Types of Metal Finishing
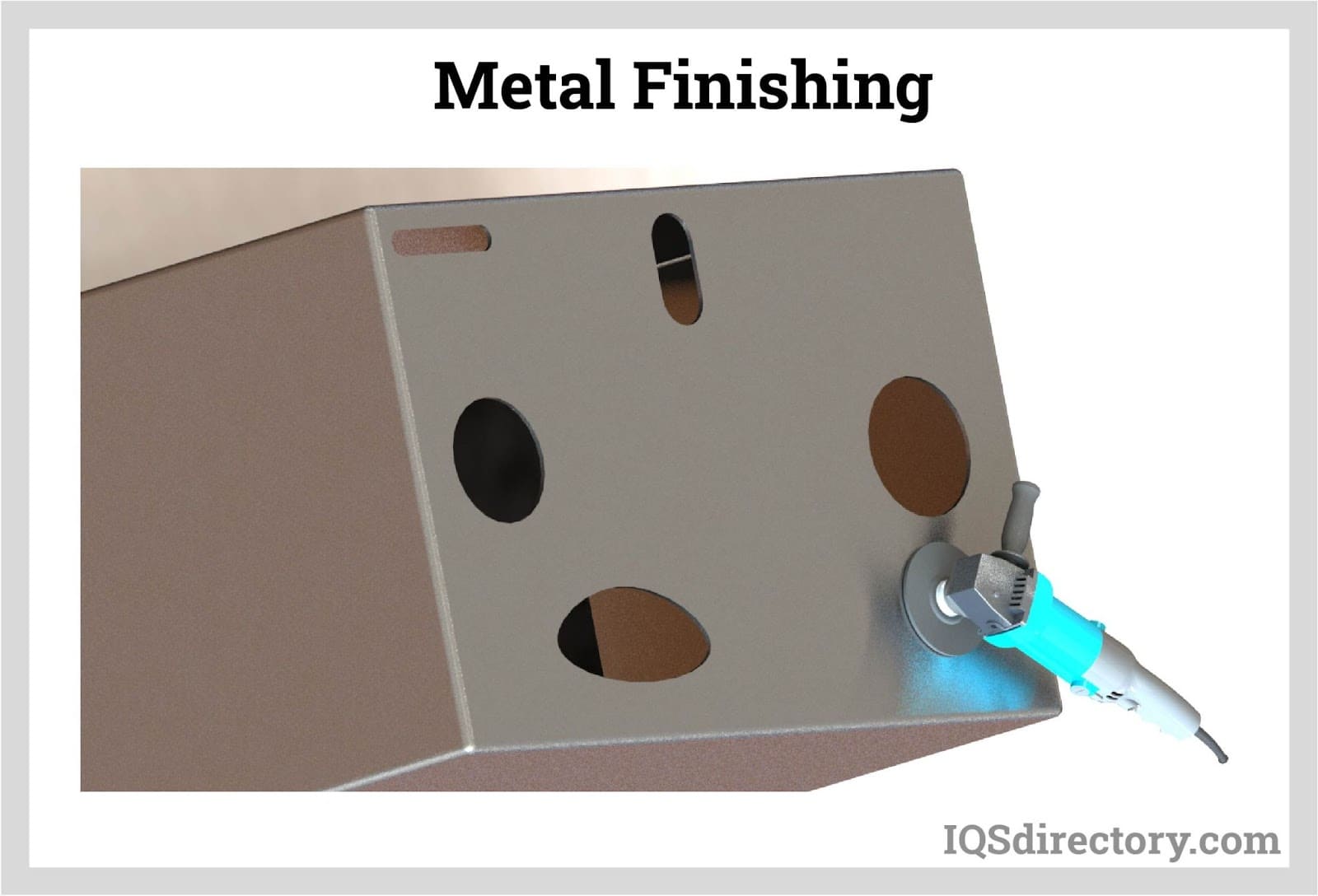
Metal finishing describes various procedures or processes that can be as simple as buffering to adding a special type of coat to the substrate. Included in the description of metal finishing are a number of cleaning...
Please fill out the following form to submit a Request for Quote to any of the following companies listed on
This article is an in depth study of electroless nickel plating and its uses.
You will learn:
And much more…
Electroless nickel deposition (END) is a process that applies a nickel-based layer via a chemical reaction. In this technique, nickel ions are reduced to their metallic form using a chemical reducing agent such as sodium hypophosphite. END is utilized to significantly boost resistance to corrosion caused by elements such as saltwater, carbon dioxide, oxygen, and hydrogen sulfide. This plating process delivers a uniform, smooth, and even finish on the entire surface, including complex areas such as slots, holes, and the internal surfaces of tubes.
The effectiveness of electroless plating hinges on adequate surface preparation, as uneven, rough surfaces with burrs and cold shuts can lead to bonding problems or accumulations that may worsen the situation. The goal of this procedure is to offer protection against wear, abrasion, and corrosion, as well as to improve surface performance. It is an exceptionally efficient and cost-effective way to achieve a durable, high-quality finish.
The electroless nickel plating process is a highly versatile and widely adopted surface finishing technique used across various industries, including automotive, aerospace, electronics, and manufacturing. Unlike traditional electroplating, electroless nickel plating is an auto-catalytic chemical deposition method that provides an even, durable nickel-phosphorus or nickel-boron alloy coating without the need for electrical current. The success of this process—and the overall quality of the finished component—depends heavily on meticulous surface preparation, effective chemical activation, and precise control during each process stage. Understanding the complete process is key for manufacturers and engineers looking to achieve optimal plating adhesion, corrosion resistance, wear protection, and surface functionality.
Before nickel plating can commence, the surface must be meticulously cleaned and pre-treated to eliminate any dirt, oil, or contaminants that might hinder the adhesion or uniformity of the electroless nickel coating. Industrial degreasers, alkaline cleaners, and ultrasonic cleaning techniques are commonly used to cleanse the surface of grease, fingerprints, machining oils, and other organic or inorganic residues. Effective surface preparation for plating is an essential step that greatly impacts plating thickness consistency, coating integrity, and long-term performance in corrosive environments.
Once the substrate is thoroughly cleaned, the next critical step is surface activation. This stage utilizes an acidic solution, such as hydrochloric or sulfuric acid, to remove any residual oxide film and reveal a fresh metal surface with greater catalytic activity. This is especially important for non-ferrous metals and complex alloys, ensuring that the electroless nickel-plated layer adheres properly to the base material. Surface activation is vital to prevent plating defects like pitting, blistering, or delamination, which can compromise the part's functionality and appearance.
Depending on the type of substrate—whether it is steel, aluminum, copper, or plastic—specific pre-treatment techniques may be needed to enhance adhesion and boost resistance to corrosion and wear. Application of a zincate treatment for aluminum substrates, or the use of palladium or platinum as a catalyst for non-conductive surfaces, is often implemented before the main plating bath stage. These surface preparation methods are critical for achieving both strong metallurgical bonding and uniform nickel deposit thickness, directly influencing the performance of the electroless coating in demanding environments.
During the chemical nickel plating process, the pre-treated substrate is submerged in a carefully formulated solution containing nickel ions, a reducing agent (commonly sodium hypophosphite or sodium borohydride), stabilizers, and a suite of proprietary additives. The reducing agent interacts with the nickel ions to initiate a controlled redox reaction, causing an autocatalytic deposition of a dense, uniform nickel-phosphorus alloy layer or nickel-boron alloy layer onto every exposed surface of the substrate, including cavities and complex geometries. Unlike electrolytic plating, electroless nickel finishes can achieve superior uniformity of thickness and exceptional coverage, offering critical benefits in applications demanding high dimension accuracy, improved surface hardness, and enhanced chemical resistance.
Once the electroless plating cycle is complete, the plated component undergoes crucial post-treatment procedures tailored to further enhance performance characteristics. Rinsing and drying remove residual chemicals, while additional steps such as heat treatment (baking) serve to increase the hardness and improve the crystalline structure of the nickel deposit. In many cases, post-treatments such as passivation, application of protective topcoats or sealants, and anti-corrosion agents are recommended to extend the lifespan and durability of the finished part. Choosing the right post-treatment depends on end-use requirements, including friction reduction, increased weldability, or achieving specific surface finishes to meet environmental, medical, or engineering standards.
By following each stage of the electroless nickel plating process with precision, manufacturers can achieve consistent and reliable surface engineering solutions. Industries seeking custom electroless nickel plating services benefit from a comprehensive, controlled workflow that ensures every finished component meets stringent industry standards for corrosion protection, surface hardness, and aesthetic quality. For those evaluating the best plating solutions for specific parts or applications, an understanding of these process steps assists in selecting the most effective coating technology for performance, cost, and compliance.
Electroless nickel plating machines are essential tools in modern industrial finishing, providing uniform, corrosion-resistant, and wear-resistant nickel coatings over a wide range of substrates. These automated plating systems are pivotal in sectors including automotive, aerospace, electronics, energy, and manufacturing, where product reliability and performance are paramount. By employing advanced surface engineering techniques, these machines deliver robust plating solutions that enhance protection, extend service life, and improve the overall functionality of critical components. Below, we examine several leading electroless nickel plating equipment manufacturers and their flagship models available in the United States and Canada, with an emphasis on their unique features, versatility, and suitability for different applications and production environments.
Features: SIFCO Applied Surface Concepts is an industry leader in selective plating and surface technology, offering a variety of electroless nickel plating equipment ranging from industrial-scale tank systems to highly portable units. The SIFCO Process® Equipment is specifically engineered for highly controlled and reliable nickel-phosphorus deposition, ideal for both localized repairs and production-scale processing. This equipment features programmable settings for precise control of bath chemistry, immersion time, temperature, and agitation—ensuring consistent deposit quality and optimally engineered surface finishes. With integrated, advanced filtration and solution circulation systems, SIFCO’s machines maintain stable bath chemistry, reduce contaminants, and minimize downtime for maintenance. Its intuitive interface and robust, energy-efficient design support high throughput, making it a top choice for industries demanding quality, productivity, and reliability from their metal finishing solutions.
Features: The Techni EN-BM Series from Technic Inc. represents a state-of-the-art line of electroless nickel plating machines designed for fully automated and semi-automated production environments. Known for process repeatability and tight quality control, the Techni EN-BM Series is equipped with programmable logic controllers (PLCs) for precise regulation of key plating parameters, including nickel ion concentration, pH balance, solution flow rate, and temperature control. These nickel electroplating systems feature advanced solution management, automatic dosing, and on-line monitoring capabilities, significantly reducing defects and increasing operational efficiency.
Integral filtration and agitation modules maintain solution integrity and facilitate even nickel deposition, resulting in superior corrosion protection and high-purity finishes. User-friendly HMI panels and modular construction simplify integration into existing production lines, while designed-in safety mechanisms enhance uptime and minimize operational risk. These features make the Techni EN-BM Series ideal for high-precision parts in aerospace, electronics, and automotive component manufacturing, ensuring parts consistently meet strict functional and regulatory requirements.
Features: C. Uyemura & Co., Ltd. is a globally recognized name in surface finishing technology, and its Miralloy Series excels in offering tailored electroless nickel plating solutions for diverse industrial applications. The Miralloy Series is engineered for flexibility, supporting a broad spectrum of substrate types and plating processes, including nickel-phosphorus and nickel-boron alloys. This equipment integrates intelligent control systems for real-time monitoring and precise adjustment of critical bath parameters such as solution temperature, chemical dosing, pH stability, and organic stabilizer levels, which are vital for delivering consistent, high-performance nickel plating results. Advanced filtration and purification technology minimizes contaminant build-up and extends solution life, improving operational efficiency while lowering running costs and reducing environmental impact. These electroless plating systems are particularly well-suited for manufacturers seeking quality assurance, process scalability, and energy-efficient operations.
Features: Sharretts Plating Company specializes in designing and manufacturing custom electroless nickel plating systems built to exacting customer specifications. Their equipment allows granular control over all bath constituents, temperature, fluid dynamics, and process parameters essential for precision plating across a range of industrial and technical applications. Each system features heavy-duty agitation mechanisms, automated dosing, digital process monitoring, and smart control panels for comprehensive oversight and enhanced quality assurance. With a reputation for system durability, robust construction, and technical support, Sharretts Plating Company's tailor-made solutions are ideal for unique manufacturing challenges that demand adaptability, high-performance finishes, and long-term reliability in both low and high-volume electroplating operations, as well as for those adhering to specific industry certifications and standards.
Features: Metal Chem, Inc. is known for process innovation in the plating industry, and the Auto Catalyst 2000 Series stands out as a next-generation electroless nickel plating solution designed for large-scale, continuous production. Key features include fully automated operation for seamless process control, intelligent dosing for bath maintenance, and in-line filtration for superior solution purity. This high-volume equipment is engineered to reduce cycle times, improve ROI, and offer exceptional throughput while maintaining rigorous quality standards across all deposited coatings. Integrated solution management, easy-to-navigate control interfaces, and compliance with modern industrial safety standards make the Auto Catalyst 2000 Series a strong choice for facilities with demanding production schedules and varied substrate materials, such as those found in the automotive, heavy equipment, and electronics industries.
How to Choose the Right Electroless Nickel Plating Machine: When selecting an electroless nickel plating system, consider factors like bath capacity, degree of automation, compatibility with specific alloys, capability for uniform and high-phosphorus coatings, maintenance requirements, uptime reliability, and support for process monitoring or data logging. Evaluate the ease of integration into your existing processes and look for equipment compliant with both industry regulations and your sustainability goals.
Because specifications and technical features are subject to change, it is recommended that prospective buyers consult industry resources and reach out directly to machine manufacturers or their authorized distributors. Request detailed literature, technical documentation, or arrange for on-site demonstrations to find the ideal electroless nickel plating equipment for your operation’s needs.
One of the attributes of nickel plating is the number of methods that can be used to complete the process. Each of the methods uses the name plating with each type having different uses and purposes. Regardless of the method, they are all intended to enhance and improve the properties of nickel and its resistance to corrosion and rust.
Electroplating involves applying a metal coating onto a metal object through the use of an electrical current. In this method, the object to be plated is attached to the negative terminal of a direct current power source, while the metal to be deposited is connected to the positive terminal. An electrolyte solution, which contains metal ions, serves as the medium through which these ions migrate and bond to the object. Unlike electroless plating, electroplating necessitates an electrical current and requires the object to be conductive.
Brush plating is a technique for applying a metal coating to specific areas of a metal object using an electroplating solution and a brush. In this method, the brush is connected to the positive terminal of a direct current power source, while the object to be plated is attached to the negative terminal. The brush, immersed in the electroplating solution that contains metal ions, transfers these ions to the targeted area of the object. This technique is primarily used for localized repairs rather than for covering an entire surface.
Hard chrome plating is an electroplating method used to apply a substantial layer of chromium to a metal surface, enhancing its resistance to corrosion and wear. Unlike electroless nickel plating, hard chrome plating relies on an electrical current to transfer the chromium onto the object, resulting in a durable, highly reflective finish that offers excellent wear and abrasion resistance. However, the use of hexavalent chromium in this process raises environmental and health concerns, leading to the development of alternative plating techniques.
In contrast to other plating methods, electroless nickel plating does not require an electrical current, as it relies on a chemical reduction reaction for deposition. This allows for a uniform coating on complex shapes and even non-conductive surfaces. Electroless nickel plating offers consistent thickness, even in hard-to-reach areas, and provides excellent corrosion and wear resistance. Ultimately, the selection of the plating process depends on the particular application and the desired coating characteristics.
Sulfamate nickel plating is an electroplating technique that employs nickel sulfamate to achieve a coating with a purer and denser structure. This method produces a high-tensile strength coating that is machinable and offers excellent corrosion resistance. It can endure temperatures up to 1400°C (2552°F). The resulting sulfamate nickel coating has a matte finish and is commonly used for repairing worn components.
Electroless nickel plating is a method for depositing a nickel alloy by chemical reduction, without the use of electric current. Most electroless nickel plating uses nickel phosphorus with a 2% to 14% phosphorus content. As the quantity of phosphorus increases, the plating material offers greater corrosion protection. The variations in electroless nickel plating are determined by the amount of phosphorus used.
This type features a high phosphorus content in the plating solution, yielding a coating with superior resistance to corrosion, wear, and non-magnetic qualities. It is widely utilized in aerospace, automotive, and electronics applications.
This variation has a lower phosphorus content compared to high phosphorus electroless nickel, producing a coating with commendable wear resistance and moderate corrosion protection. It is commonly employed in the automotive and electronics sectors.
This type contains minimal phosphorus, resulting in a coating with high brightness, excellent solderability, and good electrical conductivity. It is primarily used in the electronics industry.
These coatings include dispersed nanoparticles or other materials within the plating solution, enhancing properties such as wear resistance, corrosion resistance, and electrical conductivity. They find applications across aerospace, automotive, and electronics industries.
This variant incorporates polytetrafluoroethylene (PTFE) particles in the plating solution, creating a coating with outstanding non-stick and low-friction attributes. It is commonly used in food processing, medical, and semiconductor industries.
This type incorporates boron nitride particles within the plating solution, resulting in a coating with exceptional lubricating properties and wear resistance. It is frequently utilized in the aerospace, automotive, and electronics sectors.
This variation contains tungsten carbide particles dispersed within the plating solution and results in a coating with excellent wear resistance and hardness. It is commonly used in the oil and gas, aerospace, and automotive industries.
This type features a unique blend of nickel and other materials, producing a black matte coating. It is primarily used in the firearms industry for its visual appeal, and also finds applications in the electronics and automotive sectors.
This type includes silicon carbide particles within the plating solution, producing a coating with outstanding wear resistance, hardness, and thermal conductivity. It is frequently utilized in the automotive, aerospace, and defense industries.
This method applies a layer of electroless nickel followed by a layer of gold, combining the corrosion resistance and electrical conductivity of electroless nickel with the visual appeal and additional corrosion resistance of gold. It is widely used in the electronics and jewelry industries.
This method involves applying a layer of electroless nickel followed by a layer of cobalt, resulting in a coating with increased hardness, wear resistance, and magnetic properties. It is frequently utilized in the electronics and automotive sectors.
Each variation serves distinct purposes based on its specific characteristics. For instance, high phosphorus electroless nickel is preferred in aerospace applications for its superior corrosion resistance, whereas electroless nickel-PTFE coatings are chosen for food processing due to their non-stick qualities.
Electroless nickel plating on plastic enhances wear resistance, increases surface hardness, provides electrical conductivity, or improves the aesthetic appearance of parts. Although the technique was introduced in the 1960s, it took time to develop a method that ensured a robust bond between the nickel coating and the plastic substrate.
The challenge was addressed by using a chromic acid-based etchant to prepare the plastic surface, which significantly improved its adhesive properties. Once the process was refined, the automotive industry adopted electroless nickel plating on plastics for manufacturing grilles, emblems, and light bezels.
The effectiveness of plastic plating hinges on the proper molding of the plastic component, which reduces stress and eliminates defects. To enable plating, the plastic must be metallized to enhance adhesion, achieved through electroless metal deposition on the substrate’s surface.
Etchants like chromium trioxide or sulfuric acid facilitate the absorption of liquids by the part and create microscopic pores for metal bonding. Various surface treatment methods were explored, and it was determined that pre-etching significantly improves adhesive properties and reduces surface layer strain on the plastic.
Nickel plating offers numerous advantages, which is why it has been utilized for over 150 years. Discovered in the eighteenth century, nickel was initially called kupfernickel, meaning "devil’s copper" in German. Its strength, resistance to corrosion, durability, and appealing finish have contributed to its enduring popularity.
It was in the middle of the first industrial revolution that nickel plating was invented by an Italian chemist. Near the end of the nineteenth century, a viable method for nickel plating was introduced and became the standard for the process.
Electroless nickel plating offers superior protection against corrosion, shielding parts and components from rust and other corrosive elements. The process creates a protective layer on the surface, which prevents moisture and corrosive agents from reaching the underlying metal.
This plating method also enhances wear resistance, extending the lifespan of parts subjected to high levels of friction and abrasion. The nickel coating’s hardness and durability protect against scratches, abrasions, and other forms of wear.
Electroless nickel plating ensures precise control over the coating’s thickness and uniformity, providing an even and consistent layer. This accuracy helps in delivering optimal protection and performance across coated parts.
With excellent adhesion to various materials including metals, plastics, and ceramics, electroless nickel plating eliminates the need for additional primers or adhesives, streamlining the coating process and reducing associated costs.
This plating technique results in a smooth and consistent surface finish, free from imperfections and defects. This not only enhances the visual appeal of parts but also improves their overall functionality and performance.
Electroless nickel plating provides high electrical conductivity, making it suitable for electronic and telecommunications components. It can also enhance the conductivity of existing components, such as connectors and printed circuit boards.
The coating offers excellent resistance to various chemicals, making it suitable for parts exposed to harsh chemical environments. This resistance helps to protect the part and extend its operational life.
Electroless nickel plating can be tailored to possess non-magnetic properties, which is advantageous for components used in magnetic environments, including medical devices like MRI machines.
Electroless nickel plating offers a cost-efficient option for coating parts and components, particularly in comparison to other methods like electroplating or vacuum deposition. The process is straightforward and necessitates minimal equipment, contributing to lower overall costs.
These are some of the numerous advantages of electroless nickel plating. Additional benefits may include enhanced heat resistance, greater hardness, and improved wear resistance under high-temperature conditions.
Since its inception, electroless nickel plating has become widely adopted across various industrial applications. As the need for more durable products has increased and consumer expectations have risen, manufacturers have increasingly turned to electroless nickel plating to enhance product longevity and appearance.
An aerospace parts manufacturer faced issues with corrosion and wear on aluminum components used in landing gear systems. Implementing electroless nickel plating provided a consistent, corrosion-resistant coating, extending the life of the components and reducing the frequency of expensive replacements.
In the electronics sector, electroless nickel plating is commonly used to boost the performance and reliability of electronic components. For example, plating printed circuit boards with electroless nickel improved solderability and minimized defects, which enhanced product reliability and cut manufacturing costs.
An automotive parts supplier was dealing with corrosion and wear issues on cast iron brake components. By applying electroless nickel plating, the supplier achieved a uniform, wear-resistant coating, improving component durability and reliability while lowering the risk of costly recalls and warranty claims.
A medical device manufacturer encountered biocompatibility issues with stainless steel components in implantable devices. Using electroless nickel plating to apply a biocompatible coating enhanced the safety and effectiveness of the devices, reducing the likelihood of adverse reactions and improving patient outcomes.
Electroless nickel plating is utilized to coat equipment in oil and gas exploration, including drill bits and pipe connectors, to enhance wear and corrosion resistance. For instance, plating drill bits with electroless nickel significantly extended their service life, leading to reduced downtime and lower maintenance costs.
In the manufacturing sector, electroless nickel plating is applied to various industrial equipment, such as molds, dies, and rollers, to boost wear and corrosion resistance. For example, plating a roller used in a paper mill with electroless nickel improved its wear resistance, resulting in a longer service life and decreased downtime.
Electroless nickel plating is extensively used in chemical processing to enhance the corrosion resistance of equipment exposed to harsh chemical environments. For instance, plating a heat exchanger with electroless nickel improved its resistance to corrosion, leading to a longer service life and reduced maintenance expenses.
In the food processing industry, electroless nickel plating is used to coat equipment like blades and mixing bowls to improve their wear and corrosion resistance. For example, electroless nickel plating a mixing bowl in a food processing plant led to better wear resistance and reduced contamination, which improved product quality and minimized cleaning time.
Electroless nickel plating is widely used in military and defense applications, including firearms, to enhance wear and corrosion resistance. For example, plating a firearm with electroless nickel improved its wear resistance and reduced friction, resulting in enhanced accuracy and reliability.
These examples highlight the versatility and effectiveness of electroless nickel plating as a surface finishing technology. By applying a uniform, corrosion-resistant coating to various substrates, electroless nickel plating improves the performance and durability of a diverse range of products.
The use of electroless nickel plating has broadened across a wide range of applications, from aerospace and automotive manufacturing to medical devices and dental implants. The enhanced strength and durability provided by electroless nickel plating continue to drive its adoption in new and innovative applications.
In these industries, electroless nickel plating is applied to enhance the wear and corrosion resistance of engine parts, including pistons, valve bodies, and fuel injectors. Additionally, it is used to coat essential components of aircraft engines and landing gear to safeguard against corrosion and wear.
Electroless nickel plating is employed to shield electronic components from corrosion and wear while also improving their electrical conductivity. It is frequently used to coat connectors, printed circuit boards, and microwave components.
In medical and dental fields, electroless nickel plating enhances the biocompatibility of implants and instruments and delivers a smooth, consistent surface finish. It is widely applied to coat surgical instruments, orthopedic implants, and dental tools.
In the oil and gas sector, electroless nickel plating is employed to safeguard equipment from corrosion and wear in demanding environments, such as offshore rigs and pipelines. It is commonly applied to coat valves, pumps, and drill bits.
Electroless nickel plating enhances the wear and corrosion resistance of various industrial and manufacturing tools. It is often used to coat gears, bearings, molds, and dies.
This plating method is used to protect equipment in chemical processing, including tanks, valves, and pumps, from corrosion and wear induced by aggressive chemicals and high temperatures.
In the food processing industry, electroless nickel plating helps to prevent corrosion and wear caused by acidic and salty conditions. It is commonly used on mixing blades, choppers, and conveyors.
Electroless nickel plating improves the wear and corrosion resistance of military and defense equipment used in severe conditions, such as submarines, tanks, and aircraft.
This plating technique is applied to mining equipment, including drill bits and cutting tools, to enhance their durability and resistance to wear and corrosion in harsh mining environments.
In renewable energy sectors, such as solar and wind power, electroless nickel plating is used to coat components exposed to harsh outdoor conditions. It is frequently used for connectors, gearboxes, and bearings.
Electroless nickel plating is utilized in the printing industry to coat printing rollers, gears, and other components to reduce wear and extend equipment longevity.
This plating method is used in the textile industry to coat parts of weaving and spinning machinery, as well as components of dyeing machines, to prevent wear and corrosion.
Electroless nickel plating is used on fasteners used in the aerospace industry to prevent corrosion and improve the durability of the parts.
Electroless nickel plating is applied to firearms to safeguard them against rust and corrosion while enhancing their visual appeal.
In the case of musical instruments like flutes and saxophones, electroless nickel plating is used to prevent corrosion and enhance the quality of sound.
In the jewelry industry, electroless nickel plating is utilized to coat jewelry items, including bracelets and rings, enhancing their resistance to wear and corrosion.
In the marine industry, electroless nickel plating is applied to coat components such as propellers and valves that are exposed to saltwater and harsh marine conditions.
In the automotive industry, electroless nickel plating is employed for decorative applications, including coating wheels, trim, and other components to enhance their aesthetic appeal.
Electroless nickel plating is a chemical process that demands rigorous oversight to ensure the safety of both workers and the surrounding community. As environmental regulations become increasingly stringent, plating processes, particularly those involving chemicals, are under greater scrutiny. In the United States, electroless nickel plating must comply with various laws and regulations concerning environmental protection and worker safety.
The Clean Water Act governs the discharge of pollutants into navigable waters, including those used in electroless nickel plating processes. The Environmental Protection Agency (EPA) is responsible for enforcing this law.
The Resource Conservation and Recovery Act regulates the management and disposal of hazardous waste, including that produced by electroless nickel plating operations. Enforcement of this law is also the responsibility of the EPA.
OSHA regulations establish standards for workplace safety, including those related to handling hazardous chemicals used in electroless nickel plating processes.
The Toxic Substances Control Act oversees the manufacture, import, and processing of chemicals, including those involved in electroless nickel plating. The EPA enforces this regulation.
Alongside these federal laws, there may be state or local regulations governing electroless nickel plating. Some states impose additional rules regarding hazardous waste management and workplace safety.
Globally, several organizations also regulate electroless nickel plating processes, including:
REACH (Registration, Evaluation, Authorization and Restriction of Chemicals) is a European Union regulation that oversees the use of chemicals in various industries, including those used in electroless nickel plating.
The IARC, an intergovernmental agency within the World Health Organization, assesses the carcinogenicity of various substances, including nickel and other chemicals used in electroless nickel plating.
The IEC is an international standards organization that establishes standards for the electrical and electronics sectors. It has developed standards for the application of electroless nickel plating in electronic components.
Companies involved in electroless nickel plating, particularly those operating internationally, must adhere to these regulations to ensure both worker safety and environmental protection.
Every chemical process has potential drawbacks that can impact both human health and the environment. Additionally, these processes often involve high costs due to the chemicals required for initiation and completion. It's important to consider these factors when selecting electroless nickel plating as a manufacturing method.
Certain chemicals used in the electroless nickel plating process, such as nickel and sodium hypophosphite, can pose health risks if not managed correctly. To mitigate these risks, it is essential to adhere to safety measures, including wearing appropriate protective gear and ensuring proper ventilation in the work area.
The chemicals involved in electroless nickel plating can negatively affect the environment if they are not disposed of properly. It is crucial to follow appropriate disposal procedures to prevent contamination of soil and water sources.
Although electroless nickel plating is generally more affordable compared to methods like electroplating or vacuum deposition, it may still be more costly than alternative surface treatment options such as painting or powder coating.
Electroless nickel plating can only achieve a limited thickness, typically up to about 0.003 inches. For applications requiring thicker coatings, other methods may be necessary.
This plating method is usually suitable for specific types of substrates, including metals and certain plastics. It may not be appropriate for use on materials like ceramics or glass.
The electroless nickel plating process involves careful control of various factors, such as the plating solution, temperature, and pH. This complexity can make it more challenging to implement compared to other coating techniques, particularly for smaller enterprises with limited resources.
Effective surface preparation is vital for successful electroless nickel plating. Contaminants or imperfections on the part's surface can impact the adhesion and quality of the coating.
The future of electroless nickel plating looks promising. As technology evolves, new applications for this process are continually emerging. Furthermore, several favorable trends suggest that electroless nickel plating will play a significant role in the future.
With growing needs in industries such as aerospace, automotive, and defense for enhanced wear resistance in their components, the demand for electroless nickel plating is likely to rise due to its effective wear resistance properties.
The advent of additive manufacturing technologies like 3D printing has created a demand for surface finishing processes capable of coating complex geometries. Electroless nickel plating could be an ideal solution to address this requirement.
The medical device industry is rapidly expanding, and electroless nickel plating has demonstrated its potential in this sector. As the need for biocompatible coatings and antimicrobial properties increases, electroless nickel plating may experience further growth in this field.
Researchers are developing new electroless nickel alloys with enhanced properties, such as greater hardness, wear resistance, and corrosion resistance. As these advanced alloys become more accessible, electroless nickel plating is expected to find broader applications.
With rising environmental regulations, there is a shift towards adopting more eco-friendly coatings and plating processes. Electroless nickel plating, which has a lower environmental impact compared to other methods, may see increased adoption in industries concerned with environmental sustainability.
Renewable energy technologies, such as solar and wind power, require specialized components that need coatings with high wear and corrosion resistance. Electroless nickel plating has proven effective for components in wind turbines and could play a more prominent role in the renewable energy sector as it continues to expand.
Advances in nanotechnology are creating a need for surface finishing techniques capable of coating and protecting nanoscale structures. Electroless nickel plating shows promise in this area by coating nanomaterials and nanoparticles, potentially providing additional functionalities like electrical conductivity, catalytic activity, and biocompatibility.
The biotechnology sector requires specialized coatings for medical devices, such as orthopedic implants and cardiovascular stents. These coatings must be biocompatible, antimicrobial, and wear-resistant. Electroless nickel plating has already proven effective for some medical devices and may see increased use as the demand for such coatings grows.
In summary, electroless nickel plating is likely to play a crucial role across various industries as emerging technologies and new applications for the process are identified. Its capability to deliver wear and corrosion resistance, along with other essential properties, makes it a versatile and valuable technology for a wide range of applications.