Electric Transformers
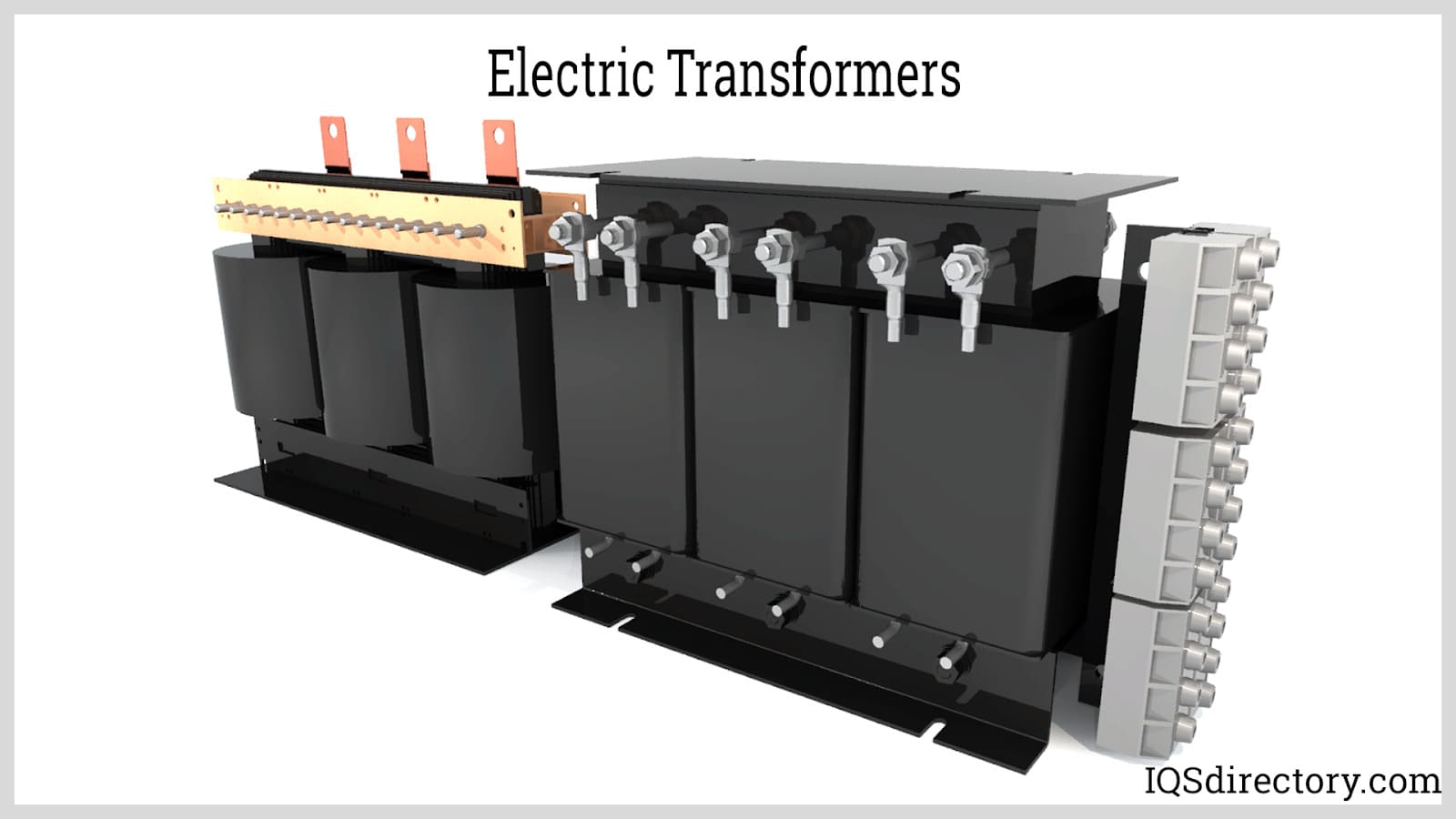
Electric transformers are static electrical machines that transform electric power from one circuit to the other without changing the frequency. An electrical transformer can increase or decrease the voltage with...
Please fill out the following form to submit a Request for Quote to any of the following companies listed on
This article takes an in-depth look at power transformers.
Read further and learn more about topics such as:
Power transformers are crucial electrical devices engineered to transfer electrical energy between circuits without changing the frequency. They work on the basis of electromagnetic induction and are pivotal in delivering power from generators to primary distribution systems. Power transformers are tasked with adjusting voltage levels in distribution networks by either stepping up or stepping down the voltage. These static devices have no moving or rotating parts, operating effectively within an alternating current (AC) system.
These transformers are categorized based on their voltage range, usually spanning from 33 kV to 400 kV, and they often hold ratings above 200 MVA. Common voltage ratings for power transformers are 400 kV, 200 kV, 110 kV, 66 kV, and 33 kV. In contrast, other transformer types, such as distribution transformers, operate within voltage ranges of 230 V to 11 kV, along with instrument transformers.
Power transformers play an essential role in minimizing substantial energy losses attributed to Joule’s effect, especially when transmitting large volumes of electrical power across extensive distances. They accomplish this by converting electrical energy to high voltage for effective transmission before stepping it down to safer, low voltages. These transformers find extensive use in power plants, industrial establishments, and electric utility firms.
Power transformers operate according to Faraday’s law of electromagnetic induction, which is fundamental to the functioning of all transformers, inductors, motors, generators, and solenoids.
Faraday’s law states that an electromotive force (emf) is induced across a closed-loop when it is exposed to a varying magnetic field.
When alternating current flows through a coil (the primary winding), it generates an alternating or fluctuating magnetic flux around the coil. This magnetic flux is directed through a ferromagnetic core to efficiently reach the secondary winding. The changing magnetic flux induces an electromotive force (emf) in the secondary winding through electromagnetic induction. This induced emf then drives a current through the secondary winding.
The total voltage in a winding is the product of the voltage per turn of the coil and the number of turns. Because the voltage per turn is the same for both the primary and secondary windings, the voltage induced in the secondary winding can be related to the input voltage of the primary winding. This relationship is expressed by the following equation:
Vs = Vp/Np x Ns
In this formula, V represents the total voltage in the winding, N indicates the number of turns in the winding, and the subscripts p and s denote the primary and secondary windings, respectively. The ratio of the number of turns in the secondary winding to the number in the primary winding (Ns/Np) is referred to as the turns ratio.
When the secondary winding has fewer turns than the primary winding, the output voltage is lower than the input voltage, characteristic of a step-down transformer. Conversely, if the secondary winding has more turns than the primary winding, the output voltage is higher than the input voltage, which is typical of a step-up transformer.
Because energy is conserved, the relationship between the alternating currents in the primary and secondary windings is expressed by the following equation:
Vp Ip = Vs Is
In this equation,I denotes the current.
The fundamental components of transformers include the core and the primary and secondary windings, which are explored in more detail in this chapter.
The core of a transformer supports the windings and provides a path of low reluctance for the magnetic flux. It is constructed by stacking and laminating thin steel sheets, which are insulated from one another by a coating. To minimize eddy current and hysteresis losses, these sheets are typically less than one millimeter thick and have a carbon content below 0.1%. Eddy currents are further reduced by alloying the steel with silicon. The vertical sections of the core that support the windings are known as the limbs, while the horizontal sections that connect the limbs are called the yokes.
The windings of a transformer are composed of copper or aluminum coils with a specific number of turns. Copper is generally preferred due to its high electrical conductivity and ductility, which reduce the amount of winding material needed and facilitate easier wrapping around the core.
A transformer includes at least two windings: the primary and the secondary. The primary winding is where the input voltage is applied, while the secondary winding is where the output voltage is received. Depending on the design and application, either the primary or secondary winding can be configured as the high voltage (HV) winding or the low voltage (LV) winding:
Additional components of power transformers include the following:
Insulating materials are essential for isolating the windings from the core, between the primary and secondary windings, and between each turn of the windings. These materials protect the transformer from potential damage. Ideal transformer insulators should possess high dielectric strength, excellent mechanical properties, and the ability to withstand high temperatures.
While paper and pressboard are used as insulators in dry-type transformers, they have limited service lives and often require frequent replacement due to degradation. Therefore, transformer oils are more commonly used than solid insulating materials. Transformer oils provide superior insulation between conductive parts, act as coolants for the coil and winding assembly, and offer fault detection capabilities. These oils typically consist of hydrocarbons such as aromatics, paraffins, naphthenes, and olefins. To maintain the oil's dielectric properties and insulating effectiveness, it is crucial to prevent oil contamination.
Tap changers are devices used to regulate a transformer's output voltage by adjusting the number of turns in one winding. This adjustment alters the turn ratio in response to varying input voltages and load conditions. When the transformer is offloaded, the output voltage increases, while it decreases under load conditions. Tap changers are usually connected to the high-voltage (HV) winding to allow fine voltage adjustments and reduce core losses. Additionally, since the current in the HV winding is lower, this configuration helps minimize the risk of sparking and igniting the transformer oil.
There are two types of tap changers. On-load tap changers adjust the voltage without interrupting the current flow to the load, allowing for continuous operation. In contrast, off-load tap changers require the transformer to be disconnected from the load before adjustments can be made.
Bushings are insulating components that facilitate the connection between the current-carrying conductors of an electrical network and the ends of the transformer windings. Typically, bushing insulation is made from porcelain or epoxy resin. These bushings are mounted on the exterior of the main transformer tank.
The transformer tank (or the main tank) houses and protects the core, windings, and other components from the external environment. It serves as the container for the transformer oil. It is constructed from rolled steel plates or aluminum sheets.
The following components are present in large transformers that are insulated with hydrocarbon mineral oil:
The conservator is a tank positioned above the main tank and bushings, serving as a reservoir for transformer oil. It supplies oil to the main tank inside the transformer through a pipeline. The conservator features a flexible bladder that accommodates the expansion and contraction of the oil, providing sufficient space for oil expansion during high ambient temperatures. It is vented to the atmosphere to manage pressure changes, allowing air to enter or exit as the oil expands and contracts.
The breather ensures that moisture-free air is supplied to the conservator by passing air through a bed of silica gel within a cylindrical container. The silica gel serves as an air filter, controlling and reducing the moisture level inside both the conservator and the main tank. The breather is connected to the conservator via a pipeline.
Moisture can compromise the insulating properties of transformer oil and potentially cause internal faults. Therefore, it is essential to effectively remove moisture to maintain the transformer’s performance and reliability.
The cooling system is an essential component of transformers, regardless of the type of insulating material used. Power losses in transformers generate heat, which increases the temperature of the windings and core. As a result, the temperature of the insulating material also rises. Without an effective cooling system, these components could suffer damage or decomposition from sustained high temperatures. Transformer cooling systems typically include fans, radiators, and cooling tubes. Heat is transferred through natural and/or forced convection and radiation.
For dry-type transformers, cooling can be achieved through the following methods:
For oil-immersed transformers, cooling can be achieved through the following methods:
The explosion vent is a metallic pipe with a diaphragm at its open end, situated just above the conservator tank. It is designed to release gases, transformer oil, and excess energy during internal faults, thereby relieving dangerous pressure levels within the transformer and preventing explosions. When internal faults cause the pressure to rise to critical levels, the vent allows this pressure to be released into the atmosphere, causing the diaphragm to burst at a relatively low pressure to safeguard the transformer.
The Buchholz relay is installed in the pipeline connecting the conservator and the main tank of a transformer. It detects faults by sensing the gases emitted during such faults and activates both the trip and alarm circuits. When the relay detects these gases, it triggers the trip circuit, which in turn causes the circuit breaker to interrupt the current flow to the primary winding. The emitted gases are produced by the heat generated from internal faults.
Power transformers can be classified according to their core and winding construction, turns ratio, number of phases, and core material.
1. Core and Winding Design and Configuration
Berry-type transformers have a core designed like the spokes of a wheel. They utilize distributed magnetic circuits and contain multiple independent magnetic circuits, typically more than two.
In core-type transformers, the primary and secondary windings encircle the core. The core is made by joining two L-shaped steel strips, which are then stacked to create the core layers. To minimize reluctance at the joints, the strips are arranged to avoid continuous joints. The flux is carried by the limbs and yoke of the core.
In shell-type transformers, the core encircles both the primary and secondary windings. The core is constructed from E-shaped and I-shaped steel strips, which are stacked to form layers. In this design, the central limb of the core carries the entire magnetic flux, while the side limbs each carry half of the flux.
2. Turns Ratio (Ns/Np)
Isolation transformers have a turns ratio equal to 1, which means the number of turns in the primary and secondary windings is equal. They are used to isolate the load from the power source while supplying alternating currents. They protect the electrical device, operation, and persons from electrical noise, shock, and damage. They are commonly used in computers, measurement devices, industrial machinery, laboratory and medical equipment, and other sensitive equipment.
Step-down transformers have a turns ratio of less than 1, which means that the primary winding has more turns. These transformers convert the high voltage and low current input from the primary winding to a low voltage and high current output on the secondary winding.
In electricity distribution, step-up transformers are located at power generating stations, while step-down transformers are installed at substations. This application is further illustrated in the image below:
Step-up transformers have a turns ratio greater than 1, which means that the secondary winding has more turns. These transformers convert the low voltage and high current input from the primary winding to a high voltage and low current output on the secondary winding.
3. Phases
Autotransformers consist of a single winding tapped at certain points across its length to supply a fraction of the primary voltage. The primary and secondary windings are linked to each other, which are wounded on a single core. Autotransformers have a more compact size and are cheaper than the conventional double winding transformer, which can deliver the same VA rating. However, they do not have electrical isolation between the primary and secondary windings. They are widely used in induction motors, railways, audio systems, and lighting systems.
Single-phase transformers consist of a single pair of windings arranged around a core and produce a single alternating voltage, represented by a single sine wave. They feature four terminals, with each winding having two terminals. These transformers do not include star (wye) or delta connections.
Single-phase transformers have a straightforward construction and are commonly used in residential and light commercial power supplies. They are particularly prevalent in rural areas where electrical demand is lower, making them a cost-effective choice for such applications.
Three-phase transformers are composed of three pairs of primary and secondary windings. They can be constructed by connecting three single-phase transformers to form a transformer bank or by assembling three pairs of windings into a single laminated core. Three-phase transformers generate three-phase alternating current flowing in separate conductors. Three sine waves represent this, and the waves are separated by 120 degrees from one another. The amplitude is reached more frequently which makes three-phase transformers supply power at an almost constant rate.
The windings of both the primary and secondary sides of three-phase transformers can be connected in either delta or star configurations. These connections can be the same or different on the primary and secondary sides. As a result, several configurations of three-phase transformers are possible:
Three-phase transformers are preferred for heavy-duty applications due to their efficient utilization of winding connections. They are widely used in large motors, electric power distribution networks, and other significant loads. Moreover, three-phase transformers are more economical than using three single-phase transformers to achieve the same VA rating.
4. Core Material
Air core transformers lack a physical core. Instead, their primary and secondary windings are wrapped in a solid insulating material. These transformers are commonly used for transmitting radio-frequency currents.
Ferrite core transformers utilize a core made of ferrite, a ceramic material composed of iron oxides, zinc, nickel, and manganese. Common types of ferrites used in transformers include manganese-zinc ferrite and nickel-zinc ferrite.
Ferrites are known for their high magnetic permeability, which enhances the flow of magnetic flux through the material. They also offer high electrical resistivity and low eddy current losses across a broad frequency range, making them well-suited for high-frequency applications. As a result, ferrite core transformers are commonly employed in wideband transformers and various electronics applications.
Iron core transformers feature an electromagnetic core constructed from laminated iron sheets. This type is the most commonly used within this category. Iron cores provide high flux linkage due to their excellent magnetic properties, making them effective for a wide range of applications.
Toroidal core transformers have cores shaped like toruses or donuts, constructed from iron or ferrite. The primary and secondary windings are wound around these ring-shaped cores. The toroidal design reduces magnetic flux leakage and enhances both inductance and Q factors, leading to high efficiency. These transformers are often used in telecommunications, power distribution, and industrial control systems.
Power transformers experience four main types of losses that influence their efficiency:
Copper losses, also known as resistive or I²R losses, occur due to the electrical resistance in the windings as current flows through them. The resistance of the winding material, which affects these losses, depends on factors such as the material’s length, cross-sectional area, nature, and temperature. The amount of current flowing through the windings also impacts copper losses. These losses are quantified using the formula I²R.
Hysteresis losses arise from the friction experienced by the ferromagnetic molecules in the core during the magnetization and demagnetization processes. As the magnetizing force alternates between forward and reverse directions, internal friction generates heat within the transformer.
Eddy currents are generated in the core's cross-section due to fluctuating magnetic fields. To minimize these losses, transformer cores are constructed from thin, laminated metal sheets. Each lamina is insulated with a special coating, which reduces the path available for eddy currents and limits their flow.
Flux losses occur when some magnetic flux lines from the primary winding bypass the secondary winding and flow through the air instead. This can happen due to magnetic saturation of the core, where the core is unable to accommodate additional flux lines. Additionally, the difference in reluctance between the air and the core can contribute to these losses.
Electric transformers are static electrical machines that transform electric power from one circuit to the other without changing the frequency. An electrical transformer can increase or decrease the voltage with...
An isolation transformer, just like typical transformers, is a non-moving device that transmits electrical energy from one circuit to another without requiring any physical contact. It works on the idea of magnetic...
An electrical transformer is a passive machine that transfers electrical energy from one circuit to another using a magnetic flux to induce an electromotive force. Transformers are used to increase (step-up) or decrease (step-down) voltages without changing the frequency of the electric current...
A toroidal transformer is a type of electrical transformer constructed with a torus or donut-shaped core. Its primary and secondary windings are wound across the entire surface of the torus core separated by an insulating material...
Electronically operated equipment depends on power transformers to convert electrical currents into voltage. Current transformers store and transport energy through power lines and grids...
Power supplies are electrical circuits and devices that are designed to convert mains power or electricity from any electric source to specific values of voltage and current for the target device...
An AC power supply is a type of power supply used to supply alternating current (AC) power to a load. The power input may be in an AC or DC form. The power supplied from wall outlets (mains supply) and...
An AC power cord is a detachable way of providing an alternating current of electric energy from a mains power supply to an electrical appliance or equipment. Serving industries like...
A DC DC power supply (also known as DC DC Converter) is a kind of DC power supply that uses DC voltage as input instead of AC/DC power supplies that rely on AC mains supply voltage as an input...
A DC power supply is a type of power supply that gives direct current (DC) voltage to power a device. Because DC power supply is commonly used on an engineer‘s or technician‘s bench for a ton of power tests...
An electric coil, or electromagnetic coil, is an electrical conductor that contains a series of conductive wires wrapped around a ferromagnetic core that is cylindrical, toroidal, or disk-like. Electric coils are one of the simplest forms of electronic components and provide...
Electrical plugs, commonly known as power plugs, are devices responsible for supplying and drawing current from a receptacle to the circuitry of an electrical appliance...
By definition a power supply is a device that is designed to supply electric power to an electrical load. An electrical load refers to an electrical device that uses up electric power. Such a device can be anything from...
Inductors are passive two terminal components of an electric or electronic circuit that are capable of storing energy in magnetic form. They oppose sudden changes in current and they are also called coils or chokes...
A NEMA connector is a method for connecting electronic devices to power outlets. They can carry alternating current (AC) or direct current (DC). AC current is the typical current found in homes, offices, stores, or businesses...
A power cord is an electrical component used for connecting appliances to an electrical utility or power supply. It is made from an insulated electrical cable with one or both ends molded with connectors...
A programmable power supply is a method for controlling output voltage using an analog or digitally controlled signal using a keypad or rotary switch from the front panel of the power supply...
A solenoid coil is a common electrical component that uses a wire that is tightly wrapped around a core, usually made of metal, to generate an electromagnetic field. When an electrical current is passed through the coil, the electromagnetic field that is created provides energy for linear motion...
A voice coil is a winding of a wire, usually copper, aluminum, or copper-clad aluminum that is wrapped around a former (often called a bobbin) and then attached to the apex of a speaker cone...
Thomas Edison developed the power distribution system in 1882. He wrapped a copper rod in jute, a soft shiny fiber from plants, as an insulator. The jute wrapped copper rod was placed in a pipe with a bituminous compound...