Fiberglass Molding
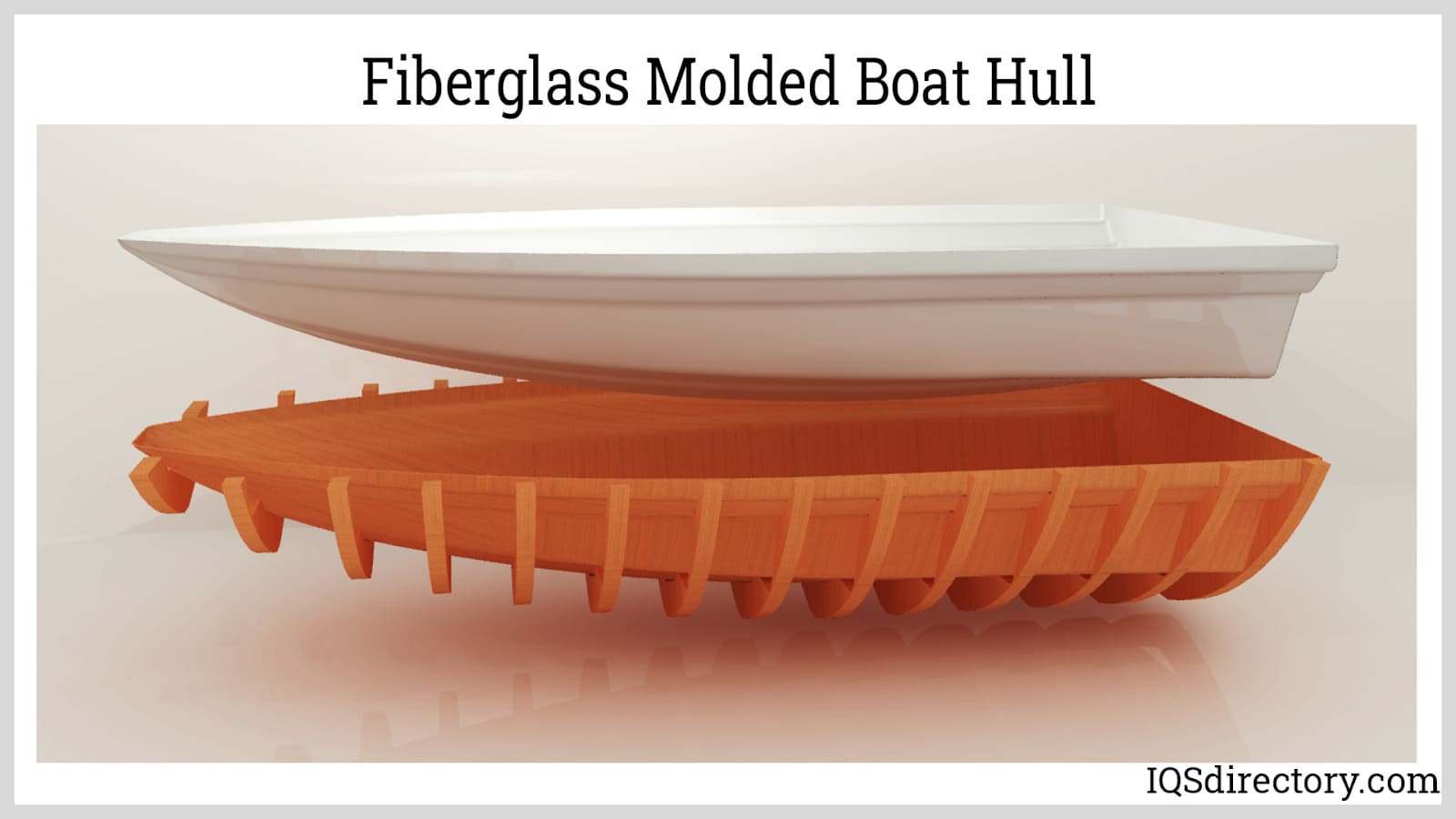
Fiberglass molding is a method for forming complex and intricate parts using fiberglass resin. Though there are several reasons for producing parts and components from fiberglass, the most pressing reasons are the...
Please fill out the following form to submit a Request for Quote to any of the following companies listed on
This article will take an in-depth look at fiberglass sheets.
You will understand more about topics such as:
Fiberglass sheets are composed of fine, small-diameter glass fibers reinforced with plastic. These sheets are renowned for their outstanding tensile strength and their resistance to corrosion, fire, and chemical elements like organic solvents, bleach, and acids. The primary advantage of fiberglass sheets lies in their impressive strength-to-weight ratio—a result of the fibers absorbing the load while the plastic evenly distributes the weight. These sheets are produced in thicknesses ranging from 1.5 mm to 75 mm.
Fiberglass is made of glass fibers interwoven within a resin matrix. Although the basic structure of fiberglass remains consistent, differences exist in the proportions and types of raw materials utilized. Key components include silica sand, soda ash, and limestone, supplemented by varying quantities of borax, calcined alumina, magnesite, kaolin clay, and feldspar. Silica sand forms the backbone of the glass fibers, while soda ash and limestone function to reduce the melting point of the glass. Other additives, like borax, are included to alter and enhance the fiberglass's specific properties and features.
The production of fiberglass sheets and panels starts with the creation of fiberglass itself. While there are proprietary methods for producing fiberglass, the core process is consistent, beginning with the formation of glass fibers.
Fiberglass is manufactured through an extrusion process, where molten material is forced through a bushing. The process begins by melting the raw materials, which are then extruded through bushings or spinnerets with 200 to 3000 fine orifices. As the filaments exit the extruder, they are coated with resin to shape and solidify them.
There are two main types of filaments: continuous and staple filaments. These filaments are sized (coated with a chemical finish) and gathered into rovings. The weight of the glass fibers, known as yield, depends on the number and thickness of the filaments in each roving.
The initial stage of fiberglass manufacture is called batching. This is when raw materials are prepared to be fed into the furnace. In this stage, raw materials must be carefully weighed in exact quantities and thoroughly mixed (batched). Due to increased technology batching has become automated, using computerized weighing units and enclosed material transport systems.
Once the batch is prepared, it is introduced into the furnace where it begins to melt. Raw materials are loaded into the furnace, and the melting process is initiated. The furnace can be heated using electricity, fossil fuels, or a combination of both. Maintaining precise temperature control is crucial to ensure a smooth, consistent flow of molten glass.
The furnace is generally divided into three main sections, each facilitating the flow of glass. In the first section, the batch is melted and homogenized while removing any bubbles. The molten glass then moves to the refiner, where it is cooled and its temperature is lowered. The final section, known as the fire hearth, houses a series of four to seven bushings used to extrude the molten glass into fibers.
After the melting process, the next step is fiberization, where the molten glass is transformed into fibers. Fiberization involves both extrusion and attenuation. During extrusion, the molten glass is forced through a bushing made of a platinum/rhodium alloy with fine orifices. As the glass exits the fire hearth, it is cooled by water jets.
The molten streams are then drawn through attenuation, which reduces them to filaments with diameters ranging from 4 to 34 micrometers (µ). A high-speed winder captures these streams, applying tension to create thin filaments. There are different methods for forming fibers, primarily the continuous filament and staple fiber processes.
In the continuous filament process, fiberglass filaments of indefinite lengths are produced. As molten glass flows through the bushing, high-speed winders collect and wind the filaments at rapid speeds, resulting in fiberglass yarn.
The staple fiber process involves passing molten material through small openings, where it is then subjected to a jet of compressed air. This converts the molten streams into long, thin fibers, which are collected into slivers and woven into yarn.
Chemical coating is the final stage where a chemical coating or sizing is applied. The sizing can range between 0.5 to 2.0% by weight, including binders, lubricants and coupling agents. Abrading filaments can be mitigated by using lubricants, which minimize breaking at the collection and wounding into forming packages.
The filaments are transformed into fabrics using weaving machines and other processing equipment. A coupling agent is used to enhance the adhesion between the fibers and the resin. This improves the bond between the fiber and the matrix, ensuring better resin penetration. Depending on the type of sizing chemistry, fibers may be more compatible with either epoxy or polyester resins. To reduce fiber abrasion, lubricants can be applied either by incorporating them into the binder or by directly spraying them onto the fibers.
The processed fibers are then used to produce fiberglass mats, which are a nonwoven, high-quality material for making fiberglass sheets. Fiberglass fibers vary in length and diameter, affecting the performance of the nonwoven material. Mats made from long, large-diameter fibers differ significantly from those made with short, small-diameter fibers.
The fibers are dispersed and suspended in a pulping system to create a uniform mixture. Whitewater chemistry is employed to keep the fibers evenly suspended, preventing them from clumping together without the use of processing chemicals. This step is crucial for ensuring the quality of the fiberglass matting.
The mat forming process operates in a closed-loop water system. Following the pulping stage, fibers are evenly spread across the full width of the mat forming machine. Adjustments to the machine control the properties and performance of the final mat. Throughout the matting process, the orientation and alignment of the fibers shift, which significantly impacts the mat's surface quality and strength.
After the mat is formed and the fibers are oriented, the mat's initial strength is relatively low, necessitating the application of a binder. Over time, various types of binders have been developed, with modern options being free of formaldehyde and derived from bio-based materials. Depending on the application, mats can be made either soft like cloth or rigid for use in laminates.
During the drying phase, water is removed from the nonwoven mats, and the binder is cured. Precise control of the drying conditions is essential to maintain the quality of the mats.
Woven fiberglass is a dense cloth with a high fiber content, created similarly to fabric by interlacing warp and fill threads at right angles. There are two primary weaving techniques: twill and satin.
In a satin weave, a fill yarn passes over three to seven warp threads before intersecting another warp thread. This creates a stronger weave due to the alignment of the fibers. A twill weave combines elements of both plain and satin weaves, providing a balance of strength and flexibility.
Woven roving fiberglass, made from continuous filaments, offers enhanced strength and is used to add thickness to laminates. Its rough texture makes it challenging to blend with other woven roving materials. To address this issue and to create layers of woven roving fiberglass, mat fiberglass layers are placed between the woven roving sheets.
The production of fiberglass fibers is the beginning of the production of a wide assortment of fiberglass products, including fiberglass sheets and panels. The type of fiberglass material, such as woven roving, mat, and the various types of woven fiberglass, are the initial materials for different types of large flat fiberglass. The combined fiberglass, depending on the thickness of the fibers, can be thick and heavy or light like fine cloth.
The formation of fiberglass panels and sheets involves a process known as pultrusion, which differs from extrusion. In pultrusion, a pulling system draws the combined materials through the pultrusion machine. This process uses a resin mixture that includes polyester, epoxy, or vinylester, along with fillers, additives, and reinforcing fibers such as rolled fiberglass mats or rovings. Pultrusion is a continuous operation that produces fiberglass components and materials in various lengths.
During pultrusion, the mat or roving is first saturated with the resin mixture and then drawn through a heated forming die. The heat from the die initiates the curing of the resin, resulting in a rigid, hardened profile. This fundamental process can vary depending on the desired geometry of the fiberglass panel or sheet.
As the reinforcement material exits the resin impregnator, it is prepared for shaping. A preformer removes excess resin before the material enters the die, where a thermosetting reaction occurs to cure the composite. Once cured, the panels or sheets are cut to the required lengths and allowed to cool to prevent cracking and deformation.
As part of the panel and sheet manufacturing process, a surface veil is applied to both the top and bottom of the panel or sheet. This surface veil is introduced before the thermoset resin is impregnated into the fiberglass mat or roving. It ensures a smooth and even finish on the final sheets or panels. Surface veils are composed of dispersed glass or polyester fibers, which provide additional protective qualities.
There are many machines available to produce fiberglass sheets, and they are important in today's society because fiberglass sheets are widely used in various industries such as construction, automotive, and aerospace for their lightweight, strong, and insulating properties. Below we examine many notable manufacturers of machines used for fiberglass sheet production:
The MFG-FLS Series by Molded Fiber Glass Companies is engineered for producing fiberglass sheets. It features continuous filament winding, accurate resin application, and sophisticated curing systems, facilitating high-efficiency and high-quality fiberglass sheet production.
The Patriot™ Filament Winding System from MVP is a highly adaptable machine designed for fiberglass sheet manufacturing. It automates the placement of continuous fibers on rotating mandrels, enhancing the precision and efficiency of the filament winding process.
RIMSTAR’s filament winding machines are equipped with advanced control systems, programmable winding patterns, and multi-axis motion capabilities, ensuring accurate fiber placement and versatile configurations for fiberglass sheet production.
Cannon SpA offers a comprehensive line of equipment for fiberglass sheet production, including resin impregnation machines, curing ovens, and cutting systems, designed to streamline and enhance the efficiency of the manufacturing process.
Ashland provides a range of equipment for fiberglass sheet production, featuring resin impregnation lines, curing systems, and finishing solutions. Their equipment ensures high-quality and efficient production of fiberglass sheets.
It is important to check with the manufacturers or industry experts for the most recent updates on models and features, as they may have changed since the last update. For the latest information on the capabilities and specifications of fiberglass sheet production machines, please consult the relevant sources.
Fiberglass offers several advantageous properties for a range of applications. When combined with composites, the glass strands exhibit enhanced benefits and performance.
Reinforced fiberglass sheets possess varying degrees of strength and flexibility, making them both lightweight and robust. Their high resin content contributes to a non-porous surface that resists moisture absorption, allowing them to perform well in diverse environmental conditions.
Even in thinner forms, fiberglass excels as an insulation material. Its low moisture absorption, high dielectric strength, and low dielectric constant make it an ideal choice for electrical insulation applications.
As a mineral-based material, fiberglass is inherently non-combustible and offers excellent heat resistance. It does not support or spread flames, and when exposed to high temperatures, it does not produce toxic fumes or smoke. Fiberglass maintains about 50% of its strength even at extreme temperatures.
Fiberglass exhibits strong resistance to most chemicals and is highly resistant to corrosion, making it suitable for harsh chemical environments.
Fiberglass maintains its shape and dimensions under varying temperature and humidity conditions. It resists warping, bending, and shrinking due to its low coefficient of thermal expansion, ensuring stability in extreme conditions.
Different sizes and types of fiberglass can bond effectively with various synthetic resins and certain mineral matrices, such as cement and plaster, enhancing its versatility.
Fiberglass composites, with their high surface area to weight ratio, prevent thermal bridging and provide significant heat insulation compared to asbestos and organic fibers. This makes fiberglass an excellent choice for thermal insulation applications.
Fiberglass retains its structural integrity and is resistant to damage from rodents and insects. It does not rot and remains unaffected by most chemicals and weather conditions, as it does not decompose.
Fiberglass remains unchanged when exposed to water. It does not absorb moisture, so its physical and chemical properties remain stable.
Fiberglass can be created using varying proportions of raw materials, resulting in different types of fiberglass. These can be classified into the following categories:
A-glass, also known as alkali glass or soda-lime glass, is known for its chemical resistance. It is the most commonly available type of fiberglass and is primarily used for manufacturing glass containers, such as jars and bottles for food and beverages, as well as window panes. Soda-lime glass is economically viable, chemically stable, hard, and easy to work with. It can be remelted and softened, making it ideal for glass recycling.
The A-glass type is composed mainly of lime, soda, alumina, dolomite, silica, and finishing agents like sodium sulfate. A-glass fiber can be found in the following forms:
Flat glass - used for making windows. The float process is utilized in forming flat glass. It contains a higher amount of magnesium oxide and sodium oxide and lower amounts of silica, aluminum oxide, and calcium oxide compared to container glass.
Container glass - typically used for making containers. It is produced through blowing and pressing methods. Container glass exhibits enhanced chemical durability, making it suitable for storing food and beverages due to its lower content of water-soluble ions like sodium and magnesium.
Advantex glass is resistant to acid corrosion and is suitable for applications involving significant thermal fluctuations due to its higher melting point. This type of fiberglass contains a high quantity of calcium oxide and is typically used in environments prone to corrosion. Advantex glass finds applications in the oil industry, mining industry, sewage systems, and power plants due to its durability and resistance to harsh conditions.
This type of fiberglass is alkali-resistant glass.
AR-glass, also known as alkali-resistant glass, is specifically designed for use in concrete. Zirconia is added to the AR-glass structure, enabling it to be used effectively in concrete. This addition helps prevent cracking and provides both flexibility and strength to the concrete. AR-glass is resistant to dissolution in water and remains generally unaffected by changes in pH. It does not rust and can be easily incorporated into steel mixtures and concrete.
The C-glass type, also known as chemical glass, offers excellent chemical impact resistance. It maintains structural stability in corrosive environments, thanks to its high calcium borosilicate content. The chemicals used in its manufacturing ensure that C-glass exhibits high resistance regardless of whether the environment is alkaline or acidic. As a result, C-glass is commonly used as surface tissue in the outer layers of laminates for tanks and pipes that store chemicals and water.
Ingredient | % Composition |
---|---|
Silica | 62 to 65 |
Soda, Potash | 1.0 |
Lime | 6 |
Boric Oxide | 3 to 4 |
Magnesia | 1.0 to 3.0 |
Alumina | 11 to 15 |
D-glass is notable for its low dielectric constant, thanks to the presence of boron trioxide in its structure. This type of fiberglass is commonly used in optical cables, cookware, and electrical appliances.
E-glass, also known as electrical glass, is renowned for its excellent electrical insulation properties. It is an alkali glass that is susceptible to chloride ions and thus is not suitable for marine applications. E-glass is a lightweight composite material used in aerospace and industrial applications. It is valued for its draping characteristics, making it cleaner to work with. Originally developed for electrical applications, E-glass is now utilized in various other fields as well. Glass reinforced plastic, made by combining E-glass with thermosetting resins, can be used to produce panels and sheets for diverse industries. This material provides structural integrity and protection against mechanical impact.
E-glass is highly popular across industries due to its high strength, affordability, nonflammability, stiffness, resistance to moisture, low density, electrical insulation properties, heat resistance, and ability to maintain strength under various conditions.
Ingredient | % Composition |
---|---|
Silica | 52.5 to 53.5 |
Soda, Potash | Less than 1.0 |
Lime | 16.5 to 17.5 |
Boric Oxide | 10.0 to 10.6 |
Magnesia | 4.5 to 5.5 |
Alumina | 14.5 |
ECR glass fiber, also known as electronic glass fiber, offers enhanced properties compared to E-glass. It features excellent acid and alkali resistance, waterproof capabilities, high heat resistance, lower electrical leakage, higher surface resistance, and improved mechanical strength. The ECR glass manufacturing process is environmentally friendly, distinguishing it from many other types of fiberglass. ECR glass fiber is commonly used to produce transparent fiberglass reinforced panels, which benefit from a longer service life. Due to its superior resistance to acid, water, and alkali, ECR glass is known for its increased durability.
Fiberglass can also be referred to as R-glass, S-glass, and T-glass. These types offer superior modulus, acidic strength, wetting properties, and tensile strength compared to E-glass. R-glass, in particular, is utilized in the aerospace and defense industries due to its high-performance characteristics and specialized production in low volumes.
S-glass, also known as structural glass, is valued for its mechanical properties, particularly its stiffness. It is especially useful when tensile strength is critical, making it suitable for applications in aircraft and building epoxies.
S2-glass is considered the highest-performing fiberglass type available. It contains higher levels of silica compared to other fiberglass types, which enhances its properties such as compressive strength, temperature resistance, cost performance, and impact resistance. Due to its superior characteristics, S2-glass is commonly used in the textile and composite industries.
Z-glass finds applications in various industries, including concrete reinforcement and the creation of transparent products. It is also used in the production of 3D printed fibers. Z-glass is known for its reliability and durability, with high resistance to acid, alkali, UV, mechanical stress, scratches, salt, and wear.
This section will explore the diverse applications and uses of fiberglass.
Fiberglass is available in various forms to meet different needs, with the primary types including:
Fiberglass tape is well-regarded for its excellent thermal insulation qualities and is composed of glass fiber threads. It finds extensive use in scenarios such as insulating high-temperature pipelines and wrapping around different types of vessels.
Fiberglass cloth is available in forms of both glass filament yarns and glass fiber yarns. This type of cloth is commonly utilized for its heat-resistant properties, often employed in fire protection materials like fire curtains.
The aviation and aerospace sectors demand materials that are both lightweight and stable. S-glass fiberglass sheets are highly favored in this industry due to their excellent mechanical properties, including superior strength and a high strength-to-weight ratio in laminates. They also maintain their integrity at elevated temperatures. These sheets are commonly used in constructing components like wings, helicopter blades, aircraft armor, flight deck armor, and even interior elements such as floors and seats. Additionally, S-glass fiberglass sheets are non-conductive and provide low radar thermal signatures.
Fiberglass sheets offer superior mechanical properties compared to traditional construction materials, making them ideal for the building industry. Their lightweight nature, fire resistance, impact durability, and high strength make them versatile. These sheets are employed in various construction applications, including commercial, residential, and industrial projects, from bathrooms and swimming pools to skylights in industrial settings.
They are also utilized in manufacturing building components such as roofing laminates, roofing panels, door surrounds, over-door canopies, window canopies, dormers, chimneys, and windows.
In the realm of consumer goods, fiberglass is used for creating furniture frames and finished products like partition screens, decorative trays, wall plaques, sporting gear, and playground equipment. Its properties—such as high strength, lightweight nature, malleability, durability, and resistance to wear and corrosion—make it a preferred material for these items.
Fiberglass is the best material to make equipment or machinery which has to be resistant to corrosion. Some items have to be resistant to corrosion because they will be exposed to unfavorable and harsh environments. Fiberglass sheets are used in the manufacture of tanks to help them last longer. They are used in the energy production industry to make corrosion resistant equipment like underground petrol tanks, storage tanks, and cooling towers.
Fiberglass is widely utilized in the marine sector because of its robustness and resilience. A key advantage of fiberglass in this industry is its ability to be molded into various shapes with ease, making it highly versatile. It is employed in the construction of boats of various sizes and other maritime equipment. Additionally, fiberglass is used to produce docks, which are prone to corrosion, rust, and wear from salty seawater, thus providing essential protection and durability.
In the automotive sector, fiberglass sheets are extensively utilized for crafting panels, sides, covers, and various other automotive components. With the growing emphasis on reducing vehicle weight to improve fuel efficiency, fiberglass sheets have become a crucial material. They offer a lightweight alternative while ensuring durability and strength. The flexibility of fiberglass sheets allows engineers to design and manufacture a wide range of automotive parts with ease.
The high resin content in fiberglass contributes to a smooth surface finish, which is particularly beneficial in producing hoods and achieving minimal aerodynamic drag. Typical automotive components made from fiberglass include front and rear bumpers, hoods, doors, and castings. It is also commonly used in sports vehicles to reduce overall weight.
Fiberglass sheets are estimated to constitute a significant portion of the outer shells of trains and buses. High-speed trains, in particular, benefit from fiberglass due to its excellent strength-to-weight ratio and smooth surface, which are crucial for aerodynamic efficiency. Beyond the exteriors, fiberglass is also employed for interior components and protective shields for carriage equipment. The fire-resistant qualities of fiberglass make it an ideal choice for the construction of trains and trams, meeting critical safety requirements for the transportation industry.
Fiberglass grating is a composite material formed by integrating resin with fiberglass, resulting in a grating that is both visually appealing and resistant to corrosion. It is valued for its lightweight nature, fire resistance, and electrical non-conductivity, making it suitable for various industrial applications such as elevated flooring, emergency exits, and drainage covers. One of the significant advantages of fiberglass grating over metal options is its ease of installation.
Fiberglass grating is available in two main types: molded and pultruded. Molded fiberglass grating is produced using molds and comes in diverse thicknesses, patterns, and dimensions. It can be cut into square mesh patterns for flooring or used in rectangular shapes for applications like trench covers and walkways. Both configurations can feature skid-resistant surfaces.
The pultrusion method for fiberglass grating involves creating profiles that are then assembled into grating shapes. This process results in highly durable, corrosion-resistant, and low-maintenance gratings. Pultruded fiberglass gratings are designed to support significant loads over extended spans and are made by pulling fiberglass rovings and mats through a resin bath and heated molds. The grating's structural integrity is enhanced by interlocking weight-bearing bars and cross bars with a recess tie bar.
This chapter will cover both the benefits and drawbacks of fiberglass sheets, along with important factors to consider when choosing fiberglass sheets.
Fiberglass sheets may have drawbacks which are:
Nevertheless, the benefits of fiberglass sheets far surpass the disadvantages. These benefits include:
When selecting the type of fiberglass, start by evaluating the project's specific requirements and the intended use of the final product. Key factors to consider include damage resistance, the mechanical and physical properties needed for the project, and overall cost. Once you have assessed these aspects, compare them with alternative materials to choose the most appropriate option.
Fiberglass molding is a method for forming complex and intricate parts using fiberglass resin. Though there are several reasons for producing parts and components from fiberglass, the most pressing reasons are the...
Many of the products used daily are made possible by producers and suppliers of rubber and plastic. These substances are robust, adaptable, and capable of practically any shape required for various industrial purposes. Several varieties are...
Plastic fabrication is the process of designing, manufacturing, and assembling a product made out of plastic material or composites that contain plastic. There are numerous plastic fabrication methods known today, considering the wide variety of products made out of plastic...
Plastic injection molding, or commonly referred to as injection molding, is a manufacturing process used in the mass fabrication of plastic parts. It involves an injection of molten plastic material into the mold where it cools and...
Plastic materials are objects artificially made from organic compounds called polymers along with other additive components. They possess excellent formability, making them extremely versatile for many different fabrication and manufacturing processes...
Plastic overmolding has a long and interesting history, dating back to the early 1900s. The first overmolding process was developed by German chemist Leo Baekeland, who invented Bakelite, the first synthetic plastic. Baekeland used a...
A polyurethane bushing is a friction reducing component that is placed between moving and stationary components as a replacement for lubricants. The use of polyurethane for the production of bushings is due to...
Polyurethane molding is the process of fabricating or manufacturing plastic parts by introducing a urethane polymer system into a tool or mold and allowing it to cure. Like any other type of plastic, the excellent processability...
Polyurethane rollers are cylindrical rollers covered by a layer of elastomer material called polyurethane. Depending on the application, the inner roller core is prone to scratches, dents, corrosion, and other types of damage...
Reaction injection molding or RIM molding is a molding process that involves the use of two chemical elements with high reactivity and low molecular mass that collide and mix before being injected into a closed mold. High pressure pumps circulate isocyanate and...
Thermoplastic molding is a manufacturing process that works to create fully functional parts by injecting plastic resin into a pre-made mold. Thermoplastic polymers are more widely used than thermosetting...
Urethane casting is the process of injecting polyurethane and additive resins into a soft mold usually made of silicone elastomer. The casting process is similar to injection molding; injection molding differs by using hard, metal molds...
Urethane wheels are wheels made of molded urethane, also known as polyurethane. Urethane is an elastomer that comprises urethane carbamate linkages and is a portmanteau phrase for elastic polymer...