Electric Transformers
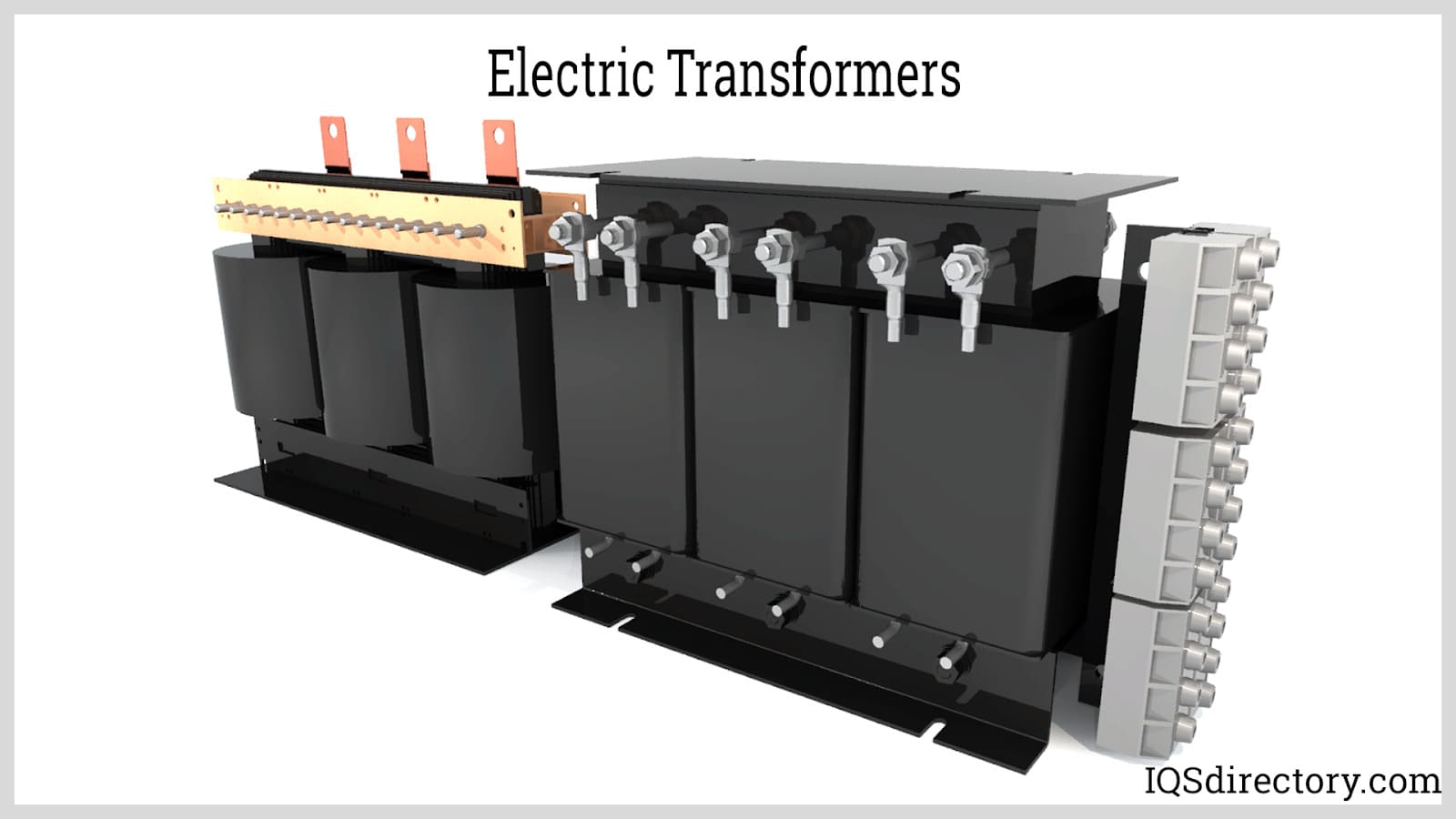
Electric transformers are static electrical machines that transform electric power from one circuit to the other without changing the frequency. An electrical transformer can increase or decrease the voltage with...
Please fill out the following form to submit a Request for Quote to any of the following companies listed on
This article provides a complete guide to the operating principles, configurations, and constructions of a three-phase transformer.
An electrical transformer is a passive component that transfers electrical energy between different circuits using magnetic flux, which induces an electromotive force. It can either boost (step-up) or reduce (step-down) voltage levels, while maintaining the frequency of the electrical current. Moreover, transformers offer electrical isolation between circuits, which is particularly advantageous in signal processing applications.
Electrical transformers operate on the principle of Faraday's law of induction, which describes the connection between changing magnetic flux and induced electric fields. It was found that when a conductor is exposed to a changing magnetic field, an electric current is generated in that conductor. The magnetic field can originate from an electromagnet with a fluctuating current, like an alternating current (AC). The part of the transformer where this happens is known as the primary winding. As the current increases and decreases at a consistent frequency, a corresponding magnetic field also fluctuates, inducing a current in nearby conductors. Typically, this conductor forms the secondary winding. The frequency of this induced electrical current matches that of the primary circuit.
A static magnetic field isn't the only way to create a current. Consider a magnetic field as being made of numerous induction lines. When a conductor traverses these lines, it can generate a current, a principle often utilized in electrical generators.
As previously explained, transformers adjust voltage according to demand. To grasp how three-phase transformers function, it's helpful to first understand the makeup of a single-phase transformer. A single-phase transformer includes two electrical coils known as the primary and secondary winding. The primary winding receives the power supply, whereas the secondary winding is where the electricity is induced.
The two coils in a transformer are not physically connected but are instead linked by a closed-loop magnetic iron core, acting as a conduit for the magnetic field. As this magnetic field courses through the core, which acts as a conductor, it induces electrical currents known as eddy currents, which cause energy losses and heating in the transformer. These effects are mitigated by boosting the core's resistivity with thin sheets or laminations to reduce eddy currents.
The two windings of a transformer are connected via magnetic linkage and are not electrically connected. Adjusting the number of coils in the secondary versus the primary winding allows for altering voltage up or down. As a linear device, a transformer's output voltage can be calculated based on the turns ratio (TR)—the comparison of primary to secondary winding loops. The voltage ratio between the windings is directly related to the turns ratio.
In simple terms, electrical power is determined by multiplying voltage by current. In an ideal transformer, free of losses, power remains constant between primary and secondary windings, ensuring that power out equals power in. Hence, if voltage increases, current decreases and vice versa.
Transformers generally have power efficiency ratings ranging from 88% to 99%. Power losses in transformers fall into categories like iron or core losses, copper losses, stray losses, and dielectric losses. Core losses include hysteresis and eddy currents. Hysteresis losses are due to energy needed to switch the magnetic field's direction, which dissipates as heat. Eddy currents are magnetically induced within the core but do no work. These currents are minimized by adding laminations to the core.
Copper loss occurs from the resistance in copper windings. As current flows through these conductors, it encounters resistance, leading to voltage drops and energy release as heat. To lessen copper loss, increasing conductor size is common, which makes the transformer larger and more costly.
Stray losses result from the leakage of the magnetic field affecting other conductive transformer parts. Even though this field is weaker than that in the iron core, it induces eddy currents in nearby conductive materials, but these currents have minimal impact compared to core-generated ones.
In transformers, dielectric materials insulate between windings, while transformer oil insulates further, prevents arcing, and helps disperse heat. Dielectric loss occurs when insulating substances and transformer oil degrade over time.
Three-phase transformers operate within a three-phase electrical system, unlike the single-phase transformers discussed earlier. Although they share the same working principle, Faraday’s Law of Induction, their wiring configurations differ. To grasp these differences fully, it’s useful to explore three-phase electrical systems in more detail.
Single-phase and three-phase electrical systems utilize alternating current (AC), which continuously varies in amplitude and direction, typically following a sine wave. Other waveforms, like complex, triangular, and square waves, can also be generated. AC signals are defined by three primary properties: period, frequency, and amplitude. The period and frequency describe the wave’s time component, while amplitude indicates the strength or magnitude of the current.
An AC waveform completes a cycle with a peak and a trough, occurring at 90° and 270° within a 360° cycle. In a single-phase electrical system, the current has one peak and one trough, flowing through a single conductor, with the amplitude reaching its maximum in opposite directions. In contrast, a three-phase system features three separate conductors, each with its own peak and trough. These currents are staggered by 120° from one another. Consequently, three-phase systems achieve peak amplitudes more frequently within a given period, providing a more consistent power delivery.
A three-phase transformer includes six windings: three for the primary side and three for the secondary side. Each set of windings can be configured in either a delta or star arrangement. Essentially, these windings function as individual single-phase windings. In principle, a three-phase transformer can be constructed by connecting three single-phase transformers together.
The two primary configurations for three-phase connections are delta and star. The delta connection, also known as mesh connection, involves connecting three windings end-to-end to form a closed loop. The ends are connected to terminals, with no neutral point present. Instead, grounding connections are utilized. Additionally, delta connections can be configured as high-leg systems by grounding the midpoint of one phase. In this setup, the voltage measured across the line opposite the center-tapped phase and ground is higher compared to the voltage measured across the terminals.
The star connection, also referred to as the wye connection, features three windings and four terminals. In this configuration, one end of each winding is connected to a common neutral point, while the other ends create the three phases of the circuit.
Using either delta or star connections comes with its own set of advantages and disadvantages. To fully understand these, it’s essential to distinguish between phase and line voltages and currents. Phase voltage and current are measured across a single component, while line voltage and current are measured between two terminals. Here’s a summary of the relationships between phase and line voltages and currents for delta and star connections:
Delta | Star | |
Voltage | VL = VP | VL = VP x √3 |
Current | IL = IP x √3 | IL = IP |
Where: VL = Line Voltage
VP = Phase Voltage
IL = Line Current
IP = Phase Current
In star connections, the line and phase currents are identical, while the voltages differ by a factor of √3. This setup allows for the supply of different voltages without requiring additional transformers. For instance, a 230V star connection can also provide 400V. The 230V supply is obtained by connecting between a phase terminal and the neutral point, whereas the 400V supply is accessed by connecting between two phase terminals.
In delta connections, the line and phase voltages are identical, but the currents differ by a factor of √3. Specifically, the line current in a delta connection is higher than the phase current. As a result, to handle the increased current, thicker insulation is necessary. Because of this, star connections are generally preferred for power transmission and distribution networks, as they require less insulation material.
One advantage of delta connections is their reliability. If one winding on the primary side fails, the secondary side can continue to supply voltage as long as the remaining two phases can handle the load. This feature allows the system to remain operational even in the event of a partial failure, thereby enhancing overall reliability.
In a three-phase transformer, the primary and secondary sides can have either the same or different configurations. The four possible permutations are: Star-Star (Y-Y),Star-Delta (Y-Δ),Delta-Star (Δ-Y),Delta-Delta (Δ-Δ)
This configuration features star windings on both the primary and secondary sides. In this setup, the line voltages on each side are √3 times the phase voltage. A key advantage of the star-star connection is that it provides access to a neutral terminal on both sides of the transformer, which can be grounded if desired. Grounding the star neutral helps eliminate waveform distortion. However, without grounding, the star-star configuration operates satisfactorily only if the loads on all three phases are balanced.
As the name suggests, this configuration has a star connection on the primary side and a delta connection on the secondary side. The star connection on the primary allows the neutral point to be grounded, which helps prevent distortion. In this setup, the phase voltage on the primary side is equal to the line voltage divided by √3, which is approximately 58% of the line voltage. Consequently, with a 1:1 turns ratio, a star-delta connection reduces the voltage on the secondary side by a factor of 0.58. This makes the star-delta configuration suitable for step-down transformers.
The main disadvantage of the star-delta configuration is that the primary side voltages are measured from line to neutral, while the secondary side voltages are measured from line to line. This results in a phase difference between the primary and secondary sides, making it challenging to parallel star-delta transformers with other types of winding connections.
On the primary side of a delta-star transformer, the line and phase voltages are the same. On the secondary side, however, the line voltage is √3 times the phase voltage. Therefore, with a 1:1 turns ratio, the secondary line voltage is increased by a factor of √3. Delta-star transformers are commonly used for step-up applications. Additionally, they are useful in distribution systems, as the secondary side provides a neutral point that can be used for single-phase power supply in addition to delivering full three-phase power.
Similar to the star-delta configuration, the delta-star setup also results in a phase difference between the primary and secondary sides due to the different winding configurations. This phase shift can complicate the paralleling of delta-star transformers with other types of transformers that have different winding arrangements.
In the delta-delta configuration, the line-to-line voltages on both the primary and secondary sides are equal to the phase voltage. One of the main advantages of this setup is that it maintains equal three-phase voltages even under unbalanced loads. Additionally, since both the primary and secondary sides use the same type of windings, there is no phase shift between them.
The disadvantages of delta-delta connections include the lack of a neutral point on both the primary and secondary sides and the higher cost of the required coils. Transformers with delta connections need to be wound to handle the full line voltage, which makes this configuration more suitable for low voltage applications.
In addition to the four standard permutations, there are other types of three-phase transformers that arise from modifications of the basic star and delta windings. These additional configurations include
The open delta connection, also known as V-V, is created by removing two windings from the primary and secondary sides of a delta-delta transformer circuit. This configuration provides three equal three-phase voltages at the secondary terminals under no load. It is typically used when the three-phase load is too small to justify the installation of a full three-phase transformer. With an open delta transformer bank, the maximum three-phase load that can be supported without exceeding the transformers' ratings is approximately 58% of what a full delta-delta transformer could handle. If the load increases, the open delta can be converted to a delta-delta configuration by adding the missing windings.
This is also known as a T-T connection. This is accomplished by having two transformers, with one transformer having center taps, on both the primary and secondary winding. The main transformer has the center taps while the other transformer has a 0.87 tap known as the teaser transformer. The full rating of the transformer is not being utilized since the teaser transformer only operates at 87% of its rated voltage. The winding is represented by the figure below. This type of connection is done to link a three-phase system with a two-phase system. A common application of this conversion is a power supply on a two-phase system electric furnace.
A high leg delta configuration is achieved by center-tapping one leg of the delta-connected secondary side and grounding this center tap. This setup provides both a three-phase, delta-connected supply and a single-phase supply. It is commonly used in residential and commercial distribution systems, allowing consumers to receive 240V line-to-line for larger equipment and 120V line-to-neutral for lighting and appliances, all without the need for an additional transformer.
High leg delta connection transformers are also known as red leg, wild leg, or orange leg connections. This configuration is commonly used in North America, particularly in the United States. The term "orange leg" refers to the 208V supply, which is typically marked with an orange outer finish.
Normal transformers are loud and lack energy efficiency. Toroidal transformers break with tradition, operate very quietly, and produce minimal heat. The core of a toroidal transformer is shaped like a donut with primary and secondary windings that are separated by insulation, a design that minimizes magnetic leakage that causes noise.
The voltage of a toroidal transformer is stepped up or down based on the magnetic fields interacting with the secondary coil. The output voltage is determined by the number of windings on the secondary coil; for example, doubling the number of windings results in a doubling of the voltage. The primary coil generates a positive magnetic field that facilitates the flow of electrons in either direction.
In a toroidal transformer with an alternating current (AC) signal, the magnetic field first reaches a peak and then decreases to zero voltage, completing the first half-cycle. As the cycle progresses, the magnetic field reverses direction, causing the electrons to flow in the opposite direction through the coil, creating a negative magnetic field. This reversal of the magnetic field brings the voltage back to zero, thereby completing a full cycle.
The noise level of a toroidal transformer is significantly lower than that of other transformers, primarily due to its design. The toroidal core's donut shape allows for very compact windings, which minimizes vibrations. This reduced vibration eliminates the possibility of noise, making toroidal transformers quieter and more secure.
The previous chapter covered the different types of three-phase transformers based on their phase windings. Three-phase transformers can also be classified according to their construction. They can be built using either a single core with combined primary and secondary windings or by connecting three separate single-phase transformers.
In a core-type transformer, the windings are evenly split and wound on the limbs of the core. The core consists of three limbs on the same plane. Each of these limbs contains both the primary and secondary windings. These windings may be better referred to as the high voltage and low voltage windings. The low voltage windings are wound closest to the core since it is easier to insulate. The high voltage coil is then wrapped around the low voltage winding with insulation between them. In this construction, the windings are magnetically coupled with each other, where one winding uses the other two limbs as a return path for its magnetic flux.
The shell-type transformer can be considered as three separate single-phase transformers due to the almost independent magnetic fields of the three phases. This transformer features a core with five limbs. The high voltage and low voltage windings are positioned around the three main limbs, with the low voltage winding closest to the core, similar to the core-type transformer. The two outer limbs provide additional return paths for the magnetic flux. As the magnetic field reaches the yoke, the flux splits into two paths. Consequently, the yoke and outer limbs can be sized to half of the main limbs. This reduction in yoke size helps decrease the overall height of the transformer.
The previous chapter provided a detailed discussion on the windings and cores of three-phase transformers. However, other components are equally important. This chapter will cover these additional parts of a three-phase transformer.
Insulations serve as a barrier system, separating the windings from the core and the two windings from each other. Transformers utilize various types of insulation, including oil, paper, tape, pressboard, and laminated wood.
Insulations act as a barrier system, providing separation between the windings and the core, as well as between the two windings themselves. Transformers use a range of insulation materials, including oil, paper, tape, pressboard, and laminated wood.
The tank safeguards the cores and windings from external environmental factors and also serves as a container for the oil. It is evacuated of air and other substances that could contaminate the oil and affect the dielectric properties of the insulation.
Heating the oil causes it to expand, so a separate vessel, called the conservator, is installed alongside the tank.
As the oil absorbs heat from the transformer, it transfers this heat to the cooling system. The cooling system collects the hot oil, cools it through air- or water-cooled tubes, and then returns it to the windings and core. The designations for transformer cooling systems, as standardized by IEC, are listed below.
Tap changers are used to adjust the output voltage of a transformer. Under load conditions, the transformer's output voltage may drop, necessitating an adjustment of the voltage ratio by modifying the tapping turns. This adjustment is achieved using a tap changer. The type of tap changer used depends on how frequently the output voltage needs to be adjusted.
Also known as the Buchholz relay, this component collects free gas bubbles from the transformer tank. The presence of these gas bubbles can indicate a fault within the transformer.
These devices are used to monitor the oil temperature in the transformer.
These devices are used to remove moisture from the air space above the oil level in the conservator, helping to maintain the dryness of the transformer oil.
These are safety devices designed to relieve overpressure in the event of oil flashing caused by short circuits.
Electric transformers are static electrical machines that transform electric power from one circuit to the other without changing the frequency. An electrical transformer can increase or decrease the voltage with...
An isolation transformer, just like typical transformers, is a non-moving device that transmits electrical energy from one circuit to another without requiring any physical contact. It works on the idea of magnetic...
Power transformers are electrical instruments used in transmitting electrical power from one circuit to another without changing the frequency. They operate by the principle of electromagnetic induction. They are used in transmitting electrical power between...
A toroidal transformer is a type of electrical transformer constructed with a torus or donut-shaped core. Its primary and secondary windings are wound across the entire surface of the torus core separated by an insulating material...
Electronically operated equipment depends on power transformers to convert electrical currents into voltage. Current transformers store and transport energy through power lines and grids...
Power supplies are electrical circuits and devices that are designed to convert mains power or electricity from any electric source to specific values of voltage and current for the target device...
An AC power supply is a type of power supply used to supply alternating current (AC) power to a load. The power input may be in an AC or DC form. The power supplied from wall outlets (mains supply) and...
An AC power cord is a detachable way of providing an alternating current of electric energy from a mains power supply to an electrical appliance or equipment. Serving industries like...
A DC DC power supply (also known as DC DC Converter) is a kind of DC power supply that uses DC voltage as input instead of AC/DC power supplies that rely on AC mains supply voltage as an input...
A DC power supply is a type of power supply that gives direct current (DC) voltage to power a device. Because DC power supply is commonly used on an engineer‘s or technician‘s bench for a ton of power tests...
An electric coil, or electromagnetic coil, is an electrical conductor that contains a series of conductive wires wrapped around a ferromagnetic core that is cylindrical, toroidal, or disk-like. Electric coils are one of the simplest forms of electronic components and provide...
Electrical plugs, commonly known as power plugs, are devices responsible for supplying and drawing current from a receptacle to the circuitry of an electrical appliance...
By definition a power supply is a device that is designed to supply electric power to an electrical load. An electrical load refers to an electrical device that uses up electric power. Such a device can be anything from...
Inductors are passive two terminal components of an electric or electronic circuit that are capable of storing energy in magnetic form. They oppose sudden changes in current and they are also called coils or chokes...
A NEMA connector is a method for connecting electronic devices to power outlets. They can carry alternating current (AC) or direct current (DC). AC current is the typical current found in homes, offices, stores, or businesses...
A power cord is an electrical component used for connecting appliances to an electrical utility or power supply. It is made from an insulated electrical cable with one or both ends molded with connectors...
A programmable power supply is a method for controlling output voltage using an analog or digitally controlled signal using a keypad or rotary switch from the front panel of the power supply...
A solenoid coil is a common electrical component that uses a wire that is tightly wrapped around a core, usually made of metal, to generate an electromagnetic field. When an electrical current is passed through the coil, the electromagnetic field that is created provides energy for linear motion...
A voice coil is a winding of a wire, usually copper, aluminum, or copper-clad aluminum that is wrapped around a former (often called a bobbin) and then attached to the apex of a speaker cone...
Thomas Edison developed the power distribution system in 1882. He wrapped a copper rod in jute, a soft shiny fiber from plants, as an insulator. The jute wrapped copper rod was placed in a pipe with a bituminous compound...