Electric Transformers
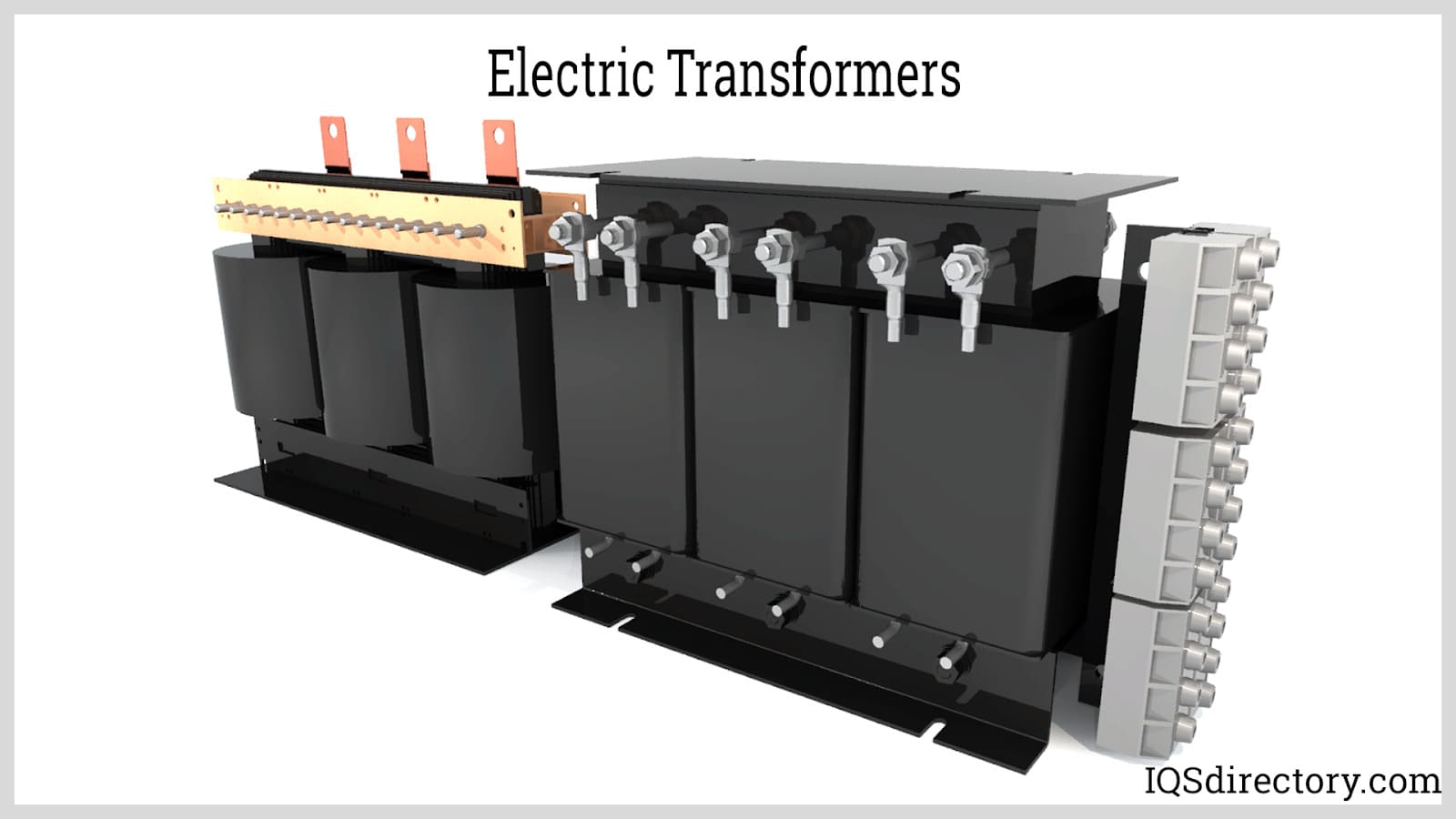
Electric transformers are static electrical machines that transform electric power from one circuit to the other without changing the frequency. An electrical transformer can increase or decrease the voltage with...
Please fill out the following form to submit a Request for Quote to any of the following companies listed on
This Article takes an In-depth look at Electric Transformers
You will learn more about topics such as:
Electronic devices rely on power transformers to change electrical currents into the necessary voltage. These transformers help in storing and distributing energy through electrical grids and power lines. Electric transformers utilize electromagnetic coupling to transmit electrical energy between circuits. Their primary function is to adjust voltage levels, either increasing or decreasing, to meet a device’s needs.
Manufacturers create electric transformers with a broad array of electrical applications in mind. These transformers come in various sizes, from small units used in electronics like lamps and microphones to large, stationary systems used in power stations.
Low voltage transformers are designed to modify currents to suit small electronics and dimmer switches, whereas high voltage transformers manage electricity transmission between power plants and end-user locations.
Most transformers are isolation transformers, designed to transfer power through induction within a single phase. Alternatively, three-phase transformers process electricity across three phases, ensuring equal voltage in each phase, offset by specific degrees.
One of the key benefits of electric transformers is their ability to improve safety for both users and devices. Proper voltage levels are essential because incorrect voltage can cause several problems. A voltage that is too high might damage equipment or lead to failures, and in severe instances, it might result in fires or electric shocks. Conversely, voltage that's too low can impair device functionality. Transformers align voltage distribution to the specifications of connected equipment.
Electric transformers consist of two sets of coils, or windings, linked by a magnetic core composed of iron, a ferrite compound, or laminated and wound with copper or enamel. In an electrical motor, AC voltage passes through a primary coil, creating a magnetic field that envelops the conductor. This magnetic field activates a secondary coil. The transformer modifies the magnetic field's voltage and transfers electrical energy.
A critical component in electricity generation is the coil windings, influencing the voltage transfer from the primary to the secondary conductor. Voltage is dictated by the ratio of turns in the primary coil to those in the secondary. For step-down transformers, the secondary coil has fewer turns than the primary, while step-up transformers have more turns in the secondary coil.
Following voltage conversion, the power is transmitted to the load center, continuing the electrical cycle. The size and cost of electric transformers depend on the number of primary windings.
The concept of the transformer owes its existence to the work of Michael Faraday who hypothesized that if magnetism is produced by electricity then electricity can be produced by magnetism. It is that conceptualization that stands at the center of how a transformer works.
Transformers use the properties of electricity to change the voltage of electricity. Electric circuits have magnetism. Whenever the magnetism changes, by moving or alteration of its strength, voltage, the measure of electric force or power, is produced. If an electric wire is close, when the change occurs, electricity will flow into the wire.
A transformer takes in electricity at high voltage and runs it through coils that are wound around a core. The current is alternating making the magnetism alternate. The core has an output wire wrapped around it with fewer coils. The fluctuating magnetism produces current in the wire.
Electricity must be transmitted at extremely high voltages, ranging from 155,000 to 770,000 volts, to efficiently cover long distances from a power plant. Upon reaching the destination, the voltage needs to be reduced, or stepped down, for practical use. Power distribution networks include substations that decrease these high voltages into more manageable levels.
Locally, another transformer changes the voltage from the substation from 7200 volts to the normal 220 or 240 to be used for air conditioners, heaters, and appliances. For other items such as toys, computers, and televisions, the voltage is stepped down further to 110 or 120.
To reduce voltage, the primary winding must have more turns than the secondary winding. Conversely, to increase voltage, the secondary winding needs more turns than the primary winding. It is rare for the primary and secondary windings to have an equal number of turns, as this would result in no change in voltage.
All transformers experience some energy loss, typically dissipated as heat. If this heat is not properly managed, it can damage the insulation on the wiring. Given that transformers are stationary devices, effectively cooling them can be quite challenging.
Cooling of a transformer comes in two forms – air and oil. The dry or air form of cooling uses circulating ambient air to carry away the heat or, when circulating air is not enough, air blasts are used to force air on the coils and keep the temperature down. An oil cooling system immerses the transformer in circulating water or oil.
As demonstrated, the main function of a transformer is to adjust voltage levels, either increasing or decreasing them, to suit specific applications. This capability has enabled the efficient transmission of electricity over long distances while ensuring safety in electrical usage.
A factor that can reduce the efficiency of an electric transformer is eddy currents, also known as Foucault currents. These are loops of electrical current generated within a conductor due to fluctuations in the magnetic field. Eddy currents circulate in closed loops perpendicular to the magnetic field and result in heat generation.
During the manufacturing of electric transformers, producers utilize specific core materials and techniques to minimize the impact of eddy currents. The presence of eddy currents in a transformer generates heat, resulting in energy loss and reduced efficiency. To combat this, manufacturers select core materials with low electrical conductivity and high resistivity to effectively reduce the formation of eddy currents.
Transformers operate based on Faraday's law, with different types tailored for specific applications. As new technologies and devices emerge, specialized transformers are developed to regulate and manage the current and voltage requirements of these new innovations.
An iron core transformer consists of multiple iron plates stacked together, providing excellent magnetic properties and making these transformers highly efficient. The plates are typically made from silicon steel and coated with an insulating paint. This design allows for rapid magnetization and demagnetization, making iron core transformers an ideal choice for many applications.
Iron core transformers are highly effective due to their rapid magnetization and demagnetization. Their exceptional magnetic properties result in a high magnetic flux linkage, contributing to their outstanding efficiency.
Iron core transformers come in various configurations, including E, I, L, and U shapes, often combining these types in practice. Metal sheets are utilized for the cores because solid iron cores can produce inefficient eddy currents. These transformers are commonly employed in devices such as computers, televisions, radios, and amplifiers.
Iron core transformers are widely used because of their high inductive electromagnetic flux and their capability to transfer flux up to fifteen hundred times more efficiently than air core transformers. Their advantages include effective power transfer, minimal magnetic flux loss, and the ability to handle large loads at both low frequencies and high voltages.
The role of isolation transformers is to transmit electrical power to a device from a power source. Technically, all transformers can be defined as an isolation transformer, due to the fact that all transformers use the process of induction to convert electricity, as opposed to the use of a conductor. The main characteristic that sets isolation transformers apart from other categories of transformers is their ability to isolate electricity or isolate a transformer from a power source. Numerous applications use isolation transformers. These applications include uninterrupted power supplies (UPS), test and measurement systems, robotics, motor controls, light fixtures, medical electronics, industrial control panels, data communications, avionics, and audio systems.
An isolation transformer separates the primary and secondary windings, ensuring that the circuits remain electrically isolated from one another. It transfers electrical energy between circuits through magnetic induction, creating an electromagnetic field without altering the frequency. By isolating power line ground connections, isolation transformers help prevent ground loops and reduce high-frequency noise interference.
Isolation transformers create a barrier between AC main power lines and the connected equipment, effectively eliminating a direct DC path between the windings. They isolate the secondary side from the ground, can either step up or step down main line voltages, and help reduce line noise.
Ferrite core transformers, known for their magnetic permeability, effectively manage energy loss in high-frequency applications. These transformers can be molded into various shapes and are often configured with an E-type core. The windings for ferrite cores are composed of non-conductive, ceramic ferromagnetic materials, including iron oxides mixed with nickel, zinc, and manganese, which exhibit low coercivity and are classified as soft ferrites.
The ceramic material used in ferrite cores acts as an insulator. Ferrite cores are designed to withstand high currents and minimize eddy current losses across a wide range of frequencies. Their high magnetic permeability, combined with low electrical conductivity, effectively suppresses the formation of eddy currents.
Ferrite cores come in four main types: manganese zinc (MnZn), nickel zinc (NiZn), sand dust, and lamination. Manganese zinc ferrite cores are known for their high saturation levels and magnetic permeability. They are suitable for applications with operating frequencies below 5 MHz and are particularly effective for inductors operating above 70 MHz.
Nickel zinc ferrite core transformers offer high resistivity and are ideal for applications operating in frequency ranges from 2 MHz to several hundred MHz. They are particularly effective for inductors used above 70 MHz. Sand dust cores are high-frequency choke coils designed specifically for use with ferrite cores. Lamination transformers, on the other hand, are commonly used in applications such as inverters, welding equipme
Audio output transformers convert input electromagnetic signals into output signals through inductive coupling. This process isolates the input circuit from the output circuit and filters the signals. They are used in various applications, including the input stage of audio equipment, microphones, output stages, loudspeakers, and for coupling and impedance matching in amplifiers. Similar to other transformers, audio output transformers feature primary and secondary windings made of copper wire wrapped around cores made of steel or nickel-iron alloys.
The cores of audio output transformers influence how electromagnetic signals are transmitted. Steel cores, with their higher hysteresis, are more suitable for lower frequencies. In contrast, nickel-iron alloy cores are ideal for high-frequency transmission due to their superior permeability. The windings around the core play a crucial role in determining impedance levels, affecting whether the signal is increased, decreased, or maintained.
Audio output transformers leverage their isolation feature to separate the output or audio circuitry from the input amplifier side. The ratio between the primary and secondary windings can be 1:1, meaning the transformer may not alter the voltage or current levels. For loudspeakers requiring substantial loads, an audio output transformer steps up the load to generate the appropriate speaker vibrations.
Audio transformers play a crucial role in matching the impedance between connected circuits or devices. This is particularly important for speakers and microphones, as impedance matching ensures that the impedance is adjusted to a level suitable for the connected device, optimizing performance and signal transfer.
Step up transformers are commonly used in applications such as power transforming and modification, due to their ability to convert lower voltages to higher voltages while reducing amperage and the effects of resistance in the process. The voltage conversion entails electrical energy traveling through two phases of coils, with the second coil phase having a greater amount of winding, defined as a complete coil assembly. Some applications require only a single coil winding, and others even require a tertiary set of windings. However, electric transformers require two to complete the conversion process. These two sets of coil windings feature a core being made from either a ferrite compound or a laminated core wound with enameled coils or uncovered copper. The coil windings of step up transformers are typically constructed from aluminum, nickel, chromium, steel alloys, and copper, the latter of which is the most expensive yet is the most energy efficient.
High voltage transformers are tools used to change the voltage of power lines in high voltage contexts. A volt is the unit of measurement for electromotive force, and the voltage of a power transmission line is the measurement of power transmission capacity in a transmission line.High voltage transformers are built to handle elevated amounts of electrical energy in the range of 600 to 5,000 volts, although custom voltage transformers are available as well. A type of instrument transformer, high voltage transformers are often used for metering and protection in high-voltage circuits and in electrostatic industrial and scientific applications.
High voltage transformers can be configured with single-phase or three-phase primaries. Single-phase primary transformer configurations include single, dual, quad, five-lead, and ladder types. Five-lead configurations use more copper in their construction, whereas ladder-type transformers are the most expensive and costly to produce.
Three-phase high voltage transformers are configured in delta and wye (or star) arrangements. In the wye-delta configuration, the primary winding is arranged in a wye (Y) shape, while the secondary winding is configured in a delta (triangle) shape. Conversely, in the delta-wye configuration, the primary winding is set up in a delta shape, and the secondary winding takes the wye form.
The donut shape of the toroidal core transformer prevents induction leakage creating high inductance. Windings are short, and the transformer weighs less than others with the same rating. They are expensive because of the slow winding process.
Toroidal cores are well-suited for sensitive and critical electronic circuits because of their high efficiency, silent operation, low heat generation, and compact design. They are commonly utilized in audio systems, control equipment, and power converters.
The efficiency of a transformer is defined as the ratio of the output power from the secondary winding to the input power supplied to the primary winding. Toroidal core transformers typically achieve an efficiency rating between 95% and 99% due to the optimal design of the toroidal core. The magnetic flux in a toroidal transformer is concentrated within the coil windings and is evenly distributed, ensuring effective coupling between the primary and secondary windings. Additionally, toroidal cores provide excellent shielding against electromagnetic interference (EMI), making them ideal for use with sensitive electronic equipment.
A key advantage of toroidal transformers is their ability to shield adjacent electronic components from electromagnetic interference (EMI), thanks to their donut-shaped design. The magnetic flux is contained within the transformer, minimizing interference with sensitive components. In contrast, solenoid cores can leak magnetic flux and typically require additional shielding to prevent such interference.
Air or antenna coil transformers do not have a magnetic coil as a core and are wound around plastic tubing or cardboard. They generate flux using coil windings that have air passing through the windings. The flux linkage is between two magnetically linked coils or windings, which are the primary and secondary windings.
Air core transformers offer several advantages, including noise-free operation, absence of hysteresis and eddy current losses, and a lightweight design. They come in two primary forms: cylindrical and toroidal. In cylindrical air core transformers, copper wire is wound around a cylindrical form, with the primary coil wound using tape and taps added to the secondary coil windings. These taps allow magnetic flux to flow through the hollow cylinder and surround the winding. For toroidal air core transformers, copper wire is wound around a cardboard or plastic donut shape. The separate coil windings help reduce stray couplings. The ratio of primary to secondary windings varies based on the operational requirements and frequency changes.
In high-frequency applications, avoiding electromagnetic interference (EMI) is crucial as it can significantly impact the output signal. Since ferromagnetic materials can introduce noise and distortions, air core transformers are preferred in situations where the flux is coupled through air. Their efficient design ensures that air core transformers remain noise-free and lightweight, making them ideal for use in compact, handheld electronic devices.
Laminated transformers feature cores constructed from punched sheets of iron and nickel that are laminated together. The addition of nickel helps to minimize energy loss when the winding is energized. A key advantage of laminated core transformers is their ability to reduce eddy currents, thereby enhancing the efficient transfer of energy from the primary coil to the secondary coil.
E-I laminated cores are commonly used in isolation transformers for both step-up and step-down applications. These cores can be cylindrical, rectangular, or oval in shape, with the laminated metal strips arranged in configurations such as E, L, U, or I. Similar to iron cores, laminated cores often combine these configurations, such as pairing E and I shapes to create an E-I core.
As current passes through a transformer's windings, small circulating currents known as eddy currents can be induced in the core. Reducing these eddy currents improves the core's performance. The lamination in laminated cores helps to disrupt the formation of eddy currents, thereby enhancing the overall efficiency of the transformer.
Laminating the core of a transformer significantly minimizes eddy current flow, which in turn reduces heat loss. Eddy currents in iron cores can cause heat buildup and decrease electrical efficiency. In severe cases, excessive heat can lead to core damage or even breakage. By reducing heat production, laminated transformer cores enhance overall core performance.
Pulse transformers operate in a direct current (DC) mode, meaning that the flux density may meet but does not cross zero. A common application for pulse transformers is the coupling of a load resistance to a source of pulsed power. An example of this application would be radar transmitters, which typically employ an output power tube like a magnetron that requires high voltages and high impedance, or electric resistance, levels. Small versions of pulse transformers create the electrical surges that are often used in telecommunication and detail logic applications such as camera flashes, radar equipment and particle acceleration. Medium-sized versions of pulse transformers are used in electronic circuit applications.
Current transformers (CTs) are tools that are used to measure the current, or flow of electricity, in electrical transmission lines. Understanding a current transformer requires an understanding of electrical current, which is measured in amperes with one ampere being equal to the movement of 6.241 × 1018 electrons passed a given point per second. While power transformers control voltage, current transformers measure and control movement for measuring purposes and to help control the flow of electricity to electronic devices.
The primary winding of a current transformer typically consists of just a few turns, which may be a single flat turn of heavy-duty wire wrapped around the core or a bus bar passing through the central opening. Current transformers are designed to reduce high current to a lower, measurable value, enabling the use of a standard ammeter to monitor current in an AC circuit. These transformers are often referred to as series transformers because their primary windings are connected in series with the current-carrying conductor supplying the load.
In contrast to the primary winding of a current transformer, the secondary windings typically consist of multiple turns wound around a laminated core made of low-loss magnetic material. The core's cross-sectional area is designed to ensure low magnetic flux density. The secondary winding provides current to a connected device, such as an ammeter or a resistive load, effectively creating a short circuit in the secondary circuit.
Low voltage transformers are power transformers that are used to change the voltage capacity of a low-voltage electrical transmission line. Typically, electronic low voltage transformers convert 120 volts into 12 volts or 24 volts. Unlike high voltage transformers, which in the most extreme cases can weigh several hundred pounds, low voltage transformers can be small enough to hold between two fingers.
In the United States, the standard supply voltage is 120 volts, which can pose safety risks. A low voltage transformer is used to reduce this input voltage to a much lower level, making it safer for operating equipment, installing light bulbs, and performing other tasks while maintaining electrical safety.
In a low voltage transformer, the secondary winding has significantly fewer turns compared to the primary winding. Both windings are wound around a magnetic iron core, but they do not come into direct contact with each other. The core is constructed from soft magnetic materials with laminated layers that are interconnected to minimize energy loss, which is caused by alternating magnetic flux within the core.
When the primary winding is connected to the power supply, current flows through it, creating an induced magnetic field. This magnetic field partially links to the secondary winding, inducing a current and voltage on the secondary side. The voltage and current in the secondary winding are proportional to the number of turns in the secondary winding compared to the primary winding.
Automatic or autotransformers have one winding that acts as the primary and secondary that are magnetically and electrically connected with three taps for electrical connections. They are smaller, lighter, and less expensive and are used where electrical systems have different voltages. Auto transformers consist of a single winding and an input and output circuit. The voltage source and the load are connected to two of the taps. One tap at the end of the winding serves as a common connection to the source and the load circuits.
A distinctive feature of autotransformers is the electrical connection between the primary and secondary windings, setting them apart from other types of transformers. In an autotransformer, the winding connected to the source is the primary winding, while the winding in parallel with the load is referred to as the secondary or common winding. As both a step-up and step-down transformer, an autotransformer follows the same principles as other transformers, with the key difference being that the voltage across the load can be either higher or lower than the source voltage, depending on the configuration.
Autotransformers function similarly to other types of transformers, with the primary current inducing a varying current in the secondary winding based on the turns ratio between the windings. The secondary winding is tapped at various points along its length, allowing for adjustable output at different steps and percentages.
To meet the demand for three-phase power supplies, it is possible to use three separate single-phase transformers. However, a more efficient solution is to utilize a single transformer that integrates all three phases, with interconnected magnetic circuits and a core designed to handle three or more phases of flux. This type of transformer is known as a polyphase transformer, which features multiple sets of primary and secondary windings on a single core. The presence of these multiple windings enables a polyphase transformer to support three or more conductors, accommodating configurations with up to 15 phases.
In a polyphase transformer, phases are separated by phase breaks or short circuits, which enhance power distribution efficiency and allow each phase to operate at different speeds. This separation also significantly reduces heat transfer between the on-off phase and the high voltage phase. The on-off phase, being hotter due to its smaller size, is less likely to transfer excess heat to the high voltage phase, thereby improving overall thermal management within the system.
In a polyphase transformer, the primary and secondary windings can be connected using either wye (star) or delta configurations, or a combination of the two. This can be wye-delta or delta-wye. Both connection types are effective as long as no neutral wires are involved.
A zig zag transformers has six coils on three cores with the first coil of each core connected in the opposite way to the second coil on the next core. The second coils are tied together to form the neutral with the phases connected to the primary coil. In the process, each phase couples with the other phase and voltage is canceled.
Interconnected star or zigzag transformers serve as grounding transformers and do not feature secondary windings. Instead, their winding connections facilitate current flow through the neutral phase. The zigzag configuration is a cost-effective design with an iron core that helps to minimize harmonic flux flow.
In a zigzag transformer, each phase winding is split into two halves. The distinct winding patterns arise from how these two halves are interconnected, influencing the connections between the coils and the core. Zigzag configurations exhibit high magnetizing resistance to both positive and negative sequence currents while offering lower leakage resistance to triple harmonics and zero sequence currents.
Zig zag transformers are used to define a reference point for ungrounded systems. Due to their ability to provide a neutral point for grounding purposes, numerous industries utilize zig zag transformers, including industrial, electronics, petrochemical, power distribution, automotive and hardware.
A three phase transformer falls into the realm of the polyphase variety. Though it is possible to connect three single phase transformers to make a three phase one, it is more economical and efficient to have all three phases compacted into one. They have three sets of primary and secondary windings, which can be star or delta configurations. Configurations can be delta-delta, star-star, or other combinations.
To effectively manage a three-phase electricity transmission system, three-phase transformers are crucial. They transform and direct electrical current from power lines into homes and businesses. Current transformers regulate the current flowing from electrical utility lines into the systems that utilize it. Power transformers are essential for the safe and efficient operation of both electrical systems and individual appliances.
Power transformers transmit electrical power from one circuit to another without changing the frequency. They use electromagnetic induction to transmit electrical power from generators and distribution primary circuits. Power transformers step up or step down voltage in distribution networks without the use of moving parts, a factor that gives them a static device status.
A Power transformer is large, sends energy to substations, and acts as a connection between generators and the grid. The three classes of power transformers are small, medium, and large with ratings from 30KVA to 700KVA. Due to their size, power transformers require a cooling agent and are normally submersed in oil. They use a three phase system, which is costly but more efficient than single phased systems with smaller versions of power transformers being single phased.
Power transformer windings are typically made from copper or aluminum coils, with copper being favored for its excellent conductivity and ductility. Laminated cores, constructed from iron or steel sheets, are employed to minimize eddy current and hysteresis losses. Tap changers are attached to the high-voltage winding to allow for precise voltage adjustments and to reduce core losses. Additionally, the current in the high-voltage winding is kept lower to mitigate the risk of sparking, which could potentially ignite the transformer’s cooling oil.
Current transformers (CT) and voltage transformers (VT) are used for measurement purposes. CTs reduce high current signals to lower levels that can be accurately measured with an ammeter. VTs, on the other hand, step down high voltage values to safer, lower levels, typically 100 volts or less, suitable for measurement instruments. Both types of transformers feature magnetic circuits in their primary and secondary windings and are essential for ensuring the accuracy and safety of power systems.
CT transformers measure current in single or three-phase mains circuits and feature a secondary winding rated at 1A or 5A AC. This allows for the connection of a current, power, or energy meter remotely from the main wiring. CTs come in various sizes, with standard ratios ranging from 50:5 to 4000:5. Split-core models can be easily clamped around existing wiring, while solid-core models are typically more cost-effective.
VT transformers reduce high voltage to a lower, measurable level. They feature a large number of primary turns and fewer secondary turns, with their performance described by the primary-to-secondary ratio. These transformers are known for their precise turns ratio, ensuring highly accurate voltage measurements.
Distribution or Step down transformers convert higher voltages to lower voltages by transferring electrical energy through two coil stages with the second coil stage having fewer coil windings to lower the voltage level. Power outlet voltages vary geographically with the two most common outlet voltages being 220 volts and 110 volts, which are the voltage differences between countries with different outlet voltage standards.
In a distribution transformer, applying AC voltage to the primary winding creates a fluctuating magnetic field in the core. This magnetic field induces a lower voltage in the secondary winding, which has fewer turns compared to the primary winding. The reduced number of turns in the secondary winding results in a lower electromotive force (EMF) compared to the primary winding.
Step-down transformers are known for their high efficiency, reaching up to 99%, and they deliver output voltage with minimal power loss. They are cost-effective, reliable, and offer high current with low voltage. Distribution transformers come in various types, including single-phase, three-phase, multi-tapped, pad-mounted, and pole-mounted configurations.
A distribution transformer represents the final stage in voltage transformation within an electric power distribution system. It adjusts the voltage to levels suitable for use in homes, businesses, and commercial buildings.
Autotransformers are single-winding transformers where the primary and secondary windings are interconnected. A portion of the winding is shared between both sides of the transformer. Under load conditions, part of the current is supplied directly from the source, while the rest is provided through the transformer itself. Autotransformers are commonly used as voltage regulators.
In an autotransformer, the primary and secondary windings are interconnected both magnetically and electrically. There are different types of autotransformers based on their construction: one type features taps along the winding, while another type has coils connected to form a continuous winding.
Autotransformers offer a cost-effective alternative to three-phase distribution transformers for adjusting supply voltage to meet load demands. They are ideal for fine-tuning voltage in commercial and industrial equipment and provide an economical solution for precise voltage regulation. Due to their single-winding design, autotransformers are more compact than traditional transformers, making them easier to install.
In an autotransformer, voltage transformation occurs at various tapping points along the winding. Adjusting these tap connections alters the voltage ratios. The direct electrical connection between the primary and secondary windings allows for more precise voltage regulation. However, autotransformers generally have lower impedance compared to isolation transformers and may offer less protection against voltage spikes or fluctuations.
Transformers are crucial to modern infrastructure, significantly impacting electricity generation and distribution. Their primary function is to adjust alternating current voltage levels, either increasing or decreasing them. The versatility of electric transformers allows them to be utilized in numerous applications, making them indispensable for controlling voltage and current across various systems.
Battery charging systems typically involve a transformer, a bridge rectifier, and an ammeter. The transformer reduces the voltage, while the bridge rectifier converts the AC output of the transformer into DC current. Directly connecting a transformer to a battery is not feasible because the transformer provides current that is unsuitable for battery charging. The use of a rectifier simplifies this process by ensuring the current is appropriately converted for the battery.
Portable battery chargers incorporate transformers within their design, typically using ferrite core transformers rather than conventional laminated core types. Due to the high operating frequencies of handheld devices, these transformers need to be compact and lightweight to fit into small, portable chargers. The precise control of DC current supplied to devices such as cell phones, computers, and other handheld electronics necessitates the use of these small transformers in their chargers.
Transformers ensure the safe charging of batteries and prevent damage to a battery through the conversion process. Unregulated voltage can result in electrical surges. The controlled voltage that enters a battery prevents damage to the components of a battery.
As electronic devices become increasingly compact and lightweight, the variety of transformers designed for small applications has expanded significantly. Today’s selection of miniature transformers includes numerous designs, configurations, and sizes, each engineered to deliver high performance and efficiency.
The effectiveness of steel production relies heavily on a stable and reliable power supply. Steel manufacturing involves specialized processes that demand various forms of power conversion. Consistent voltage regulation is crucial during transformer operation under load, making it a key requirement for efficient steel production.
Electric arc furnace (EAF) transformers are specifically engineered for the demands of steel production in electric furnaces. These transformers share the fundamental features of standard transformers but are designed with enhanced overload capacity and robust mechanical strength to withstand short circuits. They also include features for adjusting voltage regulation while under load, as well as for managing excitation voltage.
DC electric arc furnace transformers are commonly used in steel production due to their cost-effectiveness and reliability under various conditions. They can handle frequent overvoltages and overcurrents caused by short circuits within the furnace. Available in both air-cooled and water-cooled designs, these transformers can manage currents up to 200 kA. The cooling mechanisms enable precise control of the heating process during operation. Their design includes features for cyclic loading and rectification.
In steel production, high voltage is essential for melting and welding, whereas lower currents are needed for cooling. Transformers play a crucial role in managing this wide range of temperatures, ensuring that voltage and current levels are appropriately regulated throughout the process.
In chemical processing, transformers are used to power electrolysis. During the electroplating of metals like copper, zinc, or aluminum, transformers regulate the electrical current necessary for the chemical reaction, allowing precise control over the current in the process. The system must maintain a stable temperature, provide electrical insulation, and operate effectively in corrosive environments. Rectifiers are used to manage periodic unidirectional pulses of current that exceed the charging source.
Steel manufacturing involves various processes such as melting, welding, molding, and cooling. Melting and welding require substantial current, while cooling involves lower current levels. High voltage transformers are essential for managing current fluctuations throughout these processes. Step-up and step-down transformers are strategically used in different parts of the circuit to achieve the necessary current levels for each stage of production.
Electrolysis is a technique employed to divide both homogeneous and heterogeneous materials by decomposing their ions into basic elements. This method involves applying an electric current to induce a chemical reaction. For the process to work effectively, the current must be steady and is managed through an electrical transformer.
Audio transformers are integral components in microphones, speakers, and amplifiers, engineered to handle signals within the audible spectrum, typically from 20 Hz to 20 KHz. They play a crucial role in filtering out extraneous noise, ensuring that audio devices deliver crisp and precise sound quality. Their application has significantly improved audio clarity in recordings, films, and live events.
Air-dried transformers produce a cooling effect that helps maintain freshness in refrigerators. Beyond this cooling function, these electric transformers also manage current flow to prevent surges and voltage irregularities, ensuring the safe operation of refrigeration systems.
In air conditioning systems, transformers adjust the voltage from the circuit board to the required level, enabling simultaneous operation of the air conditioner and fan. Electric transformers play a crucial role in improving appliance performance, boosting efficiency, and reducing energy consumption
Electric transformers are also utilized in stabilizer circuits for appliances that handle high currents or voltages. These stabilizers adjust the input signal to produce an output that aligns with the household's electrical needs, minimizing the risk of appliance malfunctions or damage. The transformer continuously adjusts the voltage or current to match the optimal levels for the system.
A notable role of electric transformers is acting as DC blockers. This function is achieved through the design of the windings, their spacing, and the insulation used. By configuring the transformer properly within the circuit, it allows alternating current (AC) signals to pass while blocking direct current (DC) signals.
An electric motor can be seen as a more advanced application of the principles used in transformers. While a transformer adjusts voltage or current to suit an application, an electric motor converts electrical energy into mechanical energy and rotational motion. Both transformers and motors operate based
A transformer takes in AC current and converts it to DC current or adjusts it to a level suitable for a motor’s use. Unlike motors, which include an air gap between the core and rotor magnets crucial for magnetic circuit strength and efficiency, a transformer is a stationary device without such a gap.
A lighting transformer system reduces voltage from a power supply to make it compatible with lighting fixtures. These transformers are used in low voltage lighting setups to step down from the standard 120 volts to 12 V or 24 V. They ensure electrical isolation and maintain a stable output voltage despite fluctuations in input voltage, which is crucial for the proper operat
Lighting system transformers vary in size to accommodate different numbers of fixtures and power needs. They can be installed either inside or outside lighting fixtures and feature various control systems. These transformers are crucial for delivering safe and reliable electrical power to both residential and commercial lighting setups.
Medical equipment transformers are essential for ensuring patient safety and delivering consistent, reliable power. These isolation transformers are designed to protect against electrical shocks by keeping the primary and secondary circuits separate. This separation prevents any direct electrical contact between input and output, offering an added safeguard against electrical hazards.
Medical equipment transformers serve three key purposes: ensuring patient safety, minimizing noise, and adhering to healthcare safety standards. They protect patients in healthcare settings from electrical accidents and reduce noise that could affect sensitive medical devices and communication systems. Compliance with stringent regulations from the FDA and other oversight bodies is mandatory for all medical facilities.
Heating and cooling system transformers come in various types, such as furnace, AC, and heat pump transformers. Typically, these include step-up and step-down transformers. Step-up transformers increase voltage from 110 volts to 240 volts, while step-down transformers reduce voltage from 240 volts to 110 volts, commonly used in industrial settings.
Furnace transformers lower high voltage input to a safer output level, integrating timers, ignition systems, circuits, and temperature controls to stabilize the voltage. They send signals to manage relays and contacts that regulate system operations. When the thermostat activates, it energizes a coil in the relay, creating a magnetic field that closes the switch and activates the blower.
HVAC systems use various relays, controllers, and switches to ensure proper sequencing of their components. Given the sensitivity of these controllers, a transformer is needed in the control box or air handler to step down the voltage, connecting it to the thermostat for accurate operation.
Audio transformers come in two main types: step-up/step-down transformers and 1:1 transformers. These devices are used to adjust impedance, convert between balanced and unbalanced circuits, block DC current while allowing AC current to pass, and isolate different audio equipment. Step-up transformers, for instance, are used in microphones to boost the signal level and impedance before it exits the microphone.
1:1 audio transformers have equal windings in both primary and secondary coils, maintaining the same impedance and signal level without altering the audio signal. They block DC voltage and radio frequency interference (RFI), provide
Residential voltage typically is 240 V, suitable for home tools and DIY tasks. However, for heavy-duty projects, 110 V tools are preferred and need a transformer to function. On job sites, 110 V tools are favored for safety reasons, including reducing risks such as cable damage.
On job sites, power tools are connected to transformers that convert 240 V to 110 V to eliminate the need for circuit breakers. These transformers use two 55 V lines to create 110 V. In case of wire damage or accidents, the voltage is reduced to enhance user safety.
Uninterruptible power supplies (UPS) offer backup power during outages and voltage fluctuations. They utilize transformers to provide galvanic isolation between input and output, safeguarding sensitive equipment from voltage spikes, electrical noise, and disturbances.
In a low-frequency UPS, power passes through the rectifier, inverter, and transformer. The transformer boosts the AC voltage, isolates the UPS from load disruptions, and provides protection. Unlike emergency power systems and generators, a UPS quickly switches to batteries or supercapacitors to protect against power interruptions.
While a UPS may provide limited run time, it allows for implementing measures to restore power. All UPS systems include surge protectors to shield equipment from voltage spikes. They are primarily used to protect computers, telecommunications equipment, and sensitive data centers from power interruptions.
Electric transformers are static electrical machines that transform electric power from one circuit to the other without changing the frequency. An electrical transformer can increase or decrease the voltage with...
An isolation transformer, just like typical transformers, is a non-moving device that transmits electrical energy from one circuit to another without requiring any physical contact. It works on the idea of magnetic...
Power transformers are electrical instruments used in transmitting electrical power from one circuit to another without changing the frequency. They operate by the principle of electromagnetic induction. They are used in transmitting electrical power between...
An electrical transformer is a passive machine that transfers electrical energy from one circuit to another using a magnetic flux to induce an electromotive force. Transformers are used to increase (step-up) or decrease (step-down) voltages without changing the frequency of the electric current...
A toroidal transformer is a type of electrical transformer constructed with a torus or donut-shaped core. Its primary and secondary windings are wound across the entire surface of the torus core separated by an insulating material...
Power supplies are electrical circuits and devices that are designed to convert mains power or electricity from any electric source to specific values of voltage and current for the target device...
An AC power supply is a type of power supply used to supply alternating current (AC) power to a load. The power input may be in an AC or DC form. The power supplied from wall outlets (mains supply) and...
An AC power cord is a detachable way of providing an alternating current of electric energy from a mains power supply to an electrical appliance or equipment. Serving industries like...
A DC DC power supply (also known as DC DC Converter) is a kind of DC power supply that uses DC voltage as input instead of AC/DC power supplies that rely on AC mains supply voltage as an input...
A DC power supply is a type of power supply that gives direct current (DC) voltage to power a device. Because DC power supply is commonly used on an engineer‘s or technician‘s bench for a ton of power tests...
An electric coil, or electromagnetic coil, is an electrical conductor that contains a series of conductive wires wrapped around a ferromagnetic core that is cylindrical, toroidal, or disk-like. Electric coils are one of the simplest forms of electronic components and provide...
Electrical plugs, commonly known as power plugs, are devices responsible for supplying and drawing current from a receptacle to the circuitry of an electrical appliance...
By definition a power supply is a device that is designed to supply electric power to an electrical load. An electrical load refers to an electrical device that uses up electric power. Such a device can be anything from...
Inductors are passive two terminal components of an electric or electronic circuit that are capable of storing energy in magnetic form. They oppose sudden changes in current and they are also called coils or chokes...
A NEMA connector is a method for connecting electronic devices to power outlets. They can carry alternating current (AC) or direct current (DC). AC current is the typical current found in homes, offices, stores, or businesses...
A power cord is an electrical component used for connecting appliances to an electrical utility or power supply. It is made from an insulated electrical cable with one or both ends molded with connectors...
A programmable power supply is a method for controlling output voltage using an analog or digitally controlled signal using a keypad or rotary switch from the front panel of the power supply...
A solenoid coil is a common electrical component that uses a wire that is tightly wrapped around a core, usually made of metal, to generate an electromagnetic field. When an electrical current is passed through the coil, the electromagnetic field that is created provides energy for linear motion...
A voice coil is a winding of a wire, usually copper, aluminum, or copper-clad aluminum that is wrapped around a former (often called a bobbin) and then attached to the apex of a speaker cone...
Thomas Edison developed the power distribution system in 1882. He wrapped a copper rod in jute, a soft shiny fiber from plants, as an insulator. The jute wrapped copper rod was placed in a pipe with a bituminous compound...