Electric Transformers
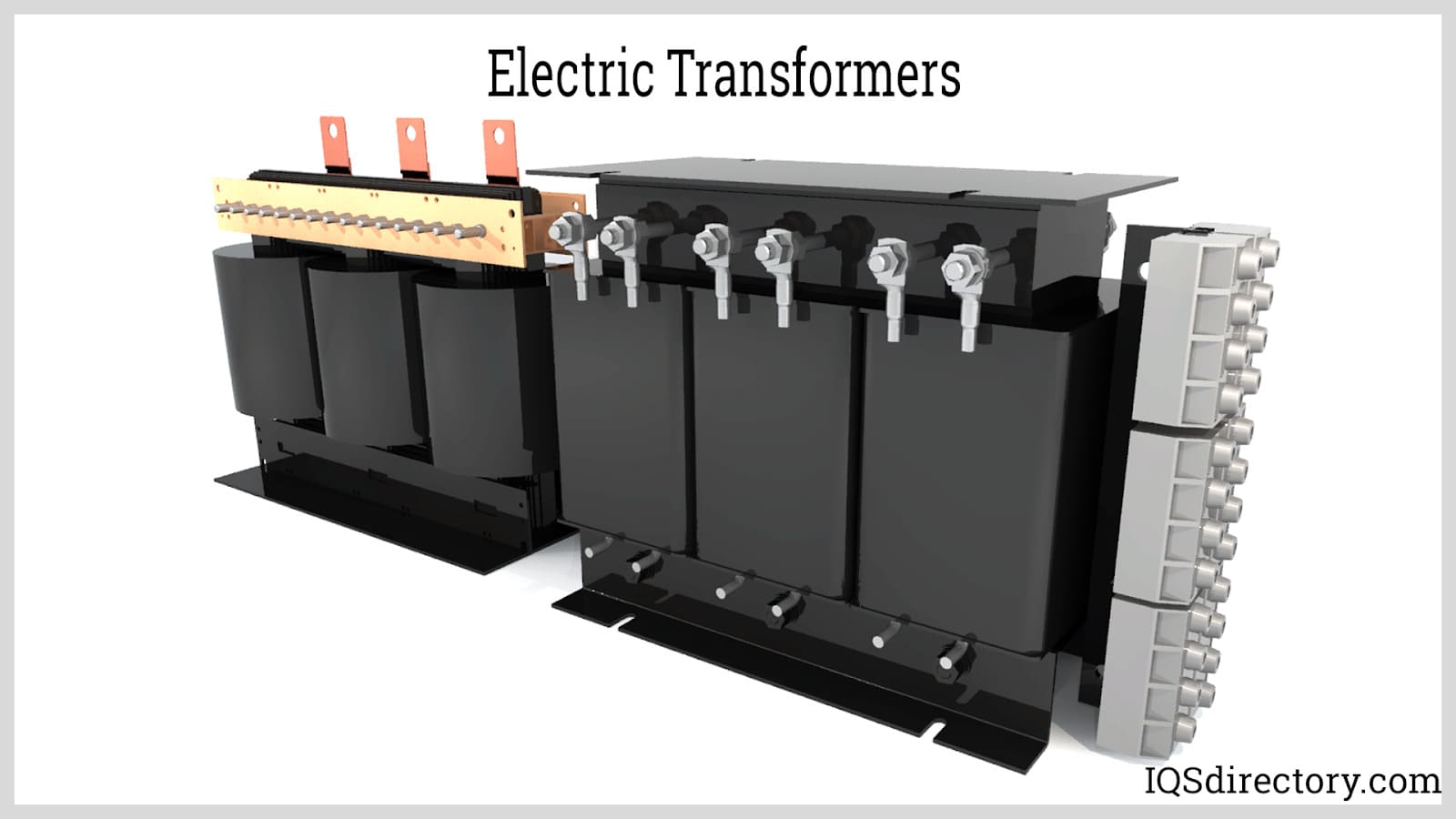
Electric transformers are static electrical machines that transform electric power from one circuit to the other without changing the frequency. An electrical transformer can increase or decrease the voltage with...
Please fill out the following form to submit a Request for Quote to any of the following companies listed on
Explanations of plug-in transformers, lists of manufacturers, and descriptions of uses for plug-in transformers
You will learn:
Plug-in transformers, classified as class 2 power supplies, are engineered for attachment to 15 amp, 120 or 240-volt alternating current (AC) branch circuits. The distinction of class 2 power supplies is established by Underwriters Laboratory (UL) 1310, which outlines the safety criteria for class 2 power units and battery chargers. UL1310 ensures user safety by adhering to these stringent standards. Plug-in transformers function as AC adapters, power supplies, or class 2 power units.
There are three definitive restrictions for plug-in transformers: they must not deliver more than 100 VAS of continuous power, should not provide current under short circuit situations, and must maintain a safety extra-low voltage (SELV) compliant open circuit voltage of either 90V DC or 42.4 V peak AC.
Compact plug-in transformers are designed to connect directly into wall outlets, delivering low direct current voltages ideal for powering electronic gadgets. They safeguard low-voltage electronics from exposure to higher voltages and eliminate the need for cooling mechanisms. This enables plug-in transformers to be more compact, lightweight, and space-efficient. They reduce heat impact on delicate circuits and provide a lower power output.
Plug-in transformers are essential electromagnetic devices for converting electrical power from one voltage to another, making devices safe and compatible with different electrical systems. Whether in household appliances, consumer electronics, or industrial automation, plug-in transformers ensure efficient voltage regulation, protection, and energy isolation. Understanding their operation is crucial for engineers, electricians, and users who must choose the right transformer for specific voltage, current, and application needs. The typical structure of a plug-in transformer includes a magnetic core and two sets of wire coils, known as the primary and secondary windings. When alternating current (AC) flows through the primary winding, it generates a magnetic field in the core. This magnetic field then induces an electromotive force (EMF) in the secondary winding, resulting in the transformation of voltage and current levels. This step-down or step-up process allows electrical devices to operate safely at required voltages, minimizing risk and maximizing performance.
The primary winding in a plug-in transformer is responsible for receiving input voltage—most commonly standard 120-volt AC for North American households or 240 volts in European regions. By converting the incoming AC voltage to a manageable, often lower, output voltage, plug-in transformers ensure electrical safety and device compatibility. The core—often made from high-permeability steel laminations—runs through the middle of the windings to maximize energy transfer and reduce core losses. As current enters the primary winding, a time-varying magnetic field is established, which is a prerequisite for electromagnetic induction in the secondary coil. The effectiveness of voltage transformation depends partly on how efficiently the magnetic field is transmitted through the core.
The secondary winding is tasked with delivering the transformed output voltage to the load or device. The voltage that appears here is determined by the turns ratio—the relative number of coil turns on the secondary winding compared to the primary. This principle underpins the design of step-down transformers (reducing voltage for low-voltage electronics, chargers, and adapters) and step-up transformers (raising voltage where required). For example, if the turn ratio between the primary and secondary coil is 2:1, the output voltage is half the input. Conversely, higher-value secondary windings can increase output. For a voltage drop to just 3 volts at the secondary, the primary coil might need up to 40 times the turns. This scalability makes plug-in transformers versatile for various voltage conversion needs in power supplies, adapters, and converters for different types of equipment.
Both windings are wrapped around a shared magnetic core, which channels the magnetic flux generated during operation. The core serves as the foundation for efficient electromagnetic energy transfer—optimizing magnetic permeability and minimizing magnetic reluctance are critical design requirements for transformer cores. In plug-in transformer construction, the core may be laminated or toroidal to further minimize energy loss from eddy currents and hysteresis, boosting transformer efficiency. Core construction varies: some units have separate windings positioned side-by-side or layered, while others employ a continuous winding structure. Typically, materials such as silicon steel and ferrite are chosen for their high saturation flux density and low energy loss. These differences allow manufacturers to optimize plug-in transformers for compactness, heat dissipation, and noise reduction, making them suitable for a range of applications, from simple power adapters to high-precision instrumentation.
The design and quality of the core directly affect energy efficiency, longevity, and safety. Adhering to international standards—such as UL, IEC, and RoHS—is vital for ensuring plug-in transformer reliability and safe operation. Compliance with these standards also impacts the acceptance of plug-in transformers in commercial and consumer markets.
Magnetic permeability and minimal resistance, or reluctance, are essential core features, promoting effective energy transfer. Choosing the proper core shape and material helps minimize losses and heat, addressing user concerns about transformer efficiency, noise, and warming during prolonged use. Some high-performance plug-in transformers use grain-oriented laminated cores, further reducing core loss.
Plug-in transformers utilize windings made from either copper or aluminum wire. Copper is typically favored due to its superior electrical conductivity—approximately 0.6 times the resistivity of aluminum—resulting in lower energy losses and higher transformer efficiency. Aluminum windings, while lighter and less expensive, must be larger to carry the same current as copper, resulting in bulkier designs. Insulation is applied to the windings to ensure safety and prevent short circuits. The winding configuration—such as layer winding, bifilar winding, or universal winding—can impact performance factors, including frequency response, inductance, and electromagnetic interference (EMI) shielding. These technical aspects are significant considerations for power supply manufacturers, engineers choosing AC-DC adapters, and consumers seeking plug-and-play transformers for sensitive electronics or charging devices.
The primary winding is connected to the power input source (e.g., wall outlet), while the secondary winding supplies power to the electrical load. Selection of the winding material and configuration directly influences electrical isolation, voltage regulation, and product durability—critical factors for users in applications from industrial control to consumer electronics.
Wire resistance has a significant impact on plug-in transformer performance and energy efficiency. Measured in ohms (Ω), resistance affects the current flow, voltage drop, and potential power loss inside the transformer. Influencing factors include the core and wire materials, wire length, ambient temperature, and wire thickness (gauge). Longer wires increase resistance, leading to more heat and reduced transformer efficiency. Thicker wires, with larger cross-sectional areas, decrease resistance, allow more current flow, and reduce undesirable heating—especially important in plug-in transformers designed for high-current applications or continuous operation.
The material's resistivity, typically lower for copper than aluminum, and proper winding gauge selection are crucial for optimizing transformer design. In practice, the primary winding is engineered for low resistance to maximize the amount of current it can carry effectively, while the secondary winding (often with thinner wires) may have higher resistance, affecting the voltage delivered to the end device. High resistance causes voltage drop and power loss, both of which decrease the efficiency and output performance of the plug-in transformer. Electrical engineers, repair technicians, and end-users therefore consider wire resistance and transformer ratings (such as VA rating, efficiency, and load capacity) when selecting the right plug-in transformer product for their needs.
Thermal management is a key factor in the longevity and safe operation of plug-in transformers. All electronic devices, including plug-in voltage converters and adapters, generate heat as a function of energy conversion. Excessive temperature rise in transformer windings, caused by resistance or inadequate heat dissipation, can degrade insulation, reduce efficiency, and shorten transformer lifespan. Manufacturers use high-temperature insulation materials—rated according to international classifications (Class A, B, F, H, etc.)—to ensure operational safety and reliability.
Insulation rating defines the maximum permissible operating temperature, accounting for ambient conditions, internal heat rise, and permissible overload. Reliable thermal management not only prolongs the service life of plug-in transformers but is also a major selling point for users concerned about device safety, efficiency, and continuous running capability. For best performance, select plug-in transformers tested for overload resistance, low heat generation, and certified by recognized safety agencies. Regular inspection and correct installation, in line with manufacturer specifications, further minimize overheating risks.
Plug-in transformers are essential electronic components used to ensure electronic equipment receives the correct voltage for safe and efficient operation. As a key part of power conversion and voltage regulation, plug-in transformers support proper function and durability of a wide variety of electrical devices. The three main voltage categories for electronic devices are dual voltage, 110V-120V, and 220V-240V. Plug-in transformers are commonly required for both 110V-120V and 220V-240V systems, providing voltage adaptation and protection, but are not needed for dual voltage devices that can already accept multiple voltage ranges.
Many modern electronics require lower voltages than the standard output from wall outlets. Wall plug-in transformers—also referred to as wall adapters, wall warts, power cubes, and wall bumps—are compact AC-DC power supplies that plug directly into electrical sockets. Available in various voltages, current ratings, power outputs, and polarities, these convenient voltage converters offer designers exceptional flexibility when dealing with high voltage input issues. Essentially, plug-in transformers safeguard sensitive, low voltage electronic devices from high voltage, electrical surges, and other power supply inconsistencies.
The primary differences between types of plug-in transformers include output voltages, rated power levels (watts), current capacities, and polarity configurations. Transformers are commonly categorized by whether their connections are additive or subtractive, which depends on the way their winding coils are linked. An additive transformer connects the finish of one winding to the start of another, resulting in cumulative voltage, whereas a subtractive transformer’s windings produce a differential effect. Polarity—how the primary and secondary windings interact—is a significant design consideration for engineers when integrating plug-in transformers into electrical systems, especially in industrial automation, consumer electronics, and global power distribution networks.
Understanding transformer polarity helps in choosing compatible step up transformers, step down transformers, or multi-voltage plug-in transformers for specific applications. This knowledge is vital for preventing power compatibility issues, electrical hazards, and device damage, particularly when designing equipment for international or multi-region use.
Interchangeable plug plug-in transformers offer flexibility for international travelers and businesses operating in multiple countries. By incorporating a removable plug design, these universal power adapters allow users to select the correct plug configuration to fit varying international power outlets. The most common function of interchangeable plug plug-in transformers is to accommodate different plug types and voltage standards encountered in global travel, thus supporting multi-region electronics and portable devices.
Offering input voltage ranges from 100V to 240V AC and output options such as 24VDC, these adapters comply with international safety certifications. They also boast high energy efficiency and are available with multiple output connectors to support both commercial and personal electronics. Interchangeable plug plug-in transformers are vital for reducing downtime, ensuring continuous power supply, and protecting voltage-sensitive devices while traveling or relocating globally.
Many countries outside North America use 220V to 240V AC as the standard outlet voltage, compared to the 110V to 120V used in the U.S. and Canada. To safely use American electronics—most of which are rated for lower voltage—in countries with higher mains voltage, a 240V plug-in voltage transformer is necessary. These plug-in step-down transformers protect American devices by converting higher input voltage down to the safe operating level, preventing electrical overload or irreversible damage to components and circuits.
The selection of the proper plug-in transformer depends on the electronic device’s wattage requirement, input voltage, and label instructions. When purchasing voltage converters, users should match the wattage (“W”) and voltage specifications of their devices. Plug-in step-down transformers also commonly include built-in surge protection and overload safeguards to ensure device safety and longevity, making them indispensable for international travel, industrial power tools, and importing electronics.
Dual voltage plug-in transformers enhance convenience for users dealing with multiple voltage standards. These specialized devices include primary or secondary windings that allow switching between two output voltages. Often labeled with dual voltage capabilities, they enable seamless voltage conversion for electronics used in both 120V and 240V environments. Multi-winding, dual voltage plug-in transformers are commonly used in laptop adapters, travel chargers, and commercial-grade equipment that must interface with diverse global power grids.
Capable of converting input voltage to various output levels, dual voltage transformers typically feature multiple tap settings, allowing the user to select the optimal output for their appliance. This design not only ensures reliable power regulation but also enhances safety by isolating different voltages as needed. For travelers, international students, and businesses operating cross-border, dual voltage plug-in transformers simplify connectivity and adaptation to varying electrical infrastructures, while reducing the risk of electrical faults.
AC to DC plug-in transformers, commonly known as AC-DC adapters, convert alternating current (AC) from the mains supply into direct current (DC) suitable for a wide range of electronic devices. This internal conversion is achieved through a rectification circuit—often with full-wave rectification—which drastically improves conversion efficiency and stability. AC/DC plug-in transformers meet the needs of devices ranging from small household gadgets to industrial automation controls, ensuring consistent DC power supply for sensitive electronics such as LED lights, routers, sensors, and consumer appliances.
Two popular form factors are available: wall mount plug-in transformers (direct-to-wall socket) and desk mount plug-in transformers (inline between the wall and device). Wall mount AC/DC adapters offer a clutter-free, space-saving solution, while desk mount units provide flexibility for stationary equipment. When selecting an AC to DC transformer, pay attention to output voltage (e.g., 5V, 9V, 12V, 24V DC), amperage rating, energy efficiency certifications, and polarity markings to ensure safe, reliable operation and device compatibility.
Among the most frequently used types, 24 VAC plug-in transformers are a staple for residential and commercial low voltage applications such as doorbells, thermostats, security systems, HVAC controls, and landscape lighting. These step-down transformers convert standard 120 VAC or 115 VAC input to a safe 24 VAC output, ideal for powering low voltage electronics with minimal risk of shock or overheating. Designed for ease of installation, 24 VAC plug-in transformers are valued for their reliability, efficiency, and simple maintenance requirements.
Many 24 VAC plug-in transformers are equipped with fuse or breaker protection, multiple output connectors, and variable cable lengths to suit diverse application needs. By maintaining steady voltage output, these transformers optimize the performance and lifespan of connected equipment, while meeting safety regulations in residential and commercial electrical systems.
Isolation transformers provide electrical isolation between the input (primary winding) and the output (secondary winding), protecting sensitive systems from voltage surges, spikes, ground loops, and electrical noise. Their primary function is to safeguard electronic equipment, improve power quality, and contribute to a safe electrical environment. Widely used in medical, laboratory, industrial, and audio equipment, isolation transformers prevent direct electrical connection that could result in damage or interference.
These transformers are available in various specialized types, including medical-grade isolation transformers, galvanic isolation transformers, ultra isolation models, and drive isolation transformers, each addressing unique safety or performance requirements. By adjusting input voltage to match the output voltage required by the load, and by providing superior electrical insulation, isolation transformers help ensure compliance with industry standards, minimize downtime, and extend the service life of critical equipment.
These six types of plug-in transformers represent only a portion of the options available to consumers, engineers, and product designers. Each transformer type plays a distinct role in meeting voltage regulation, power conversion, and safety needs for applications ranging from consumer devices to industrial and commercial electrical systems. Choosing the right plug-in transformer involves evaluating input/output voltage, current rating, device compatibility, safety certifications, and intended use environment. Manufacturers and distributors can provide expert guidance on technical specifications, regulatory compliance, and installation best practices, ensuring optimal performance and safe integration into any power supply system.
One of the challenges of working with electricity is its production of electromagnetic fields that can interfere with the performance of other electronics. While electromagnetic fields are a danger in industrial and manufacturing operations, protection against them is especially critical in the medical profession where multiple electronic devices may be positioned in a recovery room or surgical bay. Plug-in power transformers are an essential tool for such situations that helps protect equipment and patients.
The types of medical equipment that depend on plug-in transformers include dental tools, testing labs, and heart monitors. The inclusion of plug-in transformers ensures that medical devices perform properly and provide accurate readouts. Every aspect of human health requires stable electrical supplies that are protected from surges, spikes, and instabilities by plug-in transformers.
Isolation transformers for medical use act as a buffer between the power supply and hospital and medical equipment. As with all forms of plug-in transformers, isolation transformers lower voltage to fit the requirements of medical equipment. Their key feature is their ability to eliminate electrical spikes and surges, which can seriously damage sensitive and delicate equipment.
Wire selection when designing a plug-in transformer is an exceptionally critical factor since each type of wire provides benefits and drawbacks regarding the performance of a plug-in transformer. The most commonly used type of wire is insulated round copper wire, which is the wire to which most people are accustomed. The two forms of wire that are used in the manufacture of plug-in transformers are round wire and flat wire.
Wire for plug-in transformers are made of copper or aluminum with copper being the most popular due to the disadvantages associated with aluminum. The argument of copper or aluminum has been going on for years with aluminum being lighter while copper is a better conductor but bulkier.
Round wire has a round conducting section that is covered with an insulation that can be made of polyglass, polyamide, or polyester. The insulation for round wire comes in a wide variety of types, which are used in accordance with the application for which the wire is used.
The traditional option for the manufacture of plug-in transformers is round wire, which is less expensive and is the most efficient. With higher frequencies, round wire can suffer the skin effect, where current flows along the surface of the wire, increases the wire’s resistance, a factor that can be overcome using Litz wire.
The cross-sectional appearance of flat wire is rectangular or square, a shape that has benefits that are unlike those offered by round wire. It is manufactured by pulling or drawing copper or aluminum through a die with the cross-sectional appearance of the required shape. The result of the process is thinner wire with the same width as round wire.
The shape of flat wire makes it more flexible, easier to shape, and allows for more contact points. Since space is limited in plug-in transformers, flat wire is ideal since it can fit into any space regardless of the size of the space. In addition, it has 60% more surface area but with the same cross-sectional area, which limits the skin effect at higher frequencies that leads to efficient performance.
Flat wire has higher energy storage, higher thermal efficiency, and limits the skin effect at higher frequencies. The downside of flat wire is its cost and being less available.
Litz wire is made of several tiny strands of wire that have been woven together in a specific pattern. It is a very flexible wire that is easy to use and commonly used for high frequency plug-in transformers. Unlike flat wire and round wire, Litz wire seldom suffers from the skin effect. It is available in a wide range of sizes that are differentiated by the number of stands (N) and the American Wire Gauge (AWG or XX).
There are eight common forms of Litz wire numbered type 1 to type 8, which vary in their structure, method of twisting, insultation, and other factors.
Plug-in transformers are specifically designed to be low energy devices with a secondary winding that has an impedance, resistance to electrical current flow, that is higher and helps limit current flow to a load. For safety purposes, plug-in transformers are double insulated, making them safe to use if there is not a protective ground present.
The National Electric Code (NEC) defines a plug-in transformer as a portion of a system that is between the load and power source and is connected to a piece of electrical equipment. The power limitations of plug-in transformers make them safe from causing fires as well as providing protection from power spikes and power surges. Plug-in transformers are designed and constructed with high impedance, which is why they are able to offer protection for low energy devices.
The use of wall plug-in transformers is important for the protection of low voltage devices that could be damaged by higher voltages. The design of plug-in transformers removes the need for various cooling methods since electronics can overheat during use. This factor makes it possible for manufacturers to produce smaller, lighter, and intricate devices with sensitive circuits.
The main factor for audio plug-in transformers is their impedance, which is provided to microphones, amplifiers, loudspeakers, and recording equipment. Impedance is measured in Ohms, the measure of resistance between two points of a conductor. When the impedance of a plug-in transformer is high, the measure of Ohms is high and the amount of interference in a speaker or headset is lower. Headsets that are used to listen to music around the house have low resistance at 30 Ohms. Professional sound engineers have headsets with high resistance at 300 Ohms.
Plug-in transformers efficiently match impedance levels for audio equipment for efficient power transfer without any distortions or overloads. The key factor is the avoidance of distortions especially in cases where music is being recorded or being projected through speakers.
In the early days of international travel, when Americans were mainly going to Europe, travelers were shocked at the different electrical sockets they found in different countries. At the time, such differences were inconsequential since electrical devices such as computers and cell phones had not been invented. As the number of electronics have rapidly grown, it has become necessary for international travelers to be prepared of the different types of electrical supplies and socket types that are found in foreign nations. This is especially necessary for computers that can be damaged by the higher levels of output found in foreign countries, which can be up to 240 VAC.
International plugs are classified by types with certain types being used in different countries. England uses type G plugs while Denmark uses types C, E, F, and K. A very common form of tour of Europe is to land in London and cross the English Channel by ferry to the Netherlands to begin a tour of the continent. Describing such a trip using sockets and voltage types, in England, a power source is 230 VAC and requires a type G plug-in transformer. When the ferry lands in the Netherlands, the voltage remains the same but the type of plug-in transformers changes to types C and F.
Plug-in transformer manufacturers are very aware of the challenges of traveling internationally and provide safe and reliable transformers that have interchangeable input plugs. This makes it possible for a traveler to immediately adapt to the power supply of a country.
The purchase of highly sensitive technical equipment involves a huge investment that can be destroyed with the use of the wrong type of power supply. Plug-in transformers have been used for years to protect sensitive electronics and enhance their power supply. They smooth power disturbances and reduce electrical noise that can diminish the performance of sensitive devices. In essence, plug-in transformers clean up power delivered from in-home and office outlets.
Technological devices can malfunction or be damaged when the power they receive is inconsistent with the power they require for their operation. Medical equipment, computers, and audio systems necessitate the transforming of power for their proper operation. Plug-in transformers, designed to step down power input, work as a valuable tool to protect sensitive devices and ensure their safe operation.
Electric transformers are static electrical machines that transform electric power from one circuit to the other without changing the frequency. An electrical transformer can increase or decrease the voltage with...
Power transformers are electrical instruments used in transmitting electrical power from one circuit to another without changing the frequency. They operate by the principle of electromagnetic induction. They are used in transmitting electrical power between...
An electrical transformer is a passive machine that transfers electrical energy from one circuit to another using a magnetic flux to induce an electromotive force. Transformers are used to increase (step-up) or decrease (step-down) voltages without changing the frequency of the electric current...
A toroidal transformer is a type of electrical transformer constructed with a torus or donut-shaped core. Its primary and secondary windings are wound across the entire surface of the torus core separated by an insulating material...
Electronically operated equipment depends on power transformers to convert electrical currents into voltage. Current transformers store and transport energy through power lines and grids...
Power supplies are electrical circuits and devices that are designed to convert mains power or electricity from any electric source to specific values of voltage and current for the target device...
An AC power supply is a type of power supply used to supply alternating current (AC) power to a load. The power input may be in an AC or DC form. The power supplied from wall outlets (mains supply) and...
An AC power cord is a detachable way of providing an alternating current of electric energy from a mains power supply to an electrical appliance or equipment. Serving industries like...
A DC DC power supply (also known as DC DC Converter) is a kind of DC power supply that uses DC voltage as input instead of AC/DC power supplies that rely on AC mains supply voltage as an input...
A DC power supply is a type of power supply that gives direct current (DC) voltage to power a device. Because DC power supply is commonly used on an engineer‘s or technician‘s bench for a ton of power tests...
An electric coil, or electromagnetic coil, is an electrical conductor that contains a series of conductive wires wrapped around a ferromagnetic core that is cylindrical, toroidal, or disk-like. Electric coils are one of the simplest forms of electronic components and provide...
Electrical plugs, commonly known as power plugs, are devices responsible for supplying and drawing current from a receptacle to the circuitry of an electrical appliance...
By definition a power supply is a device that is designed to supply electric power to an electrical load. An electrical load refers to an electrical device that uses up electric power. Such a device can be anything from...
Inductors are passive two terminal components of an electric or electronic circuit that are capable of storing energy in magnetic form. They oppose sudden changes in current and they are also called coils or chokes...
A NEMA connector is a method for connecting electronic devices to power outlets. They can carry alternating current (AC) or direct current (DC). AC current is the typical current found in homes, offices, stores, or businesses...
A power cord is an electrical component used for connecting appliances to an electrical utility or power supply. It is made from an insulated electrical cable with one or both ends molded with connectors...
A programmable power supply is a method for controlling output voltage using an analog or digitally controlled signal using a keypad or rotary switch from the front panel of the power supply...
A solenoid coil is a common electrical component that uses a wire that is tightly wrapped around a core, usually made of metal, to generate an electromagnetic field. When an electrical current is passed through the coil, the electromagnetic field that is created provides energy for linear motion...
A voice coil is a winding of a wire, usually copper, aluminum, or copper-clad aluminum that is wrapped around a former (often called a bobbin) and then attached to the apex of a speaker cone...
Thomas Edison developed the power distribution system in 1882. He wrapped a copper rod in jute, a soft shiny fiber from plants, as an insulator. The jute wrapped copper rod was placed in a pipe with a bituminous compound...