Aircraft Cables
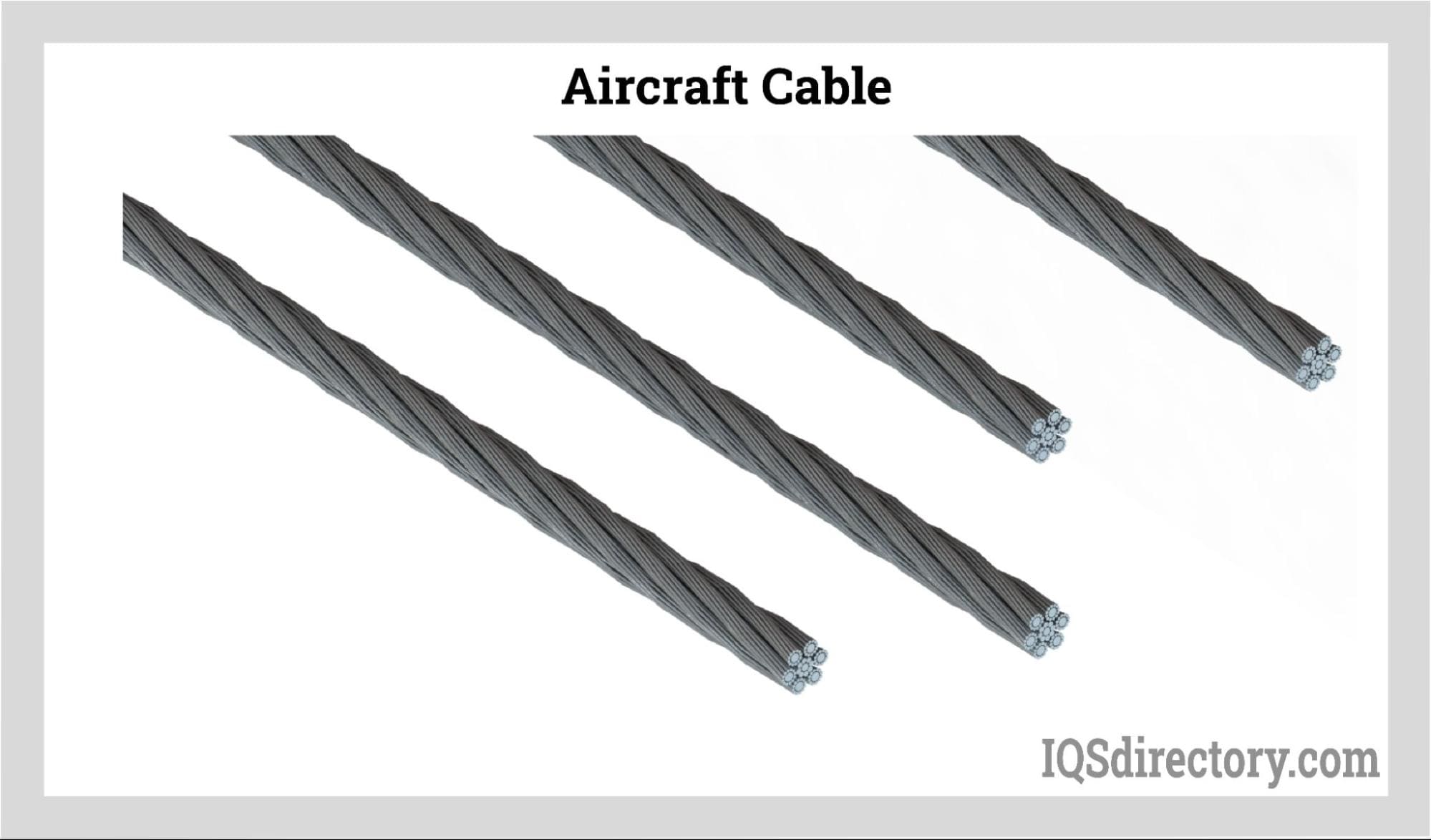
An aircraft cable is a style of highly durable cable that is used for aircraft flight controls and other applications and is differentiated from normal cables by its diameter, stranding, and wires, which provide...
Please fill out the following form to submit a Request for Quote to any of the following companies listed on
This article takes an in depth look at electric hoists.
Read further and learn more about topics such as:
Electric hoists are engineered specifically to lift, lower, and transport materials and products efficiently. Operated by an electric motor and featuring a control system for managing lifting configurations, they excel in handling substantial loads. These hoists become particularly advantageous in situations where conveyors and cranes may not be feasible or suitable. In addition to electric hoists, pneumatic (air) hoists, hydraulic hoists, and manual hoists exist, each defined by its unique power source.
Typically mounted overhead to facilitate object lifting, electric hoists require a power source, making them most effective in indoor settings. You'll often find them in use in environments such as warehouses, automotive repair sites, machining shops, and manufacturing plants. Some models are ruggedly designed to withstand hazardous and high-temperature environments, while others are suited for cleanroom applications, ideal for handling sensitive items like food and pharmaceuticals. Strict adherence to safety protocols is essential when operating electric hoists across any setting.
By automating lifting and positioning duties, electric hoists significantly enhance operational productivity, minimize manual labor, and improve workplace ergonomics. They generally boast faster operation than other hoist varieties and offer a more cost-effective and space-saving alternative to conveyor systems.
Manual chain hoists are a fundamental and widely-used type of lifting equipment in industrial and commercial settings. By leveraging mechanical advantage, a manual chain hoist transforms a low input force and high travel distance into a high lifting force with a low output distance—enabling operators to lift, suspend, or lower heavy loads safely. This engineering principle, combined with the use of durable lifting chains and precision gears, is what makes manual chain hoists a cost-effective choice for many material handling applications, including maintenance, construction, and warehousing. Because operation relies on manual power, these hoists move slower but allow for precise load positioning.
A manual chain hoist is installed above the object to be lifted, either by hooking or mounting it on a strong, stable frame or overhead beam. Once in place, the hoist uses two distinct chains: the hand chain (for manual operation) and the load chain, which is typically crafted from heat-treated steel for increased strength and durability suited for repeated lifting cycles. The longer hand chain is pulled by the operator, while the shorter load chain connects directly to the object’s lifting point. To begin the lifting process, a grab hook is secured to the load. The operator, standing clear of danger zones, pulls the hand chain, rotating the cog and engaging the driveshaft. This, in turn, actuates a system of gears with strategically varied teeth counts to maximize mechanical advantage. Force is gradually concentrated from smaller, faster gears to larger, slower ones, enabling efficient and controlled lifting of even extremely heavy machinery or materials. The resulting output turns a sprocket which draws the load chain upward, hoisting the attached object safely.
A key safety feature in manual chain hoists is the ratchet mechanism, acting as a reliable brake. The clutch tightly engages with the ratchet’s teeth, locking the load in position and preventing unexpected descent. As the cog is rotated in the lowering direction, the clutch disengages, allowing for controlled release and descent of the load. Proper use of ratchet and clutch systems is essential for maintaining safety and meeting OSHA hoist safety standards in the workplace.
Today, manual chain hoists are often chosen for lighter-duty or intermittent lifting requirements where portability, ease of installation, and minimal maintenance are prioritized. For more demanding material handling operations—or where ergonomic concerns and productivity are critical—electric hoists (such as electric chain hoists and wire rope hoists) provide greater speed and mechanical power, supporting higher duty cycles, complex lifting arrangements, and integration into overhead crane systems. These versatile alternatives accommodate diverse applications across manufacturing, automotive assembly, logistics, maintenance, and more.
Electric chain hoists are an essential category of powered lifting equipment engineered to enhance productivity, reduce manual strain, and provide precise control over lifting and lowering operations. These hoists utilize a heavy-duty load chain to suspend and elevate equipment, raw materials, or finished goods. Powered by an industrial-grade electric motor, the system converts electrical energy into mechanical force, enabling operators to reliably lift weights far exceeding human capabilities—ranging from several hundred pounds to several tons. The motor is housed within a rugged heat-dissipating shell, commonly fabricated from lightweight yet robust aluminum alloy. To counteract heat generated during continuous operation, integrated cooling fans maintain optimal temperatures, making these hoists suitable for intensive use and high-temperature industrial environments.
For safe and effective use, electric chain hoists must be properly mounted above the load—typically via a beam clamp, ceiling mount, or mobile gantry. The hook at the end of the load chain securely attaches to slings, lifting eyes, or other approved load points on heavy objects. The lift cycle begins with the operator engaging a push button or pendant controller, which activates the hoist motor and brake system. The brake ensures accurate positioning and load holding, preventing any unscheduled movement and meeting key material handling safety requirements. As the motor generates torque, this rotational force is transmitted by a highly efficient gearbox to the chain wheel, causing it to rotate and draw the load chain upwards. Excess slack from the load chain is neatly collected in a durable chain bag, constructed from reinforced nylon or polypropylene, maintaining clear work zones and minimizing tangling risks. Lubrication of the load chain is essential for preventing wear and sustaining long-term operational reliability.
To prevent overloading and enhance equipment protection, most electric chain hoists are equipped with an advanced limit switch—automatically interrupting operation if a load is raised or lowered beyond pre-set travel boundaries, or if the hoist’s rated capacity is exceeded. Additional features may include thermal overload protection, emergency stop controls, remote operation, and compatibility with overhead trolley systems for traversing loads horizontally along crane rails. Modern electric chain hoists offer simple installation and low maintenance compared to wire rope variants, making them an ideal solution for production lines, warehouses, assembly plants, and fabrication facilities needing cost-effective, reliable lifting capability.
Electric wire rope hoists are designed for heavy-duty industrial material handling, incorporating a high-strength wire rope as the main lifting element. Wire ropes are composed of a tough central core, such as fiber or steel, encompassed by tightly wound strands of high-tensile steel, stainless steel, or exotic alloys like Monel or bronze. This robust construction ensures exceptional flexibility, resistance to abrasion, and the ability to handle substantial vertical loads—making electric wire rope hoists preferred for demanding jobs such as steel manufacturing, shipbuilding, foundries, construction, and infrastructure projects. Specialized models are available for hazardous or corrosive environments where superior chemical resistance is needed.
Functionally, electric wire rope hoists use an integrated hoist motor and sophisticated braking system for reliable load control. The motor’s torque is channeled through a heavy-duty gearbox that amplifies force, which is then delivered to a hardened spline shaft and transferred onto a winding drum. As the drum rotates, the wire rope winds onto helical grooves while a precise rope guide ensures the wire rope is evenly distributed, minimizing the risk of tangles or uneven loading. This design enables smooth, high-capacity lifting over extended heights—often far exceeding the capabilities of electric chain hoists. Regular inspection and lubrication of the wire rope are required to reduce friction and maximize lifespan.
Modern electric wire rope hoists incorporate intelligent controls and redundant safety systems, including upper and lower limit switches, load sensors, and programmable controls for fine lift regulation. Many are fully compatible with bridge crane and gantry crane systems, offering seamless integration for moving large loads across shop floors or shipping yards. Their superior lifting speed, higher duty cycle, and ability to support loads over longer distances make electric wire rope hoists the solution of choice for efficient, continuous industrial lifting operations. However, the increased lifting capacity and advanced engineering often result in a higher price point compared to electric chain hoists.
Winches and hoists are closely related pieces of rigging equipment used for moving and positioning loads but are optimized for different lifting and pulling applications. Winches are primarily designed for horizontal pulling—dragging or hauling heavy objects across surfaces or inclines—whereas hoists are engineered for vertical lifting, raising loads off the ground. This functional distinction is critical in industrial and construction environments where safety, efficiency, and adherence to proper lifting protocols are paramount.
Structurally, winches and hoists share core similarities: both utilize robust steel cable (or chain, in some cases) wound around a heavy-duty drum, generating tension as the drum rotates. Power sources can be manual (hand-cranked), electric, hydraulic, or pneumatic, allowing for flexibility based on site requirements and available infrastructure. Winches frequently rely on dynamic gear braking systems to hold a static load in place, particularly on slopes, while hoists integrate more comprehensive safety interlocks and load brakes for secured vertical lifting.
In operation, a winch’s hook is attached directly to the load, often with the winch cable passing through dedicated rigging points or slings. The locking mechanism is temporarily disengaged to pull out the required cable length before attaching the hook. Unlike hoists, using a winch cable as a sling or loop for lifting is generally not code-compliant and risks safety violations. Winches are particularly favored for applications such as vehicle recovery, marine mooring, pipeline hauling, stage rigging, and utility cable installations, where precise horizontal force is needed.
For loads that require vertical movement but do not exceed moderate weight limits, winches can be adapted using pulley blocks or sheave assemblies to redirect the cable upward, effectively simulating hoisting action. Variations include floor-mounted and wall-mounted winch systems used in theater production, material staging, or light equipment lifting.
High-capacity industrial winches are essential in industries such as shipbuilding, offshore oil and gas, mining, and logistics. These units feature variable drum configurations (single-drum, double-drum, or split-drum), integrated overload and emergency stop features, and load monitoring technology for optimal performance and enhanced workplace safety. With pulling capacities from 10 or 15 kN (kilonewton) to beyond 200 kN, selecting the proper winch involves careful assessment of line pull, duty cycle, environmental factors, and power supply options—ensuring the system aligns with both application needs and regulatory requirements.
Electric hoists, a critical component in material handling, can be categorized based on the suspension method used to position them above the load. The suspension method is essential for optimizing load stability and preventing operational hazards in lifting applications across manufacturing, warehousing, and construction industries.
Hook-mounted electric hoists feature a top hook integrated with a safety latch, enabling temporary yet secure attachment to a beam clamp or trolley. As the most basic type of hoist suspension, this system offers maximum portability for diverse lifting operations and is well-suited for environments where mobility is essential. The safety latch on the hoist hook ensures the load remains secure and reduces the risk of accidental release—a critical factor for safety compliance on job sites and factory floors.
Lug-mounted hoists are permanently attached by bolting their reinforced top section to a wall, building structure, or overhead beam, thus providing exceptional stability for repetitive, high-capacity operations. This fixed suspension supports consistent load alignment and facilitates safe lifting of heavy machinery or materials during assembly line or production processes. While primarily stationary, some lug-mounted hoists can be repositioned to accommodate evolving workspace layouts.
Trolleys are essential material handling accessories that, when paired with electric hoists, facilitate lateral movement along a runway beam or crane system. They enable precise positioning of loads and streamline transportation across assembly zones or loading docks. Trolley selection depends on load requirements and desired control level in industrial overhead lifting operations.
Push-type trolleys (also known as plain trolleys) are manually operated, allowing personnel to move the electric hoist horizontally along the beam by pushing or pulling it. These trolleys are suitable for lighter loads and applications where frequent repositioning is not a priority. However, manual operation can limit accuracy and handling efficiency for complex or heavy-duty lifting tasks.
Geared trolleys enhance manual transportation by incorporating a hand chain mechanism that operators pull to precisely guide the hoist and suspended load along the runway beam. This provides improved control over movement—crucial for safe handling of delicate materials or when maneuvering around obstacles. Geared trolleys are commonly used in workshops, maintenance areas, and heavy industry.
Electric travel trolleys are engineered for rapid, effortless load positioning and higher productivity. Powered by electric motors and controlled via the hoist's integrated control panel or pendant, these trolleys offer variable travel speeds and smooth acceleration for precise, automated movement along the crane beam. They are ideal for operations that demand frequent lifting, long travel distances, or integration into automated overhead crane systems, such as manufacturing plants, logistics centers, and fabrication shops.
The beam system forms the structural foundation for overhead crane and hoist operations. The support beam, or runway beam, must be engineered to withstand the combined weight of the electric hoist, lifting trolley, and maximum load. I-beams, wide-flange beams, and patented track beams are common steel profiles chosen for their strength, durability, and compatibility with hoist and trolley assemblies. Selecting the appropriate beam type involves analyzing load distribution, span length, and frequency of use—critical considerations for plant engineers and safety managers. Furthermore, matching the specifications and dimensions of both the beam and trolley to the chosen electric hoist model ensures smooth, vibration-free operation and extends the system's service life.
Key structural specifications—such as rated capacity, working load limit (WLL), duty cycle, beam deflection, and mounting compatibility—must be carefully evaluated to ensure the safe and efficient operation of industrial electric hoists in diverse lifting environments.
The rated capacity, often referred to as lifting capacity, defines the maximum weight an electric hoist or crane system can safely handle before risking mechanical failure. This critical parameter is determined by the hoist motor's power, transmission efficiency, frame rigidity, and the strength of the load chain or wire rope. To ensure workplace safety and compliance with industry standards such as ASME and OSHA, always verify the tag-listed rated capacity and avoid exceeding manufacturer specifications during any hoisting application.
The working load limit (WLL) is the maximum mass that the hoist can consistently and safely lift when all operational and environmental safety factors are considered. The WLL is calculated by applying a safety factor to the minimum breaking load of the chain, wire rope, or lifting components. Key factors influencing WLL include the hoist's design, operator competency, usage frequency, and environmental conditions such as temperature and corrosion. Adhering strictly to WLL ratings protects personnel, equipment, and materials from the dangers of overload incidents.
The duty cycle, or operational cycle, describes how long the electric hoist can run within a specified time frame without risk of overheating or mechanical wear. Expressed as a percentage, the duty cycle is fundamental to selecting the right hoist for repetitive industrial lifting, assembly, or maintenance tasks. For heavy-duty production lines or continuous-use environments, choosing an electric hoist rated for high-duty cycles (e.g., H4 or higher) assures reliable performance and minimizes downtime due to equipment fatigue. Exceeding the recommended duty cycle can result in premature failure, increased maintenance, and safety hazards.
Lifting speed and travel speed are additional specifications that directly impact productivity, efficiency, and workflow optimization. Consider your material handling application’s cycle time, precision needs, and load type when selecting the appropriate speed settings for both hoist lift and trolley travel.
Lifting speed refers to the vertical velocity at which a load is raised or lowered by the electric hoist. Hoists can offer fixed or variable speed lifting, typically controlled via a pendant or remote system. Slow lifting speeds are advantageous for handling fragile, irregular, or extremely heavy loads requiring careful maneuvering, while higher speeds enhance efficiency in straightforward material transport or repetitive assembly operations. Balancing lifting speed with load type and operator proficiency helps maximize output and prevent damage to sensitive equipment or materials.
Travel speed measures the horizontal rate at which the electric trolley, and thereby the load, moves along the runway beam. Adjustable travel speeds improve control over positioning in congested workspaces or with precise pick-and-place requirements. Fast travel speeds boost overall throughput in high-volume storage, shipping, or warehouse environments. Modern hoist control systems may feature speed modulation for both safety and operational flexibility.
Beyond the technical specifications, users should assess power requirements (single-phase vs. three-phase electric supply), environmental exposure (indoor or outdoor operations, humidity, dust), control system compatibility (manual pendant controls, wireless remotes, or automated PLC integration), and available safety features such as overload protection, emergency shut-off switches, and thermal cutouts. Regular preventive maintenance schedules, clear compliance with OSHA hoist regulations, and thorough operator training are integral for prolonging the service life and safety integrity of your electric hoisting equipment. For specialized applications such as clean rooms, hazardous areas, or marine environments, select models designed with corrosion-resistant materials, IP-rated enclosures, or explosion-proof certifications to ensure maximum reliability and regulatory compliance.
Electric hoists can be employed as standalone units or integrated into structural frames and tracks as part of a comprehensive lifting system. The various types of lifting systems include:
Engine hoists, or engine cranes, are used to assist the workers in the installation and maintenance of engines of automobiles. They are designed to lift the engine under the automobile hood. Their electric hoists are mounted on top of the rigid and portable structural frame. The structural frame has wheels installed at its base to easily maneuver the hoist over the automobile, as well as to transport it around the machine shop. Its portability makes it suitable for outdoor applications. The structural frame of some engine hoists is foldable, so it can save space when it is stored.
The installation of overhead cranes is planned during the early stages of a building‘s construction, as they require a much greater amount of structural support. Overhead cranes lift the heaviest loads at the highest lifting heights in an enclosed facility.
In overhead cranes, there are two parallel end trucks mounted on runway beams . The runway beams are also responsible for supporting the entire overhead crane and the load. The end trucks travel along the rails of the runway beams together with the bridge and the electric hoist. The electric hoist travels across the length of the bridge. The bridge can either be a single girder or a double girder bridge. A single girder bridge crane has one trolley that moves across a single girder beam, while the double girder bridge crane has two trolleys that move the electric hoist synchronously across two girder beams. The bridge and the end trucks are positioned perpendicularly with each other. This arrangement enables the electric hoist to move left and right (via end trucks), and forward and backward (via the bridge). Lifting and positioning parameters are controlled remotely.
A jib crane has a lifting fixture that primarily consists of two large beams constructed to form a cantilever. The mast, or pillar, is the vertical beam of the fixture that supports the reach. The reach, or boom, is the horizontal beam of the fixture wherein the electric hoist travels to position the load. There are three types of jib cranes:
Floor-mounted jib cranes are self-supporting structures with a large mast fixed to the floor. These cranes are designed to support the loads of primary cranes and come in various types and designs to enhance lifting capabilities. For instance, drop-mounted cantilever jib cranes feature an adjustable boom that allows for modifications in lifting height. Many floor-mounted jib cranes are capable of rotating up to 360°.
In some contexts, floor-mounted jib cranes are also known as base-mounted hoists. They perform a similar function, being positioned on the floor for vertical lifting. These hoists operate along a load line that moves through a heel and crown block at ground level or the rooster head of a gin pole.
The primary purpose of a base-mounted hoist is to lift and lower materials. These hoists are equipped with a rope drum, gearbox, motor, brake, and control panel. To ensure durability and strength, base-mounted hoists are constructed from steel, typically bolted or welded together, with load capacities ranging from half a ton to ten tons or more.
Wall-mounted jib cranes are attached to a wall or column that must be structurally sound to support them. Their range of rotation is typically limited to 200°. There are two main types of wall-mounted jib cranes: cantilever wall-mounted jib cranes, which provide maximum clearance both above and below the boom and apply minimal force to the supporting column, and tie-rod supported wall-mounted jib cranes, which use a wall bracket and a tie rod for support. With no additional support structure beneath the boom, these cranes allow the electric hoist to travel the full length of the reach.
Articulated jib cranes feature a mast and two boom arms connected by joints that allow them to flex or fold. These cranes can be installed on the floor, ceiling, wall, or a bridge crane. The primary boom arm, which supports the load, can rotate up to 360°, while the rotation of the secondary boom arm varies based on the crane’s mounting location. Articulated jib cranes offer flexible load movement in multiple directions.
Gantry cranes are versatile lifting devices featuring a horizontal overhead bridge supported by legs. The electric hoist moves along the bridge’s length. Mobility is achieved by equipping the legs with wheels or by having them run along a track. Unlike bridge cranes and jib cranes, gantry cranes do not rely on the building’s structure for support and can be used outdoors. They are also capable of operating beneath bridge cranes to handle some of their load.
Monorail cranes are specialized overhead cranes used in production facilities and machine shops for repetitive lifting and positioning tasks. They are designed to transport loads within confined spaces. The electric hoist trolley moves along the outer flange of a single I-beam that is mounted on the building's ceiling structure.
Workstation cranes offer an ergonomic solution for lifting and moving objects within a compact workspace. They resemble overhead cranes but are supported by free-standing columns rather than being integrated into the building's structure. With a smaller frame and limited lifting heights, workstation cranes are a cost-effective choice for light to medium-duty applications.
An aircraft cable is a style of highly durable cable that is used for aircraft flight controls and other applications and is differentiated from normal cables by its diameter, stranding, and wires, which provide...
A gantry crane is an overhead crane that has an overhead beam supported by freestanding legs and moves on wheels, a track, or rail system carrying a bridge, trolley, and hoist. Workshops, warehouses, freight yards, railroads, and shipyards use gantry cranes as their lifting solution as a variation of overhead or bridge cranes...
A hydraulic lift is a device for moving objects using force created by pressure on a liquid inside a cylinder that moves a piston upward. Incompressible oil is pumped into the cylinder, which forces the piston upward. When a valve opens to release the oil, the piston lowers by gravitational force...
A jib crane is a lifting device with an arm or boom that extends off the main body of the crane to provide extra reach and has a lattice design to lower the weight added to a load. The design of jib cranes allows them to work...
A lift table is a platform capable of holding materials and raising, lowering, and adjusting them to any height to meet the needs of an application and the user’s requirements. Lift tables are supported by a strong, rigid, and stable base frame placed flat on the floor, in a pit, or equipped with casters or wheels...
An overhead crane is a type of heavy duty machinery that is capable of moving extremely heavy loads and equipment from one location to another in a safe and precise manner using the overhead space of a manufacturing facility. Due to the nature of the work they perform...
A push pull cable control is used for the transmission of multi directional precision control of mechanical motion. The many varieties of push pull cables or controls are adaptable to a wide range of applications and...
Scissor lifts are a type of manlift that is commonly used in construction and facility maintenance to raise employees and their tools to working heights. A power system and a control system make up the scissor lift...
Stranded wire refers to thin bundled up wires that are compressed and covered up in insulating material. Stranded wires are more flexible thus making them very ideal for joining electronic circuit components in confined spaces where their bending...
Wire rope is a collection of metal strands that have been twisted and wound to form the shape of a helix with the purpose of supporting and lifting heavy loads and performing tasks that are too rigorous for standard wire...
A wire rope assembly is composed of wire rope and end fittings, terminals, or lanyards that are attached to various parts of the wire rope such that the assembly can be used to lift, hoist, and move loads. The various types of...
Wire rope is constructed of multiple strands of wire that are twisted and braided together to form a spiral design or helix. Once the separate wires are shaped into a solid form, they become a single wire with greater strength because...
A hydraulic system is based on Pascal‘s principle of fluid pressure, which hypothesizes that a change in pressure in a fluid is transmitted to all points of the fluid in all directions. With a hydraulic lift, an electrically powered pump pushes fluid into a cylinder at the base of a lifting jack system that lifts the platform up and down...