Electric Transformers
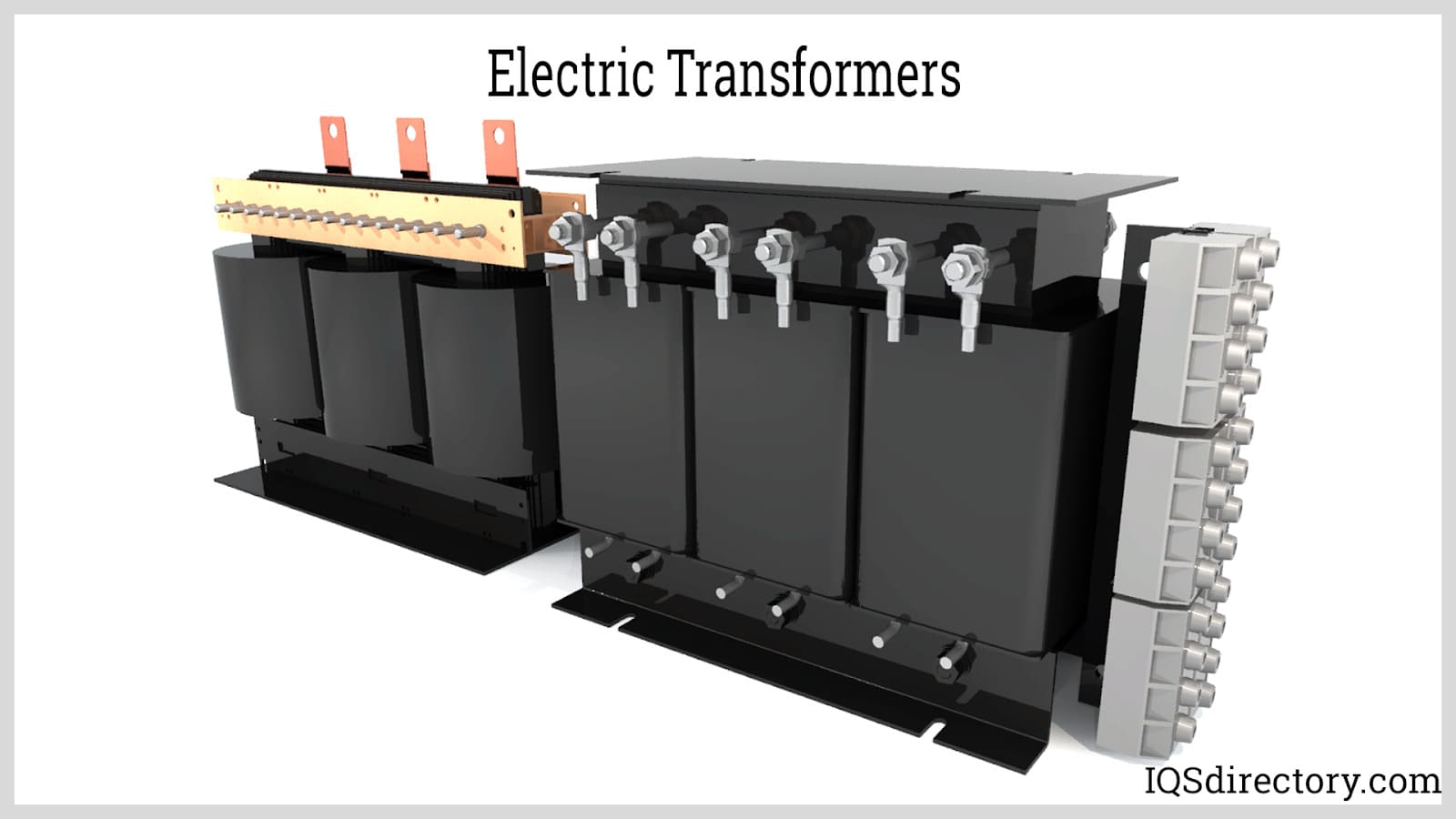
Electric transformers are static electrical machines that transform electric power from one circuit to the other without changing the frequency. An electrical transformer can increase or decrease the voltage with...
Please fill out the following form to submit a Request for Quote to any of the following companies listed on
This article offers an in-depth guide to toroidal transformers.
Read further to find out more.
A toroidal transformer possesses a core in the form of a torus or donut. The primary and secondary windings encircle the entire toroidal core, separated by insulating material. This configuration greatly reduces magnetic flux leakage, establishing the toroidal core as an excellent option for transformer design.
Toroidal transformers are particularly suitable for sensitive and critical electronic applications, attributing advantages that surpass those of conventional square or rectangular transformers. These benefits include high energy efficiency, silent operation, low heat emission, and a compact form. They find widespread use in power supply systems, audio equipment, control systems, power inverters, and an array of electronic devices.
To fully grasp the details of toroidal transformers, it’s important to first understand the fundamental principles of electrical transformers. An electrical transformer is a passive device that transfers electrical energy between circuits through a magnetic field, inducing an electromotive force. This process maintains electrical isolation between the circuits. Transformers are employed to either increase (step-up) or decrease (step-down) voltage levels while keeping the frequency of the electric current unchanged.
Electrical transformers operate based on Faraday‘s law of induction. This physical law states the relationship between the rate of change of a magnetic flux and the induced electromotive force. A magnetic flux is created when magnetic field lines pass through a conductor. It was observed that placing a conductor near a magnetic field with varying amplitude generates an electric current in that conductor.
The magnetic field involved in electromagnetic induction is typically generated by an electromagnet with a varying electric current, known as alternating current (AC). As the electrical current alternates and collapses continuously at a given frequency, the magnetic field similarly fluctuates. This varying magnetic field induces an electric current in a second conductor. The induced current in the second conductor matches the frequency of the original AC current from the electromagnet circuit.
A varying magnetic field is not the only method to induce a current. A magnetic field can be visualized as consisting of numerous lines of induction. By moving a conductor through these magnetic field lines, an electric current can be generated. This principle is exemplified in electrical generators.
The simplest transformer is a single-phase transformer. It has two electrical coils called primary and secondary windings. The primary winding is where the power supply is connected, while the secondary winding is where electricity is induced. These windings are wrapped in a closed-loop magnetic core.
The two windings in a transformer are not electrically connected but are coupled through a magnetic field. The voltage in the secondary winding can be increased or decreased by changing the number of coils relative to the primary winding. As a linear device, a transformer allows the voltage in the secondary winding to be predicted based on the ratio of the number of turns in the windings. This ratio is known as the turns ratio (TR).
In simple terms, power is calculated by multiplying voltage and current. A lossless transformer acts as a constant power device, meaning that the power output in the secondary winding equals the power input in the primary winding. Therefore, to achieve a higher voltage, the current must be reduced, and conversely, to achieve a lower voltage, the current must be increased.
Transformers typically have a power rating efficiency ranging from 88% to 99%. Power losses in transformers are due to several factors, including iron or core losses, copper losses, stray losses, and dielectric losses.
Core losses in transformers arise from hysteresis and eddy currents. Hysteresis loss occurs due to the energy required to reverse the magnetic field direction as it fluctuates, which is dissipated as heat. Eddy currents are generated by the magnetic field from the primary winding within the core but do not contribute to useful work. To minimize eddy currents, laminated cores are used.
Copper loss in transformers results from the electrical resistance of the copper windings. As current flows through these conductors, the inherent resistance causes a voltage drop, leading to energy loss in the form of heat. Reducing this loss typically involves increasing the conductor's cross-sectional area, which would necessitate a larger and more expensive transformer.
Stray loss occurs from the leakage of the magnetic field that affects other conductive parts of the transformer. Although this magnetic field is weaker than the one present in the iron core, it generates eddy currents in the surrounding conductive materials. However, these stray eddy currents have a minimal impact on overall efficiency.
Transformer dielectric materials include the insulation between turns or layers of the windings. In larger transformers, transformer oil is used to insulate, prevent arcing, and dissipate heat. Dielectric loss occurs due to the degradation of these insulating materials and the transformer oil.
Transformer core shapes are generally classified into solenoids and toroids. A solenoid consists of a long, thin conductor coiled into tightly packed loops, with the coils wound helically in a straight direction. Solenoid cores are commonly found in square and rectangular transformers. Examples of solenoid cores include laminated EI and UI cores.
In contrast, a toroid is similar to a solenoid but features a circular profile, resulting in a continuous ring-like structure. Toroid cores are used specifically in toroidal transformers.
An ideal solenoid would be infinitely long with tightly packed coils, where each coil falls into a plane perpendicular to its central axis. In this solenoid, the generated magnetic field of the electric current is concentrated inside the solenoid coil. The intensity of the magnetic field outside the solenoid coil is theoretically zero.
However, in practice, a solenoid always has a finite length. Magnetic field lines form closed loops, which means some of the magnetic flux escapes at the ends of the solenoid to complete the loop. Without a conductive material to contain the magnetic flux, it can pass through other conductors outside the solenoid, leading to energy losses in the transformer.
To contain the magnetic flux in solenoid cores, additional material is used to create a return path. These extra paths, or limbs, are integrated into the solenoid core's design to help manage and direct the magnetic flux effectively, contributing to the core's overall construction.
Similar to an ideal solenoid, an ideal toroid perfectly contains the magnetic flux. The magnetic flux density is concentrated within the coil, with no flux present in the external regions. Achieving an ideal toroid design is more feasible than that of a solenoid, as it does not need to be infinitely long; its loop configuration naturally contains the flux. The key to perfect design is uniformly and tightly winding the coil around the entire toroid. This might be why Faraday, when discovering induction, chose a toroidal core over a solenoid. Additionally, the circular shape of the toroid allows the magnetic flux to easily form a loop without requiring an extra return path.
The previous chapter explored the fundamental differences between solenoid and toroid cores. By examining these concepts further, we can identify the benefits and limitations of each design. Below are the advantages and disadvantages of toroidal transformers compared to other types of transformers.
Transformer efficiency is defined as the ratio of the output power from the secondary windings to the input power supplied to the primary windings. Toroidal transformers are known for their high efficiency, typically ranging from 95% to 99%. This high efficiency is due to their near-ideal design, which effectively contains the magnetic flux within the windings, eliminating leakage flux. The magnetic flux is concentrated within the coil windings and evenly distributed around the entire toroid core, allowing for efficient coupling between the primary and secondary windings.
Toroidal cores effectively contain magnetic flux, naturally shielding nearby components from electromagnetic interference (EMI). This makes them ideal for use in electronic devices with delicate components. In contrast, transformers with solenoid cores are more susceptible to magnetic flux leakage, often requiring extra shielding to mitigate EMI. However, this additional shielding increases both the cost and size of transformers with solenoid cores.
Transformers with low leakage flux offer minimal signal distortion, which is crucial for maintaining signal integrity. Leakage flux, or stray magnetic fields, can induce unwanted currents in nearby conductors, leading to interference with sensitive signals. This issue is particularly noticeable in low-power circuits, where even minor distortions can be significant. As a result, toroidal transformers are commonly used in applications requiring high signal resolution, such as audio systems, medical devices, measuring instruments, and power analyzers.
In single-phase transformers, EI and UI cores are designed with additional material to create a return path for the magnetic flux. EI cores feature three limbs, with only one limb carrying the conductor coil, resulting in less than one-third of the core being used for the coil. In contrast, UI cores have two limbs that both carry the coil, leading to higher core utilization. However, UI cores require a larger yoke compared to EI cores. It’s important to note that in both core types, the yokes do not carry the conductor coils.
Toroidal cores address these issues by utilizing the entire core for the magnetic flux path. Unlike EI and UI cores, which require additional material for return paths and have limitations in core utilization, toroidal cores are inherently looped, eliminating the need for extra return paths. This efficient design enables toroidal transformers to be more compact while providing the same or better performance compared to similarly rated EI and UI-cored transformers.
This advantage stems from the use of a smaller core construction, which in turn reduces the amount of material required. Transformer cores are typically made from silicon steel, but for specialized applications, more costly materials with superior properties are used. These materials are chosen for their high permeability, low hysteresis, and minimal eddy current loss. Examples include permalloys, cobalt-based amorphous alloys, and nanocrystalline materials, each offering enhanced performance for specific applications.
Off-load losses in transformers occur due to the power consumed by magnetizing the core even when no load is connected to the secondary circuit. Transformers continue to draw power in standby mode. Toroidal transformers, thanks to their efficient design, exhibit lower core losses compared to conventional solenoid-core transformers. As a result, toroidal transformers experience fewer off-load losses, making them more efficient in standby conditions.
Toroidal cores are designed with a continuous, uninterrupted construction, eliminating the air gaps commonly found in solenoid cores. Air gaps can lead to several negative effects, including magnetic flux spreading (fringing) and increased noise. In contrast, solenoid cores like the EI core have multiple air gaps—typically three—that allow magnetic flux to leak and interfere with adjacent components. The absence of air gaps in toroidal cores helps reduce these issues, resulting in more efficient magnetic flux containment and less interference.
Transformer noise primarily stems from mechanical humming caused by vibrations within the core material. These vibrations result from a phenomenon known as magnetostriction, where the dimensions of the core material change in response to magnetization. As the core material vibrates, it can impact adjacent core parts, leading to the audible noise commonly associated with transformers.
Mechanical humming is more pronounced in transformer cores with loose components. EI and UI cores, which are often made with laminated iron, can experience looseness over time, leading to vibrations and noise. Additionally, their non-continuous structure includes air gaps between limbs and yokes, which can exacerbate vibration and noise when these components impact each other.In contrast, toroidal transformers avoid these issues due to their continuous core structure. Most toroidal cores are not laminated and do not have air gaps, resulting in a more stable and quieter operation. This continuous design helps minimize vibrations and mechanical humming, making toroidal transformers inherently quieter than their EI and UI counterparts.
This is another effect of having higher efficiency. Electrical energy losses in a transformer are eventually converted into vibrations and heat. Heat is generated mostly from eddy currents, hysteresis, and copper resistance. For larger transformers, an oil cooling system is used for dissipating heat. For transformers in small electronic devices, a metal heat sink is typically used. Because of the toroidal transformer‘s high efficiency, they generate less heat and can function even without cooling systems or heat sinks.
Despite their smaller profiles and reduced material usage, toroidal transformers are more costly to produce than other types. This higher cost arises from the complexity of winding conductor coils around the toroidal core, a process that requires winding each coil individually and takes more time. In contrast, EI and UI transformers are typically assembled from disassembled E and I pieces, allowing for easier access to the limbs where coils are wound. This design facilitates mass production and contributes to lower manufacturing costs for EI and UI transformers.
Toroidal transformers are predominantly used for single-phase applications. While three-phase toroidal transformers are available on the market, they are less common compared to single-phase models. The primary reasons for this include the complexity and cost associated with winding three-phase coils around a toroidal core, as well as the challenges in maintaining the same level of efficiency and compactness in three-phase designs. Consequently, three-phase transformers with other core types, such as EI or UI cores, remain more popular in industrial and commercial applications.conventional core and shell-type transformers. Three-phase toroidal transformers are only used in special applications.
TThree-phase toroidal transformers typically use three individual toroidal cores, significantly increasing the cost due to the additional material and complexity. In contrast, core and shell-type transformers streamline the design by allowing coils to be wound on adjacent limbs. Core-type transformers have three limbs, while shell-type transformers have five limbs, all sharing a common top and bottom yoke. This configuration greatly reduces the overall profile compared to using three separate single-phase transformers, making core and shell-type transformers more cost-effective and compact for three-phase applications.
Inrush current refers to the surge of current that occurs when a transformer is first energized. This spike happens because the primary circuit draws a large initial current when the transformer is connected to a load on the secondary circuit. Highly efficient transformers, like toroidal transformers, can exhibit a higher magnitude of inrush current due to their design. Their efficient core construction and reduced losses lead to a more significant initial current surge when the transformer is powered up.
With toroidal transformers, managing inrush current is crucial as it can lead to significant issues if not properly addressed. High inrush currents can trip circuit breakers, blow fuses, and in severe cases, result in complete transformer failure. The magnitude of the inrush current impacts how many devices can be safely connected to the power source. Proper management and protection measures are essential to prevent these problems and ensure reliable operation of the transformer and connected devices.
To protect against the effects of inrush current, both active and passive devices can be employed. The choice of protection depends on factors such as the frequency of the inrush current, performance requirements, cost, and reliability.Passive inrush current limiters often utilize components like NTC (Negative Temperature Coefficient) thermistors. These thermistors act as electrical resistors with high resistance when cold, which helps limit the initial surge of current. As the thermistor heats up due to the inrush current, its resistance decreases, allowing normal current flow while protecting the transformer and associated circuitry from damage.
Active devices, while effective in managing inrush current, are typically more expensive and can increase the overall size of the system. These devices are highly sensitive and operate by switching the high incoming current to limit its magnitude. They provide protection to both electrical and mechanical systems by controlling and reducing the inrush current, thereby preventing potential damage and ensuring system reliability.
A transformer core is constructed from magnetic materials, which vary in terms of magnetic permeability, electrical resistivity, hysteresis, and other properties. The efficiency of the transformer is significantly influenced by these material qualities, as the core is responsible for the majority of transformer losses. Below are some common types of core materials used in toroidal transformers:
Ferrite Cores: Ferrite cores are made from a metal-oxide ceramic, iron oxide, mixed with other metals such as cobalt, copper, nickel, manganese, and zinc. The two common types of ferrite cores are manganese-zinc ferrite and nickel-zinc ferrite cores. Compared to other types, ferrite cores have relatively low permeability, low saturation flux density, and low Curie temperature. Their biggest advantage is their high electrical resistivity, which helps reduce the generation of eddy currents.
Laminated Iron Alloy Cores: Laminated iron alloy cores are used in conventional transformers that operate at low to medium frequencies. They are made by rolling metal into flat sheets, which are stamped into the required shape of the core. The stamped and shaped sheets are placed in stacks, glued together, and compacted into a single solid piece. The layers of the compressed sheets are separated by insulation positioned between each of the sheets.
Laminated iron alloy cores are used in conventional transformers that operate at low to medium frequencies. They are made by rolling metal into flat sheets, which are stamped into the required shape of the core. The stamped and shaped sheets are placed in stacks, glued together, and compacted into a single solid piece. The layers of the compressed sheets are separated by insulation positioned between each of the sheets.
The lamination of laminated iron alloy cores reduces eddy currents, which are trapped in the thickness of each lamination. Silicon iron and nickel iron are two of the most used materials for manufacturing laminated cores.
Tape Wound Cores - In principle, tape wound cores are the same as laminated cores. They are more commonly used for making toroidal transformers than laminated cores. Instead of stacking ring-shaped laminations, tape wound cores are made from insulated metal ribbons wound into a spiral. It is then encapsulated by a thin sheet made from aluminum, or plastic.
The manufacturing process for tape wound cores is designed to produce transformer cores with the lowest loss and magnetizing currents. Modern methodology and technical advancements have eliminated the air gap at the face of tape wound cores, providing cores with very little hum and low exciting current.
Tape wound cores are used where thousands of transformers are needed, and weight and dimensions must be reduced. They are the most common core used for manufacturing toroidal transformers and are preferred over laminated cores due to their size.
Aside from specifying the type of transformer and core material, several other specifications are crucial for completing the design. The following are key transformer specifications typically included in the product datasheet:
Number of Primary and Secondary Windings: A simple toroidal transformer has only one primary and one secondary winding. More windings can be addede for better flexibility. A usual design, there is one primary and two secondary windings. These designs have six lead wires. The secondary windings are used independently and can be configured to be in parallel or series.
Electric transformers are static electrical machines that transform electric power from one circuit to the other without changing the frequency. An electrical transformer can increase or decrease the voltage with...
An isolation transformer, just like typical transformers, is a non-moving device that transmits electrical energy from one circuit to another without requiring any physical contact. It works on the idea of magnetic...
Power transformers are electrical instruments used in transmitting electrical power from one circuit to another without changing the frequency. They operate by the principle of electromagnetic induction. They are used in transmitting electrical power between...
An electrical transformer is a passive machine that transfers electrical energy from one circuit to another using a magnetic flux to induce an electromotive force. Transformers are used to increase (step-up) or decrease (step-down) voltages without changing the frequency of the electric current...
Electronically operated equipment depends on power transformers to convert electrical currents into voltage. Current transformers store and transport energy through power lines and grids...
Power supplies are electrical circuits and devices that are designed to convert mains power or electricity from any electric source to specific values of voltage and current for the target device...
An AC power supply is a type of power supply used to supply alternating current (AC) power to a load. The power input may be in an AC or DC form. The power supplied from wall outlets (mains supply) and...
An AC power cord is a detachable way of providing an alternating current of electric energy from a mains power supply to an electrical appliance or equipment. Serving industries like...
A DC DC power supply (also known as DC DC Converter) is a kind of DC power supply that uses DC voltage as input instead of AC/DC power supplies that rely on AC mains supply voltage as an input...
A DC power supply is a type of power supply that gives direct current (DC) voltage to power a device. Because DC power supply is commonly used on an engineer‘s or technician‘s bench for a ton of power tests...
An electric coil, or electromagnetic coil, is an electrical conductor that contains a series of conductive wires wrapped around a ferromagnetic core that is cylindrical, toroidal, or disk-like. Electric coils are one of the simplest forms of electronic components and provide...
Electrical plugs, commonly known as power plugs, are devices responsible for supplying and drawing current from a receptacle to the circuitry of an electrical appliance...
By definition a power supply is a device that is designed to supply electric power to an electrical load. An electrical load refers to an electrical device that uses up electric power. Such a device can be anything from...
Inductors are passive two terminal components of an electric or electronic circuit that are capable of storing energy in magnetic form. They oppose sudden changes in current and they are also called coils or chokes...
A NEMA connector is a method for connecting electronic devices to power outlets. They can carry alternating current (AC) or direct current (DC). AC current is the typical current found in homes, offices, stores, or businesses...
A power cord is an electrical component used for connecting appliances to an electrical utility or power supply. It is made from an insulated electrical cable with one or both ends molded with connectors...
A programmable power supply is a method for controlling output voltage using an analog or digitally controlled signal using a keypad or rotary switch from the front panel of the power supply...
A solenoid coil is a common electrical component that uses a wire that is tightly wrapped around a core, usually made of metal, to generate an electromagnetic field. When an electrical current is passed through the coil, the electromagnetic field that is created provides energy for linear motion...
A voice coil is a winding of a wire, usually copper, aluminum, or copper-clad aluminum that is wrapped around a former (often called a bobbin) and then attached to the apex of a speaker cone...
Thomas Edison developed the power distribution system in 1882. He wrapped a copper rod in jute, a soft shiny fiber from plants, as an insulator. The jute wrapped copper rod was placed in a pipe with a bituminous compound...