AC Motors
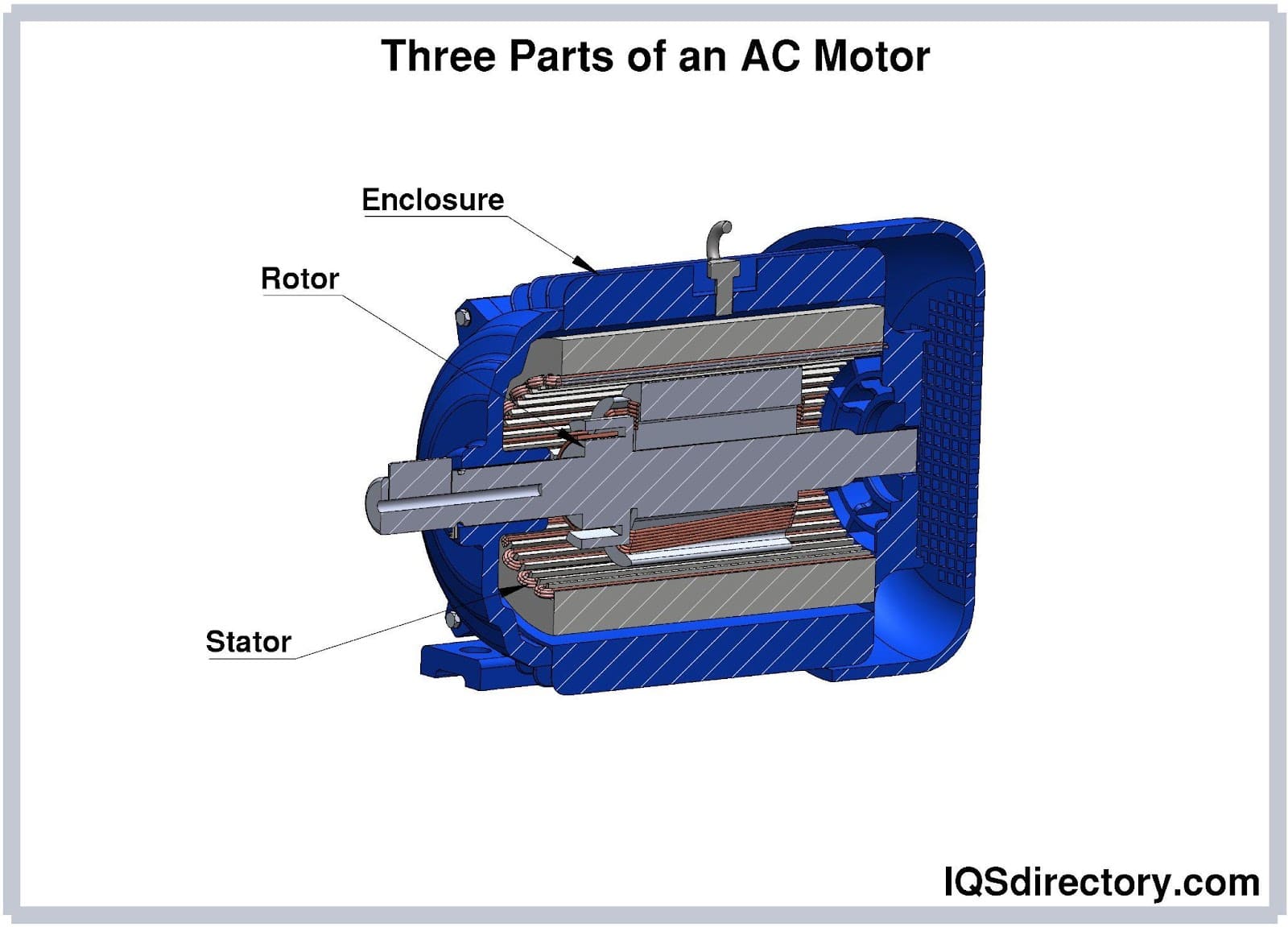
An AC motor is an electric motor that uses alternating current to produce mechanical energy using magnetism blended with alternating current. The structure of an AC motor includes coils that produce a rotating...
Please fill out the following form to submit a Request for Quote to any of the following companies listed on
This article will take an in-depth look at electric motors.
The article will bring more understanding on topics such as:
This chapter delves into the core concepts of electric motors, examining their construction and how they operate.
An electric motor is a mechanism that converts electrical energy into mechanical energy. It achieves this by generating a magnetic field through an electric current passing through wire coils, which creates torque on the motor shaft. Although an electrical generator is mechanically similar to an electric motor, it functions oppositely, turning mechanical energy into electrical energy.
Electric motors can be powered by direct current (DC) sources like batteries or rectifiers, or by alternating current (AC) sources such as power grids, generators, or inverters. They can be categorized based on power supply type, intended usage, construction, and output type. Motors may be DC or AC, either brushless or brushed, and can function on single-phase, two-phase, or three-phase power. Additionally, they can be designed for radial or axial flux and may utilize liquid or air cooling solutions.
Standard electric motors are prevalent in industrial applications, finding utility in equipment like blowers, pumps, industrial fans, machine tools, power tools, household appliances, disk drives, and vehicles. Smaller motors are employed in devices such as electric watches. Notably, in specific applications such as regenerative braking in traction motors, electric motors can act as generators to reclaim energy otherwise dissipated as heat and friction.
Electric motors comprise two main mechanical sections: the stator, which is stationary, and the rotor, which rotates. Key electrical components include the field magnets and the armature. One component attaches to the stator, while the other connects to the rotor, creating a magnetic circuit.
Field magnets, which can be permanent or electromagnets, produce a magnetic field interacting with the windings. Typically, these magnets are mounted on the stator, with the winding on the rotor, although this configuration can be reversed in certain motor designs.
Bearings support the rotor and facilitate its smooth rotation along its axis. The motor housing is responsible for supporting these bearings.
The rotor, which is the moving section, is crucial for delivering mechanical power. It generally has conductors that carry current, interacting with the stator's magnetic field to produce rotational force on the shaft. In some designs, the rotor might include permanent magnets, while conductors are positioned in the stator, leading to enhanced efficiency over a wide power and speed range.
The air gap between the rotor and stator allows for rotor movement. This gap's size significantly influences electrical performance, with a narrower gap generally enhancing efficiency and the power factor, while a wider gap increases energizing current and decreases the power factor. Conversely, if the gap is too narrow, it can cause mechanical issues, extra losses, and more noise.
The motor shaft continues through the bearings to the motor's exterior, where it accommodates the load, creating an overhung load due to the force applied beyond the furthest bearing.
The stator surrounds the rotor and typically holds the field magnets, which could be electromagnets with wound wire on an iron core or permanent magnets. These magnets generate the magnetic field that interacts with the rotor winding to produce force. The stator's iron core is made from thin, insulated metallic sheets called laminations to minimize energy loss.
Lamination helps reduce energy losses that are prevalent with a solid core. In resin-packed motors, frequently used in appliances like air conditioners or washing machines, plastic materials reduce vibrations and noise.
The armature comprises wire wound around a ferromagnetic core. When current flows through, it generates a magnetic field exerting a Lorentz force on the armature, turning the rotor to produce mechanical power. The windings, often wire coils, typically wrap around a soft, laminated iron core, creating magnetic poles as current is applied.
Motors can be either non-salient or salient-pole types. In salient-pole motors, both the rotor and stator have cores with protruding poles, each wrapped in wire forming north or south poles when current flows. Non-salient-pole motors (round-rotor or distributed field motors) maintain a cylindrical core with evenly distributed winding around it. The alternating current in these windings generates continuously rotating poles. Shaded-pole motors possess windings that partly cover each pole, causing a phase delay in the magnetic field for that pole.
A commutator, a rotary switch, provides either AC or DC to the rotor, reversing current in the rotor winding regularly as the shaft revolves. It consists of a cylinder with metal segments on the armature. Brushes, typically made from conductive materials like carbon, press against the commutator, ensuring sliding electrical contact and delivering current to the rotor.
The segments periodically reverse the rotor windings' current every 180°, maintaining the torque direction consistent. Without this, the torque direction changes each half-turn, stalling the rotor. Due to inefficiencies, commutator-based motors are being replaced by brushless DC motors, induction motors, and permanent magnet motors.
Electric motors transform electrical energy (AC or DC) into mechanical energy to create movement. This transformation involves interaction between current flowing through windings and a magnetic field. As the current's strength grows, so does the magnetic field's strength. From Ohm's Law (V = R*I), if resistance rises, the voltage must also increase to maintain equal current.
Consider the following when selecting an electric motor:
Voltage – Decide if the motor will be powered from a wall socket or batteries. For wall sockets, the typical voltage may be 230VAC or more in industrial settings.
Frequency – Motors usually operate at 60Hz in the U.S. If used outside the country, you may need a 50Hz motor.
Speed – Assess the needed speed range. If adjustable speeds are critical, ensure the motor has suitable control capabilities.
Torque – Evaluate the starting torque needed and any variations during operation. Consider maximum necessary torque under adverse conditions.
Power – Specify if the motor will operate at maximum power capacity.
Duty Cycle – Recognize the motor’s duty cycle. For continuous operation, ensure it can handle extended use without overheating. For intermittent tasks, a smaller motor may suffice, assuming it can fully cool between cycles.
Lifetime – Applications with sporadic use might suit Universal or DC motors, which generally have shorter lifespans and higher maintenance needs. Operations requiring prolonged duration benefit from brushless DC or AC motors, known for longevity and reduced maintenance.
The different types of electric motors are:
A DC motor is a type of rotary electrical machine that converts electrical energy from direct current (DC) into mechanical energy. These motors operate based on the force generated by magnetic fields. Most DC motors incorporate internal mechanisms—either electronic or electromechanical—that periodically change the direction of the current in a part of the motor to facilitate its operation.
DC motors were the first kind of motor commonly utilized, as they can be powered from present direct current lighting energy distributing systems. DC motor speed may be controlled over a broad range, utilizing either a variable voltage supply or by altering the current strength in its field winding. Small DC motors are applied in appliances, toys, and tools. The universal DC motor can work on direct current but it is a light brushed motor utilized for portable appliances and power tools. Large DC motors are presently utilized in the propulsion of elevators and hoists, electric vehicles, and in drives for rolling mills for steel. With the arrival of power electronics replacement of DC motors with AC motors has been made conceivable in many applications.
A 12V DC motor is compact and affordable, yet it provides sufficient power for a wide range of uses. Its operating voltage is a notable feature, with lower voltages generally being preferable when using batteries, as fewer cells are needed to reach the desired voltage. Nonetheless, higher voltages often offer better efficiency in electronic motor drives. While DC motors can operate from as low as 1.5V up to 100V, the 12V, 6V, and 24V variants are among the most common. Important specifications for a 12V DC motor include its torque, speed, current consumption, and power output.
Typically, 12V DC motors are brushless, meaning they operate without the need for brushes to transfer electrical current. In contrast, brushed motors can encounter issues due to their more complex design. The brushless design of the 12V DC motor has resolved many of these problems. Key components of a 12V brushless DC motor include an external rotor with permanent magnets and either a single coil or multiple coils (usually three). Additional components might include drive electronics and various sensors.
Rather than using brushes, 12V DC brushless motors use sensors, such as Hall Effect sensors, to manage the current. Although some 12V DC motors might refer to AC types, this is rare compared to the predominance of 12V DC motors.
A brushless motor, commonly known as a BL motor or BLDC motor, and sometimes referred to as an electronically commutated motor (ECM), is a type of DC motor. It may also be called a synchronous DC motor. This motor operates using direct current (DC) power and relies on an electronic controller to manage the current flowing through the windings. This process generates a magnetic field that rotates in space, causing the rotor with permanent magnets to follow suit. The electronic controller regulates the amplitude and phase of the DC current pulses to control the motor’s torque and speed. This system replaces the traditional brushes and mechanical commutators found in many conventional electric motors.
Brushless DC motors are manufactured in a manner akin to permanent magnet DC motors, but they can also be designed as asynchronous or induction motors, or as switched reluctance motors. They may incorporate neodymium magnets and come in various configurations, including out-runners (where the rotor encloses the stator), in-runners (where the stator encloses the rotor), or axial motors (where the stator and rotor are aligned parallel and flat).
Compared to brushed motors, brushless motors offer several advantages, such as higher speeds, improved power-to-weight ratios, near-instantaneous torque and speed adjustments (rpm), reduced maintenance requirements, and greater efficiency. They are commonly used in computer peripherals (like printers and disk drives), portable power tools, and a range of vehicles from cars to model aircraft. In modern washing machines, brushless motors have replaced traditional gearboxes and rubber belts with a direct-drive system.
A stepper motor, also known as a stepping motor or step motor, is a type of brushless DC motor that divides a full rotation into discrete steps. Unlike traditional brushed DC motors, which rotate continuously when a direct voltage is applied, a stepper motor moves in precise increments based on input pulses. These motors can be controlled to move and maintain their position at each step without requiring feedback from a positional sensor, provided the motor is correctly matched to the application’s speed and torque requirements. Each pulse results in a specific rotational movement of the motor shaft, enabling highly accurate control.
Stepper motors consist of several toothed electromagnets arranged around a central rotor, which is typically a gear-shaped iron core. These electromagnets are activated by a microcontroller or an external driver circuit.
To initiate rotation, one electromagnet is energized, attracting the gear's teeth through magnetic force. As the teeth align with the activated electromagnet, they are slightly misaligned with the next electromagnet in sequence. When the next electromagnet is turned on and the initial one is deactivated, the rotor moves incrementally to align with the new electromagnet. This process is repeated continuously, with each incremental movement referred to as a "step." By repeating this sequence, the motor can achieve precise angular rotation, with a full rotation completed through a specific number of steps.
An AC motor operates on alternating current (AC) and consists of two main components: the stator and the rotor. The stator is the outer part of the motor and contains coils that are energized by AC to produce a rotating magnetic field. Inside, the rotor is connected to the shaft and generates its own magnetic field, which may be created by various means including reluctance saliency, permanent magnets, or AC/DC windings.
AC linear motors, though less common, function on principles similar to those of rotating AC motors. However, instead of creating rotational movement, AC linear motors are designed with their moving and stationary parts arranged in a linear configuration, resulting in linear motion rather than rotation.
The two primary kinds of AC motors are synchronous motors and induction motors. The induction or asynchronous motor always depends on a small variance in speed between the rotor shaft speed and the stator spinning magnetic field called slip which induces rotor current in the AC winding of the rotor. Therefore, the induction motor can’t create torque close to synchronous speed where slip (induction) ceases to exist or is irrelevant. In comparison, a synchronous motor doesn’t depend on induction of slip for functioning and utilizes either salient poles (projecting magnetic poles), permanent magnets, or an individually excited rotor winding. The synchronous motor creates its ranked torque at accurately synchronous speed. The brushless wound-rotor double supplied synchronous motor mechanism has an individually excited rotor winding which does not depend on the rules of slip induced current. The brushless wound-rotor double supplied motor is a synchronous motor which can work exactly at the power source frequency. Other kinds of motors involve eddy current motors and DC and AC mechanically commutated machinery where speed relies on winding connection and voltage.
Horsepower (HP) is a commonly used unit to measure the rate at which mechanical energy is used. One horsepower is approximately equivalent to 746 watts (W) or 0.746 kilowatts (kW). Although horsepower and kilowatts can be converted to comparable units, horsepower is predominantly used for measuring mechanical power and is rarely used for other forms of power measurement.
Electric motors typically have nameplates that show their output power, not the input power. This refers to the power delivered at the shaft, rather than the power required to operate the motor. Output power is usually measured in watts or kilowatts. In the United States, however, output power is often expressed in horsepower, with one horsepower defined as exactly 746 watts. Motors rated at 1 HP can be either AC or DC types and are commonly used in applications such as vehicles and electric boats.
Similar to a 1HP motor, a 2HP electric motor provides power directly at its shaft. This equates to approximately 1.49 kW. It can be either a DC or AC motor, available in single-phase or three-phase configurations. A 2HP motor is commonly used for driving boat propellers, industrial cooling fans, or as an induction motor in various applications.
Three-phase motors are a type of AC motor and are a specific example of induction motors, also known as asynchronous motors. These motors are made up of three primary components: the rotor, the stator, and the housing.
The stator consists of a series of steel laminations wrapped with wire to form induction coils, each corresponding to one of the three phases of the power supply. Each coil receives power from the three-phase electrical input.
The rotor also comprises metal bars and induction coils connected to make a circuit. The rotor surrounds the motor shaft and it is the motor part which rotates to make output mechanical energy of the motor.
The motor's enclosure houses the rotor and its shaft on a series of bearings to reduce friction during rotation. The enclosure features end caps that secure the bearing mounts and includes a fan connected to the shaft. As the shaft spins, the fan draws in external air and circulates it through the rotor and stator to cool the motor components and expel heat generated by the coils' resistance. Additionally, the enclosure often has external cooling fins to enhance heat dissipation. The end caps also provide access for the electrical connections required for the three-phase power supply.
A single-phase motor is an electrical rotary device that transforms electrical energy into mechanical energy, powered by a single-phase electrical source. It operates using two types of wires: live and neutral. These motors can handle power up to 3kW, with input voltage varying accordingly. They operate with a single alternating voltage and involve a circuit with two wires where the AC current remains consistent. Typically, single-phase motors are compact and designed for applications requiring lower torque.
However, some single phase motors have a power of up to 10 HP which can operate with connections reaching up to 440V. They do not produce spinning magnetic fields, they can only produce an alternating field, which implies that for start-up they require a capacitor. They are simple to maintain and repair, as well as affordable. This type of motor is utilized mainly in offices, stores, homes, and non-industrial small companies. Their most popular uses include home and business HVAC, home appliances and other appliances like drills, air conditioning systems, and garage door closing and opening systems.
Industrial electric motors transform electrical energy into mechanical energy and are capable of generating either rotary or linear motion. While some industrial motors are powered by direct current (DC), it is more common for them to be driven by alternating current (AC) sources, such as the power grid or generators.
Industrial motors are comprised of several key components including the rotor (also known as the armature), stator, air gap, winding (or coil), and commutator. These motors come in various types such as DC synchronous, AC synchronous, and AC induction (asynchronous), among others.
A servomotor or servo motor is a linear actuator or rotary actuator which enables precise control of linear or angular position, acceleration, and velocity. It comprises an appropriate motor coupled with a sensor for feedback of position. It also needs a relatively complex controller, usually a dedicated device designed especially for usage with servomotors.
Although servomotors do not constitute a specific category of motors, the term is commonly used to describe motors suited for closed-loop control systems. These motors are frequently used in applications such as CNC machinery, robotics, and automated manufacturing.
The specific type of motor is less critical in a servomotor, as various motor types can be employed. Typically, basic brushed DC motors (with permanent magnets) are used due to their affordability and simplicity. Smaller industrial servomotors often feature brushless, electronically commutated designs. In larger industrial applications, AC induction motors are commonly employed, sometimes paired with variable frequency drives (VFDs) for speed regulation. For high performance in a compact form factor, brushless AC motors with permanent magnets are used, resembling scaled-up versions of brushless DC motors.
This section will cover the various uses and advantages of electric motors.
Electric motors are versatile and find applications in a wide range of devices such as fans, blowers, machine tools, turbines, pumps, power tools, compressors, alternators, rolling mills, movers, ships, and paper mills. They play a crucial role in high voltage AC heating systems, cooling and ventilation equipment, automobiles, and household appliances.
Maintaining electric motors involves the following considerations:
It's crucial for every organization to establish a cleaning routine for their motors. Regularly cleaning a motor enhances both its longevity and efficiency. Ensuring that a motor remains free from excessive dust, grease, and other debris is essential for optimal performance.
It’s possible to over lubricate an electric motor, which may lead to internal issues. However, a motor needs lubrication to work at maximum performance level. Every electric motor needs a different amount of lubrication. Lubricating a motor very early or very late may lead to premature tear and wear. Also, manufacturers generally recommend specific lubricants designed for their electric motor.
Motor bearings experience the most wear and tear, making them prone to issues over time. To prevent premature bearing failure, it's crucial to ensure proper motor alignment, as misalignment can place excessive stress on the bearings. Additionally, using the wrong type of lubricant can lead to early bearing wear. A common indicator of bearing problems is an overheating motor.
All motors produce some level of vibration, but excessive vibrations can lead to serious damage. If a motor begins to vibrate excessively, it should be shut down immediately. Common causes of abnormal vibrations include mechanical misalignment, damaged bearings, or excessive belt tension.
The rotor and stator are crucial components of the motor. It’s essential to check the gaps around these parts and measure the diameter clearance. The required clearance can vary depending on the specific motor and bearing design.
Tracking maintenance activities is vital for monitoring the motor’s lifespan and wear. Every inspection, bearing replacement, belt adjustment, and lubrication addition should be recorded. Proper documentation helps in forecasting future maintenance needs and managing related expenses more effectively.
Electric motors convert electrical energy to mechanical energy. Most of them work via the interaction of the motor magnetic field and electrical current in a wound wire to produce force in the manner of torque supplied on the motor shaft. The most important parts of a motor are the rotor and the stator. They may be energized by alternating or direct current. There are many types of electric motors including induction, servo, three phase, and industrial motors to name a few. They are used in electric vehicles, air conditioners, ships, and hydraulic machines.
An AC motor is an electric motor that uses alternating current to produce mechanical energy using magnetism blended with alternating current. The structure of an AC motor includes coils that produce a rotating...
A DC motor or direct current motor is an electrical machine that transforms electrical energy into mechanical energy by creating a magnetic field that is powered by direct current. When a DC motor is powered, a magnetic field is created...
A fractional horsepower motor is an alternating (AC) or direct (DC) current motor that produces less than one horsepower with an output rating of 746 watts or less. The low power level of fractional horsepower motors makes them...
Power supplies are electrical circuits and devices that are designed to convert mains power or electricity from any electric source to specific values of voltage and current for the target device...
An AC power supply is a type of power supply used to supply alternating current (AC) power to a load. The power input may be in an AC or DC form. The power supplied from wall outlets (mains supply) and...
An AC power cord is a detachable way of providing an alternating current of electric energy from a mains power supply to an electrical appliance or equipment. Serving industries like...
A DC DC power supply (also known as DC DC Converter) is a kind of DC power supply that uses DC voltage as input instead of AC/DC power supplies that rely on AC mains supply voltage as an input...
A DC power supply is a type of power supply that gives direct current (DC) voltage to power a device. Because DC power supply is commonly used on an engineer‘s or technician‘s bench for a ton of power tests...
Electrical plugs, commonly known as power plugs, are devices responsible for supplying and drawing current from a receptacle to the circuitry of an electrical appliance...
By definition a power supply is a device that is designed to supply electric power to an electrical load. An electrical load refers to an electrical device that uses up electric power. Such a device can be anything from...
A NEMA connector is a method for connecting electronic devices to power outlets. They can carry alternating current (AC) or direct current (DC). AC current is the typical current found in homes, offices, stores, or businesses...
A power cord is an electrical component used for connecting appliances to an electrical utility or power supply. It is made from an insulated electrical cable with one or both ends molded with connectors...
A programmable power supply is a method for controlling output voltage using an analog or digitally controlled signal using a keypad or rotary switch from the front panel of the power supply...
Thomas Edison developed the power distribution system in 1882. He wrapped a copper rod in jute, a soft shiny fiber from plants, as an insulator. The jute wrapped copper rod was placed in a pipe with a bituminous compound...