Expansion Joints: Types, Manufacturing and Benefits
Introduction
This article will provide a detailed discussion regarding expansion joints.
It is expected that after reading this article, one should better understand:
- Expansion Joints, What They Are, How They Work, Common Materials Used in Expansion Joints, and Considerations in Selecting an Appropriate Expansion Joint
- How Expansion Joints Are Manufactured
- Types of Expansion Joints
- Benefits and Applications of Expansion Joints
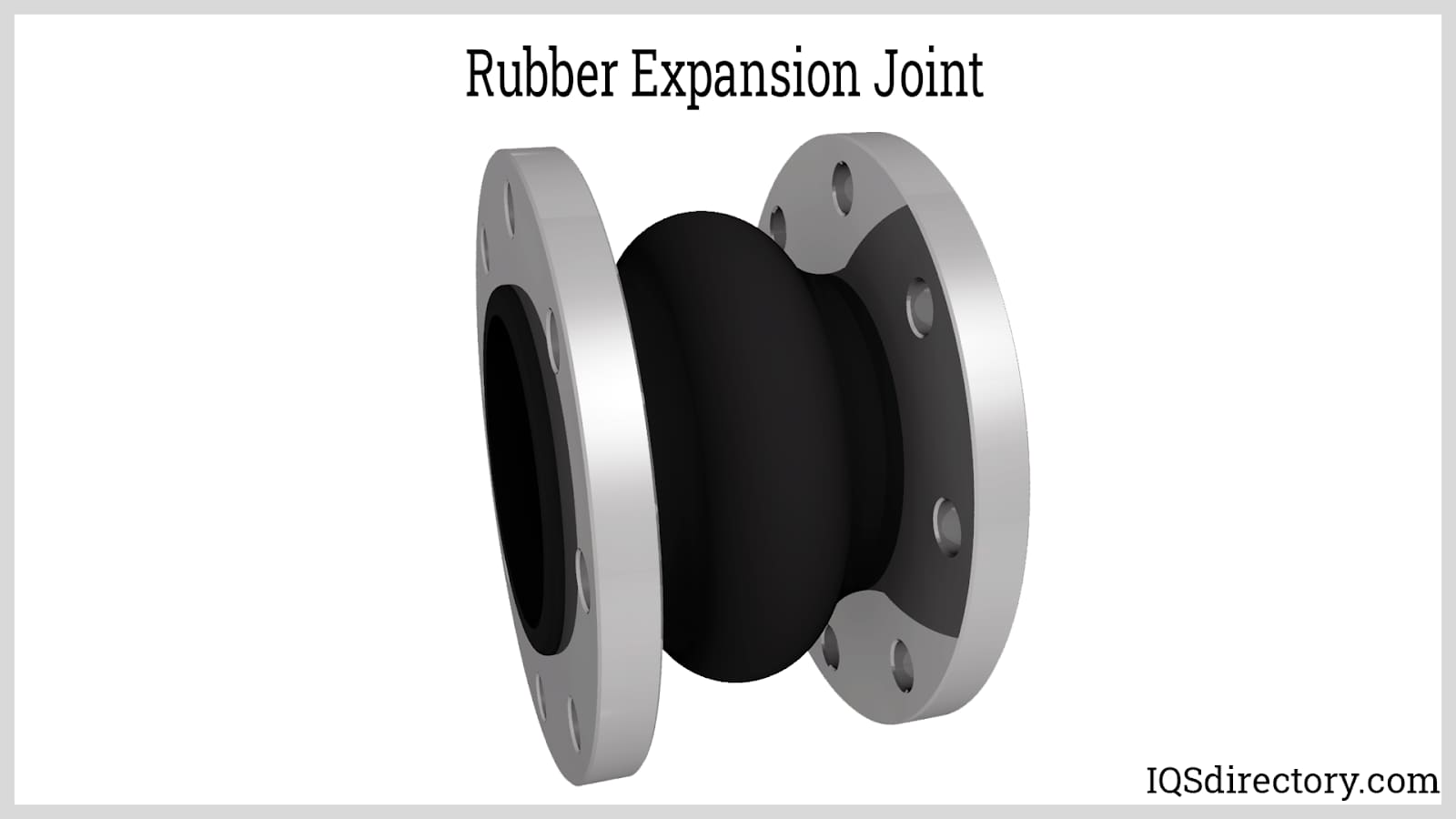
Chapter One: What is the overview of expansion joints?
Expansion joints, as the name implies, are designed to accommodate movement. They are employed to manage the movement of pipes, ducts, and other pipeline components caused by thermal and mechanical vibrations. These vibrations often result from varying temperature conditions. Expansion joints are engineered to expand with rising temperatures and contract when temperatures decrease, thereby providing secure support to the piping systems. Additionally, mechanical components can sometimes be integrated to allow for rotational and linear motion.
An expansion joint is a connecting element between two structures that facilitates their movement during thermal expansion and contraction. Expansion refers to the increase in size or volume due to a rise in temperature. As the temperature increases, the average kinetic energy of the atoms rises, causing them to vibrate more rapidly, which leads to the material's expansion. Plumbing systems use expansion joints to absorb such shocks and vibrations.
Expansion joints also offer advantages such as noise reduction and alignment compensation. While most expansion joints are designed to handle the expansion and contraction of connected structures or pipes, some are specifically engineered to handle extreme external thermal expansions in hot environments, where temperature fluctuations from the surroundings can impact the piping system.
Standard materials for expansion joints include metal (usually aluminum), rubber, and braided material. Braiding is the mechanical intertwining of three or more yarns so that no two threads are wrapped around one another. Since the braids are continuous, the load may be distributed equally throughout the structure. Braids can be made from either fiber or stainless steel. These adaptable connectors are made of stainless steel bands that have been braided and corrugated and are wrapped around a rubber or elastomer hose.
Moreover, expansion joints can help correct misalignment, reduce noise, and alleviate anchor tension. They act as a connection between two pipes, helping to absorb and manage movement. Their design varies to suit specific applications. Expansion joints are essential for preventing structural damage in systems prone to expansion or contraction, such as plumbing pipes, machinery, and hydraulic or pneumatic systems. For example, an expansion joint can maintain its seal and position effectively even when there is movement between the connected surfaces.
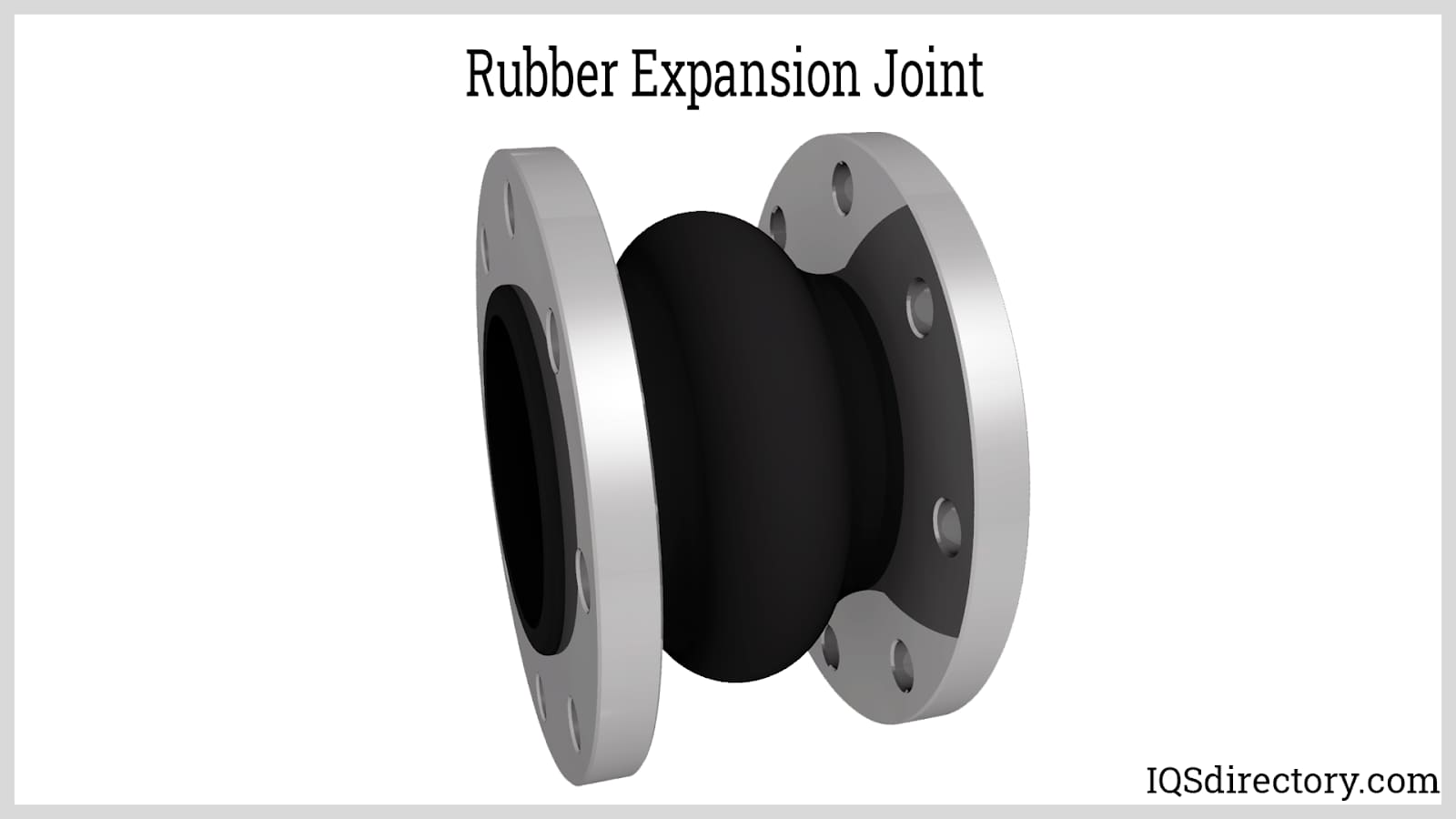
How They Work
Metal expansion joints are used to accommodate thermal expansion and relative movement in pipes, containers, and machinery. They can feature one or more metal bellows, connectors at both ends, and sometimes tie rods, depending on their application. The bellows, which can be made from rubber or metal, are flexible components that absorb movement within the pipe system. They expand and contract as temperatures change, with metal bellows compressing to manage movement and reduce stress on the pipe. These bellows can be constructed from materials such as nickel alloys and stainless steel.
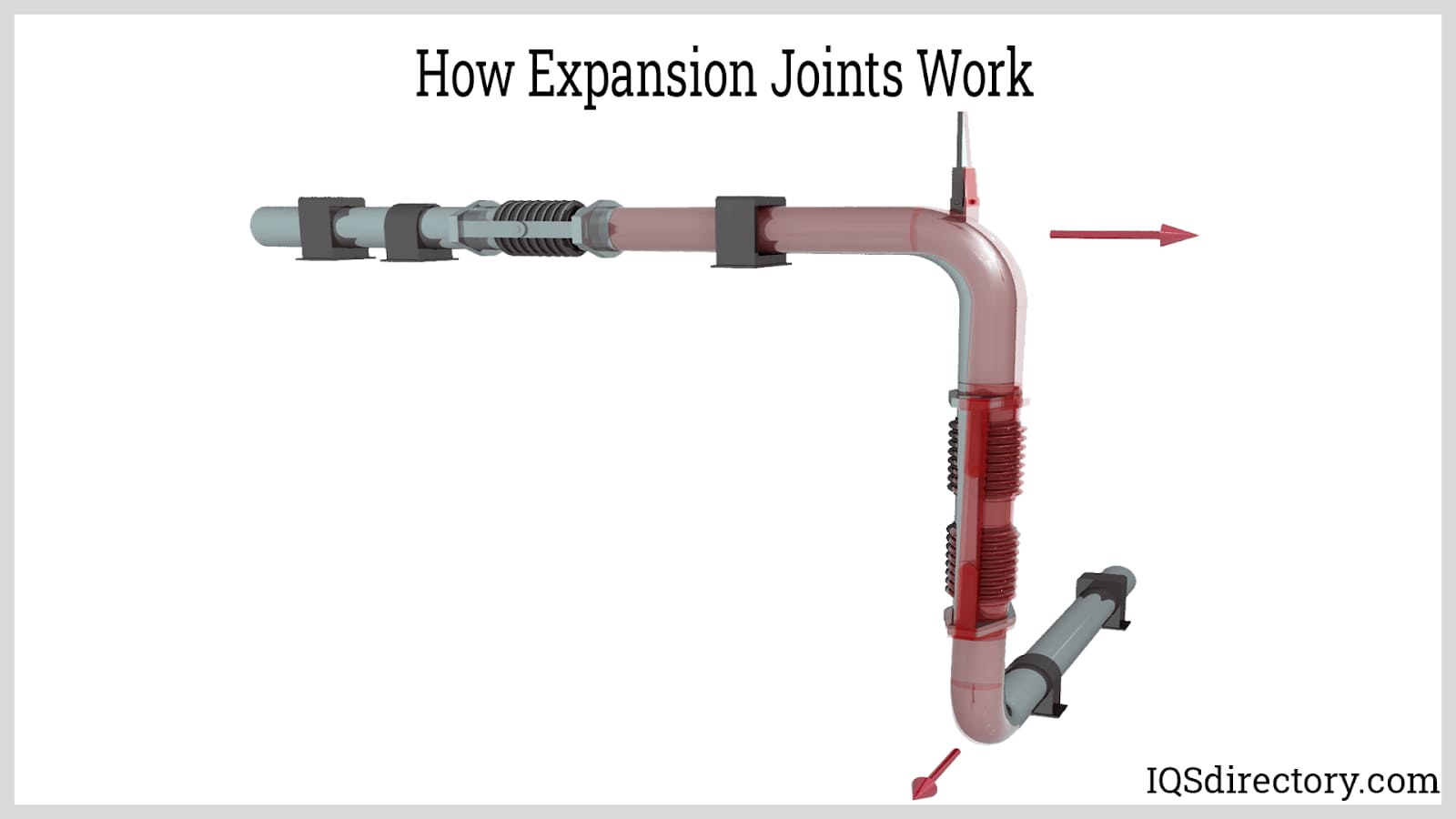
Expansion joints find application across a range of industries, including energy production, paper manufacturing, chemicals, water treatment, oil, and gas. They are utilized in any situation involving pipelines and where thermal or vibrational movement is present.
Common Materials Used in Expansion Joints
Metal
Metal expansion joints are ideal for applications involving significant thermal expansion. As temperatures increase, these joints contract to accommodate movement, thereby reducing stress on the anchors and the pipe.
Rubber
Rubber expansion joints excel in absorbing vibrations and shock waves, making them suitable for thermal expansion applications. They are effective in protecting equipment such as pumps by minimizing noise and vibration transfer. Additionally, they act as shock absorbers to mitigate damage from seismic activity and pressure surges.
Braided Stainless Steel
Braided stainless steel hoses with flexible or metal liners are more accurately described as flexible connectors rather than expansion joints. They are particularly effective in applications requiring vibration damping or addressing pipe misalignments in high-pressure and high-temperature conditions.
Factors to Consider When Selecting an Expansion Joint
Since expansion joints are often employed in demanding environments such as steel, power, pulp and paper, mining, and chemical industries, careful selection, installation, and maintenance are crucial. This ensures reliability, optimizes performance, and extends service life.
Pipe Size (in.) | Std Face-to-Face (in.) | Axial Com-pression (in.) | Lateral Deflection (in.) | Angular Rotation (deg.) | Torsional Rotation (deg.) | Std Working Pres. (psi) | Min. Burst Pres. (psi) | Vacuum Rating (in. Hg) |
---|---|---|---|---|---|---|---|---|
2 | 6 | 3/4 | 1/2 | 14.5 | 3 | 165 | 660 | 30 |
2 1/2 | 6 | 3/4 | 1/2 | 11.5 | 3 | 165 | 660 | 30 |
Application Field
The application area is the primary consideration when selecting an expansion joint. Expansion joints are used across various industries, so identifying the specific application is the first step in the selection process. Common uses include plumbing, piping, and construction.
In piping systems, expansion joints accommodate the expansion of pipes caused by fluid pressure or temperature changes. In plumbing systems, they absorb shock and vibration while also reducing operational noise.
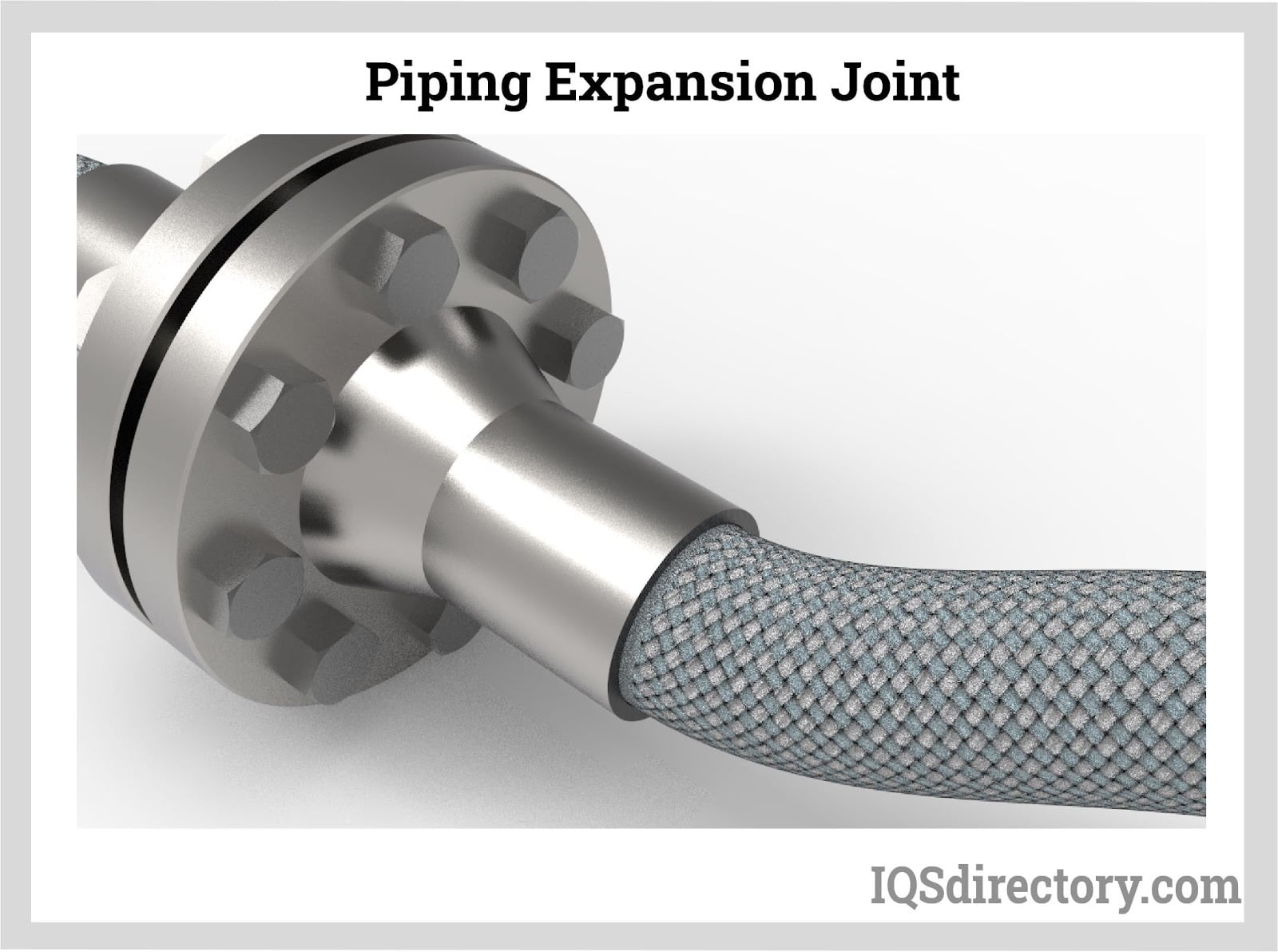
An expansion joint in construction serves as a gap or separation in a building structure designed to alleviate stress on materials due to structural movement. Key factors contributing to movement at expansion joints in buildings include temperature variations causing thermal expansion and contraction, seismic shifts from wind forces, dynamic load bending, and direct impact forces.
Piping Scheme
Before addressing the expansion junction, ensure that nearby pipes and equipment follow sound piping engineering practices. For the expansion joint to function properly, the placement and design of anchors, guides, and supports are crucial. Pipe anchors secure pipes to a fixed location to prevent movement. Pipe guides allow movement in one direction while restricting it in others. Pipe supports transmit the pipe’s weight to the supporting structures.
Placement
The positioning of the expansion joint is critical for optimal performance. Proper planning will ensure the joint is placed to allow adequate movement, sufficient ambient cooling, and easy accessibility.
Joint Motion
Expansion joints and pump flexible connectors absorb axial, lateral, and angular pipe movement and vibration. It is essential to accurately calculate these movements for the expansion joint to ensure longevity. Excessive stress on the joint may lead to premature failure, and some designs are better suited for specific types of movement.
Expansion joints used in construction may need to accommodate horizontal, vertical, or multidirectional movements. They should also handle shear movement and provide protection from degradation caused by such interactions.
Media Flow
Design considerations often depend on the air or liquid flowing through the expansion joint. Flow liners or insulation can offer additional protection against contaminants or abrasives. The medium's nature is a critical factor in material selection. Condensation inside an expansion joint can lead to chemical attacks on the materials. Improper support may cause turbulent flow, fluttering, and reduce the joint's lifespan.
Material Examination
Expansion joints should meet material certification standards to ensure compatibility with the pumped fluid. The material selection process is crucial. Choosing inferior materials can result in costly replacements and downtime.
Temperature
Accurate temperature data is vital when assessing application needs. Both internal and external temperatures influence material choice, insulation, and frame design. The expansion joint must withstand the system's highest operating pressure at the specified temperature.
Pressure
The design pressure often determines the materials or reinforcements for the expansion joint. Reinforced fiberglass fabric and metal bellows can handle higher pressures than reinforced molded rubber. Pulsations or pressure changes, if not managed, can shorten the joint's lifespan. Therefore, it is important to consider pulsing or shock pressure when using connectors at discharge points.
Installation
Many expansion joints come pre-assembled and can be easily installed between duct flanges. Larger sizes may need to be shipped in sections and assembled on-site. It is important to account for any obstacles or interferences near the expansion joint. Proper positioning and accessibility of mounting flanges are crucial for effective installation and future maintenance or replacement.
Finish Type
Various finishes and materials can be used on expansion joints. Consider factors such as color, powder coating, and the use of stainless steel or brass caps when selecting an expansion joint.
Maintenance of Expansion Joints
A well-sized, designed, and installed expansion joint generally requires minimal maintenance, but routine inspections are highly recommended. Inspections can identify issues such as leaks, corrosion, or blisters and cracks in rubber joints. While inspection does not guarantee that damage will not occur, it significantly reduces the likelihood of potential harm.
Chapter Two: How Expansion Joints are Manufactured?
Tube to Bellow Construction
The first step in manufacturing metal bellows involves creating the corrugated tubes. Initially, precision shearing is employed to cut the coil or sheet material to the desired dimensions. Following this, the sheared sheets are rolled into tubes, ensuring they are accurately round to fit over the dies used in bellows production. Each tube then undergoes longitudinal seam welding using an automated seam welder, a vital process for forming the bellows.
Forming Technique
There are various ways to corrugate the tube; mechanical die-forming and hydroforming are the most popular methods. On the bellows forming machine, the tube is positioned over the die. A metal forming technique called hydroforming uses pressurized liquid medium to create specific workpiece shapes out of tubular or sheet metal. A hollow aluminum tube is put into a negative mold that mimics the desired bellow's shape in order to hydroform aluminum or other metals into bellows. The aluminum tube is then filled with fluid at extremely high pressure by high-pressure hydraulic pumps, which forces it to expand until it fits the mold. After that, the hydroformed bellow is taken out of the mold. The machine is programmed to create the correct engineered diameter of bellows corrugation and to ensure that the overall joint was also made in the correct shape. The additional components of the joint are created during the shaping process.
Re-Rolling Process
In the secondary phase, the metal bellows are shaped and cold worked to match the exact specifications set by the design engineer. Cold working involves deforming the metal below its recrystallization temperature, which enhances the strength and dimensional accuracy of the bellows. However, some less scrupulous manufacturers may skip this step and instead use a press to compress the bellows to size, which can compromise the bellows' performance.
Welding
For multi-ply bellows, overlapping spot welds are continuously applied at the bellows' neck, a process called roll seam welding. This method involves assembling the bellows first, followed by welding them to the other components of the junction.
Chapter Three: What are the different types of expansion joints?
Request a free catalog using the form below to explore your options and gain detailed insights:
Axial Expansion Joints
The expansion joint's length will either extend or contract to accommodate axial movement, which affects the pipe system along its longitudinal axis. Axial expansion joints are designed to handle both longitudinal extension and compression. In a piping system, if axial expansion joints are installed without restraint bars, the pipeline requires fixed points and proper anchors to counteract the forces generated by the bellows. A free length refers to the expansion joint's length when it is in its neutral state. To maximize cycle life, axial expansion joints should be installed under pre-tension conditions, also known as cold pull. These joints are used to manage the thermal expansion of a straight pipe section between two fixed points, with the length of the pipeline to be compensated defined by the distance between these points. Larger movements can be accommodated by pre-tensioning or by installing multiple expansion joints in the section. Axial expansion joints capable of absorbing large movements may include one or more bellows in a single unit. While axial expansion joints can handle minor lateral and angular deflections and installation tolerances depending on their nominal diameter and length, they should be used primarily for their intended purpose to avoid reducing their service life.
Types of Axial Expansion Joints
Single Expansion Joints
Single expansion joints consist of bellows components, end connectors such as pipe ends, flanges, weld necks, and optional elements like collars, liners, and coverings. The bellows can flex in various directions or planes depending on the pipe's movement. While single expansion joints offer a practical design solution, it is essential for the piping alignment to match the direction of the bellows movements. It is not feasible to expect the pipe expansion joint to control pipe movement on its own. The piping system must be directed and constrained to ensure that movement occurs as required, particularly if the analysis indicates that the expansion joint will need to accommodate axial compression.
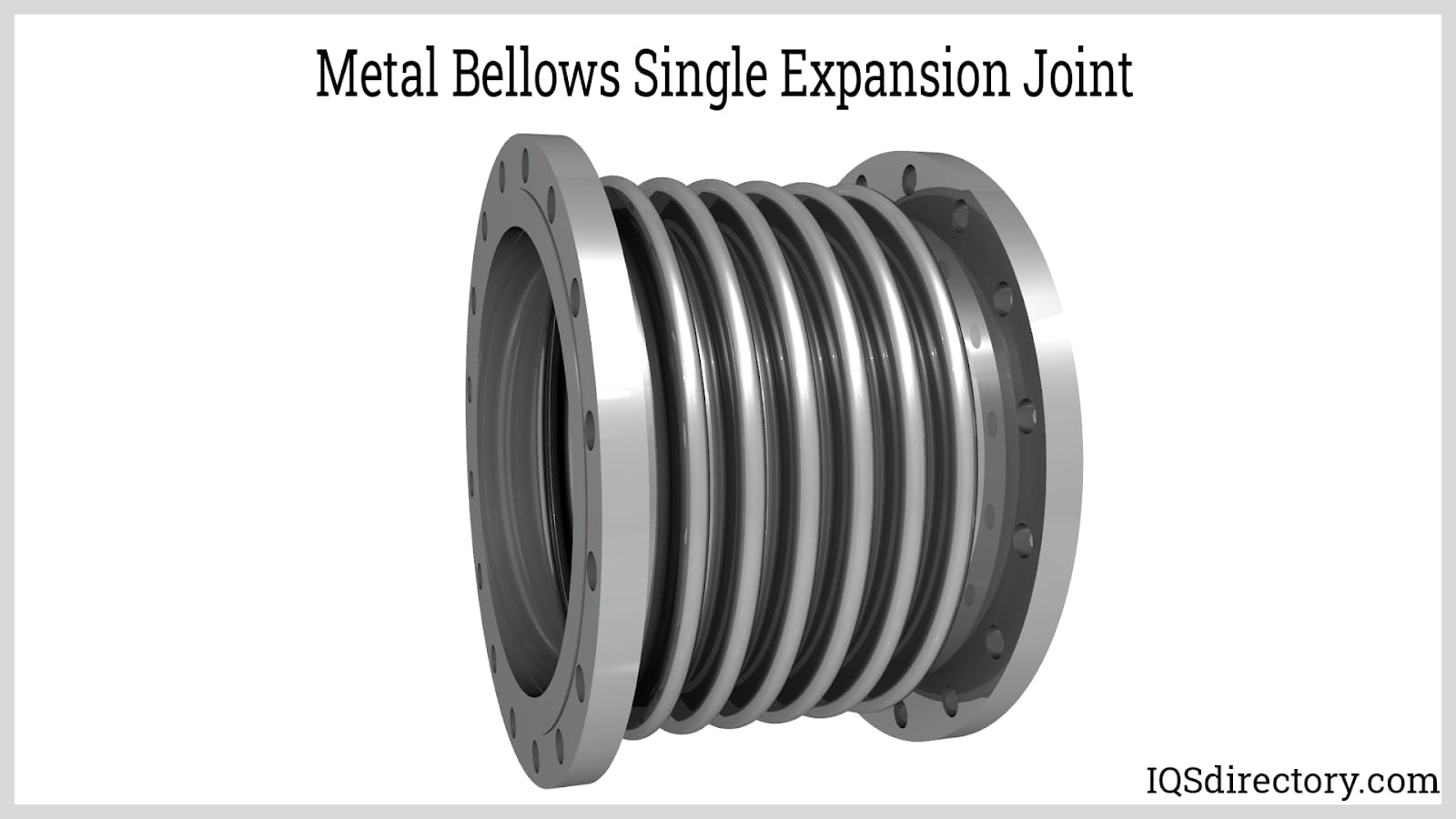
Elbow Pressure Balanced Expansion Joints
Elbow pressure balanced expansion joints are designed to address scenarios where pressure thrust forces on machinery or piping become excessive, particularly when there is a change in the direction of the pipe system. These expansion joints work by internally balancing the pressure thrust force—generated by the internal pressure of the expansion joint—so that only the spring rate force, which is the amount of force needed to move the bellows, affects the pipe system. This internal balancing reduces the load on guides and anchor points, allowing for lighter supporting structures and potentially lowering costs, especially where extensive structural or foundation work would be impractical. Pipe guides facilitate movement in one direction while limiting movement in others. Elbow pressure balanced expansion joints are particularly advantageous for pipe systems because they prevent pressure thrust loads from impacting flanges and connected machinery, such as turbines.
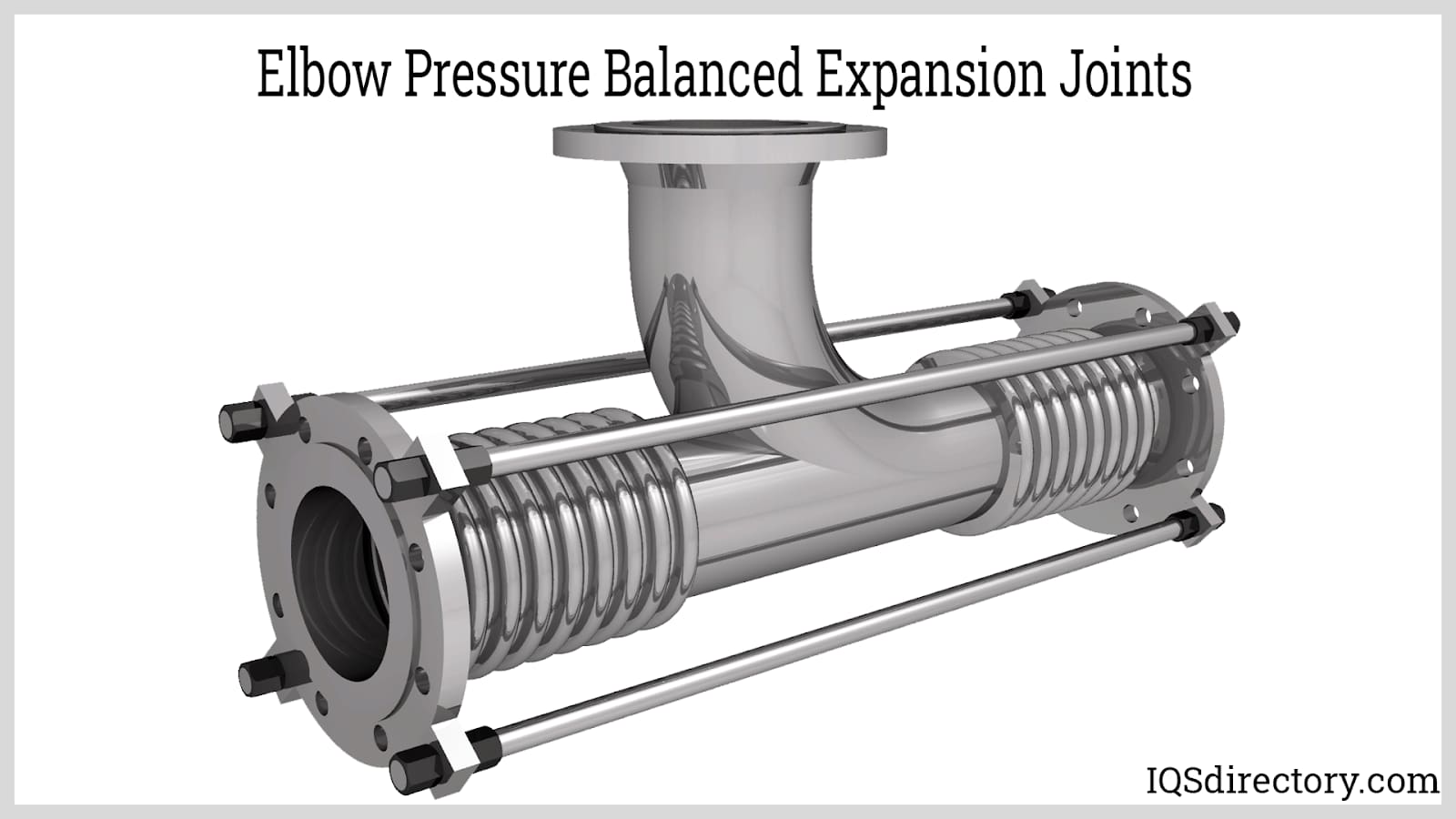
Externally Pressurized Expansion Joints
Unlike standard expansion joints, an externally pressurized expansion joint applies pressure to the exterior of the bellows component. Traditional joints, which rely on internal pressure, often struggle with significant axial shifts due to the limitations of their bellows design. Externally pressurized joints, however, are capable of accommodating larger axial movements thanks to their unique construction. This design is particularly advantageous in space-constrained environments. In these joints, the media flows along the outside of the bellows rather than inside, allowing for a more extended structure and greater movement range by reducing pressure-related design constraints.
Toroidal Expansion Joints
A toroidal expansion joint is a metal component consisting of circular tubes wrapped around the ends of pipes or weld joints, designed with an inner gap to permit axial movement while accommodating changes in pipeline length. The flexibility of this joint comes from its toroidal convolutions. These bellows are typically manufactured through high-pressure hydraulic processes, though some are formed in a free-form manner similar to inflating a balloon. More accurate convolution shapes can be achieved with toroidal dye cavities. The ability of toroidal expansion joints to withstand pressure is enhanced by this high-pressure forming process. Unlike "U"-shaped bellows, which experience bending stress due to pressure on their sidewalls, toroidal designs primarily endure membrane stress, which generally dictates the maximum pressure they can handle. Although the toroidal shape allows for minimal deflection, it can sustain higher pressures compared to "U"-shaped convolutions, which can handle more deflection but at lower pressure tolerances.
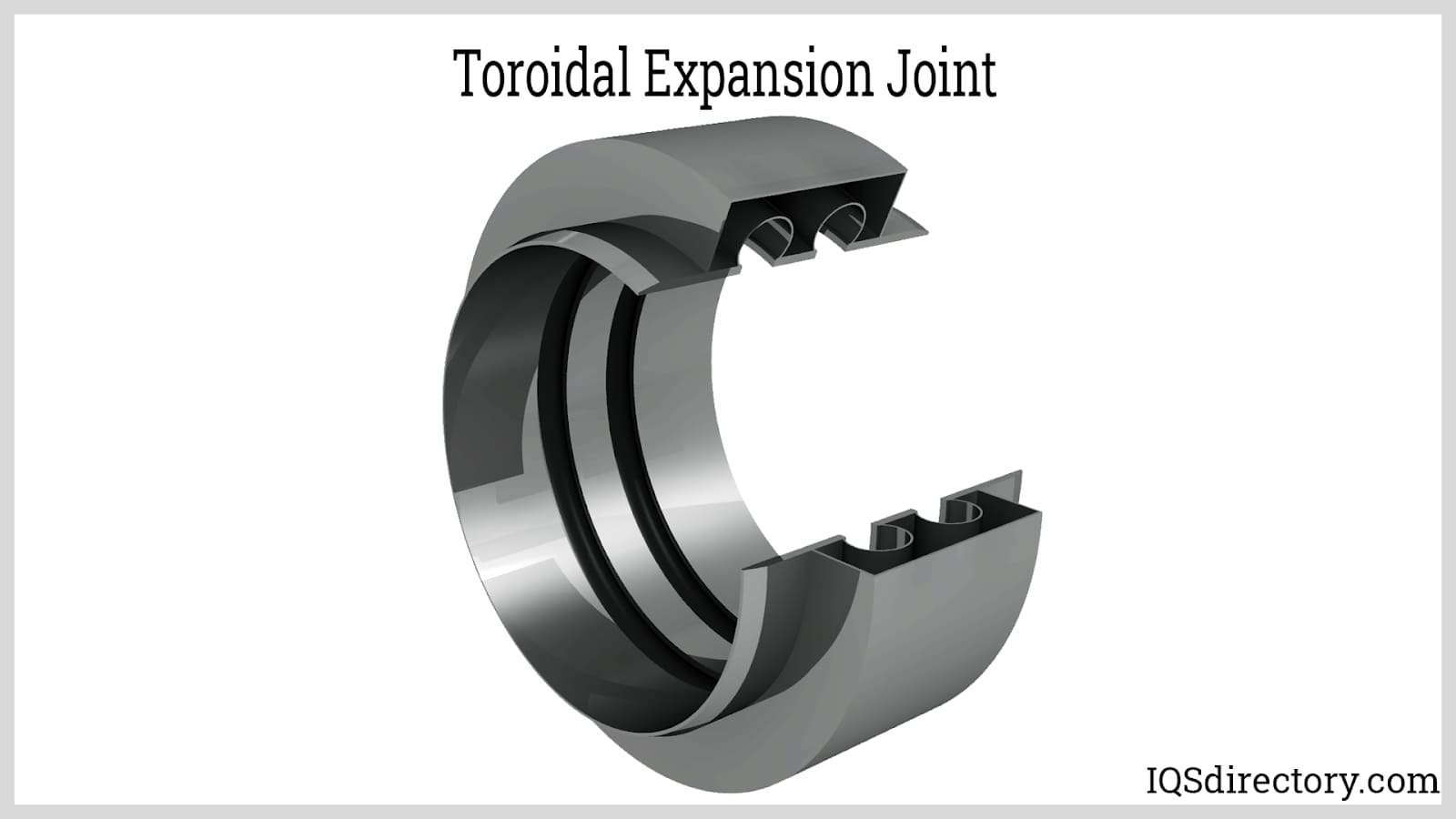
Slip Type Expansion Joints
Slip-type expansion joints, also known as sleeve expansion joints or sleeve compensators, are designed for significant axial movement in piping systems. These joints are particularly useful when dealing with high temperatures and pressures, which influence the choice of materials. Slip-type joints are ideal for pipelines that experience multiple axial displacements. They function by allowing the pipe to slide into the joint, with a sleeve fitting inside the outer shell to accommodate the expansion. To prevent leaks through the joint, sealing materials are placed around the sleeve within the shell.
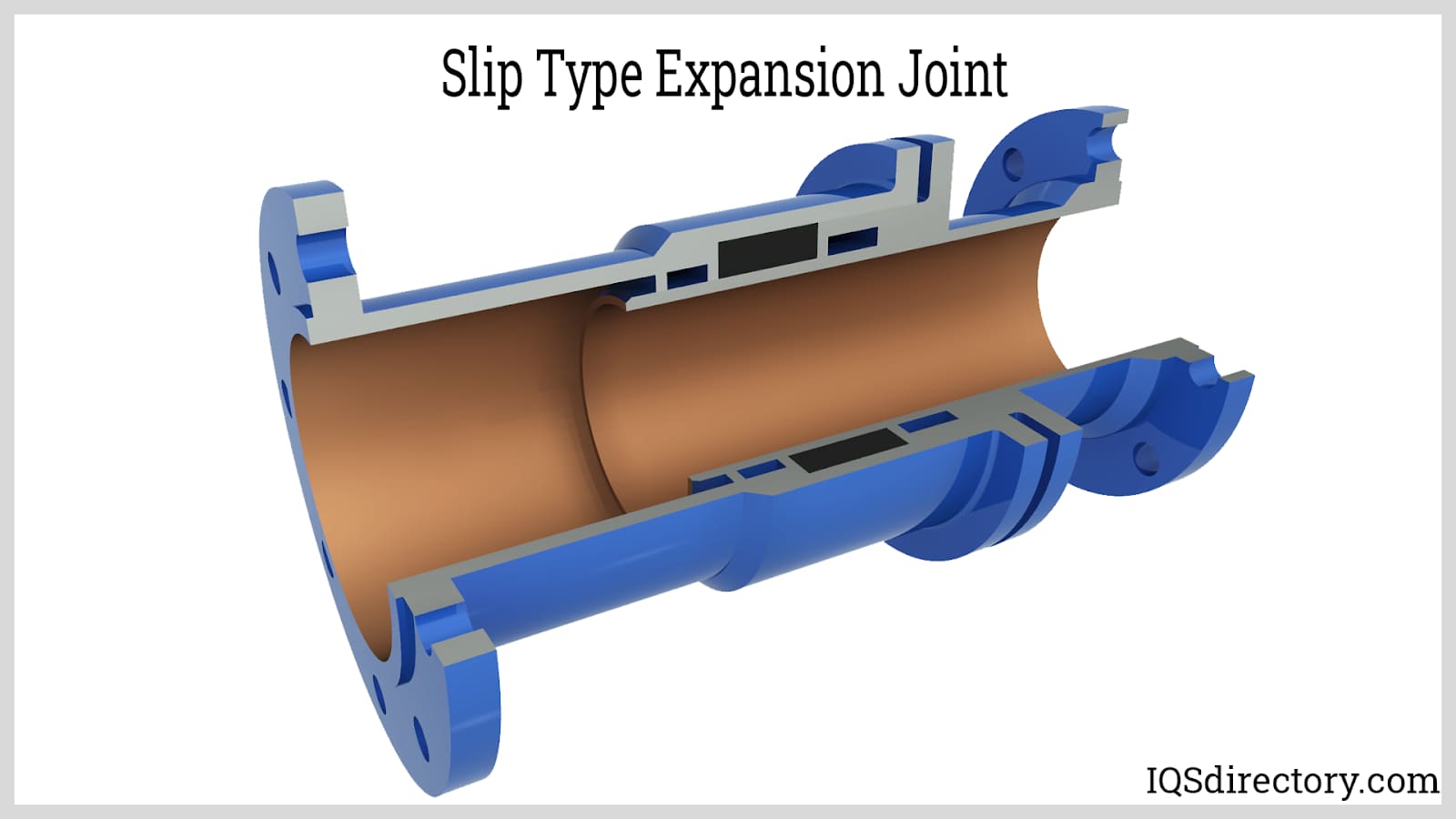
Slip-type expansion joints come with notable limitations. They are not designed to handle rotational movement or lateral displacement, which can lead to issues such as packing distortion, binding, galling, and potential leaks. To prevent these problems, proper alignment is crucial, often achieved with pipe guides and slide expansion joints. These joints are commonly used in municipal water supply systems and district heating networks. Any lateral or angular movement can cause the inner sleeve to become stuck inside the shell, compromising its ability to manage thermal stress. Regular maintenance and replacement of the packing material are necessary to prevent leaks.
Angular Expansion Joints
Axial expansion joints are designed to handle both extension and compression along the pipeline axis, whereas angular expansion joints are intended solely for angular movements. These joints utilize hinges to allow rotation in one or more planes. They can be customized with various end connections, such as welding ends, welded flanges, loose flanges, or a combination thereof, based on client specifications. Angular expansion joints are typically equipped with either hinges or gimbals and are part of a broader expansion system. Unlike axial and universal expansion joints, which manage movements independently, angular expansion joints integrate into a system that compensates for movements. They do not impose special requirements on pipe supports or guides, and swing hangers are generally suitable for their use.
Angular expansion joints can be employed for both long pipe sections in district heating systems and shorter pipelines in boiler and turbine rooms, accommodating movement in one or more planes. For installations with limited space, it may be worth considering linked universal or pressure-balanced expansion joints. Typically, a static system will involve two to three angular expansion joints, with their performance depending on the bellows' rotational capacity and the specified angular rotation detailed in technical data sheets. The installation process usually includes pre-stressing to ensure proper function, with considerations given to the installation temperature during this process.
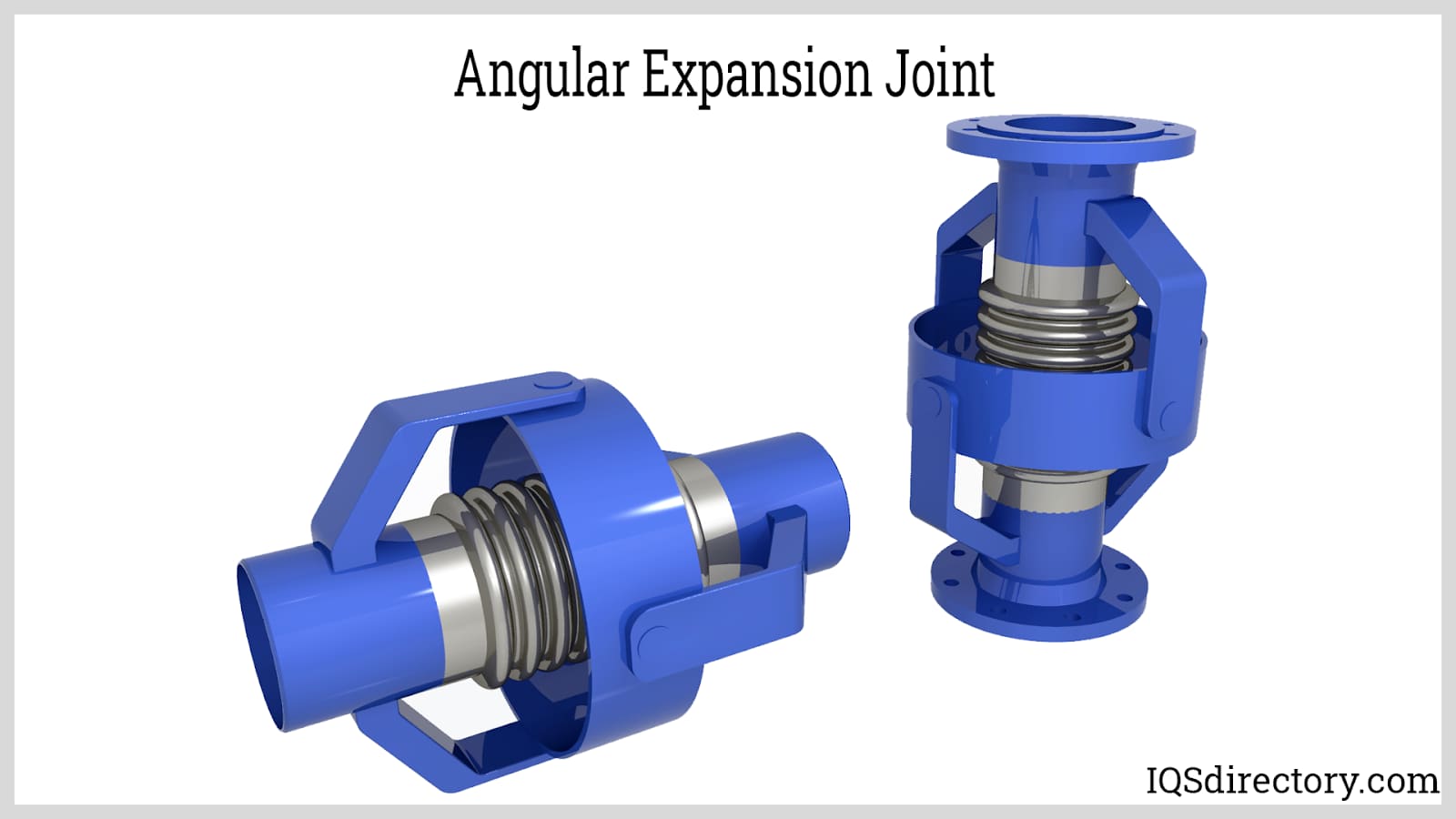
For adjusting thermal expansion angularly, it is often necessary to use two or even three angular expansion joints. A wide variety of configurations are possible with angular expansion joints in what are known as two- or three-hinge systems. In multi-plane systems, where thermal expansion needs to be managed in three axial directions, at least two gimbal expansion joints are required to provide flexibility in all directions. Conversely, single-plane three-hinged systems can function with expansion joints that are flexible in just one direction.
Types of Angular Joints
Hinged Expansion Joints
Hinged expansion joints are metallic assemblies that may rotate in a single plane to accommodate changes brought on by pipework's thermal expansion or contraction. They contain hinges secured to the ends of the expansion joint with two pins and permit angular movement in a single plane while limiting pressure thrust and preventing axial deflection of the expansion joint during either extension or compression.
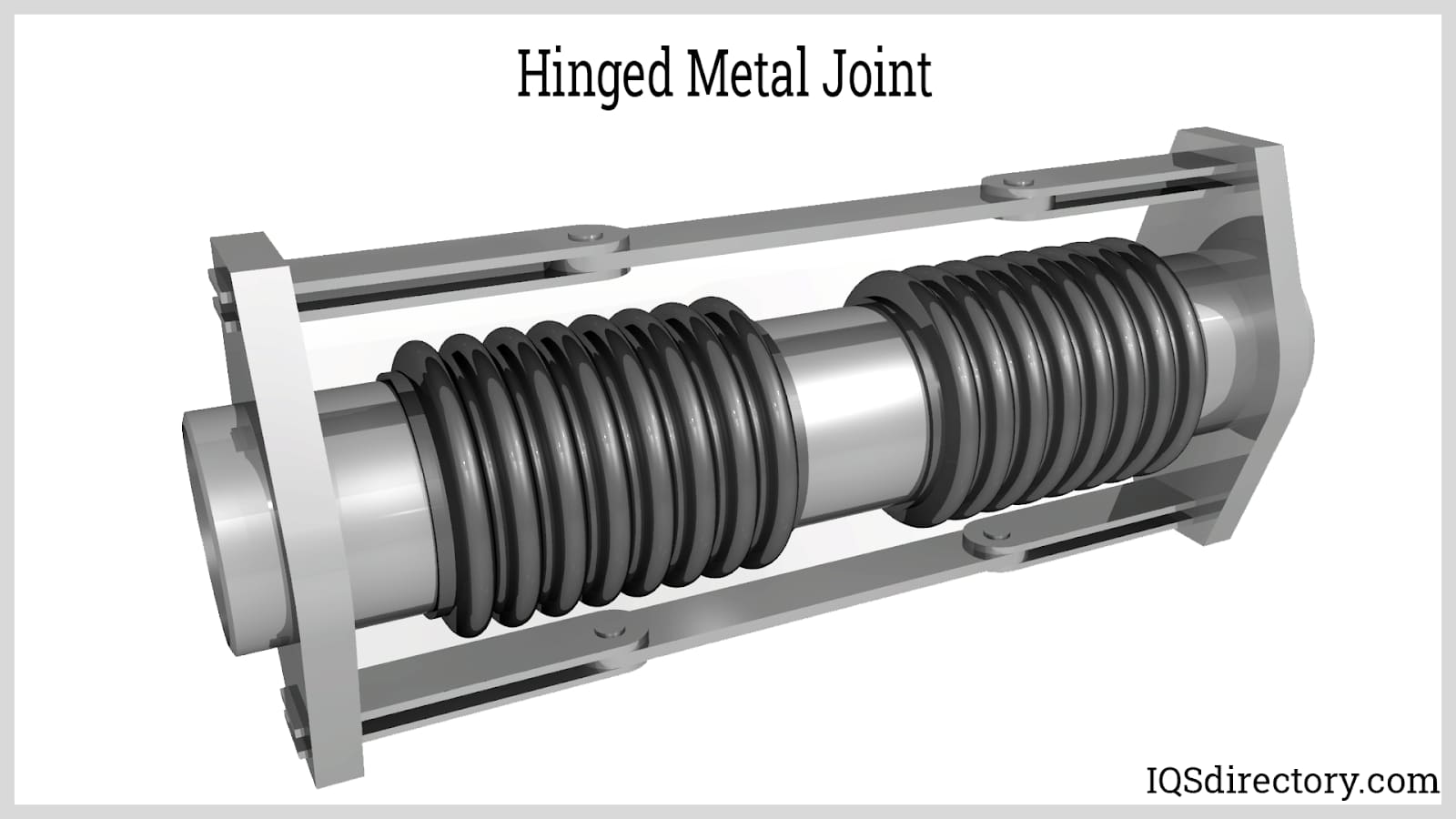
In piping systems, the hinges of each hinged expansion joint are designed to permit only pure angular rotation. These joints are used in pairs to manage lateral deflection effectively. Hinged expansion joints are known for their compact size and robust construction, making them a practical choice for many applications.
Gimbal Type Expansion Joints
Gimbal-type expansion joints enable angular rotation in any plane through the use of two pairs of hinges attached to a floating gimbal ring. A double-gimbal expansion joint consists of two single gimbal joints connected by an intermediate pipe. This setup allows for significant lateral movement in both planes at each end. However, the gimbals at each end of the bellows restrict the universal joint's ability to accommodate the thermal expansion of the intermediate pipe, meaning that the adjacent piping must handle this expansion.
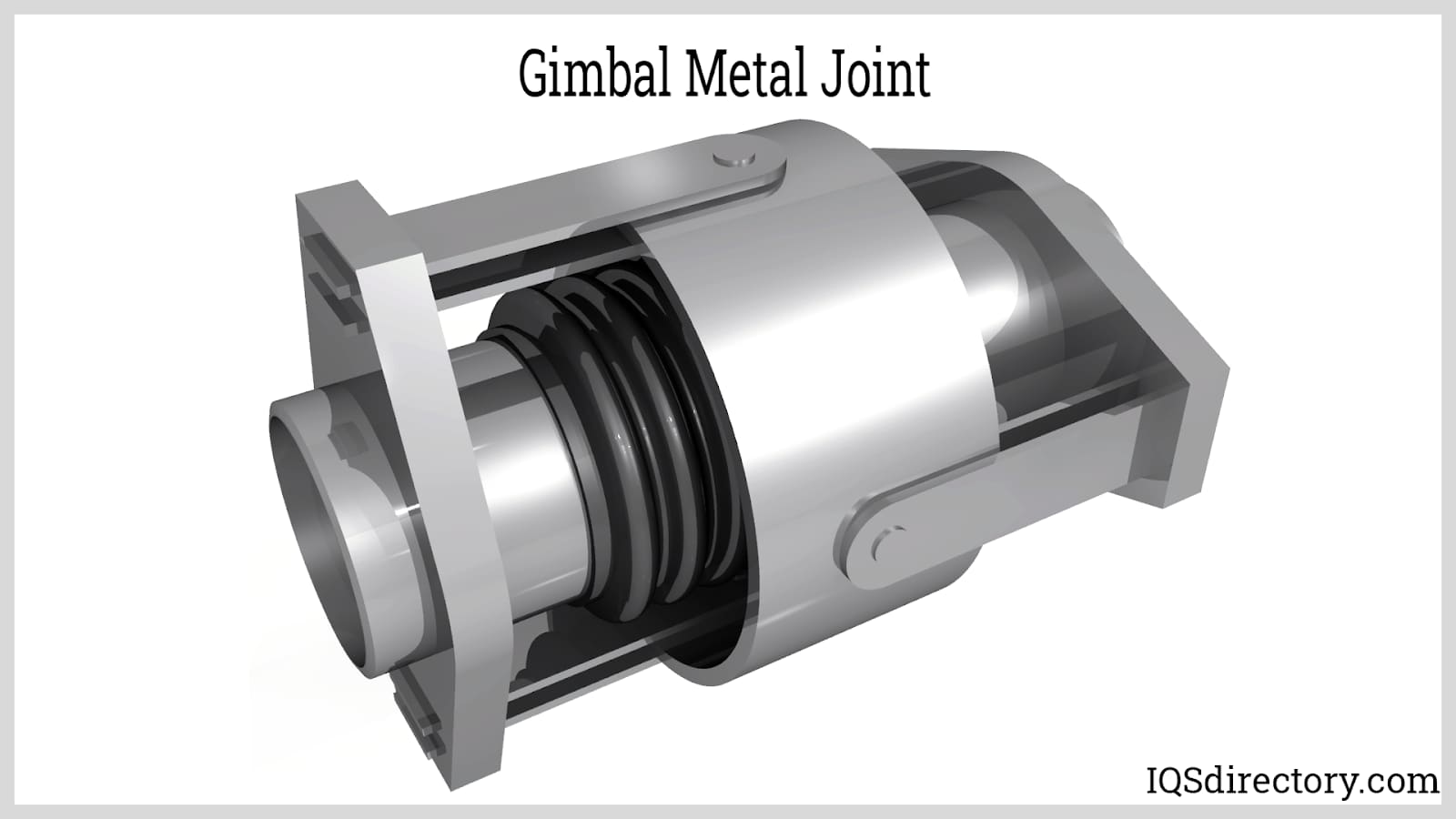
Lateral Expansion Joints
Lateral expansion joints are designed to handle lateral deflection and allow for movement in multiple directions simultaneously when two pipe sections expand in different directions. These joints often feature outer tie rods that help absorb pressure thrusts and manage movements in all lateral directions. Similar to hinged expansion joints, lateral expansion joints utilize the bellows' angular rotational capability to accommodate movement. The distance between the bellows influences the extent of the lateral movement, with greater separation allowing for more movement.
Unlike unanchored axial and universal expansion joints, lateral expansion joints use tie rods to manage the axial compressive forces resulting from internal pressure. This design helps prevent excessive load on nearby pipe support expansion joints, ensuring they remain properly aligned and functional.
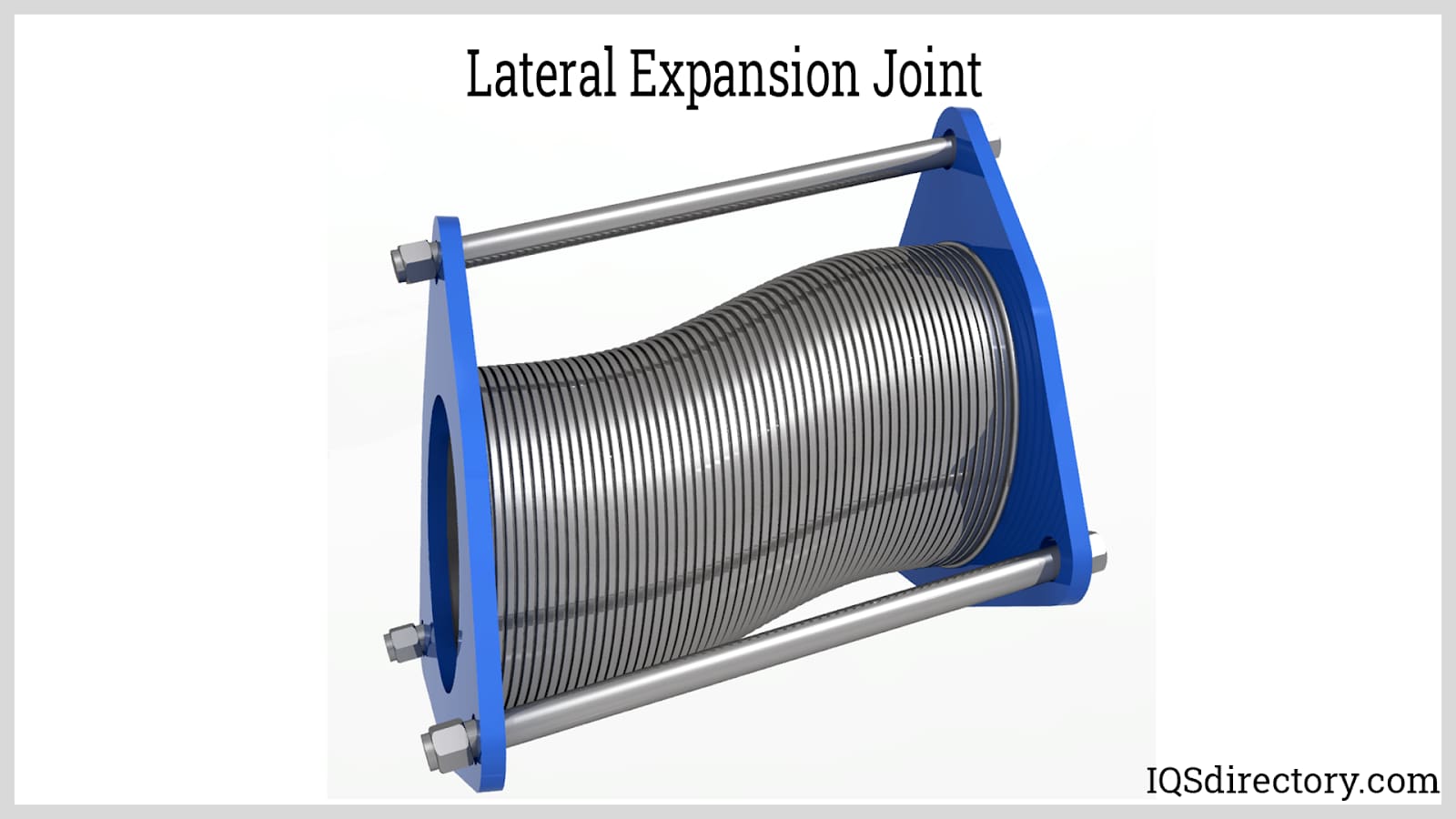
Lateral expansion joints are utilized for compensating lateral movements in single-plane or multi-plane pipe systems, especially where there is a 90° flow redirection. These joints are typically installed at existing right-angle turns in the system. The movement of a lateral expansion joint consists of the desired lateral deflection along with a small, unavoidable axial movement inherent to the joint itself.
A greater center-to-center distance between the bellows in a lateral expansion joint reduces displacement forces. Unlike single-hinged expansion joints, which are part of a unified expansion system, lateral expansion joints operate independently and feature two pins. During installation, a pre-stressing of 50% is commonly applied. This pre-stressing is part of the overall process to ensure proper function once the expansion joint is in place.
When used for lateral movements in one plane, simple lateral expansion joints offer significantly more expansion capacity compared to axial expansion joints. They can simultaneously absorb expansion from two pipe sections moving in opposite directions, effectively managing lateral movements in all planes.
Types of Lateral Expansion Joints
Pressure-Balanced Expansion Joints
Pressure-balanced expansion joints are ideal for situations where anchoring the pipe system is impractical due to structural constraints or cost considerations. These joints are designed to manage both axial and lateral movements without transmitting internal pressure forces to anchor points, surrounding machinery, or adjacent structures. In such cases, fixed points are usually not required; instead, guides ensure that thermal expansion is managed as controlled movement. This makes pressure-balanced expansion joints particularly advantageous in systems connected to turbines, pumps, valves, or other equipment that cannot tolerate pressure thrust loads.
Thick Wall Expansion Joints
Thick wall expansion joints are distinguished by their thick ply structure and high coiled profile. They can be produced in any specific shape, including circular, oval, and square. Heat exchangers, furnaces, and blast furnace pipe work typically require thick wall expansion joints.
Rectangular Metal-Pipe Expansion Joints
Rectangular pipe expansion joints, similar to their circular counterparts, are designed to handle axial, lateral, and angular movements. When designing rectangular bellows, it's crucial to understand the directions of both lateral and angular movements. Additionally, rectangular bellows must be engineered to accommodate longitudinal bending stresses, whereas circular bellows primarily deal with circumferential membrane stress due to internal pressure.
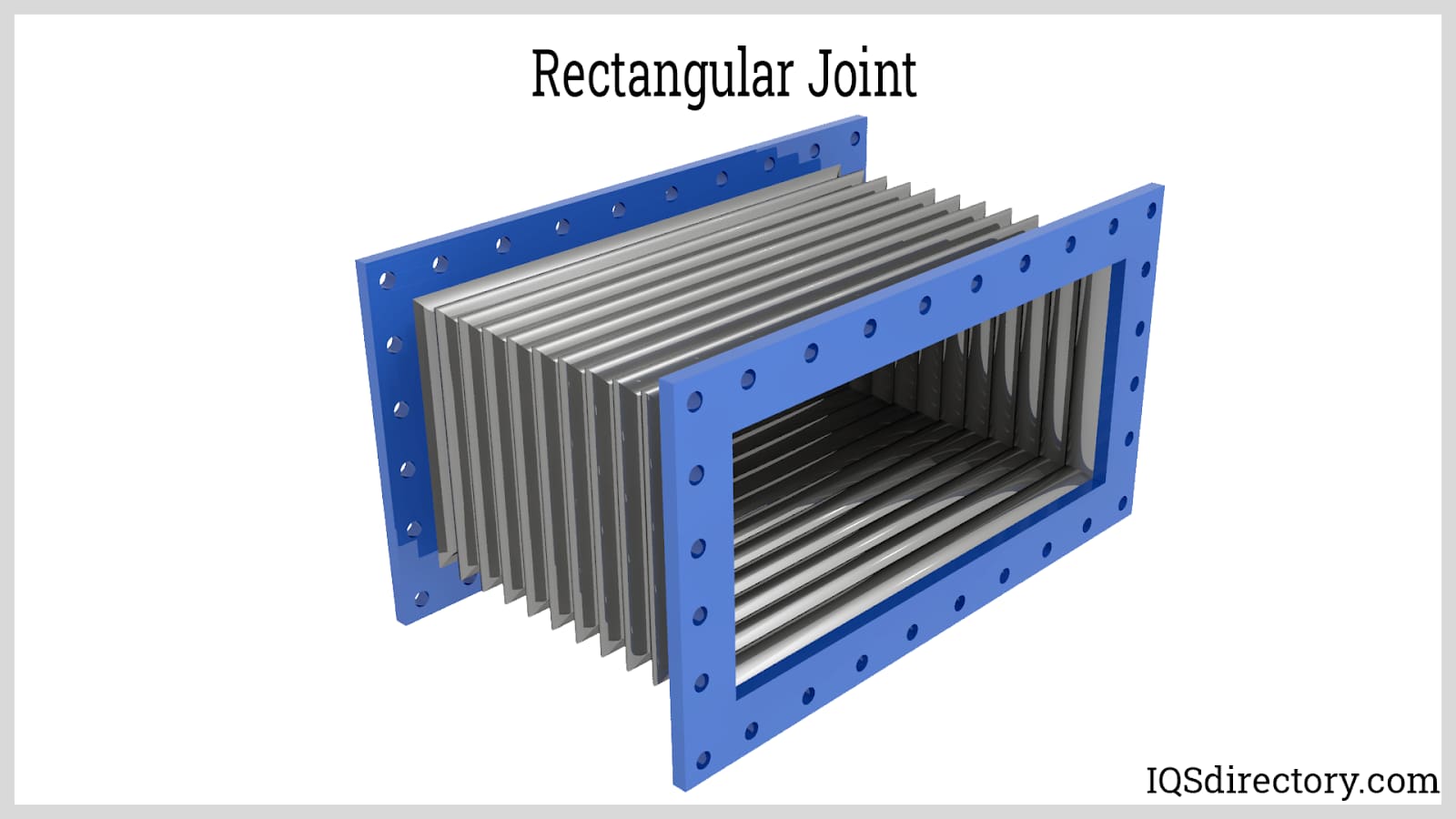
Rectangular metal-pipe expansion joints are designed to accommodate all types of movement within a segment of piping, although they are primarily used for absorbing axial movements. These joints do not control pressure thrust, so they must be used in systems with properly installed anchors and pipe alignment guides to ensure stability. Proper provision of anchors and guides is essential for their effective operation.
The Universal Expansion Joint
The universal expansion joint is designed to accommodate axial, angular, and lateral movements. It consists of two metal bellows connected by an intermediate pipe and flanged connectors on each end. As a specialized type of axial expansion joint, the universal expansion joint transfers the axial compressive forces caused by internal pressure to the adjacent pipe supports, offering only limited pressure resistance for stability. Consequently, universal expansion joints are generally used in low-pressure applications to handle significant axial and lateral displacements.
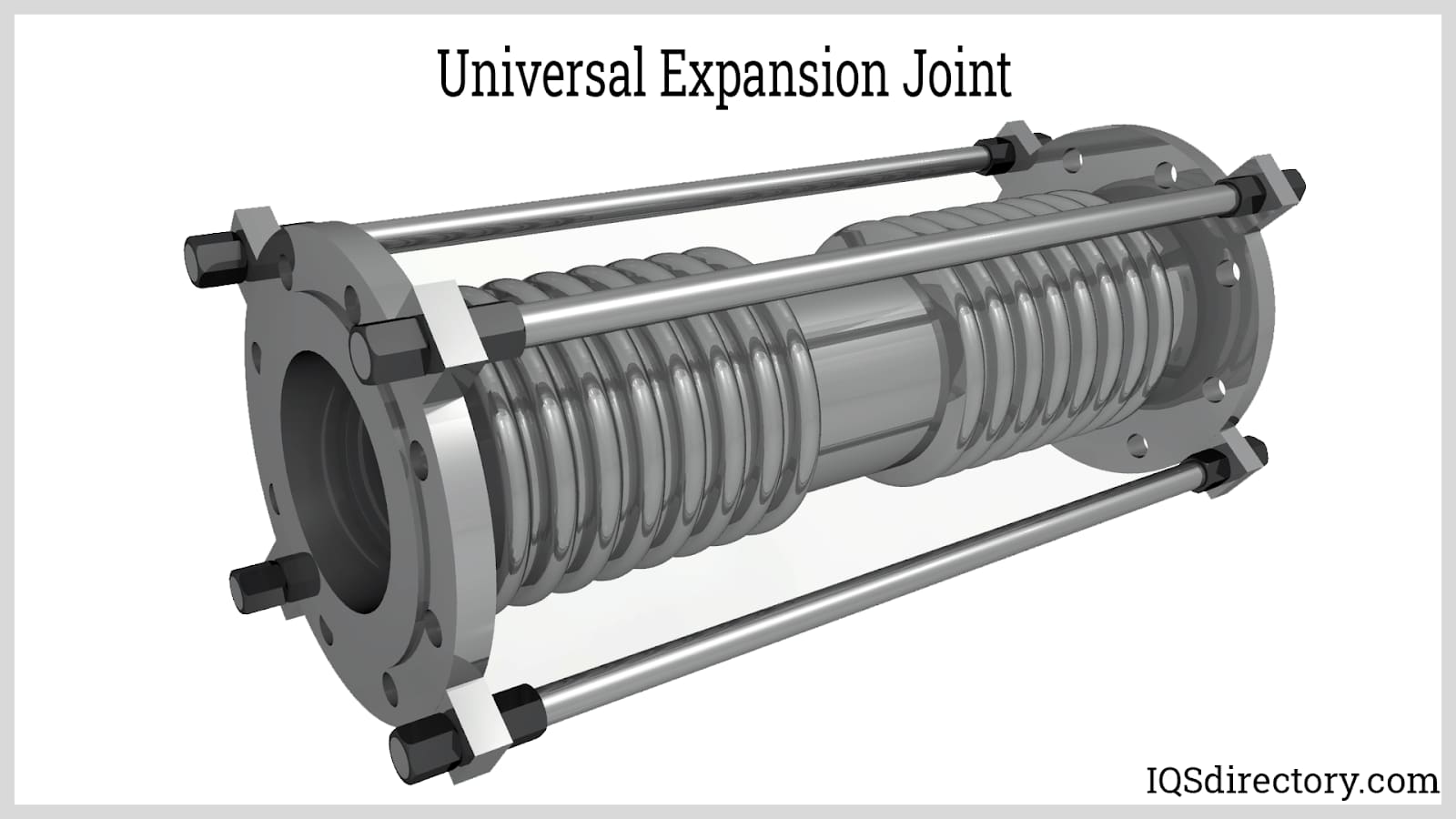
A universal expansion joint consists of two bellows connected by a central pipe or spool. Depending on the service conditions, limiting or full thrust tie rods are used to manage movement and stabilize the connection between the bellows and the center pipe. Tie rods are essential for handling full pressure thrust and other external loads. Universal expansion joints are commonly designed for multi-plane systems, accommodating combinations of axial, lateral, and angular movements, making them particularly effective for managing substantial lateral displacements. Additionally, increasing the length of the central pipe spool proportionally enhances the allowed lateral deflection, providing greater flexibility in lateral movement.
Refractory-Lined Expansion Joints
Expansion joints with refractory lining are designed to withstand extreme conditions and are used in applications involving very high temperatures and pressures. These joints can be configured as hinged, in-line pressure balanced, gimbal, or tied-universal types, depending on the specific temperature, pressure, movement, and flow medium requirements. The metallic bellows of the expansion joint are essential for reducing the temperature of the pipe wall to maintain functionality and safety.
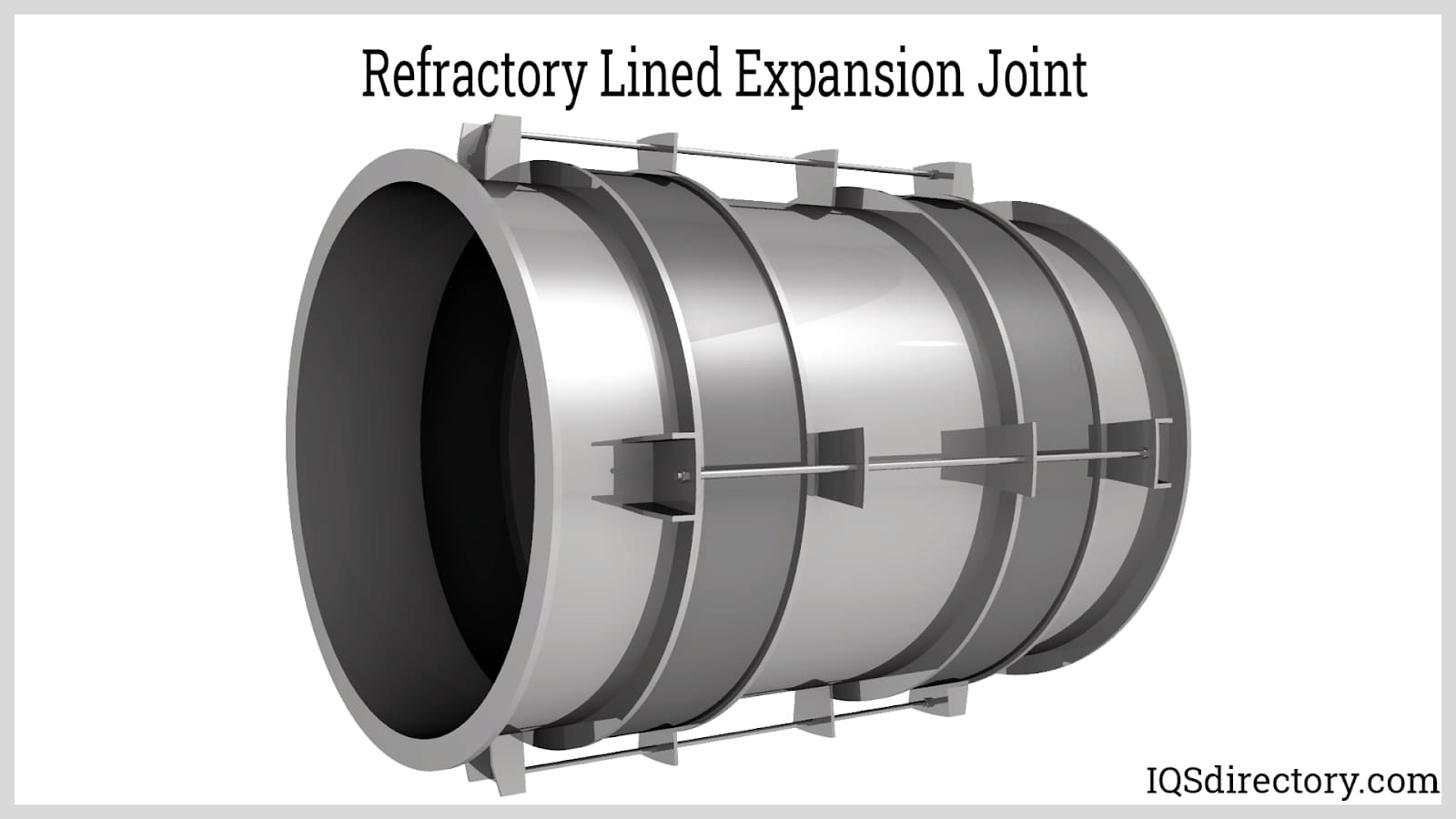
The working lining of a refractory lining is typically followed by a backup or safety layer that comes into contact with the contents of the furnace.
Chapter Four: What are the benefits and applications of expansion joints?
Benefits of Expansion Joints
- Expansion joints and bellows are employed in plumbing systems. They are constructed from add-ons like tie rods, coverings, and flow liners. Although the metal bellows are constrained to control the pressure, they behave like springs. The movement of the connecting pipes is crucial for optimum flow.
- Thermal expansion would result in severe strains if expansion joints were omitted from piping systems. Thermal expansion may generate a great deal of pressure, which may cause pipes to bend and the welds to shatter.
- An expansion joint is created using more than a coil, sometimes referred to as convolution or corrugation. Their grooves are made to withstand the intense pressure of the entire piping system. The bellows assembly is positioned so that it can move in accordance with the associated piping's thermal movement.
- Metal bellows and bellows expansion joints absorb a pipe's thermal expansion in piping systems.
- Pipeline expansion joints are more effective than substitutes, such as pipe bends and loops, due to their improved effectiveness in absorbing larger movements, higher capacity to conserve space, and superior economic efficiency.
- Expansion joints are simple in both form and operation in that they can be directly installed where needed.
Applications of Expansion Joints
- Since power production uses high pressure and temperature, expansion joints are used to assist when pipes expand.
- Co-generation systems producing both electricity and heat simultaneously use expansion joints where the industry faces heat changes.
- In chemical transportation from one place to another, expansion joints are needed to absorb shocks and vibrations.
- Expansion joints are used in transportation of cryogenic gasses. Cryogenics is the study and the production of very low temperatures.
- Expansion joints are used for vessels under pressure and heat exchangers. Vessels under pressure face chances of shaking and that shock must be absorbed by expansion joints.
- Heat exchanging may also lead to the expansion and contraction of pipes which need expansion joints to compensate for this.
- Expansion joints are used in construction and bridges to allow for shock absorption when heavy vehicles are passing.
- Pharmaceutical production utilizes some use of expansion joints in their main robotic plants. Expansion joints are used in hydraulic and pneumatic pipes in pharmaceutical production plants.
- Water treatment plants need a lot of expansion joints to absorb the shock from high flow rate.