Electric Transformers
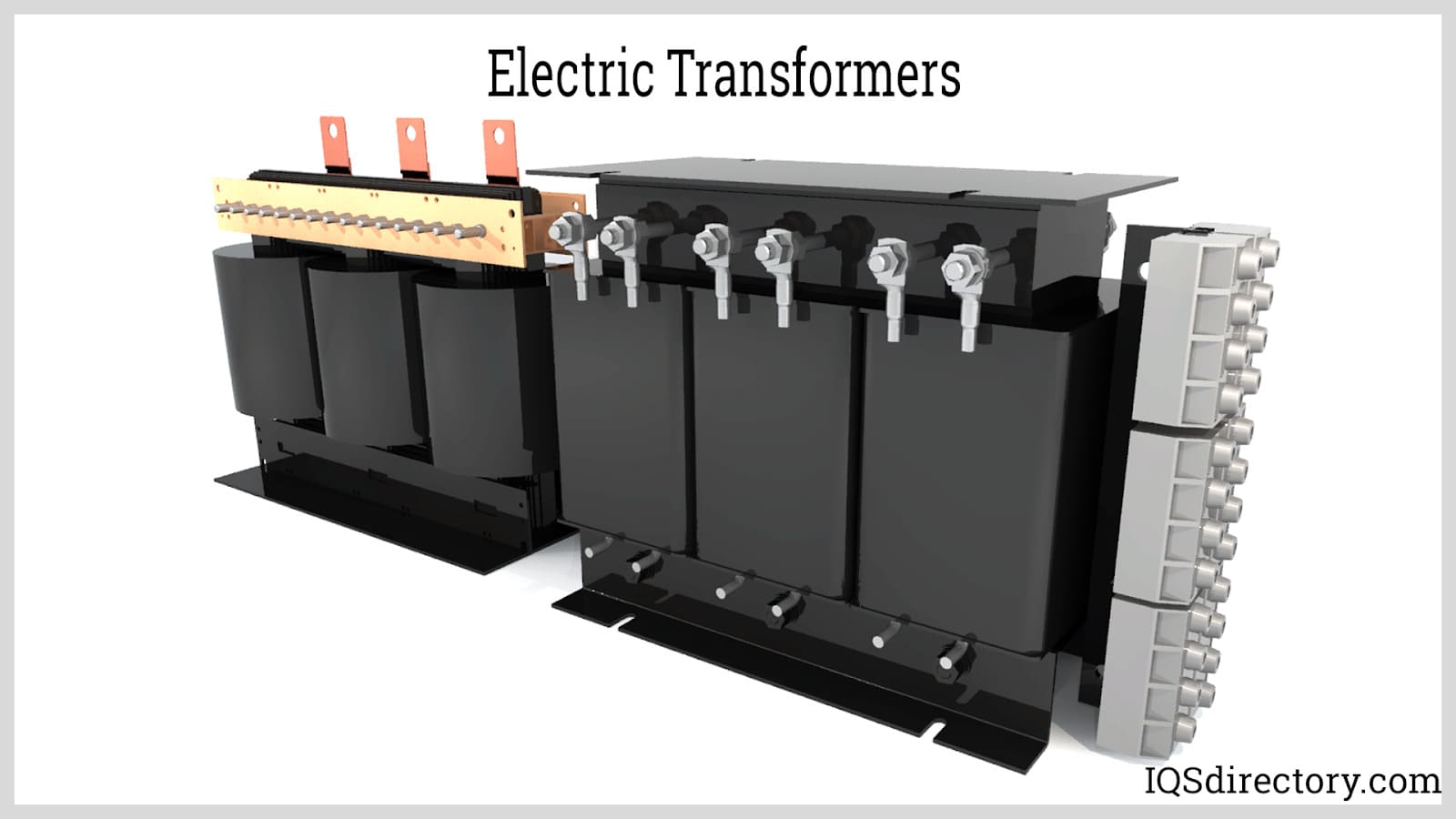
Electric transformers are static electrical machines that transform electric power from one circuit to the other without changing the frequency. An electrical transformer can increase or decrease the voltage with...
Please fill out the following form to submit a Request for Quote to any of the following companies listed on
This article will take an in-depth look at isolation transformers.
The article will look at topics such as:
This chapter delves into the functionality, design, and customization of isolation transformers, highlighting essential aspects to consider during the selection process.
An isolation transformer is an immobile device crafted to physically and electrically separate the primary and secondary windings. This ensures complete isolation between circuits, allowing energy transfer through magnetic induction. By leveraging a magnetic field, it induces an electromotive force (EMF) in the secondary circuit while preserving the original frequency.
In the realm of transmission and distribution systems, isolation transformers play a pivotal role in adjusting voltage levels by stepping them up or down to ensure compatibility between the coils' voltage and current capacities. They are vital in mitigating voltage spikes in supply lines, which otherwise might cause disruptions or equipment damage if they reach the load.
Positioned between power supply lines, an isolation transformer minimizes voltage spikes before they can impact the load. Furthermore, it prevents grounding issues on the secondary side, helping to reduce ground loop interference and diminish noise effects in load equipment.
Isolation transformers ensure that the primary and secondary coil circuits remain electrically isolated. This design facilitates the safe transmission of electrical power from an AC source to devices or equipment, maintaining electrical separation for added safety and reducing electrical transients and harmonics. In step-up transformers, the secondary coil typically contains more turns than the primary, whereas, for step-down transformers, the primary coil generally has more turns than the secondary.
Isolation transformers adjust the voltage output by transforming the voltage input according to the needed voltage, current, and turns ratio. While single-phase AC systems experience synchronous voltage fluctuations, making them less suitable for large motors and industrial machinery, three-phase power employs three distinct signals with separate peaks. This approach eradicates oscillations typical in single-phase systems, leading to smoother operations, diminished vibration, and simplified equipment design, making three-phase power particularly effective for substantial motors and heavy industrial applications.
An isolation transformer is tasked with physically and electrically separating two circuits to safeguard electronic systems and personnel from electrical shock. It transfers power from the primary to the secondary side through magnetic coupling.
The foremost function of an isolation transformer is to reduce voltage spikes occurring in supply lines. Spikes, arising from sources like lighting, static electricity, or sudden surges, are short-lived voltage increases (typically lasting 3 nanoseconds or longer). The isolation transformer attenuates these spikes, thereby offering protection to connected devices from potential harm.
Voltage spikes might carry extraordinarily high voltages, ranging from minimal to several thousand volts. If these intense spikes reach the load, they could interrupt service or inflict damage on equipment. By employing an isolation transformer between power supply lines, spikes can be significantly reduced before they impact the load.
On the primary side, when a fast-changing high-voltage spike strikes, the transformer addresses it by leveraging the primary winding's resistance, preventing an immediate current shift. This results in an exponential current change, rather than an instantaneous one, causing the voltage on the secondary side to increase as the current and flux rise.
The inductive properties inherent in both primary and secondary windings hinder the spike's direct transfer to the secondary side. Resistance to current flow intensifies with the rate of change, meaning that a rapid voltage spike faces more substantial resistance. Thus, the spike's effect on the secondary or load circuit is largely minimized, safeguarding the load equipment against injury.
Moreover, an isolation transformer averts the grounding of load devices or the secondary side, which eliminates ground loop interference and noise. This makes isolation transformers crucial for protecting sensitive apparatus—such as laboratory, measurement, and medical devices—from voltage fluctuations, ground loops, and other power line anomalies.
The construction of an isolation transformer mirrors that of a typical core-type transformer but incorporates certain enhancements. The addition of electrostatic shields completely isolates the secondary winding from the primary, effectively attenuating noise and interference. In contrast, autotransformers, where primary and secondary windings connect electrically, cannot provide the same level of isolation due to the absence of this crucial physical separation.
Isolation transformers can adopt a toroidal, or donut-shaped, form which offers benefits like reduced size and weight, making them versatile for numerous applications. Toroidal transformers boast evenly distributed windings around the core running through its center. This core may be crafted from materials like silicon iron or nickel-iron alloys, enhancing efficiency and performance.
For high-frequency applications, amorphous alloys and iron powder are preferred options for core materials. Furthermore, toroidal transformers can decrease audible noise and stray field emissions. They might be equipped with a metal band to further curtail stray magnetic fields. Isolation transformers may also feature additional insulation, vital for devices like patient monitors that require minimal interference allowance.
Various kinds of isolation transformers are available, including:
The ultra isolation transformer features a distinct design that eradicates various forms of electrical interference, especially common mode noise. By isolating the primary and secondary sides and providing a neutral ground on the secondary side, it helps create a separate power source to address current loops. It effectively diminishes transverse mode noise and reduces common mode noise through the use of advanced insulating materials and specialized shielding methods.
Ultra isolation transformers are designed for critical and sensitive equipment such as computers, medical devices, digital communication systems, CNC machinery, and more. They mitigate disturbances caused by noisy equipment that can interfere with the power supply. These transformers are specified with high voltage ratings between 1000 to 4000 volts between their windings and are equipped with robust insulation separating the primary and secondary sides.
These transformers are particularly beneficial for wireless communication stations and advanced medical devices. They feature low coupling capacitance and are built with advanced shielding techniques to ensure high noise attenuation. Their sophisticated design ensures they are highly effective, durable, and suitable for various operating voltages.
The constant voltage transformer (CVT), which employs ferroresonant technology, is a 1:1 transformer that operates at a high point on its saturation curve. It provides an output voltage that remains largely unaffected by variations in the input voltage. The CVT uses a tank circuit consisting of a high-voltage resonant winding and a capacitor to transform a variable input into a nearly stable average output. Typically, the input winding functions at relatively low flux linkage levels.
The output winding features inherent energy storage that, in conjunction with the primary capacitor, generates a self-contained AC flux field that is somewhat isolated from the input winding. Unlike traditional stabilizers, the CVT does not use relays that could briefly interrupt the output voltage, making it a preferred choice. The CVT provides comprehensive protection against voltage spikes by maintaining a regulated output voltage.
Galvanic isolation in electrical systems involves the physical and electrical separation between the input and output power circuits. This is typically achieved using an isolation transformer, which ensures that the output power wiring remains completely separated from the input wiring. Personal computers already incorporate galvanic isolation between their power supply and internal logic circuits as mandated by international safety standards to minimize shock hazards. Thus, adding an additional transformer for this purpose is generally unnecessary.
While galvanic isolation is often believed to address noise on the ground (earth) wire, in reality, isolation transformers only separate the power wires and do not affect the ground wire, which continues to pass through without obstruction. Although some uninterruptible power supply (UPS) systems provide galvanic isolation, many online UPS models do not. For example, the online UPS systems from Exide, Unison, and ON-LINE (Pheonixtec) do not feature galvanic isolation.
Isolation is a feature that can be incorporated into any UPS system, regardless of its type. The main benefit of adding an isolation transformer is the substantial reduction of common mode noise affecting the computer. Noise filters, such as those available in the APC Smart-UPS series, can also reduce common mode noise effectively. These filters can be as efficient as isolation transformers, especially at high frequencies where computers and networks operate. However, isolation transformers tend to be more effective at very low (audio) frequencies.
Audio frequency noise on the power line generally does not affect computers or their peripherals, meaning that in such applications, an isolation transformer offers no additional benefit compared to filters. Additionally, isolation transformers can generate extra heat, which may shorten the lifespan of nearby UPS batteries. Another consideration is that incorporating an isolation transformer adds significant weight to the UPS system.
Drive isolation transformers supply power for both AC and DC variable frequency drives by shifting the voltage to the required level for SCR (Silicon Controlled Rectifier) Drives, while providing magnetic isolation between the incoming power line and the motor drive. SCR drives demand strong mechanical and electrical design and testing due to the mechanical stresses, voltage distortions, and harmonics they generate. While various types of motor drives exist, they all share a common requirement: incoming power must be rectified to achieve a DC level.
The motor drive converts power through an AC-DC-AC to AC-DC process using a three-phase rectifier bridge and an SCR. This conversion generates electrical noise and harmonics, which can be particularly problematic for transformers used in isolation drive applications, as they can cause significant heating and mechanical stress at higher frequencies. Drive isolation transformers are specifically designed to withstand the thermal, voltage, and mechanical stresses associated with motor drives. They help mitigate issues like motor bearing currents, line-to-ground voltage transients, and other noise problems caused by common-mode voltages.
Grounding the secondary side of the transformer can effectively eliminate common-mode noise, thereby enhancing both system reliability and safety. Delta-wye drive isolation transformers are capable of establishing a ground reference on the secondary side. In a motor drive system, high-frequency currents often return to the transformer winding, causing wave distortion on the line. These currents can significantly increase eddy-current losses in the windings, which should be accounted for when selecting a new transformer to ensure appropriate temperature rise calculations. Eaton's drive isolation transformers are specifically designed to manage high-frequency currents, incorporating ThermoGuard protection within the coils. This protection system alerts users to high temperatures that could otherwise reduce the transformer's lifespan or lead to failure. ThermoGuard features a set of “N.O.” dry contacts to signal such conditions.
Dry isolation transformers are encased in a sealed, pressurized container or epoxy resin, which protects the core and windings. These transformers require minimal maintenance and are reliable, making them ideal for applications where safety is critical, such as in schools, hospitals, factories, and the chemical industry.
There are two main types of dry isolation transformers: cast resin and vacuum pressure. Cast resin transformers have their windings encapsulated in epoxy resin for protection. Vacuum pressure transformers, on the other hand, feature windings enclosed in a vacuum-sealed box with moisture protection to guard against the effects of moisture.
Some of the benefits of dry isolation transformers are:
This chapter will explore the origins and impacts of electrical noise in isolation transformers, as well as the maintenance practices associated with them.
Key factors contributing to electrical noise in isolation transformers include:
A power transformer is the most expensive and crucial piece of equipment in an electrical substation. To maintain the transformer's high performance and long functional life, it is desirable to carry out various preventative maintenance tasks. Measurements and tests of the transformer's numerous properties are among the routine maintenance procedures needed for a power transformer.
Transformer maintenance can be categorized into two types: routine preventative maintenance, which should be performed regularly, and reactive maintenance, which is carried out as needed. Additionally, emergency or breakdown maintenance is only undertaken when absolutely necessary. However, regular preventative maintenance significantly reduces the chances of requiring emergency interventions.
Condition maintenance involves the regular inspection and upkeep of transformers to prevent emergencies and breakdowns. By focusing on thorough condition maintenance, technical staff can minimize the need for emergency repairs, as ongoing maintenance helps ensure the equipment remains in good working order and prevents unexpected failures.
Daily maintenance should include checking the transformer's cleanliness, winding temperature, oil temperature, and load hours. It is important to monitor readings from both the main tank and the conservator tank’s Magnetic Oil Gauge (MOG). Additionally, the color of the silica gel in the breather should be inspected. If the MOG indicates a low oil level, the transformer needs to be refilled with oil, and the transformer’s tank should be checked for any leaks. If any oil leaks are found, appropriate measures must be taken to address and repair them.
Monthly maintenance should include checking the oil level in the cap located beneath the silica gel breather. If the oil level in the cup is below the recommended mark, the transformer oil must be replenished. Additionally, the silica gel breather's ventilation holes should be inspected weekly and cleaned if necessary to ensure proper operation. For transformers with oil-filled bushings, manually check the oil levels in each bushing using the connected oil gauge on a monthly basis. If needed, top off the bushing oil to the correct level. Note that oil filling should be done during a planned shutdown.
Annually, the cooling system's automatic, remote, and manual functions—including the oil pumps, air fans, and their control circuits—should be thoroughly inspected. If any issues arise, evaluate the physical condition of the pumps and fans as well as the control circuitry. Additionally, soft cotton cloths should be used to clean the transformer bushings each year, and while cleaning, inspect the bushings for any signs of cracking.
Each year, check the condition of the OLTC oil by collecting a sample from the diverter tank’s drain valve. The oil should be tested for dielectric strength (BDV) and moisture content (PPM). If the BDV is low or if moisture levels exceed recommended limits, the OLTC oil should be either replaced or filtered.
All marshaling boxes should be cleaned thoroughly at least once a year. Additionally, inspect all lighting, space heaters, and terminal connections for control and relay wires annually, ensuring that all connections are secure and tightened as necessary.
The relays, alarms, and control switches within the relay and control panels, including the remote tap changer control panel, should be cleaned with appropriate cleaning agents. Verify the functionality of the Buchholz relay and pressure release device each year. Test the operation of relays in the remote panel by momentarily short-circuiting trip and alarm contacts with a short wire. Use a battery-operated megger with a 5 KV range to measure transformer insulation resistance and polarization index annually. Also, perform annual measurements of earth connection resistance with a clamp-on earth resistance meter. For transformers, conduct Dissolved Gas Analysis (DGA) annually for 132 KV transformers, every two years for those below 132 KV, and twice every two years for transformers over 132 KV.
This chapter will explore the various applications and advantages of isolation transformers. The discussion will cover:
Isolation transformers offer robust protection against power issues for various electrical devices. Voltage fluctuations and sudden electrical surges can damage critical components, disrupting the normal operation of equipment. By isolating the equipment from the power source, isolation transformers help prevent such risks, thereby extending the lifespan and reliability of the equipment.
In medical settings such as hospitals, where electronic devices are crucial for diagnoses, treatments, and patient care, the risk of sudden equipment failures is significant. Isolation transformers help mitigate these risks, safeguarding not only expensive medical equipment but also the safety and well-being of patients and medical staff.
Power surges can inflict significant damage on electrical devices, even though these spikes in voltage are brief. Isolation transformers offer protection against such damage by providing galvanic isolation, which shields the equipment from these surges. By isolating the DC power lines, these transformers effectively prevent any potential harm that might result from power surges.
Audio systems often experience noticeable noise interference when signals from amplifiers are transmitted to the speakers. Isolation transformers can effectively address these issues by reducing noise and improving the performance of audio devices. These transformers incorporate Faraday shields, which are designed to block electromagnetic interference by preventing disruptions in the electric field. This design helps minimize electromagnetic noise and is valuable in various industries. Reliable isolation transformers are especially crucial for the proper functioning of telecommunications, CNC machinery, remote control systems, and other critical equipment.
Electronic motors are used in a variety of industrial machinery types, and they cause harmonic voltage distortions. The equipment breaks down as a result of these harmonic changes. The best options for harmonics correction are isolation transformers. As a result, they are great protectors of industrial electric and electronic machinery.
One significant benefit of isolation transformers is their ability to prevent grounding failures. By using these transformers, there is no direct conductive link between the ground and the secondary side. Additionally, the Faraday shields incorporated in these transformers enhance their efficiency and performance.
Isolation transformers reduce the risk of current leakage, which enhances the quality of power supplied to machinery. This improvement in power quality indirectly contributes to increased equipment longevity.
Isolation transformers offer great flexibility and adaptability for various industrial power supplies, communication hubs, data acquisition systems, and similar applications. Selecting the right isolation transformer depends on the specific requirements and intended use. A thorough assessment of the application helps in choosing the most suitable transformer for optimal performance.
Understanding the different types of isolation transformers can help in selecting the most appropriate one for your particular application:
An isolation transformer, just like typical transformers, is a non-moving device that transmits electrical energy from one circuit to another without requiring any physical contact. It works on the idea of magnetic induction, which uses a magnetic field to induce EMF in another circuit without affecting the frequency. Transformers are used in transmission and distribution networks to step up and down voltage levels. An isolation transformer is a type of transformer that provides electrical isolation between two circuits (primary and secondary) without modifying the secondary properties (voltage, current, and frequency levels). Therefore, it’s important to be mindful of the type, characteristics, applications, and advantages of an isolation transformer before selecting one.
Electric transformers are static electrical machines that transform electric power from one circuit to the other without changing the frequency. An electrical transformer can increase or decrease the voltage with...
Power transformers are electrical instruments used in transmitting electrical power from one circuit to another without changing the frequency. They operate by the principle of electromagnetic induction. They are used in transmitting electrical power between...
An electrical transformer is a passive machine that transfers electrical energy from one circuit to another using a magnetic flux to induce an electromotive force. Transformers are used to increase (step-up) or decrease (step-down) voltages without changing the frequency of the electric current...
A toroidal transformer is a type of electrical transformer constructed with a torus or donut-shaped core. Its primary and secondary windings are wound across the entire surface of the torus core separated by an insulating material...
Electronically operated equipment depends on power transformers to convert electrical currents into voltage. Current transformers store and transport energy through power lines and grids...
Power supplies are electrical circuits and devices that are designed to convert mains power or electricity from any electric source to specific values of voltage and current for the target device...
An AC power supply is a type of power supply used to supply alternating current (AC) power to a load. The power input may be in an AC or DC form. The power supplied from wall outlets (mains supply) and...
An AC power cord is a detachable way of providing an alternating current of electric energy from a mains power supply to an electrical appliance or equipment. Serving industries like...
A DC DC power supply (also known as DC DC Converter) is a kind of DC power supply that uses DC voltage as input instead of AC/DC power supplies that rely on AC mains supply voltage as an input...
A DC power supply is a type of power supply that gives direct current (DC) voltage to power a device. Because DC power supply is commonly used on an engineer‘s or technician‘s bench for a ton of power tests...
An electric coil, or electromagnetic coil, is an electrical conductor that contains a series of conductive wires wrapped around a ferromagnetic core that is cylindrical, toroidal, or disk-like. Electric coils are one of the simplest forms of electronic components and provide...
Electrical plugs, commonly known as power plugs, are devices responsible for supplying and drawing current from a receptacle to the circuitry of an electrical appliance...
By definition a power supply is a device that is designed to supply electric power to an electrical load. An electrical load refers to an electrical device that uses up electric power. Such a device can be anything from...
Inductors are passive two terminal components of an electric or electronic circuit that are capable of storing energy in magnetic form. They oppose sudden changes in current and they are also called coils or chokes...
A NEMA connector is a method for connecting electronic devices to power outlets. They can carry alternating current (AC) or direct current (DC). AC current is the typical current found in homes, offices, stores, or businesses...
A power cord is an electrical component used for connecting appliances to an electrical utility or power supply. It is made from an insulated electrical cable with one or both ends molded with connectors...
A programmable power supply is a method for controlling output voltage using an analog or digitally controlled signal using a keypad or rotary switch from the front panel of the power supply...
A solenoid coil is a common electrical component that uses a wire that is tightly wrapped around a core, usually made of metal, to generate an electromagnetic field. When an electrical current is passed through the coil, the electromagnetic field that is created provides energy for linear motion...
A voice coil is a winding of a wire, usually copper, aluminum, or copper-clad aluminum that is wrapped around a former (often called a bobbin) and then attached to the apex of a speaker cone...
Thomas Edison developed the power distribution system in 1882. He wrapped a copper rod in jute, a soft shiny fiber from plants, as an insulator. The jute wrapped copper rod was placed in a pipe with a bituminous compound...