NEMA Enclosures
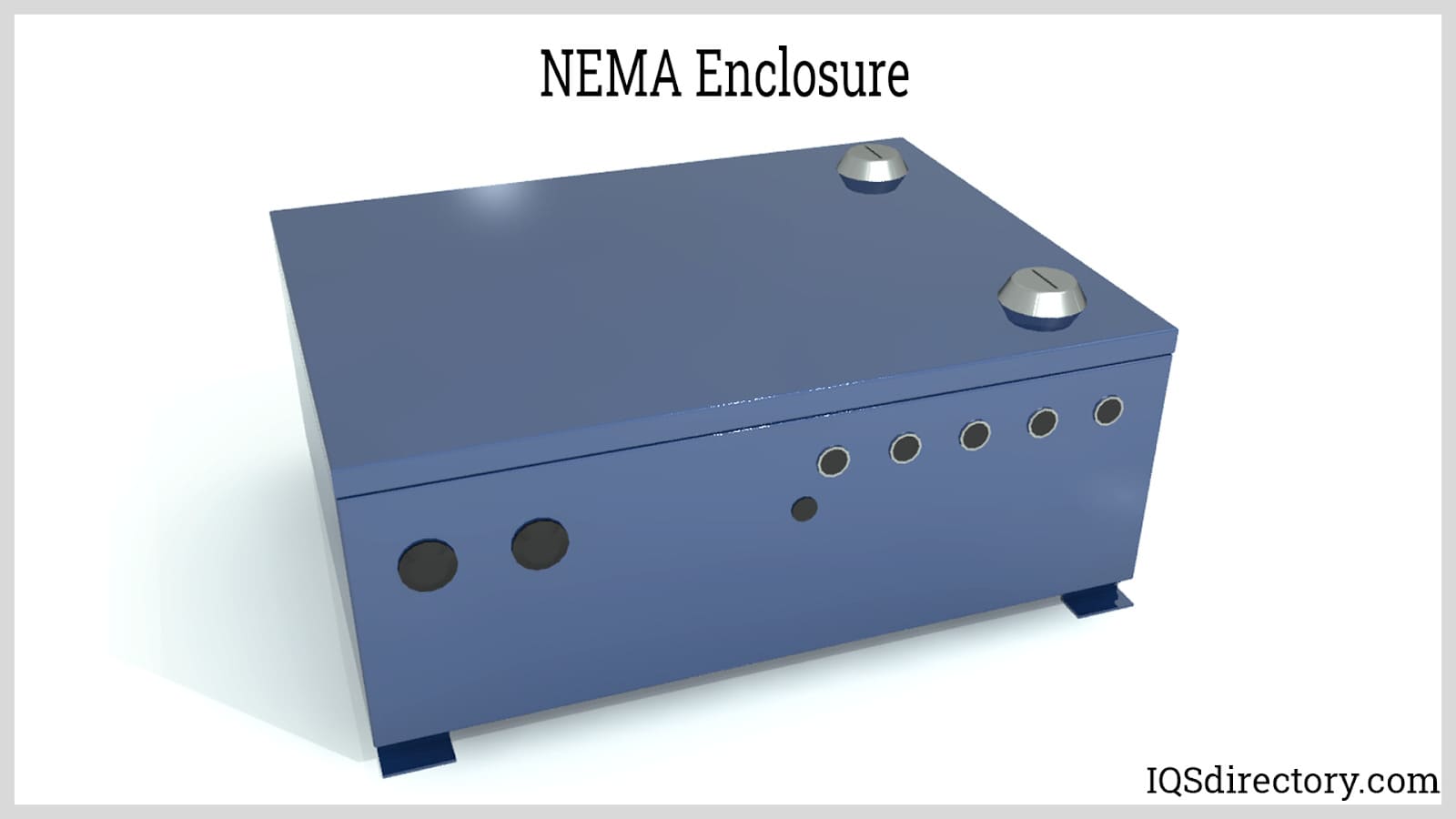
NEMA enclosures are boxes that are designed to protect electrical components from the surrounding environment. Depending on the specific NEMA rating, devices in a NEMA enclosure are protected in...
Please fill out the following form to submit a Request for Quote to any of the following companies listed on
This article will take an in-depth look at electronic enclosures.
The article will bring more detail on topics such as:
This chapter will delve into the concept of electronic enclosures and outline the steps involved in their creation.
Electronic enclosures are protective housing units, designed to safeguard electronic components like switches, relays, printed circuit boards (PCBs), integrated circuits, power sources, and processors. These enclosures are available in a variety of materials and sizes, customized to fit their intended use, purpose, operational environment, and budgetary limits. The diagram below showcases an electronic enclosure providing protection to its inner components.
Imagine an electronic device susceptible to water infiltration, accessible to children, or exposed to heat and damp conditions. Such devices could incur harm from environmental factors and present safety risks to users. To solve these problems, engineers specializing in electronics and electrical systems have created protective casings that guard against environmental exposure and other dangers linked with unprotected components, known as electronic enclosures.
A metal box is a well-designed container for sheltering, storing, and enclosing items. Aluminum and stainless steel enclosures are classified as metal boxes. Often employed as fuse boxes and outdoor electrical meter boxes, metal boxes are also utilized in business environments to encase electrical devices that supply power across the premises.
In industrial environments, electronic enclosures safeguard sensitive components from accidental impacts, debris, contamination, and dirt. They minimize damage from workplace accidents involving workers or machinery, thereby lowering the chances of severe issues like explosions or electrical failures.
The International Electrotechnical Commission (IEC) offers guidelines for selecting suitable enclosures and ratings based on their intended application. For instance, metal enclosures in telecommunications must be carefully chosen to prevent disruption or interference with information transmission. Choosing an inappropriate enclosure type can result in significant operational setbacks.
Several techniques are commonly employed in crafting electronic enclosures, as detailed below.
Computer Numerically Controlled (CNC) machining applies subtractive processes where a machine interprets CAD files to precisely guide a cutting tool. This allows precision cutting according to the specifications outlined in the CAD designs.
This process on CNC machines can be repeated as long as the program files remain accessible. This is beneficial as the same program used to create a plastic enclosure can also be used for a metal enclosure. CNC machining is ideal for producing intricate geometric designs.
Sheet metal fabrication transforms flat metal sheets, usually aluminum or steel, into metallic formations through folding and assembly processes. This method is a cost-effective and efficient solution for making electronic enclosures. Compared to CNC machining, it is usually quicker and less complicated.
Commonly used for crafting both outdoor and desktop electronic enclosures, this method's cost per part significantly drops with increased production, despite a high initial investment in sheet metal fabrication equipment.
Injection molding is a production technique that involves shaping materials like plastics, metals, glasses, elastomers, and polymers by injecting the heated substance into a mold. This approach is typically applied in producing simple enclosures such as those found in car remote controls, TV remotes, game controllers, kiosks, displays, calculators, and similar items.
3D printing is an additive manufacturing method that builds enclosures by sequentially adding material layers based on CAD files. This facilitates the creation of complex designs that may be challenging or impossible with other methods such as injection molding.
Both plastic and metal can be utilized in 3D printing, although most 3D printers operate at a slower pace compared to traditional manufacturing methods. It's beneficial for producing small batches, custom enclosures with unique designs, or for prototyping models prior to scaling up for mass production.
When developing electronic enclosures, several key elements need to be considered, including:
Product requirements define an electronic product's must-have features, functions, and operational attributes, typically detailed in a Product Requirements Document (PRD). This document offers guidelines on how the product should perform.
The PRD aids in designing an enclosure that meets these specifications. It may specify functions like heat management, moisture resistance, vibration absorption, LED visibility, and fan compatibility. By referring to the PRD, designers can determine the right materials, costs, and manufacturing processes required for the enclosure.
Optimal enclosure design requires a comprehensive understanding of internal component arrangement, involving insights into circuit design and electronic layout. For example, holes should be positioned appropriately, and spaces should be allocated for heat or ventilation if heat-sensitive components are present.
Some components should not be placed close to one another due to reasons like interference, erroneous readings, short circuits, or overheating, all of which can reduce their lifespan. Considering these factors is crucial for effective design. Consulting with or hiring experts in this field is advisable for the best results.
Once internal components are modeled, the enclosure shell can be designed by considering the component arrangement. Before choosing a manufacturing process, creating a 3D CAD model of the enclosure is crucial. This allows for any necessary adjustments or realignment before production begins.
Wall thickness is a critical factor in enclosure design. If walls are too thin, the enclosure may not withstand harsh conditions. Conversely, excessively thick walls might trap heat, potentially jeopardizing the device's functionality.
Before moving forward with the actual production of the enclosure, comparing the CAD model with the Bill of Materials (BOM) is crucial to avoid any misunderstandings. This comparison can be conducted efficiently using specialized software tools.
Electronic enclosures—also called electronic cabinets, casing, or housing—can be categorized based on the material used, their specific applications, and the intended environment. These protective cases are essential in electronics manufacturing, electrical engineering, and industrial automation, as they shield sensitive components from dust, moisture, electromagnetic interference, and physical damage. By understanding the different types of electrical enclosures, engineers and specifiers can select optimal solutions that match user needs, industry standards, and regulatory requirements such as NEMA and IP ratings.
Electronic enclosures are typically made from metals or plastics, resulting in two common types: metal enclosures and plastic enclosures. Both material groups offer unique advantages for enclosure design, environmental protection, and compliance with safety standards.
Metal enclosures are widely used in commercial buildings and industrial applications, serving as control panels, electrical junction boxes, fuse boxes, and meter boxes. These robust housings are designed to protect internal circuit boards and wiring from impacts, dust, water ingress, and electromagnetic disturbances. Metal boxes are frequently chosen for their high strength, durability, and ability to provide environmental sealing and EMI shielding. When portability is not a major concern, metal enclosures are the go-to option for stationary or high-risk settings.
In industrial automation, control rooms, and manufacturing facilities, metal enclosures help ensure reliable operation of electronics in harsh environments where exposure to dirt, debris, vibration, and chemical agents is common. By maintaining ingress protection (IP) ratings and corrosion resistance, these cabinets contribute to electronics safety and longevity.
Metal enclosures are available in a wide range of sizes, tailored to specific applications. For instance, large NEMA enclosures are installed in substations for electrical power distribution, while compact metal boxes protect circuit components in consumer electronics such as light switch fixtures. Available in box, cylindrical, and rectangular forms, these enclosures are manufactured using processes like metal stamping, punching, and precision sheet metal fabrication to meet regulatory standards and user requirements.
Aluminum enclosures are designed to safeguard electronic components from all forms of damage, including electromagnetic interference (EMI/RFI shielding), physical impacts, and corrosion. These lightweight enclosures are ideal for both indoor and outdoor use, offering strong weatherproofing against excessive heat, moisture, UV radiation, and dust. Their natural passivated surface makes them especially resistant to corrosion and oxidation. As a result, aluminum electrical boxes are popular choices for network communications, power supplies, and test instruments.
Exposure to harsh environments can cause EMI or circuit disruption, making EMI aluminum enclosures indispensable in fields like aerospace, telecommunications, automotive, and medical devices. Manufacturers often use precision CNC machining or die casting to achieve custom enclosures for handheld electronics such as remotes, portable power switches, electrical conduits, garage door openers, and automotive starters. Aluminum is also valued for enabling effective heat dissipation and thermal management, making these enclosures preferred for high-power electronics.
When designing aluminum electronic enclosures, engineers must consider critical parameters such as:
Stainless steel, composed primarily of iron and chromium (sometimes with nickel), is recognized for its exceptional corrosion resistance, hygiene properties, and longevity. Stainless steel enclosures are widely used in food processing, chemical plants, pharmaceutical labs, marine, and outdoor electrical installations. Their recyclability also makes them an eco-friendly choice. While stainless steel enclosures share similar design concepts with other metal housings, their increased material density and resistance to aggressive environments set them apart for specialized applications where sanitary environments or frequent wash-downs are required.
Plastic enclosures are molded containers specifically engineered to shield and contain sensitive electronic components. Their versatility, low weight, cost-effectiveness, and inherent insulating properties make them the top choice for portable enclosures, handheld devices, IoT products, and consumer electronics. Modern plastics allow complex shapes and subtle design details, supporting a broad range of product types and offering protection against shocks, liquids, and environmental hazards.
Plastic enclosures are often preferred for equipment that demands electrical insulation or RF transparency, such as wireless controllers, routers, digital devices, gaming peripherals, and calculators. Their ease of customization provides flexibility for engineers and product designers seeking bespoke solutions for specialized electronics projects. Plastic enclosures are found in calculators, remote controls, desktop computers, laptop computers, wireless internet controllers, coolers, and televisions.
Several factors guide the design and selection of high-quality plastic enclosures:
A wide spectrum of plastic compounds can be used for electronic enclosure manufacturing. Selection depends on application requirements such as impact resistance, flame retardancy, transparency, chemical resistance, and cost. For harsh environments or outdoor applications, high-performance plastics are favored for their mechanical strength and weather resistance.
High-density polyethylene (HDPE) excels in cold, wet, and corrosive environments due to its low temperature performance and chemical resistance. Other popular thermoplastics used in enclosures include acrylic, polyvinyl chloride (PVC), polypropylene, acrylonitrile butadiene styrene (ABS), styrene-ethylene-butadiene-styrene (SEBS), and polyamide (PA/Nylon).
Here are top options in plastic enclosure materials:
Enclosures can also be classified according to their use cases. Application-specific enclosures help meet regulatory compliance, environmental demands, and unique industry requirements.
Computer enclosures, also referred to as PC cases or computer chassis, are critical for protecting IT hardware such as servers, workstations, and mainframes from contamination and physical threat. These protective housings shield sensitive components against dust, moisture, accidental spills, and overheating—ensuring system reliability and hardware longevity. Industries as varied as information technology, aerospace, automotive, healthcare, and manufacturing all rely on specialized computer enclosures. Environmental controls and thermal management features help maintain optimal performance and safety for housed electronics.
Computer enclosures are designed to suit different operating environments, whether in residential offices, industrial sites, onboard vehicles, or even portable field equipment. While home and office computers face dust and minor impacts, industrial computer enclosures must withstand debris, temperature fluctuations, electromagnetic interference, and risks from moving machinery. Advanced enclosure designs for heavy manufacturing protect computers from harsh elements, providing enhanced ingress protection and often including cable management features for system integration.
Key considerations in computer enclosure design include:
Field and vehicle-mounted computers require ruggedized enclosures engineered to mitigate vibration, mechanical shocks, and environmental hazards common in automotive and aerospace applications. Hardened cases, vibration isolation mounts, and sealed gaskets are often used. For portable computers and laptops, lightweight yet impact-resistant plastics and alloys facilitate ease of transport without sacrificing durability.
Effective heat dissipation is another crucial factor—ventilation grids, fans, and thermal pads are designed into cases to manage temperature and prevent overheating. Cable routing, expansion slots, and modularity are also considered to facilitate system upgrades and maintenance.
Computer enclosures are crafted from various materials—metals such as aluminum and stainless steel for rugged, stationary installations, and engineering plastics for lighter, portable builds. ABS plastics and polycarbonate blends are frequently used in laptops and mobile devices for their portability and durability. Selection depends on cost, application-specific environmental risks, weight constraints, and regulatory considerations.
The National Electrical Manufacturers Association (NEMA) offers ratings that help manufacturers and users determine the protective qualities and suitability of various enclosure materials. NEMA enclosure types—including 1, 2, 12, 12K, and 13—offer varying levels of protection tailored to indoor and outdoor applications, degree of contamination, and environmental hazards. Strict adherence to NEMA and International Protection (IP) ratings ensures electronics are safeguarded across industries.
When off-the-shelf electronic enclosures do not meet the requirements for size, shape, mounting, or environmental resistance, custom enclosure solutions are developed. Custom enclosures are meticulously engineered from the ground up to fit precise dimensions, integrate specific cutouts, or address thermal, EMI, or waterproofing challenges. By optimizing the enclosure for the application, designers achieve improved safety, easier installation, and a tailored fit for unique or complex electronics assemblies.
Custom enclosures can be manufactured from a full spectrum of materials: aluminum, galvanized steel, stainless steel, polycarbonate, and advanced plastics, with configurations ranging from simple boxes to complex multi-compartment housings. While common shapes are box-like, projects often require intricate geometry, snap-fit features, or overmolded gaskets for enhanced ingress protection or wireless communication performance.
Portable enclosures are engineered for mobility, compactness, and ergonomic handling. These lightweight cases frequently protect battery compartments, LEDs, RFID modules, medical instruments, sensors, and handheld controls. Examples include car key fobs, smartphone shells, laptop chassis, computer mice, and remote controls. Their design often incorporates snap-fit lids, integrated mounts, impact-resistant plastics, and anti-slip textures for ease of daily use.
Desktop enclosures are custom-tailored to safeguard sensitive electronic instruments and PCBs located on desks or workbenches—protecting CPUs, control units, and networking hubs from ambient dust, static discharge, and accidental spills. Standard design features may include removable stands, footpads for stability, integrated cable guides, ventilation grilles, and even lockable lids for equipment security and convenience.
Display enclosures provide critical protection for monitors, touchscreens, HMI (human-machine interface) units, and operator panels. These housings shield sensitive screens against impacts, sunlight glare, dust, and liquid ingress in commercial, industrial, or public environments. Constructed with toughened glass or impact-resistant polycarbonate, display enclosures preserve display clarity while ensuring resilience to physical abuse or harsh weather. Weatherproof and vandal-resistant display enclosures are prevalent in outdoor kiosks, transportation systems, and digital signage installations.
Wall-mounted enclosures are designed to maximize space efficiency and ensure secure installation of electrical and electronic equipment—such as distribution boards, control units, and telecom hubs—on vertical surfaces. These boxes safeguard their contents from dust, heat, unauthorized access, and environmental threats. Available in metal, plastic, or composite constructions, wall-mount enclosures often include cable entry knockouts, hinged doors, and secure locking mechanisms, meeting a variety of NEMA and IP rating requirements depending on their installation environment.
Cabinet enclosures, often referred to as rack enclosures or server cabinets, provide advanced protection and cable management for electronic equipment used in audio-visual production, IT infrastructure, surveillance systems, and broadcast studios. These freestanding or wall-mounted cabinets are typically designed with removable panels, built-in cooling fans, cable organizers, and grounding systems—ensuring optimal organization, system reliability, and easy equipment access.
NEMA enclosures are engineered to comply with industry standards for electrical safety and environmental protection. They are essential in sectors such as telecommunications, utilities, public transit, electronics manufacturing, security, aerospace, sound engineering, defense, and railways. These standardized enclosures are trusted for their performance in high-stake applications like nuclear power plants, industrial control rooms, outdoor telecom, and critical infrastructure environments. NEMA defines a variety of enclosure types focused on protecting sensitive equipment from dust, liquids, corrosive agents, and unauthorized access.
NEMA enclosures are fabricated from durable materials such as polycarbonate, stainless steel (316 or 304 grades), powder-coated carbon steel, and specialized aluminum alloys (e.g., 5022). Polycarbonate is valued for its high impact resistance—about five times that of fiberglass—alongside superior insulation, heat resistance, and flame retardance. Steel and aluminum enclosures offer enhanced physical strength and corrosion resistance for demanding outdoor or industrial installations. NEMA enclosures are available in various forms, from junction boxes and floor mounts to wall-mounted cabinets and free-standing racks, ensuring compliance with project requirements and local codes.
EMI (Electromagnetic Interference) enclosures, sometimes called shielded enclosures, are engineered to prevent electronic malfunction and data loss by blocking unwanted electromagnetic or radio-frequency interference (RFI). These enclosures protect sensitive circuits and data systems by absorbing, conducting, or reflecting electromagnetic energy from external sources such as power equipment, industrial motors, lightning surges, and radio transmitters.
Applications include mission-critical communications, industrial controls, healthcare instruments, and food processing automation, where electromagnetic compatibility (EMC) and regulatory compliance (such as FCC or CE standards) are paramount. EMI enclosures contribute to device reliability, user safety, and operational continuity in challenging EMI environments.
EMI enclosures are constructed from conductive metals—including aluminum, copper, nickel, steel, and stainless steel—in both solid and perforated forms. Specialized coatings or EMI shielding foils are often applied to plastic enclosures to achieve necessary shielding effectiveness. Example use cases include microwave oven doors, shielded server racks, and electronic test equipment. EMI enclosures are standard in industries such as telecommunications, medical diagnostics, aerospace, and high-frequency electronics, where consistent electronic performance is critical for safety and regulatory approval.
The advantages of electronic enclosures vary based on the material used. Manufacturers typically use plastic and metal to fabricate enclosures, which are detailed below.
Plastic enclosures offer several benefits, including:
Magnetic interference can affect some electronic devices, but plastic enclosures virtually eliminate this risk as they do not produce magnetic fields.
Plastic, like rubber, is an insulator and does not conduct electricity. This makes plastic enclosures ideal for applications where avoiding electrical conductivity is crucial, such as covering motherboards and processors in laptops to prevent short circuits.
Plastic enclosures are resistant to water and can withstand exposure to humid environments, including water, snow, or rain, without sustaining damage. Unlike metal enclosures, they do not suffer from rust when exposed to moisture.
Plastic is an economical material, making plastic enclosures more affordable compared to metal options. This cost-effectiveness makes them a popular choice for many applications.
The lightweight nature of plastic enclosures makes them particularly suitable for portable electronic devices. Items such as car remotes, game controllers, cell phones, and chargers benefit from this characteristic.
Plastic enclosures can be easily shaped into complex forms due to their flexible chemical structure, allowing for precise fittings and custom designs.
Aluminum and stainless steel are commonly used metals for electronic enclosures. This section outlines their benefits, though these advantages extend beyond just these two metals.
When selecting an electronic enclosure, several factors should be considered:
Electronic devices are integral to many aspects of daily life and are used across various industries. These devices operate in diverse environments, which can range from harsh to mild. Designing an electronic enclosure requires evaluating the specific environmental conditions it will face, such as exposure to sunlight, dust, rain, vibrations, or chemicals. Understanding these conditions will aid in choosing the appropriate material for the enclosure.
Compliance with industry standards and regulations is crucial when designing electronic enclosures. Organizations like the International Electrotechnical Commission (IEC) and various government bodies set guidelines and specifications that must be adhered to. These standards define the necessary product specifications, and ensuring conformity is essential for creating a functional and compliant enclosure.
Understanding the thermal dynamics of the electronic components being protected is vital. It's important to know the amount of heat generated by the internal components, such as regulators, resistors, LEDs, and power circuits. While plastics are effective insulators, they may melt under high temperatures, so they are best suited for low-heat applications. Metals, on the other hand, are more suitable for enclosures dealing with high heat dissipation.
Today, various materials can be used for enclosures, with choices influenced by factors like cost, weight, size, and aesthetics. Acrylic is a popular and cost-effective option due to its lightweight, impact resistance, and flexibility. Polycarbonate is also favored for its thermal stability and impact resistance. Other materials such as aluminum, glass, copper, and steel are used depending on cost considerations and specific application needs.
For a system to be electromagnetically compatible, it must meet specific characteristics that ensure proper operation without interference.
The diagram below illustrates how emissions are distributed in electrical and electronic devices.
The electronic industry is fast-growing, and this is evident especially when we look at the portable electronic devices that almost the whole world has been exposed to. We use devices like cell phones, radios, microwaves, remote control, laptops, etc on a daily basis and the information provided in this article will give either the consumer or the manufacturer of these devices some insight on how best to interact with these electronic enclosures.
NEMA enclosures are boxes that are designed to protect electrical components from the surrounding environment. Depending on the specific NEMA rating, devices in a NEMA enclosure are protected in...
EMI shielding is a technique of creating a barrier that prevents leakage of strong electromagnetic fields that can interfere with sensitive devices and signals. They can be installed to isolate the electromagnetic field source or as an enclosure of the device that needs protection...
Precision sheet metal fabrication is a common manufacturing process where the structure of a metal workpiece is cut, bent, and assembled by machining. There are any number of operations that are performed in the creation of a finished sheet metal product...
Radiofrequency (RF) shielding is the practice of blocking radiofrequency electromagnetic signals that cause radio frequency interference (RFI). RFI can disrupt the electrical circuits of a device from working normally...
Secondary manufacturing processes, or fabrication, work on products from primary processes to create a metal part or structure that is suitable for end-use. In these processes, semi-finished metal products are reshaped and joined...