generating temperatures from 1300 °F to 1600 °F (704 °C to 871 °C), and, in the case of some metal-sheathed units, even higher. Selecting the appropriate industrial infrared heater supports optimal system efficiency, throughput, and product quality, depending on application-specific requirements such as wavelength, heating rate, and durability.
When choosing an industrial infrared heater, it is essential to consider factors such as energy efficiency, wavelength match for the materials and process, safety certifications, and long-term maintenance requirements. By integrating the right type of infrared heating technology, manufacturers enhance quality control, reduce operational costs, and achieve faster production turnaround—critical factors for staying competitive in sectors such as electronics, plastics, automotive manufacturing, textiles, and food processing.
Infrared heaters can additionally be categorized according to the wavelength of the infrared radiation they produce:
NIR heaters instantaneously warm the environment and are typically used in outdoor heating applications.
Infrared heaters can also be identified based on the materials used in their construction. Here are a few examples:
Below are some types of infrared heaters classified by their specific uses:
Infrared heaters offer versatility, simple installation and maintenance, and come in various designs to meet different requirements. The advantages of infrared heating include:
Despite their many advantages, infrared heaters pose some safety risks. The hot core material of an infrared heater needs to be managed to effectively radiate heat, which can lead to severe burns if touched or if there is prolonged exposure at a close range. Directly viewing the intense glow from high-powered infrared heaters can potentially harm vision. Implementing engineering controls and maintaining vigilance can help prevent injuries. However, these drawbacks are outweighed by the numerous benefits that infrared heaters offer.
Radiant heaters are systems that generate heat internally and then radiate it to the nearby objects and people. The sun is a basic example of a radiant heater. When we feel warm on our bodies on a sunny day...
A band heater is a heating device that clamps onto objects to provide external heat using radiant and conductive heating. The different mounting methods of band heaters makes it possible to secure them tightly and...
A cartridge heater is a cylindrical tubular heating device that provides concise and precise heating for various forms of materials, machinery, and equipment. Unlike an immersion heater, a cartridge heater is inserted into a hole in the item to be heated to furnish internal radiant heat...
Ceramic heaters are electric heaters that utilize a positive temperature coefficient (PTC) ceramic heating element and generate heat through the principle of resistive heating. Ceramic materials possess sufficient electrical resistance and...
Electric heating is produced by using a known resistance in an electric circuit. This placed resistance has very few free electrons in it so it does not conduct electric current easily through it. When there is resistance in...
A flexible heater is a heater made of material that can bend, stretch, and conform to a surface that requires heating. The various forms of flexible heaters include polyimide film, silicone rubber, tape...
An immersion heater is a fast, economical, and efficient method for heating liquids in tanks, vats, or equipment. Known as bayonet heaters, they have heating elements that can be directly inserted into a container of water, oil, or other material in order to heat the entire contents...
The idea of an electric heater seems to be out of place in modern society since most buildings have a sophisticated central heating system. That may be true, but electric heaters can be a helpful way of saving energy while providing efficient heating...
A heating element is a material or device that directly converts electrical energy into heat or thermal energy through a principle known as Joule heating. Joule heating is the phenomenon where a conductor generates heat due to the flow of electric current...