RF Shielding
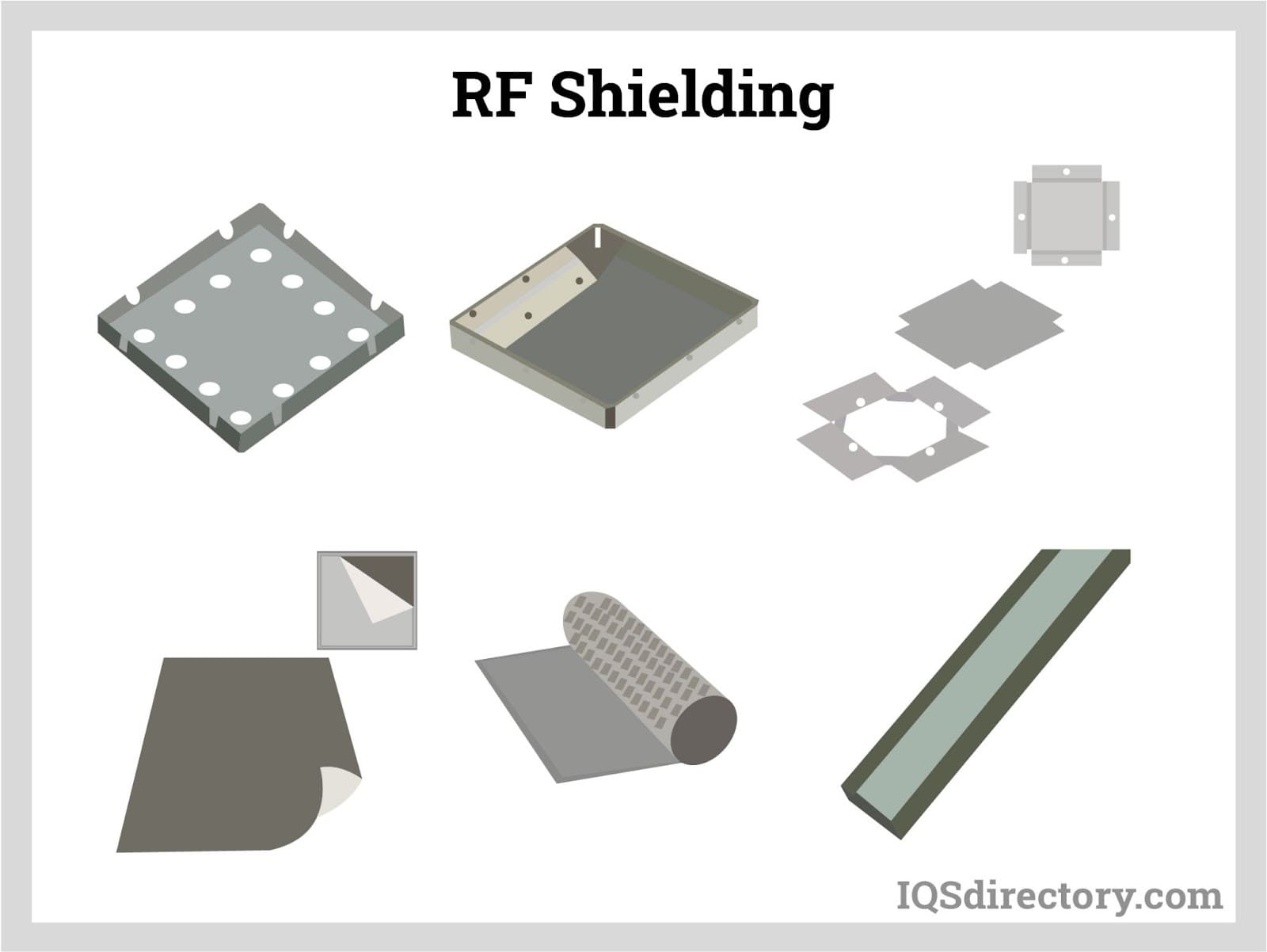
Radiofrequency (RF) shielding is the practice of blocking radiofrequency electromagnetic signals that cause radio frequency interference (RFI). RFI can disrupt the electrical circuits of a device from working normally...
Please fill out the following form to submit a Request for Quote to any of the following companies listed on EMI Shielding .
This article provides a complete guide to EMI and EMIF shielding.
Read further to learn more about:
EMI shielding refers to creating a protective barrier to stop strong electromagnetic fields from leaking out and interfering with delicate devices and signals. Such shielding can be used to separate the electromagnetic field's origin or as a protective enclosure around the device requiring safeguarding. Electromagnetic interference (EMI), also known as radio frequency interference (RFI), is a common issue for many electronic devices, as it can degrade circuit performance and even lead to device malfunctions. Because modern electronics often function with minimal voltages and currents, they are especially susceptible to disruptions caused by electromagnetic fields.
Electromagnetic interference (EMI) describes the unwanted coupling of signals from one system infiltrating another. EMI consists of three essential elements: the source, the transmission path, and the receiver. The source is the origin of interference, which could be natural (e.g., lightning, auroras, cosmic microwave background, solar flares) or man-made (e.g., cellular networks, AM/FM radio waves, power lines, measurement, and control devices). The receiver, or the affected device, experiences distortion due to the interference. The transmission path is the medium over which signal coupling happens, and this can occur in four distinct modes.
EMI can be categorized by the interference duration. The two primary types are continuous and pulse interference. Continuous interference takes place when the source continuously releases disruptive signals, typically of low energy and frequency, such as radio waves, electromagnetic leaks from machinery, and power lines. Conversely, pulse, intermittent, or transient interference occurs briefly, often lasting less than one AC cycle (roughly 16.67 milliseconds), defined by high bursts of energy, and may be repetitive or irregular. Repetitive interference is generally man-made and predictable in amplitude and duration, while random events could be artificial or natural, like lightning, power spikes, or electrostatic discharges.
Another method for EMI classification is by disturbance bandwidth, which includes narrowband or broadband. This distinction depends on whether the signal's bandwidth is smaller or larger than the receiver's resolution bandwidth. A narrowband disturbance has a bandwidth not exceeding the receiver's bandwidth, whereas a broadband disturbance surpasses that bandwidth.
With rapid technological advancements, a plethora of electronic devices floods the market, designed for convenience. Nonetheless, these devices could interfere with one another if not adequately shielded. EMI shielding is crucial to confine a device’s electromagnetic energy from affecting nearby equipment and to shield the device itself from external interference. Every electronic gadget emits some level of electromagnetic energy and remains vulnerable to EMI threats.
Recognizing the nature of EMI demonstrates its potential varying impacts on surroundings. It affects electronics through direct contact (conducted EMI), near contact without physical touch (capacitive and magnetic EMI), and even over significant distances (radiated EMI). As the information age advances, growing reliance on electronics for processing and communication contributes to electromagnetic pollution, compounded by electrical distribution disturbances and natural events like lightning and solar flares. Here are some impacts of EMI:
To mitigate electromagnetic interference issues, global entities have set forth electromagnetic compatibility (EMC) standards. EMC ensures device functionality amid an electromagnetic environment, avoiding causing or receiving undesirable interference. Standards are developed by international organizations like the International Special Committee on Radio Interference (CISPR) of the International Electrotechnical Commission (IEC) and the International Organization for Standardization (ISO). Within the United States, EMC standards fall under the jurisdiction of the Federal Communications Commission (FCC).
Many machines are designed for producing EMI (Electromagnetic Interference) shielding, crucial in today's society for protecting electronic systems across various industries, including telecommunications, aerospace, medical devices, and automotive. These machines are essential for manufacturing components that ensure reliable and safe operation by mitigating electromagnetic interference. Below, we explore leading brands of machines available in the United States and Canada used for creating EMI shielding materials, highlighting specific models and their unique features or components:
Features: Chomerics offers manufacturing equipment for producing EMI shielding materials such as conductive gaskets, films, and coatings. Their equipment includes various machinery like extruders, calenders, coaters, and curing systems, enabling precise control over material thickness, conductivity, and other properties. It supports different manufacturing processes including extrusion, coating, and lamination, designed for high-volume production and customization of EMI shielding materials.
Features: Schaffner Group offers manufacturing systems tailored for producing EMI shielding solutions such as filters, contact strips, and ferrites. Their systems encompass machinery for metal stamping, injection molding, and assembly, providing precise tooling and production capabilities for high-quality EMI shielding components. Automation features are incorporated to ensure efficient and cost-effective manufacturing processes. Schaffner Group's manufacturing systems are designed to meet industry standards and fulfill customer-specific requirements.
Features: Integrated Microwave Corporation specializes in equipment for manufacturing EMI/RFI shielding materials like conductive foams and absorbers. Their production equipment includes laminating machines, die-cutting systems, and custom tooling solutions, enabling precise fabrication and customization to meet specific requirements. The equipment supports various manufacturing processes such as lamination, cutting, and shaping, ensuring high-quality EMI/RFI shielding materials with consistent performance.
Features: JEMIC Shielding Technology provides a range of machines for manufacturing EMI shielding materials, such as conductive fabrics, tapes, and gaskets. Their equipment includes coating systems, cutting machines, and sewing machines, allowing for precise coating, cutting, and assembly of EMI shielding materials. These machines offer flexibility in material selection, thickness, and configuration, designed for efficient production and customization of EMI shielding products.
Features: Leader Tech Inc. offers equipment for manufacturing EMI shielding materials such as conductive elastomers, vents, and thermal pads. Their equipment lineup includes mixing and dispensing systems, molding presses, and curing ovens, enabling precise material formulation, molding, and curing processes to ensure consistent EMI shielding performance. It also provides customization options for material properties, shapes, and sizes, ensuring high-quality EMI shielding materials with reliable performance.
Please note that specific model availability and features may vary. For the most up-to-date information on models that meet your requirements, it is advisable to contact the manufacturers or their authorized distributors.
EMI shielding is a key method for achieving Electromagnetic Compatibility (EMC), alongside grounding, filtering, and bonding techniques. It involves constructing enclosures using suitable materials, structures, and forms to modify the paths of undesired electromagnetic waves entering or exiting equipment. This modification is achieved through absorption or reflection of electromagnetic waves using conductive or ferromagnetic materials.
An electromagnetic wave comprises electric and magnetic components that travel at the same frequency and are perpendicular to each other. Conductive materials block the electric component, while materials with high magnetic permeability block the magnetic component. Since these components cannot exist without each other, shielding one is sufficient. EMI shielding involves various mechanisms to filter out these components. Below are the three mechanisms of EMI shielding:
The primary mechanism of EMI shielding is reflection, which attenuates the electric component of EMI. To achieve EMI reflection, the shielding material must have mobile charge carriers, making conductivity essential. The incoming electromagnetic wave interacts with these mobile charge carriers, causing them to flow and redistribute along the conductor, creating an opposing electromagnetic field. This field cancels out the external magnetic field. Higher conductivity in the material enhances its shielding effectiveness.
A challenge with this mechanism is that any enclosure discontinuity larger than the wavelength of the external electromagnetic field can compromise shielding. Therefore, enclosure designs minimize the sizes of holes and openings. However, this approach becomes impractical at higher frequencies. For high-frequency EMI, the solution lies in employing filtering devices to mitigate electromagnetic interference effectively.
Another challenge is the skin effect, observed in AC circuits. In AC flow through a conductor, charges accumulate at the surface or top-most layers, increasing current density in those areas. This reduces conductivity and affects shield performance, especially in high-frequency electromagnetic waves. One solution is to increase the conductor's surface area, effectively enhancing the conducting cross-section. Another approach is electroplating the surface with highly conductive materials like silver to mitigate this effect.
This is the secondary mechanism of EMI shielding that targets the magnetic component of EMI. To achieve EMI absorption, the material must possess electric and magnetic dipoles, typically characterized by high dielectric constant and high magnetic permeability. When subjected to an external magnetic field, these materials allow magnetic field lines to pass through, effectively absorbing them. Enclosures made from such materials create a pathway for absorbing magnetic and electric field lines internally. However, a drawback is their lower conductivity, making them less effective at shielding against the electric component of electromagnetic waves.
Another aspect of the absorption mechanism involves weakening the incoming electromagnetic wave through eddy currents. This occurs when the wave oscillates at high frequencies, inducing currents within the conductor. These eddy currents generate their own magnetic fields that oppose the external magnetic field. Materials with high electrical conductivity are capable of generating stronger eddy currents.
Another mechanism is observed in composite materials with large interfacial areas or porous structures on their surfaces. Shielding is achieved through multiple reflecting boundaries that reflect the electromagnetic wave, resulting in the scattering of electromagnetic waves.
The preceding section discussed the mechanisms of EMI shielding and the essential material properties needed to achieve it. Two primary properties crucial for EMI shielding are electrical conductivity and magnetic permeability. Below are some materials that exhibit these properties:
Metals: Metals are the first choice for cheap and simple EMI shielding. Their properties such as electrical conductivity, magnetic permeability, strength, and ductility make them suitable for shielding structural materials. Silver has the best electrical conductivity with good corrosion resistance, making it the most efficient electric field attenuator. The downside of using silver is its relatively high cost compared to other metals, which is why it is used as an alloying component or surface coating through electroplating. Balancing the cost and shielding efficiency, copper and aluminum are the most widely used metals for EMI shielding. The electrical conductivity of copper is almost the same as silver, while that of aluminum is 40% less.
Carbon steel alloys such as mild carbon steel and ferritic stainless steel, and iron-nickel alloys such as Mu-metal, Permalloy, and Supermalloy are common materials used for magnetic shielding. The most popular is Mu-metal which has a relative permeability of 100,000 at 1kHz.
Carbon Allotropes: Carbon allotropes are forms of carbon, such as exfoliated graphite, graphene, carbon fibers, and carbon nanotubes. They are used as filler materials for EMI shield composites. They are effective filler materials due to their intrinsic strength and conductivity. They mainly operate through the multiple reflection mechanism of shielding. Exfoliated graphite is widely used as EMI shielding gaskets due to its flexibility and ability to flow on the surface irregularities of the sealing surfaces. They have a highly porous structure that promotes EMI absorption. Graphene, carbon fibers, and carbon nanotubes are used as filler materials due to their high aspect ratio. They are commonly embedded in polymers, ceramics, cement, and metals to create rigid structures. For high-frequency shielding applications, graphene and carbon nanotubes are mostly used because the dimension of these materials is lesser than the skin depth. This makes them better conductors than metals in the GHz range.
Intrinsically Conducting Polymers (ICPs): These are special polymers that can conduct electricity within themselves without the need for additional conducting materials. They are desired because of their light weight and processability. ICPs can conduct electricity between atoms due to the conjugated bonds (alternating single and double bonds). This enables the delocalization of π-electrons (loose electrons), which act as mobile charges. The electric conducting property of ICPs can be modified through doping or de-doping. Popular ICPs are polyaniline (PANI) and polypyrrole (PPy). The use of ICPs is still under development since several problems exist concerning their mechanical and chemical stability. They are more extensively used as components to composites containing metal nanoparticles and carbon filaments.
Foam: The type of foam used for EMI shielding is carbon foam, which is lightweight, high temperature tolerant, and has adjustable thermal and electrical properties. The two types of carbon foam are graphitic and non-graphitic. Non-graphitic foams are stronger, can be used as a thermal insulator, and cost less.
Graphitic foam is made from petroleum, coat tar, or synthetic pitch and is more expensive to produce. Due to the expense of production, graphitic foam is in limited supply but is widely used for EMI shields. Used as an EMI shield, it is capable of shielding radio frequencies from 100 Mhz up to 20 GHz without any metal component.
Foam is an ideal material for EMI shielding due to its flexibility and adaptability. These characteristics have made it a popular choice for EMI shields. Additionally, foam lasts longer in extreme and harsh conditions, weighs very little, and does not rust or corrode. Foam is the most environmentally friendly of the many materials used to make EMI shields.
Fabric: Although EMI fabric may seem to be traditional fabric, it is used like textile fabric in EMI protection and has physical properties like conventional fabric. The substrate of EMI fabric is nylon or polyester that has been interwoven with metal. The flexibility of EMI fabric makes it possible to engineer it so that it can be effective in a wide variety of conditions and applications.
EMI fabric is not the strongest form of EMI protection, but it is ideal for conditions where a moderate amount of protection is required. Since EMI fabric has a metal content, it tends to get surface corrosion in certain conditions.
EMI shielding is often regarded as the most cost-effective method for achieving EMC compatibility as it reduces the reliance on intra-equipment devices to manage undesired signals. Effective EMC through shielding depends on two key factors: the structural or form design and the choice of materials. A basic EMI shield design example is a Faraday cage constructed from conductive materials like copper. The design of an EMI shield varies based on the electromagnetic environment within which the equipment must operate reliably. Below are some considerations for designing an EMI shield:
For uneven surfaces, it is best to use an EMI shielding gasket. EMI shielding gaskets are commonly used for enclosures with removable panels, drawers, and covers. The gaskets fill in the gaps to provide continuous electrical contact between surfaces. The following properties must be considered in selecting an EMI shielding gasket:
Shielded cables are used for signal lines penetrating shielded enclosures. These cables are grounded to the outer shield of the enclosure.
EMI shielding components come in various forms depending on the application. Below are some common types of EMI shields found in the market:
Solid Enclosures: Typically, metallic cases have sufficient rigidity to contain and support the device. Thus, it serves two functions. First, it acts as structural support or frame to the unit. Second, it prevents electromagnetic waves from getting into or out of the system. The enclosure is grounded so that any stray current will be diverted to ground, which minimizes the risk of electric shock.
Wire Mesh and Screens: These are shielding materials with penetrations or discontinuities less than the expected wavelength of the EMI. They function similarly to solid enclosures, but with the added benefit of allowing ventilation, especially for electronics that generate heat. Moreover, using wire mesh creates a translucent characteristic to an enclosure, which is useful for see-through enclosures and displays. Since the discontinuities need to be very small, they are manufactured through high-resolution processes such as photochemical etching and printing.
Gaskets and O-rings: As mentioned before, the enclosures must be fully continuous without any penetrations so as not to defeat the purpose of EMI shielding. In reality, this is not the case since all enclosures must have access to the components inside. Thus, there is a continuity problem with the removable parts of the enclosure. EMI shielding gaskets and O-rings solve this problem by being able to absorb EMI, and at the same time, have the flexibility and elastic characteristics of ordinary sealing materials.
Cable Shielding: These are tapes or wire braids that cover the insulated conductor of a power or instrument cable. When used in a power cable, this prevents creating electromagnetic waves that can affect nearby electronic components. When used in instrument cabling, the main function is to prevent external electromagnetic waves from distorting the signal that flows through the cable. The shielding is grounded so that any leaking current or stored electricity through parasitic capacitance is diverted to ground.
Coatings: EMI shielding materials can also be coated through painting, spraying, dispensing, and electroplating. These are typically used in lightweight applications, such as mobile devices, where metallic shielding is impractical.
Radiofrequency (RF) shielding is the practice of blocking radiofrequency electromagnetic signals that cause radio frequency interference (RFI). RFI can disrupt the electrical circuits of a device from working normally...
Acid etching, also known as chemical etching or photo etching, is the process of cutting a hard surface like metal by means of a specially formulated acid for the process of etching in order to allow for the creation of a design onto the metal...
Chemical milling is a subtractive machining process that removes material from a workpiece to achieve a desired shape. Unlike aggressive milling methods that depend on sharp tools to produce a design, chemical...
Electronic enclosures are box-like structures that are designed to protect, contain, and enclose electronic components such as switches, relays, printed circuit boards (PCB), integrated circuits, power supplies, processors, etc...
Gaskets are a type of mechanical seal that inhibits leakage by filling the gap between static mating surfaces. It takes advantage of the compressive force that drives the gasket material to plastically flow between the...
Gaskets are seals that are mechanically made to prevent either process fluids from escaping or contaminants from entering the delicate areas. Each given system has its best suited gasket, and it is critical to make the right...
The head gasket is a motor engine component that seals the combustion part of the engine so that oil and the motor coolant circulate. The head gasket also seals the combustion chamber inside the engine...
Metal etching is a metal removal process that uses various methods to configure complex, intricate, and highly accurate components and shapes. Its flexibility allows for instantaneous changes during processing...
NEMA enclosures are boxes that are designed to protect electrical components from the surrounding environment. Depending on the specific NEMA rating, devices in a NEMA enclosure are protected in...
Photochemical etching, also known as photochemical machining or metal etching, is a non-traditional, subtractive machining process in which photographic and chemical techniques are used to shape the metal workpiece...
Rubber gaskets are elastic components used for mechanically sealing the microscopic gap between two mating surfaces or joints. Examples of these surfaces are flange faces of piping and fittings, mating surfaces of an...