Fiberglass Sheets
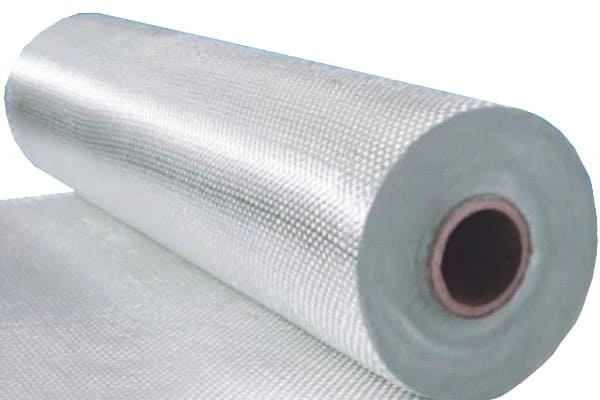
Fiberglass is a plastic reinforced material where glass fiber is used as reinforcement, and the glass fiber is flattened into a sheet. It is also known as glass fiber reinforced plastic or glass reinforced plastic...
Please fill out the following form to submit a Request for Quote to any of the following companies listed on
Here is everything you will need to know about fiberglass molding available on the internet.
You will learn:
The process of fiberglass molding is employed to manufacture detailed and complex components from fiberglass resin. Some primary benefits of utilizing fiberglass are its economical nature, simple production process, long-lasting properties, and efficient part replication.
The creation of a fiberglass component initiates with a pattern, acting as a precise duplicate of the end product. Various materials can be used to make these patterns, meticulously designed to capture even the finest and most intricate details of the intended design. This ensures high precision and quality in the final fiberglass components.
Parts molded from fiberglass are both robust and cost-efficient for producing components. These parts can either be used right out of the mold or prepared with a surface suitable for painting, providing versatility in the product's ultimate look and functionality.
Fiberglass molding is a cost-effective method for producing durable and long-lasting products and parts. Beyond its affordability, fiberglass offers several advantages: it is stronger and more resilient than some metals, non-conductive, capable of being molded into intricate and complex shapes, and chemically inert. Fiberglass is used across a wide range of industries, from leisure products to components for passenger aircraft.
Fiberglass storage tanks can be installed above or below ground and are versatile for various applications, including rainwater harvesting, oil field storage, liquid fertilizer, water treatment, and irrigation. Available in sizes ranging from small tanks suitable for backyard use to large tanks with capacities exceeding 1,000,000 gallons, they can be shaped, fitted, and customized to meet specific needs.
Storage tanks come in several different varieties, which include horizontal, upright, cone bottomed, and open topped.
Modern boat building has largely transitioned away from traditional materials like wood and steel, favoring molded fiberglass instead. Today, every component of a boat is crafted from fiberglass, with polyester being the most commonly used resin.
The manufacturing process begins with spraying a female mold with gelcoat, followed by the application of fiberglass cloth. A resin is then applied to saturate the fiberglass. Once the resin cures, the boat or its components are ready for assembly.
Fiberglass is commonly used in home construction for facades and roofing due to its versatility and ease of shaping. Architects favor fiberglass because it can be easily customized to meet project requirements. Additionally, fiberglass is employed for shades and awnings, providing effective sealing and protection for structures.
Fiberglass reinforced pipes (FRP) are used in trenchless installation of pipelines. The many factors that make fiberglass piping ideal is its lightweight, resistance to temperature changes, strength, and resistance to corrosion or chemicals. Their low maintenance and ease of installation make them an ideal choice as piping material. It can be used for trenchless installations due to its exceptionally smooth outer finish.
Fiberglass's durability, strength, and corrosion resistance make it an ideal material for manufacturing both interior and exterior platforms. Platforms require exceptional stability to endure rugged use, and fiberglass's flexibility allows it to be molded into various dimensions, making it perfect for this purpose.
Molded fiberglass grating is impact-resistant and offers excellent traction. Like other fiberglass products, it is corrosion-resistant, lightweight yet sturdy, nonconductive, and nonmagnetic. These properties make it particularly well-suited for use in manufacturing and production environments where conductivity and magnetism are concerns.
Fiberglass doors are an excellent alternative to metal or steel doors. They offer a tight seal and are resistant to corrosion. Unlike wood doors, which can warp, rot, swell, or shrink, fiberglass doors maintain their integrity and do not dent or splinter. Additionally, they are energy-efficient.
In industrial environments, fiberglass doors are particularly well-suited to withstand the challenging and hazardous conditions often found in manufacturing settings.
Fiberglass sinks are a popular modern addition to homes due to their durability and longevity. Unlike other types of sinks, fiberglass sinks are resistant to stains and easy to clean. They maintain a neat and clean appearance and are highly resistant to damage.
Fiberglass sinks can be customized to fit any configuration, including corner sinks or models with integrated drain boards. They are also straightforward to install and mount.
Fiberglass is commonly used in the production of office chairs and outdoor furniture due to its durability, attractive appearance, and versatile design. Unlike furniture made from other materials, fiberglass furniture requires minimal maintenance and can endure continuous and heavy use. In office environments, it withstands constant traffic, frequent movement, and daily wear and tear effectively.
As the demand to reduce vehicle weight for better fuel efficiency increases, fiberglass molded components have become crucial in automobile design and manufacturing. Many car parts, including hoods and panels, are made from fiberglass. Its versatility in molding allows engineers and designers to create parts in a wide range of shapes, making it an ideal material for automotive applications.
Fiberglass was first developed during the early stages of the industrial revolution. The modern version we use today was invented by a researcher at Owens-Illinois, which later became Owens Corning. They patented the name "fiberglas" with one "s." This breakthrough occurred by chance when a jet of compressed air was directed at molten glass, causing it to form fibers.
Initially discovered for use as insulation, fiberglass has since evolved into a versatile material used in countless applications. Today’s manufacturing process is highly technical, involving various polymers and materials to create what we commonly refer to as fiberglass.
Fiberglass consists of glass fibers, which are categorized into two types based on their geometry: continuous and discontinuous. Continuous fibers resemble yarns such as cotton or wool. The use of glass fibers dates back to the Renaissance, where they were employed as decorative elements in artwork.
To make fiberglass, the primary ingredients include silica sand, limestone, and soda ash. Additional materials such as calcined alumina, borax, feldspar, nepheline syenite, magnesite, and kaolin clay are added to enhance specific properties of the fiberglass. These raw materials are meticulously measured and blended to create the batch used in production.
The mixed batch is fed into a furnace where it is melted. In order to produce a smooth even flow of glass, the temperature is carefully and precisely controlled. The molten mixture must be kept at 2500° F or 1371° C, which is higher than the temperature to form other types of glass.
Fiberglass fibers can be formed using various methods. For textile-type fibers, the molten glass is directly taken from the heating process. In the case of marble fibers, the molten glass is directed into a marble-forming machine, where the resulting marbles are then visually inspected for impurities.
Whether creating marbles or textile fibers, the glass is extruded through an electrically heated bushing, known as a spinneret. This spinneret has hundreds to thousands of openings, through which the glass passes to become fine filaments. The size of these openings determines the diameter of the fiberglass fibers.
Once the filaments are formed, they undergo various finishing processes. Below is a brief overview of some of the methods used to process these filaments.
After the glass exits the bushing, the strands are collected by a high-speed winder, which spins at speeds of up to two miles per minute. The tension from this process pulls the filaments through the bushing holes, forming strands that are much finer. During winding, a binder is added to help prevent the fibers from breaking. The filaments are then wound onto tubes, where they are twisted and plied into yarn.
In the staple fiber forming process, molten glass is subjected to jets of cold air as it exits the bushing, which rapidly cools the fibers and breaks them into various lengths. The filaments then pass through a spray of lubricant and into a revolving drum, where they are collected into a web. This web is then pulled apart to create loosely assembled fibers that are further processed into yarn.
In the chopping process, continuous strands are cut into short lengths and mounted on bobbins or creels. They are then fed through a machine that further chops them into shorter pieces. The chopped fibers are then formed into mats, coated with a binder, cured in an oven, and finally rolled into finished mats.
Glass wool is produced using a rotary or spinner process. In this method, molten glass flows into a cylindrical container with small holes on its side. As the cylinder spins, the molten glass exits through these holes. The stream of glass is then subjected to blasts of air, hot gas, or a combination of both. After this treatment, the glass falls onto a conveyor, where it interlaces to form a fluffy mass. This mass is coated with a binder, compressed, and then cured in an oven to set the binder.
In the filament process, various binders are used to provide cohesion to the glass fibers. While the binder holds the filaments and fibers together, it might not offer additional protection. For this reason, a protective coating may be applied.
During binder application, lubricants may be included to reduce fiber abrasion. The method of application varies depending on the manufacturing process. Additionally, an anti-static compound might be applied during cooling to act as a corrosion inhibitor and stabilizer. If the fiberglass is intended for reinforcing plastics, a coupling agent may also be applied at this stage.
The choice of molding process for fiberglass depends on the type of part or component being created. Factors to consider include the type of fiberglass material used, such as vinyl ester or polyester resin, fiberglass roving or matting, and gelcoat. Each material offers distinct advantages depending on the specific application.
Similar to the production of fiberglass filaments, there is no single method for molding fiberglass. The selection of a molding process must account for various factors, including the intended use of the product. The methods used for molding commercial products often differ significantly from those employed in industrial applications.
In the fiberglass molding process, the plug represents the final part, which can be the actual part, a scaled model, or a completely new design. When engineering the mold, factors such as surface finish, draft angles, undercuts, and production methods are carefully considered.
Achieving an excellent surface finish starts with thorough planning. Any imperfections in the plug will be transferred to the final part. Producers aim for a "Class A" finish, characterized by a polished, high-luster appearance free from porosity or scratches.
Even if the plug is smooth and well-formed, it can still adhere to the applied fiberglass during the molding process. To prevent this, a release agent is used to ensure that the final part can be easily removed from the mold.
In industrial operations, fiberglass release agents are designed to efficiently and quickly release the part from the mold in a single step. These release agents often include a sealer that protects and seals the substrate.
Gelcoat is a specially formulated polyester resin applied as the initial coat in a mold. It creates an opaque, UV-resistant surface. Once the part is removed from the mold, the gelcoat serves as the exterior finish. After applying the gelcoat, the mold is cured to solidify the coating.
The open molding process uses a single-sided mold that defines the shape and surface of the finished part. Gelcoat is first applied to the mold surface, followed by the addition of reinforcements. Resin and fiberglass can be either sprayed into the mold or applied by hand over the gelcoat. Layers of laminate are built up to achieve the desired thickness of the final part.
Once all materials are added, it is crucial to remove any air pockets or bubbles by rolling over the mold. After ensuring the mold is properly filled and free of air pockets, it is cured to complete the process.
Open molding offers significant flexibility, allowing for the production of a wide variety of sizes, designs, configurations, and components.
Closed molding encompasses several techniques, including resin transfer molding (RTM), resin infusion, vacuum infusion, and compression molding.
Curing is the process of allowing the fiberglass mold to harden and set. It generally refers to the process where a liquid solidifies into a solid. Several methods can be used to cure fiberglass molds. The simplest method involves allowing the molded shape to cure at room temperature after applying a catalyst or hardening additive.
The curing process can be accelerated by applying heat using an oven and pressure. The vacuum bagging process helps consolidate the various layers of the mold and removes any voids by off-gassing.
Electron beam (E-beam) curing is used by some manufacturers for curing thin laminates. In this method, the molded part is exposed to electrons, which provide ionizing radiation that causes crosslinking of the resins.
Ultraviolet (UV) curing uses UV radiation to activate a photoinitiator added to the resin. When UV rays hit the workpiece, the photoinitiator triggers a crosslinking reaction in the resin.
Careful monitoring of the curing process is essential. This involves measuring the conductivity of ions in the resin material. Higher viscosity resins result in slower ion movement.
For certain applications, regulations require building materials to be fire retardant and not contribute to the spread or prolongation of a fire. While fiberglass itself is incombustible, the resin used is highly flammable and must be coated to prevent it from fueling a fire. Several flame control and flame retardant coatings are applied during production to meet federal, state, and local building and fire codes.
Building materials are typically tested using the American Society for Testing and Materials (ASTM) E-84 test. This test assesses flame spread and burning behavior of a material sample. The test results include a Flame Spread Index (FSI) and a Smoke Developed Index (SDI), which classify materials as A, B, C, D, or E.
One type of fiberglass coating, known as intumescent flame retardant (IFR), uses intumescent technology to retard fire spread and reduce heat. IFR is an eco-friendly, high-efficiency flame retardant that produces low smoke and toxicity. It contains aluminum oxide, silicon oxide, and various metal oxides.
Fire retardant paint coatings react to heat by releasing a flame-dampening gas, which slows the spread of fire and provides time to extinguish it. This coating is highly effective in suppressing fire reactions in fiberglass and has an ASTM E-84 Class A rating, indicating very slow fire spread and high resistance to severe fire exposure.
Numerous machines are available for fiberglass molding, playing a crucial role in today’s industries by enabling efficient and precise manufacturing of fiberglass components. These components are widely used in sectors such as automotive, construction, and marine, providing lightweight, durable, and corrosion-resistant solutions. Below, we explore several brands of machines commonly used for fiberglass molding in the United States and Canada:
Features: The MVP Patriot RTM System is designed for closed-mold fiberglass manufacturing processes, such as resin transfer molding (RTM). It provides precise control over resin injection and flow, ensuring consistent part quality and reduced material waste. This system includes advanced features like temperature control, pressure monitoring, and automated controls, making it efficient for producing complex fiberglass parts with excellent surface finish and dimensional accuracy. The Patriot RTM System is renowned for its reliability, durability, and ease of use.
Features: The GRACO Reactor E-XP2 is a plural-component proportioning system used in fiberglass composite manufacturing. It ensures precise mixing and dispensing of reactive resins and catalysts for various fiberglass molding processes. The Reactor E-XP2 offers advanced control features, including ratio monitoring, temperature control, and programmable settings. It supports efficient and accurate material application, ensuring proper curing and optimal part properties. This system is widely used for applications such as spray-up and hand lay-up processes.
Features: Fiber-Tech Industries specializes in complete FRP (Fiberglass Reinforced Plastic) panel manufacturing lines. These lines include machinery for resin impregnation, continuous lamination, and curing. The FRP Panel Manufacturing Line offers high-speed production capabilities with consistent quality and dimensional control. It is suitable for producing fiberglass panels for construction and transportation applications. Known for its efficiency, automation, and versatility, this manufacturing line excels in delivering reliable results.
Features: RTM North Ltd. offers the Hydra Filament Winder for the automated production of fiberglass composite products, such as pipes, tanks, and tubes. This machine provides precise fiber placement, tension control, and resin impregnation, ensuring consistent and high-quality parts. It supports various filament winding techniques and accommodates different part sizes and shapes. The Hydra Filament Winder is recognized for its reliability, flexibility, and efficient production capabilities.
Features: KOBELCO’s FCP Series filament winding machines are designed for the precise and automated production of cylindrical or conical composite structures. These machines offer control over winding patterns, fiber tension, and resin impregnation, resulting in uniform and high-strength parts. The FCP Series supports customization for specific part requirements and production volumes. KOBELCO’s filament winding machines are known for their advanced technology, reliability, and performance.
Please note that the availability and specific features of these models may change over time. For the most up-to-date information, it is advisable to contact the manufacturers or their authorized distributors.
Among various fabricating materials, fiberglass stands out as the most popular choice for reinforcing and stabilizing polymers due to its numerous benefits. Initially used during World War II as a substitute for plywood in aircraft construction, fiberglass has since expanded into a wide range of industries. Its strength, cost-effectiveness, and ease of fabrication have made it a versatile material in applications beyond aircraft design.
Fiberglass parts offer strength comparable to steel but with only a quarter of its density, significantly reducing the weight of the finished product. The high MPa rating of fiberglass ensures excellent rigidity, making it ideal for construction projects that demand substantial strength.
The remarkable strength of fiberglass is evident in its applications, including the manufacture of bridges, balconies, building facades, and platforms. Its high strength-to-weight ratio makes it particularly suitable for gratings designed to support vehicular loads.
Fiberglass is an effective insulation material, even at relatively low thicknesses. Both the glass and resin used in fiberglass are non-conductive because they do not contain metals or free electrons, which makes them excellent insulators against electricity.
Incombustibility refers to a material's ability to resist burning. Fiberglass is composed of mineral materials that are naturally incombustible, meaning they do not support or produce flames. When exposed to heat, fiberglass does not emit smoke or release toxic substances.
Dimensional stability is crucial for parts, as maintaining their original shape and size is essential for their functionality. Fiberglass excels in this regard because it is not affected by temperature fluctuations, humidity, or moisture. Its low coefficient of thermal expansion ensures that it retains its original shape and configuration even under the harshest conditions.
Thermal conductivity, or the transfer of heat, is a key factor in evaluating building materials. Fiberglass is essential in construction primarily because of its low thermal conductivity. It does not burn, remains unaffected by curing temperatures, and retains 50% of its strength at 700°F and 25% at 1000°F.
Fiberglass has become widely used primarily due to its resistance to substances that cause rot or decay. It is highly resistant to prolonged exposure to water and is unaffected by most acids, except for hydrofluoric and phosphoric acids.
Similar to its nonconductivity, materials with dielectric properties do not permit electric currents to pass through and are the opposite of electrical conductors. This characteristic of fiberglass makes it ideal for applications that require protection from electromagnetic fields (EMF).
In addition to its exceptional tensile strength, fiberglass is highly durable, as it does not rot, corrode, or rust. This durability ensures the integrity and longevity of parts and materials made from fiberglass. It is designed to withstand tough, rigorous, and harsh conditions, making it a preferred choice for environments involving corrosive substances or materials.
Despite having strength comparable to steel, fiberglass weighs significantly less—approximately one-fourth the weight of steel. This lightweight nature, combined with its dimensional stability, enhances its usability and durability. The reduced weight simplifies installation and allows for flexibility in design and configuration.
One drawback of heavy materials is the higher cost associated with their installation, which often requires cranes, lifts, and other equipment. In contrast, fiberglass installation is more cost-effective, as it does not necessitate such heavy machinery.
Fiberglass is known for its durability and low maintenance requirements, which significantly reduces its overall cost of use. Throughout its lifespan, a fiberglass part typically needs minimal upkeep, such as painting or chemical cleaning.
Fiberglass is used to create a wide range of products due to its versatility, allowing designers to bring their visions to life. From broom handles and electrical enclosures to car doors and fenders, fiberglass can be molded, shaped, and customized to meet the specific requirements of various products.
Various types of fiberglass are effective for soundproofing, with their suitability determined by the NRC (Noise Reduction Coefficient) rating. A higher NRC rating indicates better sound absorption. For example, fiberglass insulation with a thickness of 3.5 inches typically has an NRC rating of 0.9 to 0.95, making it highly effective for soundproofing applications.
Several biological and environmental factors can affect the lifespan of a product. However, fiberglass is known for its longevity and resistance to environmental contamination and microorganisms. Once installed, fiberglass typically lasts throughout the lifespan of the application.
Fiberglass also boasts biological resistance, including its inability to absorb materials like water, which can cause other fabrics to rot.
Ultraviolet degradation, a type of photo corrosion caused by light with wavelengths between 10 and 400 nanometers (NM), is harmful to various materials, including textiles, wood, certain steels, aluminum, and polymers. Although these UV rays are not visible to the naked eye, they can lead to inconsistencies and accelerate corrosion.
To counteract UV degradation, fiberglass is often treated with specialized coatings that help preserve the integrity and strength of the fibers.
Fiberglass can be tailored for specific applications, with each type varying in composition to produce distinct characteristics. Despite the differences, the basic composition of fiberglass remains largely the same, with variations arising from specific raw materials.
The variation in fiberglass types is due to the different proportions of raw materials used. While the core materials include silica sand, soda ash, and limestone, additional ingredients such as borax, calcined alumina, magnesite, kaolin clay, and feldspar can be incorporated to modify the fiberglass's properties and characteristics.
The classification of fiberglass types is based on their properties and characteristics. For instance, adding certain raw materials can enhance chemical resistance, while others may be used to create fiberglass suited for applications like cookware.
A-glass, also known as alkali or soda-lime glass, is the most common type of fiberglass material. It accounts for approximately 90% of glass production and is used in making jars, bottles, and windows. A-glass is chemically stable, inexpensive, highly workable, and durable. Its ability to be remelted and softened multiple times adds to its popularity.
There are two main types of A-glass: flat glass and container glass. Flat glass is produced using the float process, while container glass is made using the blow method. The key difference between the two types lies in the quantity and mixture of raw materials used in their production.
C-glass, also known as chemical glass, is specifically designed to resist chemical influences and offer protection in corrosive environments. Its high calcium borosilicate content imparts these chemical-resistant properties. C-glass is commonly used as a laminate, similar to surface tissue, for applications such as pipes and tanks that store water and chemicals.
D-glass, known for its low dielectric constant due to the inclusion of boron trioxide, is ideal for manufacturing optical cables. The addition of borosilicate further provides it with a low coefficient of thermal expansion. These characteristics make D-glass well-suited for electrical appliances and cookware, where minimal thermal expansion and excellent electrical insulation are essential.
The "E" in E-glass stands for electrical glass, reflecting its lightweight nature and suitability for aerospace, marine, and various industrial applications. Its excellent draping properties make it easy to handle and clean.
Originally developed for electrical applications, E-glass is now widely used to reinforce thermosetting plastics. Its robust nature provides strong protection against mechanical impacts, making it versatile for many different applications beyond its initial scope.
HR-glass, known for its exceptional thermal resistance, can withstand temperatures up to 800°C. This aluminosilicate material is a viable alternative to E-glass due to its superior high-temperature performance.
Advantex glass combines E-glass with ECR glass, offering the same corrosion resistance as ECR glass but at a lower cost. With its higher melting point, Advantex fiberglass is suitable for environments with thermal fluctuations and is commonly used in the oil, gas, mining, and wastewater management industries.
ECR glass, or electronic glass fiber, is known for its mechanical strength, waterproofing properties, and resistance to alkali and acids. Made with calcium aluminosilicates, it offers durability, acid resistance, and electrical conductivity at a lower cost compared to other fiberglass types.
AR-glass, or alkali-resistant glass, is specifically designed for use in concrete. It contains Zirconia, which enhances the concrete's strength and flexibility. AR-glass is highly resistant to dissolution in water and remains stable across varying pH levels.
R, S, and T-glasses offer superior tensile strength and better wetting and acidic resistance compared to E-glass. Their improved properties come from reduced filament diameter. These types are used in military and aerospace applications, as well as for rigid ballistic armor, and are priced higher due to their specialized uses.
S2-glass is the highest quality fiberglass, characterized by its increased silica content, which enhances weight, temperature resistance, compressive strength, and impact resistance. It boasts a tensile strength 85% greater than other fiberglass types, making it exceptionally durable and resistant to damage.
SiO₂-glass, with its remarkable temperature resistance of over 1000°C, is a durable fiberglass that does not vaporize or melt under extreme heat. Its tetrahedral and amorphous molecular structure contributes to its longevity and distinguishes it as a next-generation fiberglass.
M-glass fibers are known for their strength and ability to endure high pressure and impact. Made with silicone-treated reinforced fiber plastic, M-glass offers greater dimensional stability due to its densely aligned fibers, enhancing strength without increasing weight. The addition of beryllium increases its elasticity.
Z-glass features outstanding mechanical properties and resistance to UV rays, acids, alkali, salts, scratches, wear, and temperature changes. It is one of the most durable fiberglass types, offering semi-transparency and compatibility with 3D printing. Z-glass is a reliable alternative to brittle glass, used in automotive prototyping.
Tow and roving fiberglass, known for its superior properties, is delivered in spools for use in filament winders or cut for stiffening. It must be stored under tension to maintain its mechanical properties.
Veil mats consist of thin continuous strands of fiber arranged in a roll with a tissue-like consistency and held together by a light binder. While not intended for structural applications, they are used in molds behind surface coatings.
Chopped strand mat is made from fibers a few inches long, placed haphazardly. Though not very strong, it is isotropic, providing uniform strength in all directions. It is the most economical and commonly used type of fiberglass mat, suitable for mold production.
Woven fiberglass fabric is anisotropic, with fibers oriented in two directions and bundled like yarn, resulting in high strength. It must be aligned parallel to the load, and additional fabric is needed for strength in other directions. Various weaves, including plain, twill, and satin, offer differing levels of pliability and strength, with plain weaves being the least pliable.
Woven fiberglass fabric comes in various types, with plain weave being the most common yet least pliable. Twill and satin weaves offer greater pliability and strength compared to plain weaves. Their increased flexibility allows them to conform easily to complex shapes and designs.
The discovery that fiberglass, when combined with resin, enhances strength and durability revolutionized its role in various industries. Its widespread use is attributed to its affordability, resistance to impact, corrosion, and chemicals, as well as its outstanding strength-to-weight ratio.
Fiberglass plays a crucial role in numerous industries, so much so that its applications could fill a book. Below are a few examples of industries where fiberglass is an essential resource for product manufacturing.
Fiberglass is integral to boat construction, used in everything from hulls to decks, tables, and chairs. Since its first application in boat design in 1942, advancements in resin technology and production methods have made fiberglass the material of choice for manufacturers. Compared to wood, aluminum, and steel—materials that are more challenging and costly to shape—fiberglass offers a cost-effective and versatile alternative.
Fiberglass is widely utilized in home furnishings, with applications including door frames, window frames, shower stalls, bathtubs, swimming pools, hot tubs, and even kitchen sinks and appliances. Its versatility and durability have expanded the possibilities in the home furnishing industry, offering a range of innovative products.
Fiberglass is essential for creating amusement park attractions, such as water slides, troughs, and funnels. Its ease of shaping and forming allows for the construction of themed elements like rocks and facades, either crafted on-site or off-site. Amusement parks employ specialists skilled in fiberglass repair to maintain the many attractions effectively.
Fiberglass is crucial in electronics, providing the base material for circuit boards in devices such as laptops, computers, and cell phones. Its lightweight properties make it an ideal choice for these applications, ensuring that fiberglass is a fundamental component in various electronic devices found in homes.
The first car body made entirely of fiberglass was introduced in 1953. While the initial design faced challenges in terms of efficiency and practicality, advancements in fiberglass technology and the demand for fuel efficiency have since made it a key material in automotive design and production.
Fiberglass's versatility in shaping and forming allows automobile designers to create unique and intricate designs with ease. It facilitates the production of custom and replacement parts, as well as the reproduction of classic designs.
Additionally, fiberglass offers a significant cost advantage over metal tooling. The manufacturing of fiberglass parts is more cost-effective and efficient compared to metal presses, making it a valuable material in today's automotive industry.
For aircraft and aerospace applications, components must be sturdy, durable, and lightweight. S-glass, known for its high strength-to-weight ratio, is ideally suited for these requirements. It offers exceptional resistance to fatigue and maintains its dimensions even under high temperatures, making it a preferred material in aerospace construction.
Additional benefits of S-glass fiberglass include its superior mechanical strength and electrical nonconductivity. For military aircraft, its low radar thermal profile provides a tactical advantage, enhancing stealth capabilities.
In the construction industry, fiberglass is valued for its dimensional stability, lightweight nature, and durability. Its resistance to combustion, impact, and long lifespan make it a versatile material. Fiberglass is used for a wide range of applications, including exterior finishes, interior design elements, fences, skylights, swimming pools, solar heating systems, fixtures, railings, stairs, and platforms.
Fiberglass, also known as glass wool, fibrous glass, or glass fibers, consists of extremely fine glass and chemical fibers. During processes like sanding, cutting, chopping, or trimming, fiberglass can produce harmful dust. This dust contains fibers that may come into contact with the skin or eyes, posing health risks to workers.
Manufacturers of fiberglass products are acutely aware of these hazards and implement stringent safety measures to protect their workforce. This concern for safety is a significant priority in the industry.
Furthermore, the Occupational Safety and Health Administration (OSHA) has established guidelines for the safe handling and production of fiberglass. The Environmental Protection Agency (EPA) also regulates the installation and use of fiberglass products, as well as the pollutants generated during their production.
Fiberglass fibers can cause irritation to the skin, eyes, and upper respiratory tract. Prolonged exposure may lead to serious health issues. Unprotected skin contact with fiberglass can result in irritation and rashes, while inhalation of fiberglass dust may irritate the nose, throat, and respiratory passages.
Swallowing fiberglass dust can cause stomach irritation, and inhaled fibers can settle in the lower lungs, leading to persistent irritation and breathing problems.
To mitigate the hazards of handling fiberglass, employers provide employees with inspected and approved safety gear. Basic protection includes safety glasses to shield the eyes, and goggles for full eye enclosure. Various types of masks that cover the nose and mouth are also used to prevent particle inhalation.
Gloves are a standard piece of equipment designed to prevent fiberglass particles from coming into contact with the hands. These gloves usually extend up to the elbow, covering the forearm.
For those who work with fiberglass regularly, more comprehensive protective gear is provided, including head and neck coverings with built-in respirators and interchangeable air filters.
Additionally, protective clothing such as jumpsuits covers workers from neck to ankles. This clothing is crafted from a fine weave of resilient material designed to block dust particles.
Work areas involved in fiberglass production are equipped with eye washing fountains featuring dual jets of water. Additionally, manufacturers provide showers and hand washing stations to ensure thorough hygiene and protection for employees.
Several sections of OSHA regulations address concerns for workers exposed to fiberglass dust:
General Industry 29 CFR 1910: This regulation pertains to dust from synthetic fibers.
Health Effects: OSHA publishes information on the health effects of exposure to synthetic fibers, based on data from various national and international organizations.
Exposure Limits: This section provides details on exposure limits for all chemicals, including synthetic fibers, with specifics for each type of toxic material.
OSHA No. 2005-149: This document describes exposure limits, measurement methods, protection and sanitation practices, first aid, respiratory recommendations, symptoms, targeted organs, and potential cancer risks.
OSHA also offers guidance on appropriate protective gear, lung protection strategies, and identifies carcinogenic materials.
Standard 1926.957: This standard is specifically tailored for the construction industry, addressing the use of fiberglass in construction.
The EPA provides information on the pollutants produced by fiberglass fabrication, including methods for reducing these pollutants and resources for managing them effectively.
Fiberglass is a plastic reinforced material where glass fiber is used as reinforcement, and the glass fiber is flattened into a sheet. It is also known as glass fiber reinforced plastic or glass reinforced plastic...
Many of the products used daily are made possible by producers and suppliers of rubber and plastic. These substances are robust, adaptable, and capable of practically any shape required for various industrial purposes. Several varieties are...
Plastic fabrication is the process of designing, manufacturing, and assembling a product made out of plastic material or composites that contain plastic. There are numerous plastic fabrication methods known today, considering the wide variety of products made out of plastic...
Plastic injection molding, or commonly referred to as injection molding, is a manufacturing process used in the mass fabrication of plastic parts. It involves an injection of molten plastic material into the mold where it cools and...
Plastic materials are objects artificially made from organic compounds called polymers along with other additive components. They possess excellent formability, making them extremely versatile for many different fabrication and manufacturing processes...
Plastic overmolding has a long and interesting history, dating back to the early 1900s. The first overmolding process was developed by German chemist Leo Baekeland, who invented Bakelite, the first synthetic plastic. Baekeland used a...
A polyurethane bushing is a friction reducing component that is placed between moving and stationary components as a replacement for lubricants. The use of polyurethane for the production of bushings is due to...
Polyurethane molding is the process of fabricating or manufacturing plastic parts by introducing a urethane polymer system into a tool or mold and allowing it to cure. Like any other type of plastic, the excellent processability...
Polyurethane rollers are cylindrical rollers covered by a layer of elastomer material called polyurethane. Depending on the application, the inner roller core is prone to scratches, dents, corrosion, and other types of damage...
Reaction injection molding or RIM molding is a molding process that involves the use of two chemical elements with high reactivity and low molecular mass that collide and mix before being injected into a closed mold. High pressure pumps circulate isocyanate and...
Thermoplastic molding is a manufacturing process that works to create fully functional parts by injecting plastic resin into a pre-made mold. Thermoplastic polymers are more widely used than thermosetting...
Urethane casting is the process of injecting polyurethane and additive resins into a soft mold usually made of silicone elastomer. The casting process is similar to injection molding; injection molding differs by using hard, metal molds...
Urethane wheels are wheels made of molded urethane, also known as polyurethane. Urethane is an elastomer that comprises urethane carbamate linkages and is a portmanteau phrase for elastic polymer...